Rubber Bushings
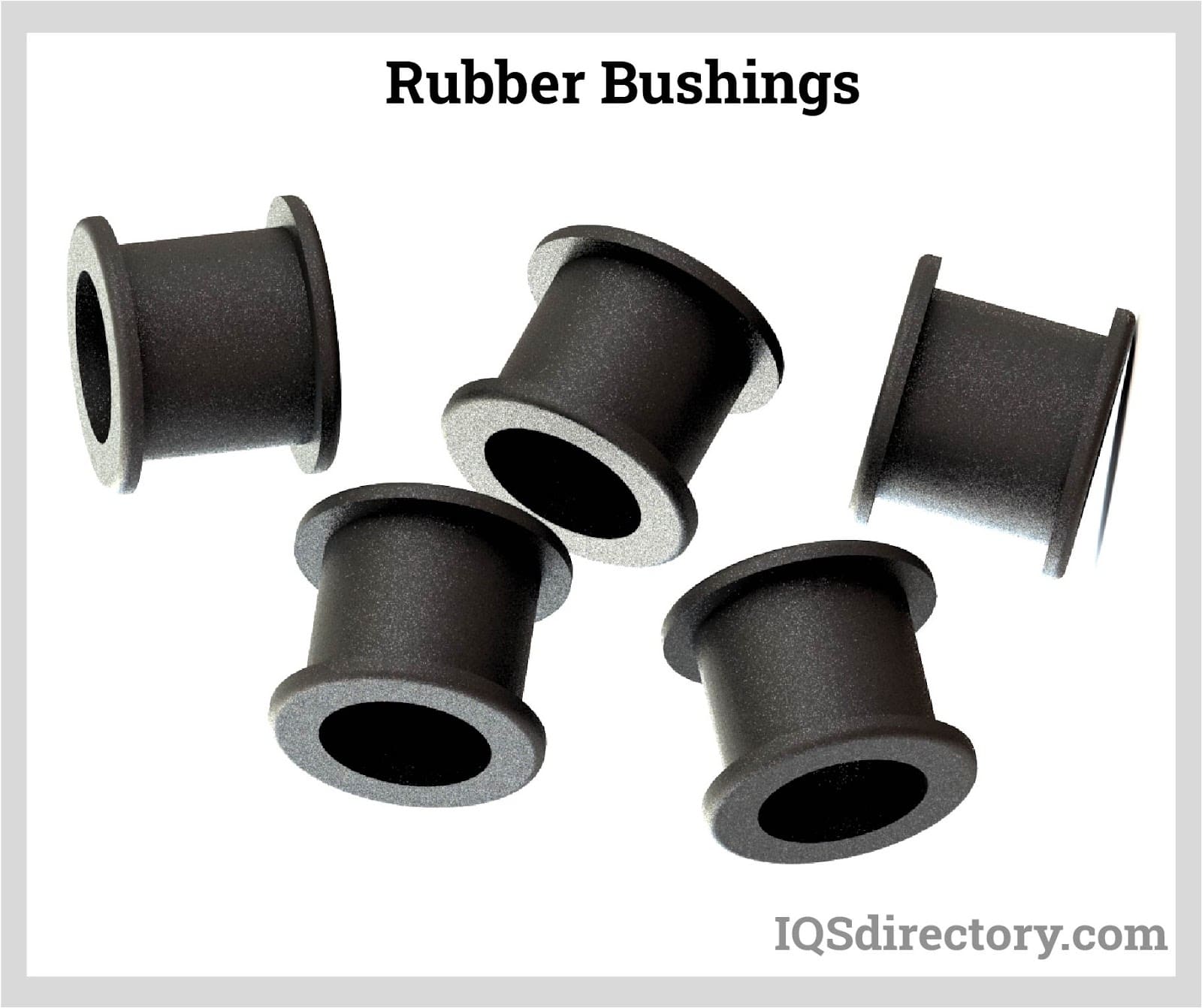
A rubber bushing is a form of vibration isolator that is placed between two parts to limit the motion between them and absorb, mollify, and buffer the energy produced by their interaction. They are very...
