AC Power Cord
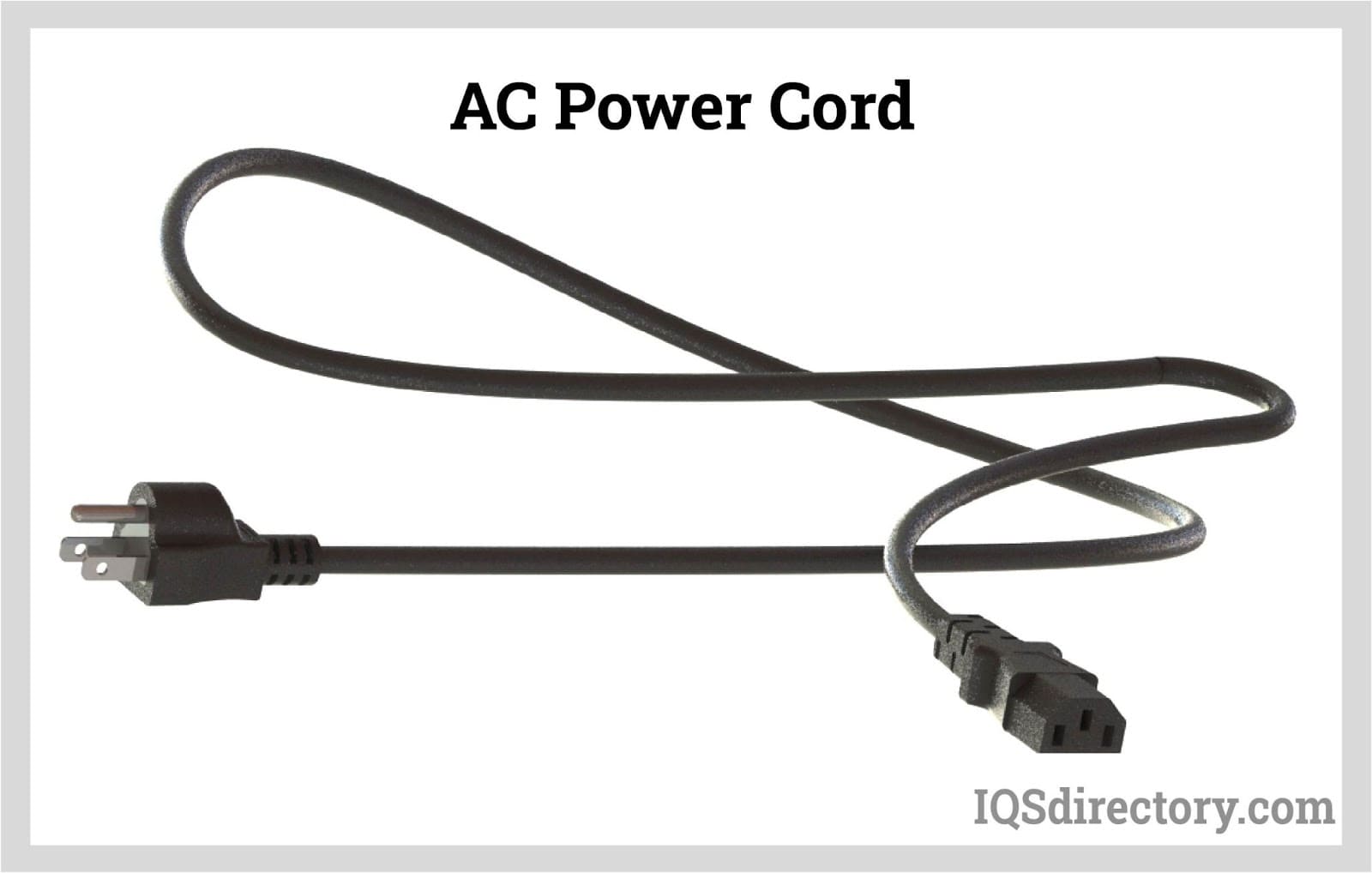
An AC power cord is a detachable way of providing an alternating current of electric energy from a mains power supply to an electrical appliance or equipment. Serving industries like...
Please fill out the following form to submit a Request for Quote to any of the following companies listed on
This Article takes an In-depth look at Power Cords
This article includes everything you need to know about power cords and their use.
You will learn:
A power cord, often referred to as a line cord or power cable, functions as a connection medium between electronic devices and their power sources, facilitating the transmission of electricity. Typically, they feature copper wires encased within an insulating material and covered by a non-conductive protective layer. These cords come with plugs that meet international standards, ensuring they are compatible with different regions around the globe. Power cords are generally categorized into two types: basic power cords, which have a plug at one end and bare wires at the other, and connector power cords, which include a connector at one end and wires at the opposite end.
