AC DC Power Supply
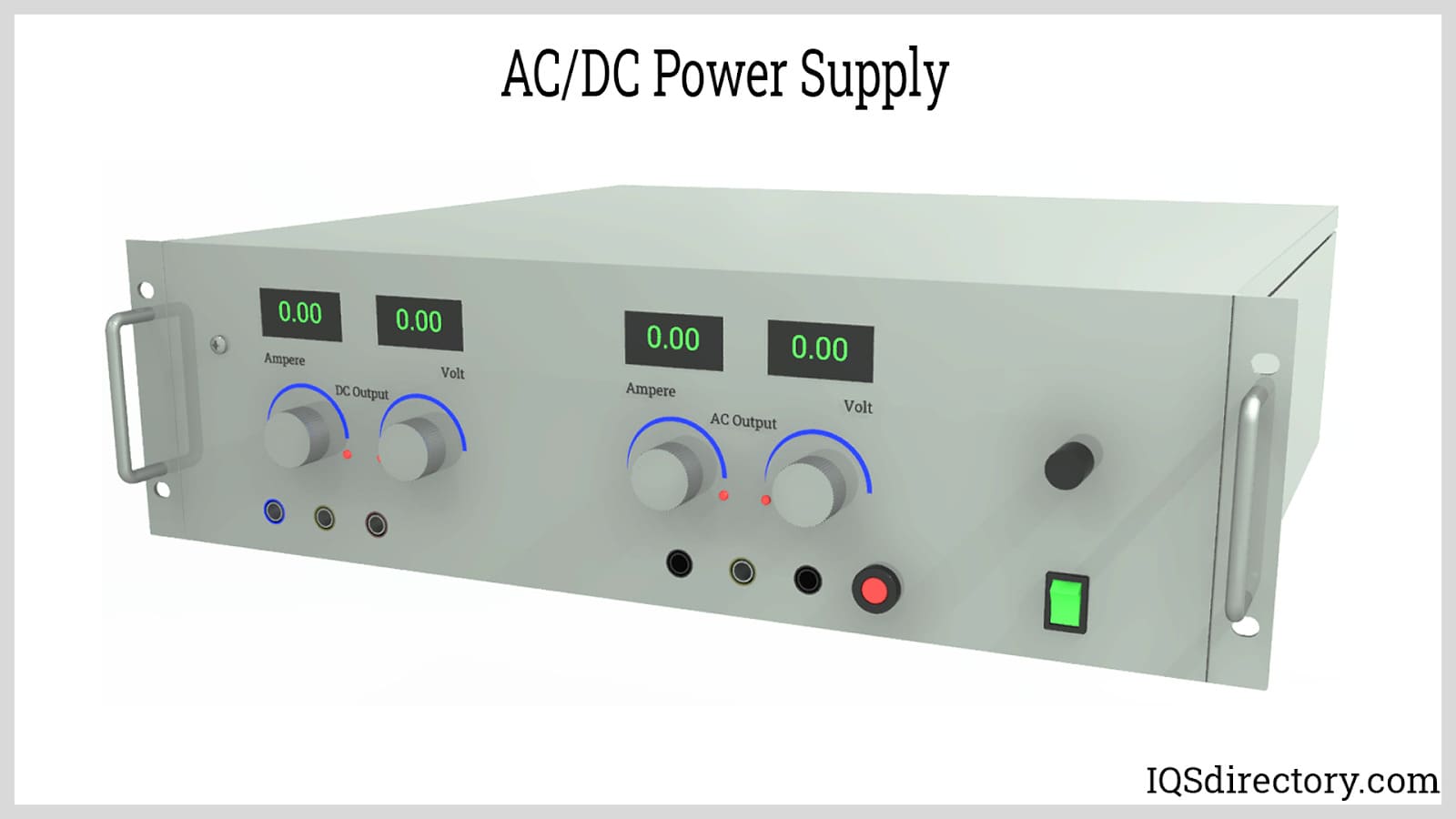
Power supplies are electrical circuits and devices that are designed to convert mains power or electricity from any electric source to specific values of voltage and current for the target device...
