Compression Molding
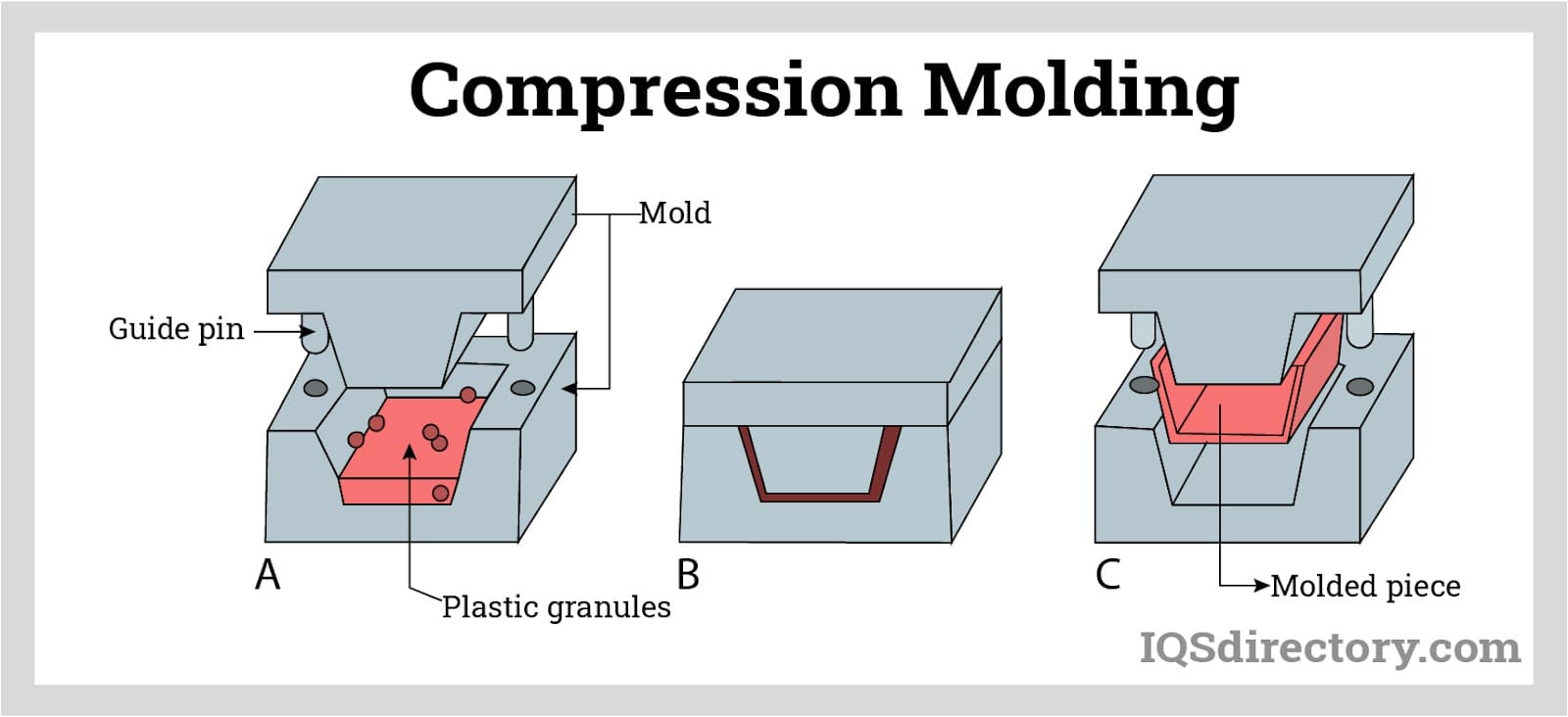
Molding is a manufacturing process that uses a mold - the latter being a solid container used to give shape to a piece of material. It is a forming process. The form is transferred from the mold to the material by...
Please fill out the following form to submit a Request for Quote to any of the following companies listed on
This article will take an in-depth look at rubber to metal bonding.
The article will bring more understanding on topics such as:
This chapter delves into the fundamentals of rubber-to-metal bonding, highlights the traits of bonded rubber, and explores various techniques for adhering rubber to metal surfaces.
The rubber-to-metal bonding process is essential for creating a robust and long-lasting link between rubber and metal parts. This procedure commonly uses adhesives such as rubber-based adhesives, silicone-based glues, two-part adhesives, polyurethane solutions, and epoxy resins.
