Compression Molding
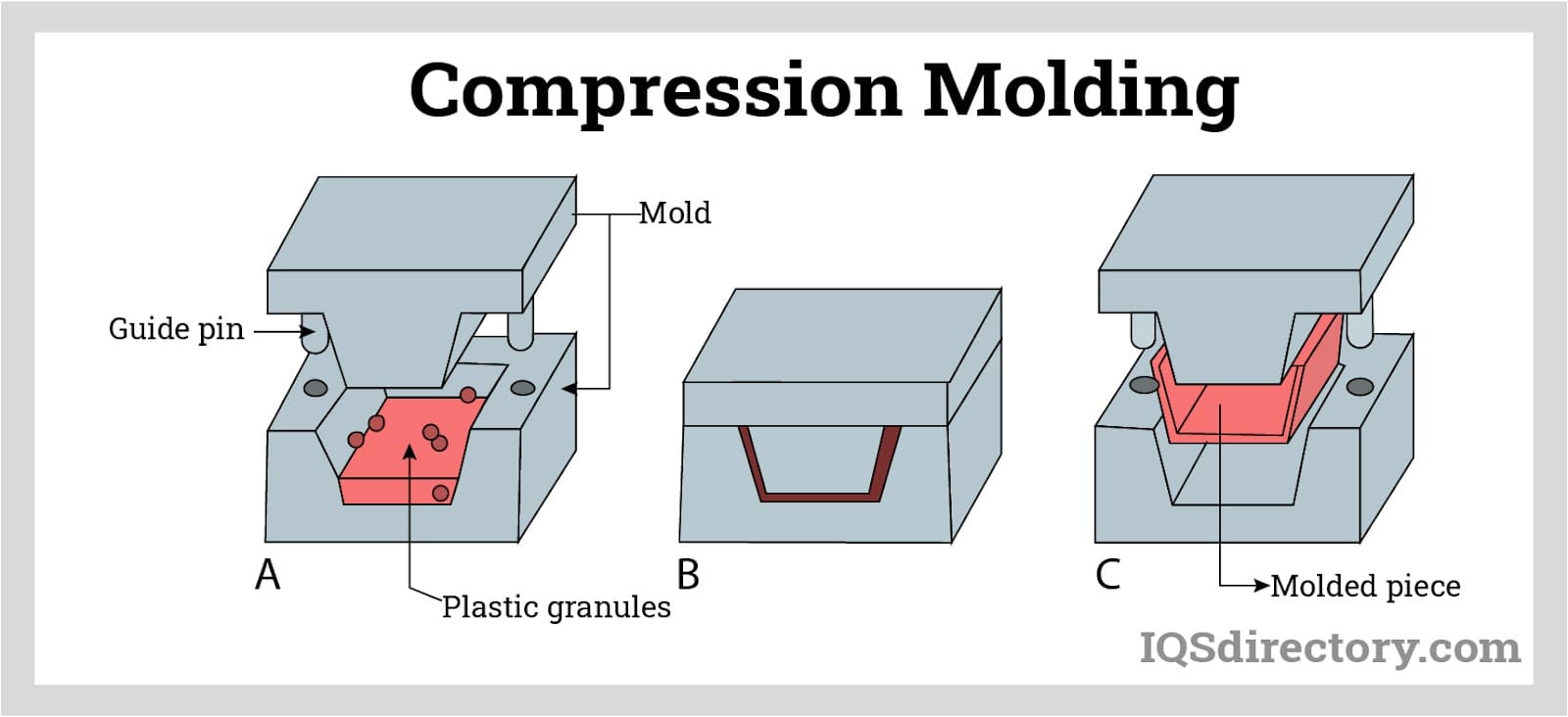
Molding is a manufacturing process that uses a mold - the latter being a solid container used to give shape to a piece of material. It is a forming process. The form is transferred from the mold to the material by...
Please fill out the following form to submit a Request for Quote to any of the following companies listed on Rubber Overmolding .
This article will provide a reader with more information regarding topics, including:
Rubber overmolding can be executed through several techniques, each offering specific benefits and drawbacks. Choosing the right method depends on various factors, including the product's material and design specifics, production scale, budget limitations, and the precision required for the final output.
