Rubber Injection Molding
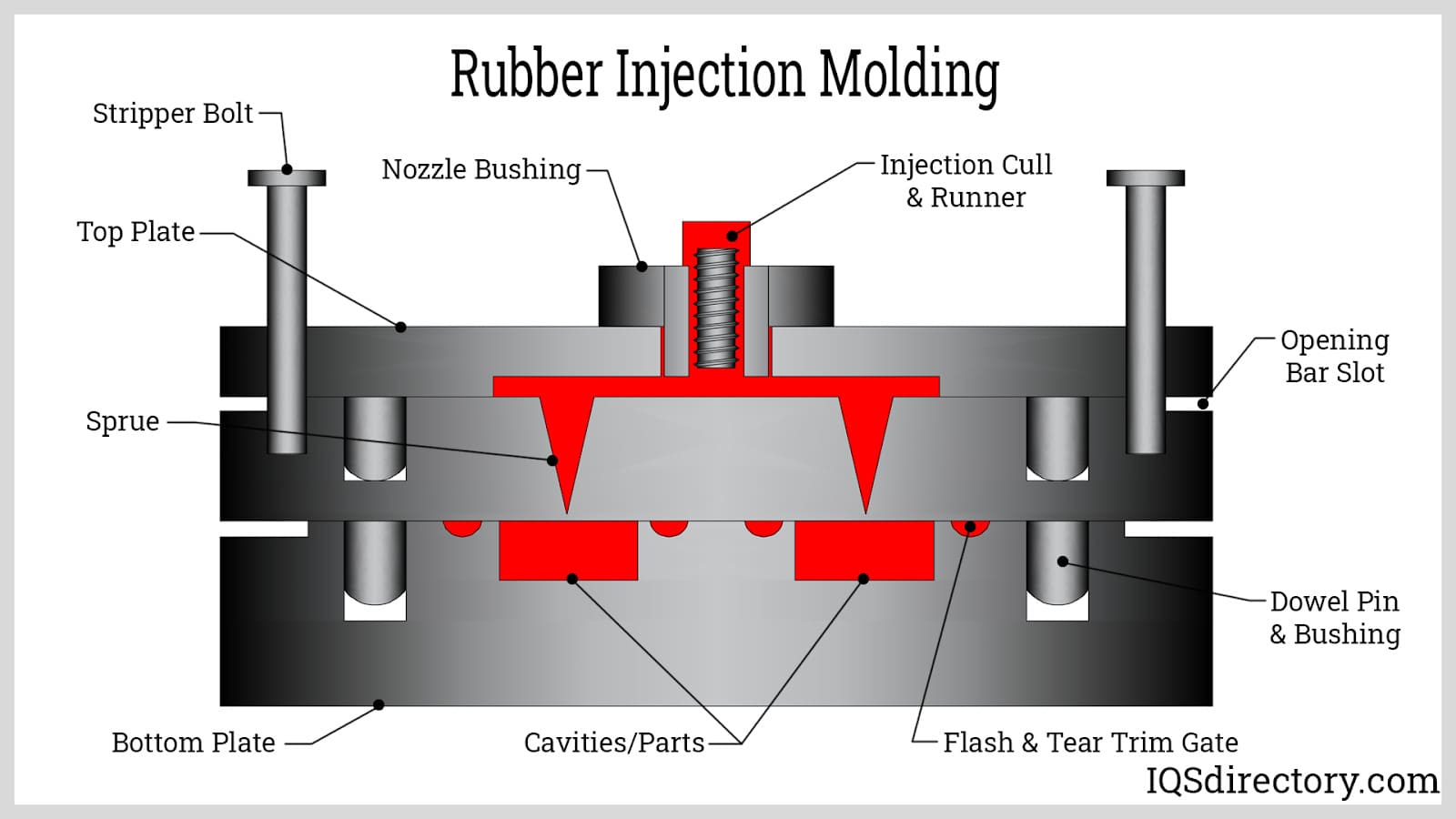
Rubber injection molding is when uncured rubber is transformed into a usable product by injecting raw rubber material into a mold cavity made of metal. The applied pressure produces a chemical reaction like...
Please fill out the following form to submit a Request for Quote to any of the following companies listed on
This article will take an in-depth look at compression molding.
