Bungee Cords
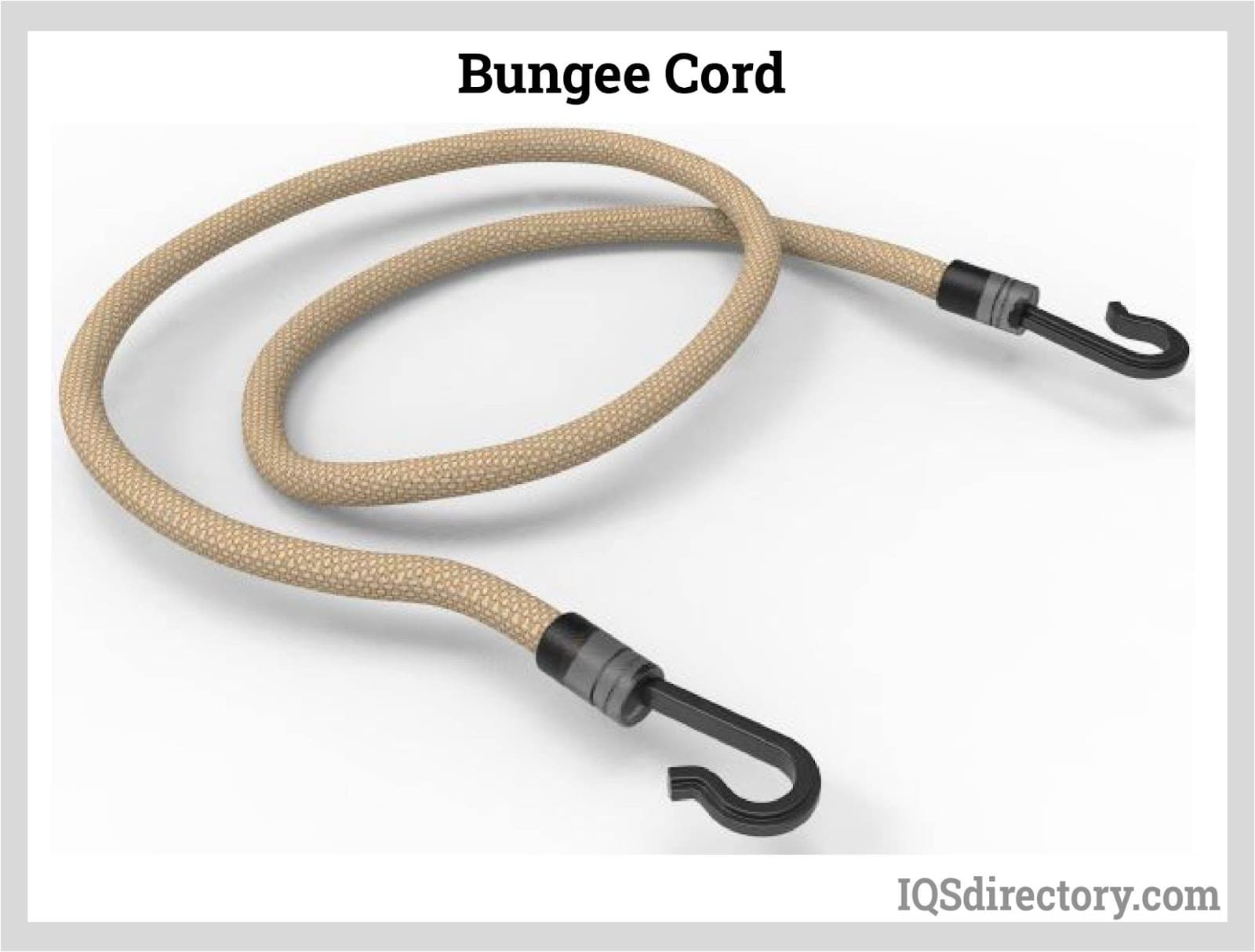
A bungee cord is a rope that is composed of two or more elastic strands coated with a woven fabric. It has hooks that are placed on both ends. A bungee cord is also known as shock cord and elastic cord...
Please fill out the following form to submit a Request for Quote to any of the following companies listed on Cordage .
Here is everything on the internet you need to know about cordage.