Rubber-based adhesives are extensively utilized due to their superior bonding strength and flexibility. For applications requiring very strong and stable bonds, two-component adhesives along with polyurethane solutions are the top choice. The specific bonding agent is selected based on the environmental conditions where the part will be used and the manufacturing industry's requirements.
Methods such as molding and adhesion are avenues for combining metal and rubber. The selection of a suitable process depends on considerations like production quantity, space requirements, manufacturing speed, and cost of equipment.
Several molding processes are available, as detailed below:
Over molding entails coating a metal substrate with rubber to create a component where both elements are apparent. This method allows for multiple layers, if necessary, and is widely used in manufacturing seals.
During complete encapsulation, a metal insert is placed first within a mold before adding rubber. This is commonly known as insert molding, resulting in a component where the metal is minimally visible. It is particularly prevalent in parts such as o-rings where wiring is involved.
Transfer molding and injection molding are the two predominant methods used in rubber-to-metal bonding processes.
Transfer molding involves inserting metal parts into a preheated mold. Solid rubber is then forced into the mold by a heated plunger, enveloping the metal components to form a bond.
This setup is subsequently cured and vulcanized under conditions of high heat and pressure.
In this approach, akin to transfer molding, a metal part is set into the mold during the initial phase.
A liquid elastomer is then injected into the mold, and after curing and vulcanization, the part is extracted.
Compression molding is a closed-mold technique that requires placing an uncured rubber preform or shape into a heated mold cavity. High-pressure clamps force the rubber to fit the mold, where it cures under the applied heat and pressure, conforming to the mold's design.
After the curing phase is completed, the rubber solidifies and is ejected from the mold, followed by trimming and testing procedures.
The essential steps for rubber to metal bonding are as follows:
Vibration isolation mounts are primarily fabricated using natural rubber or neoprene. After receiving the raw rubber or neoprene, various additives and fillers are blended to attain specified qualities. The rubber is processed through rollers to ensure even distribution of these ingredients.
The mixed rubber is then shaped into pellets to facilitate the transfer molding process or cut into strips for injection molding. Before curing in the molding process, the rubber is kept in a climate-controlled setting.
Post-vulcanization, natural rubber boasts excellent mechanical traits, including high tensile strength, abrasion resistance, and impact durability, suitable for environments between -40°F and 190°F.
Produced by polymerizing chloroprene, neoprene shares similar mechanical traits after curing but excels in oil resistance, suitable for use from -30°F to 212°F. Neoprene and natural rubber find common usage in industries dealing with pumps and similar components.
A slightly coarse and oil-free metal surface is crucial for effective bonding. Phosphate dipping is commonly used to remove oil and prepare the surface, adding a rust-resistant layer. Alternatives include grit blasting, tumble blasting, or wiping the surface clean.
To remove oils, alkaline cleaning or solvent degreasing methods are recommended. Any rust or debris should be eliminated via aluminum oxide grit blasting or machining. Post-cleaning, metal parts require storage in a low-humidity environment for protection.
Diverse metals like steel, aluminum, brass, beryllium, and copper are employed in rubber-to-metal bonding, chosen based on application demands and working environments for economical yet durable solutions.
Once cleaned, the metal surfaces are ready for adhesive application. A typical two-layer adhesive system, comprising a primer base and an adhesive topcoat, is applied when bonding rubber or neoprene to low carbon steel.
The primer is administered through techniques like dipping, rolling, spraying, or brushing to achieve a dry primer layer thickness of 0.2 to 0.4 mil and an adhesive layer thickness of 0.5 to 1 mil. Stirring before application ensures optimal ingredient distribution.
Components should dry at room temperature but can use a circulating air oven to expedite this. Molding should proceed as soon as components dry to prevent surface contamination.
Natural rubber and neoprene typically use transfer or injection molding at temperatures soaring to 340°F. Components with the two-layer adhesive system are inserted into these heated molds for processing.
Completion of the molding process entails quality assessment. Sample pieces from a production batch undergo breaking to meet tensile strength standards, with breaks in the rubber rather than the bond. A load deflection test may also occur to verify accuracy.
Offering a continuous surface alternative, bonded rubber is created from larger pieces for an organic aesthetic in exterior uses, combining rubber mulch with a binding compound smoothed manually. Its enhanced characteristics make it superior for safety, shock absorption, and satisfying ASTM fall height norms.
Aside from consistent impact resistance, bonded rubber possesses slip-resistant properties and remains in place without scattering, reducing hazards in pathways. It stands resilient in humid conditions or low temperatures, thanks to its durable nature.