The article will give a better understanding of the following topics:
Compression molding is a versatile manufacturing technique that shapes materials using compressive force to align them with a two-part mold, consisting of an upper and lower section. When compressed, these mold halves enclose a cavity that precisely forms the material to the desired shape. The mold is crafted in such a way that the finished product can be easily removed following the setting and curing process.
Although originally innovated for synthetic materials, compression molding remains the most economical method for processing thermosetting plastics. In contrast, injection molding is generally favored for thermoplastics.
There are various types of compression molds available, such as flash, positive, landed positive, and semi-positive molds, with the flash mold being the most prevalent. The processes within compression molding are categorized into bulk and sheet molding. Bulk molding combines ingredients like fillers, catalysts, stabilizers, pigments, and fiber reinforcers. The significant benefits of using compression molding for thermoset plastics include greater strength, reduced weight, and excellent resistance to corrosion.
Compression molding is a robust and cost-efficient manufacturing approach.
Contrary to single-use molds, the molds utilized in compression molding are constructed to endure repeated use throughout numerous production cycles.
Below is a thorough explanation of the key steps involved in the compression molding process.
The initial step is setting up the mold, which commonly involves:
Compression molding can accommodate various materials, resulting in diverse shapes, sizes, compositions, and conditions.
This preparation process transforms the material from its original state into a form more suitable for compression molding. The preparation might include:
Preparation of the charge is often the most labor-intensive phase due to minimal automation.
This phase involves placing the charge in the mold's lower portion to optimize the compression outcome. The charge is distributed within the mold based on its shape, anticipated thickness, and other factors.
The upper and lower halves of the mold come together to compress the charge effectively. During this compression, the process aims to achieve some of the following:
Three main parameters are important throughout the compression stage:
This molding stage is critical for solidifying the compressed charge into the finished product, involving cooling or the use of hardening agents and catalysts to set and solidify the material.
Different types of curing methods include:
Curing agents such as Dimethyl stannane and Tetraethoxysilane are employed with resins, polyurethane, and silicone, facilitating condensation curing processes.
Additional agents for curing silicones include organopolysiloxane.
Common curing agents comprise Benzoyl peroxide, Peroctoate, and t-butyl perbenzoate.
Cooling serves critical roles such as:
Following curing, the product is separated from the mold, a phase that might be manual or automated. Manual ejection is frequently used in small-scale or hobbyist molding applications, including medical accessory production. Automated ejection may involve a plunger underneath the mold or a dedicated suction mechanism.
Ejection typically involves applying a release agent or coating to the mold to prevent sticking and ease removal. This process, sometimes called mold curing, differs from the curing phase mentioned earlier. The ejection step is crucial in determining the final geometry of compression-molded products. Though products can feature threads, holes, and grooves, these complexities can complicate ejection and automation.
Examples of common release agents are:
To ensure the mold fills correctly, the charge is usually placed slightly above the required volume, resulting in excess material that emerges at the mold's part lines during compression. After removal, this excess material, termed flash, remains attached to the product and is removed in the de-flashing stage.
De-flashing can be handled manually or automatically. Manual de-flashing, using a blade to cut off excess, is often reserved for larger molded items challenging for automation or when cost is a consideration. Automated de-flashing utilizes methods like water jets and ice blasting, with some processes being cryogenic. Vibration tumbling is another automated method. The flash's orientation—either vertical or horizontal—depends on the mold's parting line geometry, dictated by how the mold's halves align.
Below are some of the different types of compression molds:
In flash compression molding, the charge is intentionally overfilled so that excess material, or flash, is produced at the end of the compression process. This causes a small gap between the mold parts, allowing the flash to escape. While this method can lead to considerable waste, it is less likely to result in blistering.
This method requires precise measurement of the charge and does not create a gap between the mold parts at the parting line. It has the following characteristics:
This method is more costly than the other two flash control methods but offers a blend of their advantages. It falls between the two approaches in terms of flash management.
Charge measurement with this method does not need to be as precise as with positive-type molds. Some excess material may be allowed to escape during compression.
As with other areas of industrial technology, compression molding is continually advancing, especially in terms of automation and environmental sustainability.
Various technologies are applied to different aspects of compression molding, including:
Hydraulic systems are commonly employed for pressing in most applications, though lighter presses may utilize pneumatic systems.
