Data Acquisition Systems
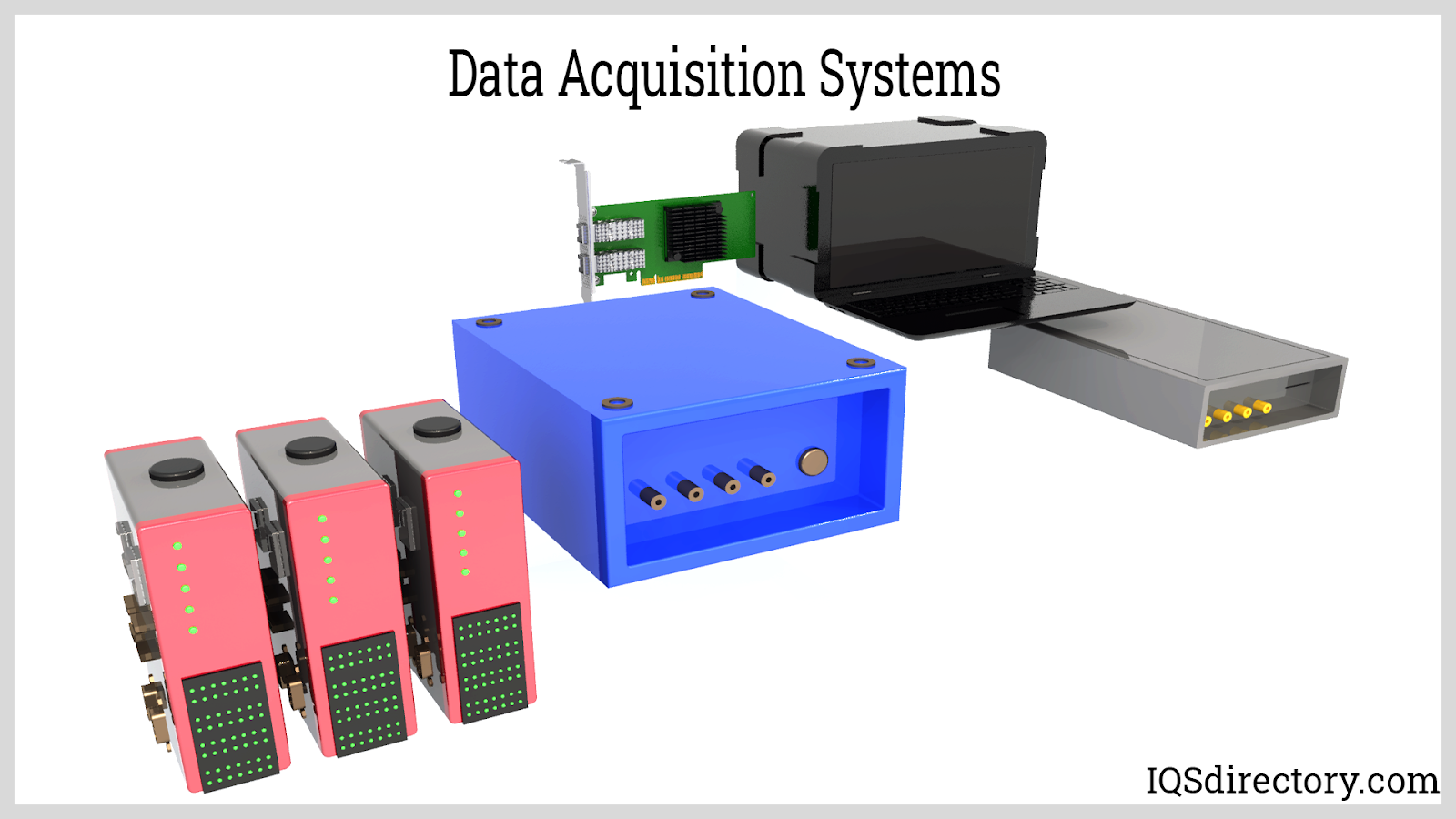
A data acquisition system is a system that comprises sensors, measurement devices, and a computer. A data acquisition system is used for processing acquired data, which involves collecting the information...
Please fill out the following form to submit a Request for Quote to any of the following companies listed on
This article contains everything you need to know about Platform Industrial Scales.
