Compression Molding
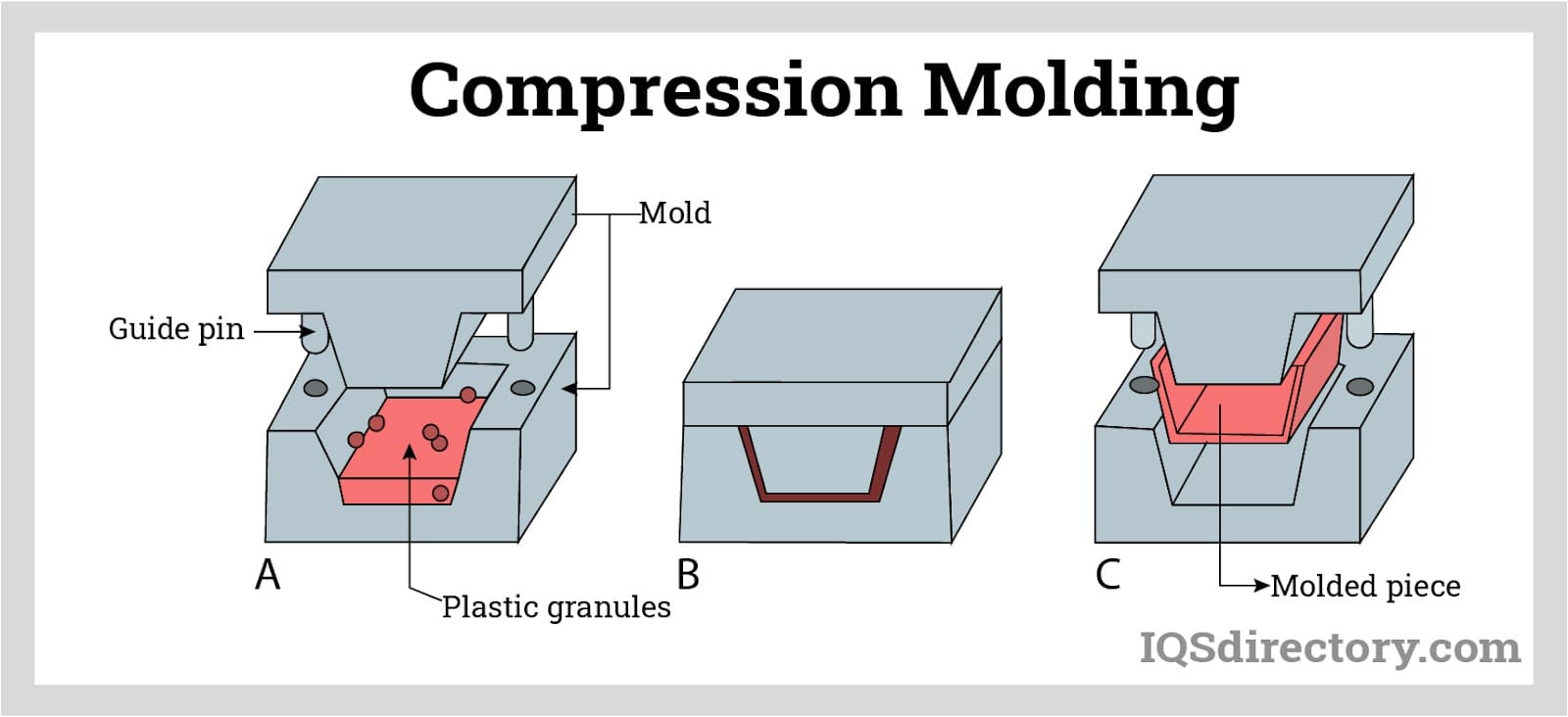
Molding is a manufacturing process that uses a mold - the latter being a solid container used to give shape to a piece of material. It is a forming process. The form is transferred from the mold to the material by...
This article takes an in depth look at grommet edging.