The pressing motion is typically vertical, which simplifies the design of the pressing mechanism and its support structure, especially given the considerable weight of the mold. While the pressing mechanism can technically be designed in any orientation, compression is generally applied through a telescoping action as the mold parts come together.
Compression molding employs durable, non-flexible molds, typically made from steel for commercial use. These molds are machined from solid blocks rather than cast, as they are usually not produced in large enough quantities to warrant casting.
Machining can be done manually (e.g., milling, drilling) or through automated processes (e.g., CNC). Steel is the primary material used for molds, and the machining process is generally subtractive rather than additive.
Compression molding is a versatile and scalable technique used across various applications, including:
Bench-top compressors are commonly used for experimentation, such as refining molding techniques and developing new materials. They are also utilized in prototyping, where they compete with 3D printing technologies.
This scale of molding is suitable for recreational use as well. Additionally, due to the relatively simple principles involved, it is possible to assemble the necessary components for demonstrations and educational purposes.
This could be part of auxiliary operations that are outside the core business functions of a company. For example, a firm specializing in servicing irrigation equipment might choose to mold some of the components in-house rather than outsourcing.
This approach is commonly adopted by companies whose primary business involves selling compression-molded products or components. However, the scale of production may be limited by economic considerations.
This scale encompasses both the mass production of molded products and the manufacturing of large-sized items. At this level, automation becomes essential to justify the production requirements.
This process involves combining fabrics with a liquid or molten charge, like epoxies, to create durable products. This technology is increasingly being adopted in the automotive industry.
This technology quickly reduces the pressure in the mold cavity during pressing, resulting in improved surface finishes on the products.
This technology is an advanced form of compression molding. In transfer molding, the charge is held in a transfer port. Initially, the two mold parts are brought together, and then the charge is transferred into the mold cavity. The key distinction from compression molding is the use of the transfer port in transfer molding, whereas in compression molding, the charge is placed in the mold cavity before the mold parts are closed.
Transfer molding is typically employed for producing more complex products that are not feasible with compression molding.
This process is similar to transfer molding, but with a key difference: the charge is injected into a partially closed mold. This partial closure means that the cavity volume during injection is larger than the final volume achieved after compression.
Once the injection is completed, the mold parts fully close to compress the injected charge. This method is generally faster than compression molding but requires more costly equipment.
In this process, a charge is compressed onto a pre-made component, known as the insert. The charge then encapsulates or attaches to the insert, which is prepared separately before being inserted into the mold for encapsulation.
For example, an insert might be a knife blade, and the insert molding process could result in attaching a plastic handle to it. Common inserts also include threads (sometimes referred to as nutsets) and electrical contacts.
Insert molding offers a convenient method for assembling components, particularly those that do not require disassembly during their service life. The advantages of insert molding include:
However, it also comes with the following disadvantages:
Overmolding involves the molding of material onto a pre molded component. It is usually done on materials with different mechanical properties to combine their advantages.
Examples would be a power tool handle and a toothbrush. To produce the handle, an elastomer can be over-molded onto a PTFE substrate (the PFTE substrate molded in some previous stage). The PTFE would provide rigidity for the handle, and the elastomer would improve the handle's grip, ergonomics, and aesthetics.
Although both methods are technically possible, over-molding is more frequently achieved through injection molding rather than compression molding. This is because the substrate for over-molding is typically produced using compression molding.
A variant of over-molding is two-shot molding, which is exclusively performed using injection molding.
Compression molding is recognized as one of the traditional molding techniques, with several others having emerged since. Below are some of the alternative molding methods:
Extrusion molding is well-suited for products with a consistent cross-section or for long items where creating a full-sized mold would be impractical. Even for smaller dimensions, extrusion molding is often faster than other methods, such as injection molding, as it allows for the production of products with a uniform cross-section, which can then be cut to size as needed.
Blow molding is used to create hollow objects, typically with an opening smaller than the final product's cavity. Bottles are a common example of blow-molded items. The process begins with placing a preform into the mold. The mold is then closed and heated, and the preform is blown to expand and fill the mold, taking on its shape in the process.
