Metal Channel
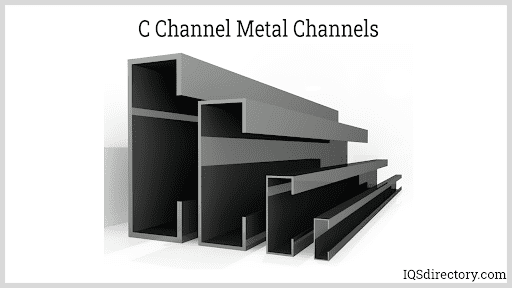
A wire brush is an abrasive tool that has stiff bristles made from a variety of rigid materials designed to clean and prepare metal surfaces. The filaments of wire brushes are small diameter pieces of inflexible material that...
Please fill out the following form to submit a Request for Quote to any of the following companies listed on Metal Moulding .
This article will take an in-depth look at metal moulding, interchangeably known as metal Moulding.
The article will bring more detail on topics such as:
In this section, we delve into the principles of metal moulding and roll forming, emphasizing mouldings crafted through roll forming methods. We will also detail the metal moulding process.
Roll forming is a technique where a flat metal sheet is progressively bent to create a consistent profile using sequentially arranged tool dies, continuing until the desired configuration is achieved.
This process enables the production of metal mouldings by systematically bending sheet metal with matched dies, resulting in long, uniform profiles.
Though roll forming may require higher initial tooling investments than other methods, it provides advantages like continuous production, suitability for medium to large volume runs, and enhanced output. The technique achieves fine tolerances and a superior finish quality. Additional tooling allows for creating intricate designs without length restrictions, as the material is continuously coiled through the setup. In high-volume manufacturing, roll forming becomes economically viable, capable of producing high-strength steels with excellent ductility while reducing labor costs through integrated fabrication.
Roll forming has limited downsides. For instance, smaller production orders can be more costly compared to other forming processes like press brake forming. Despite higher tooling costs, labor savings over time can offset these on a per-piece basis. A skilled operator must set up the roll forming line. End flare, where one component end flares outward due to linear stresses, can be mitigated through design adjustments. Roll forming is ideal for projects requiring medium to high volume, exact tolerances, and appealing aesthetics.
Metal moulding involves various methodologies for shaping metal components, including casting (such as sand and die casting), forging, and machining. The chosen method relies on specific manufacturing needs.
Metal Injection Molding represents a specialized, relatively new manufacturing technique combining fine metal powder with a polymer binder to form a feedstock. This is then injected into a mold, similar to plastic injection molding, and shaped through heat and pressure, eliminating the binder and sintering metal particles.
Metal moulding processes can use various metals like aluminum, steel, and copper, chosen based on finished part properties required.
Metal Injection Molding (MIM) typically uses powdered metals and alloys such as stainless steel, tungsten, titanium, and other high-performance materials.
Metal moulding techniques allow for varying levels of precision and complexity, as determined by the method used. Precision machining, for example, can achieve tight tolerances and intricate designs.
Metal Injection Molding (MIM) excels in producing small to medium-sized components with intricate designs and precise tolerances, ideal for complex parts with near-net shapes.
The cost and production scale vary widely across metal moulding methods, with some being more economical for mass production and others suited for lower volumes or customized components.
Due to its efficiency in producing parts with minimal waste and post-processing, Metal Injection Molding (MIM) is cost-effective for mid-to-high-volume operations, although its initial tooling costs may be higher than other metal moulding techniques.
Depending on the technique employed, metal moulding may require post-processing steps like machining, heat treatment, or surface finishing to meet the specified requirements.
Metal Injection Molding (MIM) typically needs less post-processing since parts are formed close to final specifications during molding.
This chapter will cover architectural metal mouldings and the process of creating metal mouldings through roll forming.
