Polyurethane Bushings
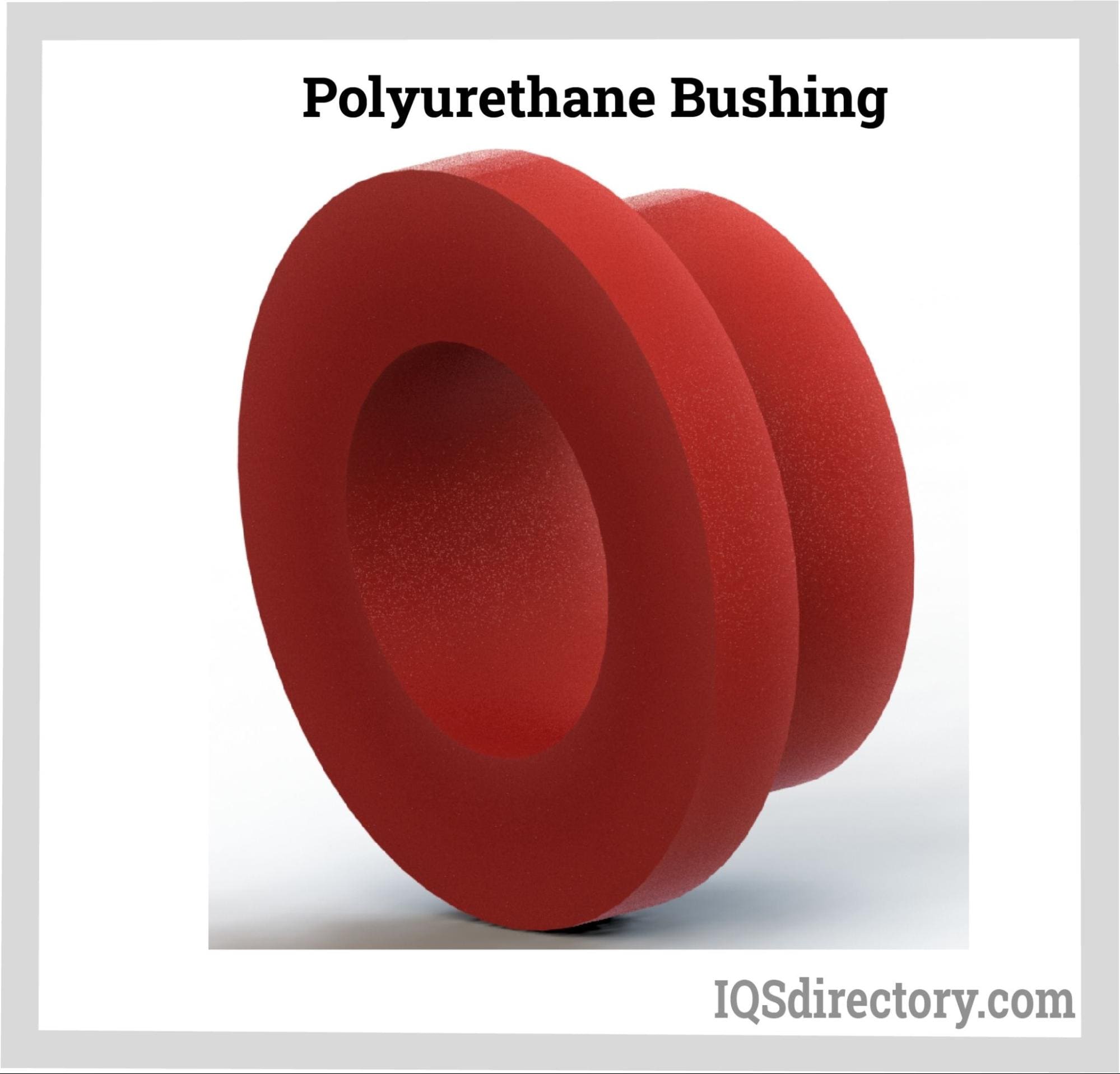
A polyurethane bushing is a friction reducing component that is placed between moving and stationary components as a replacement for lubricants. The use of polyurethane for the production of bushings is due to...
