Electrical Plugs
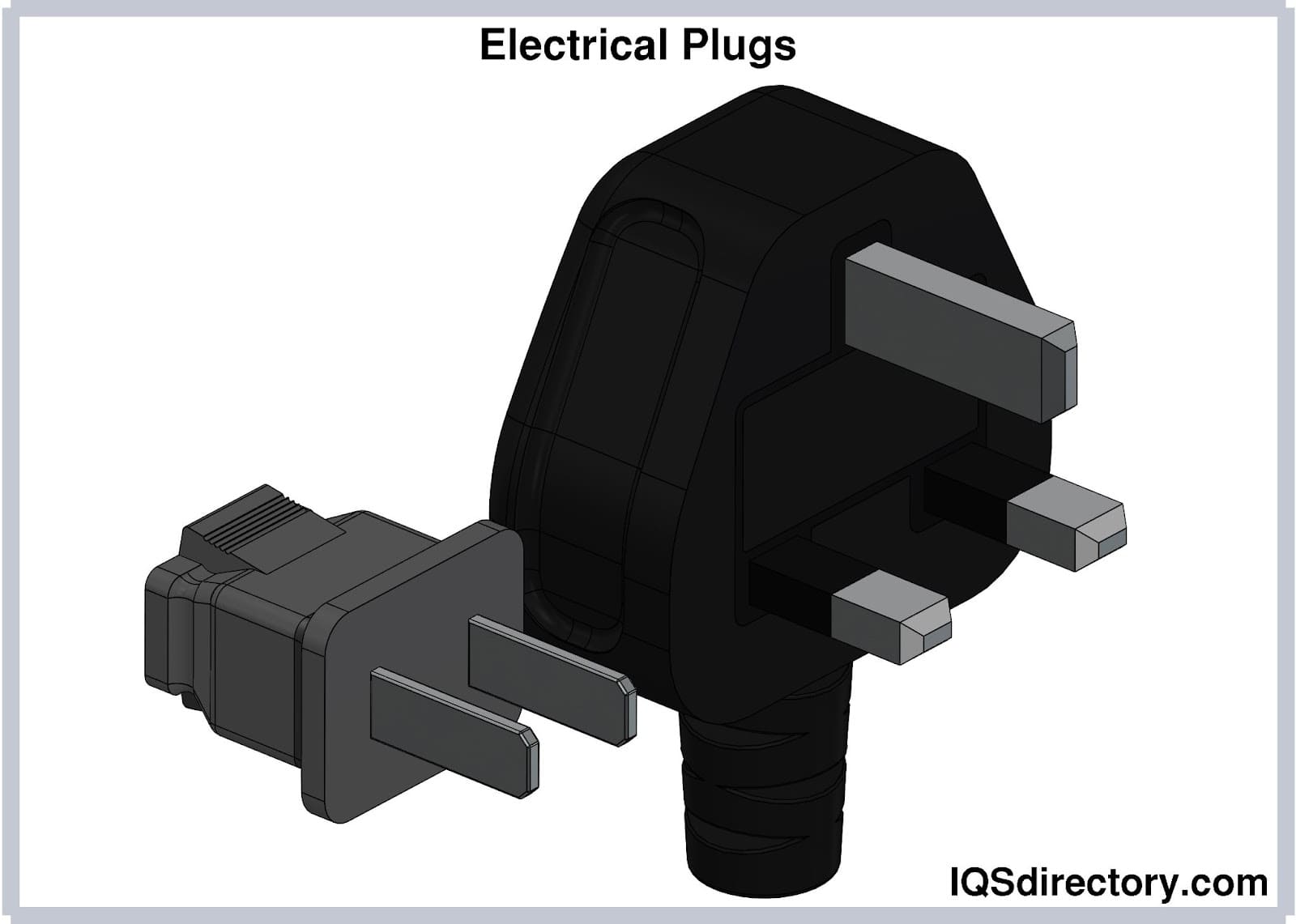
Electrical plugs, commonly known as power plugs, are devices responsible for supplying and drawing current from a receptacle to the circuitry of an electrical appliance...
Please fill out the following form to submit a Request for Quote to any of the following companies listed on
This article will take an in-depth look at AC power cords.
The article will bring more detail on topics such as:
This section explores the basic principles of AC power cords, detailing their construction and operational functionality.
An AC power cord is a detachable device that delivers alternating current (AC) from a mains supply to electrical devices and appliances. Utilized across a wide range of sectors like retail, industrial, electronics, entertainment, and residential, these cords power applications such as lighting, power tools, home appliances, shop equipment, and musical instruments, among other uses.