Please fill out the following form to submit a Request for Quote to any of the following companies listed on
This article contains everything you need to know about programmable power supplies and their use.
You will learn:
A programmable power supply enables precise control of output voltage using an analog or digital signal, which can be adjusted via a keypad or rotary switch on the device's front panel. These power supplies manage output voltage, current, and for an AC power supply, frequency control. Key components include a processor, voltage and current programming circuits, a current shunt, and a readback circuit for feedback.
Equipped with diverse functionalities, programmable power supplies offer protection against overvoltage, overcurrent, and short circuits, in addition to thermal management. They are available in multiple configurations: modular, bench-top, floor-standing, and rack-mounted. These devices often utilize Standard Commands for Programmable Instruments (SCPI) for programming purposes, though some units may operate on manufacturer-specific proprietary languages.
Utilizing a programmable power supply enables the precise delivery of electrical power tailored to specific requirements such as desired voltage, current, and frequency, making it an essential tool for laboratory testing, electronics manufacturing, and automated testing environments. Unlike conventional power supply solutions, which may not always meet the exacting standards required by sensitive electronic equipment and prototypes, programmable power supplies offer advanced versatility, flexibility, and remote control options. This adaptability is especially valuable when developing or testing equipment under development (EUD), providing enhanced power management, reliability, and traceability in experimental and production settings.
Programmable power supplies deliver stable, adjustable voltage and current with clean output signals and safeguard against power grid fluctuations or electrical noise. This precise regulation and monitoring capability is a cornerstone of circuit design, prototyping, and device validation. They offer real-time measurement of both input and output parameters for connected devices, supplying critical feedback for efficient troubleshooting, calibration, and product optimization. Advanced programmable power supplies often feature integrated remote sensing, data logging, overcurrent protection, and automated sequencing to simulate real-world power conditions and rigorously test electrical components and systems. Such features are indispensable in industries prioritizing quality assurance, safety compliance, and regulatory standards.
With a programmable power supply, users can adjust voltage and current parameters with high accuracy through various user interfaces, such as numeric keypads, rotary encoders, computer software interfaces, or even via remote programming using SCPI commands and communication protocols like USB, GPIB, or LAN. The device’s built-in display or digital readout provides real-time feedback on voltage, current, power settings, and operational status, allowing for comprehensive monitoring and fine-grained control. This ensures optimal performance, efficient workflow integration, and safer operation for both manual and automatic test sequences.
Automatic Test Equipment (ATE) is highly effective for gathering diagnostic data and is indispensable in testing electronics across a range of technology-driven sectors such as defense, aerospace, consumer electronics, automotive, medical devices, and industrial automation. It ensures end-users receive equipment that is fully functional, reliable, and compliant with quality standards while protecting operators from hazardous electrical currents and faults.
ATE systems utilize advanced computerized control and automated test scripts to assess the performance, functionality, and quality of electronic devices. They also simulate extreme operating conditions to measure the resilience and endurance of a device under various environmental or electrical stress factors. ATE systems are designed for minimal human intervention, increasing efficiency and reducing human error; their automated workflow evaluates devices, often known as Device Under Test (DUT), Unit Under Test (UUT), or Equipment Under Test (EUT).
An essential element in ATE effectiveness is the integration of a programmable power supply, providing precise, programmable control and real-time monitoring of voltage, current, and frequency delivered to the DUT. Modern ATE solutions leverage remote programmability, automatic voltage ramping, and safety limit enforcement—boosting test throughput and ensuring repeatable, high-quality test results. The typical ATE configuration also includes analysis software, signal generators, oscilloscopes, measurement instruments, switching matrices, and a range of high-precision probes and interconnects.