Please fill out the following form to submit a Request for Quote to any of the following companies listed on
This article will take an in-depth look at urethane wheels.
The article will bring more detail on topics such as:
This chapter delves into urethane wheels, exploring their composition, structure, and the core principles of their operation.
Constructed from molded urethane, also referred to as polyurethane, urethane wheels belong to a class of elastomers known for urethane carbamate linkages, derived from the concept of "elastic polymers."
Urethane wheels skilfully amalgamate the advantages of metal, plastic, and rubber wheels. They present superior cost-efficiency, heightened flexibility, enhanced noise dampening, resilience, and stronger defenses against impacts, abrasion, and corrosion when compared to metal wheels.
When dealing with low temperatures, impact resistance, low cold flow, abrasion, and radiation resistance, urethane surpasses plastic. In comparison with plastic wheels, urethane wheels excel in noise reduction, resilience, elastic memory, and cost-related benefits. Furthermore, urethane's extensive hardness range, ease of customization, and outstanding impact resistance give it an edge over rubber. Additionally, urethane wheels can be retooled and recoated, which helps avert costly fine-tuning tasks.
Urethane wheels are produced through polyurethane molding, which involves the encapsulation of a urethane polymer system within a tool or mold, allowing it to cure, thereby fabricating or manufacturing plastic entities. Thanks to polyurethane's superior processability, it stands out as an effective material used in producing various consumer goods and industrial components just as other plastics. Polyurethane molding can achieve precise tolerances and complex shapes, including those used in urethane wheels.
Polyurethanes, being versatile materials, can be formulated to accomplish a wide spectrum of plastic attributes, showcasing different mechanical properties ranging from soft and flexible to hard and strong. Some formulations can produce high-performance engineering-grade outputs.
This part delves into the way urethane wheels are constructed.
Fabricating urethane wheels involves the integration of standardized components through two primary methodologies.
Urethane is heated into a liquid and poured into a mold resembling a wheel, where it gradually cools and solidifies. Synthetic resins may also be incorporated in this procedure, primarily used for prototyping and small-batch manufacturing.
This method involves melting urethane into a liquid state then injecting it into a wheel-shaped mold via fill holes with a low-pressure pneumatic injection gun. Injection molding systems incorporate numerous motors, heaters, and other moving parts, consuming significant energy. Research aims at enhancing this process's energy efficiency. Injection molding accounts for approximately 32% of all plastic processing applications, remaining a prevalent plastic processing approach today.
Alternative methods can be employed to craft urethane wheels from molded urethane. These can be made from solid urethane or composite materials including cast iron, aluminum, and steel. Such wheels are ideal for heavy-duty applications. In bonded-to-metal wheels, the core is metal, and the tread is made of urethane. Manufacturing urethane wheels is notably cost-effective, and their usage is FDA-approved for clean rooms and sterile environments.
Though polyurethane is a form of urethane polymer, there's no substantial difference between the two materials. Polyurethanes primarily comprise polyols and diisocyanates, complemented by curatives and additives for specialized property enhancement. For polyurethane foams, blowing agents, surfactants, and catalysts are vital for developing foam structures.
Polyurethanes include several materials with primary polyols and diisocyanates, and additional curatives and additives for specific polyurethane enhancement. Blowing agents, surfactants, and catalysts assist in generating the gases required for the foam structure formation.
Polyol is an organic molecule possessing one or more hydroxyl (OH) groups. In urethane casting, polyols fall into two categories: polyether polyols and polyester polyols.
Generated through the interaction of organic oxides with glycol, polyether polyols are noted for outstanding impact resistance, low heat buildup in dynamic scenarios, hydrolysis resistance, and low-temperature performance. In the polyurethane domain, PTMEG (polytetramethylene glycol) and PPG (polypropylene glycol) prevail, with PTMEG being a superior choice due to better performance albeit higher costs.
Formed through the polycondensation of di-acids and glycol, polyester polyols exhibit superior abrasion and oil resistance, heat aging resistance, shock absorption, solvent resistance, and tear resistance compared to polyether polyols.
Common polyester polyols include polycarbonate and polycaprolactone. Polycarbonates are valued for their strength and rigidity, while polycaprolactone boosts resistance against water, oil, solvent, and chlorine in cast urethanes.