Read further and learn more about:
Grommet edging plays a crucial role in safeguarding electrical cables, wires, and other delicately important components from wear and damage due to contact with rough or sharp edges. Without this essential protection, abrasive contact could lead to data loss, operational disruptions, fires, electric shocks, equipment malfunction, and pose safety threats to personnel.
Most machinery and manufactured products have openings cut or stamped into their structure to allow wires to pass through. These cutting processes often leave metal or plastic panels with rough, abrasive edges.
To protect wiring from these sharp edges, grommet strips, also referred to as trim, are applied directly to panel surfaces, enclosures, or bulkheads.
Grommet strips come in various materials, such as nylon, EPDM, PVC, silicone rubber, polyethylene (PE), and metal spring fasteners encapsulated in a protective layer. One notable distinction is that grommets made of nylon, EPDM, PVC, silicone, and PE generally require adhesives to secure them, whereas those with encapsulated metal spring fasteners do not.
Cable chafing happens when the weight of a cable presses it against the edge it spans, gradually wearing down its insulation. This can lead to the exposure of bare wires, resulting in potential hazards. Grommet edging is engineered to prevent such abrasion by absorbing impacts, reducing vibrations, and limiting heat transfer, helping to decrease the likelihood of wire damage.
While grommets can be installed manually using finger pressure, their adhesion can vary based on the product type, especially when securing them into circular openings, around bends, or along irregular surfaces. For example, nylon grommets often need adhesives and additional securing measures like tape or clamps while the adhesive sets, which can increase production costs and time. Encapsulated metal spring fastening grommets, however, avoid this issue.
Available in diverse sizes to fit different sheet thicknesses, grommet strips can be found in both fixed and continuous lengths, with some manufacturers offering custom lengths upon request.
Grommet edging remains indispensable across nearly all industries producing powered equipment. This includes sectors such as aerospace, automotive, rail, telecommunications, power, medical, construction, military, mining, and forestry, where grommet edging is frequently utilized.
Manufacturers and OEMs depend heavily on grommet edging to prevent chafing, ensuring their equipment operates safely and reliably.
Grommet edging is made from flexible and resilient materials such as nylon, PTFE, EPDM, PVC, silicone rubber, and polyethylene, or from a metal spring clip substrate encapsulated in a polymeric coating.
Grommets typically feature a U-shaped cross-section and often include “fingers” or “castles” along their length. These features enhance the strip’s flexibility and, in the case of encapsulated metal substrate grommets, provide a strong gripping force onto the edge. The main types of grommets fall into these groups:
Initially introduced in the 1940s, these classic grommets are crafted from molded nylon 6/6, such as the Mil Spec MS21266 variant.
Nylon, a type of synthetic thermoplastic polymer, is known for its robustness, dimensional stability, and resistance to abrasion, chemicals, and corrosion. It remains unaffected by UV exposure and functions within a temperature range of -40°F to 122°F (-40°C to 50°C). Nonetheless, over time, nylon and any adhesives used with it may deteriorate. Being hygroscopic, nylon absorbs moisture, which can soften and weaken the grommet. In dry conditions, nylon can lose moisture and become brittle, potentially leading to detachment from the edge.
With a low surface friction, nylon ensures that wire insulation remains intact. Although it can be molded into a strip that adapts to two axes, its molded "fingers" or "castles" do not grip the edge securely, often necessitating the use of adhesives and additional fixturing for proper installation.
When glue is required for performance, installing a nylon grommet like the MS21266 involves a detailed, multi-step procedure. This includes preparing the surface with Scotch-Brite abrasive, cheesecloth, VOC solvent, and disposable gloves, applying the bonding material, and then securing the grommet with tape or clamps. This setup ensures the grommet remains in position as it cures for up to 12 hours. The process concludes with inspections and cleanup, which may involve Hazmat disposal, adding significant time and cost to the overall installation.