You will learn:
Cordage is formed by twisting or braiding together a collection of fibers, strands, strings, or fabrics to construct a more durable and powerful rope. This combination results in a final product with superior strength compared to its isolated elements. Known widely as rope, cordage has been a fundamental tool used by sailors, farmers, and cattlemen for ages. Its impressive strength and versatility make it indispensable for a variety of tasks, including securing, fastening, and moving furniture and equipment safely and efficiently.
Over the years, the design and manufacture of cordage have undergone substantial advancements. While traditional materials such as hemp, cotton, and thread were once dominant, modern synthetic fibers like nylon and polypropylene have taken their place, providing enhanced longevity and performance.
The process of manufacturing cordage and rope has evolved significantly from its traditional roots while maintaining the essential principles of rope-making. In the past, craftsmen produced rope by hand, stretching strands of material over hundreds of yards, anchoring one end to hooks, and twisting them together using a turning wheel—a labor-intensive process known as a "rope walk." This time-honored technique laid the foundation for today's advanced production methods.
With the advent of modern technology, rope manufacturing has become highly mechanized. State-of-the-art rope-making machines have replaced manual methods, allowing for high-volume production, consistent quality, and greater precision in the braiding and twisting processes. These innovations not only improve efficiency but also expand the range of industrial and commercial applications for both braided and twisted rope.
There are two primary techniques for manufacturing rope—braiding and twisting. Although braided and twisted ropes may appear similar, their structural properties, strength characteristics, and applications differ based on their unique manufacturing processes. Understanding these differences can help in selecting the ideal type of rope or cordage for various needs, from marine and climbing ropes to industrial hoist lines and utility ropes.
Braided rope is manufactured by interweaving multiple yarns or strands—ranging from as few as eight or nine up to several hundred—into a cohesive, flexible rope structure. Industries such as arboriculture, sailing, rescue, and rigging favor braided rope for its strength, smooth surface, low stretch, and resistance to kinking. There are three main forms of the braiding process used for rope fabrication:
Twisted rope, often referred to as laid rope, is produced by twisting together several strands of fiber in a helical pattern—commonly three or four strands—before twisting them around each other to form a unified rope. Twisted rope is prized for its cost-effectiveness, ease of splicing, and ability to absorb shock loads, making it popular in construction, agriculture, landscaping, general tying, and towing. Common applications include dock lines, anchor lines, and utility ropes.
The rope manufacturing process begins with the selection of fiber materials—either natural or synthetic fibers—each offering distinct advantages for different rope applications. Natural fibers such as hemp, sisal, cotton, flax, and jute are chosen for their flexibility, eco-friendliness, and ideal grip surfaces, though they generally have less tensile strength and abrasion resistance compared to synthetics. Despite these limitations, natural fiber ropes remain an excellent choice for decorative, agricultural, or traditional maritime uses.
Synthetic fibers, including nylon, polyester, polypropylene, high-performance polyethylene (HMPE), and aramid (e.g., Kevlar®), provide superior strength-to-weight ratios, high durability, excellent weather and chemical resistance, and low moisture absorption. These properties make synthetic rope the preferred solution for demanding environments such as offshore marine, climbing, rescue, firefighting, lifting, and industrial applications, where safety and performance are critical.
The initial stage of rope production involves preparing the raw fibers—cleaning, lubricating, and treating them as necessary to optimize the rope's performance characteristics. Modern rope manufacturing utilizes specialized machinery; steel-toothed combs thoroughly separate and straighten the fibers, aligning them into a uniform, continuous ribbon known as a sliver. Proper fiber preparation not only increases consistency in the finished rope but also enhances its strength, flexibility, and resistance to wear.
To increase density and prepare for the next manufacturing steps, the sliver passes through a drawing machine, where rollers compress the fibers into a denser, stronger form. The drawn fibers are then wound onto bobbins, ready for further processing. At this point, fibers may be dyed to achieve the desired rope color—especially important for custom rope, safety lines, or identification in critical operations.
The loaded bobbins are placed on a creel, where the ends of the yarn are threaded through precise holes in a metal plate. This step ensures the correct alignment and separation of individual yarns or strands. As the material progresses through the plate, it moves into a compression tube, where the braiding or twisting action takes place. The result is a rope or cord with tightly interwoven strands, optimizing strength, flexibility, and durability. This stage is crucial for producing ropes tailored to high-performance requirements, such as climbing rope, safety harness cordage, and mooring lines.