Diisocyanate compounds, similar to polyols, are fundamental components of the polyurethane system's resin. The two major categories of diisocyanates are aliphatic and aromatic.
A defining trait of aliphatic diisocyanates is their non-yellowing nature. Their reduced reactivity makes them apt for chemical-resistant coatings. These compounds are prevalent in polyurethane coatings, castings, and films where color stability is paramount. Leading aliphatic diisocyanates include hexamethylene diisocyanate (HMDI), hexamethylene diisocyanate (HDI), and isophorone diisocyanate (IPDI).
Aromatic diisocyanates constitute more than 90% of total diisocyanate usage. They segregate into toluene diisocyanate (TDI), naphthalene diisocyanate (NDI), and methylene diphenyl diisocyanate (MDI).
Specific features of polyurethane foams also arise. In addition to the prepolymer system's polyols and diisocyanates, blowing agents, surfactants, and optional catalysts are employed to manufacture the foam. These elements play a role in generating foaming gases and regulating them for ideal foam structure realization.
These agents introduce gas into the polymer system, forming the foam's cellular framework. Gas introduction can be chemical or physical. Originally, CFC-11 (trichlorofluoromethane) was favored for its non-combustibility, suitable boiling point, compatibility with polyurethane, and low toxicity. However, it was banned due to ozone depletion concerns under the Montreal Protocol of 1987, leading to replacements like water, pentane, methylene chloride, hydrocarbons, and other zero ozone depletion potential blends.
Surfactants, predominantly silicone-based, assist in foam formation and stabilization of polyurethane foams. They essentially reduce surface tension, prevent foam collapse pre-cross-linking, control cell size, minimize post-cure shrinkage, and counteract particle-induced solution deformations.
Catalysts control the reaction speed between isocyanate and hydroxyl groups and the gas production rate. Both these processes must synchronize for optimal foam formation. If polymerization outpaces gas creation, the cell formation collapses resulting in curing shrinkage and cooling. Conversely, rapid gas generation risks premature cell expansion before stabilization. Balanced reaction rates are crucial for forming uniformly open cells.
Used to crosslink long chain-like molecules formed in the polyol-diisocyanate reaction, curatives and chain extenders mixed with the prepolymer system produce solid or semi-solid elastomers, featured in most thermosetting polyurethane formulations. The predominant variants include hydroxyls and amines.
These curatives comprise hydroxyl group terminal molecules, facilitating prepolymer linkage. A regularly used hydroxyl curative at ambient temperatures is 1,4-butanediol (BDO), often utilized in MDI prepolymer systems.
Apart from hydroxyl groups, amine groups can attach to prepolymer terminals. For TDI prepolymer systems, 4,4-methylenebis(2-chloroaniline) or MOCA is used but is considered carcinogenic by OSHA. Thus, alternatives like 4,4-methylenebis(3-chloro-2,6-diethylaniline) are increasingly adopted.
Additives elevate polyurethane product characteristics. Type and amount depend on polymer formulation and the intended application. Common polyurethane additives include fillers, plasticizers, stabilizers, antistatic agents, degassing aids, flame retardants, pigments, and colorants.
Preferred over harder materials such as steel or cast iron in industrial use, urethane wheels offer quieter operations. They serve as shock absorbers and cushion against uneven landscapes, decreasing noise levels to help adhere to OSHA guidelines, safeguarding employee hearing.
In contrast to rubber, urethane tires, known for their load-bearing prowess, deliver enhanced strength while retaining rubber's shock absorption and quiet operation alongside floor protection.
The larger surface area of urethane wheels versus tougher materials like nylon aids in spreading shear forces, preserving floor surfaces for longer. Furthermore, urethane wheels increase traction, lowering wheel load and transferring driving force more effectively.
Considering these specs, urethane wheels are set to deliver a satisfactory experience in industrial settings.
Correctly used, polyurethane displays impressive durability. Yet, its endurance can wane in high-heat environments or applications creating heat. Conventional urethane fails to endure over 110 degrees Celsius longer than 60-90 minutes without harm. Internal heat from cyclic urethane deflection at about 121 degrees Celsius can render it liquid within 15 minutes.