One of the most frequently employed techniques for rubber overmolding is injection molding. This approach involves injecting molten rubber into a mold that houses the substrate, generally made from either plastic or metal. After the rubber cools and solidifies, the mold is opened to extract the finished piece. Injection molding is favored for its high accuracy and consistency, making it particularly suitable for large-scale production runs with repeated cycles.
Compression molding is also a popular technique for rubber overmolding. This process involves positioning the substrate within a mold, which is then sealed and heated to a designated temperature. Molten rubber is applied, and pressure ensures the rubber contours perfectly with the substrate. Once cooled, the molded product is extracted. This method is ideal for items possessing complex shapes or when dealing with small batch production.
Transfer molding is another effective technique in rubber overmolding, resembling compression molding but incorporating an additional transfer pot. This chamber is filled with molten rubber, which gets injected into the mold through a channel. Transfer molding suits products necessitating high precision and detailed designs.
LIQUID Injection Molding, or LIM, is another rubber overmolding method that involves injecting liquid rubber into a mold where it is cured. Renowned for its rapid cycle times, exceptional precision, and ability to effectively over-mold fragile substrates or electronic parts, LIM is a favored option.
Two-shot molding refers to the process of injecting two distinct materials into a single mold to produce a product. Often utilized for rubber overmolding, it enables the manufacture of products incorporating various layers or segments of different materials. Especially useful for creating intricate designs or multilayered products, two-shot molding can optimize production costs and improve overall efficiency, rendering it a popular choice across numerous industries.
Ultimately, selecting an appropriate rubber overmolding technique involves considering factors like complexity, production needs, precision levels, and budget constraints. Each has its distinct set of benefits and challenges, so making an informed decision depends on the product's specific manufacturing requirements and objectives.
Design considerations are crucial in rubber overmolding, as they directly impact the quality, functionality, performance, and long-term durability of the final product. Whether you’re manufacturing automotive seals, consumer electronics, medical device grips, or industrial equipment handles, understanding the fundamentals of rubber overmolding design is essential for achieving optimal results. Below are the key considerations that should guide every successful rubber overmolding project:
Selecting the right materials for rubber overmolding is essential to achieve a robust and reliable bond between the core substrate and the rubber layer. Important factors to evaluate include the hardness (durometer) of the materials, their thermal expansion properties, and their resistance to chemicals, solvents, and environmental conditions. It's critical to ensure that the selected elastomer is compatible with the underlying plastic or metal substrate, which will promote superior adhesion and long-term product integrity. Popular material choices in rubber overmolding include TPE (thermoplastic elastomers), silicone rubber, EPDM, and natural rubber, each with unique properties suited for specific applications and industries.
The finish of the core component's surface plays a key role in the rubber overmolding process, as it impacts the adhesion strength between the core and the rubber. An uneven or contaminated surface can lead to poor adhesion and a compromised final product. Hence, it's crucial to ensure the core component's surface is smooth and free from imperfections like scratches, burrs, or oil residues. In high-precision applications, pre-treatment techniques such as plasma treatment or applying a primer may be recommended to optimize surface energy and maximize bond strength, especially in challenging environments where reliability is paramount.
Tolerances define the allowable deviations from the core component's specified dimensions. Designing the core component with precise tolerances is critical to ensure that the rubber overmold fits properly and securely. Maintaining tight tolerances ensures a strong interlock and minimizes defects such as flashing, warping, or voids. Inaccurate tolerances can lead to a weak bond between the rubber and the core, causing leaks, separation, or part failure in demanding applications like sealing solutions or electrical overmolded connectors.
Undercuts are areas on the core component's surface that are not aligned with the molding direction, which can complicate the removal of the core from the mold after the rubber overmolding process. It's important to design the core component to minimize or avoid undercuts, or to use advanced molding techniques like mold release agents, collapsible cores, or sliding cores to aid in the core's removal. Proper undercut design streamlines the production process, reduces cycle times, and prevents costly damage to both parts and molds.
