Nylon Tubing
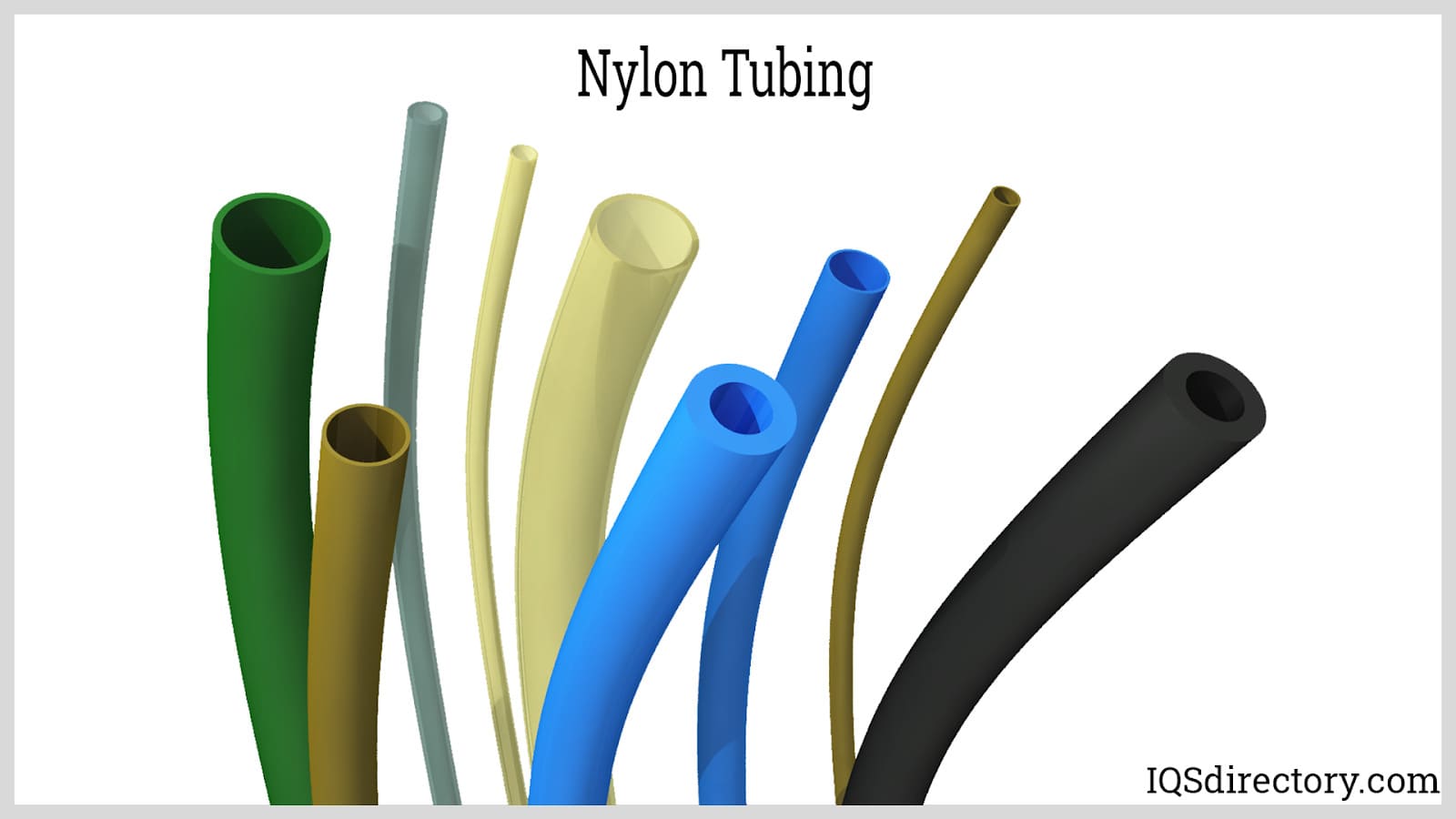
Nylon tubing, also known as polyamide tubing, is a type of tubing made from polyamide resin, which has a strong resistance to abrasion. It is used in high-pressure and high-temperature applications...