Industrial-grade polyurethane needs to outperform urethanes used in non-dynamic contexts. Optimal selection requires considering properties like tensile strength, tear strength, modulus, and abrasion resistivity.
The hot casting method is exclusive for creating industrial wheels. Hot-cast urethanes, poured at 60 to 76 degrees Celsius and cured at 87 to 114 degrees Celsius, yield robust wheels for challenging dynamic conditions. Room temperature-produced urethanes lack the physical attributes needed for industrial wheel usage.
Here's what to remember when picking urethane wheels:
A wheel's small contact area with the rolling surface makes weight distribution critical. Overloading risks deformation and thus heightened friction, resistance, and eventual failure. Understanding maximum supportable loads ensures proper wheel selection.
Even with urethane's adaptability to rough surfaces, surface type influences wheel performance. Smooth concrete versus rough terrain might entail alternative materials or diameters. Encountering chemicals, while urethane performs well in such environments, is another crucial factor.
Extreme braking and acceleration can impact wheel specs. Ensuring consistent traction while maintaining contact with rolling surfaces is critical. Although urethane wheels generally offer great traction, dust, grease, or oil can threaten it. Tackling these during planning is beneficial. Maintaining clean surfaces and tracks extends wheel efficiency and longevity.
Like rubber, urethane wheels respond to environmental temperature changes by expanding and contracting. Comprehending temperature ranges is essential for short-term exposure operations, like entering/exiting a freezer or mining scenarios. Specialized formulas exist for extreme conditions to boost wheel durability and lifespan.
Extremes beyond normal may cause irreparable harm. High heat can degrade a urethane wheel permanently, while very low temperatures risk brittleness, causing irreversible damage.
Shifting wheels between settings introduces environmental variables like temperature, humidity, and surface variations. Transition points, like seams, might harm wheels. Despite urethane wheels' robustness, reducing environmental variability maintains their integrity, preventing delamination. A smoother area with minimal surface transitions boosts their lifespan.
Unexpected conditions often lead to traction loss or deformation, risking build-up on wheels, casters, or tracks. Such accumulation can lead to premature failures. Regular inspection and maintaining ventilation directing airflow from tracks is vital, along with consistent track cleaning.
In challenging environments, wheels encounter bumps, sudden loads, or drops. While urethane is designed to withstand impacts, wear still affects axles, wheels, or bearings. Understanding impact dynamics beyond load handling capacities is vital. A redesign utilizing materials capable of higher damage resistance may prove necessary in such cases.
What are the key machines used for producing urethane wheels in the United States and Canada? These state-of-the-art manufacturing machines play a crucial role in the modern urethane wheel production process, enabling the fabrication of high-quality, durable, and customizable polyurethane wheels for diverse sectors such as material handling, automotive, aerospace, and warehouse equipment. By leveraging advancements in precision engineering, automation, and polyurethane processing technology, these machines ensure efficiency, consistency, and innovation in the manufacture of specialty urethane wheels and polyurethane rollers. We will explore several of these leading industrial machines and equipment below, highlighting their functions, advantages, and impact on urethane wheel manufacturing workflows.
Features: Wabash MPI Compression Molding Presses are renowned for their precision and consistency in molding urethane wheels. Employing advanced compression molding techniques, these presses deliver optimal pressure and temperature control, producing durable, high-performance polyurethane wheels with superior surface finish. This automated molding equipment is ideal for manufacturing wheels used in heavy-duty applications, minimizing material waste and maximizing process efficiency.
Features: These cutting-edge injection molding machines are noted for their outstanding efficiency, automation, and reproducibility in producing urethane wheels. Designed for high-volume manufacturing, RimStar Compact systems enable precise metering, mixing, and casting of polyurethane compounds, ensuring exceptional dimensional accuracy for custom and standard wheel profiles. Their popularity stems from the ability to scale production while maintaining rigorous quality standards, making them a top choice for industrial urethane wheel manufacturers.