Traditionally, OEMs have relied on adhesive to secure nylon grommets due to their tendency to exhibit "coil set" or "straight set," depending on their post-manufacturing treatment. Grommets that are spooled during production often retain a "coil set," causing them to deviate from straight or curved edges, leading to detachment. Conversely, grommets that are not spooled tend to maintain a "straight set," making them resistant to bending, which can be problematic for curved edges or circular penetrations, often resulting in dis-bonding despite adhesive use.
Operational challenges arise when applying glued nylon grommets. Their rigidity can make them difficult to install on burred metal edges, often causing snags and requiring multiple attempts. Once installed, careful inspection is necessary to ensure proper adhesion. The tendency of nylon grommets to dis-bond results in a high rate of rework, increasing costs and compromising quality. Grommets excessively coated in adhesive may not reflect a high-quality, precision product or process.
Considering its limitations, nylon is more suitable for long, straight runs without curves or corners. Even in these cases, adhesive application may still be needed to secure the grommet.
To address these issues, many OEMs are transitioning to encapsulated spring fastening metal substrate grommets, which offer a more reliable solution.
Encapsulated metal grommet edging features a core of spring stainless steel covered with a robust flame-retardant thermoplastic elastomer (TPE), with some variants including an additional cushion for enhanced protection.
The stainless steel core provides excellent edge retention, eliminating the need for adhesive during installation. This results in a 49% reduction in installed costs compared to nylon grommets and glue.
These grommets exhibit outstanding abrasion resistance due to their low friction coefficient. They are also highly resistant to corrosion, water absorption, and are flame-rated to UL94 V-0. In addition, they provide excellent electrical insulation, resist a wide range of chemicals, and are UV stable. They are produced using precision metal stampings and thermoplastic extrusions with a powder-coated finish.
Installation is straightforward and requires only finger pressure—no glue is needed. The spring steel core is designed with angled teeth, or "castles," that grip the edge securely without adhesives.
Made from an optimal stainless alloy that retains its spring flexibility, these grommets can be removed and repositioned multiple times without losing their retention strength. They have been tested for static loads up to 20G on all three axes without the need for adhesives.
The angled "lip" on each castle aids in aligning and installing the grommet onto edges, even if they are rough or burr-laden, making the installation process faster and more efficient. The flexible spring steel prevents issues like coil set and straight set, allowing the grommet to be pre-formed, applied, and adjusted without losing its grip.
This advanced grommet technology delivers top-tier performance at a 49% lower total installed cost compared to nylon, PTFE, or PE grommets with glue, thanks to the elimination of lengthy adhesive preparation, application, fixturing, curing, cleanup, and frequent rework.
EPDM, or ethylene propylene diene monomer, is a type of synthetic rubber classified as M-class under ASTM standard D-1418. It features a saturated polymer backbone and possesses active sites for cross-linking, which provide it with exceptional durability, flexibility, and thermal stability. EPDM is resistant to heat, ultraviolet light, and ozone, making it an excellent electrical insulator. However, it does not perform well with hydrocarbons or halogenated solvents.
Typically extruded with a core of steel wire, EPDM grommets are self-fastening and generally do not require adhesives. They are preferred for covering larger openings and surfaces where a low-profile solution is not necessary but where durable edge protection is needed without stringent environmental performance demands.
Due to its relative stiffness and bulkiness, EPDM is most effective on straight-edge runs. It does not adapt well to sharp corners or irregularly shaped edges with tight radii.
PVC, or polyvinyl chloride, is a synthetic thermoplastic known for its inherent rigidity. It can be made flexible by incorporating plasticizers like phthalates and adipates, while its aluminum core helps maintain good retention without needing adhesives.
Flexible PVC is often used for grommet edging as a cost-effective alternative to synthetic rubber. It boasts high tensile strength, density, and impact resistance. Additionally, PVC serves as a good electrical insulator and resists corrosion and most chemicals.