Please fill out the following form to submit a Request for Quote to any of the following companies listed on
This section examines the nature of silicone tubing, delving into its characteristics and the technological process employed for its production.
Silicone tubing, a resilient elastomer, is celebrated for its robustness, adaptability, and resistance. Remarkably durable, it retains its flexibility even when subjected to repeated bending and twisting. Due to its safe and non-toxic attributes, it's highly suitable for medical-grade uses, making it a top pick in healthcare environments.
Renowned for its ability to function under a vast temperature range and accommodate sudden climate fluctuations, silicone tubing is incredibly versatile. It is indispensable in various sectors where the transfer of liquids and gases is crucial. Due to its exceptional properties, it often emerges as the preferred tubing material across numerous applications.
Offering excellent UV and heat resistance, silicone is ideal for industries such as electronics and aerospace. Its facile cleaning and sterilization make it perfect for high-hygiene environments like medical, pharmaceutical, and food production sectors. Available in an array of sizes and grades, including high-temperature variants, silicone tubing meets diverse industry needs.
High-temperature silicone tubing withstands extreme thermal variations, making it superior to plastic or rubber options. FDA-approved food-grade tubing ensures stability, heat resistance, and non-stick characteristics, ideal for the food and beverage sectors. Medical-grade silicone tubing adheres to rigorous purity and non-toxicity standards necessary for medical fields.
Silicone tubing is crafted using the well-established rubber extrusion technique.
Favored for its efficiency and capability to create vast volumes promptly, the extrusion method is prevalent among rubber producers. It starts with heating and curing a silicone compound, which is then pre-shaped into slabs or strips.
This prepared silicone is introduced into a screw extruder. The extruder exerts pressure to push the compound through a steel die, held firmly by the extruder head. The die then molds the silicone into tubing as it passes through, followed by continuous curing in a heated curing oven.
The curing process employs various oven types, such as salt bath cures, steam vulcanization, and infrared cures. Sometimes, the silicone is further vulcanized by immersion in salt water. The primary challenge lies in selecting raw materials that perform optimally under specific conditions, ensuring the final product conforms to specifications.
The key distinctions between extrusion and molding include product shape, application, and production orientation. Extrusion is ideal for creating extended, circular shapes, whereas molding handles irregular forms but in limited lengths.
For tubing longer than 50 feet, extrusion requires re-sulfurization of the vulcanization tunnel. With extrusion, lengthy silicone tubes are produced continuously. Conversely, the solid-liquid injection technique involves liquid glue, reminiscent of plastic injection molding, starting with high-temperature sulfurization.
Post-injection, the product is de-molded. While this yields complex structures, it results in lower tubing hardness compared to extruded alternatives. Soft and smooth, injection silicone tubing suits the power industry for its unique attributes.
With exceptional resistance and insulating features, silicone is highly valued in the power sector. The solid-liquid injection process crafts set and irregular shapes, whereas extrusion generates extended tubes, both capable of meeting high-voltage demands in power systems.
In the healthcare industry, silicone tubing extrusion frequently pairs with the injection process. Extrusion is mainly for standard pipings like drains, while injection suits non-regular shapes. Despite higher costs associated with injection, including raw materials and equipment, extrusion remains a budget-friendly choice for producing standard pipes.
The dimensions of silicone tubing are instrumental in determining its use. Small tubing, with thin walls, is utilized in electrical sleeving; medium tubing, often employed for fluid and powder transport, is key in industries requiring precision and hygiene. Large tubing is utilized in applications demanding durability, like air ducts.
In the pharmaceutical and food industries, medium tubing is prized for hygiene. Platinum-cured silicone tubing, devoid of ketones and peroxides, finds widespread application in medical, food, dairy, and vending industries, ensuring taste preservation and product integrity. Moreover, cured silicone tubing serves as a versatile, food-compatible solution.