The thickness of the rubber overmold significantly affects the final product's strength, durability, and flexibility. Thicker rubber layers offer enhanced impact resistance, vibration dampening, and environmental sealing, which are especially important in the automotive, medical, and industrial sectors. However, excessive wall thickness can increase weight and drive up production costs. Achieving optimal wall thickness is a key aspect of design for manufacturability (DFM), as it ensures a balance between desired performance characteristics and efficient material usage, ultimately controlling manufacturing expense.
Draft angles refer to the angled slopes on the core component's surface designed to ease the removal of the molded part from the mold cavity. Proper draft design is crucial in rubber overmolding to prevent damage, tearing, or distortion of the rubber layer during ejection. Typically, draft angles ranging from 0.5 to 1.5 degrees are recommended, although specific requirements may vary depending on part geometry, elastomer selection, and application needs. Incorporating sufficient draft also enhances mold longevity and reduces maintenance costs.
Beyond the primary elements outlined above, several advanced considerations can further optimize your rubber overmolding project:
In conclusion, paying close attention to these design considerations can dramatically enhance the quality, functionality, and longevity of rubber overmolded components. For manufacturers and engineers, collaborating with experienced rubber overmolding experts and utilizing best practices in both design and material selection is critical to ensuring that the final product aligns with all performance specifications, regulatory standards, and customer requirements. These principles support the success of new product development, cost-effective production, and long-term product reliability in the competitive rubber molding industry.
Rubber overmolding generally involves various types and grades of rubber materials, each providing distinct properties and benefits. The selection of rubber type and grade depends on the specific needs of the end product and its intended application. Understanding the range of available elastomers and their suitability is essential for achieving optimal performance, quality, and durability in overmolded components. Below are some of the most frequently used types and grades of rubber in the overmolding process, along with insights into how industries select these materials based on end-use requirements, regulatory standards, and user expectations.
Silicone rubber is a popular choice for rubber overmolding applications because it offers high thermal stability, chemical resistance, and flexibility. As an elastomer, it delivers excellent resilience over a broad temperature range and is highly resistant to aging, weathering, and UV exposure. Its non-reactive and biocompatible nature makes it suitable for injection molding in medical, food-grade, and electronics applications. Manufacturers in the healthcare and consumer goods sectors favor silicone rubber for overmolded parts such as seals, medical device handles, and waterproof enclosures due to its easy sterilization and non-toxic properties.
EPDM (Ethylene Propylene Diene Monomer) rubber is commonly used in rubber overmolding due to its superior resistance to weathering, ozone, and UV rays. This synthetic rubber type offers excellent performance in outdoor and automotive applications, especially where exposure to harsh environmental conditions is a concern. EPDM shows outstanding flexibility at low temperatures and strong resistance to water and steam, making it ideal for weather seals, window gaskets, door seals, and general-purpose overmolded products in the transportation and construction industries.
Neoprene rubber is a synthetic rubber that offers excellent resistance to oil, chemicals, and heat. It is often used in industrial applications where resistance to harsh environments is required. Neoprene is valued for its flame resistance, durability, and moderate weather and ozone resistance, which make it a preferred material for overmolded cable jackets, keypads, grips, and protective boots. Its flexibility and vibration damping properties further contribute to its use in demanding industrial and automotive overmolding applications.
Natural rubber is a flexible and durable material that is made from the sap of rubber trees. It offers excellent elasticity and tear resistance, making it suitable for applications such as seals, gaskets, and hoses. This type of elastomer is prized for its high tensile strength and abrasion resistance, which are critical in dynamic components subject to repeated flexing and load. Overmolded products made from natural rubber are commonly found in vibration-isolation mounts, adaptive grips, and cushioning pads in both industrial equipment and consumer products.
Nitrile rubber is a synthetic rubber that offers excellent resistance to oils, fuels, and chemicals. It is often used in automotive and industrial applications where resistance to harsh environments is required. Nitrile’s superior oil and fuel resistance makes it an ideal candidate for overmolded seals, grommets, fuel-system components, and o-rings, as well as applications in the hydraulics and oil & gas industries. Its versatility enables manufacturers to meet demanding specifications for fluid containment and safety-critical assemblies.