For certain types of cordage—especially in double braided and plated rope—the bobbins move next to a secondary braiding machine. Here, sophisticated braiding patterns are created using S and Z twist formations: the Z twist turns yarn to the right, while the S twist goes to the left. Skilled manufacturers ensure equal numbers of S and Z twists for optimal balance and resistance to untwisting—qualities essential in safety-critical applications like fall protection, winch ropes, or load-bearing systems.
The final rope can incorporate up to eight or more strands with balanced twists, resulting in a product that is strong, stable, and abrasion-resistant. This process delivers robust rope solutions for a wide array of sectors—from rigging and lifting in construction to marine anchoring and rescue operations—thanks to precise control over rope structure and performance.
Before rope and cordage are shipped to end-users, they undergo rigorous quality testing to ensure compliance with safety standards (such as ISO or ASTM requirements) and to verify breaking strength, flexibility, elongation, and resistance to UV, moisture, and chemicals. Modern rope manufacturers also offer a wide range of customization options—varying diameter, color, construction type, and fiber blend—to meet specific customer requirements for application-specific ropes such as marine dock lines, industrial winch lines, climbing ropes, and specialty lashing cordage.
Whether you are sourcing rope for heavy-duty industrial use, maritime applications, rescue and safety, or general utility, understanding the manufacturing methods and the unique benefits of each rope type will help you choose the best cordage solution for your needs.
The rope and cordage industry has advanced far beyond the traditional image of simple rope, offering an extensive selection of cordage products designed to meet a broad spectrum of application requirements. Today’s rope products are manufactured in an array of materials—including natural fibers like cotton and manila, as well as synthetic fibers such as nylon, polyester, polypropylene, and Kevlar—to address commercial, industrial, marine, safety, and recreational needs. Whether for lifting, towing, climbing, rigging, or general utility, understanding the differences in rope type, construction, and material properties is crucial for selecting the right cordage product.
When selecting a rope, one of the crucial factors to consider is its working load limit and tensile strength. These measures indicate how much stress—expressed as maximum load or ultimate tensile strength—the rope can endure before failing. The working load limit, often specified by manufacturers in compliance with OSHA and industry safety standards, defines the maximum weight the rope can safely and consistently support without risk of breakage or structural failure. For specialized applications such as arborist work, marine mooring, climbing, or industrial rigging, choosing cordage with the proper load-bearing rating is essential for safety, performance, and compliance.
It’s important to note that different rope fibers and rope constructions—such as twisted, braided, or plaited ropes—offer varying levels of abrasion resistance, UV resistance, stretch (elongation under load), and durability. Users should evaluate these properties based on their intended use, whether for marine environments (where rot- and mildew-resistance may be priorities), outdoor utility, or high-stress industrial projects.
Three-strand twisted rope is one of the oldest and most reliable rope designs, valued for its simplicity, strength, and flexibility. Manufactured by twisting three bundles of fibers together, it offers easy handling, quick splicing, and good shock absorption, making it a favorite for marine anchor lines, dock lines, pulleys, and general utility. Common materials include nylon, polypropylene, and manila, each bringing distinct advantages in strength, abrasion resistance, or buoyancy. For marine applications, three-strand nylon rope is highly sought after due to its superior elasticity and resistance to saltwater and UV rays.
Solid braided rope is constructed from 9, 12, or 18 strands tightly braided together using a lock stitch pattern, ensuring excellent durability and preventing unraveling even with frequent use. This construction creates a round, firm rope profile that resists kinking and holds its shape well, which is especially beneficial for applications like flag halyards, clotheslines, general purpose lanyards, and pet leashes. Solid braid ropes are available in nylon, polyester, and cotton blends, with synthetic versions offering enhanced UV and abrasion resistance for extended outdoor use.
Diamond braided rope, known for its distinctive diamond pattern, is produced by interlacing 8 to 144 strands in a circular over-and-under weave. This design is especially popular for general utility cord, boating, tying down loads, and DIY projects due to its flexibility and secure knot-holding capabilities. Diamond braid cordage can be constructed as either hollow or with a core (coreless vs. core), with core variations generally providing higher tensile strength and stability under load. Polypropylene diamond braid is often chosen for its floatability and low cost, whereas polyester or nylon versions are preferred where strength and UV resistance are critical.