The different types of silicone tubing are:
Silicone peroxide tubing is available in translucent formats and comes in various diameters. This type of silicone tubing is typically used in applications where high purity and repeated sterilization are not critical. It is well-suited for general pump and transfer applications where the primary requirements are flexibility and durability rather than stringent cleanliness or precise dosing.
Silicone peroxide tubing is often used in automotive and industrial applications due to its ability to withstand temperatures up to 392°F (200°C). Additionally, it is more cost-effective compared to many other silicone compounds, making it a practical choice for general tubing applications.
Platinum-cured silicone tubing offers several advantages over peroxide-cured silicone tubing, making it a popular choice in the food and beverage industries. It boasts high tear strength and can operate within a broad temperature range of -40°F (-40°C) to 392°F (200°C). This versatility allows it to be used in various applications and environments without deterioration.
Platinum-cured silicone tubing is free from peroxide by-products, ensuring it does not yellow over time. It is available in translucent, black, or white options. This type of tubing is particularly well-suited for use in peristaltic pumps due to its long life expectancy, making it more durable compared to other options. Additionally, platinum-cured silicone tubing performs well in both hot and cold water applications and is widely used in non-invasive medical and pharmaceutical industries.
Silicone dairy tubing, as its name suggests, is specifically designed for use in the dairy industry. Its high resistance to mechanical wear and tear makes it ideal for such demanding applications. Most silicone dairy tubes are platinum-cured, which offers several advantages over other types of tubing. These include being non-yellowing and free from peroxide by-products, ensuring durability and maintaining the integrity of dairy products.
This tubing maintains its flexibility and does not harden or corrode even after prolonged use. Additionally, it features an extra-smooth inner bore, which enhances flow rate and ensures high hygiene standards.
Silicone fuel hoses are widely used in the radio-controlled car hobby. These hoses are highly resistant to methanol and nitro fuels, which helps to keep the fuel pure and extends the life of the tubing. Available in a variety of vibrant colors, silicone fuel hoses can complement the appearance of any model car. However, it is important to remember that these hoses are specifically intended for use with radio-controlled models and are not suitable for petrol engines.
High-temperature silicone hoses are designed to endure extreme fluctuations in temperature. These hoses are often labeled with a number, such as 550, which signifies the maximum temperature they can handle. By accurately predicting the operating temperatures, selecting the right high-temperature silicone hose becomes straightforward.
However, it is crucial to distinguish between thermal resistance and flammability. While a hose may resist high temperatures, it does not necessarily mean it is fireproof. The term "burn point" refers to the temperature at which a material will ignite when exposed to flames. If your application involves direct exposure to fire, ensure the hose is certified as flame retardant to meet safety standards.
Depending on the application, a high-temperature silicone hose may need to be flexible. Such hoses are particularly valuable when they need to bend and adapt to tight spaces. Although silicone hoses are generally flexible, they can suffer from flex fatigue if they are repeatedly bent, which might eventually cause them to tear. Typically, these hoses retain their straight shape unless manually curved.
High-temperature silicone hoses are also capable of withstanding harsh chemicals and elevated temperatures. The silicone material can endure exposure to various chemicals, including certain oils, solvents, and gases. To ensure the hose's effectiveness, it is essential to verify its compatibility with the specific chemicals involved in the application.
Food-grade silicone is an excellent material for use in food and beverage applications, offering a durable and long-lasting alternative to plastics. Unlike plastics, silicone does not contain plasticizers, which means it is less likely to release harmful chemicals like BPA into food and drinks. Additionally, silicone prevents the transfer of flavors and odors, making it ideal for food storage and transport. Its strength, non-porous nature, and resistance to various temperatures make it a valuable option in reducing reliance on single-use plastics.
This type of silicone tubing is highly dependable due to its stability, temperature resistance, and non-stick features. It is particularly suited for the food and beverage sectors because it does not interact with food substances and fluids. Food-grade silicone tubing can also be sterilized in standard autoclaves and has a surface that resists material buildup inside the tubing.
