Pressure Vessels
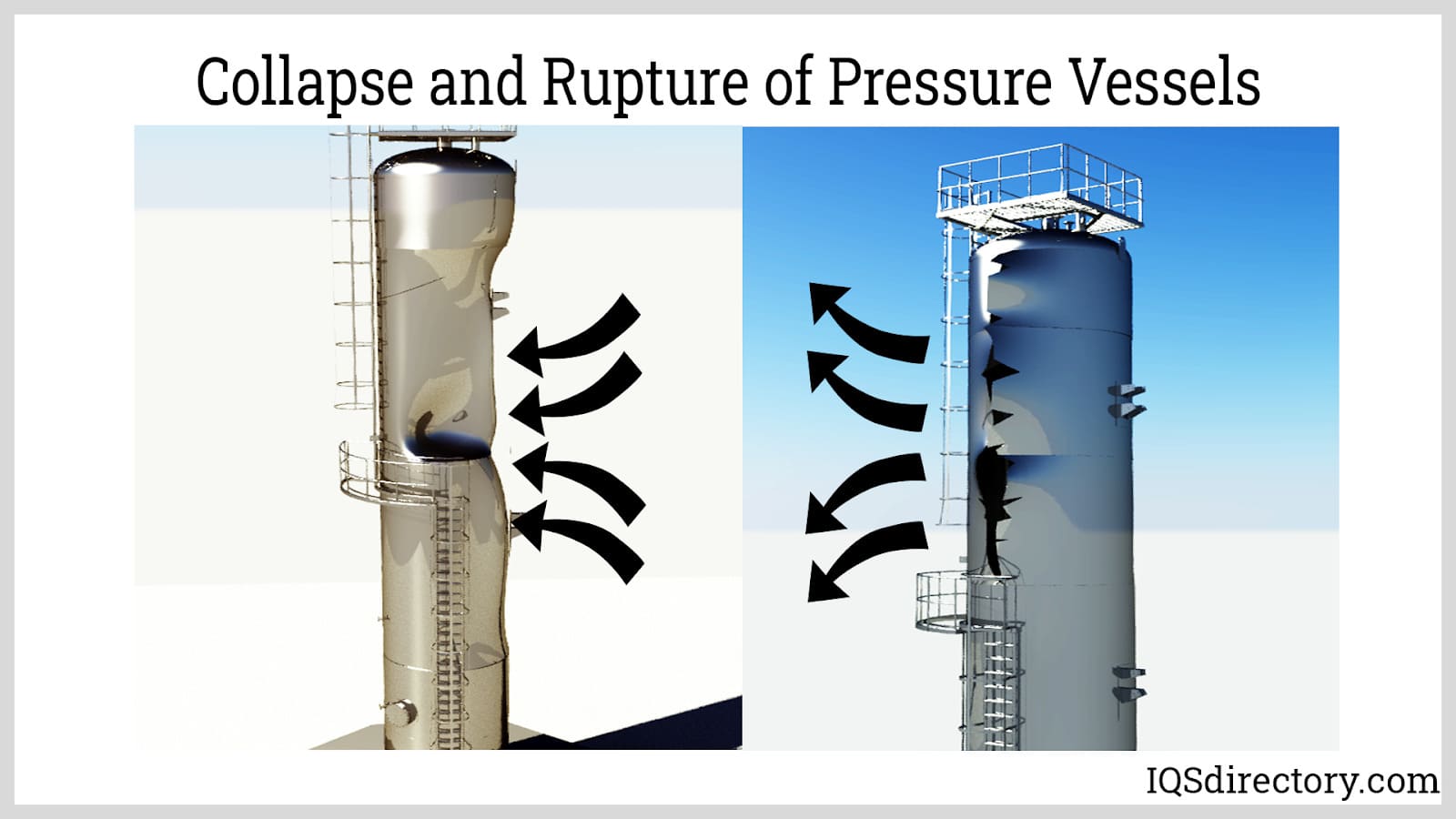
Pressure vessels are enclosed containers used to hold liquids, vapors, and gases at a pressure significantly higher or lower than the ambient pressure. They are widely used in various industries such as...
