Fasteners
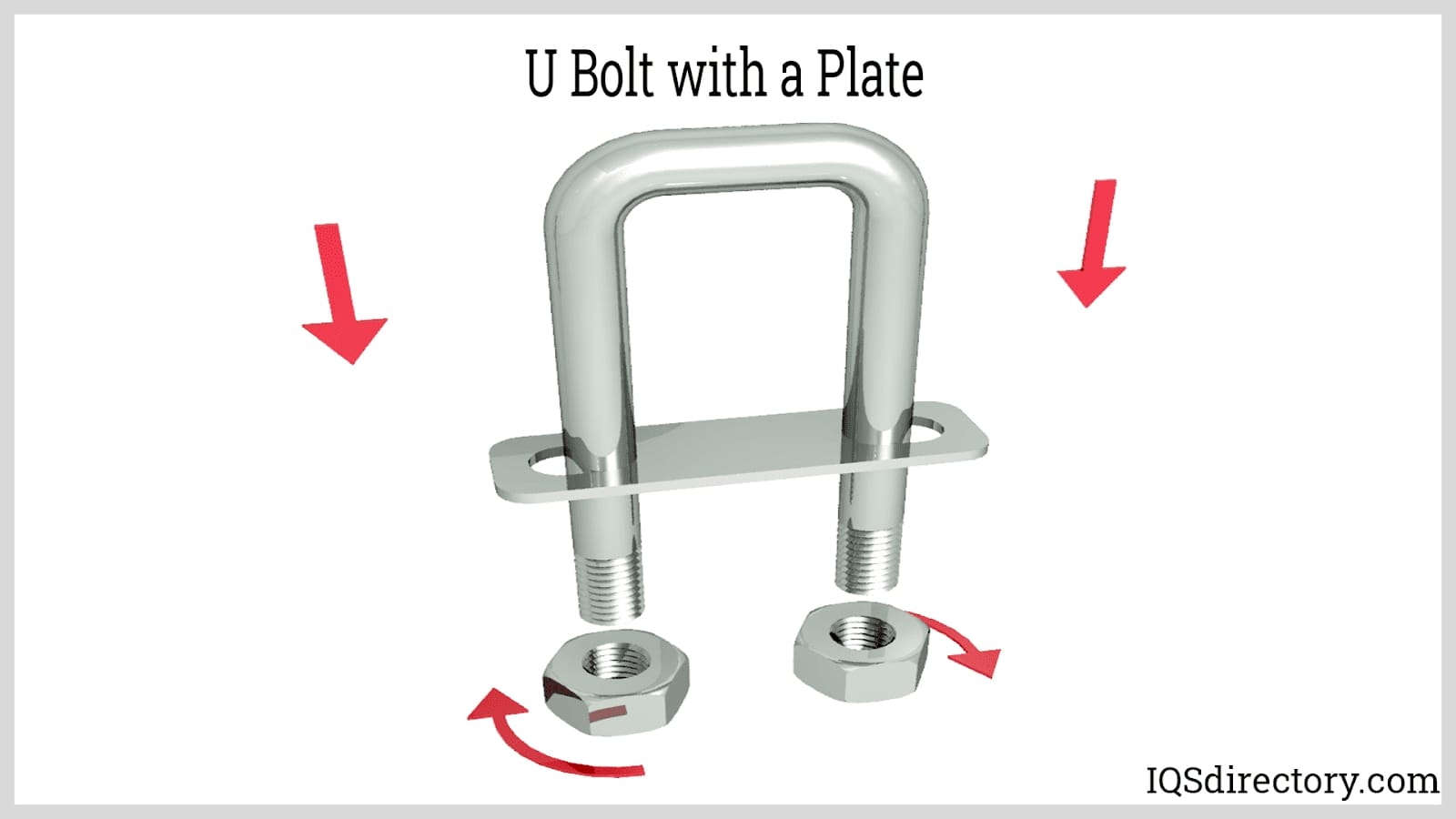
A fastener is a non-permanent or permanent mechanical tool that rigidly connects or affixes two surfaces or objects together. Non-permanent fasteners can easily be removed without damaging the joined materials...
