Rubber Bushings
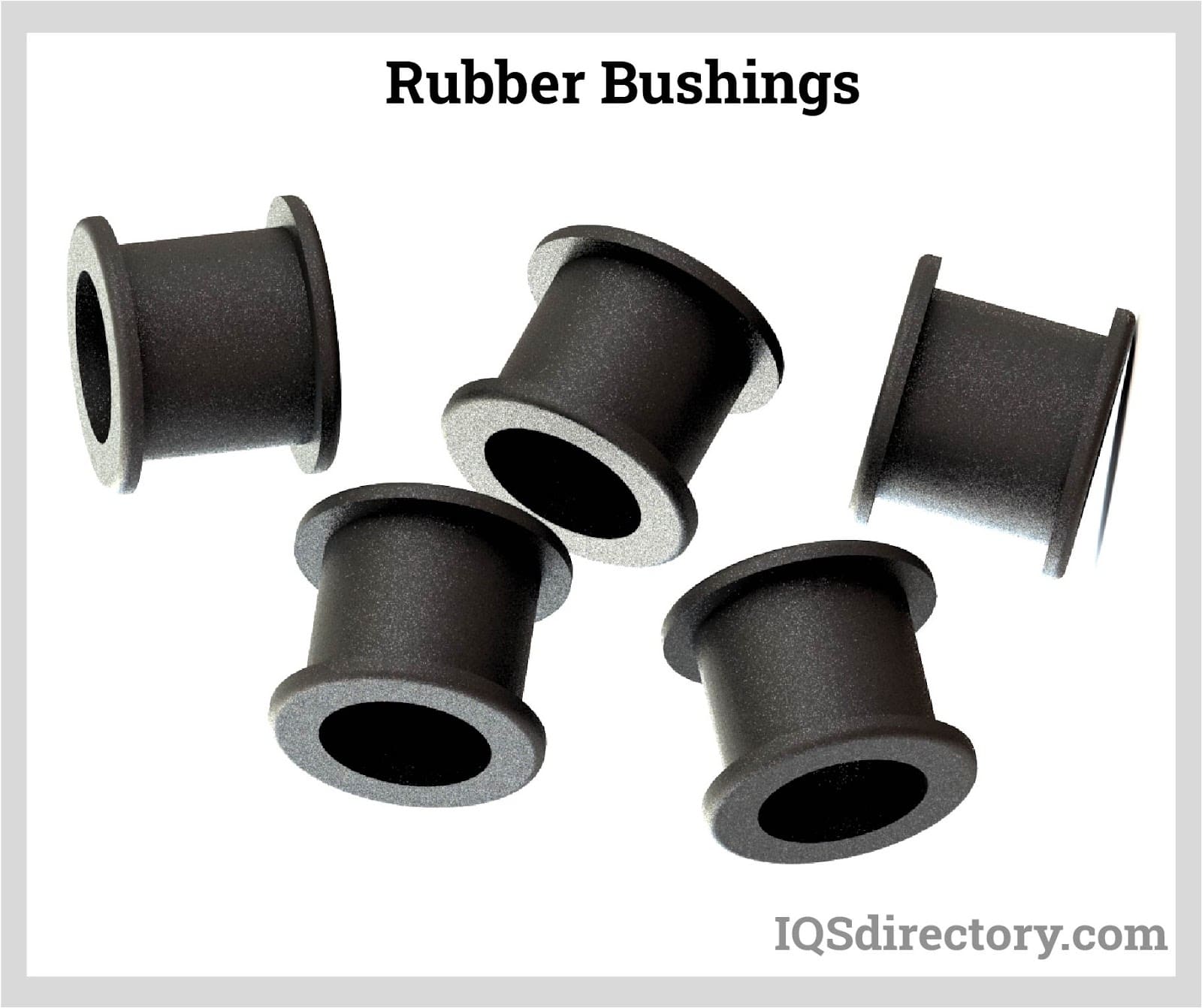
A rubber bushing is a form of vibration isolator that is placed between two parts to limit the motion between them and absorb, mollify, and buffer the energy produced by their interaction. They are very...
Please fill out the following form to submit a Request for Quote to any of the following companies listed on
Here is the most complete guide on the internet about
You will learn:
This chapter elucidates the definition of rubber sheets, their manufacturing techniques, and the diverse spectrum of their applications.
Rubber sheets are essentially flat materials crafted from rubber or fabric coated with rubber, aimed at enhancing material properties like greater tensile strength and reduced elongation.
This superior and adaptable material finds its utilization in oil and petroleum applications, such as fuel pumps and control valves, and is applicable for various uses across industries.