This non-toxic material resists microbial growth and boasts longevity, often surpassing cheaper alternatives in maintenance and lifespan, offering high design versatility, making it suitable for playgrounds or trails in recreational areas.
Bonded rubber's natural visuals stem from its mulch-like form, available in varied dyed colors, more so than poured rubber materials.
Material properties influence the balance of rigidity and flexibility, impacting adhesive choice for rubber-to-metal bonds. The application scope and bonding surface size dictate the ideal adhesive for securing an effective bond.
For compact areas, cyanoacrylate superglues prove effective, whereas larger surfaces benefit from two-part adhesives. Polychloroprene-based contact adhesives handle expansive areas like square meters effectively.
Surface pre-treatment is crucial for cohesive bonding, involving solvent cleaning or using cleansers to rid surfaces of residues. Sanding may be necessary for coated metals. Despite precautions, predicting bond durability is complex due to potential rubber degradation.
Testing a small sample with the adhesive first is recommended to evaluate effectiveness before full application. Once cured, the adhesive allows for further modifications, such as drilling, while also efficiently filling in imperfections such as cracks or holes, particularly useful for aluminum assemblies.
This chapter will cover rubber bonding techniques, the various rubber products available, and the specifics of silicone bonding.
Proper surface preparation is crucial for successful rubber-to-metal bonding. Contamination of the surface can occur during the bonding process due to improper application of the adhesive. Every step in the bonding process must be handled meticulously to ensure a strong and secure bond. Understanding the bonding agent, the type of metal, and the specific process is essential for successful bonding.
Before proceeding with rubber bonding, it is necessary to use a solvent degreaser to remove any mold release agents, slip additives, or other processing lubricants from the surfaces. A quick wipe with isopropanol alcohol is often effective. Acetone can also be used, but its aggressive nature may attack some types of rubber, so caution is required.
Even after wiping the surface clean, rubbers may still contain plasticizers that can migrate back to the surface over time, potentially leading to debonding at a later stage.
Cyanoacrylate instant adhesives are generally more effective for bonding rubber compared to epoxies. Epoxies can often peel the rubber off a surface. Cyanoacrylate adhesives cure quickly, allowing for immediate assessment of their effectiveness. It is best to apply a small amount and ensure that the components are tightly aligned and pressed together during the curing process.
Types of rubbers such as natural rubber, silicone rubber, and EPDM can be challenging to bond, often resulting in joints that fail even after ample curing time. For difficult rubbers like EPDM and natural rubber, specialist cyanoacrylate adhesives, such as Permabond 105, are recommended. These adhesives can effectively bond without the need for a primer. For silicone rubber bonding, it is advisable to use a primer like Permabond POP in conjunction with Permabond 105. For applications requiring flexibility, Permabond 2050 Cyanoacrylate is recommended. This adhesive maintains flexibility in the joint, which is especially useful for bonding soft o-rings.
While cyanoacrylate adhesives offer several advantages, they are not the only option for rubber bonding. Their benefits include excellent adhesion, which often results in the rubber tearing rather than the bond breaking. The rapid curing time of cyanoacrylate makes it ideal for high-speed assembly processes on production lines. However, drawbacks include its inability to realign joints after bonding, as it sets in seconds. Additionally, cyanoacrylate has a limited gap-filling capacity (up to 0.5mm) and cannot cover large areas effectively. Its strong odor can be off-putting, which is why contact adhesives might be preferable for larger surfaces, though they can also be challenging to align.
For a cost-effective bonding solution, solvent-based rubber bonders can be used. However, silicone-based adhesives are better for silicone rubber bonding, though they can be messy and slow to cure, making them less suitable for rapid production lines.
Permabond TA46XX series are two-part structural acrylic adhesives designed for bonding difficult plastics such as polypropylene, polyethylene, and PTFE. These adhesives also provide good adhesion to some rubbers, though not to silicone rubber. Compared to cyanoacrylate, structural acrylics offer accurate alignment and spreading due to their slower cure time. They are not solvent-based and have a less pungent odor. The TA46XX series is also suitable for applications where rubbers may later be submerged in water, thanks to their excellent environmental durability.
Rubber products are typically categorized into three major classes: tires, industrial rubber goods used in motor vehicle and ship construction, and consumer goods such as footwear and mats. These products are made from various forms of rubber, including hard, raw rubber, latexes used for seamless gloves with thin walls, rubber threads, and foam rubber used in automotive seats and furniture.