In addition to the common elastomers above, custom rubber overmolding may utilize specialty polymers such as Fluoroelastomer (Viton), Butyl, and Thermoplastic Elastomers (TPEs). These offer unique combinations of chemical resistance, temperature tolerance, and mechanical performance. Thermoplastic elastomers, in particular, are increasingly used in overmolding because they combine the benefits of rubber-like flexibility with traditional thermoplastic processing, enabling complex part geometries and compatibility with various substrate materials.
Having discussed the various rubber materials used in overmolding, it’s important to delve into the different grades of rubber employed in this process. Rubber grades are typically defined by standards set forth by organizations such as the American Society for Testing and Materials (ASTM) and the Society of Automotive Engineers (SAE). These standards specify rubber material grades based on factors such as heat resistance, oil resistance, weathering, tensile strength, and other critical performance criteria. Engineers and product designers often refer to these standards during the selection process to ensure that the chosen material matches end-use requirements and compliance guidelines for regulated industries.
The ASTM D2000 standard is a key reference for defining rubber grades. This standard outlines a comprehensive range of specifications and assigns a letter-number combination to each grade. The letter indicates the type of elastomer, while the number represents the material's quality level and key properties, such as hardness, compression set, elongation, and low-temperature resistance.
For instance, "S" stands for silicone elastomer, and "N" indicates nitrile elastomer. The numerical designation reflects specific performance attributes like tensile strength, elongation, and compression set. Understanding these designations is vital when custom-creating overmolded components that demand precise functional and mechanical properties to guarantee performance, safety, and service life.
Choosing the appropriate rubber grade is crucial for the performance and longevity of a rubber overmolded product. High-grade rubber may be necessary for applications demanding significant resistance to temperature extremes, chemicals, or UV light, such as aerospace parts, medical devices, or electrical insulation. Conversely, a lower-grade rubber might be adequate for less demanding applications, helping to reduce costs while maintaining necessary performance standards for consumer or light-duty products.
During the evaluation stage, users often compare grades based on factors like compression set, aging resistance, cost, and certification requirements. It is recommended to work closely with a material specialist or experienced rubber overmolding manufacturer to confirm that the selected rubber type and grade align with all functional, regulatory, and economic considerations for your project.
In conclusion, the variety of rubber types and grades available for overmolding each offer distinct benefits, material characteristics, and processing advantages. The selection of the right rubber material and grade is driven by the specific requirements of the intended application, with rubber grades serving as an indicator of material quality, compliance, and expected performance. For tailored applications or exacting industry needs, engaging a knowledgeable supplier or engineering consultancy can significantly improve product outcomes and lifecycle value. For more information on sourcing or customizing rubber overmolded products, consult an industry expert or refer to established standards such as ASTM D2000 for material specifications.
Regulations and guidelines governing rubber overmolding primarily focus on ensuring consumer safety and maintaining product quality. Although there isn't a dedicated set of regulations for rubber overmolding itself, the broader use of rubber materials in various sectors has long been regulated. Here are some key rules and standards pertinent to rubber overmolding:
The RoHS Directive is a regulation from the European Union that limits the use of specific hazardous substances in electrical and electronic equipment. This directive is relevant to rubber materials incorporated into products like cables and electronic components used in rubber overmolding.
REACH is another EU regulation that mandates the registration and assessment of chemicals used in manufacturing. This regulation impacts rubber materials in a broad spectrum of products, including those utilized in rubber overmolding.
The FDA oversees the use of rubber materials in products that come into contact with food, pharmaceuticals, and medical devices. This includes rubber materials used in seals, gaskets, and hoses that may be involved in rubber overmolding.
ASTM sets forth standards for rubber materials used across various products. These standards encompass characteristics such as hardness, tensile strength, and elongation, helping to ensure that rubber materials in rubber overmolding adhere to specific quality and performance benchmarks.
ISO provides standards for rubber materials used in multiple industries. These standards cover attributes like temperature resistance, chemical resistance, and mechanical properties, ensuring that rubber materials in rubber overmolding meet established industry criteria.
