Rubber Bushings
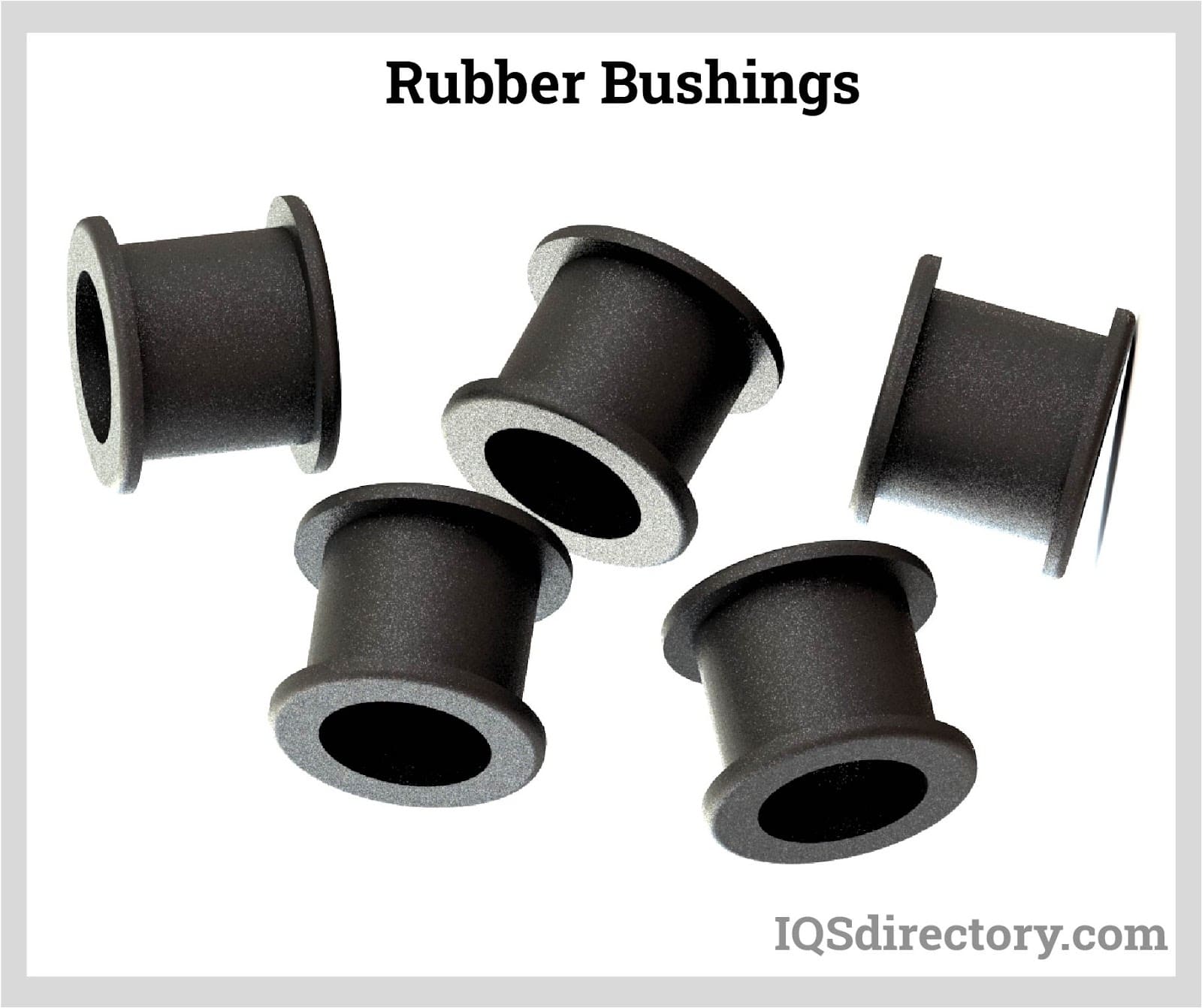
A rubber bushing is a form of vibration isolator that is placed between two parts to limit the motion between them and absorb, mollify, and buffer the energy produced by their interaction. They are very...
Please fill out the following form to submit a Request for Quote to any of the following companies listed on
This article takes an in-depth look at extruded rubber.
Read further to learn more about topics such as:
Extruded rubber refers to items manufactured by heating and pressurizing an elastomer compound and pushing it through a die, a precise tool with a specific shape. This process results in a continuous material with a consistent cross-section throughout its length. The shape of the cross-section depends on the die design, and a multitude of profiles are utilized across various sectors, such as automotive, aerospace, electronics, construction, consumer products, and more.