Creating durable and reliable food-grade components is straightforward with food-grade silicone. Some key benefits of choosing food-grade silicone over other plastics are:
Medical-grade tubing is specifically engineered to meet rigorous cleanliness and non-toxicity standards essential for medical applications. The United States Pharmacopeial Convention (USP) has established a set of six tests that define the criteria for medical device certification. The primary requirement for silicone tubing is biocompatibility, which ensures safety when in contact with human tissue. Furthermore, USP Class VI standards mandate that silicone tubing must resist adhesion and inhibit bacterial growth.
Silicone tubing is highly favored in the pharmaceutical, biotech, and medical fields due to its flexibility and adaptability. It provides a safe, cost-effective solution while adhering to the stringent purity and hygiene standards necessary for medical applications.
Key advantages of medical-grade silicone tubing include:
This silicone tubing is designed to meet rigorous cleanliness and non-toxicity standards essential for medical applications. It is both sterile and chemically inert. The composition of medical-grade silicone tubing ensures it is entirely non-toxic, free of odors and tastes, and does not promote bacterial growth. To achieve high purity, processes such as platinum curing are used during manufacturing. Additionally, this tubing is compatible with delicate pharmaceuticals and body tissues, avoiding any adverse reactions.
Shear refers to the force that acts parallel to a surface and results from an increase in the velocity gradient of a fluid. This tangential force causes the fluid to flow in layers at varying speeds, creating resistance between these layers. This resistance can exert force on cells passing through the tubing, potentially leading to cell damage or destruction.
The stress on the cells can lead to the release of proteases, unprocessed products, host cell proteins, and DNA into the fluid. This contamination can compromise product quality, reduce yield, and disrupt measurement equipment, all of which need to be minimized. One approach to mitigate shear force is to use fittings designed to create turbulence and backflow, which can help in managing shear stress levels.
Overmolding is a production process for creating fittings with exceptionally smooth interiors that reduce turbulence and limit shear stress. Overmolded junctions are leak resistant, smooth flowing connections produced in Y’s, T’s, crosses, and reducers and are cell saving.
Barbed fittings are designed to insert easily into silicone tubing for establishing connections. However, their construction can induce turbulence and backflow, which may result in shear stress. This shear stress can lead to entrapment, creating dead volume and reducing the efficiency of product recovery.
In contrast, overmolded connectors offer a smooth and seamless transition at junctions. They ensure a continuous, uninterrupted flow without causing entrapment or shear stress, leading to complete product recovery.
This range of colored tubing features thick walls and is crafted from general-purpose silicone rubber, making it suitable for high vacuum applications. It comes in an array of colors and is commonly used in various industries, including the electrical sector, where it serves as sleeving for electrical cables.
This silicone tubing is ideal for applications where high-pressure resistance or stringent compound purity is not essential. Thanks to its impressive thermal resistance and flexibility, it is well-suited for use in various household appliances as well as in hobby and workshop settings.
This section will explore the various applications and advantages of silicone tubing.
The applications of silicone tubing are:
Silicone tubing offers several advantages that make it highly valuable in the medical field. Known for its durability, ease of cleaning, and sterilization, it is a preferred choice among healthcare professionals. A crucial feature of silicone tubing from a medical perspective is its biocompatibility. This property ensures that it is safe for contact with living tissues, minimizing the risk of toxicity or allergic reactions. Consequently, silicone tubing is widely used in medical implants, drains, catheters, feeding tubes, and other medical devices where biocompatibility is essential.
Silicone tubing plays a crucial role in medical devices by offering essential sealing, gasketing, and secure fluid transfer capabilities that other materials may not provide. In the medical industry, silicone tubing is typically manufactured to a higher standard, using continuous extrusion and vulcanization processes. This allows for the production of very fine tubes, often used in capillary applications, as well as wider tubes designed for the transfer of critical fluids.
Silicone tubing is highly valued in analytical instrumentation due to its flexibility and ability to maintain sterility in equipment.