In the highly specialized world of semiconductor fabrication and integrated circuit (IC) production, programmable power supplies (PPS) play a critical role in maintaining ultra-precise control over the power supplied to process equipment. For example, the creation of a single-cell pure silicon crystal—an essential step in wafer production—relies on programmable power supplies to regulate electrical current and voltage for equipment such as crystal pullers, chemical vapor deposition chambers, and ion implantation devices. These power supplies manage and monitor parameters for light sources, polyelectrolyte deposition, stirring motors, and temperature control devices including heaters and coolers.
By supplying precisely controlled power and providing feedback through built-in sensors or external SCADA systems, PPS ensure optimal conditions for crystal growth and semiconductor process stability. Their programmability and repeatability are essential for maintaining yield, improving process consistency, and meeting the stringent quality benchmarks demanded in the semiconductor industry. Additionally, PPS enable swift adaptation to new process recipes or test requirements, facilitating innovation and rapid development cycles.
X-ray generators are widely used in industrial inspection (such as non-destructive testing and material analysis), medical diagnostics, scientific research, and even security screening. Programmable power supplies are fundamental components within x-ray systems, precisely controlling the electrical power required to energize x-ray tubes and supporting strict adherence to safety standards. Through programmable controls, these power supplies allow for the adjustment of emission current and voltage parameters, optimize imaging performance, and protect sensitive x-ray tube components from overcurrent or overheating.
A programmable power supply’s real-time monitoring features and programmable safety limits ensure that x-ray generators operate within their specified input/output range. High-performance x-ray generator power supplies support output voltages from 160kV up to 450kV, commonly featuring polarity selection (bipolar, positive, negative) to accommodate different imaging modalities or test applications.
Effective regulation and rapid response from programmable power supplies help generate consistently accurate data, improve image quality, enhance system reliability, and extend the service life of expensive x-ray tubes. Such capabilities are particularly vital in radiography, computed tomography (CT), and advanced laboratory analysis.
Scanning electron microscopes (SEMs) rely on precisely calibrated high-voltage power for focusing electron beams and generating high-resolution images. The programmable power supply forms the backbone of a SEM’s electron optics subsystem, allowing operators to adjust voltage parameters and achieve targeted image contrast and resolution. Advanced SEMs are equipped with sophisticated graphical user interfaces and integrated programmable power modules, supporting features such as remote diagnostics, fast power sequencing, automatic calibration, and system health monitoring.
External signal control of the PPS within a SEM enables accurate, repeatable acquisition of detailed specimen images. Enhanced digital communication, high-frequency ripple suppression, and programmable ramp/hold cycles provided by these power supplies result in improved imaging accuracy, increased hardware reliability, and simplified maintenance routines.
Programmable power supplies are indispensable for rigorous testing, certification, and analysis of new electronic devices. They deliver critical test data, streamline validation protocols, and enable design engineers to refine, troubleshoot, and advance product architectures. Central to these processes is the precise, programmable regulation of voltage, current, and frequency, which ensures repeatability, accuracy, and compliance with evolving industry standards.
In laboratory and research settings, programmable power supplies are utilized to test electronic circuits, prototype innovative designs, and simulate real-world operating conditions for a variety of components and modules. They enable detailed experiment automation, remote data collection, and rapid configuration changes—essential for academic institutions, advanced research facilities, and training labs seeking repeatable, accurate results. Their precision and reliability also make them ideal for classroom demonstrations and hands-on engineering education.
Programmable power supplies are critical in test and measurement applications, supporting precision instrument calibration, quality control audits, and environmental testing of electronic devices. Their programmable nature ensures consistent power delivery during functional tests, burn-in testing, and device characterization, which is fundamental to product safety, compliance, and long-term reliability.
The success of any new product in competitive markets is directly linked to thorough research and development (R&D), which encompasses feasibility studies, performance analysis, and iterative prototyping. During the R&D phase, innovative electronic technologies and emerging concepts undergo rigorous power supply management, enabling controlled test environments, data integrity, and accelerated design validation. Programmable power supplies increase flexibility, accelerating development cycles and enabling complex test routines involving variable power scenarios.