The National Electrical Manufacturers Association (NEMA) establishes criteria for designing and producing electrical plugs, covering aspects like voltage ratings and socket designs. There are 15 different plug types existing globally, named from Type A to Type O. Various adapters are available from electrical suppliers to bridge the gap between these plug variations worldwide. In the United States, Types A and B are prevalently used.
Typically, power cords consist of three primary components: a plug, a socket, and the cord itself. Certain high-priority power cords are equipped with locking features to avoid accidental disconnections, which is of particular importance for medical equipment and heavy-duty applications.
Power cords are classified according to their voltage or kilovolt capacity, which indicates how much power they can convey. The rating of power cords depends on the wires, plugs, and connectors. The lowest rated component of the three determines the overall rating of the cord set. The plug also plays an important role, as it specifies where the cord set is intended for use and its manufacturing origin.
The ability of a power cord to carry an electrical load relies on the wire gauge and the length of the cord. The thickness or diameter of the wire affects its capacity for carrying current and the extent to which it heats. Moreover, the length of the cord impacts voltage drop—a reduction in voltage that happens from the connector to the cord's end.
The gauge rating is a basic number assigned by the American Wire Gauge (AWG) standard numbering system. For example, a 12 AWG is a 120-volt cord with a 12-gauge wire suitable for connecting to 120-volt outlets. In the AWG system, a lower number signifies a thicker wire.
As the length of a power cord extends, the voltage drop similarly increases due to power loss from the connector to the cable's far end. Shorter cords maintain stable power levels from the outlet to their endpoint. However, for very lengthy power cords, especially those extending beyond 50 feet, higher-rated American Wire Gauge (AWG) wires are necessary to manage increased resistance, alleviating significant voltage drop.
In 1882, Thomas Edison devised the power distribution system by insulating a copper rod with jute, a soft, shiny plant fiber. This jute-wrapped copper rod was then inserted into a pipe lined with a bituminous compound, contributing to his project of electrifying New York City.
Although vulcanized rubber emerged in 1844, its application in electrical wiring did not occur until 1880. Rubber-coated cords were standard until the 1930s when metal-sheathed cable, known as armored cable, gained popularity due to its durability, though it was costly and used until the 1950s. It was eventually replaced by two-wire PVC insulated cables.
Today, PVC-coated cords dominate the market thanks to their ability to withstand high temperatures and endure tough use. It has proven to be an effective and robust solution for manufacturing power cords.
Understanding the various types of power cords is essential for anyone working with electrical systems, electronics, or any device that requires a safe and reliable connection to an electrical outlet. Unlike other equipment categories, power cords cannot be universally classified by a single standard across different regions. Instead, their variations are determined by country-specific electrical codes and infrastructure. Global differences in electrical outlets, voltages, frequencies, and plug shapes mean that power cord compatibility is a critical aspect of selecting the right product for both industrial and residential use. Proper knowledge of power cord types assists businesses, frequent travelers, and equipment manufacturers in choosing cords that meet international compliance and safety standards.
Anyone traveling internationally with devices like laptops, smartphones, gaming systems, or tablets quickly becomes aware of the differences in power cord and plug types, as each country has its own standards for plugs and power supplies. There are 14 distinct plug types used globally, designated as Type A through Type N. The standards for these electrical plugs and connectors have been set by organizations such as the International Electrotechnical Commission (IEC), the National Electrical Manufacturers Association (NEMA), and the International Commission on Rules for the Approval of Electrical Equipment (CEE). These regulatory bodies define specifications for a variety of male and female connectors, voltage ratings, safety features, and design requirements, ensuring safety and compatibility across different power environments. Understanding these global standards is critical for selecting the appropriate power cord for international travel, industrial use, data centers, or specialized electronic equipment.
AC power cords are the most common type of electric cable used to supply alternating current from main power sources to electrical equipment or appliances. Designed to handle standard voltages, AC power cords are essential in a wide range of applications—spanning electrical power tools, lighting systems, HVAC equipment, computing devices, consumer electronics, kitchen appliances, musical instruments, and shop equipment.
AC power cords are composed of several key components: a cable assembly containing internal wires made of copper or aluminum, insulation sheathing from high-grade polymers or rubber, and molded plugs featuring prongs, casings, wire terminals, and sometimes fuses or other safety elements. Voltage and current ratings, wire gauge, wire shape (flat or round), cord length, sheathing material, and plug type are standardized for specific usage scenarios. The connector interfaces with the powered device, while the plug connects to the wall outlet or power distribution unit (PDU) in industrial or data center environments.
As electrical systems around the world operate at different voltages (often 100V, 110V, 120V, 220V, or 240V) and frequencies (50Hz or 60Hz), power cords must be precisely matched to local standards. AC power cord plugs are categorized using an international type-system from Type A to Type O, with numerous sub-variations for country-specific standards. For those sourcing power cords for global operations, understanding these distinctions is critical to avoid equipment failure or safety hazards.