Double braid rope features a braided core sheathed within a second, protective braided cover, combining strength with flexibility and abrasion resistance. This high-performance rope is commonly made from nylon or polyester and is engineered to withstand high-tension loads and repeated flexing. Double braid construction is a top choice for marine dock lines, winch lines, towing, arborist rigging, sailing sheets, and any application requiring consistent handling, strength, and durability. Its balanced combination of stretch and control makes it ideal for demanding environments where safety and reliability are non-negotiable.
When selecting cordage or rope products—whether for construction, marine, industrial safety, hauling, climbing, or recreational use—it's essential to compare various rope types for their material composition, manufacturing technique, working load, and environmental resistance. Be sure to review product specifications and safety standards to ensure the rope you choose meets all operational and regulatory requirements for your intended application. For professional consultations, technical data sheets, or specialized product recommendations, consult experienced rope suppliers or cordage manufacturers.
Originally, rope was used primarily for lifting and transporting people and materials. Its applications have since broadened to include various industrial uses. As the rope and cordage industry has evolved, organizations such as the Rope Access Trade Association (IRATA) and the Society of Professional Rope Technicians (SPRAT) have established training and certification methods for rope techniques and products.
While remote devices equipped with video cameras are commonly used for inspecting bridges and buildings, in-person inspections by technicians often yield more precise information. High-quality ropes are employed to enable inspectors to traverse surfaces and high-altitude structures safely and efficiently.
Rope serves many purposes in the construction industry. One notable use is for specialized technicians who need to access difficult-to-reach areas on a project. Using ropes to lower workers into these locations is more cost-effective and time-efficient compared to building scaffolding, and it optimizes resource use. Highly skilled professionals can safely access and work in these hard-to-reach spots quickly and effectively.
Rope has been a crucial component of rescue operations for centuries, allowing rescuers to reach otherwise inaccessible areas. Its reliability is unmatched, as it does not conduct electricity and is resistant to damage from chemicals or water. This makes rope one of the most dependable tools in the rescue worker's toolkit.
Though wire slings have become a very normal method for lifting heavy materials, it has been found that rope is just as reliable and a more economical solution to lifting operations. Rope slings have been engineered to be used with cranes, rigging, and other lifting mechanisms. They are safe, light weight, and highly reliable. Rope ensures the avoidance of injuries from snapping, recoiling, or dropping of loads from incorrect rigging.
The mining industry has relied on wire for underground operations for many years, but this often led to issues such as rusting and the formation of fishhooks and kinks, which created unsafe conditions. Ropes and cordage have since become a safer and more durable alternative to wire. Modern engineering advancements in rope design enhance visibility, longevity, and overall reliability, making them a superior choice for mining applications.
Ropes used for marine applications are specially treated to be pre-stretched, preventing elongation during use. Additionally, these ropes are designed to resist damage from fish bites, a common issue in ocean work. A major challenge in maritime environments is saltwater, which can cause significant wear and tear on materials. To combat this, marine ropes are infused with chemical treatments that enable them to endure the severe conditions of constant water exposure.
Rope serves various functions in the military, from securing gear during troop movements to assisting soldiers in navigating challenging terrain. It can be employed for crossing rivers and overcoming other obstacles. Additionally, rope has long been a crucial element in endurance training exercises during basic training.
Since the advent of ships and boats, ropes have been essential tools in maritime activities. Like ropes used in ocean work, those for boating and shipping must be crafted from materials that can endure the severe conditions of the sea. Historically, cordage has been vital for securing cargo, fastening hatches, and hoisting sails. Today, modern ropes made from synthetic materials offer the advantages of not unraveling and maintaining superior elasticity.
While modern machinery has largely replaced manual labor in agriculture, ropes remain essential for various tasks. They are used in applications such as loader wagon ropes, tedders, rakes, mowers, pulling ropes, poultry feeding systems, and feeding boxes. Unlike other fields, agriculture demands specific types of ropes tailored to each application, designed with particular tensile strength and durability in mind.
Durability and longevity are critical in industrial operations, making rope a vital tool with a range of applications. In contemporary industrial settings, rope is utilized for various purposes, including sun protection systems, ascenders for wind turbine maintenance, electrical tools, convertible top mechanisms, deep drilling, helicopter operations, pipe access systems, and component installation, among others. The range of uses is extensive, encompassing numerous applications and processes across different industries.