AC power cords facilitate alternating current (AC), with electrons changing direction periodically, transferring energy from the power source to the intended device. The cords comprise conductive wires, often copper, shielded in insulation and encased in an outer jacket made from rubber or polymers. Cord construction can vary based on specific application needs.
Key considerations in the construction and material selection for AC power cords include:
Copper serves as an electrical conductor in diverse wiring applications, essential for power generation and transmission, electronic circuitry, telecommunications, and manufacturing electrical contacts. Construction wiring dominates the market for copper wires, with nearly half of mined copper transformed into wires and cable conductors.
Copper wires within cords are frequently stranded by braiding, twisting, or bonding, enhancing the cable's flexibility.
Copper wires can be bare or plated with tin to minimize oxidation, and sometimes coated with silver or gold to extend their longevity and aid in soldering. Coaxial and twisted pair cables are designed to lower electromagnetic interference, maintain signal integrity, and improve transmission properties. Shielding with wire mesh or foil further safeguards these cables.
The material's electrical conductivity is key, as it measures the efficiency of electric charge transfer. Copper, renowned for outstanding conductivity, presents a resistivity of 16.78 nΩm at 20°C. According to solid-state metal theory: copper’s conduction band is partially filled, allowing numerous electrons to transport electric current. When electricity is introduced to copper, electrons flow towards the positive end, initiating the current.
Electrons encounter resistance due to impurities or lattice interference, known as "mean free path" inversely related to resistivity. Copper's excellent conductivity serves as a benchmark. Electrolytic-tough pitch (ETP) copper, with reduced oxygen, is often selected for its conductivity efficiency.
Despite copper’s denser nature, it remains optimal for conductive capacity without needing extensive cross-sectional width, unlike aluminum, which requires a cross-section 1.56 times larger due to its 0.6x conductivity.
Silver outperforms copper only slightly in conductivity, with a resistivity of 15.9 nΩm at 20°C.
Tensile strength indicates the maximum force a material withstands before failure. Copper's high tensile strength inhibits stretching, breaking, and deformation.
Copper’s tensile strength resists necking and creep but adds weight compared to similarly conductive aluminum wires, which might counteract its strength once installed.
Ductility reflects a material's ability to handle tensile stress, allowing it to be drawn into a wire form. Copper ranks high in ductility, only surpassed by silver and gold, facilitating very fine wiring with precise specifications.
Copper’s advantageous mix of hardness, flexibility, and ease of handling supports straightforward installation without special tools for joining or adjustments. It permits bending and twisting during installation without breaking, and it has secure connections, eliminating the need for fittings or lugs.
Aluminum wire, an electrical conduit for residential applications, is used widely for power grid infrastructure like distribution and transmission lines. Aluminum offers better conductivity per weight than copper, presenting an effective cost-efficient alternative in specific applications.
Its commendable electrical and thermal conductivity, about 60% relative to copper, combined with lower density makes aluminum susceptible to AC magnetic fields and eddy current issues.
Yet, aluminum’s use is limited by potential fire risks from loose connections. It has higher electrical resistance, requiring thicker wires to perform equivalently to copper.
Aluminum's higher resistance means it requires thicker wires than copper for the same current load, affecting installation space and circuit design.
Aluminum’s reduced ductility leads to faster fatigue under stress, causing internal wire problems and heat buildup due to increased resistance.
Moisture exposure exposes aluminum to galvanic corrosion in contact with certain metals, posing safety hazards.
Aluminum oxidizes more readily than copper, resulting in an oxide less conductive than copper oxide, threatening connection integrity and increasing fire risk.
Increased malleability can cause aluminum to compress and deform, leading to loosening and increased resistance, creating hazards.
Higher thermal changes compared to copper can degrade connections, especially in long-term setups, affecting performance.
Sensitivity to vibration leads to loosening over time, affecting aluminum's suitability in high-vibration environments.
Insulation serves as a protective measure against current leakage, environmental threats, and external damage to the conductor. High-quality insulation is essential for durability and performance.
Different insulation types cater to specialized applications—rubber, plastic, and fluoropolymer are primary materials. Insulation covers either individual conductors or multi-wire cords, and choice depends on the intended application and environmental challenges.
Plastic options such as:
PVC offers an economical and versatile insulating choice suitable for a range of temperatures from -55°C to 05°C. It is resistant to flames, abrasion and moisture, and withstands chemicals and solvents.