Please fill out the following form to submit a Request for Quote to any of the following companies listed on
Here is the most complete guide on the internet about
You will learn:
This section delves into the essence of pressure tanks, their creation process, and their roles in a range of applications.
Pressure tanks are specially designed containers for storing, controlling, and transporting gases, vapors, or liquids at pressures above atmospheric levels, often known as elevated pressures.
Pressure vessels are closed containers utilized for storing liquids, vapors, and gases at much higher or lower pressures than the surrounding atmosphere. They are prevalent in numerous industries such as petrochemical, oil and gas, chemical, and food processing. Pressure vessels encompass items such as reactors, flash drums, separators, tanks, and heat exchangers.
Pressure vessels are designed to operate within specified temperature and pressure limits, known as safety standards. Their design, production, and inspection are performed by certified professionals following rigorous standards to avoid accidental leaks or emissions posing environmental hazards. Important standards include the API 510 Pressure Vessel Inspection Code and ASME Section 8 of the Boiler and Pressure Vessel Code.
The main distinction between pressure tanks and pressure vessels lies in the maximum allowable operating pressure (MAOP) they can handle. Pressure vessels are engineered to manage pressures significantly exceeding atmospheric conditions, often surpassing 15 PSI, with MAOPs reaching up to 3000 PSI or more in specific scenarios. In contrast, pressure tanks are primarily meant for static liquid storage, typically featuring an MAOP of 15 PSI or lower, and often functioning at or below atmospheric pressure.
Pressure vessel design and safety regulations are governed by ASME Section VIII, covering Divisions 1, 2, and 3. In Europe, comparable safety measures are established by BS5500 and other national guidelines. Meanwhile, pressure tanks are built according to industry-specific standards and pressure thresholds as follows:
In summary, pressure vessels are typically completely enclosed, whereas pressure tanks can be open or sealed, particularly in vertical cylindrical designs. For example, a fuel tank might feature an open top with a breather accommodating ambient pressure. Moreover, pressure tanks generally have a larger capacity than pressure vessels, with the latter requiring more caution during maintenance due to the potential for hazardous explosions.
The production of pressure tanks involves these critical stages:
Pressure tanks are typically crafted from steel and stainless steel, due to steel's durability, robustness, and capacity to endure major stress and extreme conditions. Stainless steel adds additional benefits, including ease of cleaning and corrosion resistance, making it suitable for hygiene-sensitive environments such as food and drink production, medical uses, or laboratory conditions.
Besides steel and stainless steel, pressure tanks can also be constructed from materials like aluminum, carbon fiber, titanium, zirconium, and various high-strength polymers. Based on the application requirements, tanks might also feature coatings composed of polymers, rubber, metals, or ceramics to enhance structural integrity and prevent leakage.
When selecting a material, consider these factors:
The design calculations for pressure vessels encompass several vital parameters. These elements are crucial for determining the shell and head wall thickness.
Design Pressure: This parameter is essential for defining the vessel's specifications. It is chosen based on the maximum operating pressure, considering variations during start-ups, emergency shutdowns, and process fluctuations. Design pressure must exceed the system's maximum operating pressure and influences the vessel’s pressure relief mechanisms to prevent explosions. It is generally advised that design pressure be 5-10% above peak operating pressure. For vessels potentially exposed to vacuum conditions, design pressure should accommodate a full vacuum (-14.7 psi).