Parachute cord, commonly known as paracord or 550 cord, was initially designed for parachute lines. Its applications have since broadened significantly. Constructed from 32 strands woven around a seven-strand inner core, paracord features a smooth outer surface and is made from durable nylon fibers that ensure strength and longevity. Although it has been superseded by other materials in parachute design, paracord remains a key tool in the military for creating harnesses, rope bridges, and tree nets. The term "550" refers to its 550-pound tensile strength.
Rope-making dates back to ancient Egypt, where it was traditionally crafted from natural materials like plant fibers and animal parts. In contemporary times, the advent of synthetic materials has revolutionized rope production, with modern ropes being made from materials such as nylon, polypropylene, Kevlar, and Vectran.
Hemp is a natural fiber derived from the outer layer of the hemp plant. It is produced by twisting bundles of hemp fibers into yarn, which is then twisted with other yarns to create rope. Hemp rope is commonly used for bundling packages and securing a variety of items and materials. Its durability and versatility have made it a vital resource across multiple industries, including construction, sailing, communications, and shipping.
Flax material is used for making hemp rope. It is strong, durable and a fine material for ropes. Flax ropes are stronger than those of cotton and jute, and also get stronger when wet. Flax is actually a plant which grows up-to 50 to 100 cm. When this plant is mature, it produces two colored flowers, white and blue. The fiber collected from the blue flowers is the finest one, but the fiber collected from the white flower is the strongest but a coarser one. Flax fiber is also used along with wool and cotton to produce clothing. Flax rope is actually a natural one so it is soft to handle, has resistance to friction burns and can be used in a variety of applications. Flax ropes are usually used in skipping ropes, gymnasium and in theaters etc.
Cotton rope is made from cotton yarn, which is twisted or braided into rope. Cotton ropes are soft, pliable, hold knots well, and are easy to handle. Cotton ropes are stretchy and flexible as compared to other natural fibers. However, cotton rope is not very durable and strong. It also has very low corrosion and heat resistance. Cotton ropes also lose their strength in sunlight. Cotton ropes are available in their original white color, with 3 or 4 strand configurations. Size range of cotton rope ranges from 4mm to 37mm. The largest size of cotton rope is known as elephant ropes. It is used for boating, horse halters and leads, camping equipment, towing, and securing materials for shipping.
Manila rope is crafted from natural fibers derived from the abaca banana plant, a type of hemp known for its exceptional strength. This rope is highly durable, flexible, and resistant to saltwater damage. However, it tends to shrink when wet, so it is pre-soaked and dried before being sold to mitigate this issue.
Manila rope shrinks up-to 10-15% when it becomes wet therefore, if it gets wet while working, it should be dried thoroughly. Manila ropes are easy to handle and knot well. They have a poor resistance to acids and alkalis. Therefore, exposure to chemicals and water should be avoided. These ropes should be stored in a dry place to avoid any damage. Average available size of these ropes is 6mm to 50mm. Manila ropes are widely used in exercise climbing, art and craft, landscaping, outdoor decorations, swings and other farming work.
Sisal rope is produced from the fibers of the agave sisalana plant, native to Mexico. Known for its stiff and robust fibers, sisal is an ideal material for rope-making. The process of producing sisal rope involves crushing the plant’s leaves to extract the fibers, a method called decortication. Sisal rope stands out for its durability and resistance to decay, making it superior to many other natural fiber ropes.
Similar to manila rope, sisal rope is often treated with cordage oil to enhance its resistance to water and friction. Sisal is a preferred material for agricultural twines such as binder and baler twine due to its high strength, durability, stretch, dye affinity, and resistance to saltwater damage. While sisal offers excellent grip and knotting capabilities, it can be vulnerable to weather-related damage. Therefore, sisal ropes are commonly used for decorative purposes as well as in farming and gardening applications.
Jute fibers are sourced from two main types of jute plants: white and tossa. Tossa jute is known for its greater strength and silky texture compared to white jute, although white jute is more commonly used for rope-making. Jute, an edible plant with a long history as a food source in Asia, provides fibers from its outer skin and stem. These fibers are extracted through a process called retting, where the plant material is submerged in water to decompose. For industrial purposes, jute rope is treated with a specific oil known as jute batching oil.