Modern manufacturing facilities rely on programmable power supplies for comprehensive automated production testing, in-circuit testing, final quality inspections, and on-line debugging of electronic assemblies. Incorporating programmable power management into the production line ensures product batches consistently meet performance standards, regulatory requirements, and customer expectations. Their integration with factory automation systems allows seamless communication, quick changeovers, and detailed process analytics—key factors for lean manufacturing and zero-defect strategies.
Ultimately, programmable power supplies represent a versatile and indispensable technology for organizations prioritizing precision, efficiency, and reliability in electronic testing, manufacturing, and engineering innovation. As the demand for smarter, safer, and more efficient electronic devices grows, the role of programmable power supplies in enabling quality control, product optimization, and accelerated innovation continues to expand across industries worldwide.
Programmable power supplies are essential for precise and automated control of electrical power in modern electronics testing, product development, and industrial automation. These versatile power sources are categorized primarily by the type of electrical current they manage and their ability to be remotely configured for voltage, current, and even timing cycles. DC programmable power supplies are engineered to deliver a stable and controlled DC output, making them ideal for applications that require precise voltage regulation, including laboratory testing, R&D, and production line testing. In contrast, AC programmable power supplies not only provide stabilized AC voltage but also enable the generation of user-configurable AC waveforms and frequency variations. This makes AC models invaluable for simulating grid disturbances, performing compliance testing, or evaluating device performance under fluctuating line conditions. Certain AC programmable power supplies also double as frequency stabilizers, increasing their utility for sensitive testing scenarios.
When selecting a programmable power supply, users frequently evaluate specifications such as maximum voltage, current range, output power, programmability (via USB, LAN, or other digital interfaces), reliability, and available safety features. Detailed comparison and application-specific considerations help ensure the supply matches user requirements, minimizes noise, and supports various integration options.
DC programmable power supplies deliver either a constant current or constant voltage and are categorized into linear regulated and switching regulated power supplies based on control methods. As a core power conversion technology, they support a wide range of output voltages (from a few volts up to tens of thousands of volts), enabling reliable operation for electronic circuits, device characterization, and automated test equipment.
Common configurations include benchtop, rack-mounted, modular, and PCB-mounted programmable power supplies, with some offering flexible input for both AC and DC power sources. Devices can be set to either constant voltage (CV) or constant current (CC) modes, prioritizing voltage stability or current limiting depending on the application’s requirements. This control is especially critical for precise load testing, battery charging, and semiconductor evaluation.
DC programmable power supplies play a vital role in electronic design validation, product burn-in testing, and automated manufacturing. Key programmable parameters include:
These features allow for repeatable, automated testing processes in electronics manufacturing and quality assurance.
The output voltage is fixed as set by the user, and the output current changes in response to variations in the load’s resistance. This mode is frequently used for powering electronic circuits that require precise, ripple-free voltage for optimal operation.
The Constant Current (CC) mode is primarily used for applications such as LED testing, battery charging, and stress testing components, where consistent current is essential. If the load attempts to draw more than the programmed limit, the supply automatically switches from constant voltage (CV) to CC mode to protect both the supply and connected devices from damage; it automatically reverts to CV once the draw decreases.
Critical parameters to compare when choosing a DC programmable power supply include:
AC programmable power supplies are purpose-built to deliver ultraprecise alternating current with adjustable voltage, frequency, and waveform customization for simulating real-world grid conditions. Test engineers and design verification teams use them to replicate brownouts, surges, harmonics, and other AC line disturbances that electrical devices may encounter. These power supplies are critical for standards compliance, such as IEC, MIL-STD, or various quality certifications for global distribution.
Common use cases include power electronics, lighting systems, electric motors, aerospace components, defense electronics, and laboratory testing where variable AC waveform generation is required. Users can program these supplies to generate complex AC waveforms—including sags, interruptions, surges, trapezoidal, and phase-dimmed waves—with frequency ranges typically from 45 Hz up to 500 Hz, or even beyond for high-frequency testing. Advanced models may feature arbitrary waveform generation, distortion simulation, and synchronized output for three-phase systems.