The creation of rubber sheets is influenced by variables such as length, width, thickness, color, size, and their intended purposes.
Prominent rubber sheets include recycled, reclaimed, synthetic, and natural rubber. Recycled rubber typically originates from crumb rubber from old tires bonded with adhesives, distinct from reclaimed rubber, which undergoes de-vulcanization and re-vulcanization. Synthetic rubber mainly consists of butadiene and styrene, derived from petroleum, and can be blended with various materials for versatile chemical and physical properties. Lastly, natural rubber comes from the latex of the Hevea brasiliensis tree, harvested mainly in South America, Africa, and Asia.
Thermoplastic polymers, like Polystyrene, Polyethylene, and Polypropylene, can be remolded several times with minimal quality loss. Blended polymers, such as PVC and ABS, may degrade during recycling, although additives can improve their stability at a higher cost.
Thermoset plastics, once processed, form a 3-dimensional network distinctly different from thermoplastics. The curing process transitions them from thermoplastic-like states to ones with permanent molecular bonds, diverging significantly from thermoplastics.
Rubbers, as a subset of thermosets, are largely thermoplastic before vulcanization, allowing for reshaping without major property loss. Vulcanization involves molecular cross-linking, but de-vulcanization remains largely unexplored. Research primarily focuses on recycling issues, with Reclaim and marketed Crumb being the primary types of recycled rubber. The challenge of de-vulcanization persists.
Polymers are optimized by compounding with mineral fillers and other polymers, enhancing capabilities and achieving varied properties, particularly in rubbers, thermosets, and PVC.
Key considerations for selecting materials for rubber sheets include:
Four crucial manufacturing techniques for producing rubber sheets include molding, extrusion, latex dipping, and calendaring.
Molding utilizes molds to shape compounds, effective for complex designs in smaller quantities and includes compression, transfer, and injection molding. Despite its cost-effectiveness for intricate designs, this method offers a slower production rate.
Products like O-rings and seals often stem from this process.
In extrusion, unvulcanized compound enters extruders, forming through dyes before vulcanization. Known for producing high volumes cost-effectively, extruded products include profiles, tubing, and gaskets.
This process involves dipping molds into latex solutions for thin-walled products, undergoing vulcanization post-dip. It's ideal for complex shapes like gloves and balloons, not feasible through extrusion.
Calendering uses rollers to flatten material, determining thickness by roller spacing. It's precise for thin, wide parts but has high operational costs.
Rubber sheets can be bonded via adhesives or vulcanization, with vulcanized joints offering superior durability. Adhesives might not perform under high pressures or temperatures.
A vulcanized joint involves carefully preparing and cutting rubber before using a bonding agent and jig for the process. While vulcanized joints offer strength, they might lack precise dimensions. This method, efficient for certain quantities, presents challenges in achieving uniformity when forming rings or profiles.
The major specifications are:
This specification addresses flexible cellular rubber products like sponge rubber but excludes ebonite cellular rubber. The products could be made from natural, synthetic, or reclaimed rubber, with polymers and additives for property enhancement.
For fabricated products, this specification requires synthetic, vulcanized, or rubber-like materials, either solo or combined, detailing inspection methods to uphold standards.
The different types of rubber sheets are:
These materials exhibit excellent dynamic and rebound characteristics and are resistant to tearing. For packaging applications, they serve effectively as anti-vibration pads. They offer superior dynamic performance, rebound, elasticity, and mechanical strength. Additionally, these sheets are commonly used as general sealing materials. Their versatility makes them widely adopted in various environments without the need for specialized conditions.
These materials are ideal for corrosion-resistant coatings and are commonly used in power transformers and other electrical applications. They offer excellent resistance to petroleum products, oils, flames, acids, and alkalis. In industrial settings, neoprene rubber sheets are employed for cushioning external metal cases to protect their contents, as corrosion-resistant coatings, for noise isolation in power transformer installations, and for various other electrical uses.
Neoprene rubber with a 40A durometer rating is highly compressible and can endure minimal force or pressure, making it easy to compress.
Neoprene rubber with a 50A durometer rating also withstands lower levels of force or pressure and is similarly easy to compress.
Neoprene rubber with a 60A durometer rating offers a balanced hardness, suitable for applications involving water, oil, beverages, and food. It remains durable and weather-resistant.
Neoprene rubber with a 70A durometer rating provides greater hardness and strength, making it more resistant to compression compared to softer grades.
Nitrile rubber is specifically engineered to resist oil and solvent exposure, making it ideal for use in electrical transformers, sealing applications, the food industry, and in environments involving dielectric oils for electrical systems. It is commonly used in flange joints and other connections exposed to fluid or atmospheric pressures.