In summary, regulations concerning rubber overmolding are designed to ensure safety and quality. They include the RoHS Directive, REACH Regulation, FDA regulations, ASTM standards, and ISO standards, among others. Adherence to these regulations is often mandatory across various industries, with non-compliance potentially leading to legal and financial repercussions for manufacturers.
Quality control is essential in rubber overmolding to ensure that the finished product conforms to the required specifications and standards. Here are some important elements of quality control in rubber overmolding:
Monitoring and controlling the temperature and pressure during the molding process are critical for ensuring that the final product meets quality standards. These factors can significantly influence the consistency and performance of the molded parts, so maintaining precise conditions is essential for achieving reliable results.
The final product's surface finish is crucial as it influences its visual appeal, functionality, and durability. It is necessary to check each part's surface finish to confirm it aligns with the required standards.
Dimensional accuracy measures how well the final product conforms to the specified dimensions. Any deviation can impact the product's functionality and performance. Hence, verifying the dimensional accuracy of each part is essential to ensure it meets the intended specifications.
The material properties of the finished product, including hardness, chemical resistance, and tensile strength, are vital for its performance and longevity. Testing these properties is important to confirm that they adhere to the specified standards.
Performance testing involves evaluating the final product to ensure it meets expected performance criteria, such as grip strength, durability, and resistance to vibration. This testing may simulate real-world conditions, including extreme temperatures, high humidity, or impact scenarios.
Various inspection methods can be employed to verify the quality of rubber overmolded parts, such as visual checks, dimensional measurements, and material assessments. These techniques are essential for detecting defects and ensuring the product meets quality standards.
Maintaining documentation and traceability is crucial for quality control, providing a record of the manufacturing process and facilitating the identification and resolution of any issues. Manufacturers should document each part's design specifications, materials used, and any inspections or tests conducted.
In conclusion, quality control in rubber overmolding is vital for ensuring the final product's consistency, functionality, and durability. A robust quality control program should include monitoring molding conditions, checking surface finishes and dimensional accuracy, testing material properties and performance, utilizing suitable inspection techniques, and keeping comprehensive documentation and traceability records.
In addition to the design considerations, quality control factors, and other aspects previously discussed regarding rubber overmolding, there are additional factors to consider when selecting rubber overmolding, including:
Tooling is crucial in rubber overmolding as it determines the final shape and dimensions of the product. It is essential for manufacturers to design and construct the tooling with precision to endure the stresses of the molding process and ensure the production of high-quality parts.
Rubber overmolding can be costly due to the complexity of tooling and the need for specialized equipment. It is important for manufacturers to evaluate the costs associated with materials, tooling, and labor when deciding whether rubber overmolding is the right choice for a given product.
The environmental impact of rubber overmolding involves the use of chemicals and energy throughout the manufacturing process. Manufacturers should explore methods to reduce this impact, such as incorporating eco-friendly materials and adopting sustainable processes.
By addressing these additional considerations, manufacturers can enhance their rubber overmolding practices and produce parts that fulfill customer requirements while optimizing cost and environmental impact.
While rubber overmolding provides numerous advantages, it also has some drawbacks and limitations that should be taken into account when determining if this process is suitable for a specific application. Here are some of the key negatives and limitations of rubber overmolding:
Rubber overmolding often necessitates specialized equipment and tooling, which can be costly to produce. This can be a significant obstacle for manufacturers, especially those involved in low-volume production runs.
The design of the final product is constrained by the tooling used in the overmolding process. Modifications to the design might require new tooling, which can be both expensive and time-consuming.
For a strong bond between the overmolded materials, they must be compatible with each other. This can be challenging, particularly when using different types of rubber or materials with varying chemical properties.
Rubber overmolding may not be ideal for high production volumes due to the slow and labor-intensive nature of the process.
Although various rubber materials are available for overmolding, some may not be appropriate for specific applications based on factors such as temperature or chemical resistance.
Maintaining consistent quality can be challenging with rubber overmolding, especially in large-scale production. Effective quality control measures are essential to ensure each product meets the necessary specifications.