Please fill out the following form to submit a Request for Quote to any of the following companies listed on
This article will take an in-depth look at quick disconnect couplings and their function.
The article will bring more detail on topics such as:
This introductory chapter delves into the concept of couplings and their significance across multiple industries.
Quick disconnect couplings, often referred to as quick connect or quick release fittings, are specially designed to facilitate the effortless and swift connection and disconnection of air and fluid pipelines. Unlike conventional fittings that necessitate tools for assembly or disassembly, these couplings eliminate the need for tools, offering a user-friendly solution for various applications.
Couplings predominantly play the role of linking two rotating pieces of equipment, allowing for a degree of flexibility or misalignment between them.
Couplings are integral to machinery and systems, serving several purposes. Their chief role is to transmit power between components. Additionally, couplings embody many other essential functions, elaborated below:
The different purposes of couplings will be expanded upon below.
Couplings primarily function to convey power and torque between two interconnected components or fluid lines.
Couplings help absorb shocks and reduce vibrations between components, lessening wear and prolonging the machinery's operational life.
Misalignments can arise from initial setup errors or progressive changes. Most couplings are equipped to handle various misalignment types such as angular, axial, or parallel.
Couplings can act as a barrier to heat flow between connected components, safeguarding the driven machinery when the prime mover generates excess heat during operation.
Couplings are essentially classified into rigid and flexible categories, which will be described in the following sections.
Rigid couplings are ideal for circumstances where components are perfectly aligned, with no room for misalignment. They do not compensate for misalignment, so precise lateral and angular alignment is necessary. Their uses are more limited compared to flexible couplings.
Without the ability to adjust for misalignment, rigid couplings are suitable for settings with accurately aligned shafts, as misalignment can result in heightened stresses and loads on bearings. They are best for applications involving vertical drivers.
Commonly used to transmit driving torque between a prime mover and a rotating part, flexible couplings can endure some misalignment, though relying solely on them for misalignment correction is generally inadvisable.
The flexible coupling efficiently manages temperature variances between connected components and allows axial shaft movements without interference, all while ensuring power is transmitted from the driver to the rotating element.
Flexible couplings find applications in two primary sectors: the miniature sector, containing couplings for office equipment, servomechanisms, precision tools, and light machinery; and the industrial sector, which includes couplings used in fields like petrochemicals, steel production, off-road vehicles, utilities, and heavy machinery.
This part will cover fittings, quick-connect couplings, and quick-disconnect connectors.
A fitting is a component used at the ends of pipes to regulate flow, alter its direction, or modify the pipe's diameter.
The different types of fittings are:
These fittings are designed to convert the end of a non-threaded pipe to either female or male threads as needed. They are commonly used in plastic and copper plumbing systems.
Caps are used to seal the end of a pipe that does not have an outlet. They are either welded or fitted onto the pipe end, ensuring a tight seal for gases or liquids. Caps come in materials such as carbon steel, stainless steel, aluminum, and malleable iron.
Copper tubing fittings typically use compression fittings. Examples include couplings, tees, and ells.
Couplings are used to connect two straight sections of pipe with the same diameter. They can also be used to attach a pipe to another device. Half couplings fit onto one pipe piece, with the other side serving as a branch connection to a same-size or larger pipe. Full couplings connect two pipe segments directly. Available materials include malleable iron, aluminum, carbon steel, and stainless steel.
Elbows are fittings designed to change the direction or angle of a pipe, commonly at 45-degree or 90-degree angles. The sweep of the fitting describes the speed of the transition or directional change.
Hex bushings are used to reduce the diameter of a pipe fitting abruptly, unlike reducers which create a gradual change. They decrease the diameter of female threads from a larger size to a smaller one. These threaded fittings have female threads inside and male threads outside, and are tightened using a hex head.
Nipples are short pipe segments with threads on both ends. The male threads on each end allow them to connect to other fittings. The stated length of a pipe nipple includes the threaded sections.
Plugs are used to seal the end of a pipe fitting, typically for cleanout or inspection purposes. They are inserted into threaded pipe fittings to close off pneumatic or hydraulic systems. Unlike caps that cover the outside, plugs fit inside the fitting and are often used in systems requiring maintenance or draining of gases and fluids. They come in forged steel, malleable iron, or cast or forged stainless steel.