As described earlier, roll forming produces metal mouldings by gradually bending flat sheet metal into a long, consistent profile using large machinery and matched tool dies. The process involves uncoiling a metal coil and feeding it through a series of roll dies. Each set of dies is driven by its own gear system to ensure smooth and synchronized movement of the material through the machine, ultimately forming the metal mouldings.
Think of these paired dies like a railway wheel and track. They are designed to fit together precisely, with just enough space between them to allow the metal to pass through smoothly.
Each set of dies progressively bends the metal towards the final shape. Complex geometries require more die sets than simpler profiles. Typically, a roll forming mill will have between 10 and 30 or more pairs of roller die supports.
Bending metal in just one direction often isn't enough because it relies on force to alter the metal's flat structure. This force creates stress, which needs to be managed and relieved throughout the entire workpiece. To achieve this, additional techniques such as twisting or curling are used. The force must be applied gradually and controlled to "massage" the metal into its final shape during roll forming. This careful process allows the metal to adapt almost perfectly to its new form by managing the direction in which stresses are released.
After passing through the forming dies, the metal is cut into distinct pieces using one of two methods. It may go through a cutoff mechanism designed specifically for the final moulding profile, ensuring precise measurements and clean ends. If no dedicated cutoff mechanism is used, the metal is roughly pinched or crushed. After cutting, the moulding undergoes a deburring process to smooth and secure the edges.
Once finished, the moulding is placed onto a run-out table, where it is prepared for safe packaging and storage or shipping.
In a drawbench machine, an uncoiler and roll die sets are still used, but they lack individual power sources. Instead, a large clamp connected to a chain drive grips the leading edge of the metal ribbon. This clamp pulls the metal through the roll dies, moving it away from the coil as the chain drive operates. Once the material runs out, the chain drive stops, and the finished product is cut using a hacksaw or large metal snips. For each required length of moulding, the clamp is reset, and the process is repeated.
Modern drawbench tool sets are relatively basic, typically featuring 4-8 sets of rolling dies. This results in rapid application of forming stresses, often causing the finished product to emerge twisted or bent. To address this, a machine called a stretcher is used. The stretcher applies opposing forces to the moulding, reducing stress and restoring it to its original straightness.
There are five primary categories of decorative metal moulding used to reinforce and coat other metals. These include rusted steel moulding, sublimation moulding techniques, bronze and copper moulding methods, galvanized steel, and stainless steel.
Rusted steel is a relatively recent metal moulding technique popularized by designers seeking unique aesthetics. The goal is to create an appealing, high-class look by deliberately accelerating the rusting process of the metal. This technique requires both skill and significant resources to achieve the desired decorative effect.
To rust steel, iron, or other metals, start by placing the metal in a container or bucket. Pour distilled white vinegar over the metal to ensure it is fully immersed. Alternatively, you can spray the vinegar onto the metal and leave it in a humid environment. After soaking for over an hour, drain or wipe off the vinegar. Then, apply a heated peroxide mixture to the metal. The peroxide will bubble on the surface, promoting rust formation for a decorative effect.
In this moulding method, the metal is dipped into a container of molten metal to achieve a stylish appearance. The coating material is first heated until it melts. The metal to be coated is then immersed in the molten substance and left to cool. Before the coating fully solidifies, additional designs, patterns, customizations, and branding can be applied.
Bronze and copper are popular choices for decorative metal moulding. An example is the Statue of Liberty, which features a copper coating that has turned green over time due to oxidation and moisture. In industrial applications, metals are coated with bronze or copper, and additional oxidants can be used to create appealing colors on the coating.
Galvanized steel is another type of moulding used for protection. The galvanization process involves applying a zinc coating to iron or steel to prevent rusting. This is achieved by melting the zinc into a liquid and then dipping the metal into the molten zinc bath, resulting in a smooth, protective finish on the steel or iron surface.
Stainless steel is a visually appealing and reflective metal created through decorative moulding processes applied during the purification of iron ore. Key raw materials such as nickel, chromium, silicon, and molybdenum are added incrementally to achieve the desired finish. This results in a beautifully decorated metal suitable for a wide range of applications.
