Compression Molding
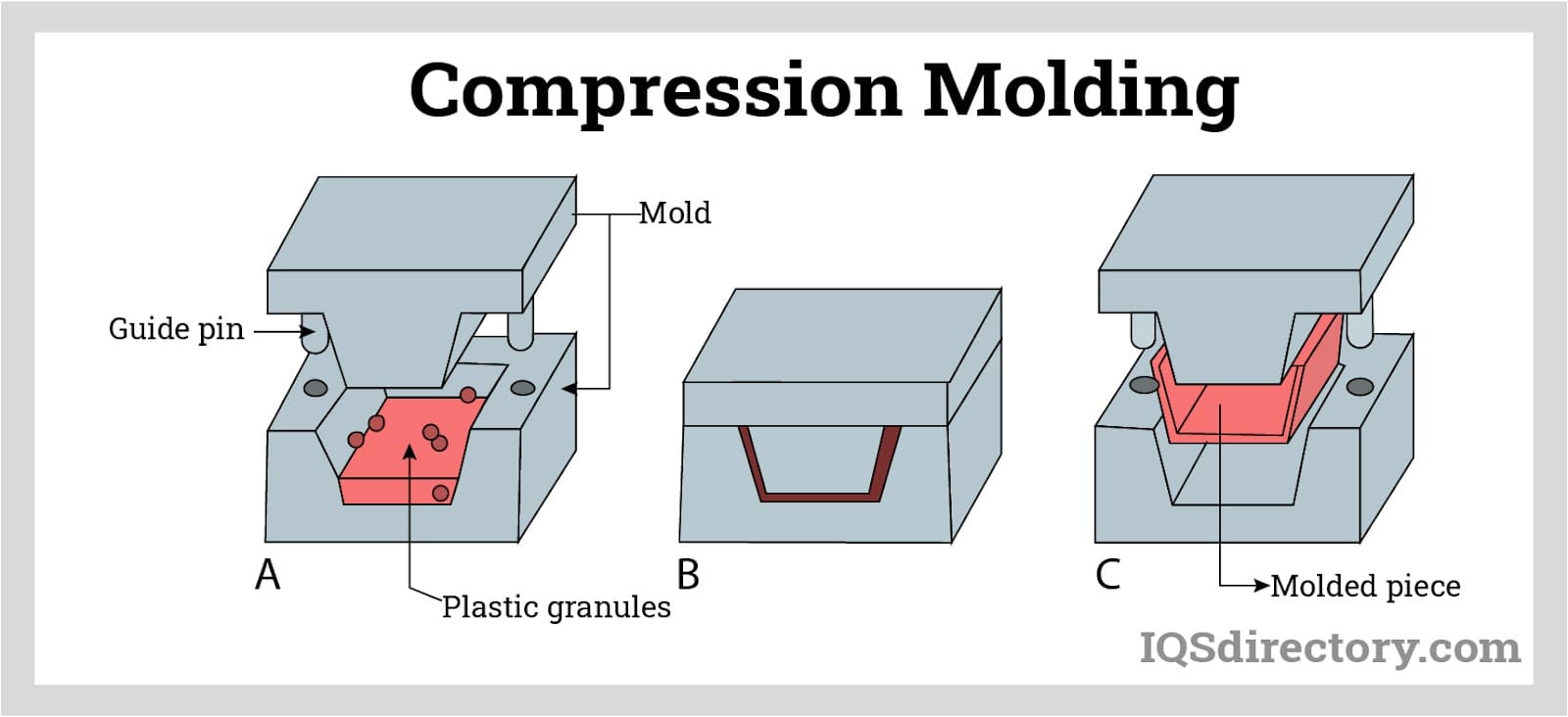
Molding is a manufacturing process that uses a mold - the latter being a solid container used to give shape to a piece of material. It is a forming process. The form is transferred from the mold to the material by...
Please fill out the following form to submit a Request for Quote to any of the following companies listed on Rubber Injection Molding .
This article will take an in-depth look at rubber injection molding.