Features: These robust extrusion machines are favored for manufacturing urethane wheels and polyurethane profiles with complex geometries. Davis-Standard Thermatic Extruders offer exceptional process flexibility, accommodating a wide range of wheel sizes, custom durometers, and special tread configurations. Their advanced screw technology and precise temperature control allow for consistent output, high throughput rates, and the production of wheels for specialized use cases such as conveyor systems, industrial carts, and robotics.
Features: Haas VF Series Vertical Machining Centers are critical assets in the tooling and mold-making phase of urethane wheel production. By utilizing CNC machining for precise carving, finishing, and surface preparation of aluminum and steel wheel molds, manufacturers can achieve intricate designs, tight tolerances, and smooth finishes. This translates to enhanced accuracy in cast urethane wheels and optimized performance characteristics for end users.
Features: Baulé machines are extensively utilized for small to medium-scale production of urethane wheels and specialty polyurethane products. Thanks to their excellent repeatability, automated process control, and energy-efficient design, these casting machines excel at producing prototype wheels, low-volume orders, and specialty roller components with minimal lead times.
To remain competitive in the fast-evolving urethane wheel manufacturing industry, producers often evaluate a range of equipment that meets their production requirements, quality benchmarks, and application demands. From automated polyurethane pouring systems to post-cure ovens and finishing equipment, the integration of advanced machinery is essential for ensuring repeatable quality, reducing cycle times, and enabling cost-effective production. Buyers should assess features such as cycle speed, casting or molding capacity, precision, ease of maintenance, and compatibility with custom wheel designs.
It's important to recognize that technological advancements and the popularity of manufacturing equipment can change rapidly. For the most current and accurate information on the best machines for urethane wheel production in the United States and Canada, it is advisable to consult with industry-specific sources, leading polyurethane machine manufacturers, or reputable equipment suppliers directly. Industry events, trade shows, and online directories like IQS Directory can also provide authoritative insights into trending machines, emerging fabrication technologies, and best practices for polyurethane wheel and roller production.
What types of urethane wheels are available, and what applications are they best suited for? Urethane wheels, also known as polyurethane wheels, come in a range of designs and constructions to meet the needs of various industrial, commercial, and specialized applications. Understanding the different types of urethane wheels can help you select the ideal option for conveyor systems, material handling equipment, automated machinery, and custom manufacturing processes. Below, we explore several of the most common varieties, their performance characteristics, and functional advantages.
Crowned poly wheels, sometimes referred to as crowned polyurethane wheels, offer significantly reduced rolling resistance compared to standard flat-treaded wheels or rubber wheels. These high-performance wheels typically range from 100 to 200 mm in diameter and feature a noise-reducing, non-marking urethane tire encasing a lightweight aluminum core. The crowned tread profile helps promote smooth tracking and enhances overall efficiency in conveyor belt systems and industrial carts.
Crowned urethane wheels are highly resistant to solvents, chemicals, and abrasive wear. Their construction features precision ball bearings, which contribute to extended bearing life and superior load distribution. With a load capacity of up to 600 kg, these industrial wheels are commonly used in conveyor systems, factory automation, production lines, and heavy-duty equipment requiring durable and long-lasting wheel solutions.
Engraved urethane wheels feature custom-engraved patterns—such as brand names, part numbers, identification marks, or serial codes—directly onto the tread surface. Unlike crowned wheels, engraved wheels use a flat tread, which generally provides a higher rolling resistance but allows for precise sorting and identification functionality. These high-precision wheels are available in a variety of sizes and custom hardness grades. While their load capacity is often lower than crowned wheels, they offer excellent wear resistance, reliable performance for moderate loads, and easy integration in processes where traceability or marking is required.
Desk wheels, a type of soft urethane idler or guide wheel, are frequently found in document processing equipment and automated sorting machinery. They help accurately orient and guide materials for improved optical reading, scanning, or labeling. Desk wheels are commonly used in light-duty roller applications and can be designed as soft-touch or compliant wheels, with various spring rates achieved by changing the urethane durometer (hardness). Their flexibility and smooth rolling characteristics protect sensitive documents and minimize noise in office and mailing environments.