Jute is an eco-friendly and biodegradable natural fiber that is both versatile and easily reusable. While its breaking strength is about 20% lower than that of manila rope and it has limited stretch, jute ropes are durable and resistant to heat. However, jute is susceptible to moisture and should be stored in dry conditions to prevent damage. Available in 3 and 4 strand configurations with Z and S twists, jute ropes find applications in towing, gardening, steel wire ropes, the transportation industry, and packaging.
Polypropylene is the most cost-effective among synthetic rope materials. It offers excellent insulation properties and has the advantage of floating on water. Its resistance to rot and mildew makes it highly suitable for aquatic environments. As a polymer, polypropylene is resilient against solvents, bases, and acids, with a melting point of 170°C. Polypropylene ropes are constructed from continuous filaments that are either twisted or braided into rope form.
These ropes maintain their shape even under bending or flexing conditions. Similar to nylon ropes, polypropylene ropes are resistant to rot and provide excellent abrasion resistance as well as resilience against acids, alkalis, and various chemicals. They also resist marine growth and mildew. To prolong their lifespan, it's advisable to keep polypropylene ropes out of direct sunlight when not in use. Typically yellow, these versatile ropes are employed in a variety of applications including mooring, dock lines, anchor lines, boat lines, trampolines, pool barriers, builder lines, and various household, agricultural, and industrial uses.
Polyester rope is known for its resistance to UV rays, heat, and abrasion, which contributes to its higher cost compared to other synthetic fibers. It resembles nylon in appearance and is available in fine fibers. Polyester boasts strength comparable to nylon and exhibits minimal stretch due to pre-stretching. It has a melting point of 240°C and demonstrates low creep under load.
Polyester fibers are highly resistant to chemicals, abrasion, and sunlight. They are also relatively easy to splice with materials such as nylon, stainless steel, or galvanized thimbles. Common uses for polyester rope include mooring, rigging, industrial applications, fishing nets, bolt slings, and hawser. Additionally, it is utilized in anchor lines, fenders, and fender lines.
Kevlar is renowned for its outstanding strength, stiffness, toughness, and thermal stability. A notable feature of Kevlar is its increased strength in subzero temperatures. Its minimal stretch makes it ideal for applications that demand high stability. Kevlar is commonly used in winch lines, mooring lines, and environments with extreme temperature fluctuations.
Nylon is a highly durable synthetic fiber known for its excellent elasticity and resistance to abrasion. It also offers protection against UV rays, rot, mildew, and various chemicals. Due to its robust nature, nylon rope is frequently used in applications such as towing lines, anchor lines, and pulleys. Its ability to maintain flexibility even after extensive use makes it perfect for tie-downs and knotting.
One of the notable features of nylon rope is its "memory," meaning it returns to its original shape after being stretched. This characteristic, combined with its ease of handling and elasticity, makes nylon rope a reliable choice for numerous applications. It is commonly utilized in mooring lines, towing slings, fishing, utility ropes, safety lines, and industrial slings.
HMPE, or High Modulus Polyethylene, is renowned for its remarkable strength while remaining lightweight. It offers superior flexibility and stability, making it capable of supporting substantial loads without showing signs of wear or damage. Additionally, HMPE ropes are buoyant, enhancing safety compared to other synthetic ropes. Their minimal elongation and stretching properties facilitate easy handling in critical and hazardous situations. HMPE ropes boast a strength-to-weight ratio that is 7 to 9 times greater than steel and about 3 times stronger than polyester of the same weight.
Vectran is produced from a liquid crystal polymer (LCP) and is known for its outstanding strength and rigidity, boasting a tensile strength of 26 grams per denier. This makes it five times stronger than steel and ten times stronger than aluminum. Vectran is highly resistant to abrasion, flex fatigue, and chemicals, and it maintains excellent thermal stability even under extreme temperatures and cryogenic conditions. In industrial applications, Vectran remains unaffected by radiation and microwave energy, exhibiting minimal creep and shrinkage.
Dacron rope is constructed from a blend of polypropylene and Dacron fibers, which are twisted into strands and braided together. Often called combination rope due to its dual-material composition, Dacron rope offers flexibility and exceptional resistance to fractures, heat, abrasion, and ultraviolet rays. This makes it ideal for demanding applications requiring robust and durable performance under harsh weather conditions and high impact scenarios. Common uses include sailing, climbing, fitness training, and roofing projects.