Silicone tubing is ideal for electrical insulation, making it a versatile choice for electronics in various industries. It is commonly utilized for insulating electrical components within automotive enclosures.
Since silicone tubing is non-toxic and has a smooth inner and outer surface, it is utilized mostly in water filtration and purification systems.
Food-grade silicone tubing is well-suited for applications in dairy processing, beverage dispensing, and other areas of the food industry that demand sterile, flexible materials with excellent chemical and heat resistance.
In the aerospace sector, silicone tubing is widely employed in systems such as climate control and conveyance. Its high tensile strength, flexibility, and temperature resistance make it ideal for use in vacuum seals for both vehicles and aircraft.
Additional applications of silicone tubing include:
The benefits of silicone tubing are:
Silicone tubing maintains its flexibility across a wide temperature range. Unlike some high-temperature rubber tubing, it remains resilient without softening at high temperatures or hardening in cold conditions. This characteristic makes it particularly well-suited for use in extreme environments.
Silicone tubing is designed to perform well across a wide temperature spectrum, enduring temperatures from -130°F to 600°F (-90°C to 315.5°C). It also resists UV radiation and ozone exposure, reducing the likelihood of degradation. These characteristics make it well-suited for outdoor and aerospace applications.
Silicone tubing is known for its high tensile strength, which minimizes wear, tear, and breakage. This durability makes it ideal for high-traffic applications in industries such as plumbing and food service. Its flexibility and toughness contribute to a long service life, as it resists cracking and breaking due to its excellent elongation and tensile strength. This resilience makes it appropriate for demanding environments like breweries, dairy farms, water treatment facilities, milking parlors, and aquariums.
Silicone tubing comes in a wide range of colors and can be customized to match specific color requirements.
Food-grade and medical-grade silicone tubing feature a smooth surface both inside and out, making them ideal for applications that require a sterile, contaminant-free surface. This smooth finish is crucial for preventing contamination in industries such as food service, medical, and analytical instrumentation.
Silicone tubing is highly durable, exhibiting exceptional resilience and resistance to repeated compression cycles.
Silicone tubing is available in a range of hardness levels, from 20 Shore A to 90 Shore A, and is resistant to surface penetration.
Silicone tubing offers excellent pliability, making it suitable for use in tight spaces or high-pressure environments where more rigid materials might fail. Additionally, its flexibility facilitates easier management and control of fluid flow.
Silicone tubing withstands ultraviolet (UV) radiation and inhibits pathogen growth, making it ideal for use in food processing, pharmaceuticals, and medical applications. It is hygienic and resistant to bacterial growth and solid accumulation. Furthermore, it offers good resistance to ozone, weather conditions, salt water, cleaners, synthetic compounds, and various chemicals.
Silicone tubing can be produced in a variety of sizes and lengths to suit different needs.
Silicone tubing is simple to clean and remains durable even after repeated exposure to chemicals, without becoming brittle or stiff.
Silicone tubing does not interact with the substances it carries, making it suitable for applications involving food, water, air, and beverages, as it does not affect the taste or quality of the transported products.
Despite its numerous advantages, silicone tubing is not suitable for transporting concentrated fuels or oils, as these substances can degrade its structure.
This chapter will cover methods for cleaning, sterilizing, and connecting silicone tubing.
Regular cleaning of silicone tubing is essential in food production environments, such as homebrewing setups or soft drink dispensing systems. Silicone tubing is easy to clean and can be thoroughly sanitized by boiling, which removes any residue inside the hoses. This regular cleaning is necessary to prevent buildup, blockages, and unpleasant odors.
For other applications, like those in the automotive industry, frequent interior cleaning of silicone tubing may not be required. A simple method for cleaning silicone tubing is to use hot soapy water, either wiping down the tubing or flushing it through.
Silicone’s high heat resistance means that the water temperature is not a concern during cleaning. However, certain cleaning agents can negatively react with silicone tubing, leading to damage and discoloration. It is important to avoid using WD40 or petroleum-based cleaners on silicone tubing.
