Data Acquisition Systems
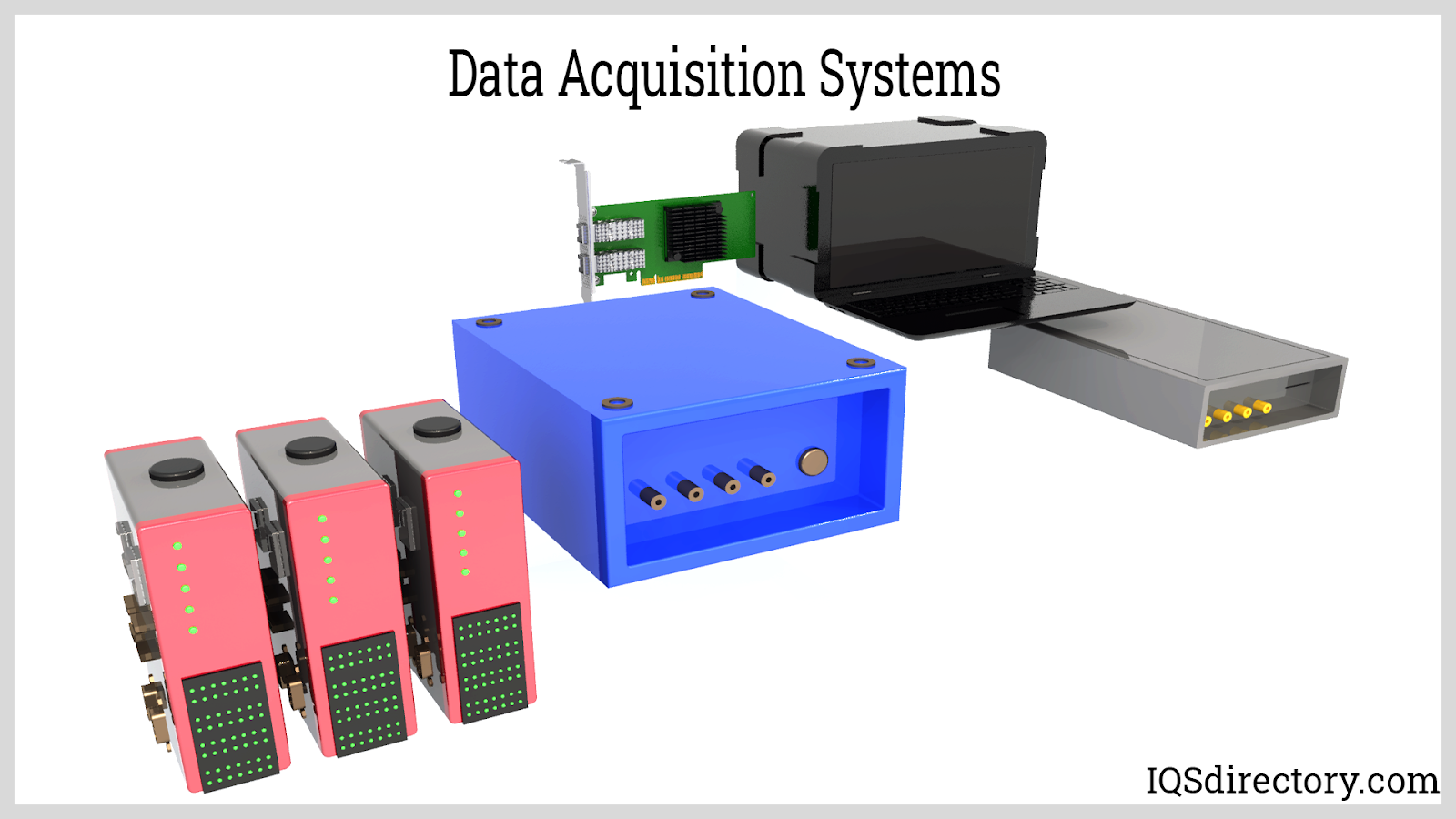
A data acquisition system is a system that comprises sensors, measurement devices, and a computer. A data acquisition system is used for processing acquired data, which involves collecting the information...