In injection molding, material is forced into a closed mold under pressure. The mold must be fully closed before the material is injected to ensure it fills the cavity properly. The material’s viscosity must be low enough to flow into the mold effectively under the applied pressure, so the charge is continuously heated. Preforms for blow molding are often produced using injection molding. In practice, any thermoplastic product suitable for compression molding can also be made with injection molding. Charge preparation is simpler with injection molding, as it typically involves using plastic pellets. While injection-molded components face similar geometric constraints as compression-molded ones, injection molding is generally more cost-effective for producing most thermoplastic products.
Thermoforming is employed to produce very thin products, such as fast food packaging. In this process, the material is first draped over the mold and heated. Then, a vacuum is used to draw the material tightly onto the mold's surface.
This method is used to create large hollow objects where blow molding might encounter technical or practical limitations.
Although 3D printing operates on a fundamentally different principle than molding, it competes with molding techniques in the realm of prototyping. Molding methods are typically better suited for mass production, while 3D printing excels in producing a diverse range of designs.
Casting involves pouring liquid material into molds under the influence of gravity. This method is not typically used for large-scale plastic production. Unlike other methods mentioned, casting can utilize pliable and temporary molds.
Most compression-molded products are made from thermosets, though rubber, thermoplastics, and polymer composites are also commonly used. The prevalence and scale of compression molding across different industries are largely driven by demand.
Compression molding is particularly effective for products that are typically flat or have solid, flat surfaces, such as:
Various materials are used in compression molding, including:
Thermosets are plastics that can be melted only once. Once hardened through an irreversible chemical reaction involving polymerization and cross-linking, they cannot be re-melted or recycled. When exposed to high heat, thermosets tend to smolder and char rather than melting.
The inability to recycle thermosets is a major disadvantage, making them particularly difficult to dispose of in an environmentally friendly manner. Despite this, thermosets offer specific properties that make them advantageous for certain applications:
Compared to metals:
Compared to thermoplastics:
Thermosets offer excellent dimensional stability and heat resistance. In molding processes, they are often combined with other materials, particularly carbon fibers, to create composites. Some common thermosets used in molding include:
This material is named for its chemical structure, which features a phenyl group in its monomer. Commonly known as Bakelite, it is valued for its excellent heat resistance and dimensional stability.
This category encompasses various substances due to the presence of an epoxide group in their chemical structure. They exhibit mechanical properties similar to those of phenolic molding compounds.
Polyester can be used as either a thermoset or a thermoplastic.
This is another type of thermosetting plastic.
Thermoplastics can be melted repeatedly. Polyester is one of the few materials to fit in both lists: thermosets and thermoplastics, depending on how it is hardened. Thermoplastics can be disposed of more sustainably. They are relatively low cost. However, their mechanical performance is bettered by thermosets.
Below are some of the thermoplastics used in molding:
Polypropylene foam is manufactured using compression molding with a chemical blowing agent (foaming agent).
This is another example of a thermoplastic.
Polyethylene can be combined with rubber to create a composite that can be molded as an elastomer.
Polyester acts as a thermoplastic if it is not combined with a hardening agent.
This thermoplastic is known for its very high viscosity and excellent non-stick properties.
Polyaryletherketones (PAEK) are used in compression molding to replace metals in specific applications. Polyetheretherketones (PEEK) and polyetherketoneketones (PEKK) are also part of this material family.
Fibers are incorporated into resins to create composite materials. These composites leverage the advantages of their constituent materials, offering improved properties compared to the individual components. For instance, sheet molding compounds are examples of glass-reinforced composites.
Carbon fibers perform a similar function to glass fibers but typically result in a more rigid composite and come at a higher cost.
This material usually consists of two layers of polymer resin, such as polyester, surrounding a layer of glass fibers. A polyethylene film covers the compound to facilitate handling; this film is removed before molding. The finished sheets are typically around 5mm thick. For products requiring greater thickness, multiple layers of SMC can be stacked. There is also a variant known as Thick-walled SMC, which can reach thicknesses of up to 50mm.
BMC is a dough-like mixture of polymer resins, chopped fibers (as opposed to the long fibers used in SMC), and a hardening agent. Loading BMC into the mold involves ensuring the correct amount of charge is used, making it more pliable than SMC.
Chemically, an elastomer is a polymer characterized by its viscoelasticity. Their applications are driven by their insulating properties and resistance to various substances.