The article will bring more detail on topics such as:
In this chapter, we will examine the definition of rubber injection molding, survey the various types of rubber materials, and explore the intricacies of the rubber manufacturing process.
Rubber injection molding is the process of converting raw rubber into a finished product by injecting it into a pre-formed metal mold cavity. The procedure uses pressure to initiate a chemical reaction, such as vulcanization or curing, which helps in linking the polymer chains within the rubber material.
The creation of rubber products uses both pressure and heat. As the demand for various components like gaskets, hoses, O-rings, tubing, and grommets grows, manufacturers continually innovate to meet changing product specifications.
The molding process is used for making rubber parts and products, replacing manual shaping. This method allows for chemical reactions in the rubber, enhancing the toughness or resilience of the polymer chains within.
These reactions cause polymer chains to interlink, limiting their independent movement, which enables the rubber to stretch or shrink under stress. Often, heat is used to hasten the curing process, allowing rubber to be precisely molded into complex shapes.
In the design phase, engineers plan the geometry of rubber components to optimize cost efficiency. Placing the parting line with a minimal draft angle is critical to efficient molding. The mold design is a crucial element for part development, greatly influencing the production process's success.
Once designed, molds are created from metals like aluminum, hardened steel, or beryllium-hardened copper. Steel, known for its strength, is often chosen despite its higher initial cost as it proves economically viable in the long run. Computer-aided technology is employed to produce molds with accurate adherence to design specifics.
Using these advanced methods reduces the time needed for mold production. After casting, molds undergo testing to ensure dimensional accuracy and that they meet the original design intentions.
Injection molding is a preferred method for creating finished products requiring specific tolerances and high precision. Initially, the raw rubber is heated until it liquefies, allowing it to flow easily into the mold cavity—this liquid form is often referred to as "gum stock."
Preheating the material reduces the curing duration, allowing for higher curing temperatures. During injection molding, the mold is tightly clamped to prevent flashes. The rubber is delivered to the mold through a barrel and nozzle system that ensures a constant material flow.
The rubber makes its way into the mold through a series of runners and sprues, entering the mold cavity via a gate. The liquified rubber fills the cavity and adheres tightly to the mold's walls, forming the precise desired shape.
This chapter will cover the various types of rubber utilized in injection molding as well as the different injection molding processes for rubber.
The types of rubber used in rubber injection molding are:
Natural rubber is a type of rubber that comes from latex, which is produced by rubber-producing trees. Its tensile strength is very high, and it has friction and abrasion properties that make it an appropriate material for seals, O-rings, diaphragms, dampers, and bumpers. Natural rubber can be used as a coating because it bonds very well with metals.
Nitrile rubber is synthesized from butadiene and acrylonitrile. The production process involves mixing these compounds with an emulsifier and catalyst in a polymerization vessel, which must be maintained at approximately 104°F (40°C) to ensure proper mixing.
Nitrile rubber is known for its outstanding mechanical properties and is widely used in rubber molding due to its excellent resistance to oils, solvents, water, and various fluids. Additionally, nitrile rubber exhibits significant resistance to abrasion and tearing.
Hydrogenated nitrile butadiene rubber (HNBR) is produced through the hydrogenation of NBR, which eliminates the olefinic components prone to degradation. HNBR is highly resistant to petroleum-based oils and offers durability against aliphatic hydrocarbons, silicone oils, petroleum fuels, vegetable oils, salt solutions, greases, water, dilute acids, ethylene glycol, bases, and steam. This makes it especially useful in automotive applications.
This type of rubber, known as ethylene propylene diene monomer (EPDM), is composed of propylene, ethylene, and a diene comonomer, which facilitates cross-linking. The structure of EPDM provides enhanced resistance to light, ozone, and heat, and it can endure high temperatures effectively. Its durability ensures a long service life in various applications. EPDM is commonly used in steam systems, automotive panels, braking systems, and trucks.
Silicone rubber is a versatile material composed of silicon, oxygen, carbon, and hydrogen. The term "silicone rubber" encompasses a range of rubber types distinguished by their chemical structures and organic classifications.