Please fill out the following form to submit a Request for Quote to any of the following companies listed on
Details regarding the types of scales and their manufacturers
You will learn:
Scales are categorized based on the materials they measure and their intended function. While numerous types exist, they generally fall into three main groups: mechanical, digital, and analytical scales. Digital scales are particularly popular due to their high precision and accuracy.
Mechanical scales are considered the traditional form of weighing devices, functioning with a spring or lever system, and are commonly found in residential and commercial settings. The development of the load cell, dating back to the first industrial revolution, has profoundly transformed the weighing industry, establishing digital scales as the most dependable option. In environments like research labs, scientific experiments, and the chemical field, analytical scales or balances are indispensable for their precise measurement of tiny quantities. These scales utilize electromagnetic force restoration (EMFR) technology to achieve precise measurements down to a thousandth of a gram or milligram (mg).
The fundamental concept behind scales is grounded in the gravitational pull on objects. This principle is widely used to weigh food, chemicals, and people, providing a standard measurement method. A typical scale calculates weight by measuring the force exerted by a mass times the gravitational acceleration.
For incredibly precise measurements, comparative techniques, also known as balance measurements, are utilized, where the weight of an object is compared to a standard reference or matching object. These scales are extremely accurate and are essential for scientific and technical applications.
The two classic types of scales are digital and mechanical. The use of scales for weighing materials, things, objects, products, and commodities has been around for centuries using a long list of measurement units. Although modern society has embraced the metric system, every society, culture, and country on earth has had its own method for identifying weights and measures.
The use of mechanical weight measuring devices is based on the force of gravity using readings created by the compression of springs. In very ancient times, measurements were taken using a balance where the item being weighed was compared to a rock, piece of metal, or something of the same size. Eventually, due to inaccuracies, different methods were developed that improved readings and the credibility of measurements. In the 18th century, spring scales were introduced that used the effects of gravity on a spring using Hooke’s Law.
In the latter part of the 20th century, scales were introduced that measured weight using electrical resistance to detect changes in conductivity according to the pressure placed on a scale. Referred to as digital weighing scales, this highly advanced form of scale uses load cells and strain gauges for precision measurements. When an object is placed on a digital scale, the exerted force is converted into an electrical signal that is displayed on a digital screen.
The modern era saw the introduction of digital measuring scales that calculate measurements using electrical resistance. As precise and accurate as digital scales are, they are unable to measure minute quantities of less than a tenth of a gram, precision measurements that are necessary for scientific and chemical research and experiments. In 1945, the Mettler Toledo company introduced analytical scales that measure weight using a combination of electrical and mechanical components. Referred to as EMFR Weigh Cells, analytical scales measure the force necessary to counter the mass being measured.
The evolution of scales has taken many forms as technology has advanced and the need for accuracy has increased. In the 21st century, new methods are being developed that use the integration of advanced touch screen technology with the internet of things (IoT) to connect scales and methods of weighing to the internet.
Mechanical beam scales take several forms and are used to weigh chemicals in a laboratory and shipments for delivery. The design of mechanical beam scales includes the use of the lever principle where a fulcrum is placed between the force of the counterweights and the load. Mechanical beam scales take several forms with some having a pan attached to a beam with weights on it to platform scales. The load is placed on the platform and weights are added to the beam until it balances. The determination of the weight of the load is determined by the amount of weight that has been added.
Floor scales are heavy duty scales that are used to weigh large loads up to 600 kg (1322.77 lbs.). They are designed to weigh pallets and are referred to as platform or pallet scales. To accommodate the needs of a variety of industries, floor scales are available in an assortment of shapes and sizes. The types of floor scales include deck scales, drum scales, and portable scales that can be moved to load locations. Designed for industrial work environments, floor scales can have several features, such as counting and check weighing. The durability of floor scales enables them to do repetitive heavy-duty work in demanding and harsh environments.