When designing metal mouldings, consider the following factors:
The product's shape is the first consideration of a metal mould design. If the product is generally round, centrifugal moulding is probably the most suitable metal moulding process. However, investment casting or sand casting is the most suitable method if the part's shape is not round and its geometry has complex features like internal ribs or passageways.
Sand moulding is often more accessible than investment moulding for various sizes. However, for products weighing less than 1200 pounds (544 kg), the choice between investment moulding and sand moulding should be based on the level of detail and the overall geometry required.
Solidification modeling software enhances casting quality by simulating molten metal flow into molds and analyzing the solidification process during cooling. This tool helps ensure that the part meets specifications by aiding in the design of the mold.
This term refers to the allowable deviation from the desired dimensions of the moulding. Investment moulding typically achieves tighter tolerances compared to other metal moulding methods.
Surface finish describes the texture of the part’s exterior after metal moulding, measured by the root mean square. Typically, investment moulding produces a finer root mean square range compared to sand moulding, leading to less need for additional machining. While sand castings can be machined to achieve a smooth surface finish, this adds extra cost and lead time.
Various types of roll-formed and metal-molded parts include:
Channels are among the most commonly used and requested roll-formed metal parts.
Johnson Bros. leads the nation in producing metal channels with existing tooling for U-Channels, J-Channels, various C-Channels, and Hat Channels. They manufacture channels from materials like steel, stainless steel, and aluminum. In recent years, Johnson Bros. has developed around 250 unique U-Channels and J-Channels, with sizes ranging from 0.060" O.D. to 19" O.D.
Some U and J channels are designed with legs bent at angles other than 90°, or with uneven legs, or both. Certain U and J channels are also available with hemmed legs for added strength and without edge burrs. The most common channels are those with equal legs bent to 90°, which utilize the most frequently used tooling in standard inventory.
"Channels" encompasses a wide range of metal profiles with different shapes, but the most common types of channels are typically categorized as follows:
Metals of every kind are used to create channels, although stainless steel, steel, and aluminum are the most prevalent.
With the extensive variety of tooling designs in the industry, unconventional cross-sections and forms can be created in numerous ways. Given the widespread application of roll-formed profiles, moldings, and shapes across different fields, pinpointing a specific industry as the main user is challenging.
Johnson Bros Metal Forming boasts tooling for over 300 unique parts in this category. This includes both publicly accessible tooling and private tooling owned by clients, which may not be available for general use. Unlike channels, the tooling in this area tends to be fixed, making it rare to repurpose tooling from one part to another. However, existing tooling can be slightly adjusted, and features such as hemmed edges can be added with minimal extra cost. Their equipment generally accommodates parts up to 3" in height and 15" in width, though smaller components are also commonly produced.
Metal mouldings are generally crafted from thinner materials compared to profiles and custom shapes. Decorative metals are often employed in the creation of mouldings. While profiles can be produced from thinner metals as well, they are usually intended for structural applications. The term "Special Shapes" encompasses both metal profiles and mouldings. Although structural shapes are common, they can also be designed to be sleek and visually appealing.
Pre-punching and post-punching are commonly utilized in pre-punch presses for profiles, mouldings, and various shapes. At companies like Johnson Bros Metal Forming, the cutoff process includes precise length cutting, end fabrication, and other tasks considered part of the pre-punch procedure. Additionally, gag punching is performed during the cutoff phase to achieve tighter tolerances compared to pre-punching and to address issues such as uneven holes and fabrication irregularities. It’s important to note that the areas around pre-punched fabrications may experience stretching during the roll forming process, potentially leading to distortions.
Post-punching is primarily employed to prevent distortion, but pre-punching is often used when post-punching cannot achieve the desired fabrication or becomes prohibitively expensive. Pre-punching, alongside gag punching, supports a variety of fabrications and patterns. Johnson Bros Metal Forming handles lengths ranging from 4 to 40 feet (1.2 to 12.2 meters). Their advanced flying pre- and post-press operations utilize servo-driven accelerators and die boosts to ensure high speed and accuracy. These technologies also enable precise cutting of very thin items, such as foil.