PVC fittings are available in various configurations and can be either glued or threaded.
Reducers connect pipes of differing diameters by gradually changing the pipe's diameter from larger to smaller. This gradual change helps meet flow requirements or adapt to existing pipes. The reduction length is generally equal to the average diameter of the larger and smaller pipes. Eccentric reducers are used to maintain a level pipe bottom or top, while concentric reducers are more common.
Street elbows feature one end with female threads and the other end with male threads. They are commonly used with galvanized steel and copper pipes, eliminating the need for a nipple. Their compact design makes them suitable for tight spaces.
Tee fittings are shaped like the letter T and allow for branch lines with two outlets positioned 90 degrees to the mainline connection. They are frequently used in piping systems and are available in various materials.
These fittings are used to connect pipe segments in situations where the pipes cannot be rotated or when equipment needs to be removed for maintenance or replacement. A pipe union consists of three parts: a male end, a female end, and a nut. The nut applies pressure to seal the connection, bringing the male and female ends together. This design allows for the disassembly of the fitting without affecting the connected pipes.
Valves are mechanisms used to manage the flow of gases or liquids within or from a pipe. They control and direct the flow by varying the degree to which the valve is open or closed. Valves serve various functions and are constructed from different materials depending on their industrial applications.
These are versatile couplings that can be attached at either end of a connection. Quick couplings are designed for easy connection and disconnection, offering compact yet durable performance. They are highly dependable and consistently perform well in transferring fluids across hydraulic, pneumatic, and vacuum systems.
The couplings on the side of the flow consist of a floating ball valve that automatically closes when the couplings are disconnected. This prevents the spillage of fluid from the system. Their design is generally according to the maximum working pressure. Quick couplings can be made from brass, steel, or stainless steel, depending on the type of fluid and application. The major fluids that are applicable are oil and water.
Over time, quick couplings may become less responsive and may develop rust due to the characteristics of the transferred fluid. Therefore, it is important to handle them with care when removing them from a pressurized system.
There are different types of quick couplings which are:
This double-end shut-off coupling is commonly employed in high-pressure applications, including water, hydraulic, and compressed air systems. It is crafted from specially annealed steel to ensure enhanced reliability and strength. When disconnected, the internal valve seals both the plugs and sockets. The typical operating pressure is around 210 bars, with a maximum pressure rating of approximately 215 bars.
The double-end shut-off coupling is designed to simultaneously and instantly close both the plug and socket when disconnected. These couplings can be constructed from materials such as steel, stainless steel, or brass, and are available in various pressure ranges, sizes, and for different fluid applications. They are commonly used in standard pressure settings, with a typical working pressure of up to 100 bars and a normal operating pressure of around 20 bars.
This double-end shut-off coupling is specifically designed for high-pressure hydraulic oil applications. It features a ring lock mechanism to protect against vibration and shock, ensuring high reliability and leak prevention. The usual operating pressure is around 700 bars, while the maximum pressure can reach up to 2500 bars.
Line couplings are utilized to connect multiple couplings in a single line simultaneously. They are commonly employed in hydraulic couplings for cylinder heads in main engines.
This type of coupling shuts off only one side, usually the socket side, which is the male part, effectively preventing fluid leakage. Single-end shut-off couplings are designed for low-pressure applications and are commonly used with water, oil, and air, handling pressures up to 20 bars. They feature a ball float mechanism that closes the flow when disconnected. Available in various sizes to suit different applications, single-end shut-off couplings come in several types:
These types of couplings are used to provide easy and fast connection and disconnection of fluid lines. They are often referred to as QCDC i.e quick connect disconnect. These fittings are also called quick connects or quick release couplings. Typically, the operation of these couplings is done by hand. They are often used to replace fitting connections that require tools to assemble and disassemble.
Quick disconnect fittings come in various types and are widely used across different industries. They enhance user convenience by making connections and disconnections easier while minimizing fluid leakage. However, due to the complexity of their components, these fittings often result in higher pressure drops compared to simpler designs.