Standard output for AC programmable power supplies is a sine wave; however, precise frequency and voltage control support regional standardization across international power grids. This adaptability helps manufacturers verify designs for North American, European, and Asian power environments.
Benchtop programmable power supplies are compact, portable units specifically designed for laboratory, prototyping, and educational environments. They provide easy, on-the-fly adjustment of voltage and current for circuit development, breadboarding, and testing. Benchtop supplies feature high accuracy, low ripple, and advanced protection for Device Under Test (DUT) safety.
These supplies are essential in electronics laboratories for characterizing components, performing functional circuit verification, and facilitating R&D workflows. Typical features include:
Benchtop models are available with either linear or switching topologies; linear supplies provide excellent noise performance, while switching supplies offer high efficiency and lighter form factors. High-end benchtop programmable power supplies may feature touchscreen interfaces, programmable sequencing, and networked operation for highly automated test setups.
Rack-mounted programmable power supplies are industrial-grade power delivery solutions optimized for integration into test racks, production lines, and automated test equipment (ATE). Their stackable form factor and ability to be connected in series or parallel expand power output, supporting extensive system testing or high-current/high-voltage applications.
Typical rack-mounted models support advanced programmable features such as:
Power output ranges from 200 W to 15 kW per unit, with modular scalability to 60 kW total output and voltages reaching 1500 V or more. Rack-mounted programmable power supplies are preferred by aerospace, automotive, and semiconductor industries for continuous, reliable operation in demanding environments.
Chassis-mounted programmable power supplies are installed directly into equipment or system enclosures and often serve as embedded power delivery modules for OEM products, industrial controls, and precision instrumentation. They are available in linear or switching topologies, delivering AC-DC or DC-DC power conversion based on required use cases.
Key form factors include:
Chassis-mount models are engineered for optimal heat dissipation, electromagnetic interference (EMI) management, and highly customizable mounting options. Their rugged construction and advanced safety features make them well-suited for harsh industrial or laboratory environments.
Digital programmable power supplies feature digital interfaces, microcontroller-based regulation, and encoder knobs for precise electronic control and monitoring. Programmed via front-panel inputs or remote software commands, these supplies convert digital settings into accurate voltage and current output adjustments. Advanced models offer USB, Ethernet, or SCPI-compliant control for integration with test automation and data acquisition software.
Benefits of digital programmable supplies include:
Analog programmable power supplies employ traditional analog adjustments using knobs and dials, making them ideal for simple systems, manual calibration, and legacy equipment testing. While less flexible than digital models, they deliver high reliability and instant, tactile control. Analog regulators use voltage and current sensing, error amplifiers, and optocouplers for robust closed-loop feedback.
Best suited for dedicated, unchanging applications, analog programmable power supplies are preferred for their stability, low susceptibility to digital glitches, and ability to deliver reliable power where frequent parameter adjustments are not required. However, customization and remote programmability are limited compared to modern digital power supplies, making them less attractive for automated or iterative testing.
Programmable power supplies convert electric power from their input source to deliver to the load. The input and output can be either AC or DC current. DC current, which flows consistently in one direction, is typically preferred for electronic devices. Conversely, AC current is used for power transmission through lines and alternates direction periodically.
Programmable power supplies come in various types, each designed and configured to meet the requirements of different electronic devices and applications. They are programmed with the necessary parameters to achieve the desired performance.
These power supplies continuously monitor and adjust the output voltage to maintain the specified value. They also include additional controls for setting current and voltage limits, filtering noise, and adjusting output. The primary types of programmable power supplies are linear and switching models, with linear power supplies being simpler and less complex.
The main use for linear programmable power supplies is in applications where precision control is necessary and removal of noise is important. They are the least efficient of the types of programmable power supplies but offer the best performance. The name of linear programmable power supplies comes from the power supplies not using switches as a means to regulate the voltage output.