Multiple pre- or post-presses may be used, and press controllers can manage a wide range of fabrications and designs with a single die. Flying die presses generally feature mechanical, hydraulic, and pneumatic systems from top manufacturers. To ensure optimal performance, roll forming equipment can be maintained through a preventative maintenance plan, and many units are equipped with DC and high-speed drive systems.
Metal angles represent the most basic type of roll-formed profiles. The tooling required for these profiles is straightforward and cost-effective to set up. Hemmed legs can be added to thinner materials using existing tooling. While most angles feature equal legs, custom options are available for L-shaped angles or those with unequal legs. Vee angles are formed with bends greater than 90°. Additionally, there are angles where the legs are more prominently exposed compared to a standard 90° bend. The most common angle bend is a 90° angle.
Johnson Brothers excels in forming angles to precise and custom lengths quickly and affordably. This is achieved using cutoff die boosters and accelerators on their hydraulic and pneumatic presses. They specialize in producing angles with unbalanced legs that can be thinner or of the same width as hot-rolled mill angles, extrusions, or angle irons, though these specific forms are not available in those traditional types. Notably, roll-formed angles feature a larger outer corner radius and a sharper inner corner radius compared to hot-rolled mill angles, which have a tighter outer corner and a broader inner corner.
Roll-formed metal tubes and tubing are designed for advanced and highly specialized applications, distinguishing them from standard, everyday tubing grades. In some cases, these tubes are produced with cost efficiency in mind, such as opting for pre-finishing rather than post-finishing. Additional examples include:
Roll-formed tubing is not meant to substitute popular types of tubing like extruded, welded seam, seamless, or drawn metal tubing. Rather, it is designed to offer cost-effective solutions or to be utilized in more economical design processes, due to its distinct nature compared to traditional tubing types.
Stiffener plates are used in steel, aluminum, and plastic materials to enhance their rigidity. These plates help increase load-bearing capacity and are commonly employed in construction. Beyond their structural benefits, stiffener plates can also serve to enhance the visual appeal of components and architectural elements.
Stiffener plates serve a distinct purpose compared to gusset plates, which are attached to beams or columns to reinforce their joints. While gusset plates focus on joint reinforcement, stiffener plates are designed to bolster the strength of beams, columns, equipment, and plastic materials, enhancing their overall structural integrity.
Headlamp bezels secure a vehicle's headlight assembly in place. This assembly includes components such as the wire harness, socket, bulb, reflector, and lens. The bezel, which encircles the headlight, ensures that the lens remains correctly positioned. Its design is tailored to match the shape of the lens, which in turn is dictated by the vehicle's overall design. Headlamp bezels are fitted on trucks, SUVs, vans, and jeeps, with each bezel custom-made to fit the specific model of the vehicle.
Headlamp bezels are manufactured from aluminum and chrome. To enhance durability and extend the life of the headlamp, these bezels are treated with various coating methods and techniques for added protection.
This tubing is commonly available in square, round, and rectangular shapes, and can also be customized into unique forms. The square and rectangular varieties are often referred to as purlins, C-channels, box channels, and cees. It is easily pre-finished and frequently pre-fabricated with features such as perforations, slots, holes, and custom lengths or end fabrications. While existing tooling covers most standard and many non-standard sizes, modifications or new equipment may be required for custom designs.
To accommodate an insert in the cutoff die, a precise aperture or gap is necessary. This ensures a clean cut, optimizing cost efficiency and eliminating the need for pre-notching.