Please fill out the following form to submit a Request for Quote to any of the following companies listed on
This article provides comprehensive information about rubber trims and their production process. Read further to learn more about:
Rubber trim, whether extruded or molded, is designed to protect edges and surfaces from impact-related damage. Typically found on panels, windows, doors, removable covers, and hatches, it additionally provides sealing for the edges of adjoining components, acting much like rubber gaskets or O-rings. Crafted from dense rubber, this highly adaptable material offers outstanding durability and ozone resistance, securing and fitting tightly.
Rubber trim sometimes comes with a pre-applied adhesive like hot melt or butyl adhesive to enhance adhesion and reduce slippage. Its widespread use is due to its superior resistance to abrasion from repeated impacts and grazes.
Made from various profiles, rubber trims are frequently tailored for specific uses. Profiles are engineered and crafted onto a die before being installed on an extrusion machine to create the rubber product. The U-channel is the most prevalent, used for protecting edges. The part's edge or substrate is inserted into the channel's open end, secured by either fasteners or adhesives. Some designs include inside protrusions or tongues to secure the rubber trim without needing permanent fasteners.
For applications requiring a reliable seal, a solid or hollow cord or profile is integrated into the channel. This configuration, known as edge trim with a built-in seal, is produced through co-extrusion, where two different rubber types, each with distinct characteristics, are extruded together. When compressed, the cord conforms to mating surfaces, delivering a secure seal while the edge trim preserves structural integrity. Rubber trims are esteemed for their versatility in achieving varied hardness levels and their formidable resistance to chemicals, moisture, and elevated temperatures.
Rubbers belong to a group of polymers known as elastomers, characterized by their exceptional elasticity, which is achieved through the cross-linking of long polymer chains into amorphous structures. The relatively weak intermolecular forces between these polymer chains enable them to rearrange when subjected to stress. This flexibility allows elastomeric materials to adapt seamlessly to the contours of adjacent surfaces.
Elastomers can be vulnerable to degradation depending on the curing process or vulcanization used. Exposure to water, ultraviolet light, oils, and specific solvents can lead to deterioration. High temperatures may cause expansion and oxidation or aging, while low temperatures can render the materials brittle. Common elastomers employed in rubber trim production include nitrile (NBR), ethylene propylene diene monomer (EPDM), neoprene, silicone, and natural rubber.
Polybutadiene Rubber (BR):Polybutadiene rubber is produced from the polymerization of butadiene monomers containing four carbon atoms and six hydrogen atoms (C4H6). The three types of polybutadiene rubber are high Cis polybutadiene, lithium-based polybutadiene, and high trans polybutadiene, which have different isomers of butadiene.
The types of polybutadiene rubbers are made using a solution process that includes transition metals like neodymium, nickel, or copper complexes or an alkyl metal like butyllithium as catalysts. Generally, butadiene rubber has good cracking, abrasion, and rolling resistance but is prone to ozone degradation.
Butyl Rubber (IIR): This is a copolymer of isobutylene and isoprene; hence, the abbreviation IIR. Isoprene only consists of around 3% of the copolymer which gives the required unsaturation for vulcanization. The low unsaturation of IIR enables it to repel most chemicals (gas and liquids) and is highly resistant to aging when vulcanized properly.
The structure of butyl rubber is similar to polyethylene and polypropylene, with every other carbon atom being substituted with two methyl groups instead of one. It is the only elastomer that is resistant to gasses and is biocompatible with resistance to acidic or alkaline chemicals, ozone, heat, and weather and includes good aging properties. Butyl rubber does not perform well in the presence of petroleum-based fluids, hydrocarbons, or flames.
Acrylonitrile Butadiene (Nitrile) Rubber (NBR): This rubber is a copolymer of acrylonitrile and butadiene. They are polymerized in an emulsion similar to SBR polymerization systems. NBR is widely used due to its resistance to oils and petroleum-based solvents. However, they have low tensile strength and poor low-temperature performance. Reinforcing fillers are added to solve these problems.