Modern AC power cords incorporate grounding and polarization features for enhanced safety. Grounded cords lower the risk of electric shock and are essential for powering high-wattage devices. Polarization ensures a secure connection to the circuit’s neutral, grounded side. Safety certifications, such as UL, CSA, VDE, or CE, are often required and should be verified when purchasing cords for sensitive computing equipment, laboratory devices, or healthcare machinery.
NEMA power cords define the standard for North American electrical plugs, power cord voltage capacities, and receptacle configurations. The most recognized NEMA plugs—Type A (2-prong) and Type B (3-prong with ground)—are present in homes and businesses throughout the U.S., Canada, and Mexico. While NEMA Type A plugs have largely been replaced by the more grounded Type B, variations persist throughout the world, and many devices still support both configurations for backward compatibility. Other international standards, such as IEC C13 and C19 connectors, feature heavily in IT and data center installations.
Devices built to meet NEMA codes are generally designed as either one-wire or two-wire systems, depending on whether they incorporate a ground (for increased safety and surge protection). When selecting electrical components, consider key factors like the intended application (industrial equipment, portable tools, household use), plug/connector configuration, anticipated energy load (measured in amperes and watts), and specific requirements for power delivery. Note that NEMA standards only apply in North America; international travelers require plug adapters and may need voltage converters for compatibility abroad.
NEMA connectors are further divided into two categories: straight blade and locking. Straight blade connectors, commonly found in consumer electronics and appliances, utilize metal prongs or blades (flat or folded), with a rounded ground pin for added safety. Locking connectors, used in commercial and industrial facilities, feature curved blades and twist-locking technology that keeps the plug securely fastened, preventing unintentional power interruptions. This is especially important in critical industrial environments and for heavy-duty extension cords.
NEMA non-locking and straight connectors are categorized into 25 distinct subtypes, while locking connectors include 24 subtypes. Each subtype is identified by a unique specification code (such as NEMA 5-15P, NEMA L14-30P) that clearly distinguishes between power capacities, grounding features, and intended usage—making it easier for facility managers and procurement professionals to source the proper replacement cords or components.
NEMA power cord products are available in ranges from 15 to 60 amperes and 125 to 600 volts. Each product type is distinguished by a specific classification. For example, NEMA 1 power cords have a two-prong design for non-grounded connections, while NEMA 5 power cords feature a three-prong configuration for grounded use. NEMA 5 cords, widely used for residential and office electrical outlets, are rated for a maximum voltage of 125 volts. The NEMA 5-15 rating identifies a grounded version of the NEMA 1-15 device, making it one of the most prevalent choices for powering computers, small kitchen appliances, and portable electronics. Higher NEMA classifications, such as NEMA 6 and above, are often used in heavy-duty industrial machinery, air conditioning systems, or large household appliances requiring greater current and voltage ratings.
While all NEMA 5 15P power cords have three prongs, some are designed with specialized ends. For example, low-profile right-angle plugs are available for use behind furniture, allowing the cord head to turn sideways and sit flush to the wall without bending. Others have a traditional straight plug for direct insertion. Some NEMA power cords are equipped with multiple outlets or built-in surge protectors, allowing users to extend a single power source to multiple devices (e.g., via a power strip) and provide protection for sensitive electronics.
To maintain safety and compliance, always match the NEMA power cord's amperage, voltage, and plug type to the corresponding outlet and device requirements. Manufacturers often display the correct NEMA code on both the cord and plug for ease of identification.
Generator power cords are specially designed to transfer power from portable or standby generators to home backup systems, RVs, job site tools, or emergency equipment. These cords are available in a diverse range of amp ratings (typically 15 to 50 amps), voltage compatibility (120V or 240V), wire gauges, and connector types. The most common types of generator plugs include NEMA 5, L5, L14, 14, TT, and CS series, which are directly related to generator receptacle labels. For example, L14-30P describes a twist-lock, 30-amp plug, essential for secure generator connections where accidental disconnection is a safety concern.
When choosing a generator power cord, it is crucial to know the generator’s wattage output, the amperage requirements of the connected appliances or tools, and distance required for deployment. Higher amp generator cords are built with heavier, thicker insulation to safely handle more electrical current, resulting in improved performance and reduced overheating risk. Generator cords must also match the generator’s outlet type, plug configuration, and required voltage. For extended reach, always select the appropriate cord gauge (wire thickness) to prevent voltage drop and loss of power efficiency—long or undersized cords may limit the amount of electricity delivered to the devices in use.
Generator power cords come with a variety of plug types: 3-prong plugs are suitable for 120-volt systems, while 4-prong plugs are designed to support both 120V and 240V applications. With the prevalence of 240V receptacles in many homes and workplaces, 4-prong generator cords are often preferred for connecting high-demand appliances such as air conditioners, sump pumps, or heavy construction equipment. Always use cords rated with higher wattage than your intended load and ensure proper safety certifications from the manufacturer for reliable and secure power distribution.