The most common shapes for this type of tubing include round, square, and hexagonal, and they are usually pre-finished. This tubing is particularly cost-effective due to its ability to have thin walls and be pre-finished. It can be efficiently produced with various in-line processes such as perforating, embossing, cutting to length, and creating holes. The flying cutoff die is used for end fabrication, which includes:
Lock seam ends are usually cut with a slight tapered dimple to maximize production speed. This dimple results from the blade imprint as it cuts through. For high-volume production, pre-punching can be used to achieve a dimple-free cutting process, though this method is somewhat slower and more expensive. In low-volume scenarios, hand de-dimpling plugs or secondary de-dimpling processes can be employed. Additionally, secondary roll edge deburring can be used if a cleaner finish is desired compared to in-line crimp cutting, and further secondary fabrication may be applied to the tubing as needed.
While a finned seam typically denotes external flanges, a flanged seam can refer to both internal and external flanges. The seam may feature flanges or fins on one or both sides. The characteristics, tolerances, capabilities, and applications of open seam tubing also apply to this type of material. Adding flanges to the open seam tube significantly enhances its strength. Consequently, in square and rectangular forms, inward flange seams are often referred to as “strut” or “framing channels” and are commonly used in structural applications.
Finned seam and externally flanged tubing are particularly effective when a tube needs to align with the edge of another product. Customers may weld the fins together either before or after installation. This type of tubing is versatile, serving as framing, rails, tracks, guides, stiffeners, slides, and channels, among other uses, and it is also ideal for creating a refined structural or decorative edge. Flanged seam tubing is not only decorative but also lightweight and efficient for applications such as sliding curtain tracks. While tooling for standard sizes is readily available, additional tooling
Open and split seam tubes with hems need a burr-free, smooth edge for optimal performance. They are commonly used in applications such as rails, slides, or tracks where components need to slide into place. These tubes are often pre-finished or have decorative elements while maintaining their strength. Tooling for producing hems is already available for many thicknesses, especially thinner ones. These tubes offer similar clearances, characteristics, capabilities, and applications as open seam tubing.
Split seam tubing is a viable alternative when welded seam or seamless tubes could serve a similar purpose, particularly when size, thickness, and volume considerations make sourcing from welded seam or seamless tube suppliers challenging. While split seam tubing may not offer the same torque strength as welded or seamless options, enhancements in width and temper can help compensate. It remains a cost-effective choice, especially when used with pre-finished or decorative metal treatments where maximum strength is not critical.
Existing tooling for split seam tubing is readily available, particularly for round sizes. However, tooling for rectangular, square, and custom hollow profiles is less common. Split seam round tubes are used for applications such as inner compression bushings, sleeves, and curtain or drapery rods. These tubes generally require a pre-punch operation to ensure clean cuts; otherwise, they may feature dimples larger than those found on lock seam tubes. For lower production volumes, achieving clean cuts often involves the expense of new tooling.
This tubing is manufactured differently from other types. Initially, it is produced as a straight profile or moulding shape before being bent into a ring form. The edges of the moulding ring or profile are then inline-locked together to create a corrugated or flexible tube or pipe. Although this technology is relatively obscure, it has been in use for over a century, particularly for making culvert pipes. Today, it is primarily used for high-voltage applications, HVAC ducting, and other purposes. The tubing can be made from materials such as stainless steel, aluminum, copper, and galvanized steel. While heavy-duty applications may feature wall thicknesses up to 0.75", thinner wall thicknesses are more commonly used.
This chapter will explore the various applications of roll-formed metal mouldings.
Different roll-formed metal mouldings are used in a variety of applications, including:
Channels are utilized across nearly every industry, with various terms for different types, such as:
Angles find applications in a wide range of industries, commonly for framing purposes. Additional uses include:
Open seam tubes are frequently employed for:
Applications of lock joints and lock seams include:
Interlocking seams enhance strength and rigidity, making them ideal for supporting sign faces, panels, framing components, and similar structures.
Lock joints enable the assembly of long tubes into robust shelving units, storage racks, and organizers without the need for additional fasteners.
Lock seam tubes can be roll-formed into decorative fence panels, handrails, and guardrails that interlock for easy assembly.