Hydrogenated nitrile rubber (HNBR) offers superior chemical and oil resistance compared to standard nitrile rubber. It can endure higher temperatures and provides outstanding resistance to fuels, oils, various chemicals, ozone, and steam. HNBR also boasts excellent tear and tensile strength, abrasion resistance, and elongation properties. However, it is more expensive and has limitations, such as poor electrical insulation, limited flame resistance, and incompatibility with polar organic solvents and aromatic oils. HNBR is predominantly used in the automotive industry for various applications, including hoses, static seals, and belts, among others.
Due to their resistance to acids, alkalis, and ketones, these materials are well-suited for outdoor and high-demand environmental applications.
These materials feature low permeability and resistance to high temperatures, weathering, ozone, and various chemicals. They are particularly well-regarded in the pharmaceutical industry for their reliability and durability.
This type of sheet is constructed from natural or synthetic rubber and includes one or more layers of fabric reinforcement. This layering provides enhanced strength and durability under high pressure, making the sheets suitable for a range of applications.
Styrene-butadiene rubber (SBR) is a cost-effective synthetic rubber known for its abrasion resistance, excellent impact strength, high tensile strength, and good resilience. However, SBR has limited resistance to ozone, sunlight, oils, and steam. It is primarily used in automotive components, tires and tire-related products, and various mechanical rubber goods.
Viton™ sheets are made from fluoroelastomer materials, widely used across various applications. This durable fluoropolymer elastomer offers temperature stability from -20°C to 205°C. Viton™ can handle fluorinated solvents but may degrade if the incorrect grade is used and tends to be expensive. It is one of the most popular elastomers for sealing applications, including gaskets, O-rings, and seals, alongside nitrile.
Developed in the 1950s for the space program, Viton™ fluoroelastomers are renowned for their exceptional heat resistance, withstanding temperatures above 204°C for over 10,000 hours and up to 325°C for shorter periods. Besides its thermal resilience, Viton™ also resists most chemicals, making it a versatile choice for demanding applications.
Butyl rubber is an excellent choice for shock absorption due to its superior properties. It exhibits outstanding moisture resistance, low gas permeability, and excellent durability against aging, heat, ozone, weather, chemical exposure, flexing, tearing, and abrasion. Additionally, butyl rubber is resistant to ester-based phosphate hydraulic fluids and provides exceptional electrical insulation. However, it may experience issues like blistering, creeping, and air entrapment during manufacturing. Common applications for butyl rubber include O-rings, sealants, tank liners, and seals for vacuum applications due to its gas-impermeable nature.
This chapter will explore the various applications and advantages of rubber sheets.
Flooring and roofing applications are the most popular uses of rubber sheets in the industry. Rubber provides good resistance to substances like oil and petroleum, ultra violet lights, and oxidizing elements. Furthermore, it has the capacity to maintain flexibility even in cold temperatures. It is elastic and that even makes it suitable for various kinds of shock absorbers and for specialized machinery mountings designed to reduce vibration.
Rubber sheets are utilized across a wide range of applications, including industrial buildings, agricultural machinery, and Original Equipment Manufacturer (OEM) parts. They are also commonly used in commercial and residential settings such as storerooms, gyms, dance studios, garages, under shower pans, in drainage systems, and for weather stripping, as well as various construction and remodeling projects.
These sheets find applications in virtually every industry, including scientific, footwear, medical, engineering, railways, automotive, defense, aerospace, and marine sectors. Examples include their use in railroad tank cars, as linings for storage tanks, and in the creation of floor mats, gaskets, bearing pads, horse stall mats, sandblasting equipment, orthopedic footwear, and heavy-duty curtains. Rubber sheets are also used in wet areas like under showerheads and in washrooms to enhance slip resistance.
As the use of rubber sheets continues to expand, their demand is expected to grow significantly. Rubber sheets offer a cost-effective alternative to other materials and their versatility in combining with various products further enhances their appeal in the industrial market.
The benefits of rubber sheets are:
Protection of Work Surfaces – Rubber sheets provide excellent cushioning and impact absorption, making them effective at safeguarding work surfaces in industrial environments from damage.
Safety – Rubber is known for its safety benefits, being user-friendly and suitable for public areas. Its non-slip and shock-absorbing properties contribute to a safer environment for both users and staff.
Protection of Equipment – Rubber is an ideal material for protecting machinery due to its shock-absorbing qualities, helping to reduce wear and tear on equipment.