Additionally, for users investing in backup power solutions or portable generators, check for weather-resistant and outdoor-rated generator cords equipped with locking mechanisms and ergonomic handles for easy, safe operation in challenging environments.
Generator Power Cords Based on Power Requirements | ||||||
---|---|---|---|---|---|---|
Device Requirements | Wire Gauge by Length (ft.) | |||||
AMPS | Watts (120/240V) | 10 | 25 | 50 | 100 | 150 |
5 | 600/1200 | 18 | 16 | 14 | 14 | 14 |
10 | 1200/2400 | 16 | 16 | 14 | 14 | 12 |
15 | 1800/3600 | 14 | 14 | 12 | 12 | 10 |
20 | 2400/4800 | 14 | 12 | 12 | 12 | 10 |
25 | 3000/6000 | 12 | 12 | 10 | 10 | 8 |
30 | 3600/7200 | 12 | 10 | 10 | 10 | 8 |
40 | 4800/9600 | 10 | 8 | 8 | NR | NR |
50 | 6000/12000 | 8 | 6 | 6 | NR | NR |
*NR = Not Recommended |
A power supply cord, also referred to as an electric cord or electrical cable, serves as the critical connector between an electrically powered piece of equipment and the main electricity supply. Power supply cords are integral to lighting and sound equipment, power tools, small and large household appliances, servers, medical devices, and laboratory instruments. Made from copper or aluminum wire protected by rubber or high-durability polymers, power supply cords may be either detachable for convenience or permanently attached for increased safety in fixed installations.
Power supply cords are manufactured as flat or rounded cables, with optional coiled or retractable designs for portability and space-saving storage—an important feature in workplaces where cable management is a priority. Cord lengths vary by application, with short cords ideal for close-quarters installations and longer cords used for flexible placement. For every application, the correct cord length and thickness (gauge) are vital to maintaining optimal electrical performance, minimizing voltage drop, and ensuring user safety.
The amperage rating of a power supply cord is a crucial metric, typically ranging between 18 and 10 gauge, with 14 gauge being most popular for general use. The cord’s gauge and insulation determine the maximum current it can carry without overheating or causing energy loss. Voltage ratings are based on the local power grid; in North America, typical supply voltages are 110V or 120V, while many other countries use 220V to 240V. Selecting a power cord with appropriate certifications (such as UL, CSA, or VDE) and matching its technical specifications to the device and outlet is key for safety and compliance in regulated industries or international settings.
For consumers and businesses purchasing replacement power supply cords, be sure to confirm compatibility with device connectors, verify proper voltage and amperage support, and check for safety features such as surge suppression, fuse protection, or weather-resistant insulation for outdoor applications.
Cord sets are pre-assembled units designed to safely conduct electricity between a wall outlet and an appliance or device. They consist of a conductor (usually copper wire), robust insulation, and a protective outer jacket. Some cord sets also incorporate electrical fuses to prevent voltage surges, a current leak detection component, or features for monitoring electrical voltage and current—vital functionalities for laboratories, hospitals, and highly sensitive industrial environments. For advanced applications, cord sets may be shielded to minimize electromagnetic interference (EMI), which can impact the performance of electronics and communications equipment.
The design of cord sets includes a molded plug and a country-appropriate molded connector. These products serve as a critical interface, directly linking the main power supply to appliances or production processes. An essential consideration for cord sets is ensuring compatibility with the target country's plug and outlet configurations—failure to do so may result in improper fit, inefficient power delivery, or complete device incompatibility. Always verify the amperage and voltage ratings to guarantee safe and efficient power transfer and long service life of the connected device.
Cord sets are utilized in virtually every environment—from retail stores and office buildings to industrial facilities, laboratories, and residential homes. Most cord sets are used for AC power applications. Extension cords, a type of long cord set, enable the delivery of electricity over longer distances where outlets are not immediately available, and are invaluable for temporary setups, events, and job sites.
The National Electrical Manufacturers Association (NEMA) provides strict manufacturing and quality guidelines for cord sets, plugs, voltage ratings, and receptacle designs in the United States and Canada. Equivalent standards exist globally (such as IEC and CEE), and users should verify the relevant marks when selecting cord sets for use in international or high-regulation sectors. Proper measurement of cord length—taking into account both reach and voltage drop—is necessary for all cord set purchases, ensuring the right fit for application needs while maintaining safety and compliance.
When selecting custom power cords, it is important to fully assess the technical requirements, physical environment, and regulatory considerations of your application before consulting a custom power cord manufacturer. Custom power cords are tailored to meet the exact needs of unique processes, specialized machinery, or challenging environments—often diverging from standardized NEMA or IEC plugs in favor of bespoke connectors, cable assemblies, or enhanced safety features. High-performance custom cords routinely incorporate thicker wire gauges for power-intensive equipment, ruggedized insulation for construction or outdoor use, heavy-duty grounding pins for industrial safety, and weatherproof or water-resistant plugs for wet environments.