The various types of quick disconnects are:
Commonly referred to as the ball-latching quick connect, this is the most widely used type. It features a spring-loaded ball-latching mechanism that automatically secures the two halves when they are joined. Pulling back the releasing sleeve allows for instant disengagement of the inner and outer ends. This design is particularly suited for applications requiring frequent connections and disconnections due to its user-friendly quick-release functionality.
Dry break quick disconnects are used when a higher level of sealing is required compared to double-end shut-off couplings. They ensure that shut-off valves on both internal and external ends are completely closed before disconnection. Often referred to as no-spill disconnects, they feature a dead volume design that prevents the release of trapped fluids.
Non-latching quick disconnects are ideal for situations requiring rapid service in tight spaces. They are particularly useful when:
Non-latching quick disconnects are designed with self-sealing valves that automatically contain the fluid upon disconnection.
These couplings are specifically designed for use with air, particularly for connecting air compressors to pneumatic tools. While air quick couplings are of high quality, the seals are generally not as tight or as quick as those in other couplings, due to the lower risk of air spillage.
These couplings use balls to secure flow lines together. When an operator presses a button, the balls, located on either or both the male and female parts, retract and connect the two halves. Once the balls are properly positioned, the operator can release the button, and the halves will lock into place.
These couplings are typically employed for transferring hazardous materials. They remain open during normal operations but close rapidly under excessive force, reducing product loss and enhancing safety.
Commonly known as cam and groove hose couplings, these are primarily used with petroleum and chemical transfer lines. They consist of a male adaptor and a male coupler. The connection is made through the cam arms of the coupler and the grooves on the adaptor, forming a robust gasket seal.
These couplings employ two seals to isolate the liquid on both sides, trapping only a minimal amount of fluid between the valves. They also eliminate the need for draining or collecting spilled product from the lines before disconnecting the coupling.
These disconnect couplings feature a mechanical internal lock with a device designed to prevent accidental openings and releases. To disconnect the coupler from the pipe or hose, the valves in both the female and male halves close and seal with matching discs. They provide a drip-free connection, making them suitable for handling hazardous materials.
These specialized disconnect couplings are designed for efficient connection and disconnection of hydraulic fluid lines, ensuring that the fluid pressure is maintained and no air is introduced into the system.
These disconnects are the most basic and cost-effective type. They use a ball-bearing sleeve lock to connect the male and female components.
These quick disconnects are ideal for applications where only minimal spillage is allowed, as they seal off the liquid supply using a single seal.
These couplings are designed to prevent any fluid loss and block air from entering a poppet valve system.
These couplings are used to minimize spillage in hazardous chemical applications. They feature seals that are flush with the exposed ends of the female and male halves, leaving space to accommodate potential dirt and bacteria.
Other couplings that have capabilities of quick couplings are:
Bellows couplings have twin coupling ends called hubs. Bellows couplings are popular due to their remarkable torsional rigidity for the accurate transmission of velocity, torque, and angular position. Their slight flexibility functions to address amounts of angular, axial, and parallel misalignment that is limited between the shafts or other joined components.
These couplings are generally crafted from hydroformed stainless steel tubes that create deep corrugations. The process begins with a stainless steel sheet or another metal, which is formed into a tube. This tube is then pressurized against a ribbed die to produce a corrugated shape. Finally, end hubs are welded to these coupling bellows.
Bush couplings are mainly used as flexible connectors in situations that demand dependable link transfer under harsh operating conditions. They consist of two hubs made from different materials, with pins designed to attach rubber bushes.
These couplings are highly flexible and dependable, making them ideal for hoisting applications. They use bolts known as pins, with rubber or leather bushes mounted on top. The two parts of the coupling are constructed differently, with a 5mm gap between their faces. There is no rigid connection between the halves; instead, drive is transmitted through the leather bushes or compressed rubber.
A beam coupling features a flexible material shaped with a helical pattern along its length. Unlike rigid couplings, beam couplings can accommodate angular misalignment, axial motion, and parallel offsets between shafts. They have a one-piece construction, which helps prevent backlash commonly seen in multi-part couplings. Available in various materials such as acetal and titanium, they are most commonly made from aluminum and stainless steel. While stainless steel offers enhanced strength and torsional stiffness, it is also heavier, which affects its responsiveness.
This type of coupling features at least one metallic diaphragm attached around the outer diameter of the drive flange. It transfers torque radially through the diaphragm to an attachment on the inner diameter.