Maximum Allowable Working Pressure (MAWP): MAWP is the highest pressure at which the vessel is safely designed to operate at its set temperature. It is the utmost pressure that the weakest vessel part can sustain at this temperature. Established by the American Society of Mechanical Engineers (ASME), MAWP ensures safety by preventing operation beyond this level, thus lowering explosion risks. Unlike design pressure, which considers operational conditions, MAWP is a more overarching metric based on the vessel's material thresholds. While risks like corrosion or wear can lessen MAWP, design pressure is dictated by operational conditions and may be equivalent to or below MAWP.
Design Temperature: Temperature affects the maximum allowable stress on a vessel, as material strength declines at higher temperatures and becomes fragile at very low temperatures. To calculate maximum allowable pressure, the vessel must not function at temperatures exceeding the design temperature. This design temperature is set higher than the highest operating temperature but lower than the lowest temperature the vessel may encounter.
When setting the design temperature, several guidelines should be adhered to. It is recommended to set the design temperature 500 degrees Fahrenheit above the highest operating temperature and 250 degrees Fahrenheit below the lowest operating temperature. For vessels operating in the range of -30°C to 345°C, a maximum design temperature allowance of 250°C is advised. Additionally, potential disturbances that might significantly impact the tank's temperature should be considered by designers.
Maximum Tolerated Stress: Maximum tolerated stress is obtained by applying a safety factor to maximum allowable stress. This safety factor compensates for potential deviations from ideal parameters during the pressure vessel's construction and operation.
Joint Effectiveness: The ASME Boiler and Pressure Vessel (BPV) Code classifies welded joints into four categories. Joint effectiveness measures the relative strength of the base material compared to the welded joint. Typically, welded joints exhibit lower strength. Without complementary inspection and radiographic testing, welded joints are deemed weaker due to defects like porosity. The ASME BPV Code Section supplies guidelines for evaluating joint efficiency.
Corrosion Allowance: Estimating corrosion allowance follows various guidelines that may differ by manufacturer. Generally, a corrosion allowance varies from 1.5 to 5 mm. It is advised to allocate 0.25 to 0.38 mm annually or roughly 3 mm over a decade. For high corrosion rate environments, allowances may extend to 8.9 mm. In less corrosive environs, around 3.8 mm is typical. Air receivers and steam drums frequently have a corrosion allowance of 1.5 mm. In heat exchanger systems, where wall thickness affects heat transfer efficiency, the corrosion allowance should be minimized.
The vessel's shell and heads are formed through forging, rolling, and welding metal plates. The plate thickness, which determines wall thickness, is meticulously calculated in line with prior criteria. Subsequently, various auxiliary equipment, devices, and accessories are added to ensure optimal pressure vessel operation.
Post-weld heat treatment alleviates stresses accrued during welding and forming processes.
Pressurized containment vessels can be constructed to align with the standards set by the American Society of Mechanical Engineers (ASME). Commonly referred to as ASME tanks, these vessels are crafted to comply with ASME's strict criteria for design, construction, fabrication, operation, and maintenance. To retain ASME certification, these pressure tanks must undergo routine inspections. While ASME certification isn't always mandatory, numerous manufacturers comply with these standards to assure quality and customer safety.
Pressure tanks may also adhere to an assortment of local and international standards, including UL, ASTM International, TUV, USDA, ISO, Canada, and the European Union, among others. Additionally, many manufacturers produce non-code vessels. For the latest and most relevant information tailored to a customer's needs, it is advisable to consult a seasoned pressure tank manufacturer.
Pressure vessels are engineered to operate at specific pressure levels determined by their intended functions, such as air storage in scuba tanks. They manage pressure either directly through valves and gauges or indirectly through heat transfer. Pressure conditions can vary widely, from 15 psi to 150,000 psi, with temperatures frequently.
Essential considerations when selecting pressure tanks include:
Material selection is vital in pressure tank manufacturing and significantly impacts cost. Options include carbon and low alloy steels, nickel alloys like Monel, Inconel, and Hastelloy, various stainless steels including series and high-temperature grades, duplex stainless steels like 2205 and 2507, and aluminum. Material selection hinges on specific process conditions and the tank's purpose, making it crucial to choose the best-suited material for the tank's envisioned use and specifications.