Urethane drive wheels are engineered for maximum adaptability and load-bearing performance. These versatile wheels can be customized in terms of durometer, width, and core material to handle specific application requirements across multiple industries. Drive wheels attach securely to their hub using a key slot or bolt, providing reliable torque transfer necessary for moving heavy items, industrial robotics, AGVs (Automated Guided Vehicles), lift trucks, and conveyor systems. Due to their oil and chemical resistance, long operational life, and ability to operate in harsh environments, urethane drive wheels are widely preferred for applications that demand both durability and smooth, controlled directional changes.
Compliant polyurethane wheels, also called no-crush wheels, zero-crush wheels, and compliance wheels, are designed to handle materials of varying thickness in industrial automation and packaging machinery. These specialty wheels absorb shock and compensate for fluctuations in material feed, which eliminates the need for complex or expensive external spring mechanisms. Their spring-like deflection protects products during handling and ensures consistent processing—even with irregular item sizes.
Industries such as printing, converting, and mail processing depend on compliant wheels for reliable material separation, jam reduction, and gentle handling. The unique advantages of these urethane components extend to improved abrasion resistance, extended service life, and versatile use for both driven and idler roller applications.
The benefits of urethane compliant wheels include:
When selecting a urethane wheel for your application, consider important factors such as load capacity, abrasion and chemical resistance, wheel profile (crowned, flat, or custom), durometer/hardness, and compatibility with the intended environment. Consulting with a reputable polyurethane wheel manufacturer or supplier can help you navigate options like custom wheel molding, specialty coatings, or precision bearing integrations.
Urethane wheels deliver excellent performance in industrial casters, automation systems, conveyors, packaging equipment, and robotics, making them a smart choice for operations seeking longevity, cost efficiency, and premium wear resistance.
This chapter will explore the applications and benefits of urethane wheels.
Urethane wheels are used in a variety of applications, including:
Overhead conveyors, like many other objects, frequently employ wheels to move items. These wheels are used to transfer products down the rails of overhead conveyors and in conjunction with various carrying devices. These rails frequently contain joints in their construction, which, like expansion joints in a floor, can cause chunking and tearing. Urethane wheels can withstand a wide range of load requirements while also resisting wear, chunking, and tearing. They are designed to be exactly round and smooth, eliminating wear and wobbling.
Carts come in various sizes and strengths to accommodate different needs. Urethane wheels are commonly used on equipment carts that handle parts and components on automotive assembly lines. These carts and wheels are designed with high load capacities to support the heavy products they transport.
Urethane wheels are also well-suited for railroad applications. For instance, Stellana's urethane wheels are employed in tugger systems to move boxcars along train tracks. This material allows the wheels to operate directly on the rails while delivering reliable grip on a minimal surface area.
Several components work in tandem to dry clothing inside large industrial dryers. Urethane wheels are used in the drum's idler wheels, allowing them to rotate smoothly. As the load dries, these wheels help tumble the clothing for even drying.
In the metal construction sector, this equipment shapes metal sheets into rain gutters, siding, metal roofing, and other products. Urethane wheels serve two key functions on the equipment: the drive wheel pulls the aluminum sheets through, while the idler wheels assist in creating the required angles and bends.
Elevator contractors often choose urethane for their elevator guide wheels. These guide wheels are crucial components, working in conjunction with guide rails installed along the elevator shaft to ensure smooth movement of the elevator car. In regular operation, the guide wheels help the car travel smoothly up and down the rails. Additionally, the system includes backup safety mechanisms to quickly stop the car if the cable snaps, ensuring the car is securely halted on the rail.
Hyperloop, the high-speed transport system being developed by Tesla and SpaceX, relies on a vacuum to operate efficiently. In the event of a pressure loss that disrupts the vacuum, urethane wheels play a critical safety role by stabilizing the vehicle and gradually slowing it down from high speeds. Although the vehicle is designed to float above the ground, these urethane wheels are essential for ensuring a safe and controlled stop, highlighting the remarkable capabilities of polyurethane in demanding applications.
Urethane wheels find diverse applications across various industries. They are used in carrying cases, conveyor bearings, grocery carts, skateboard wheels, forklift drives, roller coaster wheels, and load wheels. Industries such as medical, athletic equipment, retail, transportation, industrial manufacturing, and material handling all benefit from the durability and performance of urethane wheels.