Silicone tubing is widely used in medical instruments and equipment due to its ease of sterilization. Several sterilization techniques commonly employed in medical laboratories are available. The most prevalent method is gamma irradiation, although this process may alter the silicone's properties, increasing its tendency to kink. Another option is electron beam irradiation, which can produce similar physical effects.
Another effective sterilization method is ethylene oxide. This technique works well because silicone tubing absorbs ethylene oxide, but it is crucial to ensure that the ethylene is fully removed before the tubing is used in medical applications.
The methods of joining silicone tubing are:
Isopropyl alcohol (IPA) is commonly used to lubricate silicone tubing, facilitating its movement over barbed fittings. IPA is hygroscopic, meaning it absorbs moisture. When used with silicone tubing, IPA should be applied in its pure form. It is readily available and generally affordable.
IPA is effective because it evaporates cleanly without leaving residue on medical devices. However, its main drawback is the slower drying time, which can make the process more time-consuming and increase production costs. To accelerate drying, techniques such as applying low temperatures to the silicone tubing can be used.
Another approach for joining silicone tubing involves using silicone oil-based lubricants. This method is often favored by engineers due to its intuitive nature, as using silicone fluid with silicone tubing ensures material compatibility. However, there are significant drawbacks to using silicone oil.
One major drawback of using silicone oil-based lubricants is their tendency to create a mess. The oil does not evaporate and is designed to remain on surfaces indefinitely. Since silicone easily migrates to other surfaces, controlling the application to specific parts of a device can be challenging. This often leads to a time-consuming process, as more cleanup is required after the coating and joining are complete.
Additionally, the risk of contamination increases during the coating process because the oil can attract and trap dust and dirt from the surrounding environment. Even in a clean room, the likelihood of contamination remains high. Moreover, medical-grade silicone, which is necessary for such applications, is more expensive compared to lower-grade silicones used in other industries.
The silicone swelling process is similar to how a sponge absorbs water. When silicone tubing absorbs a solvent, it expands like a sponge and then contracts as the solvent evaporates, eventually returning to its original size. This process creates a tight seal around metal parts or barbed fittings, making the attachment of silicone tubes or parts to barbed fittings both quick and straightforward.
Typically, silicone only needs to expand by 1 to 2% for effective fitting, and the entire swelling process can be completed in less than a minute. To begin, the end of the silicone that will connect to the barbed fitting is dipped into a swelling agent. The tubing or part begins to swell almost immediately upon immersion. The duration it remains in the solution dictates the extent of swelling, which can be timed precisely in high-volume operations to optimize efficiency.
Once removed from the solvent, the swelling agent starts to evaporate right away. As the solvent evaporates, the part returns to its original dimensions. Compared to other methods, the silicone swelling process—both the expansion and the subsequent recovery—can be completed very quickly.
Barbed fittings utilize serrations or ridges to grip the interior surface of the connecting tubing, creating a secure seal without causing damage to the tubing wall. Commonly referred to as hose barbs or hose barbed connectors, these fittings are popular due to their ease of installation.
The secure connection provided by barbed connectors makes them suitable for low-pressure applications, typically up to 200 psi, involving fluids, gases, and airflow. The effectiveness of the seal relies on the interaction between the connector’s surface and the tubing wall.
Push-to-connect fittings function similarly to barbed fittings but lack the barbs or ridges. These fittings use a uniquely shaped connector into which the tubing is inserted. A securing ring within the connector keeps the tubing firmly in place. For a proper fit, the tubing must be cut to a clean, uniform 90° end. The gripper ring in the connector not only secures the tubing but also allows for easy removal when needed.
PFA compression fittings offer a more secure and tighter connection compared to push-to-connect fittings. Constructed from PFA fluoropolymer, these fittings are designed for use with rigid and semi-rigid tubing. They operate by compressing the outer diameter of the tubing to create a secure seal.
Unlike barbed fittings, compression fittings engage with the outside of the tubing, requiring the tubing wall to be robust enough to handle the applied pressure. A PFA compression fitting consists of four main parts: the body, the ferrule, the gripper, and the nut. For a proper fit, the tubing must be cut to a clean 90° angle.