Design is a crucial aspect of developing a new pressure tank, as it must withstand demanding industrial conditions. Welded construction plays a key role, as imperfections can lead to severe failures. BEPeterson ensures all vessels meet ASME standards using the latest version of Compress software. Advanced fabrication methods refine designs, confirming thorough consideration of cost implications.
When acquiring a pressure tank, it's essential to ensure compliance with applicable industry standards and specifications:
Manufacturers perform numerous tests to assess the tank's load-bearing capacity and performance under extreme conditions. These evaluations include Ferrite Testing, Hydro-testing, Positive Material Identification (PMI), Helium Leak Testing, Dimensional Inspection with a FaroArm, alongside Radiography and Non-Destructive Examination (NDE) methods like Penetrant Testing (PT), Ultrasonic Testing (UT), and Magnetic Particle Testing (MT). These inspections provide insightful data regarding the tank’s strength and reliability.
This chapter will explore the various classes and types of pressure tanks, providing valuable guidance for homeowners, facility managers, and industrial professionals seeking the right pressure vessel solution for water systems, steam applications, chemical storage, and more.
Well pressure tanks are crucial components of residential and commercial well water systems, designed to regulate water pressure and store water for on-demand use. A pump—either submersible or jet—pulls groundwater into the home or facility, while the well pressure tank maintains steady water pressure, minimizes pump cycling, and extends pump life. Acting as a pressure vessel and storage reservoir, these tanks automatically signal the pump when water levels drop, ensuring an uninterrupted, efficient water supply. Understanding the different types of well pressure tanks will help you choose the ideal system for your property’s water needs.
Commonly known as galvanized or stainless steel pressure tanks, these traditional water pressure tanks store both water and air together within a single chamber. To prevent internal corrosion from prolonged water contact, many feature specialized coatings, often referred to as "glass-lined" or "epoxy-coated" interiors.
In air-over-water pressure tanks, air and water are in direct contact without a fixed barrier. While increasingly rare in modern well systems, these tanks utilize compressed air to maintain water pressure throughout the home's plumbing. Their larger size doesn't necessarily translate to greater capacity, often resulting in more frequent pump cycling, which can shorten the lifespan of water pumps due to additional wear. Furthermore, these tanks are prone to air loss—which can occur through small pinhole leaks—leading to water-logging, inconsistent water pressure, and the need for manual air recharging or tank replacement.
Diaphragm pressure tanks feature two distinct, sealed compartments—one for air and one for water—separated by a flexible rubber diaphragm. This diaphragm is permanently anchored inside the pressure vessel, flexing according to the volume of water entering the tank.
As water is pumped into the lower chamber, it presses upward on the diaphragm, compressing the air in the upper compartment. When optimal pressure is achieved, a pressure switch activates, turning off the water pump until water is drawn again.
These hydro-pneumatic tanks offer precise pressure control and minimize pump short-cycling. However, common issues include diaphragm detachment or rupture, which allows water to infiltrate the air chamber and makes the tank inoperative. Another concern is diaphragm “fold-over,” which causes inaccurate pressure readings, inefficient pump operation, and potential premature failure of both the tank and pump. Opting for high-quality, properly sized diaphragm tanks can reduce maintenance and system downtime.
Bladder tanks represent a modern, high-performance option for well water systems, featuring separate internal chambers for air and water. An inflatable, replaceable bladder (similar to a robust balloon) isolates water from air, expanding as the tank fills and contracting as water is drawn, precisely controlling pump activation.
Because air and water never mix, bladder-style pressure tanks prevent water-logging and minimize the risk of corrosion, resulting in lower maintenance. They deliver consistent water pressure, have a longer service life than traditional tanks, and reduce pump cycling. Bladder tanks are available in vertical and horizontal configurations, and in a wide range of storage sizes to suit residential, agricultural, and light industrial applications.