Molded urethane offers several advantages, including exceptional durability due to its resistance to cuts and rips. It also provides heat resistance, chemical resistance, noise reduction, and elastic memory. Urethane wheels can vary in hardness, ranging from sponge-soft to iron-hard, and can be customized to various hardness levels in between. Additionally, they can be manufactured in a range of colors, sizes, and shapes to meet specific needs.
Urethane wheels are resistant to ultraviolet radiation, ozone, oxygen, and various environmental conditions. They also withstand abrasive substances better than other materials. Under similar conditions, urethane experiences slower wear, extending its lifespan. Additionally, due to its higher tensile strength, urethane can support heavier loads effectively.
Urethane's chemical manufacturing process allows for a wide range of variants, enabling adjustments to its density and physical properties based on specific applications. Urethane wheels can support 6 to 7 times the load capacity of rubber caster wheels of the same size. Additionally, urethane's high elastic memory and flexibility make it suitable for various applications where traditional plastics might not perform as well.
Urethane manufacturing supports automatic and continuous production with minimal waste. Notably, some of the waste residues can be recycled into new urethane products, reducing environmental impact. Liquid casting, a straightforward process used in the production of no-cord casting wheels—often referred to as the "green wheels" of the 21st century—demonstrates urethane's efficiency. With its growing range of applications in the automotive sector, urethane wheels are poised to be a key trend in the future of automotive tires.
Failures of urethane wheels on drive wheels, industrial rollers, and industrial caster wheels can lead to significant costs for companies, including the expense of replacing the wheels and downtime for equipment. Many of these failures are preventable and can be attributed to:
In wheel or roller applications, polyurethane is often chemically bonded to a plastic or metal substrate. Delamination occurs when the tread separates from the wheel or hub, which can be caused by several factors. Poor application of adhesive before attaching the polyurethane to the hub, overheating the wheel, or exposing it to water and/or solvents at the bonding line can contribute to this issue. Additionally, some hub materials are challenging to bond. If adhesive was correctly applied, external conditions did not interfere, and delamination still occurs, considering a mechanical bond might be a better solution.
When a wheel is stationary under load, a flat spot can develop on the polyurethane tread. When the wheel starts spinning again, this flat area may or may not "roll out," making it more difficult to move the wheel from a standstill. The compression set value of the polyurethane material influences its tendency to develop flat spots. To address this issue, you can use polyurethane with a lower compression set value. Alternatively, opting for a larger diameter or wider wheel can reduce the stress on the urethane and help mitigate flat-spotting.
When urethane treads experience cyclic loading and unloading, friction within the material generates heat due to mechanical hysteresis. If the heat buildup exceeds the material's ability to dissipate it, the urethane can melt internally, leading to pressure buildup and potentially a blow-out. This problem is often caused by operating the wheel or roller at excessive speeds, overloading, or uneven loads. To address this issue, consider using urethanes with lower heat generation properties, increasing the diameter or width of the wheel, or adjusting other operational parameters to better manage heat and load conditions.
If a wheel is subjected to excessive loading in a dynamic position, the polyurethane tread may develop cracks. To mitigate this issue, you can replace the tire material with one better suited for the application. Alternatively, redistributing the weight by increasing the wheel's width or expanding its diameter can help reduce stress on the tread and minimize cracking.
Despite some drawbacks, the benefits of urethane wheels far outweigh their limitations.
Urethane wheels are made of molded urethane. They come from polyurethane molding which is the process of placing a urethane polymer system into a mold and allowing it to cure in order to fabricate or manufacture plastic items. Polyurethane's exceptional processability makes it a particularly effective material in the manufacture of wheels. Polyurethane molding can readily attain tight tolerances and complex shapes, which include urethane wheels.
Types of urethane wheels include crowned, drive, engraved, compliant, and desk. All benefits of metal, plastic, and rubber wheels are found in urethane wheels. They are more affordable, more flexible, have better noise reduction, are more resilient, and are more impact resistant, abrasion, and corrosion than metal. In terms of low temperatures, impact, cold flow, abrasion, and radiation resistance, urethane outperforms plastic. They can also reduce noise, are more resilient, have superior elastic memory, and are less expensive than plastic. However like any other material they have their disadvantages as discussed above.