Read further and learn more about:
A platform scale is a type of weighing instrument equipped with one or two metal plates that provide support for the items being weighed. These plates may feature either a diamond-patterned or smooth surface. Built to withstand rigorous use, platform scales come in a range of sizes, capacities, styles, and models tailored to meet a variety of industrial needs.
Featuring a low-profile design, platform scales are suitable for weighing sizable items, including pallets, animals, large loads, or individual crates and boxes. Items are placed directly on the scale's surface for weighing.
The platform's main purpose is to transfer the item's weight to an internal measuring system while providing dependable support throughout the weighing operation. Various devices can be integrated into the platform scale to enhance weight measurement capabilities. Available in multiple designs, sizes, and load capacities, platform scales are crafted to meet a wide array of user or customer demands.
Platform scales have practical applications across a spectrum of environments. They are commonly utilized in industries such as trading, manufacturing, logistics, and services to measure or verify weights. In sectors where precise weight measurement is crucial, platform scales serve an essential role in revenue generation, ensuring safety, and upholding product and service quality. Beyond commercial and industrial applications, these scales are apt for small-scale weight determinations in personal, domestic, medical, and laboratory settings.
Understanding how platform scales function is essential for anyone seeking accurate and reliable industrial weighing solutions. A platform scale operates on a straightforward principle: to weigh an object, you simply place it on the weighing platform, and the scale does the rest. The object exerts a downward force due to its mass and gravity, which is then transferred to an internal weighing mechanism. This mechanism, whether mechanical or electronic, converts the force into a readable weight measurement appearing on the scale’s digital display or analog indicator for easy, precise recording. Platform scales provide high-accuracy measurements for a wide variety of applications, ranging from industrial warehouses and shipping, to laboratories and medical environments.
There are two main types of platform scales: electronic platform scales and mechanical platform scales. The primary distinction lies in their weight measurement technology. Mechanical platform scales utilize levers, springs, and calibrated reference weights to indicate mass. In contrast, electronic platform scales employ advanced load cells and digital sensors to instantly deliver accurate readings. Electronic scales often offer additional features such as data logging, USB connectivity, and integration with ERP systems, providing real-time weight tracking and inventory management capabilities. This makes electronic platform scales highly suitable for industries that require speed, accountability, and traceability in their weighing processes.
Load cells are critical components in modern weighing systems, serving as the heart of most electronic platform scales. A load cell is a transducer that converts mechanical force—such as compression, tension, or shear—into an electrical signal. Most commonly, platform scales utilize strain gauge load cells, which incorporate a spring element and an array of strain gauges. As an object is weighed, the load cell deforms slightly. This deformation, whether from heavy or light loads, changes the electrical resistance within the strain gauge, enabling precise weight measurement and high accuracy, even at low capacities.
The type of load cell used in a platform scale depends on several factors: the maximum capacity required, the environment (including potential exposure to moisture, chemicals, or vibration), platform size, and the specific weighing application. For example, robust shear beam load cells excel in industrial settings for bulk material weighing, while compact single point load cells offer reliable performance in bench scales and process control environments.
Common industry uses of load cells include inventory tracking, quality assurance, batching, bulk packaging, and product inspection. Advanced load cell technology allows manufacturers to achieve quick, repeatable, and highly accurate readings, reducing errors and maximizing operational efficiency.
The most widely used load cells in industrial platform scales are strain gauge load cells, which measure strain or deformation caused by applied loading. Strain gauges transform mechanical forces—such as tension, pressure, or compression—into proportional electrical signals that can be displayed digitally and transmitted to other devices for further analysis or integration with industrial automation systems.
Strain gauges are integral to load cell design and play a pivotal role in ensuring measurement accuracy. They detect the amount of force or strain applied to the load cell structure, and this strain directly alters the gauges’ resistance. This change can be calibrated with high precision, making strain gauge load cell technology the leading standard for most commercial and industrial weighing applications.
Within a load cell, the strain gauge assemblies are housed inside the load cell body, acting as sensitive electronic sensors. Each strain gauge consists of ultra-thin metal foil mounted to a flexible substrate, which changes its electrical resistance in direct proportion to the minute deformations it experiences when a load is applied. As current passes through the circuit, these variations in resistance are measured as voltage fluctuations and interpreted by a digital meter to produce a precise, real-time weight reading.