Here are some examples of elastomers used in molding:
This is an acrylonitrile-butadiene rubber known for its oil resistance. It can be used in various molding processes, including compression molding, injection molding, transfer molding, and over-molding.
This rubber is resistant to water and performs well against organic acids. However, it has limited resistance to strong acids, ozone, and oils.
This elastomer is highly resistant to ozone and weather conditions, making it suitable for applications like sealing hot water. It also performs well with greases, alcohols, and detergents but is less effective with petroleum fuels.
Viton is one of the most durable and expensive elastomers, known for its high-temperature resistance and performance in exposure to fuels and water. It is commonly used in O-rings, fuel injectors, and boat propeller fittings.
This rubber is suitable for mechanically demanding applications, enduring significant stretching and temperature fluctuations. It also performs well at very low temperatures and is used in aerospace applications and electrostatic discharge protection.
Compression molding offers several benefits, including:
However, there are some drawbacks associated with compression molding, including:
Overall, the advantages of compression molding generally outweigh its drawbacks.
Below are some of the standards applied in compression molding:
Compression molding finds itself amidst a rapidly advancing manufacturing industry, to which new techniques are continually introduced. As a result, it has endured some moderate longevity compared with some methods competing in the same space. Its ability to meet the evolving needs of the industry has been aided by its adaptation into emerging trends, for instance, robotics. In the broader context of the manufacturing industry, compression molding is not an end in itself but a means to some other end.
Rubber injection molding is when uncured rubber is transformed into a usable product by injecting raw rubber material into a mold cavity made of metal. The applied pressure produces a chemical reaction like...
Rubber latches are latches made of rubber or are composed of rubber components. They are used in the automotive, aerospace, and medical equipment industries due to their flexibility, durability, and non-abrasive properties...
Rubber molding is a process of transforming uncured rubber or an elastomer into a usable product by transferring, compressing, or injecting raw rubber material into a metal mold cavity...
There are several methods to perform rubber overmolding, and each method has its own unique advantages and disadvantages. The choice of method typically depends on the design and material requirements of the product being...
Silicone rubber molding is a method for shaping, forming, and fabricating silicone rubber parts and products using a heated mold. The process involves compressing or injecting silicone rubber into a mold...
A rubber bushing is a form of vibration isolator that is placed between two parts to limit the motion between them and absorb, mollify, and buffer the energy produced by their interaction. They are very...
Extruded rubber is a group of products made by softening and pressurizing an elastomeric compound and forcing it to flow through a hard tool called a die. The resulting product is a continuous piece of material that has the same cross-section throughout its length...
Rubber gaskets are elastic components used for mechanically sealing the microscopic gap between two mating surfaces or joints. Examples of these surfaces are flange faces of piping and fittings, mating surfaces of an...
A rubber O ring is a mechanical gasket in the shape of a torus or donut and is used for static and dynamic applications where there is relative motion between parts and the possibility of friction. Some of the benefits of rubber O rings are...
A rubber roller is a machine part that is composed of an inner round shaft or tube covered by an outer layer of elastomer compounds. The inner shaft is made of steel, aluminum alloys, or other strong and rigid material composites...
Rubber sheets are basically sheets made of rubber or cloth that are coated with rubber to improve the mechanical properties of rubber sheeting such as increased tensile strength and reduced elongation...
Rubber to metal bonding is when a rubber part has to be adhered to a metal part, a metal component is chemically prepared and is attached or encapsulated as part of the process to become a bonded rubber part...
Rubber trim is an extruded, sometimes molded, elastomer that is used to protect the edges or surfaces of objects from sudden impacts. They are usually found on panels, windows, doors, removable covers, and hatches...
Rubber tubing, also known as rubber hose or rubber piping, is made of natural and synthetic rubber and is used to circulate and transport liquids and gases for household and industrial uses. The natural or synthetic rubber materials used for the manufacture of rubber tubing...
Urethane casting is the process of injecting polyurethane and additive resins into a soft mold usually made of silicone elastomer. The casting process is similar to injection molding; injection molding differs by using hard, metal molds...
A grommet edging is a flexible rubber or plastic strip that covers rough and sharp surfaces found in openings and edges of panel walls to protect the passing electrical cables, wires, and other sensitive components...