Linear power supplies have been in use for many years and represent one of the earliest types of power supplies. With the advent of new controls and technological improvements, linear programmable power supplies have been updated to meet modern requirements in the 21st century.
Compared to switched programmable power supplies, linear models feature larger and heavier components, which can make them bulkier and generate more heat. Despite their improved accuracy, linear programmable power supplies are approximately 50% less efficient than their switched counterparts.
Linear programmable power supplies are ideal for applications demanding precise regulation, minimal ripple, low electromagnetic interference, and superior transient response. They reduce input voltage to achieve a lower output voltage. This voltage adjustment is accomplished through a transformer that steps down the voltage from an AC source to a lower AC voltage, which is then converted to DC voltage via rectifier circuits and filters.
Switched programmable power supplies are advanced and versatile devices that offer greater efficiency compared to linear power supplies. Despite their complexity, they are typically smaller, lighter, and more cost-effective than linear models.
One key advantage of switched programmable power supplies is their minimal power loss across the switch due to their high-frequency operation. However, this high frequency can generate noise that may affect other circuits. This drawback is offset by their broad input voltage range and high output capability, which enhance their overall efficiency.
Despite their benefits, switched programmable power supplies come with challenges, including complex circuitry, potential interference with AC mains, elevated noise levels, and the need for shielding to manage their high operating frequencies.
The widespread adoption of switched programmable power supplies is driven by the trend toward smaller, more portable electronic devices. These power supplies use semiconductor technology to regulate and convert power by rapidly switching on and off.
The different types of switched programmable power supplies include:
Traditional power supplies offer fixed settings with limited options for adjustments, whereas programmable power supplies provide enhanced flexibility with multiple modes. Users of programmable power supplies can adjust various settings, such as voltage, current, power, and operational modes, according to their specific needs.
Controlling these parameters offers several advantages, including:
With a programmable power supply, a battery charger can initially provide a constant current during the early stages of charging and then transition to constant voltage (CV) as the battery approaches full charge. If the current exceeds the limit while in CV mode, the power supply will automatically revert to constant current (CC) mode. In CC mode, the programmable power supply maintains the current at a set level, ensuring safe operation. The output current and voltage are regulated according to user-defined settings.
A programmable power supply consists of several key components, including a transformer, rectifier, filter, and regulator circuits. These components work together to ensure a stable power supply for multiple devices and are essential for experiments where precise control of current and voltage is required.
In a programmable power supply, the transformer is a static component that transfers electrical energy from the primary winding to the secondary winding without altering the frequency. It is used to either step up or step down the AC voltage. Additionally, the transformer provides isolation between the electronic system and the AC power source.
The primary winding of the transformer connects to an AC voltage source, while the secondary winding connects to the load. Although energy is transferred from the primary to the secondary winding, the two are electrically isolated from each other. This energy transfer occurs through electromagnetic induction, which generates a voltage in the secondary winding.
The transformer in a programmable power supply serves three main functions: adjusting the voltage level (either stepping it up or down) and providing electrical isolation between the primary and secondary circuits.
The rectifier or diode in a programmable power supply changes AC power into pulsating DC power. The diode is a unidirectional component that operates as a rectifier in the forward direction. The circuits of a rectifier using a diode are half wave, full wave center tapped, and full wave bridge type.
Half wave rectification is not used for the majority of power applications. It is a simple method for reducing power to resistive loads.
Full wave rectification center tapped is used to rectify AC power to get full use of the half cycles of the sine wave. A full wave rectifier with a center tap design is used with a transformer that has a center tapped secondary winding and two diodes.
A full wave bridge rectifier has a four-diode bridge design and converts the complete AC signal into DC signal. It is the most used type of rectifier. Full wave bridge rectifiers convert positive and negative half cycles of AC current into DC current and provide double output voltage compared to half wave rectifiers, which is possible due to the four diodes.
In a programmable power supply, the filter is crucial for removing ripple components from the output. It transforms pulsating DC current from the rectifier into a stable, smooth DC voltage. There are two main types of filters used: capacitance (C) filters and resistor-capacitor (RC) filters.