Custom power cord manufacturers offer a variety of safety and identification enhancements. Brightly colored insulation increases visibility and reduces tripping hazards, making it easier to identify and manage cords in busy environments. Integrated surge protection is another popular option, protecting valuable equipment from damaging voltage spikes and short circuits. Industry-specific customizations—such as locking mechanisms for healthcare or laboratory cords, oil-resistant jackets for manufacturing plants, or coiled designs for space-sensitive applications—further ensure that the power cord precisely matches user requirements.
Whether you are sourcing cords for a complex production line, specialized test chambers, marine or aviation equipment, or consumer electronics, working closely with a reputable manufacturer ensures regulatory compliance and optimal long-term performance. Comprehensive design consultations guarantee that factors like length, amperage, flexibility, durability, and the number/type of connectors are tailored to your exact needs. This engineered approach increases efficiency, safety, and the life span of both the power cord and the powered equipment.
Any piece of electrical equipment—whether an industrial machine, household appliance, office computer, or medical device—relies on an electric cord for reliable and safe power transfer from a wall socket or PDU. Power cords may be flexible for easy handling or semi-rigid for improved durability in demanding environments such as factories or workshops. To ensure an effective and secure transfer of electrical energy, it is critical that the connection between the plug and the receptacle—the point where the cord meets the outlet—is engineered for a tight, stable fit and built with materials that prevent heat build-up or corrosion over time.
Electrical receptacles—also referred to as female connectors—are typically produced from robust materials such as nickel, silver, galvanized steel, or high-temperature plastic for enhanced safety. Standard receptacles in North America are commonly rated for 120-volt systems, but higher voltage designs (240V and above) are available for industrial or commercial equipment. Most power cords include a ground pin and polarization features for added safety and compliance with modern building codes. Grounding helps protect users from accidental electric shocks, while polarized plugs ensure the line and neutral conductors are correctly inserted to prevent miswiring.
Non-detachable (or permanently attached) power cords are hardwired directly into specific equipment, secured using double-crimped lugs or ring terminals. These cords are commonly found in large appliances, industrial machinery, and specialized electrical systems where user removal is not intended. Detachable power cords—also called line cords—are more common in consumer electronics, computer equipment, and portable tools. They feature molded plugs and connectors (male and female), and are designed for easy replacement or swapping between appliances with matching inlets (such as IEC C13 or C15 connectors widely used for computers, monitors, and server racks).
When selecting an electric power cord for your device, always verify the voltage and amp ratings, connector types, and local regulatory certifications. For industrial users, additional considerations include environmental resistance (oil, moisture, heat), cable flexibility, and electromagnetic shielding.
NEMA power cords are essential cables equipped with standardized plugs and connectors for alternating current (AC) power transmission, as defined by the National Electrical Manufacturers Association (NEMA). Established in 1926, NEMA set out to unify the electrical industry's approach to safety, reliability, and energy efficiency by creating consistent standards for electrical devices. NEMA standards ensure compatibility and interoperability for power cords and outlets across the United States and Canada, supporting both residential and commercial electrical systems.
NEMA connectors are primarily divided into two categories: straight blade, non-locking connectors and locking (twist-lock) connectors with curved blades. Straight blade NEMA connectors, also known as non-locking power cord plugs, feature a neutral wire, a hot wire, and a grounding pin or wire. These plugs are directly compatible with standard wall outlets, making them ubiquitous in household and office settings. Common current ratings range from 15 amps to 60 amps, with voltage support spanning 125 V to 600 V. These connectors, typically seen in residential power delivery, offer simplicity and ease of use.
Locking NEMA connectors, easily identified by their curved blades and twist-lock mechanism, provide enhanced security in power connections. By twisting the plug after insertion, these connectors lock into place, preventing accidental disconnections or power loss due to vibrations or movement. The locking feature is especially valuable in industrial, medical, and commercial environments such as data centers, server racks, heavy machinery networks, and critical facility power strips, where consistent and stable connectivity is vital. Locking connectors include a neutral conductor, hot conductor(s), and ground, supporting a wide range of voltages and amperages.
There are 25 types of straight blade, non-locking NEMA plugs and receptacles, categorized numerically from NEMA 1 to NEMA 24, including the travel trailer connector, NEMA TT-30. NEMA 2 and NEMA 10, previously common, have been phased out and replaced by updated, safer types. Among these, NEMA 1, NEMA 5, NEMA 6, and NEMA 14 are the most widely used for different voltage requirements and devices. NEMA 1, the most basic power plug, is characterized by two flat, parallel blades and no grounding pin.
NEMA 1 plugs and receptacles, with ratings of 125 V and typically 15 amps, were once standard in residential and light commercial applications. Over time, the industry has shifted toward grounded configurations (such as NEMA 5-15) for improved electrical safety and reduced risk of electrical shock or fire hazards, aligning with modern building and safety codes.