When selecting the appropriate rope for a particular task, three key factors should be considered: length, diameter, and load-bearing strength. Each type of rope is engineered to fulfill specific roles and functions. It is crucial to evaluate these factors carefully, especially in scenarios where the rope will serve as a safety harness or a tool for critical work tasks.
Each type of rope, whether made from synthetic or natural fibers, has specific metrics for breaking strength and safe working load limits. Traditionally, the strength of natural fiber ropes is benchmarked against the breaking strength of manila rope. Synthetic ropes are also compared using similar standards. To calculate the breaking strength of manila rope, you multiply its circumference by 900 lbs.
Rope strength is generally assessed using two key factors: tensile strength and working load limit. While these terms are sometimes used interchangeably, they actually represent distinct aspects of rope performance.
The diameter of a rope significantly affects its maneuverability, handling ease, and overall comfort and safety. Generally, a thicker rope is preferred for its enhanced strength and ability to distribute pressure more evenly, providing a more reliable grip. However, as the diameter increases, the rope becomes stiffer, which may pose challenges for certain applications.
To estimate the required length of rope, a traditional method involves extending four full arm lengths of rope from armpit to fingertip and multiplying this measurement by four. This age-old technique provides a reasonable approximation for many tasks. For more precise needs, especially in industrial settings, exact measurements are made using calibrated tools.
When selecting the appropriate length of rope, key considerations include the number of obstacles the rope must navigate and its flexibility. Longer ropes generally become heavier, wider in diameter, and less flexible, which can complicate their deployment. Engineers often rely on mathematical calculations to determine the optimal rope length for specific applications.
The work life of a rope is very much dependent on how it is maintained. Each type of rope and their fibers have to be treated according to their specifications and guidelines. Certain general parameters can serve as guidelines for enhancing rope usage.
Regular inspections are crucial to ensure the longevity of any tool, including ropes. Despite being a common tool, ropes require the same level of attention as any other equipment. Thoroughly inspecting ropes before use is essential for ensuring safety in various operations such as construction, military tasks, and search and rescue missions.
The working load limit of a rope should always be adhered to, as specified in the product description. Ropes should be used for straight pulls only; side or angled pulls can significantly affect their load-bearing capacity.
It is important to use hooks, links, or shackles that are compatible with the rope's fiber and size. These components must be correctly installed and match the rope's working load capacity. Mismatched or improperly aligned components can damage the rope and reduce its effectiveness.
Shock loading occurs when a load is jerked or allowed to fall freely, increasing the force on the rope and potentially exceeding its working load limit. This can cause the rope to fail under conditions that far exceed its design specifications.
Even ropes designed to resist abrasion can be damaged by rough or sharp surfaces. When a rope is used with equipment like hoists or winches, ensure that the surfaces are smooth and free from debris such as metal filings or wood chips. Equipment used for winding ropes should operate smoothly and be appropriately sized.
Exposure to temperatures above 140°F can reduce the strength of synthetic ropes by up to 50%. When ropes are wound or winched, friction can cause overheating, which further weakens their tensile strength.
Ropes are frequently used for lifting and pulling, which involves tying and bending. The strength of a rope can be significantly reduced by frequent knotting and bending. Always refer to the manufacturer's specifications to prevent excessive strength loss.
All types of ropes should be stored in a clean, dry area, shielded from direct sunlight and extreme temperatures. It's essential to keep ropes off the floor by placing them on a rack or shelf. Ensure the storage area is well-ventilated. Avoid storing ropes on concrete or dirt floors, and keep them away from chemicals to maintain their integrity.
When storing ropes, they should be coiled properly. The ideal method is to use a reel, either handheld or mounted on wheels. Proper coiling ensures that the fibers relax without undue stress and minimizes the risk of tangling. A reel helps to avoid damaging entanglements and keeps the rope in good condition.
Sharp bends can weaken a rope and potentially cause damage or failure. When incorporating components, the bending radius should be at least three times the diameter of the rope. For optimal results, the ratio of the component to the rope's diameter should be 5 to 1. Thimbles typically follow a 3 to 1 ratio.
Rope is typically shipped on reels for easy handling and protection. When removing a new rope from its reel, ensure that the reel is mounted on a pipe to allow free movement. Avoid unreeled the rope while it is lying on the ground or in a stationary position, as this can cause tangling and potential damage.