Platform scales may feature several types of strain gauge load cells, each offering specific advantages for different weighing requirements:
A shear beam load cell is constructed from a solid metal element engineered to deform elastically when subjected to applied force. Strain gauges, carefully bonded to precise locations on the metal, measure this deformation and convert it into an electrical signal that can be read with a high degree of accuracy. Shear beam load cells are commonly used in floor scales, tank weighing, and batching systems, typically handling medium-sized loads up to about five tons. Their compact, robust design makes them ideal for heavy-duty industrial weighing solutions that require durability and resistance to side forces or vibration.
Single point load cells feature a precisely engineered aperture—essentially a machined cut-out—in their structure that controls the thickness of the metal and allows for predictable deformation under load. Strain gauges affixed to strategic points in this section detect small changes in shape as weight is applied. The resulting electrical output signal is directly proportional to the mass of the object, delivering highly accurate and repeatable measurements. Single point load cells are favored in low-profile bench scales, retail price computing scales, and postal platform scales due to their ability to maintain accuracy even when loads are placed off-center.
Magnetic force restoration (MFR) scales represent the highest precision available in electronic weighing technology. These advanced electromechanical balances utilize electrodynamic force compensation with permanent magnets to convert the force on the weighing platform into a proportional electric current. MFR scales are among the most expensive weighing instruments, but they offer ultra-high resolution, exceptional stability, and top-tier repeatability, making them indispensable for analytical laboratories, pharmaceutical research, and metrology applications.
Unlike strain gauge-based systems that directly measure the force, MFR scales create a counterbalancing electromagnetic force to maintain equilibrium, allowing for extremely precise and drift-free measurement of small mass changes. This is achieved by suspending the platform from a force coil placed within a stationary magnetic field generated by a precision amplifier. As weight is applied, the system automatically adjusts the current through the force coil to keep the platform in balance, and the system monitors the amount of current required—directly correlating to the object's mass.
The resulting voltage is processed by a high-resolution analog-to-digital (A/D) converter and interpreted by an embedded microprocessor equipped with specialized weighing algorithms. The output is a clear, digital weight readout designed for maximum precision. Additional features such as automatic internal calibration, temperature compensation, and digital filtering ensure that MFR balances maintain uncompromising accuracy in demanding environments.
The superior reliability and measurement accuracy of magnetic force restoration technology make it the preferred choice for critical weighing tasks—such as reference weight calibration, chemical analysis, and the preparation of pharmaceutical formulations—where even minute deviations can have significant consequences.
Weighing oversized and heavy materials requires a highly durable and resilient weighing device that can handle the rigorous demands of industrial and commercial settings. Among the various industrial weighing solutions available, platform scales are the most commonly utilized due to their superior efficiency, versatility, and ease of operation in demanding weighing processes such as warehouse, logistics, manufacturing, and distribution environments.
Despite their straightforward operation, platform scales are engineered with advanced technical features that deliver highly accurate weight measurements for a wide range of applications. These industrial weighing scales are designed for reliability and can support both static and dynamic weighing tasks. Each scale is equipped with a user-friendly digital indicator that connects directly to the platform, allowing for immediate and clear display of weight data.
Every platform scale consists of several essential components: load cells (with advanced strain gauge technology for precise force measurement), a platter or deck designed to accommodate various load types, a sturdy platform base, and easy-to-read indicators or terminals. The load cells are the critical force-measuring elements, capturing the weight and generating signals processed by the indicator. The platter—or weighing deck—sits atop the load cells, providing a stable, level surface to support products, materials, pallets, or containers during the weighing process. Lastly, the terminal (indicator) aggregates and displays the weight readings in user-defined units, streamlining process control and data recording in diverse workflows.
Floor scales are industrial-grade weighing platforms engineered to handle heavy, oversized, and cumbersome loads that are unsuitable for bench or tabletop scales. A typical heavy-duty floor scale system features a robust deck, a digital weight indicator, and four shear beam load cells. Within the industrial platform, a protected junction box contains a summing device to calibrate and synchronize the load cells for standardized readings, which is essential for accurate industrial weighing operations.
Floor scales are designed for ground-level installation, allowing direct access for loading and unloading. They are routinely deployed in high-traffic areas like factories, manufacturing plants, warehouses, and shipping departments. These scales are constructed to support substantial loads, often exceeding several tons, and to withstand harsh, hazardous, or wet environments. Many industrial facilities rely on floor scales to guarantee accurate shipping, minimize waste, and ensure regulatory compliance. A variety of specialized models are available, with features tailored to different operational requirements and industries.