Anti-Vibration – Rubber effectively dampens vibrations from machinery, which helps prevent annoyance and reduces the risk of damage from excessive vibrations.
Resistance – Rubber is resistant to electricity, discoloration, and rust, enhancing its durability and longevity in various applications.
Versatility – Rubber sheets can be cut into a variety of shapes and sizes, including pads, washers, and gaskets, making them highly adaptable to different needs.
Availability – Rubber sheets come in various materials and colors, making them suitable for numerous settings, including retail and commercial applications. They can be customized into various forms, such as gaskets, washers, and pads.
Natural rubber has limited resistance to hydrocarbons, fats, oils, and greases, which can lead to swelling or dissolution upon contact with these substances. Ethylene propylene rubber (EPDM) sheets are unsuitable for food applications or exposure to aromatic hydrocarbons. They are commonly used for high-temperature water vapor seals, bathroom equipment seals, brake system components, and radiator seals in automotive applications. Silicone rubber sheets, though effective, are generally more expensive. Additionally, some rubber sheets can be affected by moisture and may not have a long lifespan. They may expand with temperature fluctuations, so they should be used in environments where these properties can be managed appropriately.
Rubber sheets can have a long service life with proper care and maintenance. This includes initial cleaning, regular upkeep, and the application of suitable finishes. It is advisable to use doormats at main entry points and to perform daily cleaning with a wet vacuum to remove dirt particles from the grooves of the sheet.
Avoid using chemicals on rubber sheets as they may cause adverse reactions. In healthcare settings, such as labor rooms and neonatal units, rubber sheets should be washed with running water and treated with an antiseptic solution. After cleaning, they should be hung to dry, then powdered before being rolled and stored.
If cracks, scratches, or thinning are observed on the rubber sheet, it may no longer maintain its insulation properties and should be replaced promptly. To prevent aging and deterioration, avoid exposing the sheets to direct sunlight, sharp metal objects, or excessive heat. Additionally, keep them dry and clean, and prevent contact with acids, alkalis, and other corrosive substances to avoid damage and maintain effective insulation performance.
Therefore, rubber sheets are basically material that is made from rubber. They are cost effective and safe for use by the public. Manufacturing rubber sheets is a lucrative business as they have immense and various uses in every industry worldwide (chemical, biological, commercial, environmental, and physical). They can be molded into various shapes and in various colors.
A rubber bushing is a form of vibration isolator that is placed between two parts to limit the motion between them and absorb, mollify, and buffer the energy produced by their interaction. They are very...
Extruded rubber is a group of products made by softening and pressurizing an elastomeric compound and forcing it to flow through a hard tool called a die. The resulting product is a continuous piece of material that has the same cross-section throughout its length...
Rubber trim is an extruded, sometimes molded, elastomer that is used to protect the edges or surfaces of objects from sudden impacts. They are usually found on panels, windows, doors, removable covers, and hatches...
Molding is a manufacturing process that uses a mold - the latter being a solid container used to give shape to a piece of material. It is a forming process. The form is transferred from the mold to the material by...
Rubber gaskets are elastic components used for mechanically sealing the microscopic gap between two mating surfaces or joints. Examples of these surfaces are flange faces of piping and fittings, mating surfaces of an...
Rubber injection molding is when uncured rubber is transformed into a usable product by injecting raw rubber material into a mold cavity made of metal. The applied pressure produces a chemical reaction like...
Rubber molding is a process of transforming uncured rubber or an elastomer into a usable product by transferring, compressing, or injecting raw rubber material into a metal mold cavity...
There are several methods to perform rubber overmolding, and each method has its own unique advantages and disadvantages. The choice of method typically depends on the design and material requirements of the product being...
A rubber roller is a machine part that is composed of an inner round shaft or tube covered by an outer layer of elastomer compounds. The inner shaft is made of steel, aluminum alloys, or other strong and rigid material composites...
Rubber to metal bonding is when a rubber part has to be adhered to a metal part, a metal component is chemically prepared and is attached or encapsulated as part of the process to become a bonded rubber part...
Rubber tubing, also known as rubber hose or rubber piping, is made of natural and synthetic rubber and is used to circulate and transport liquids and gases for household and industrial uses. The natural or synthetic rubber materials used for the manufacture of rubber tubing...
Silicone rubber molding is a method for shaping, forming, and fabricating silicone rubber parts and products using a heated mold. The process involves compressing or injecting silicone rubber into a mold...
A grommet edging is a flexible rubber or plastic strip that covers rough and sharp surfaces found in openings and edges of panel walls to protect the passing electrical cables, wires, and other sensitive components...