While PVC has natural flame retardant qualities, in high-temperature electronic applications it can release chlorine gases, which may create corrosive conditions for adjacent metal components. Its design allows for self-fastening applications, typically requiring no adhesives. However, the softer aluminum core, which adds pliability and flexibility to adjust to various sheet thicknesses, also makes it easier to be scraped off an edge.
Due to its stiffness, PVC is best suited for use on straight edges or applications with wide radii, as it does not conform well to sharp corners or irregularly shaped turns.
Silicone rubber, or polydimethylsiloxane, is an inorganic synthetic elastomer renowned for its excellent flexibility and durability. As a thermosetting polymer, it is highly resistant to most chemicals, corrosion, UV radiation, and ozone. Additionally, it serves as an effective insulator and can endure elevated temperatures.
Its high abrasion resistance and low coefficient of friction offer substantial protection for cable insulation against chafing. Similar to EPDM profiles, silicone rubber grommets typically feature a steel wire core and are self-fastening, often eliminating the need for adhesives.
Due to its inherent stiffness, silicone rubber is most effective for use on straight edge runs and does not adapt well to corners or irregularly shaped edges.
Polyethylene is a lightweight, durable thermoplastic known for its good abrasion resistance due to its low coefficient of friction. It exhibits low water absorption, provides excellent electrical insulation, and is compatible with most chemicals, though it does not perform well with hydrocarbons, oils, or oxidizing agents.
Despite its lower cost compared to many other grommet edging materials, polyethylene has limitations such as reduced temperature resistance, susceptibility to UV degradation, and lack of flame retardant properties. These factors have led to a decline in its usage.
The cost advantage of polyethylene is often negated by the need for adhesives to ensure proper attachment and retention, which can raise the overall installation costs.
Additionally, like nylon, polyethylene grommets with their narrow, castellated tips can be challenging to install on sheet metal edges, particularly if the edges are burred. The material's rigidity makes it prone to getting caught, leading to multiple attempts during installation.
Several specialized types of grommet edging cater to specific needs.
Teflon (PTFE) grommets are available in similar forms to nylon ones but are designed for applications involving high temperatures, such as in ovens, engines, or heat shields. PTFE is also useful in applications requiring minimal friction due to its extremely low coefficient of friction. However, PTFE is relatively expensive and typically requires special chemical etching for adhesive bonding to be effective.
All Metal/High Heat: An all-metal grommet is suitable for high-temperature environments and is commonly used in automotive and aerospace sectors, such as in engine heat shields or furnaces. This type of grommet does not need adhesive because the inward-leaning metal "castles" provide the necessary gripping force.
Four critical tests are commonly conducted to assess the performance and reliability of grommets:
A salt spray test provides a quick, standardized method to assess the corrosion resistance of the grommet's polymer strip or coating. During this test, the grommet is placed in a sealed chamber where it is exposed to a dense fog of saltwater. This fog may consist of acetic acid salt, sodium chloride, simulated acid rain, or seawater. The test measures how well the grommet withstands accelerated corrosion, with results typically reported as either pass or fail.
UL94 is a standard developed by Underwriters Laboratories (UL) in the USA, focusing on the safety of plastic materials used in devices and appliances. This test evaluates how materials respond to ignition, specifically how they extinguish or spread flames once ignited. Materials are rated based on their flame-retardant properties, with ratings ranging from the least to the most flame-retardant:
UL94 Rating | Definition |
---|---|
HB | Slow burning on a horizontal part. |
V-2 | Burning stops within 30 seconds on a vertical part. Flaming particle drips are observed. |
V-1 | Burning stops within 30 seconds on a vertical part. Particle drips which are not inflamed are observed. |
V-0 | Burning stops within 10 seconds on a vertical part. Particle drips which are not inflamed are observed. |
5VB | Burning stops within 60 seconds on a vertical part. No particle drips are observed. A burn-through hole is present. |
5VA | Burning stops within 60 seconds on a vertical part. No particle drips are observed. A burn-through hole is not present. |
The Taber Abrasion Test, according to ASTM D 1044, evaluates a material's resistance to abrasion and wear. During this test, a sample with defined dimensions and weight is placed beneath two rotating grinding wheels that apply a specific load. The wheels rotate for a predetermined number of cycles, causing abrasion to the sample.