A basic floor scale is the most straightforward and economical option, featuring a standard rectangular platform that rests slightly elevated above the floor surface. These heavy-duty scales are ideal for industrial processes that require weighing of pallets, containers, or production batches. Items can be placed onto the platform either manually or via common material handling equipment such as pallet jacks, forklifts, pushcarts, or hand trucks. Loading methods for basic industrial platform scales include:
One popular option is the installation of access ramps at the edge of the floor scale, facilitating smooth transit of materials. While ramps greatly ease transfer of heavy loads, they do require additional floor space and may pose a safety risk if proper handling procedures are not followed.
Alternatively, a pit frame installation is available for basic floor scales, reducing safety risks and space requirements. In this setup, a structural pit is prepared below floor level so the platform aligns flush with the surrounding floor, facilitating easier movement and compliance with health and safety standards. Pit installations can, however, increase up-front costs due to additional construction requirements.
Low-profile floor scales are a specialized variant designed for ergonomic and accessible weighing. By positioning the platform just 1 to 2 inches above ground level, these scales simplify manual loading and unloading, minimize perceived lift height, and enhance worker productivity and safety. A hinged ramp can easily be integrated to further streamline material transfer, particularly in restricted spaces.
Many low-profile platform scales include raised side rails or metal guides, with load cells placed underneath, ensuring consistent accuracy for larger, awkwardly shaped items. Note, however, that these side rails can create clearance challenges for some irregularly shaped products.
Washdown scales (also called sanitary floor scales or lift scales) are engineered for environments that demand high sanitation and hygiene standards. These platforms feature a top deck that can be easily lifted, either manually or via powered mechanisms, providing unrestricted access for cleaning and preventative maintenance. During the cleaning process, advanced sealing technologies protect critical electronic components from water, detergents, and corrosive substances.
Washdown platform scales are ideal for food processing, beverage manufacturing, agriculture, and pharmaceutical industries, where rigorous compliance with sanitation and quality control regulations is paramount. The corrosion-resistant construction—often utilizing 304 or 316 stainless steel—enables reliable weighing of liquids, powders, and corrosive chemicals while facilitating rapid, thorough washdowns to mitigate risks of contamination. These features make washdown scales indispensable in HACCP-compliant facilities and locations subject to frequent or high-pressure cleaning cycles.
Portable floor scales are designed for locations that require flexible or temporary weighing stations. Their enhanced mobility reduces costs compared to installing multiple fixed-bay scales throughout a facility. These scales typically run on rechargeable battery packs and feature rugged casters or rubber wheels for effortless movement between weigh zones or workstations, maximizing workflow efficiency in dynamic environments.
Their portable design allows materials to be weighed at the point of need, which is particularly advantageous for large warehouses, production floors, or remote receiving areas. Optional ramps, lightweight construction, and rapid re-deployment boost productivity while minimizing bottlenecks and wait times during shipping, receiving, or inventory control procedures.
Flexure lever scales leverage advanced S-beam load cell technology, making them highly effective for applications prone to shock loading and sudden heavy impacts. These platform scales are engineered for tough industrial environments where impact and overload resistance is essential—such as foundries, metal works, and materials processing plants—helping to extend the service life and measurement reliability of heavy-duty weighing solutions.
Truck scales—also known as vehicle scales or weighbridges—are heavy-capacity platform systems engineered for weighing entire trucks, trailers, and vehicles with their loads. These industrial solutions are essential for monitoring axle weights, verifying compliance with highway regulations, and managing logistics at shipping facilities, recycling centers, and bulk material distribution sites.
Truck scales function as oversized floor scales, delivering very high capacity (often exceeding 100 tons) and robust structural steel construction. These vehicle weighing solutions use multiple high-capacity load cells—typically ranging from 6 to 12 or more—to provide precise measurements, even under varying environmental or load conditions. Many modern truck scales support data connectivity, ticket printing, and integration with inventory management, helping companies optimize operations and reduce lost loads or overweight penalties.
Manufacturers of advanced platform scales offer a comprehensive selection of industrial weighing accessories and add-ons designed to extend the functionality and durability of their weighing systems. As the products, weights, and environments encountered across applications can vary greatly, these specialized accessories enable customization and adaptation of each platform scale to suit demanding requirements—improving efficiency, productivity, and safety. Smart selection of accessories can also minimize capital outlay by expanding a scale’s capability without the need for redundant weighing equipment.