There are various types of silicone rubbers, and these include methyl, fluoro vinyl methyl, methyl phenyl, methyl phenyl vinyl, and methyl vinyl. The silicone rubbers have high resistance and can cope with extremely high temperatures. They are also flexible and are widely used for their weather resistance.
Fluorosilicone is a specialized form of silicone rubber that includes trifluoropropyl groups, providing superior resistance to fuels, chemicals, oils, non-polar solvents, and alkalis. Like silicone, fluorosilicone maintains flexibility across a broad temperature range. It is commonly used in the aerospace industry due to its excellent resistance to petroleum products.
Another name for neoprene rubber is polychloroprene or chloroprene. It is manufactured by the process of emulsion polymerization of chloroprene. The process is aided by the use of a potassium catalyst. Neoprene is used for multiple purposes. Its properties include fire, weather, temperature, and abrasion resistance. Its uses include gaskets, various forms of coating, and hoses. Neoprene is ideal for use in the molding process of rubber due to its versatility, and this does not consider the type of molding being used.
Styrene-butadiene rubber is primarily composed of butadiene with a minor amount of styrene. It is created through copolymerization using the emulsion process. This rubber is known for its excellent resistance to aging, abrasion, and cracking. Its desirable properties make it particularly well-suited for molding applications such as seals, gaskets, and diaphragms.
Fluorocarbon rubber, also known as Viton or fluororubber, is distinguished by its fluorine content, chemical composition, or cross-linking method. Fluorocarbon rubbers are categorized into groups ranging from one to five, each with its specific type of copolymer. Cross-linking in fluorocarbon rubbers can be achieved through diamine, peroxide, or dihydroxy methods. These rubbers are renowned for their exceptional resistance to chemicals and their ability to withstand very high and extreme temperatures, making them ideal for molding applications such as fuel lines, hoses, and O-rings.
Butyl rubber is created through the copolymerization of isobutylene and isoprene, both derived from crude oil or natural gas. The process requires cooling the materials to extremely low temperatures, around -238°F (-150°C), to combine them effectively. Butyl rubber is known for its gas impermeability, making it well-suited for manufacturing seals used in high-pressure and vacuum applications. Additionally, its sound-dampening properties make it useful as a bumper material for various types of equipment.
Urethane rubber, also known as polyurethane rubber, is produced by reacting a polyol with polymeric isocyanate or diisocyanate, along with a catalyst. Due to the variety of polyols and diisocyanates available, different formulations of urethane rubber can be created through various compound combinations. Urethane rubber is commonly used in applications requiring materials with high tensile strength and excellent abrasion resistance.
Thermoplastic elastomers (TPE) are a category of materials that include TPR, TPU, and TPV, combining the properties of plastics and rubbers. TPE is particularly effective for rubber injection molding due to its ability to flow easily when heated, especially under shear force.
During TPE production, physical cross-linking occurs, which allows for easy recycling and reuse of waste material. TPEs are naturally soft, making them well-suited for injection molding. Various grades of TPE are available under different trade names to meet specific application requirements.
Thermoplastic vulcanizate (TPV) is akin to ethylene propylene diene monomer (EPDM) but is a blend of polypropylene and EPDM. During its production, the rubber undergoes vulcanization, which enhances the polymer's durability through cross-linking. This process endows TPV with resistance to compression, fatigue, abrasion, and heat, allowing it to maintain its appearance and properties even after years of use.
The key distinction between TPV and thermoplastic elastomers (TPE), both of which are thermoplastic materials, lies in their chemical composition. TPV, a type of rubber that mimics EPDM, was developed to bridge the gap between plastic and rubber. In contrast, TPE contains a different polymer as a core component of its structure, while TPV incorporates EPDM.
Various specifications are considered to select the appropriate molding process for a particular application. Cost-effective molding solutions are determined by factors such as weight, size, geometry, and material compatibility. Injection molding, originally developed for plastics, has become a widely used and popular method for working with rubber. Engineers have refined the process to achieve greater precision with rubber, leading to several specialized techniques, including organic rubber injection, liquid injection molding, and thermoplastic rubber injection, which are briefly outlined below.