C filters are the most basic and cost-effective type of filter. RC filters, on the other hand, are employed to further reduce ripple voltage that persists after C filters, allowing for the passage of the DC component. RC filters work by blocking certain frequencies while permitting others to pass. They come in two varieties: high-pass filters, which allow signals above a certain cutoff frequency to pass, and low-pass filters, which permit signals below a cutoff frequency to pass.
The primary role of filters is to control the ripple factor, which represents the unwanted AC component remaining after rectification. This ripple can potentially harm the load, so filters are designed to smooth the signal and attenuate the AC component. The ripple factor is calculated as the ratio of the root mean square of the ripple voltage to the DC component of the output voltage, and is often expressed as a percentage. Evaluating the ripple factor helps determine the filter's effectiveness.
The primary function of a programmable power supply is to deliver a stable output voltage to ensure proper operation of the connected load. This output voltage must remain constant despite fluctuations in the input voltage. Voltage regulation is achieved using two main types of regulators: series voltage regulators and shunt voltage regulators.
A series voltage regulator manages the unregulated input voltage that is delivered to the output. It employs a feedback circuit to sample the output voltage, which is then compared to a reference voltage by a comparator circuit. This feedback mechanism helps maintain the desired output level. In contrast, a shunt voltage regulator diverts current away from the load to regulate the output voltage.
Integrated circuits (ICs) used in programmable power supplies typically include a reference source, comparator, amplifier, control device, and overload protection. These components work together to control the output values, which can be adjusted by the user to meet specific requirements.
The ITECH IT7321 employs linear amplification to generate output signals that closely replicate the input. It is particularly valued in avionics for meeting stringent testing standards required for aviation electronics and for its capability to operate at 400 Hz AC during evaluations. The ITECH IT7321 facilitates precise, high-resolution testing, making it a reliable tool for accurate and efficient testing procedures.
The PLS series single-output programmable DC power supply provides a range of DC output voltages, including 30V, 50V, 100V, 200V, and 400V, with power ratings between 600 W and 1500 W. This versatility allows users to achieve various voltage and current settings from a single unit. The PLS series supports operation in series, parallel, or combined configurations, enabling output voltages up to 800V and power up to 6 kW. It also offers remote control options through USB, Ethernet, and analog inputs.
The EDU36311A is a compact triple-output power supply designed to fit comfortably on a workbench. It features a 7-inch color display that allows for simultaneous monitoring of all outputs. Each output is independent, enabling configurations such as series connections for higher voltages, parallel setups for increased current, or stacking. The EDU36311A includes a sequencing function to enable or disable outputs in a predetermined sequence, and its control logic can be configured before applying power to a device. Additionally, the unit comes with proprietary software for remote control and data logging capabilities.
The Sequoia series is a versatile four-quadrant regenerative grid simulator, optionally equipped with a regenerative electronic load mode. This series offers high power capabilities and flexibility, making it an advanced solution for AC applications. Featuring SIC power switching technology, the Sequoia series is designed with a compact and durable floor-standing chassis. It provides an easy configuration for both single and multiphase AC power, as well as single and multichannel DC power. The Sequoia series is suitable for applications including power conditioning, grid-interactive green energy systems, and power distribution generation.
The GENESYS+™ is a portable and user-friendly programmable power supply, known for its lightweight design and multifunctional front panel. It features isolated analog and optional communication interfaces. Available in power levels of 30kW, 45kW, and 60kW, the GENESYS+™ is housed in a 23U rack system profile. A key highlight of the GENESYS+™ is its low-noise output, with voltage ranges from 10V to 600V. It supports AC input options, including built-in active power factor correction, with choices of three-phase 208 VAC, 400 VAC, or 480 VAC. Additional features include programmable slew rate control, constant power limit control, an arbitrary waveform generator with auto-trigger functionality, and internal resistance programming.
Programmable power supplies offer a wide range of applications and are crucial for testing, diagnosing, and safeguarding electrical devices. Choosing the right programmable power supply involves evaluating key factors to ensure it meets the requirements for effective use.