Polyisoprene Rubber (IR): Isoprene rubbers are general-purpose rubbers created from the polymerization of isoprene monomers. The polymer chain is similar to that of natural rubber. Because IR is synthesized in a controlled environment, it is chemically purer than natural rubber with similar or more superior characteristics.
Silicone Rubber: These polymers, instead of having a carbon backbone, have a silicon-oxygen chain with groups of methyl, vinyl, and phenyl. Silicone rubbers have good oxygen, ozone, heat, light, and moisture resistance. However, they are more expensive and have poorer mechanical properties than organic rubber.
The manufacturing of extruded rubber is a very complicated process. The processes can be divided into two: the production of the raw rubber and the downstream processes that mainly involve compounding, forming (extrusion), and curing. The production of raw rubber converts gaseous or liquid petroleum-based compounds into polymers. This process is usually done in petrochemical plants. The rest is done in the rubber manufacturing plant, where the raw rubber and other materials are combined and formed to create the final product.
Rubbers are created through the polymerization of organic compounds, which form long chains and are cross-linked to achieve their elastomeric properties. This polymerization can occur via either step-growth polymerization or chain-growth polymerization.
Step-growth polymerization, also known as polyaddition polymerization, involves a reaction mechanism where monomers with at least two reactive sites or functional groups link together to create oligomers. These oligomers further connect to form longer polymer chains. The process is managed by introducing monomers with a single functional group, which reacts with the oligomer's active sites. This method, known for its straightforwardness, is among the earliest used for polymerization. Common elastomers made using step-growth polymerization include polysiloxane (silicone) and polyurethane.
Chain-growth polymerization, also referred to as chain polymerization, involves the sequential addition of monomers to a growing polymer chain. This process is initiated by reactive species or intermediates, which start the reaction by breaking a bond in a monomer, creating an active site for further monomer addition. These initiators can include free radicals, cations, anions, or organometallic catalysts.
During chain propagation, the active site on the growing chain facilitates the addition of new monomers, which in turn opens one of their bonds, creating more active sites. The polymer chain continues to grow until it encounters another chain or a terminating agent, leading to chain termination.
To control the molecular weight of the polymer, a process known as chain transfer is used. This method helps regulate the average length of the polymer chains. Common rubber compounds produced through chain-growth polymerization include butadiene, isoprene, and chloroprene. In addition to homopolymers (polymers made from a single type of monomer), this process also allows for the creation of copolymers, such as styrene-butadiene (SBR), nitrile butadiene (NBR), and ethylene propylene diene monomer (EPDM).
Compounding is the process of mixing specific chemicals with raw rubber to enhance its physical and chemical properties, reduce costs, and improve its processability and vulcanization. This formulation process aims to tailor the rubber's characteristics to suit its intended use. In addition to the base rubber (whether natural or synthetic), common ingredients used in compounding include:
Filler Systems: Filler systems include carbon blacks, clays, silica, and calcium carbonate, which are added to reinforce the elastomer structure to meet the required tensile strength and impact and abrasive resistance.
Carbon black is the most widely used reinforcing filler, which is produced from the incomplete combustion of heavy petroleum-based compounds, such as oil and tar. There are different types of carbon blacks, including super abrasion furnace (SAF), high abrasion furnace (HAF), fast extruding furnace (FEF), and semi-reinforcing furnace (SRF). Carbon black reinforces the elastomer by entangling the elastomer molecules on the porous surface of the filler. The deposition of carbon black particles into the elastomer matrix creates a composite with improved mechanical properties.
Non-carbon-based fillers, such as silica, clay, and calcium carbonate, are added to improve tear strength, reduce heat buildup, and create better compound adhesion for multicomponent products. These fillers do not bind well with elastomers in comparison with carbon blacks, resulting in a lower level of reinforcement, a problem that is solved by adding a silane coupling agent.