Organic rubber injection heavily depends on the meticulous preparation of materials. Once the rubber is processed and mixed, it is fed into a screw mechanism in precise amounts. When the required quantity of rubber fills the barrel, it is injected into the mold cavities, where it then undergoes curing. One of the benefits of this method is that it eliminates the need for manual insertion of pre-forms and preheats the rubber, which helps to reduce the overall cycle time.
Liquid Silicone Rubber (LSR) injection is the second type of injection molding. This process involves introducing a liquid silicone compound into a mixer, which is then cured and placed into an injection unit. The flow of the prepared silicone is controlled through runners and gates integrated into the mold cavity. The rubber cures within the mold, after which the finished parts are ejected to prepare for the next cycle. A major advantage of LSR injection molding is its closed system, which minimizes contamination. Additionally, the cycle times are significantly reduced. This method is particularly beneficial for manufacturers in the medical industry, who frequently use liquid injection molding for rubber products.
Thermoplastic rubber injection is the third type of rubber injection molding. This method processes elastomers similarly to plastics, offering performance characteristics akin to rubber. The injection molding process for thermoplastic rubber mirrors that of plastic injection molding, eliminating the need for mixing or vulcanizing if traditional rubber materials are not used. Thermoplastic elastomers are recyclable and can be colored during the molding process. However, they are typically suited only for applications that do not involve high temperatures. These injection molding techniques are widely used and available as standard processes, with options for custom rubber injection tailored to specific requirements.
Different manufacturers and businesses have unique requirements for their components. Engineers often face the challenge of developing effective, cost-efficient solutions to meet these needs. Typically, the answer lies in creating custom-made products, which is why the concept of custom rubber injection molding has emerged.
Injected rubber, whether natural or synthetic, can be molded into a wide range of shapes and configurations, enhancing its functionality. Its flexibility and durability enable engineers to design various geometries and cushioning components. Rubber's stability is particularly valuable in applications where it is used to cushion machinery, reducing vibrations and impact.
While natural rubber is commonly used, manufacturers have developed synthetic alternatives that not only match the strength of natural rubber but also offer improved longevity and durability.
Rubber injection molding is utilized in a variety of applications and uses, including:
Rubber bumpers are available in various shapes and sizes and are used in the production of items such as stem, mushroom, tack bumpers, recessed bumpers, and grommets. These bumpers are designed to reduce vibration and movement within equipment, protecting rigid components from damage caused by impact and vibrations.
Rubber bumpers offer protection on work surfaces, circuit boards, furniture, displays, and packaging. The type of material used to manufacture the rubber bumpers includes many polymers resulting from the mixture of plastics and rubber.
Rubber bushings, much like rubber bumpers, are designed to absorb vibrations and impacts in machinery. They are typically shaped and configured to fit specific applications, with the most common design being cylindrical. Rubber bushings are widely used in machinery to reduce vibrations and enhance performance.
Rubber bushings can be installed between two pieces of equipment to prevent the transfer of vibrations from one component to another. They are commonly used in automobiles, bicycles, trucks, and motorcycles to absorb and dampen vibrations caused by uneven road surfaces.
Rubber diaphragms are designed primarily to prevent friction and leakage. Their specific design and geometry enable them to withstand pressure while effectively preventing any liquid leakage.
Rubber diaphragms also serve as barriers between two chambers or enclosures, blocking contaminants from entering. They can be either dynamic or static in form. A dynamic rubber diaphragm responds to even a small amount of pressure to activate its function.
Rubber grommets are ring-shaped components used to protect materials or objects that pass through metal openings. Commonly, they are used where wires or cables pass through holes. Rubber grommets can be made from either natural or synthetic rubber.
Rubber grommets are produced using various molding processes. They are essential in protecting electrical cables from abrasion caused by metal openings. By preventing wear and tear, rubber grommets help avoid short circuits and safeguard the wiring.