The production of rubber products from raw rubber involves two main stages. In the preparation stage, rubber stock is created by mixing raw rubber with essential ingredients using machines like internal rubber mixers or milling machines.
In the final stage, the semi-finished rubber product is vulcanized. This process involves heating the rubber to temperatures between 140°C and 200°C and applying pressures ranging from 0.3 to 20 meganewtons per square meter.
The equipment used in the vulcanization process includes presses, boilers, and various other machines, depending on the type of rubber products being manufactured. To ensure strong bonds between the rubber and any textile materials or metals used in the product, these materials must be pre-treated before the vulcanization process. This pre-treatment is crucial to achieving optimal performance under operational conditions.
Textile materials are bonded to rubber using rubber cement or other adhesives in specialized machines, followed by coating with a rubber stick-on coating. Metals are degreased using organic solvents and then coated with a layer of cement or brass. This process, known as brass plating, is accomplished through electroplating in a bath.
Industrial rubber goods are typically categorized into major groups: molded goods, unmolded goods, conveyor belts, hoses, and belts.
These goods are produced through a process that simultaneously molds and vulcanizes rubber stock. This is accomplished using a compression mold mounted on a press or through injection molding. Examples of molded industrial rubber goods include packing parts, shock absorbers such as gaskets, dust protection components, and rings with various cross-sections.
Unmolded industrial rubber goods are used for sealing doors and windows in motor vehicles, aircraft, and for hermetically sealing construction panels. These goods are produced by extruding rubber stock into cords of various shapes, lengths, and cross-sections. The semi-finished products are then vulcanized either in continuous action apparatus or through periodic batching in boilers. The resulting seals can be either monolithic or porous.
These are many types of conveyors and made for the transportation of friable and other materials. Using fabrics made from synthetic fibers, cotton, or other fabrics which can contain a tearing stress of about 65 to 300 kN/m reinforcement of conveyor belts is possible. A strong conveyor belt needs brass plated steel lines. The production of rubberized fabric belts includes assembling the core with the required thickness of rubber stock. The vulcanizing of the belt takes place in a press which has plates with a length of about ten meters.
Belts are flexible components used in belt drives for automobile engines, agricultural machines, and various industrial devices. There are several types of belts, including V-belts and flat belts. The production process for flat belts is similar to that used for conveyor belts: the rubber sheet is cut into strips to achieve the desired belt width, either before or after vulcanization. V-belts, which have a closed design and a trapezoidal cross-section, are assembled on machines and then vulcanized in boilers or diaphragm vulcanizers. The length and cross-section of the belt determine the appropriate vulcanization equipment needed.
Hoses are tubes which are flexible and they are used for conveying liquids, gasses, and other materials which are friable and this is done under excess pressure or under vacuum. The basic elements included are the inner sealing which is of rubber, a carcass of heavy duty and an outer layer which is also made of rubber. Suction hoses contain a possible vacuum of 80 kN/m² and are made with a metal spiral on top of adding the heavy duty carcass. Through extrusion, the inner and outer layers of a hose are made. The hose is either wrapped using a fabric brand or molded using a shell made of lead. It is then vulcanized in a boiler and then the shell is removed after vulcanization.
Rubber footwear is categorized into three main types: industrial, athletic, and everyday footwear. Industrial footwear is designed to protect the feet from harmful substances, extreme temperatures, and physical injuries. Examples include boots used by miners, fishermen, and dielectric rubber footwear.
The production method used for rubber footwear can also distinguish different types. For example, glued rubber footwear is assembled from previously produced parts on conveyor lines, glued together, lacquered, and then vulcanized in boilers. Galoshes, made using impact stamping on special presses followed by vulcanization in boilers, represent another production method for stamped rubber footwear. Molded rubber footwear is created by pressing rubber into molds and then vulcanizing the material.
Boots and footwear with fabric upper sections can be produced using these methods. Injection molding involves compounds such as polyvinyl chloride and thermoelastic plastics. Liquid molding, a more modern technique, uses liquid oligomers, including polyurethanes and plastisols, to create the footwear.
Silicone is an elastomeric material known for its high performance and flexibility, making it ideal for use in seals and gaskets. Surface preparation for silicone bonding is generally minimal, primarily because silicone surfaces often contain plasticizers that migrate to the surface, which can complicate bonding.
For improved surface preparation, a solvent wipe containing isopropanol is commonly used. This helps clean the surface and remove any processing lubricants, providing a better binding surface. However, some solvents, like acetone and white spirits, can be overly aggressive and may leave behind residues that could affect bonding quality.