Pit riser stands are robust structural frames engineered for mounting floor scales inside pits that exceed the scale’s standard installation depth. When installed beneath the platform—and securely anchored—these risers ensure the scale deck sits flush with the surrounding floor surface, optimizing workflow, improving accessibility, and supporting regulatory compliance for workplace safety.
Portability frames allow fixed floor scales to be easily converted into mobile weighing units. These kits may feature industrial-grade casters or forklift channels, enabling efficient movement of platform scales between locations—critical for fast-paced environments that require on-demand weighing of products or components at multiple staging areas or process points.
Access ramps are essential for seamless transfer of bulky loads by pallet jack, dolly, or hand truck. By eliminating the need for lifting, ramps reduce worker fatigue and the risk of material-handling injuries. They are especially useful for environments that frequently weigh drums, barrels, or bulk containers transported on rolling carts, enhancing the scale's versatility and operational safety.
Pit frames are structural surrounds used to mount standard floor scales in below-ground pits. This creates a low-profile or flush-mounted platform, improving accessibility for wheeled material handling equipment while enabling compliance with workplace safety standards. Pit installation is popular for high-throughput industrial weighing applications where trip hazards must be minimized.
Bumper guards are designed both to protect a platform scale from accidental impact—such as collisions with forklifts, pallet jacks, and carts—and to enhance operator safety. By providing a visual and physical barrier, bumper guards help prevent trips, falls, and scale edge accidents, particularly in busy material handling environments.
Constructed from highly durable materials such as reinforced steel or engineered plastics, some bumper guards also feature high-visibility coatings or reflective surfaces to improve hazard awareness, especially in low-light or congested settings. This dual purpose boosts both the longevity and safety rating of floor scale installations.
Mixing scales are specialized platform scales used for the precise measurement and batching of fine ingredients. They are critical in quality control and recipe formulation, where even small inaccuracies can alter product characteristics or lead to non-compliance with specifications. These industrial scales are widely adopted in automotive paint production, food processing, chemical blending, and laboratory-scale manufacturing, ensuring accuracy and repeatability for high-value materials.
Surface Acoustic Wave (SAW) platform scales represent cutting-edge weighing technology that differs significantly from traditional strain gauge-based designs. Instead of relying on resistive changes, SAW scales utilize the precise measurement of wave displacement created by receiver and transmitter transducers. These waves travel across the platform, and the frequency changes as the load induces a deflection in the structural spring element.
This highly innovative measurement methodology offers improved accuracy, exceptional stability, and minimizes long-term drift common to older technologies. SAW platform scales are increasingly adopted in scientific laboratories, high-volume bulk material weighing, and environments requiring unsurpassed accuracy and reliability, positioning them as the next evolution in industrial scale technology.
Digital platform scales are now the industry benchmark for industrial, commercial, and scientific weighing. These advanced electronic weighing solutions are engineered to handle exceptionally large objects—sometimes up to 10 tons—with outstanding reliability, repeatability, and precision.
Today’s digital platform scales operate using precision sensors and microprocessor-based electronics to process force signals from load cells and relay highly accurate digital readouts. These scales often include features such as tare functionality, multiple weighing units, programmable outputs, and connectivity with data management or ERP systems. Their robust design ensures accurate performance even in the harshest industrial settings.
The move from mechanical to digital weighing systems has revolutionized process control, inventory management, and production quality assurance. By delivering enhanced measurement consistency and minimizing human error, modern digital platform scales deliver measurable ROI—enabling manufacturers to meet strict tolerances, minimize waste, and gain a competitive edge through improved process accuracy and data-driven decision making.
The previous chapter described various types of platform scales, each offering different features tailored to the needs and desired levels of service and automation of customers. When selecting, upgrading, and maintaining a platform scale, the following aspects should be carefully considered:
Capacity denotes the maximum load that a platform scale can accurately measure. It is a critical specification to review when choosing a scale. However, scales with higher capacities may not always be ideal, as increasing capacity can often compromise accuracy. Additionally, higher-capacity scales typically involve greater investment and maintenance costs. Therefore, it is advisable to select a capacity that is only slightly above the maximum expected load.