Locking NEMA connectors are assigned designations from NEMA L1 to NEMA L23 and are further divided based on their wiring configurations: two-pole ungrounded, two-pole grounded, and three-pole ungrounded. Primary voltage ratings include 125 V, 250 V, and specific higher-voltage variants for industrial power distribution. Midget locking plugs, marked with "ML" in their nomenclature, are designed for compact, dedicated applications. The letter "L" in the NEMA code clearly distinguishes these twist-lock connectors from straight blade types. Frequently used locking connectors include NEMA L5 (commonly used for 125 V power distribution), NEMA L6 (preferred for 250 V circuits), NEMA L14 (widely adopted for 120/240 V split phase), and other variants such as NEMA L7, L15, L21, and L22, each optimized for distinct electrical environments, generator hookups, and heavy-duty appliances.
To facilitate universal understanding and application of electrical connectors, the National Electrical Manufacturers Association (NEMA) introduced a robust plug and receptacle identification system. This standardized naming convention employs a set of numbers to define the essential characteristics of each connector. The first number specifies the plug series—including voltage rating, number of poles, and number of wires—while the second number, separated by a dash, indicates the amperage rating, such as 15 amps, 20 amps, 30 amps, 50 amps, or 60 amps. For instance, the popular NEMA 5-15 represents a grounded, two-pole, three-wire configuration used for general-purpose 125 V power outlets throughout North America.
Additional designations can further specify connector functionality. The inclusion of the letter "L" prior to the code, as in NEMA L5-30P, highlights a locking plug with two poles, two wires, a hardware lock for secure connection, a 125 V voltage rating, and a 30 amp current capacity—a common choice in network and industrial settings where uninterrupted power is essential for server racks or heavy-duty tools.
Although NEMA rules form the basis for most American electrical connections, non-NEMA (or international) plugs—such as IEC, CEE, or custom industrial connectors—are still encountered in certain applications. These alternatives are typically engineered for unique equipment requirements or imported electronics, and their quality can vary in terms of blade material, durability, and electrical grounding compliance. For critical or demanding power applications, it’s recommended to use NEMA-compliant cords to guarantee maximum safety, compatibility, and performance with code-compliant electrical systems.
Choosing the Right NEMA Power Cord: Selecting the optimal NEMA power cord involves evaluating the specific voltage, current rating, plug type, equipment compatibility, and intended usage environment—whether for residential electronics, industrial machinery, or data center power distribution. For sensitive electronics, server racks, or medical devices, always ensure the cord you select meets the latest NEMA and UL safety certifications. If you need guidance for a particular application, consult an experienced electrical supplier or licensed electrician to avoid hazards and ensure code compliance. This critical step not only enhances safety but also extends the life span of both the power cord and the attached equipment.
Understanding NEMA connector types and their various applications empowers users to make informed decisions when buying, installing, or maintaining electrical systems. With the increased adoption of NEMA standards by manufacturers and regulatory bodies, high-quality NEMA power cords remain fundamental to safe, reliable, and efficient power distribution in homes, businesses, and industrial settings. For more detailed specifications, technical resources, or purchasing options, reference the full NEMA standards documentation or consult supplier product guides online.
Extension cords supply power to equipment and are used in locations that do not have a convenient power source such as construction sites, emergency medical defibrillators, and power tools. They have a long cable that has a power plug at one end and receptacles at the other end and can be used as power adapters or “adapter cords”. Available in countless numbers of designs and options, extension cords are the best accommodation for a room that does not have a sufficient number of power boards.
When selecting an extension cord, flexibility is a crucial factor, as they vary in size, gauge, construction, and intended use. Unlike permanently installed power supplies, extension cords are meant for temporary use, although they are built to be rugged and durable. Extension cords are categorized into light duty, medium duty, and heavy duty types.
Similar to NEMA codes, extension cords use a letter coding system to specify their usage capabilities. This system includes six letters—S, W, J, T, P, O, and E—each with various subcategories. For example, the code SJOOW represents a heavy-duty, portable service extension cord suitable for both indoor and outdoor use. It features synthetic rubber insulation and a neoprene rubber jacket for added durability.