Rubber extrusion is a vital manufacturing process in the industrial sector, used to efficiently produce uniform shapes and custom profiles with minimal material waste and highly cost-effective pricing. Extruded rubber products are renowned for their durability, longevity, and reliable performance in demanding environments. They exhibit outstanding resistance to chemicals, extreme temperatures (both heat and cold), UV radiation, impact, abrasion, and weathering—making extruded rubber seals, gaskets, tubing, and profiles ideal for a wide range of industrial, automotive, construction, and commercial applications.
Extrusion is a cornerstone production technique that dates back to the 1930s, initially designed for creating continuous-profile products such as rods, pipes, tubes, and weatherstripping. Over time, advancements in extrusion technology have enabled manufacturers to efficiently produce a diverse array of materials—including thermoplastics, aluminum, and, most notably, synthetic and natural rubber compounds. In addition to rubber, extrusion processing is also widely used with metals and plastics to generate precise custom parts. The versatility and efficiency of the extrusion process allow for the production of tailor-made solutions to meet unique customer requirements in industries like automotive manufacturing, aerospace, marine, and general OEM.
Rubber, being an exceptionally elastic material, can be compounded with various additives and reinforcing agents to achieve specific mechanical and chemical properties such as increased tensile strength, enhanced flexibility, flame retardance, or resistance to oils and solvents. Like engineered plastics, rubber offers lightweight construction, durability, and the ability to be shaped into complex or custom geometric profiles using advanced die tooling in the extrusion process. Despite requiring less energy for processing and forming compared to other materials, extruded rubber components retain all the advantageous properties of high-grade rubber sheeting and molded products. One of the biggest advantages is their low manufacturing cost, regardless of the selected rubber compound—be it EPDM, neoprene, nitrile (NBR), silicone, SBR, or natural rubber.
In addition to producing homogeneous rubber profiles, modern manufacturing allows for the combination of plastic and rubber through co-extrusion technology. This advanced process enables manufacturers to produce multi-material products featuring both rigid and flexible sections. Co-extruded products effectively leverage the unique properties of each material—such as the flexibility of thermoplastic elastomers and the strength of rigid PVC—which results in a more economical, versatile, and high-performance solution for challenging sealing, gasketing, or weatherproofing applications across multiple industries.
Rubber extrusion offers a multitude of benefits for manufacturing, design, and end-use performance. The process enables production of an extensive variety of high-quality extruded rubber products, including intricate shapes, customizable configurations, specialty gaskets, industrial seals, tubing, and architectural weatherstripping. Customers can specify unique designs, cross-sections, dimensions, and lengths, while manufacturers benefit from highly automated production that reduces waste and increases throughput. This results in fast turnaround times, lower total manufacturing costs, and greater design flexibility—ensuring ideal solutions for custom sealing, vibration dampening, insulation, and protective applications.
Superior Quality – A key advantage of extruded rubber products is their consistently high quality, which includes excellent resistance to heat, cold, UV exposure, aging, friction, abrasion, and everyday wear and tear. These qualities make them a preferred choice in applications demanding reliability and performance.
Exceptional Resistance – Extruded rubber components are engineered to withstand harsh operating conditions and resist degradation from exposure to chemicals, oils, ozone, moisture, and environmental stressors, ensuring long lifespan in critical sealing and gasketing applications.
Cost Savings – With minimal material waste and high efficiency, rubber extrusion significantly reduces production costs. This process delivers optimal price-performance ratios, making extruded rubber products affordable for high-volume OEM orders and custom, prototype runs alike.
Product Diversity & Customization – Rubber extrusion can accommodate a vast array of product requirements—including custom profiles, intricate cross-sections, complex geometries, and multi-durometer designs. Manufacturers can meet demanding applications with special, unique, and unconventional extrusions—whether for door seals, conveyor belts, bumpers, edging, or weatherproofing strips—offering endless design flexibility and material options.
Fast Turnaround & Scalability – Advanced extrusion lines support rapid production cycles, scalable batch sizes, and quick tooling changes, helping customers respond quickly to market demands while maintaining product quality and consistency.
Eco-Friendly Manufacturing – The efficiency of rubber extrusion translates into reduced raw material consumption and less scrap, supporting sustainability initiatives and environmentally responsible manufacturing.
If you are searching for custom extruded rubber seals, high-performance gaskets, or weather-resistant rubber profiles, partnering with an experienced rubber extrusion company is critical. Leading manufacturers offer expert material selection assistance, in-house design engineering, prototyping, and value-added secondary operations such as cutting, splicing, or adhesive backing, ensuring the highest quality final product for your unique application needs.