To prevent unraveling, the ends of ropes can be knotted. However, if damage occurs, you can often repair it by trimming the damaged section and sealing or re-knotting the end. If the middle of the rope is damaged, it should be taken out of service immediately. Even with repairs, the rope's tensile and load-bearing strength may be compromised.
Tools used in industrial and manufacturing settings are subject to oversight by various organizations to ensure worker safety and product quality. For ropes, key regulatory bodies include the American Society of Mechanical Engineers (ASME), the International Organization for Standardization (ISO), the American Cordage Institute, the Rope Access Trade Association (IRATA), the Society of Professional Rope Technicians (SPRAT), and the American Society for Testing and Materials (ASTM).
In 2010, the International Organization for Standardization (ISO) introduced three standards specifically for ropes.
ASME's B30.30 standard outlines the guidelines for the construction, selection, installation, attachment, testing, inspection, maintenance, repair, and replacement of wire rope, hybrid rope, and synthetic fiber rope used in lifting operations. As a subsection of B30, this standard is aimed at owners, users, employers, and manufacturers of rope products.
The ASTM standards detail the specifications for ropes used in rescue systems and the testing methods required to ensure their reliability. This includes drop tests designed to replicate the most extreme conditions that a rope might encounter during use.
The American Cordage Institute is a collective of manufacturers, producers, and suppliers focused on establishing standards for fiber ropes. It provides comprehensive guidelines on rope products, raw materials, machinery, and suppliers, aiming to ensure proper manufacturing practices and usage of fiber ropes.
The IRATA offers recommendations and guidance for the safe use of ropes, with a focus on training experts in rope practices. It provides protocols and standards for rope use in high-risk environments, such as working at heights or in hazardous conditions.
Established in the early 1990s in response to increased work at dangerous heights, the SPRAT initially focused on rescue operations. Over time, as rope use expanded into construction and manufacturing, the organization broadened its scope to cover all aspects of rope access operations. It provides standards and guidelines for companies involved in high-altitude or extreme environment work.
A bungee cord is a rope that is composed of two or more elastic strands coated with a woven fabric. It has hooks that are placed on both ends. A bungee cord is also known as shock cord and elastic cord...
Rope is a collection of strands, fibers, piles and yarns joined together to form a strong and a large structure. These strands or fibers are either twisted or braided with one another to give high tensile strength to the rope...
An aircraft cable is a style of highly durable cable that is used for aircraft flight controls and other applications and is differentiated from normal cables by its diameter, stranding, and wires, which provide...
Electric hoists are material handling equipment used for lifting, lowering, and transporting materials and products. They are powered by an electric motor and have a controller to adjust the lifting parameters...
A gantry crane is an overhead crane that has an overhead beam supported by freestanding legs and moves on wheels, a track, or rail system carrying a bridge, trolley, and hoist. Workshops, warehouses, freight yards, railroads, and shipyards use gantry cranes as their lifting solution as a variation of overhead or bridge cranes...
A jib crane is a lifting device with an arm or boom that extends off the main body of the crane to provide extra reach and has a lattice design to lower the weight added to a load. The design of jib cranes allows them to work...
An overhead crane is a type of heavy duty machinery that is capable of moving extremely heavy loads and equipment from one location to another in a safe and precise manner using the overhead space of a manufacturing facility. Due to the nature of the work they perform...
A push pull cable control is used for the transmission of multi directional precision control of mechanical motion. The many varieties of push pull cables or controls are adaptable to a wide range of applications and...
Stranded wire refers to thin bundled up wires that are compressed and covered up in insulating material. Stranded wires are more flexible thus making them very ideal for joining electronic circuit components in confined spaces where their bending...
Wire rope is a collection of metal strands that have been twisted and wound to form the shape of a helix with the purpose of supporting and lifting heavy loads and performing tasks that are too rigorous for standard wire...
A wire rope assembly is composed of wire rope and end fittings, terminals, or lanyards that are attached to various parts of the wire rope such that the assembly can be used to lift, hoist, and move loads. The various types of...
Wire rope is constructed of multiple strands of wire that are twisted and braided together to form a spiral design or helix. Once the separate wires are shaped into a solid form, they become a single wire with greater strength because...