To assemble the fitting, start by sliding the nut onto the tubing. Next, place the gripper over the tubing and inside the nut, with its smaller end facing the nut. Then, insert the ferrule into the nut, positioning its larger end towards the gripper. With these components in place, push the body of the fitting over the tubing and towards the nut as far as possible.
Once all parts are assembled, thread the body of the fitting onto the nut and tighten it carefully with a wrench. It is crucial to tighten the fitting with care to avoid over-tightening, which could deform the fitting.
Compression fittings are available in various forms, including Ts and elbows, making them suitable for diverse applications. Although they are more expensive than other types of fittings, they are essential for high-pressure situations.
As mentioned above, silicone tubing is a tough elastomer that exhibits many good properties, including high resistance to temperature ranges, high flexibility, good wear and tear resistance, and resistance to UV and ozone. These benefits make silicone tubing a popular choice in a variety of applications, such as in the medical and food industries. Its high flexibility and strength make it a better choice over other rubber materials that can be used in its place. One of the other benefits that make silicone tubing a popular choice in the medical field is that it is easy to clean. This can be easily done by boiling it to remove the dirt that builds up in the material. The flexibility and high tensile strength of silicone tubing make it suitable for various applications in the medical, automobile, dairy, food, beverage, and pharmaceutical industries. Because of the different grades in which silicone tubing is available, careful considerations must be made when opting for silicone tubing for a specific type of application.
Nylon tubing, also known as polyamide tubing, is a type of tubing made from polyamide resin, which has a strong resistance to abrasion. It is used in high-pressure and high-temperature applications...
Plastic tubing is a form of tubing that is manufactured from a mixture of a polymer with a variety of chemicals to form a material that can be solid or flexible. Since its first use in the 1950‘s, plastic tubing has revolutionized industrial processes and has found a use in a wide variety of applications...
Poly tubing is a highly flexible, lightweight, and durable tubing that is produced from polyethylene, a polymer that is made from the polymerization of ethylene. It is a very versatile form of tubing that has break and crack resistant walls...
PVC is a tough chemically resistant synthetic polymer of vinyl chloride used especially for making pipes, films and electrical insulation. It is made by polymerizing vinyl chloride, and...
Plastic channels are plastic products that have linear extruded profiles. They have a constant cross-sectional shape across their axis. They are long and narrow structures, and their depth is relatively short. These products serve a variety of functions and uses...
Plastic extrusion, also known as plasticating extrusion, is a continuous high volume manufacturing process in which a thermoplastic material -- in a form of powder, pellets or granulates -- is homogeneously melted and then forced out of the shaping die by means of pressure...
Plastic materials are objects artificially made from organic compounds called polymers along with other additive components. They possess excellent formability, making them extremely versatile for many different fabrication and manufacturing processes...
A plastic tank is a large capacity liquid or granular storage unit that can be vertical, horizontal, below or above ground, as well as movable. They are designed to hold several gallons of a variety of substances for long periods without experiencing wear, weathering, or deterioration...
A plastic rod is a solid plastic shape made by the process of plastic extrusion or plastic co-extrusion. These have a contrast of plastic tubing and hollow plastic profiles. Plastic rods are found in various industries, including...
Plastic trim products are extruded linear profiles that can be made to any length. Because of its ability to attach, hold, and seal, plastic trim has many applications. Plastic, HDPE, LDPE, butyrate, PVC, acrylic, and...
A plastic water tank is a large capacity container designed to store water for household, agricultural, irrigation, and industrial manufacturing use. There are various types of water tanks produced to meet the needs of specific applications, with...
A coupling is a device that is used to transmit power between two shafts connected together at their ends. Couplings serve one primary purpose: to join two pieces of rotating equipment together, while...
Silicone rubber molding is a method for shaping, forming, and fabricating silicone rubber parts and products using a heated mold. The process involves compressing or injecting silicone rubber into a mold...