A steam drum is a critical pressure vessel component in water-tube steam boilers, engineered for safe generation and separation of saturated and superheated steam. Located at the top of the boiler assembly, the steam drum acts as a centralized reservoir, collecting steam from water tubes, separating moisture, and equalizing pressure throughout the boiler system. The density gradient between hot steam and cooler water facilitates natural circulation and efficient steam management.
The main functions of a steam drum include distributing dry steam for process use, separating moisture via demisters, providing a water-level reference for controls, and containing essential components such as safety valves and feedwater pipes. Steam from the drum is routed to superheaters to create high-temperature, high-pressure steam for steam turbines and other power generation or industrial processes. Modern designs often incorporate advanced instrumentation for monitoring water level, pressure, and system integrity, ensuring operational safety and efficiency.
Steam drums can operate as standalone devices or work in conjunction with mud drums (or feedwater drums) located at lower boiler elevations. Systems utilizing both are called bi-drum boilers, optimal for low- to medium-pressure applications with variable load profiles. Conversely, mono-drum (single drum) boiler designs are favored in high-pressure, high-efficiency power plant settings, due to their streamlined design and superior stress tolerance.
Types of steam drum boiler configurations include:
Three and Four Drum Boilers: Traditional multi-drum configurations frequently used in older stationary boilers continue to serve in various process industries. These boilers offer greater steam separation and storage capacity.
Bi Drum Boilers: Suitable for process steam generation and thermal power plants requiring stable operation under fluctuating load conditions. While commonly replaced by advanced single drum designs in high-capacity power stations, bi drum boilers remain popular in industrial processing due to flexible controls, simplified maintenance, and robust performance in moderate-pressure systems.
Single Drum Boilers: The industry standard for modern power plants, single drum designs support both reheat and non-reheat cycles, accommodate high steam pressures, and ensure optimal heat transfer. Styles include top-supported and corner tube boilers, which offer superior mechanical stability and ease of inspection.
Safe and effective storage of ammonia is essential for industries such as agriculture, refrigeration, and chemical manufacturing. Ammonia storage tanks are specialized pressure vessels engineered to contain either liquefied anhydrous ammonia or low-temperature refrigerated ammonia, each requiring precise safety strategies and robust construction materials. The choice between high-pressure vessels and atmospheric pressure refrigerated storage is mainly determined by volume needs, regulatory compliance, and safety considerations.
Low-pressure ammonia storage tanks have gained popularity due to their lower capital costs per storage volume and increased operational safety. Unlike spherical "Horton spheres," these horizontal or cylindrical tanks store ammonia at atmospheric pressure and –33°C, minimizing risk of rupture or hazardous leaks. Large-scale ammonia storage installations, often accommodating up to 50,000 tonnes, prioritize environmental compliance and feature advanced insulation, pressure relief, nitrogen blanketing, and automatic leak detection systems to ensure workplace and community safety.
When selecting an ammonia tank, buyers should consider tank capacity, design pressure, applicable codes (such as ASME Section VIII), required accessories (valves, level gauges, safety relief devices), and site-specific needs such as secondary containment, monitoring, and spill control. Partnering with reputable pressure vessel manufacturers will ensure regulatory compliance and long-term, reliable operation of ammonia storage systems.
Hot water tanks, sometimes called hot water storage tanks, thermal storage tanks, hot water cylinders, or heat storage tanks, are essential for storing and delivering hot water in homes, multifamily residences, and commercial facilities. These pressure vessels are used in space heating, domestic hot water supply, and hydronic heating systems, serving as efficient thermal reservoirs.