Lock joints enable pre-finished metal strips to be assembled into architectural details, cornice work, and window or door trim without the need for welding or soldering.
Roll forming can be used to create and assemble complete frames, walls, and roofs for small buildings, sheds, workshops, and other similar structures, utilizing lock joint connections for assembly.
Interlocking metal panels are ideal for constructing durable soil retention walls that do not require mortar or poured concrete for assembly.
Durable lock joint tubing is frequently used to construct framed sign structures, poster displays, and billboards, providing rigidity and stability under wind loads.
Roll-formed metal moulding provides several advantages, making it a preferred option for a variety of applications. Key benefits include:
Roll forming is a cost-effective and efficient method for producing metal mouldings. This process enables the continuous production of long profiles with minimal waste, which helps lower material and labor costs.
Roll forming delivers consistent and precise shapes and dimensions, making it ideal for applications that require tight tolerances.
Roll forming ensures consistent and precise shapes and dimensions, making it ideal for applications that require tight tolerances.
Roll forming is a high-speed production process that facilitates the rapid manufacture of large quantities of mouldings, making it particularly advantageous for industries with high production demands.
Roll forming can process a range of metals, including steel, aluminum, copper, and stainless steel, enabling the production of mouldings with diverse material properties tailored to specific applications.
Roll-formed mouldings can be produced in long, continuous lengths, minimizing the need for joints or seams. This enhances both the aesthetic appeal and structural integrity of the final product.
After the tooling is set up, roll forming machines can consistently produce the same profile, which helps minimize downtime and reduces changeover costs.
Roll-formed metal mouldings can be finished with various surface treatments, such as painting, powder coating, or galvanizing, to improve aesthetics and provide corrosion resistance.
The continuous cold-forming process can improve the metal's mechanical properties, resulting in strong and durable mouldings that are well-suited for a variety of applications, including structural components.
Roll forming is an environmentally friendly option, generating minimal waste during production and fitting well into closed-loop recycling systems.
Roll-forming tooling is typically more cost-effective than stamping or other forming methods, especially for extended production runs.
The precision of roll forming often reduces the need for additional post-processing steps, which saves both time and resources.
The cold-forming process of roll forming exerts less stress on the material compared to hot forming, helping to preserve its properties and prevent distortion.
Using a set of matched tool dies, a flat sheet of metal is gradually bent during the roll forming process to create a longitudinal profile. The procedure is continued until a consistent shape is attained. Thus, by gradually bending flat sheet metal into long, consistent profiles using large machinery, roll forming can be used to produce metal mouldings.
Roll forming may require more expensive tooling than other forming methods; however, it offers greater in-line production, larger runs, and higher output. Roll forming uses a progressive developing sequence to produce beautiful finishes with incredibly tight tolerances. By including tooling, any shape—no matter how complex—can be produced using this process. Because the material is passed through while being coiled, there are no length constraints. Roll shaping is more cost-effective when done in high volumes. High-strength steels may be produced while maintaining ductility, allowing in-line production at a lower labor cost.
A wire brush is an abrasive tool that has stiff bristles made from a variety of rigid materials designed to clean and prepare metal surfaces. The filaments of wire brushes are small diameter pieces of inflexible material that...
Roll forming is a process that uses a set of precisely placed rollers to perform incremental bending to a continuously fed strip of metal. The rollers are mounted in sets on a consecutive stand with each roller...
Steel channels are "C"-shaped hot-rolled carbon steel built with vertical web and inside radius corners on the top and bottom horizontal flanges. Steel channels consist of a wide web and two flanges, which can...
Metal spinning is a metalworking process that transforms a blank or preformed metal sheet (which will be referred to as the workpiece) into an axially symmetrical hollow figure. It is accomplished through the lateral force applied by...
Contract manufacturing is a business model in which a company hires a contract manufacturer to produce its products or components of its products. It is a strategic action widely adopted by companies to save extensive resources and...