Portable Extension Cord Letter Meanings | ||
---|---|---|
Letter | Meaning | Explanation |
S | Service | Severe heavy duty Service. These cords are portable cords that have a voltage rating of 600V (also 277/480 or 480) and can be used in place of SJ or SV in extra-severe service where abrasion resistance is needed. |
J | Junior Service | These service cords have a rating of 300V (also 120 or 120/208 or 120/240 or 240 or 277, but not 277/480). Examples include SJ SJO, SJOW, and SJT. |
T | Tinsel Cord | Only applicable if it is the first letter of the code for a portable cord. Example: TTXOW. |
T | Thermoplastic (if not the first letter of code) | This refers to the material the cord jacket is made out of. Thermoplastic material is light-duty and can be used as a consumer-grade portable cord. Examples include SJT, SPT, and SVT |
E | Elastomer | Short for Thermoplastic Elastomer, a flexible thermoplastic that looks and feels like rubber. This refers to the material the cord jacket is made out of. Thermoplastic elastomer material is medium-duty and performs better in colder temperatures than thermoplastic. (If a portable cord does not have a 'T' or an 'E', it is made of thermoset material, which makes it heavy-duty.) Examples include SEO/SEOW and SJEOOW. |
N | Nylon | Outer jacket material. |
O | Oil-Resistant Outer Jacket | Examples include SEO, SO STO, and SVO. |
OO | Both the Outer Jacket and the Insulation are Oil Resistant | Examples include SJOOW and SOOW. |
F | Fixture Wire | These cables are rated to 90°C. Examples include H07RN-F. |
P | Parallel | This cable is parallel-jacketed, meaning the conductors are not twisted around each other. Sometimes called "zip cord." Examples include SPT. |
H | Heat Resistant | Referred to as heater cord. This is used in UL cord types like HSJ, HS, HSO, and HSJO. |
HH | High Heat Resistant | |
V | Vacuum Cord | This is a light-duty portable cord, rated at 300 volts. Typically used with vacuum cleaners and other portable cleaning equipment. "V" is the UL marking in parts like SVT and SVO. |
RD | Range or Dryer Cord | Product examples include SRD, SRDE, and SRDT cord. |
W-A | Weather Resistant | UL approved for indoor and outdoor use. Examples include SEOO-WA and SJTO-WA. |
W | Weather and Water Resistant | A portable cord with a W means it's approved as weather (sunlight, moisture, etc.) and water-resistant and can be used indoors or outdoors. Examples include SEOW and SJOOW. |
Power cord splitters, also referred to as cord splitters or power cable splitters, enable the use of a single outlet to power multiple devices. They split a single power source into several outlets, increasing the number of available electrical connections. These splitters come in various configurations, including three-way, four-way, and more complex designs.
Although power splitters may be assumed to be a version of extension cords, they have a very striking difference. Splitters are designed to provide power to devices that are in close proximity to the power supply, which is unlike extension cords that provide power at a distance from the power supply. Power cord splitters are used in relation to the power load they are able to handle and are a safe solution for multiple power distributions.
A power cord splitter enables the connection of two or more devices to a single outlet. Commonly used in home entertainment setups, computer systems, workshops, and office environments, these splitters are available in 10 or 15 amps and can handle voltages of 125 V or 250 V. They come in various wire gauges, including 12, 14, 16, or 18, with heavier gauges designed for more demanding applications.
Electrical receptacles are crafted from various insulating materials, including nickel, silver, galvanized steel, or plastic. These receptacles serve as the entry points for plugging in devices to access electrical current. Most standard receptacles operate on a 120-volt system, while higher voltage receptacles, such as those rated for 240 volts, are used for heavy-duty equipment like industrial machinery. All receptacles must be properly grounded. For scenarios where multiple devices need to be connected, cord splitters facilitate the use of a single receptacle for several devices, with options available to accommodate different wire sizes and voltage levels.
Specifications for electric cords include factors such as cable temperature, jacket materials, wire configuration, wire size, cord length, current rating, voltage rating, and the types of plugs and receptacles used. In North America, the National Electrical Manufacturers Association (NEMA) sets the standards for these configurations and voltage capacities.
The NEMA system, as well as other international sets of standards, assist in maintaining consistency in fabricating electric cords to minimize the risk of malfunctions. Polarizing, or grounding, reduces the risk of electric shock or electrocution, which allows the plug to be inserted in only one direction to the socket ensuring the connected circuit is neutral, or grounded.
Electrical plugs vary globally, as do the types of outlets or receptacles. While the three-prong grounded version is commonly used, some regions still use two-prong designs. Many of these designs allow the plug to be inserted only in one direction, with prongs positioned at an angle.
Electrical receptacles can pose risks such as electric shocks, power surges, or fires. Self-testing receptacles provide protection by conducting automatic tests on the device every second to detect potential hazards.
Self-testing receptacles are equipped with features to prevent overloads or short circuits. They alert users to the need for a Ground Fault Circuit Interrupter (GFCI) replacement with a flashing light when a fault is detected. These receptacles also include a ground terminal back wire clamp, an auto ground clip, and two back wire holes per termination to offer flexibility and save space within the electrical box.
Most electrical receptacles operate on alternating current and include live (or phase), neutral, and ground components. They are constructed from insulating materials like nickel, silver, plastic, and galvanized steel, typically featuring three slots to accommodate two prongs and a grounding prong.