Disk coupling is another type of metallic membrane coupling. In this design, one or more plates or diaphragms serve as the flexible components. Torque is transmitted from the outer diameter of a flexible plate to the inner diameter across a spool or spacer piece, and vice versa. Diaphragm couplings accommodate parallel, angular, and significant axial misalignments, and are capable of handling high torque, making them suitable for high-speed applications.
This coupling transmits torque between a driving and a driven bolt or shaft that share a common bolt circle and work tangentially. Torque is conveyed through a stack of thin, stainless steel discs. Misalignment is accommodated by deforming the material between the bolts.
This type of coupling is designed to transmit torque while accommodating shaft misalignment. It remains flexible yet strong under high torque loads. Disc couplings can typically handle speeds of up to 10,000 r/min.
There are two variations of disc couplings: single disc style and double disc style. Single disc style couplings consist of two hubs and a single flat stainless steel disc spring. Double disc style couplings also have two hubs but include a center spacer that sandwiches two disc springs. The center spacer is usually made from the same material as the hubs, but it can also be made from insulating acetal, which provides electrical isolation.
These couplings connect rotating shafts using flanges. Each shaft has a fixed flange at its end, and the two flanges are bolted together with a ring of bolts to complete the drive. The flange coupling joins two tubes, with one side of the coupling being keyed to attach securely to the flanged end, allowing it to connect with the opposing flanged tube end.
Each flange is designed with either a male or female coupler opening so that when the two ends are joined, they align smoothly without any resistance or interference with the material passing through them.
Flange couplings are used in pressurized piping systems to connect two pipe or tubing ends. They typically create strong connections using high thread count nuts and bolts to secure the flanges. These bolts and nuts are usually made from tempered steel or alloys to provide durability and allow for tight fastening, ensuring a leak-proof flanged junction. Most flange couplings use four, six, or up to twelve bolt assemblies.
These couplings are designed to transmit torque between two non-collinear shafts. They generally consist of two flexible joints, each attached to one of the shafts, and are connected by a spindle or a third shaft. Gear couplings are often used to link a drive motor to a gearbox in hoist mechanisms, but they can also connect the gearbox directly to smaller wire rope drums via a flanged half.
Gear couplings are designed to transmit torque through hubs with crowned gear teeth that mesh continuously with the straight gear teeth of the sleeves. This design allows for maximum torque transmission in a compact size. They operate at very high speeds and adhere to the AGMA bolting pattern, while also accommodating radial, angular, and axial shaft misalignment.
Grid couplings, like disc and gear couplings, are engineered for high torque density applications. They comprise two shaft hubs, a horizontally split cover kit, and a serpentine grid. Grid couplings are particularly well-suited for applications involving shock loading.
Torque is transmitted between the shaft hubs via the grid element, which absorbs and dissipates shock loads. This helps to reduce the impact on connected equipment. With proper installation, lubrication, and maintenance, grid couplings can provide years of dependable service.
Grid couplings are versatile and feature interchangeable components, which are readily available from major coupling manufacturers. They offer high power density, are relatively easy to install, and withstand various environmental conditions. Grid couplings are available for both inch and metric bores.
Jaw couplings are commonly used in motion control applications. They are designed to transmit torque while absorbing system vibrations and accommodating misalignment, thereby protecting other components from damage.
Jaw couplings are composed of three components: two metallic hubs and an elastomer insert, often referred to as a spider. The hubs each feature jaws that alternate with the lobes of the spider, which are press-fitted together. Torque transmission in a jaw coupling occurs through the compression of the elastomer lobes.
Oldham couplings consist of three components: two lightweight hubs made from corrosion-resistant stainless steel or aluminum, and a central disk. They are commonly used in servo-driven mechanisms that require low inertia and precise motion control.
The Oldham coupling is a flexible coupling designed for applications requiring backlash-free operation. It consists of three discs: two are attached to either side of the drive, while the third, made from various plastics, is sandwiched in between using a tongue-and-groove design. The tongues and grooves on either side are oriented perpendicularly to each other.