In conclusion, while rubber overmolding has many benefits, it also presents some negatives and limitations, including high tooling costs, restricted design flexibility, material compatibility issues, limited production volume, restricted material options, and quality control challenges. Manufacturers need to weigh these factors carefully when considering rubber overmolding for a particular application.
Rubber overmolding provides several advantages, making it a favored method in various manufacturing applications. Some of the key benefits of rubber overmolding include:
Rubber overmolding can boost product performance by offering features such as a non-slip grip, shock absorption, vibration dampening, and increased durability. These benefits contribute to greater comfort, safety, and longevity of the product.
This process allows for the integration of multiple materials into a single part, which enhances design flexibility. It enables the creation of more intricate and innovative designs that might not be achievable with other manufacturing methods.
Rubber overmolding can be a cost-effective method, especially for high-volume production. By eliminating the need for additional assembly and minimizing waste, it helps lower overall production costs.
This technique can also improve a product’s appearance by incorporating colors, textures, and decorative elements. Such enhancements make products more attractive and distinguishable in the market.
Rubber overmolding can enhance the ergonomics of a product by offering a comfortable, non-slip grip. This is particularly beneficial for products used over extended periods, as it reduces user fatigue and improves performance.
By adding a protective layer, rubber overmolding can enhance a product’s durability, making it more resistant to wear and tear. This prolongs the product’s lifespan and reduces maintenance or replacement needs.
Rubber overmolding provides effective waterproofing, which is crucial for products exposed to moisture or other liquids. This is especially important for electronics and outdoor equipment used in wet or humid conditions.
This process can help lower noise levels by dampening vibrations and providing cushioning. It is particularly useful for products that generate noise, such as power tools or machinery.
Rubber overmolding offers thermal insulation, protecting sensitive components from extreme temperatures and improving product performance in challenging environments.
In summary, rubber overmolding presents a broad array of benefits that enhance the performance, durability, appearance, and functionality of products. The versatility and flexibility of this process make it a popular choice across various industries.
Rubber overmolding finds applications across diverse industries, such as automotive, medical, consumer electronics, and industrial equipment. Here are some examples of its use in these and other fields:
In automotive applications, rubber overmolding enhances grip and comfort, while also reducing noise and vibration. Components such as steering wheels, shift knobs, and door handles often feature rubber overmolding. Additionally, rubber overmolded seals are used to prevent water and air leaks in various automotive parts.
In medical equipment, rubber overmolding is utilized to offer a secure and comfortable grip for users. Examples of medical products featuring rubber overmolding include surgical instruments, handles for medical devices, and dental tools.
In consumer electronics, rubber overmolding enhances the grip and durability of various products. Common examples include cell phone cases, computer mice, and remote controls.
In industrial equipment, rubber overmolding is employed to enhance grip and minimize vibration. This includes applications such as tool handles, hand grips for machinery, and control panels for heavy equipment.
In the aerospace industry, rubber overmolding is utilized to improve the grip and durability of various components, including cockpit controls, aircraft handles, and switches. It is also applied to airframe components to offer a non-slip surface for maintenance personnel.
In the sports and recreation industry, rubber overmolding enhances grip and comfort for users. This application includes items like golf club handles, bicycle grips, and fishing rod handles. Additionally, it is used in exercise equipment, such as weightlifting bars, to minimize vibration and improve grip.
In the toy industry, rubber overmolding is utilized to enhance the safety and durability of toys. Examples include balls, action figures, and toy vehicles. This technique provides a non-slip surface, making it easier and safer for children to handle the toys, thereby reducing the risk of accidents.
Rubber overmolding is utilized in military and defense equipment to ensure a secure and comfortable grip for soldiers. This process is applied to items like firearm grips, knife handles, and tactical gear. Additionally, military vehicles benefit from rubber overmolding to minimize vibration and improve grip.
In summary, rubber overmolding is a highly adaptable manufacturing technique that delivers a range of advantages across different industries. It boosts the functionality and durability of products, enhances grip and comfort, and reduces noise and vibration.
The outlook for rubber overmolding is promising, with numerous benefits that appeal to both manufacturers and consumers. Several potential advancements could influence the future trajectory of rubber overmolding:
With the introduction of new materials, rubber overmolding might be used to produce composite products with enhanced properties beyond current capabilities. For instance, integrating rubber with conductive materials could open up innovative applications within the electronics sector.