Electrical receptacles in the United States use a standard 120-volt system. Heavy-duty, 240-volt receptacles are designed for equipment with higher voltage such as electric ranges or industrial machinery. Aside from standard grounding or polarization, other safety features for receptacles include tamper and corrosion resistance for uses in harsh or hazardous conditions.
Plug adapters are designed to enable plugs from various devices to fit into different types of outlets. They typically allow three-prong plugs to be used with older two-prong outlets by bypassing the grounding pin. However, plug adapters are not a long-term solution and should be used cautiously. They are generally suitable for locations with a metal breaker box and an established grounding system.
Plug adapters, or plug converters, allow electrical devices to connect to sockets and plugs that are incompatible, which is determined by the configuration of the electrical receptacle where the prongs of the plug do not match the holes of the receptacle. Aside from making it possible for unlike plugs to connect, a plug adapter can also step voltage up or down to even out electrical differences. Voltage adapter converters are necessary for higher or lower voltage systems where electrical equipment will overload a device or not provide enough power.
In the United States, plug adapters commonly accommodate two-prong receptacles that lack a grounding pin. These adapters are particularly crucial for international travel, as different countries use various types of outlets and voltage levels not compatible with those in the U.S.
Plug adapters generally feature a socket and a plug. The socket is designed to connect with the electrical device, while the plug aligns with the configuration of the power source, typically a wall outlet. Universal plug adapters are equipped with a socket that can fit plug types from nearly any country, though they typically do not cover South Africa.
The most prevalent plug types include Type A, which has two prongs for conducting, one for live and one for neutral connections, and Type B, which adds a third prong for grounding, enhancing safety against electrical shock. Both plug types feature a plastic casing, known as a "jack," that separates the two prongs and connects them to the cord through the plug body.
Electricity flows through the blades, the blade-cord connection, and the power supply cord. Safety standards for electrical plugs were established in 1962 requiring all plugs to be three pronged grounded plugs forcing the plug to be connected to a socket in only one direction.
Globally, there are 15 distinct plug types, ranging from Type A to Type O. Type A, which features two prongs, is largely obsolete. Since 1962, Type B, which includes a grounding prong, has been the standard in the United States, Canada, and Mexico. Other types, from C to O, are used across various regions worldwide, with Type C commonly found in Europe, South America, and Asia.
Outlet plug covers are safety additions that help prevent accidents and injuries from electrical shock. They protect outlets from environmental hazards and temperature changes. Plug covers allow electrical cords to be plugged and unplugged while blocking access to the receptacle when it is not in use.
For harsh or corrosive environments, specialized plug outlet covers are essential. These covers are designed for durability and resistance to extreme conditions. While dummy covers can provide some protection, a full switch cover with a closing door offers more robust security. These covers are typically made from durable plastics to withstand tough environments.
In addition to outlet covers, various accessories such as cord grips, dust shields, and tamper-resistant covers are also used. For the most demanding and hazardous environments, industrial-grade grounding systems are employed to ensure safety and reliability.
An AC power cord is a detachable way of providing an alternating current of electric energy from a mains power supply to an electrical appliance or equipment. Serving industries like...
Electrical plugs, commonly known as power plugs, are devices responsible for supplying and drawing current from a receptacle to the circuitry of an electrical appliance...
A NEMA connector is a method for connecting electronic devices to power outlets. They can carry alternating current (AC) or direct current (DC). AC current is the typical current found in homes, offices, stores, or businesses...
A power cord is an electrical component used for connecting appliances to an electrical utility or power supply. It is made from an insulated electrical cable with one or both ends molded with connectors...
Power supplies are electrical circuits and devices that are designed to convert mains power or electricity from any electric source to specific values of voltage and current for the target device...
An AC power supply is a type of power supply used to supply alternating current (AC) power to a load. The power input may be in an AC or DC form. The power supplied from wall outlets (mains supply) and...
A DC DC power supply (also known as DC DC Converter) is a kind of DC power supply that uses DC voltage as input instead of AC/DC power supplies that rely on AC mains supply voltage as an input...
A DC power supply is a type of power supply that gives direct current (DC) voltage to power a device. Because DC power supply is commonly used on an engineer‘s or technician‘s bench for a ton of power tests...
Electronic connectors are devices that join electronic circuits. They are used in assembling, installing, and supplying power to electrical devices. Connectors are an important component of every electronic equipment used in...
An electric switch is a device – usually electromechanical – that is used to open and close an electric circuit. This disables and enables the flow of electric current, respectively...
By definition a power supply is a device that is designed to supply electric power to an electrical load. An electrical load refers to an electrical device that uses up electric power. Such a device can be anything from...
A programmable power supply is a method for controlling output voltage using an analog or digitally controlled signal using a keypad or rotary switch from the front panel of the power supply...
Push button switches are electrical actuators that, when pressed, either close or open the electrical circuits to which they are attached. They are capable of controlling a wide range of electronic gadgets...