The rubber industry is predominantly driven by tire production, which constitutes two-thirds of global demand. The remaining demand is divided among non-tire automotive applications, industrial uses, footwear, electrical components, construction materials, and other specialized categories. Extruded rubber is widely utilized in most non-tire automotive and industrial sectors, thanks to its flexibility, durability, and adaptability. Manufacturers in industries ranging from automotive engineering to electrical insulation rely on a diverse array of high-performance extruded rubber profiles. Below are key examples of extruded rubber products, essential for a wide range of sealing, insulating, dampening, and protective applications.
Rubber Bushings: Extruded rubber bushings act as shock absorbers within equipment, isolating moving parts and minimizing the transfer of vibration and noise. They play a critical role in vehicle suspension systems, industrial machinery, and power transmission applications, helping to enhance performance, comfort, and product longevity.
Rubber bushings are typically shaped as hollow cylinders, a form that is easily produced through rubber extrusion processes. These vibration dampeners are cut to length based on the dimensions they are intended to fit, with variations in compound and design to meet the specific needs of high-load, high-temperature, or corrosive environments. While some rubber bushings are used as bare rubber, others are enclosed and bonded within metal casings or sleeves for added durability, enhanced chemical resistance, and improved performance in dynamic settings.
Rubber Trims: Rubber trims are extruded products designed to safeguard the edges or surfaces of rigid objects from sudden impacts, wear, or abrasion. They are commonly used on panels, windows, doors, removable covers, and hatches in automotive, marine, appliance, and machinery applications. In addition to impact protection, extruded rubber trims also serve sealing functions, providing air-tight and water-tight seals between mating parts to enhance energy efficiency and weather resistance.
The market offers thousands of rubber trim profiles, including custom-designed extrusions tailored to unique project requirements. One of the most in-demand shapes is the U-channel trim, which fits securely over the edge of panels or glass to prevent chipping and damage. These trims may incorporate metal reinforcement or use advanced adhesive technologies to ensure long-lasting installation and superior edge protection.
Rubber Tubing, Hoses, and Piping: Extruded rubber tubing, hoses, and pipes are core components in countless industries and are produced using advanced extrusion techniques for consistent quality and performance. These products are frequently used in hydraulic systems, pneumatic controls, chemical transfer lines, and fluid delivery setups. In the food and pharmaceutical industries, high-purity silicone tubing stands out for its safety, biocompatibility, and compliance with FDA and USP Class VI standards.
Rubber’s exceptional flexibility and resilience allow tubes and hoses to be routed around obstacles and withstand repeated flexing without damage or loss of integrity. This flexibility, combined with chemical and temperature resistance, makes rubber tubing, hoses, and piping ideal for transmitting fluids such as compressed air, hydraulic oil, water, coolants, and corrosive chemicals in industrial, medical, and laboratory environments.
Rubber Bumpers: Rubber bumpers, similar to rubber trims and bushings, utilize the material’s shock-absorbing and impact-dampening properties. Through advanced compounding, rubber bumpers also gain superior abrasion resistance, enabling long-term use in high-traffic areas. Typical applications include trailer truck loading docks, loading bays, warehouse equipment, jetty and boat fenders, and roadway safety devices. D-shaped or rectangular profiles are popular because they provide maximum cushioning and protect both equipment and vehicles from collision damage. The extruded design ensures uniformity and repeatability across large production runs.
Rubber Gaskets and Seals: Although most gaskets and seals are produced through die-cutting and injection molding, extrusion is also a viable method for manufacturing continuous-length profiles or custom shapes that require flexible, airtight, or watertight sealing. Extruded rubber gaskets and weatherstripping are commonly used for weatherproofing cabins, enclosures, vehicle doors, truck compartments, and electrical panels by providing protection against environmental factors such as moisture, dust, ozone, and temperature fluctuations. For these challenging environments, rubber materials like EPDM, silicone, nitrile, and neoprene are selected for their outstanding chemical, UV, and ozone resistance. Profiles are available in both hollow and solid cross-sections to provide effective compression seals in a variety of use cases. Selecting the proper durometer and formulation is crucial for ensuring reliable sealing performance over a wide temperature range.