Water’s high specific heat capacity makes it an ideal thermal storage medium, enabling efficient energy use and retention for extended periods. Most hot water tanks are well-insulated to minimize heat loss and lowering energy consumption for heating. Fuel sources can include gas or oil burners, electric immersion heaters, heat pumps, solar thermal collectors, or external heat exchangers that integrate with central heating or renewable energy systems. Selecting the right tank size and heat source ensures adequate hot water supply and can significantly reduce utility costs, aligning with green building and energy-saving goals.
Modern water heaters for domestic hot water applications—such as for washing, bathing, or cleaning—feature electronic thermostat controls with temperature ranges typically between 40°C and 60°C (104°F to 140°F), ensuring user comfort and safety. These systems are directly connected to the municipal or private well cold water supply and can be paired with circulation pumps or recirculation lines for instant hot water access.
To improve system longevity, tanks may include sacrificial anode rods, glass linings, and scale inhibitors, especially in regions with hard water or high mineral content. Without adequate water treatment, mineral scaling and internal corrosion due to dissolved oxygen can eventually cause leaks or equipment failure. Regular maintenance protocols, such as flushing and anode rod replacement, are recommended to preserve the life of your hot water tank investment.
For commercial or industrial operations with large-volume hot water needs, custom-engineered pressure vessels can provide high-efficiency, scalable hot water storage integrated into complex energy systems or district heating networks.
A process tank is a versatile vessel or containment system used in industrial, water treatment, and manufacturing settings for batching, mixing, blending, reacting, or temporarily holding chemicals, water, food ingredients, pharmaceuticals, and other fluids or solids. Designed for specific applications, process tanks may include agitation systems, heating or cooling jackets, level sensors, and various piping or pumping assemblies, allowing customized integration into automated process controls and facility operations.
Process tanks can be fabricated from a range of materials—including stainless steel, carbon steel, fiberglass reinforced plastic (FRP), or specialty alloys—to resist corrosion, withstand pressure fluctuations, and contain hazardous or reactive materials. Key considerations when specifying a process tank include required capacity, maximum working pressure, design temperature, chemical compatibility, and compliance with codes such as ASME, API, or UL. Custom tanks can also include features for sanitization, drainability, and integration into clean-in-place (CIP) systems, suited to demands in food processing, pharmaceuticals, water treatment, or chemical manufacturing.
When researching process tanks for your facility, compare options for agitation, heating, pressure ratings, compliance with industry standards, and lifecycle service offerings from reputable pressure vessel manufacturers. Investing in quality process tanks will help ensure efficient, compliant, and safe operations tailored to your industry’s requirements.
This chapter will explore the various uses and advantages of pressure tanks.
Pressure tanks are utilized across various industries for storing and transporting substances. These industries include food and beverage, chemicals, recreation, plastics and polymers, rubber, military and defense, water treatment and filtration, pharmaceuticals, oil, fuel, and energy.
Furthermore, they are frequently associated with well systems, from which residential residences and structures obtain their water supply. Other pressure tank applications include nuclear reactor vessel operation, autoclaves, recompression chambers, and road vehicle air brake reservoirs, powering of air tools, and the functionality of diving cylinders and other cylinders of gas utilized in medical, chemical, and industrial processes. The most common pressure tank applications are discussed below.
In the oil and gas industry, pressure vessels are widely used as receivers for high-temperature and high-pressure physical and chemical processes. These vessels serve various functions, but their construction generally follows similar principles. For example, distillation columns are utilized to separate feed streams into different components based on their boiling points. Due to the similarities in their manufacturing processes, pressure vessels and columns are often produced by the same manufacturers.
Stainless steel and carbon steel are the two most often utilized building materials in the oil and gas industry. Other components, in addition to the external body, are required for a pressure vessel to be usable, like vessel internals and distillation trays. Such components are extremely complicated, necessitating standards that differ greatly from those required for the manufacturing of pressure vessels, which are provided by specialized vendors.
This type of pressure tank is used for processes such as chemical reactions, which result in significant transformations of the contents within the container. These operations might involve combining substances to create a new product, breaking down a product into one or more new products, or removing components from an existing product to produce a different item. In the chemical industry, various types of pressure vessels are often utilized simultaneously to achieve these processes.