A polyurethane bushing is a friction reducing component that is placed between moving and stationary components as a replacement for lubricants. The use of polyurethane for the production of bushings is due to...
Polyurethane molding is the process of fabricating or manufacturing plastic parts by introducing a urethane polymer system into a tool or mold and allowing it to cure. Like any other type of plastic, the excellent processability...
Polyurethane rollers are cylindrical rollers covered by a layer of elastomer material called polyurethane. Depending on the application, the inner roller core is prone to scratches, dents, corrosion, and other types of damage...
Urethane casting is the process of injecting polyurethane and additive resins into a soft mold usually made of silicone elastomer. The casting process is similar to injection molding; injection molding differs by using hard, metal molds...
Blow molding is a type of plastic forming process for creating hollow plastic products made from thermoplastic materials. The process involves heating and inflating a plastic tube known as a parison or preform. The parison is placed between two dies that contain the desired shape of the product...
Molding is a manufacturing process that uses a mold - the latter being a solid container used to give shape to a piece of material. It is a forming process. The form is transferred from the mold to the material by...
Fiberglass molding is a method for forming complex and intricate parts using fiberglass resin. Though there are several reasons for producing parts and components from fiberglass, the most pressing reasons are the...
Fiberglass is a plastic reinforced material where glass fiber is used as reinforcement, and the glass fiber is flattened into a sheet. It is also known as glass fiber reinforced plastic or glass reinforced plastic...
Many of the products used daily are made possible by producers and suppliers of rubber and plastic. These substances are robust, adaptable, and capable of practically any shape required for various industrial purposes. Several varieties are...
Plastic bottles are bottles made of high or low-density plastic, such as polyethylene terephthalate (PET), polyethylene (PE), polypropylene (PP), polycarbonate (PC), or polyvinyl chloride (PVC). Each of the materials mentioned has...
Plastic caps and plugs are two distinct ways for sealing the ends, tops, and openings of tubes and containers. Caps are placed over the opening, and plugs are placed in the opening. Due to the many varieties of...
Plastic coating is the application of liquid polymers or plastic on the surface of a workpiece by dipping or immersion. The result is a thick plastic finish for protective and decorative purposes. This gives the material additional resistance against...
Plastic injection molding, or commonly referred to as injection molding, is a manufacturing process used in the mass fabrication of plastic parts. It involves an injection of molten plastic material into the mold where it cools and...
Plastic overmolding has a long and interesting history, dating back to the early 1900s. The first overmolding process was developed by German chemist Leo Baekeland, who invented Bakelite, the first synthetic plastic. Baekeland used a...
Reaction injection molding or RIM molding is a molding process that involves the use of two chemical elements with high reactivity and low molecular mass that collide and mix before being injected into a closed mold. High pressure pumps circulate isocyanate and...
Rotational molding, commonly referred to as "rotomolding", is a plastic casting technique used to produce hollow, seamless, and double-walled parts. It uses a hollow mold tool wherein the thermoplastic powdered resin is heated while being rotated and cooled to solidify...
Rubber injection molding is when uncured rubber is transformed into a usable product by injecting raw rubber material into a mold cavity made of metal. The applied pressure produces a chemical reaction like...
Rubber molding is a process of transforming uncured rubber or an elastomer into a usable product by transferring, compressing, or injecting raw rubber material into a metal mold cavity...
There are several methods to perform rubber overmolding, and each method has its own unique advantages and disadvantages. The choice of method typically depends on the design and material requirements of the product being...
Silicone rubber molding is a method for shaping, forming, and fabricating silicone rubber parts and products using a heated mold. The process involves compressing or injecting silicone rubber into a mold...
Thermoplastic molding is a manufacturing process that works to create fully functional parts by injecting plastic resin into a pre-made mold. Thermoplastic polymers are more widely used than thermosetting...
A grommet edging is a flexible rubber or plastic strip that covers rough and sharp surfaces found in openings and edges of panel walls to protect the passing electrical cables, wires, and other sensitive components...