Rubber isolators are widely used in the industry to protect machines and equipment from vibration-related damage. They also help maintain machinery in its proper position and level. Rubber isolators encompass various components, including mounts, bumpers, leveling pads, bushings, and shock mounts. Effective vibration control is crucial for the proper operation and longevity of equipment.
Uncontrolled vibrations can cause equipment malfunctions and produce substandard products. Without proper management, vibrations can lead to excessive damage and wear. Rubber vibration isolators are frequently used in residential air conditioning units to reduce noise during operation and enhance overall performance.
Rubber mounts are similar to the aforementioned isolators. They typically consist of two components: an isolator and a fastening mechanism. The fastening mechanism is usually a threaded metal component. The isolator itself is made from either natural or synthetic rubber. Like rubber isolators, rubber mounts come in a variety of shapes, designs, and sizes to suit different applications.
Most rubber mounts are custom-designed to meet specific requirements or applications. For equipment such as transfer systems and conveyor lines, cylindrical mounts are commonly used as supports. Other rubber mounts are employed to support tabletop equipment like printers and computers. Their straightforward design makes rubber mounts easy to maintain and install. The metal threads are engineered for quick attachment to the equipment being supported and protected.
Rubber plugs are designed for specific applications, typically to cover edges and joints of equipment. In certain cases, they are used to seal wires connected to a unit’s intake system. Rubber plugs come in various types, including connector plugs, T-shaped plugs, plus-shaped plugs, and washers. The plus-shaped plug is primarily used to hold components together, while the T-shaped plug is designed for insertion into different types of tubing.
Washer rubber plugs serve a function similar to the T-shaped plugs, but they provide coverage for the entire area surrounding the hole where they are inserted. Connector rubber plugs, on the other hand, are used to protect female threaded connectors from dust and moisture contamination.
Rubber seals are used to protect surfaces, close gaps, and insulate spaces against liquids and water. As a crucial component for many equipment and processes, they can be easily customized to meet specific needs. Rubber seals can be shaped and fitted to be installed as a single unit in various types of equipment.
One important use of rubber seals is found in a process involving the use of pressurized gasses or liquids. Rubber seals come in various forms; for example, they can be a gel, strip, putty, or film and be able to stick and adhere to ceramics, paper, glass, concrete, porous surfaces, and many other different materials.
Rubber pads serve a similar purpose to bumpers, isolators, and mounts by reducing machine noise and controlling vibrations. Designed to insulate machinery, rubber pads protect equipment from potential damage, minimize noise, and manage vibrations effectively. Due to their versatility, rubber pads can be used with both small equipment, such as tabletop mixers, and larger machines, like power generators. They offer a cost-effective and efficient solution for noise reduction in factories with numerous machines. Typically made from synthetic rubbers like nitrile, neoprene, and polychloroprene, rubber pads are also easy to maintain, adding to their practicality and affordability.
Rubber suction cups, also known as vacuum cups, are used in handling systems to manipulate items with flat surfaces, such as metal sheets, glass, tubes, wood panels, or molded parts. These suction cups come in various shapes, sizes, diameters, and rubber materials. The two primary types of rubber suction cups are bellows and flat.
Flat rubber suction cups are typically used for smooth, even surfaces. In contrast, bellows rubber suction cups are designed to handle objects with irregular shapes, such as tubes, vehicle panels, and various molded products. Bellows suction cups offer greater versatility and adaptability compared to flat rubber suction cups.
Rubber washers are disk-shaped components with a central hole. They are used to distribute weight or load evenly, act as wear pads and spacers, reduce vibrations, or secure seals. The dimensions of a rubber washer, including its inner and outer diameters, vary depending on its specific application and intended use.
In pipe connections, rubber washers are commonly used to prevent leaks and secure joints. Their ability to form a tight seal makes them suitable for a wide range of applications and conditions.
Rubber O-rings are circular, ring-shaped seals primarily used to prevent leaks of liquids, lubricants, and other substances within mechanical units. They are also utilized in chemical feed lines and gas lines to provide secure seals. Beyond their leak-stopping capabilities, O-rings are employed to seal connections in various applications. They find extensive use across multiple industries, including aerospace, vacuum flow systems, petrochemical piping, and hydraulic and pneumatic equipment.