Rubber Cord Stock or O-Rings: O-rings are a specialized type of gasket, most recognized for their uniform, circular cross-section that forms a continuous, effective seal when installed between mating surfaces. While compression and injection molding are widely used for small, high-volume O-rings, extruded rubber cord stock is the preferred solution for larger-scale equipment, custom assemblies, and irregular shapes. The extruded cord is precisely cut to match the circumference or perimeter of components like tank lids, vessel flanges, or custom industrial machinery, then carefully joined with adhesives or vulcanization to create a robust, leak-proof seal. Materials such as EPDM, nitrile, Viton®, and fluorosilicone are commonly selected based on their resistance to fuels, oils, chemicals, or high temperatures.
Medical Silicone Rubber Tubing: Among the various types of extruded rubber products, medical-grade silicone tubing is distinguished by its high quality, biocompatibility, and precise dimensional tolerances. The stringent standards of the medical device industry require tubing that can be sterilized repeatedly through autoclaving or chemical processes, while maintaining flexibility and clarity. These features are critical for applications such as IV delivery systems, catheters, peristaltic pump tubing, and laboratory equipment, where the safe and accurate transport of fluids is vital.
When sourcing extruded rubber products, it is important to consider critical application requirements such as temperature range, chemical compatibility, mechanical properties, and environmental exposure. Leading rubber extrusion suppliers offer a variety of custom solutions, including co-extruded profiles, flame-retardant compounds, and specialty shapes designed to address complex engineering challenges. Whether your operation demands precision sealing, long-lasting vibration isolation, or high-performance tubing, understanding the specific benefits of each extruded rubber product type will help inform purchasing decisions and optimize equipment efficiency. High-quality extruded rubber components provide unmatched durability, cost efficiency, and performance across a wide range of industries — from OEM automotive manufacturing and HVAC systems to industrial processing and medical device fabrication.
The properties of extruded rubber products are primarily determined by the chemical and physical characteristics of their base elastomer chain. This elastomer chain consists of a carbon-based polymer backbone with various active sites or functional groups. The specific chemical composition of the elastomer chain dictates the type and properties of the rubber material.
In addition to general properties like elasticity, thermal and electrical insulation, and shock absorption, the choice of rubber material depends on specific attributes such as chemical resistance, aging and degradation resistance, mechanical properties, and cost. Below are the various types of rubber materials used in the production of extruded rubber products.
Styrene-Butadiene Rubber (SBR): Styrene-butadiene rubber (SBR) is a copolymer of styrene and butadiene. It is a crucial type of rubber used not only for extruded rubber parts but also in the production of tires, gaskets, and footwear. SBR is a general-purpose rubber that rivals natural rubber in market share, favored for its superior abrasion, tear, and thermal resistance compared to natural rubber.
Ethylene Propylene Rubber (EPM, EPDM): EPDM (Ethylene Propylene Diene Monomer) is produced by copolymerizing ethylene and propylene with an added diene to facilitate curing. Without the diene, the resulting material is EPM (Ethylene Propylene Monomer), which can only be cured with peroxide. Both EPDM and EPM offer excellent weathering resistance, superior insulating and dielectric properties, and outstanding mechanical performance at both high and low temperatures. They also exhibit strong chemical resistance. In automotive sealing applications, they are produced in volumes comparable to NBR (Nitrile Butadiene Rubber).
Fluorocarbon (Viton) Rubber (FKM): Fluorocarbon rubbers, commonly known as Viton (a trademark of DuPont), are fluoro-elastomers made from the copolymerization of vinylidene fluoride (VDF) with other chemicals like hexafluoropropylene (HFP) and tetrafluoroethylene (TFE). FKM is renowned for its exceptional resistance to nearly all chemicals, alongside its robust mechanical properties. This makes it ideal for producing cord stocks for O-rings and various sealing products.
Silicone Rubber: Unlike other rubber materials with a carbon-based polymer backbone, silicone rubbers feature a silicon-oxygen chain bonded with methyl, vinyl, and phenyl functional groups. These materials are known for their excellent resistance to oxygen, ozone, heat, light, and moisture. Despite their higher cost and relatively poorer mechanical properties compared to organic rubber, silicone rubbers are widely used in various industrial applications, with a prominent role in food and drug manufacturing.
Rubber extrusion is a downstream process that includes several stages: compounding, heating, kneading, pressurizing, extrusion, and vulcanizing. This process utilizes rubber and chemical feedstocks derived from various primary operations in the chemical and petrochemical industries.
Rubber extrusion, while fundamentally straightforward, involves several detailed steps. The basic process includes feeding rubber material into the extruder, collecting the extrudate, vulcanizing it, and then cutting and splicing it to meet the client’s specifications. However, successful extrusion depends on managing numerous parameters, such as the formulation of the rubber compound, extruding conditions (including temperature and throughput rate), and vulcanizing time. Precise control of these factors is essential to produce a consistent and reliable product.