Stabilizer Systems: Stabilizer systems include antioxidants and antiozonants, which are added to prevent the degradation of rubber. Polymers, especially elastomers, tend to degrade due to the presence of carbon-to-carbon double bonds that can easily be broken and bonded onto by oxygen in the presence of ultraviolet light (photochemical reaction). The result is a broken polymer chain and a decrease in cross-linking density of the elastomer.
A broken polymer chain softens the elastomer, which decreases its abrasion resistance, while the decrease in cross-linking reduces the elastic property of the rubber and makes it stiff and prone to fatigue failure. Adding stabilizers helps limit the rate of oxidation by scavenging free radicals that can break the bonds of the polymer chain and prevents compounds, such as peroxides and hydroperoxides, from producing more free radicals by decomposing them.
Common antioxidants are phosphites, phenols, and hydroquinones. For the antiozonant, PPDs or paraphenylene diamines are the only classes used in significant quantities due to their potency and ability to further improve the fatigue and heat resistance of the rubber.
Vulcanizing or Curing Agents: Curing or vulcanizing agents are sulfur, peroxides, accelerators, activators, and retarders. The process of vulcanizing is where elastomers react with a system of compounds that inserts cross-links between the elastomer chains. It is often associated with sulfur systems, which are the most common method.
Sulfur curing systems consist of three main components: the vulcanizing agent (sulfur), the accelerators, and the activators. Accelerators act as catalysts that promote the vulcanization process by increasing the rate of the cross-linking process resulting in faster curing time and lower reaction temperatures. Accelerators increase the degree of cross-linking, resulting in a rubber matrix with better mechanical properties. Each type of accelerator works through different reaction mechanisms. Common accelerators are benzothiazoles, thiocarbamates, and amines.
Activators enable the efficient use of sulfur to increase the density of cross-links. The most common activator is zinc oxide combined with stearic acid. Zinc, when compared to other metal oxides, is most suited to forming sulfurating intermediates.
Adding the vulcanizing agents, accelerators, and activators to the elastomer prepares it for curing, which can occur prematurely during processing, making it harder to form. Premature vulcanization is termed as scorching. Retarders or inhibitors are added to prevent scorching without affecting the rate of vulcanization. The most popular rubber retarder is cyclohexylthiophthalimide (CTP), which is simply termed PVI or pre-vulcanization inhibitor.
Special Ingredients: Colorants, process oils, resins, and fibers are special ingredients used to give specific properties to the rubber. Colorants and pigments are supported by various compounds such as silica and titanium dioxide. Rubber is usually black due to the addition of carbon black.
Process oils are added to improve the processability of rubber. They can be paraffinic, naphthenic, and aromatic. Process oils also act as an extender to lower the cost of the rubber bulk. The type of process must be compatible with the elastomer to prevent it from migrating out of the compound.
Resins and fibers are added to improve the mechanical properties of the rubber. Hydrocarbon resins increase the viscosity of the compound when heated to achieve better flow, while fibers increase tensile strength and chipping resistance.
Mastication is a key step in the compounding process where the polymer chains are exposed to intense shear forces, which break the molecules into shorter chains. This treatment enhances the polymer’s ability to integrate with compounding ingredients. However, not all polymers need mastication, particularly those with stable and consistent chemistry. The use of chemical plasticizers or peptizers can aid in mastication by acting as oxidation inhibitors. These additives help prevent the reformation of broken polymer chains by neutralizing free radicals produced during the mixing process.
Mastication is usually done in open roll mills or internal mixers. Open mills consist of two rollers heated for temperature control. The rubber compound is sheared as it passes through the fixed clearance between the rollers. Internal mixers are high shear mixers that can either be a tangential rotor type or an intermeshing rotor type. The tangential rotor design shears the rubber between the clearance of the rotor and the walls or stator parts of the mixer. The intermeshing rotor design performs shearing by impinging the rubber between two rotors.