To reduce the coupling’s backlash, springs are often used. During operation, the center disk slides on the tongues or tenons of each bulb for transmitting torque. While a small amount of angular and axial misalignment is accommodated by the couplings, they are especially useful in applications that involve parallel misalignment.
Oldham couplings offer electrical isolation due to their plastic center disk. They can also act as a protective fuse for machinery. If the torque exceeds the coupling's limits, the center disk will break to stop torque transmission and prevent damage to more expensive machine components.
This coupling is a mechanical device featuring a double-strand roller chain and two modified sprockets. Its design is both simple and effective, despite its compact size. The robust chain and specially hardened-tooth sprockets enable the transmission of high torque levels.
Roller chain couplings are both compact and flexible. Their design ensures that torque is evenly distributed across the roller chain and sprocket teeth during operation. While these couplings do not require precise shaft alignment to function, achieving perfect alignment is strongly recommended for optimal performance.
Often referred to as quick-connect couplers, these couplings are versatile and can be connected at either end. They are designed for ease of connection and disconnection, offering both compactness and durability. Quick couplings are highly reliable and provide consistent performance in transferring fluids across hydraulic, pneumatic, and vacuum systems.
The couplings feature a floating ball valve on the flow side that automatically seals when the couplings are disconnected, preventing fluid spillage. Their design typically adheres to the maximum working pressure requirements. Quick couplings can be constructed from materials such as brass, steel, or stainless steel, based on the fluid type and application. They are commonly used for fluids like oil and water.
Over time, quick couplings may become sluggish and potentially rust due to the transferred fluid's nature. Therefore, it's crucial to handle them carefully when removing them from a pressurized system.
Sleeve or muff couplings are fundamental coupling types, consisting of a pipe with an internal bore machined to precise tolerances for the shaft size. A keyway is incorporated into the bore to facilitate torque transmission through the key, based on the coupling's intended use.
To secure the coupling in place, two threaded holes are included. Sleeve couplings, also known as box couplings, involve connecting and aligning the ends of shafts, which are enclosed by the sleeve or muff. The shafts and sleeve are fastened together using gib head sunk keys.
Sleeve couplings are used for transmitting light to medium torques and represent the simplest form of shaft coupling. They consist of a thick, hollow cylindrical tube, referred to as a sleeve or muff, with an inner diameter matching that of the shaft. The sleeve transmits torque between the shafts.
This coupling, also referred to as a compression or clamp coupling, is classified as a rigid coupling. It consists of a sleeve divided into two halves, typically made from cast iron. The halves are secured together with bolts and nuts, or mild steel studs.
In this type of coupling, one half of the muff is positioned below, while the other half is placed above. The clamping of the two halves is accomplished using either four or eight bolts, which are inserted into recesses within the sleeve halves. An advantage of this design is that it does not require repositioning of the shafts for assembly or disassembly. This coupling is suitable for heavy-duty applications and moderate speeds.
These couplings are known for their torsional softness, featuring a flexible design that accommodates misalignment and shields other components in the transmission system. Tire couplings, which exhibit high flexibility and lack torsional backlash, are often used in machines with non-uniform torque due to their low torsional stiffness and damping properties.
Tyre couplings are ideal for connecting machines with significant shaft misalignment. The elastic tire can be easily slipped over the hub components, and a clamping ring is employed to secure the coupling in position.
The connection transmits torque through frictional engagement. Standard tire coupling designs often feature shaft-to-shaft connections, but custom designs for specific applications can be requested. Couplings can be fitted with tires made from natural rubber or chloroprene rubber.
Natural rubber tires can operate in ambient temperatures ranging from -50°C to +50°C, while chloroprene rubber tires are suitable for temperatures from -15°C to +70°C. Chloroprene rubber tires are also marked FRAS (fire-resistant and antistatic). These couplings help reduce the transmission of vibration and shock loads.
These types of couplings connect two components whose axes intersect at a small angle. While there may be constant bending of the components, the actual angle changes during the transfer of torque from one component to the other.
Universal couplings are commonly used to transmit torque from the gearbox to the differential or rear axle in automobiles. Typically, a hook-type coupling is employed for this purpose. One end connects to the gearbox and the other to the differential on each end of the propeller shaft. Additionally, universal couplings are used to transmit power in various drilling machines' spindles and are utilized as knee joints in milling machines.