Readability indicates the smallest measurement increment that the scale can display. It refers to the number of decimal places in the scale's measurements. Greater readability implies enhanced accuracy and a higher number of significant figures in the measurement. This is especially important for laboratory scales to minimize calculation errors and for weighing valuable items where precision is crucial. Smaller increments also reflect the higher functionality of the scale's weighing sensors.
Accuracy measures how closely the scale's measurement aligns with the true value. To ensure accurate performance, platform scales require regular calibration to maintain their accuracy.
Linearity describes the scale's ability to provide correct measurements from zero weight up to its maximum capacity. It is assessed by measuring objects with known weights and plotting the results; a straight line should be produced. Another method involves cutting a stable sample into equal parts, weighing each part separately, and verifying that the combined weight matches the weight of the whole sample.
Drift refers to the variation in readings while weighing a sample, leading to unstable and inaccurate measurements. It is caused by environmental factors such as temperature fluctuations, vibrations, air currents, static electricity, and radio frequency interference (RFI). To minimize drift, install ionizers and position the scale in an environment free from RFI, vibrations, and air currents.
When choosing a platform scale, the materials used in its construction are crucial. Scales should be made from strong and durable materials like steel (such as carbon steel or stainless steel) or aluminum (for smaller capacities) to support the load during weighing. Corrosion resistance is also important and can be enhanced with protective coatings. Additionally, rugged platform surfaces can be selected to prevent loads from slipping during placement.
When selecting a platform scale, consider the dimensions of the items to be weighed and the available floor space where the scale will be placed. Large items are best weighed on a floor scale, while smaller items are suited for a bench scale. Additionally, evaluate the platform's inclination to determine if a ramp or pit frame is needed. A high inclination can make it difficult to load heavier items onto the scale.
For platform scales exposed to harsh or wet environments, where spills might occur, regular and thorough cleaning is essential to prevent cross-contamination. Certain platform scales, such as washdown scales, are designed to facilitate frequent cleaning and sanitation in such conditions.
Platform scales can be equipped with automated systems, such as automatic weight verification and data transmission, to enhance operational efficiency and accuracy. However, incorporating more automation features can lead to higher investment costs.
Various types of industrial scales are utilized to measure and weigh products and materials. Each scale type is tailored to the specific industry, the materials being weighed, the weighing method, and the precision required. Among these, platform scales feature a flat surface that accommodates cumbersome and irregularly shaped loads with ease.
Platform scales are adaptable to any industry and purpose. Whether in warehouses or production facilities, they offer durability and precision even in challenging work environments. They can serve as a single scale for various locations or be used at multiple sites.
The design of platform scales with a flat platform allows for efficient weighing of heavy loads. A forklift can place a pallet on the scale, weigh it, and remove it swiftly, which is advantageous for time-sensitive tasks. Measurements are delivered quickly, enhancing operational efficiency.
Platform scales facilitate rapid and precise measurement of loads, which boosts productivity by reducing turnaround times and improving the ability to meet deadlines.
Errors in data and calculations can hinder operations. Advanced platform scales are equipped with security software and digital displays that help minimize errors and prevent inaccuracies. This ensures that every load leaving a location is correctly weighed and documented.
Overloading a truck can lead to several issues, including increased stopping distances, diminished brake performance, and mechanical failures, all of which can result in accidents, delays, and higher costs.
Platform scales ensure accurate measurements, helping to keep truck loads within recommended limits. Adhering to these limits helps shipping operations comply with regulations and avoid fines for exceeding weight restrictions.
A data acquisition system is a system that comprises sensors, measurement devices, and a computer. A data acquisition system is used for processing acquired data, which involves collecting the information...
Force sensors are transducers that transform mechanical input forces like weight, tension, compression, torque, strain, stress, or pressure into an electrical output signal whose value can be used to...
A load cell is a transducer which converts mechanical energy (tensile and compressive forces) into electrical signals. There are different transducer operating principles that can be utilized to convert forces...
A load pin is a sensor utilized to measure force or weight in various research, control, measurement and testing applications. The load pin force sensor converts a force into an electrical signal. The load pins provide...
A strain gauge, or strain gage, is a sensing device used for measuring strain experienced by an object. It is made from a long, thin piece of conductor bonded to an elastic backing material called a carrier...
At the heart of every weighing device is a sensor called a load cell. When an item is put on a load cell, it senses the force of the gravitational pull of the weight, which an electronic circuit processes to display...