After the test, the specimen is weighed to measure the amount of material lost due to abrasion. The abrasion resistance is assessed based on the weight loss, the number of cycles, the applied load, and the type of grinding wheel used. For instance, a material might be evaluated based on a weight loss of 8 mg after 5000 cycles with a 1 kg load using a C17 Wheel.
In demanding sectors such as automotive and aerospace, components are subjected to extreme conditions including high levels of vibration, pressure, and acceleration, which can reach up to 20 Gs. It is essential for these components to perform reliably to ensure operational success and the safety of personnel.
The MIL-STD 1344A, Method 2005.1 outlines the standard procedure for testing electrical connectors.
For instance, the Mil Spec grommet M22529/2 from Device Technologies, Inc. was tested under this standard, enduring 8 hours of longitudinal and 8 hours of perpendicular vibration, withstanding forces equivalent to rms G 41.7.
Molding is a manufacturing process that uses a mold - the latter being a solid container used to give shape to a piece of material. It is a forming process. The form is transferred from the mold to the material by...
Rubber injection molding is when uncured rubber is transformed into a usable product by injecting raw rubber material into a mold cavity made of metal. The applied pressure produces a chemical reaction like...
Rubber latches are latches made of rubber or are composed of rubber components. They are used in the automotive, aerospace, and medical equipment industries due to their flexibility, durability, and non-abrasive properties...
Rubber molding is a process of transforming uncured rubber or an elastomer into a usable product by transferring, compressing, or injecting raw rubber material into a metal mold cavity...
There are several methods to perform rubber overmolding, and each method has its own unique advantages and disadvantages. The choice of method typically depends on the design and material requirements of the product being...
Silicone rubber molding is a method for shaping, forming, and fabricating silicone rubber parts and products using a heated mold. The process involves compressing or injecting silicone rubber into a mold...
A rubber bushing is a form of vibration isolator that is placed between two parts to limit the motion between them and absorb, mollify, and buffer the energy produced by their interaction. They are very...
Extruded rubber is a group of products made by softening and pressurizing an elastomeric compound and forcing it to flow through a hard tool called a die. The resulting product is a continuous piece of material that has the same cross-section throughout its length...
Rubber gaskets are elastic components used for mechanically sealing the microscopic gap between two mating surfaces or joints. Examples of these surfaces are flange faces of piping and fittings, mating surfaces of an...
A rubber O ring is a mechanical gasket in the shape of a torus or donut and is used for static and dynamic applications where there is relative motion between parts and the possibility of friction. Some of the benefits of rubber O rings are...
A rubber roller is a machine part that is composed of an inner round shaft or tube covered by an outer layer of elastomer compounds. The inner shaft is made of steel, aluminum alloys, or other strong and rigid material composites...
Rubber sheets are basically sheets made of rubber or cloth that are coated with rubber to improve the mechanical properties of rubber sheeting such as increased tensile strength and reduced elongation...
Rubber to metal bonding is when a rubber part has to be adhered to a metal part, a metal component is chemically prepared and is attached or encapsulated as part of the process to become a bonded rubber part...
Rubber trim is an extruded, sometimes molded, elastomer that is used to protect the edges or surfaces of objects from sudden impacts. They are usually found on panels, windows, doors, removable covers, and hatches...
Rubber tubing, also known as rubber hose or rubber piping, is made of natural and synthetic rubber and is used to circulate and transport liquids and gases for household and industrial uses. The natural or synthetic rubber materials used for the manufacture of rubber tubing...
Urethane casting is the process of injecting polyurethane and additive resins into a soft mold usually made of silicone elastomer. The casting process is similar to injection molding; injection molding differs by using hard, metal molds...