There are different types of quick couplings which are:
The double end shut off coupling can simultaneously and instantaneously shut off both the plug and the socket upon disconnection. These couplings can be made from materials such as steel, stainless steel, or brass, and are available in various pressure ranges, sizes, and fluid applications. They are commonly used in applications with standard pressure, typically having a normal working pressure of 20 bars and a maximum working pressure of up to 100 bars.
This type of double end shut off coupling is designed for high-pressure applications, such as those involving water, hydraulic systems, and compressed air. These couplings are made from special annealed steel to ensure higher reliability and strength. Upon disconnection, the inner valve closes off both the plug and the socket. They typically have a normal working pressure of 210 bars and a maximum working pressure of 215 bars.
This type of double end shut off coupling is specifically designed for high-pressure hydraulic oil applications. It features a ring lock device that protects against vibration and shock, enhancing reliability and minimizing leakage. The normal working pressure for these couplings is typically 700 bars, while the maximum working pressure can reach up to 2500 bars.
Line couplings are designed to connect multiple couplings in a single line simultaneously. They are commonly used in hydraulic systems, such as those found in cylinder heads of main engines.
This type of coupling only shuts off one side, typically the socket side, preventing fluid leakage. Single end shut-off couplings are low-pressure couplings used for water, oil, and air applications with pressures up to 20 bars. They feature a ball float that seals the flow when disconnected.
Single end shut-off couplings are available in various sizes depending on the application. Types of single end shut-off couplings include:
This chapter will explore the various applications and benefits of quick couplings.
The applications of quick couplings are:
The various benefits of some of the quick couplings discussed in the preceding sections are:
These benefits can be categorized into the following category of benefits which are:
Quick disconnects are often designed with advanced non-spillage features that enhance system performance by minimizing fluid leakage. This helps to safeguard against exposure to hazardous fumes and chemicals.
Inclusion refers to the introduction of air into the system during the process of disconnecting the coupling. Generally, most couplings allow for a maximum inclusion of 2ml when they are being disconnected and then reconnected.
Quick couplings are engineered for rapid and effortless connection and disconnection, which helps in reducing equipment downtime.
Quick disconnects can be engineered to prevent unintended separations, ensuring both optimal performance and safety of the equipment.
Quick disconnect couplings are fittings used to provide air and fluid lines’ connection and disconnection easily and fast. They are sometimes known as quick release or quick connect couplings. These quick disconnect couplings are used in place of fitting connections which would typically need tools to be assembled or disassembled. Therefore when choosing a coupling for a certain application, consider the coupling capabilities and the type of material that it is made of.
A fastener is a non-permanent or permanent mechanical tool that rigidly connects or affixes two surfaces or objects together. Non-permanent fasteners can easily be removed without damaging the joined materials...
Nylon tubing, also known as polyamide tubing, is a type of tubing made from polyamide resin, which has a strong resistance to abrasion. It is used in high-pressure and high-temperature applications...
Plastic tubing is a form of tubing that is manufactured from a mixture of a polymer with a variety of chemicals to form a material that can be solid or flexible. Since its first use in the 1950‘s, plastic tubing has revolutionized industrial processes and has found a use in a wide variety of applications...
Poly tubing is a highly flexible, lightweight, and durable tubing that is produced from polyethylene, a polymer that is made from the polymerization of ethylene. It is a very versatile form of tubing that has break and crack resistant walls...
PVC is a tough chemically resistant synthetic polymer of vinyl chloride used especially for making pipes, films and electrical insulation. It is made by polymerizing vinyl chloride, and...
Rubber tubing, also known as rubber hose or rubber piping, is made of natural and synthetic rubber and is used to circulate and transport liquids and gases for household and industrial uses. The natural or synthetic rubber materials used for the manufacture of rubber tubing...
A self-drilling screw is a type of tool that has the same design features as a drill bit or cutting tool. As the name implies, self-drilling screws do not require a pilot hole in order to perform as a fastener...
Silicone tubing is a very tough elastomer that exhibits high strength, flexibility, and resistance. Silicone tubing can be stretched without tearing and is highly versatile. It cannot be weakened with repeated bending and twisting due to...