Masterbatching involves integrating most of the compounding ingredients into the masticated polymer, excluding the vulcanizing agents. This process helps prevent premature vulcanization, which could occur due to the heat generated during mixing. Masterbatching ensures an even dispersion of carbon black and achieves the desired viscosity of the rubber blend.
Final mixing is the stage where the vulcanizing agents are introduced. This step is typically performed using separate mixers that operate at lower speeds to control the mixing process. It is crucial to ensure thorough distribution of the final mix to avoid early vulcanization. Once mixing is complete, the blend is cooled and formed into slabs or bales, preparing it for the next stages of production.
In many manufacturing setups, the output from the mastication and mixing stages is fed directly into an extrusion machine equipped with either a single-screw or twin-screw system. This machine further blends the rubber compound, applies compression, and forces it through a die.
The die is crafted to the specific cross-section of the intended final product, accounting for any dimensional changes due to die swelling and vulcanization. Temperature control within the extruder is managed by steam jackets, water jackets, or electric heaters along the barrel to maintain optimal conditions.
Some extrusion systems integrate the processes of compounding, masticating, and mixing into a single unit. These machines feature screw elements with varied profiles to perform different functions: one set for mastication (kneading), another for mixing, and a third for compression. The extrudate is then passed through a heater or oven to commence the vulcanization process.
As previously discussed, the process of curing, also known as vulcanization, involves forming cross-links between elastomer chains. This process enhances the stability of the rubber, allowing it to withstand various environmental factors like heat, cold, and solvents. Historically, "curing" was the general term for this cross-linking process, while "vulcanization" specifically referred to curing rubber with sulfur. Sulfur was the first curing agent used to cross-link natural rubber or latex. Nowadays, other curing methods are employed that do not rely on sulfur as the primary agent. These modern methods use alternatives such as peroxides, and occasionally phenols and metal oxides.
Vulcanization is achieved by heating the rubber compound, which contains curing agents, to activate the sulfur molecules (S8) or sulfur donors. This heating process breaks the sulfur bonds, creating sites for cross-linking. Cross-links are formed when elemental sulfur or sulfur donors interact with the functional groups or unsaturated bonds on elastomer chains. Traditional vulcanization with elemental sulfur involves heating at approximately 284 °F (140 °C) for about five hours. This method produces rubber with good physical properties but tends to age quickly. The addition of activators, such as zinc oxide, shortens the curing time to around three hours. When combined with accelerators, this process further reduces the curing duration to just a few minutes, enhancing the rubber's aging resistance and overall properties.
Peroxide curing agents operate similarly to sulfur-based curing agents. Heating decomposes the peroxide into free radicals, which extract hydrogen atoms from the polymer chain, creating sites for cross-linking. Generally, peroxide curing offers superior temperature resistance, aging characteristics, solvent resistance, and reduces odor compared to sulfur curing. Additionally, peroxide curing does not require the use of activators and accelerators that can potentially produce carcinogenic nitrosamines.
Secondary processes are supplementary operations performed on products to tailor them for specific uses. These processes might include cutting, drilling, notching, splicing, coating, and other modifications. For rubber trims, common secondary processes involve splicing, applying slip coatings, injecting sealants, and using adhesive tapes, in addition to cutting.