PVC's nontoxic nature makes it suitable for medical and food applications. However, its limitations include limited flexibility and unfavorable performance in low temperatures. Its higher attenuation and capacitance loss can negatively impact energy efficiency.
SR-PVC offers primary insulation with high abrasion resistance, providing a defense against chemicals, heat, and flame.
Meeting stringent fire safety requirements, plenum PVC is ideal for air-circulating voids like ceilings or floors.
Favored for low-capacitance wires and coaxial cables, PE's low dielectric constant offers high-speed transmission capability. Cross-linking enhances durability against grading and solvents, useful for broader temperature ranges.
With structural stiffness, it is flammable, but flame retardants raise dielectric loss, impacting energy transmission.
Similar to PE with a broader temperature range, PP is utilized in thin-wall applications, offering improved electrical insulation by foaming.
Widely used where flexibility and chemical resistance are key, such as military cords. Flammable as an insulator but viable as a jacket material.
Environmentally friendly with robust resistance qualities for industrial control and power cables.
Nylon is strong and durable against chemicals and cuts but susceptible to moisture absorption, impacting some electrical properties.
Rubber offers an array of options:
An evolution from thermoset, TPR improves processing rates and color options, though cut-through resistance is less compared to alternatives.
Suits portable cord applications and military products, thanks to its excellent cut-through, flame, and oil resistance capabilities.
Silicone withstands high operational temperatures with average abrasion resistance and flexibility, useful across electrical spaces.
Favored for high-voltage use due to small cross-sectional accommodation, possesses excellent versatility but requires thoughtful management during installation due to its relatively soft nature.
Combining natural rubbers with SBR provides mixed properties suitable for general applications depending on thermal demands or electrical resistance.
With options such as:
High temperature-ready with limited applications, representing a more expensive insulating solution.
Flexible and resistant to chemicals and high temperatures, PTFE is valuable where mechanical flexibility prevails.
By merging rubber’s elasticity and plastic’s processing, TPE serves in homes and automobiles, though challenged by heat and chemical resistance.
AC power cords convey alternating current to devices, ensuring a secure current flow. The live wire supplies voltage, alternating at regular intervals, to the appliance. The neutral wire returns current to the ground or busbar in the distribution box, maintaining a steady circuit flow. Earth wires safeguard from electric shocks, directing faults to the ground, and activate safety breaks in emergencies.
When it comes to choosing AC power cords, consider these aspects:
A cord's current rating shows its capacity to handle maximum current without overheating, influenced by insulation, current frequency, resistance, and ambient conditions.
The rated voltage dictates critical design elements like insulation type and thickness, harmonizing safety standards with performance needs for high-voltage scenarios.
```AC power cords are distinguished by their connectors, also known as couplers. These connectors facilitate the link between electronic devices or appliances and available power outlets. In addition to connectors, plugs are also used. There are various types of connectors and plugs, with the most common ones discussed below.
The International Electrotechnical Commission (IEC) established the IEC 320 C13/C14 connector standard. The "320" refers to the specification that outlines power connectors. While "60320" is the official designation of the standard, it is commonly shortened to "320" in everyday use.
The C13 line socket is widely used in the AV and PC industries. The C14 plug serves as the male connector for the C13 female socket and is typically mounted on a recessed chassis or panel, such as those found on power transformers or PC power supplies.
A polarized power connector is commonly used on notebook computer AC power cords. The C5 connector features three circular prongs arranged in a triangular pattern, which has led to the informal nickname "Mickey Mouse ears connector" due to its resemblance to the Disney cartoon character's silhouette. This type of power cord is typically used with laptop power supplies.
The C7 power connector is a 2-pronged, non-polarized plug commonly used in AC power cords for various electronic devices, including radios and power transformers. It features two round pins placed side-by-side and is typically employed to power low-voltage equipment such as portable laptop power supplies, CD players, and audio or video equipment.
The C7 connector also has a polarized version, characterized by a square-shaped overmold that ensures the prongs are oriented correctly on one side of the connector. This design ensures that the neutral terminal of a device is consistently connected to the neutral wire of the AC power supply.
The C15/C16 connectors are designed for use in environments where equipment temperatures can be high. For example, they are commonly used in data centers where devices are positioned closely together in confined spaces. These connectors feature keys that prevent mismatching the inlet and connector, ensuring correct "cold" and "hot" configurations. The shape of the C15/C16 is similar to the C13/C14 connectors, except for a notch at the bottom.
The C15/C16 connector has a higher temperature rating compared to the C13/C14 connector. There is also a variant, the C15A/C16A, designed for even higher temperature applications. This version features a rectangular ridge at the upper end of the molding. These AC power cords are commonly used in industrial settings.