There are not as many industrial adhesives which can properly be used in bonding with the silicone. To have a faster cure and exclude the use of isocyanate chemicals, polyolefin primer such as Permabond POP can be used. This primer can be used to prime the surface of the silicone and then take cyanoacrylate in the bonding of the parts. Permabond 2050 is usually preferred as it is flexible and doesn’t affect the feel of the silicone. The bonded joint can be hard to detect as it will remain soft like the original material. This result is great for the use in seals and o-rings as the design will not have a hard or crunchy part.
This chapter will explore the uses and advantages of bonding rubber to metal.
Rubber to metal bonding is highly versatile and widely used across various industries. In the automotive sector, it is utilized for creating seal gaskets and engine mounts. In agriculture, this bonding method is employed to manufacture components such as ball joints and stabilizers. Additionally, the medical industry benefits from rubber to metal bonding in the production of O-rings and pump compressor isolations.
With the expansion of the construction industry, rubber to metal bonding is also applied in the creation of conveyor belts, which are essential for efficient construction due to their strength and durability. In the mass transit sector, it is used for making valve seals and pedals. The durability provided by rubber to metal bonding ensures longer-lasting parts, contributing to both user safety and equipment reliability. The effectiveness of these applications depends on the use of appropriate materials.
Rubber to metal bonding streamlines the assembly process by reducing the number of components needed. By directly bonding the rubber to the substrates, fewer parts are required, which enhances assembly efficiency and decreases both labor and production time. This method results in a more robust bond, leading to durable materials with an extended lifespan. Additionally, the substrate gains resistance to harmful factors such as water and corrosion. Rubber is also a more environmentally friendly option compared to other bonding agents, as it is free from lead. Furthermore, rubber to metal bonding supports a broad temperature range, making it suitable for use in demanding conditions without compromising performance.
Rubber to metal bonding is a phrase that is generic in nature as it covers a number of interdependent processes. In general terms this includes combining the rubber element with a steel or metal element for it to attain properties which are advantageous in nature. Some of the rubber bonded elements obtained are used in areas like automotives and in other engineering applications. Larger units are used in construction to decouple movement in buildings in translation ways.
Molding is a manufacturing process that uses a mold - the latter being a solid container used to give shape to a piece of material. It is a forming process. The form is transferred from the mold to the material by...
Rubber injection molding is when uncured rubber is transformed into a usable product by injecting raw rubber material into a mold cavity made of metal. The applied pressure produces a chemical reaction like...
Rubber molding is a process of transforming uncured rubber or an elastomer into a usable product by transferring, compressing, or injecting raw rubber material into a metal mold cavity...
A rubber bushing is a form of vibration isolator that is placed between two parts to limit the motion between them and absorb, mollify, and buffer the energy produced by their interaction. They are very...
Extruded rubber is a group of products made by softening and pressurizing an elastomeric compound and forcing it to flow through a hard tool called a die. The resulting product is a continuous piece of material that has the same cross-section throughout its length...
Rubber gaskets are elastic components used for mechanically sealing the microscopic gap between two mating surfaces or joints. Examples of these surfaces are flange faces of piping and fittings, mating surfaces of an...
There are several methods to perform rubber overmolding, and each method has its own unique advantages and disadvantages. The choice of method typically depends on the design and material requirements of the product being...
A rubber roller is a machine part that is composed of an inner round shaft or tube covered by an outer layer of elastomer compounds. The inner shaft is made of steel, aluminum alloys, or other strong and rigid material composites...
Rubber sheets are basically sheets made of rubber or cloth that are coated with rubber to improve the mechanical properties of rubber sheeting such as increased tensile strength and reduced elongation...
Rubber trim is an extruded, sometimes molded, elastomer that is used to protect the edges or surfaces of objects from sudden impacts. They are usually found on panels, windows, doors, removable covers, and hatches...
Rubber tubing, also known as rubber hose or rubber piping, is made of natural and synthetic rubber and is used to circulate and transport liquids and gases for household and industrial uses. The natural or synthetic rubber materials used for the manufacture of rubber tubing...
Silicone rubber molding is a method for shaping, forming, and fabricating silicone rubber parts and products using a heated mold. The process involves compressing or injecting silicone rubber into a mold...
A grommet edging is a flexible rubber or plastic strip that covers rough and sharp surfaces found in openings and edges of panel walls to protect the passing electrical cables, wires, and other sensitive components...