Testing and quality control are essential for assessing the final properties of the product and ensuring its uniformity and consistency. Major manufacturing facilities with compounding operations typically maintain an in-house testing laboratory. The final rubber compound is subjected to various tests, which may include:
Property |
Method / Standard |
Description / Instrument |
---|---|---|
Cure Quality |
ASTM D2084 |
Oscillating disk cure meter (rheometer) |
Hardness |
ASTM D2240 |
Measurement of indentation using a durometer |
Tensile Strength |
ASTM D412 |
Universal testing machine (tensile test) |
Elongation |
ASTM D412 |
Analysis of stress-strain curve by elongating until rupture |
Compression Set |
ASTM D395 |
Measurement of residual deformation upon compression and deflection |
Heat Resistance (Thermal Aging) |
ASTM D865 / ASTM D572 / ASTM D573 |
Analysis of stress-strain curve or mechanical characteristics before and after heating in air or oxygen-rich atmosphere |
Abrasion Resistance |
ASTM D1630 / ASTM D2228 |
Measurement of material loss using NBS abrader or Pico abrader |
Tear Resistance |
ASTM D624 |
Similar to tensile test until rupture; the difference is the profile of the specimen cut by standard dies |
Resilience |
ASTM D2632 |
Measurement of rebound using vertical rebound tester |
Impact Resistance |
ASTM D256 |
Measurement of load causing permanent deformation using Izod and Charpy impact testers |
Flex Resistance |
ASTM D813 / ASTM D1052 |
Measurement of the number of cycles before failure using DeMattia or Ross flexer |
Heat Buildup |
ASTM D623 |
Measurement of the rise in temperature after rapid cycling using Goodrich flexometer |
Ozone Resistance |
ASTM D1149 / ASTM D3395 |
Analysis of mechanical properties in an ozone-rich atmosphere |
Outdoor Exposure |
ASTM D518 |
Analysis of physical properties when exposed to sunlight, soil, moisture, and bacteria |
Water absorption |
ASTM D570 |
Measurement of tensile properties after aging in humidity or water spray in the presence of ultraviolet light |
Solvent Resistance |
ASTM D471 |
Assessment of volume, weight, and other physical properties upon contact with test liquids |
Brittleness |
ASTM D746 |
Determining the temperature at which brittle fracture occurs |
Low Temperature Stiffness |
ASTM D1053 |
Measurement of modulus of rigidity in low temperatures using Gehman torsion tester |
It is important to note that not all tests are mandatory; the specific tests required depend on the customer’s needs and the product’s intended application. Once quality inspections are completed, the products are typically rolled, bundled, or packaged in preparation for distribution.
A rubber bushing is a form of vibration isolator that is placed between two parts to limit the motion between them and absorb, mollify, and buffer the energy produced by their interaction. They are very...
Extruded rubber is a group of products made by softening and pressurizing an elastomeric compound and forcing it to flow through a hard tool called a die. The resulting product is a continuous piece of material that has the same cross-section throughout its length...
Rubber sheets are basically sheets made of rubber or cloth that are coated with rubber to improve the mechanical properties of rubber sheeting such as increased tensile strength and reduced elongation...
Molding is a manufacturing process that uses a mold - the latter being a solid container used to give shape to a piece of material. It is a forming process. The form is transferred from the mold to the material by...
Rubber gaskets are elastic components used for mechanically sealing the microscopic gap between two mating surfaces or joints. Examples of these surfaces are flange faces of piping and fittings, mating surfaces of an...
Rubber injection molding is when uncured rubber is transformed into a usable product by injecting raw rubber material into a mold cavity made of metal. The applied pressure produces a chemical reaction like...
Rubber molding is a process of transforming uncured rubber or an elastomer into a usable product by transferring, compressing, or injecting raw rubber material into a metal mold cavity...
There are several methods to perform rubber overmolding, and each method has its own unique advantages and disadvantages. The choice of method typically depends on the design and material requirements of the product being...
A rubber roller is a machine part that is composed of an inner round shaft or tube covered by an outer layer of elastomer compounds. The inner shaft is made of steel, aluminum alloys, or other strong and rigid material composites...
Rubber to metal bonding is when a rubber part has to be adhered to a metal part, a metal component is chemically prepared and is attached or encapsulated as part of the process to become a bonded rubber part...
Rubber tubing, also known as rubber hose or rubber piping, is made of natural and synthetic rubber and is used to circulate and transport liquids and gases for household and industrial uses. The natural or synthetic rubber materials used for the manufacture of rubber tubing...
Silicone rubber molding is a method for shaping, forming, and fabricating silicone rubber parts and products using a heated mold. The process involves compressing or injecting silicone rubber into a mold...
A grommet edging is a flexible rubber or plastic strip that covers rough and sharp surfaces found in openings and edges of panel walls to protect the passing electrical cables, wires, and other sensitive components...