The terminals of the C15/C16 connector are horizontally oriented. The connector molding is rectangular with rounded edges. This connector is used in power cords for high-power electrical devices and power supplies where C13/C14 connectors are insufficient, such as in servers or professional IT equipment. It has a maximum amperage rating of 15A and can be used in Class I equipment.
The Type G plug features a built-in fuse, typically rated at 13A. Its primary purpose is to protect the flexible power cord connecting the appliance to the plug, thereby also safeguarding the appliance from overload. A Type G socket can also accommodate a Type C plug.
This practice is unsafe and not recommended. The primary standard for Type G plugs and sockets is BS 1363. Additional standards based on BS 1363 follow the same specifications for these plugs and sockets.
This chapter will explore the applications and advantages of AC power cords.
AC power cords are used in a variety of applications, including:
When dealing with materials that transfer electrical current, it's crucial to observe safety considerations. Polarization and grounding are especially important for higher-voltage electrical equipment and appliances, which may pose a greater risk of electric shock. Polarizing an electric plug ensures that the appliance is properly connected to the ground or neutral side of the circuit, reducing the risk of electric shock for users. Sensitive electrical products and equipment should always be used with properly grounded or polarized AC power cords.
AC power cords require minimal maintenance since they are passive devices with no moving parts. However, several practices can help extend their lifespan. Ensure that the power cord is used within the manufacturer's specified amperage to prevent overheating. In environments with numerous power cords, such as server rooms, they should be organized and tied to avoid entanglement. It's also important to use AC power cords in dry areas to prevent moisture from entering the connectors. Regular dusting of the power cords helps keep them clean and in good condition.
An AC power cord is a removable means of offering alternating current of electric energy from a mains power supply to an electrical appliance or equipment. Serving industries like retail, commercial, industrial, electronics, entertainment, and residential, AC power cords are utilized for applications such as lighting, electrical power tools, household appliances, shop equipment, musical instruments, and many personal uses. They offer a low resistance path for alternating current to flow through. Live wire carries the 230V/120V AC from the power supply to the appliance. The current alternates periodically at 50 times per second. The cord is a cable made of a conducting wire, generally copper, covered by cord covers, insulation, and an outer rubber or polymer jacket which protects the wire. AC power cords are differentiated by their connectors or more formally known as couplers. AC power connectors enable the connection between electronic devices and appliances to available power outlets. Besides connectors, plugs are also used. The choice of an AC power cord is determined by rated current and voltage.
Electrical plugs, commonly known as power plugs, are devices responsible for supplying and drawing current from a receptacle to the circuitry of an electrical appliance...
A NEMA connector is a method for connecting electronic devices to power outlets. They can carry alternating current (AC) or direct current (DC). AC current is the typical current found in homes, offices, stores, or businesses...
A power cord is an electrical component used for connecting appliances to an electrical utility or power supply. It is made from an insulated electrical cable with one or both ends molded with connectors...
Thomas Edison developed the power distribution system in 1882. He wrapped a copper rod in jute, a soft shiny fiber from plants, as an insulator. The jute wrapped copper rod was placed in a pipe with a bituminous compound...
Power supplies are electrical circuits and devices that are designed to convert mains power or electricity from any electric source to specific values of voltage and current for the target device...
An AC power supply is a type of power supply used to supply alternating current (AC) power to a load. The power input may be in an AC or DC form. The power supplied from wall outlets (mains supply) and...
A DC DC power supply (also known as DC DC Converter) is a kind of DC power supply that uses DC voltage as input instead of AC/DC power supplies that rely on AC mains supply voltage as an input...
A DC power supply is a type of power supply that gives direct current (DC) voltage to power a device. Because DC power supply is commonly used on an engineer‘s or technician‘s bench for a ton of power tests...
Electronic connectors are devices that join electronic circuits. They are used in assembling, installing, and supplying power to electrical devices. Connectors are an important component of every electronic equipment used in...
An electric switch is a device – usually electromechanical – that is used to open and close an electric circuit. This disables and enables the flow of electric current, respectively...
By definition a power supply is a device that is designed to supply electric power to an electrical load. An electrical load refers to an electrical device that uses up electric power. Such a device can be anything from...
A programmable power supply is a method for controlling output voltage using an analog or digitally controlled signal using a keypad or rotary switch from the front panel of the power supply...
Push button switches are electrical actuators that, when pressed, either close or open the electrical circuits to which they are attached. They are capable of controlling a wide range of electronic gadgets...