Here is a step-by-step overview of the rubber extrusion process:
Rubber Compounding: In the compounding stage, the rubber formulation is prepared by mixing the primary elastomer, such as NBR, SBR, BR, FKM, or others, with various additive ingredients. These additives enhance and modify the intrinsic properties of the base elastomer to achieve the desired characteristics for the final product. Some common compounding ingredients used in rubber extrusion include:
As the rubber progresses through the extruder barrel, the rotating screw masticates and mixes the material. The screw consists of engineered, precisely machined elements that either heat, knead, or pressurize the rubber. Heating the rubber increases its flowability, making it ready for the subsequent stages of the production process.
Extrusion: The extrusion operation occurs at the end of the extruder barrel, where a die is installed. This die features an opening that shapes the cross-section of the finished material. The die is designed to account for any dimensional changes that may occur after extrusion, as the extrudate typically swells upon exiting the die and during the vulcanization process.
As the rubber is pressurized by the screw, it is pushed through the die to form the extrudate, which takes on the physical characteristics of the final product. Once ejected from the machine, the extrudate is directed by a series of rollers and wheels to proceed to the next stage of the process.
Vulcanizing or Curing: Vulcanization, or curing, is the stage where the physical and chemical properties of the rubber are permanently set. During this process, cross-links are formed between the elastomer chains in the rubber. Vulcanizing agents, such as sulfur or peroxide, facilitate the bonding of sites within the rubber’s long molecular chains, creating an interconnected network. This cross-linked molecular structure results in a stretchable material that returns to its original shape when relaxed.
To start the vulcanizing process, the extrudate is heated or maintained at elevated temperatures of approximately 140 to 160°C. The duration of this process can vary depending on the rubber compound and vulcanizing agents used, typically taking several minutes. Vulcanizing time can be reduced by incorporating vulcanizing modifiers such as activators and accelerators.
In the co-extrusion process, different plastics and rubbers can be combined to create composite components. The choice of materials depends on the design requirements of the final product. It is essential to carefully monitor this aspect of the process to ensure the quality and performance of the finished product.
Co-extrusion involves the simultaneous extrusion of multiple layers of materials, requiring multiple extruders to melt and prepare both the rubber and plastic before they are combined. This process leverages the beneficial properties of each material to produce a stronger and more resilient final product.
A rubber bushing is a form of vibration isolator that is placed between two parts to limit the motion between them and absorb, mollify, and buffer the energy produced by their interaction. They are very...
Rubber sheets are basically sheets made of rubber or cloth that are coated with rubber to improve the mechanical properties of rubber sheeting such as increased tensile strength and reduced elongation...
Rubber trim is an extruded, sometimes molded, elastomer that is used to protect the edges or surfaces of objects from sudden impacts. They are usually found on panels, windows, doors, removable covers, and hatches...
Molding is a manufacturing process that uses a mold - the latter being a solid container used to give shape to a piece of material. It is a forming process. The form is transferred from the mold to the material by...
Rubber gaskets are elastic components used for mechanically sealing the microscopic gap between two mating surfaces or joints. Examples of these surfaces are flange faces of piping and fittings, mating surfaces of an...
Rubber injection molding is when uncured rubber is transformed into a usable product by injecting raw rubber material into a mold cavity made of metal. The applied pressure produces a chemical reaction like...
Rubber molding is a process of transforming uncured rubber or an elastomer into a usable product by transferring, compressing, or injecting raw rubber material into a metal mold cavity...
There are several methods to perform rubber overmolding, and each method has its own unique advantages and disadvantages. The choice of method typically depends on the design and material requirements of the product being...
A rubber roller is a machine part that is composed of an inner round shaft or tube covered by an outer layer of elastomer compounds. The inner shaft is made of steel, aluminum alloys, or other strong and rigid material composites...
Rubber to metal bonding is when a rubber part has to be adhered to a metal part, a metal component is chemically prepared and is attached or encapsulated as part of the process to become a bonded rubber part...
Rubber tubing, also known as rubber hose or rubber piping, is made of natural and synthetic rubber and is used to circulate and transport liquids and gases for household and industrial uses. The natural or synthetic rubber materials used for the manufacture of rubber tubing...
Silicone rubber molding is a method for shaping, forming, and fabricating silicone rubber parts and products using a heated mold. The process involves compressing or injecting silicone rubber into a mold...
A grommet edging is a flexible rubber or plastic strip that covers rough and sharp surfaces found in openings and edges of panel walls to protect the passing electrical cables, wires, and other sensitive components...