Pressure tanks are essential in the energy sector for several reasons. They play a crucial role in managing hazardous gases, which are often stored in facilities such as oil refineries and metal works. Additionally, nuclear power plants employ specialized pressure vessels known as Reactor Pressure Vessels (RPVs). These large cylindrical steel containers house the reactor core, steam, and cooling water. RPVs must be extremely reliable to withstand high temperatures, pressures, and neutron irradiation, making them a critical component in a nuclear power plant. It is important to note, however, that not all power reactors use reactor pressure vessels.
Pressure tanks are utilized across a range of industrial applications, including nuclear reactors and mining operations. They also play a role in everyday processes such as heating water and distillation. These tanks are essential for safely storing liquid gases and are crucial for handling and transporting volatile chemicals like propane, ammonia, and LPG.
In water distribution systems, pressure tanks provide notable benefits, including extending pump lifespan and reducing hydraulic shocks when the pump is activated. As water is pumped into the tank, it compresses the air inside, which helps manage pressure more efficiently and protects the system from sudden pressure changes.
Elastic Deformation - Elastic buckling or instability is influenced by factors such as the vessel's shape, stiffness, and material properties. These factors collectively determine the vessel's resistance to buckling under applied loads.
Brittle Fracture - Brittle fractures can occur at low or moderate temperatures and are often observed in vessels made of low carbon steel. These fractures may be detected during hydrotesting in the 40° – 50°F range, especially where minor flaws are present.
Excessive Plastic Deformation - To prevent excessive plastic deformation and gradual collapse, the ASME's main and secondary stress limits are established. These limits ensure that the vessel maintains its structural integrity under operating conditions.
Stress Rupture - This phenomenon involves progressive fracture due to creep deformation, which is a time-dependent process, or fatigue resulting from cyclic loading. Creep and fatigue are distinct but can both lead to stress rupture in pressure vessels.
Plastic Instability - Also known as "incremental collapse," this phenomenon occurs due to cumulative cyclic strain or deformation. It leads to vessel instability caused by plastic deformation over time.
Stress Corrosion - Chlorides can induce stress corrosion cracking in stainless steels, whereas caustic environments may cause stress corrosion in carbon steels. Selecting the appropriate materials is crucial for preventing these issues.
High Strain - Low cyclic fatigue, often influenced by strain, is typically observed in materials with low strength and high ductility.
Despite these drawbacks, the benefits of using pressure tanks far outweigh the potential issues.
Pressure vessel closures are pressure-retaining devices that allow easy access to pipelines, pressure vessels, pig traps, filters, and filtration systems. Pressure vessel closures often enable maintenance staff access. An elliptical access hole form is typically utilized, allowing the closure to be inserted through the opening and twisted into the working position, and is kept in place by an outer bar secured by a central bolt. Internal pressure prevents it from being opened accidentally while under load.
Pressure tanks are vessels that are used to store or convey gasses, vapors, and fluids at pressures greater than atmospheric pressure, also known as high pressures. They come from pressure vessels which are sealed containers that store the same contents. Steel and stainless steel are the ideal materials for pressure tanks. Material selection, design industry standard, and pressure tests conducted are to be considered when choosing a pressure tank. Several various types of tanks may be considered as pressure tanks. These examples are hot water tanks, ammonia tanks, steam drums, process tanks, and refractory lined vessels.
Pressure vessels are enclosed containers used to hold liquids, vapors, and gases at a pressure significantly higher or lower than the ambient pressure. They are widely used in various industries such as...
Stainless steel tanks are widely used in food, beverage, dairy, medicine, cosmetics, and other manufacturing processes where cleanliness and purity are important. These are also used in industrial plants for storing chemicals and gases where strong resistance from chemical degradation is required...