Choosing a programmable power supply starts with assessing the voltage and current requirements of your application. The output specifications must align with the testing needs or power demands. It's crucial for the power supply to handle both maximum and minimum values without compromising precision or safety. Excessively high voltage or current settings can negatively impact the accuracy of the output.
The appeal of programmable power supplies largely stems from their diverse range of controls and data feedback options. Key features include the ability to set voltage and current limits. While many models offer remote control capabilities, it's important to consider the type of remote interface available. Additional common features include ramping, sequencing, overcurrent and overvoltage protection, electronic current limiting, and thermal resets.
Output stability denotes a programmable power supply's capability to maintain stable voltage and current levels despite varying load conditions over time. This characteristic is detailed in the power supply's specifications, which cover load and line regulations to indicate its stability performance. For applications requiring precise and stable power output, selecting a power supply with high stability is essential. The final choice should align with the specific needs of the application.
Multiple outputs enhance efficiency and allow for connection of several loads to a single programmable power supply. When selecting a power supply with multiple outputs, ensure each output is isolated and can function independently or in parallel to provide greater flexibility.
This feature, while optional, is generally recommended as it allows users to turn outputs on or off without interrupting the load supply. It facilitates setting up different tests without concerns about their impact on the load.
Constant voltage is a standard feature in all programmable power supplies, designed to provide stable voltage while varying the current for testing. Occasionally, switching to constant voltage mode is necessary for applications requiring stepped voltage sequences.
An easy setup process for a programmable power supply allows more time for testing and monitoring applications. Many programmable power supplies feature intuitive controls that facilitate quick and efficient setup. Units with separate controls for voltage and current and fine-tuning options offer enhanced precision.
Effective temperature management is crucial for the reliability and safety of a programmable power supply. It is highly recommended to choose a power supply with an integrated high-performance cooling system. Various cooling designs are available, each suited to specific types of programmable power supplies.
Power supplies are electrical circuits and devices that are designed to convert mains power or electricity from any electric source to specific values of voltage and current for the target device...
An AC power supply is a type of power supply used to supply alternating current (AC) power to a load. The power input may be in an AC or DC form. The power supplied from wall outlets (mains supply) and...
A DC DC power supply (also known as DC DC Converter) is a kind of DC power supply that uses DC voltage as input instead of AC/DC power supplies that rely on AC mains supply voltage as an input...
A DC power supply is a type of power supply that gives direct current (DC) voltage to power a device. Because DC power supply is commonly used on an engineer‘s or technician‘s bench for a ton of power tests...
By definition a power supply is a device that is designed to supply electric power to an electrical load. An electrical load refers to an electrical device that uses up electric power. Such a device can be anything from...
An AC power cord is a detachable way of providing an alternating current of electric energy from a mains power supply to an electrical appliance or equipment. Serving industries like...
Electrical plugs, commonly known as power plugs, are devices responsible for supplying and drawing current from a receptacle to the circuitry of an electrical appliance...
Electronic connectors are devices that join electronic circuits. They are used in assembling, installing, and supplying power to electrical devices. Connectors are an important component of every electronic equipment used in...
An electric switch is a device – usually electromechanical - that is used to open and close an electric circuit. This disables and enables the flow of electric current, respectively...
A NEMA connector is a method for connecting electronic devices to power outlets. They can carry alternating current (AC) or direct current (DC). AC current is the typical current found in homes, offices, stores, or businesses...
A power cord is an electrical component used for connecting appliances to an electrical utility or power supply. It is made from an insulated electrical cable with one or both ends molded with connectors...
Push button switches are electrical actuators that, when pressed, either close or open the electrical circuits to which they are attached. They are capable of controlling a wide range of electronic gadgets...
Thomas Edison developed the power distribution system in 1882. He wrapped a copper rod in jute, a soft shiny fiber from plants, as an insulator. The jute wrapped copper rod was placed in a pipe with a bituminous compound...