Rubber molding plays a crucial role in the rubber production industry due to its ability to manufacture components, designs, and parts tailored to specific application needs. Rubber's exceptional endurance and durability make it an ideal material, capable of withstanding harsh conditions over extended periods.
Rubber injection molding is highly automated, significantly reducing labor costs. This process offers numerous benefits, some of which are outlined below:
Rubber has a broad range of applications across various industries:
Rubber injection molding is defined as a process where uncured rubber is transformed into a usable product by injecting raw rubber material into a mold cavity made of metal. The flexibility of rubber and its durability offers manufacturers and engineers ways to design cushioning components and seals. The rubber molding process is crucial in the rubber manufacturing industry. The reason for its importance is that the designs, configurations, components, and parts can be produced to fit the exact requirements of an application. Over the century, rubber molds and products have been of great significance to humanity. Its application in many sectors and industries has made it safer for people and the machines and appliances they work with. Rubbers have had a great impact on the working industry. New molding processes are being tested to come up with much better and more cost-efficient ways that reduce tooling time and have highly precise results.
Molding is a manufacturing process that uses a mold - the latter being a solid container used to give shape to a piece of material. It is a forming process. The form is transferred from the mold to the material by...
Rubber latches are latches made of rubber or are composed of rubber components. They are used in the automotive, aerospace, and medical equipment industries due to their flexibility, durability, and non-abrasive properties...
Rubber molding is a process of transforming uncured rubber or an elastomer into a usable product by transferring, compressing, or injecting raw rubber material into a metal mold cavity...
There are several methods to perform rubber overmolding, and each method has its own unique advantages and disadvantages. The choice of method typically depends on the design and material requirements of the product being...
Silicone rubber molding is a method for shaping, forming, and fabricating silicone rubber parts and products using a heated mold. The process involves compressing or injecting silicone rubber into a mold...
A rubber bushing is a form of vibration isolator that is placed between two parts to limit the motion between them and absorb, mollify, and buffer the energy produced by their interaction. They are very...
Extruded rubber is a group of products made by softening and pressurizing an elastomeric compound and forcing it to flow through a hard tool called a die. The resulting product is a continuous piece of material that has the same cross-section throughout its length...
Rubber gaskets are elastic components used for mechanically sealing the microscopic gap between two mating surfaces or joints. Examples of these surfaces are flange faces of piping and fittings, mating surfaces of an...
A rubber O ring is a mechanical gasket in the shape of a torus or donut and is used for static and dynamic applications where there is relative motion between parts and the possibility of friction. Some of the benefits of rubber O rings are...
A rubber roller is a machine part that is composed of an inner round shaft or tube covered by an outer layer of elastomer compounds. The inner shaft is made of steel, aluminum alloys, or other strong and rigid material composites...
Rubber sheets are basically sheets made of rubber or cloth that are coated with rubber to improve the mechanical properties of rubber sheeting such as increased tensile strength and reduced elongation...
Rubber to metal bonding is when a rubber part has to be adhered to a metal part, a metal component is chemically prepared and is attached or encapsulated as part of the process to become a bonded rubber part...
Rubber trim is an extruded, sometimes molded, elastomer that is used to protect the edges or surfaces of objects from sudden impacts. They are usually found on panels, windows, doors, removable covers, and hatches...
Rubber tubing, also known as rubber hose or rubber piping, is made of natural and synthetic rubber and is used to circulate and transport liquids and gases for household and industrial uses. The natural or synthetic rubber materials used for the manufacture of rubber tubing...
Urethane casting is the process of injecting polyurethane and additive resins into a soft mold usually made of silicone elastomer. The casting process is similar to injection molding; injection molding differs by using hard, metal molds...
A grommet edging is a flexible rubber or plastic strip that covers rough and sharp surfaces found in openings and edges of panel walls to protect the passing electrical cables, wires, and other sensitive components...