Improvements in automation technology could enhance the efficiency and cost-effectiveness of the rubber overmolding process. This could expand the range of applications for rubber overmolding, making it more accessible and affordable for manufacturers.
As sustainability becomes a higher priority for manufacturers, rubber overmolding might evolve into a more eco-friendly option. Utilizing recycled rubber materials in the overmolding process could help minimize waste and reduce the overall carbon footprint of production.
Progress in 3D printing technology could introduce new opportunities for rubber overmolding. For example, 3D printed molds could simplify and lower the cost of creating custom rubber overmolded products, offering greater design flexibility.
In conclusion, the future of rubber overmolding is poised to benefit from technological advancements and a stronger emphasis on sustainability. As industries continue to recognize the advantages of rubber overmolding, its popularity is expected to grow in the coming years.
In conclusion, rubber overmolding is a versatile manufacturing process that has many applications in various industries. Understanding the different processes used, the types and grades of rubber, and the rules and regulations governing the process is essential for producing high-quality, durable products. While there are some limitations and negatives to consider, the benefits of rubber overmolding make it an effective and efficient way to improve product functionality, durability, and safety for both today and the foreseeable future.
Molding is a manufacturing process that uses a mold - the latter being a solid container used to give shape to a piece of material. It is a forming process. The form is transferred from the mold to the material by...
Rubber injection molding is when uncured rubber is transformed into a usable product by injecting raw rubber material into a mold cavity made of metal. The applied pressure produces a chemical reaction like...
Rubber latches are latches made of rubber or are composed of rubber components. They are used in the automotive, aerospace, and medical equipment industries due to their flexibility, durability, and non-abrasive properties...
Rubber molding is a process of transforming uncured rubber or an elastomer into a usable product by transferring, compressing, or injecting raw rubber material into a metal mold cavity...
Silicone rubber molding is a method for shaping, forming, and fabricating silicone rubber parts and products using a heated mold. The process involves compressing or injecting silicone rubber into a mold...
A rubber bushing is a form of vibration isolator that is placed between two parts to limit the motion between them and absorb, mollify, and buffer the energy produced by their interaction. They are very...
Extruded rubber is a group of products made by softening and pressurizing an elastomeric compound and forcing it to flow through a hard tool called a die. The resulting product is a continuous piece of material that has the same cross-section throughout its length...
Rubber gaskets are elastic components used for mechanically sealing the microscopic gap between two mating surfaces or joints. Examples of these surfaces are flange faces of piping and fittings, mating surfaces of an...
A rubber O ring is a mechanical gasket in the shape of a torus or donut and is used for static and dynamic applications where there is relative motion between parts and the possibility of friction. Some of the benefits of rubber O rings are...
A rubber roller is a machine part that is composed of an inner round shaft or tube covered by an outer layer of elastomer compounds. The inner shaft is made of steel, aluminum alloys, or other strong and rigid material composites...
Rubber sheets are basically sheets made of rubber or cloth that are coated with rubber to improve the mechanical properties of rubber sheeting such as increased tensile strength and reduced elongation...
Rubber to metal bonding is when a rubber part has to be adhered to a metal part, a metal component is chemically prepared and is attached or encapsulated as part of the process to become a bonded rubber part...
Rubber trim is an extruded, sometimes molded, elastomer that is used to protect the edges or surfaces of objects from sudden impacts. They are usually found on panels, windows, doors, removable covers, and hatches...
Rubber tubing, also known as rubber hose or rubber piping, is made of natural and synthetic rubber and is used to circulate and transport liquids and gases for household and industrial uses. The natural or synthetic rubber materials used for the manufacture of rubber tubing...
Urethane casting is the process of injecting polyurethane and additive resins into a soft mold usually made of silicone elastomer. The casting process is similar to injection molding; injection molding differs by using hard, metal molds...
A grommet edging is a flexible rubber or plastic strip that covers rough and sharp surfaces found in openings and edges of panel walls to protect the passing electrical cables, wires, and other sensitive components...