Counting scales are used to simultaneously count and weigh a variety of items and objects. Their ability to weigh and count materials is based on a comparative process where the weight of one item is recorded by the scale or entered by a user. When a collection of the same items is placed on the scale, it divides the total weight by the weight of the recorded or entered item.
Uses for counting scales include checking the number of pieces in a lot, CD manufacturers, metal workers, and plumbing supply companies. Counting scales make it possible to check lots and create identical lots with the correct number of pieces, which speeds up inventory and packaging. They save time, increase efficiency, and eliminate certain mundane counting processes.
Crane scales, also referred to as hanging scales, make it possible to weigh extremely large loads suspended from crane hooks. They are used in industries where lifting and weighing such loads is a typical part of daily operations and processes. The working mechanism for crane scales is a load cell, which converts force applied by a load into an electronic digital signal. Included with crane scales is overload protection that prevents damage to the load and scale by signally that the load is greater than the capacity of the crane.
The versatility of crane scales makes it possible to weigh materials at mid-lift, which helps in avoiding accidents and overloads. The unique nature of heavy loads and the variety of loading and unloading operations has led to the development of different types of crane scales, which include digital, electronic, and hydraulic.
Washdown scales are waterproof and designed for environments where the use of water for cleaning a scale is necessary. They can be hosed, steam cleaned, and used in conditions where caustic chemicals are present. Any type of scale can be a washdown scale, which is determined by a scale’s construction.
The standards for washdown scale design are determined by the European Hygienic Engineering and Design Group (EHEDG) and the National Sanitation Foundation (NSF), which outline construction materials, accessibility for cleaning, and how waste material accumulation is avoided. The ingress protection or IP rating of a scale from the International Electrotechnical Commission (IEC) determines if a scale is a washdown scale.
The IEC developed ingress protection codes in order to determine the resistance of enclosures against dust and liquids. Since their inception, IP codes have become a standard that industries use to rate their products. IP rating codes consist of two numbers. The first number is a rating of solid objects while the second number refers to protection against liquids. Each scale begins at zero with the solid’s rating being from 0 to 6 and the liquid’s rating being from 0 to 9.
Most washdown scales use strain gauges or electromagnetic force compensators that are protected from the negative effects of exposure to damaging materials for providing accurate and precise weight readouts. This unique and durable type of scale is widely used in the food, retail, medical, pharmaceutical, and manufacturing industries.
The standard form of a truck scale includes a concrete base with a weighbridge, 6 to 15 load cells, and some form of digital readout or junction box. The weighbridge is the surface upon which a truck is driven to be weighed and is constructed of heavy-duty materials to be able to endure the weight of trucks. Although weighbridge truck scales are common, recently, advanced types of truck scales have been introduced referred to as weigh-in-motion scales where trucks are weighed as they drive through the scale.
The weight of a truck is calculated using its axle weight and gross weight. The axle weight of a truck is the amount of weight that is carried by each tandem axle, which is found by dividing the weight of the load and trailer by the number of axles. The gross load is the weight of all parts of a truck including the load, trailer, tractor, and accessories.
As one might imagine, the load cells for truck scales are larger, heavy duty, and made of high-grade steel. Each type of truck scale uses a different type of load cell, such as canister, double ended shear beams, or simple floor load cells. Truck scales have between 6 to 15 load cells placed between the ground and the weighbridge. When the weighbridge is compressed, each load cell sends a signal based on the force of the compression.
Since the multiple load cells are sending multiple signals, truck scales have to have some form of device that combines the inputted data from the load cells to be interpreted by an operator. This aspect of the weight reading is completed by the junction box that combines the information from the load cells and presents a single reading. The operator runs the raw data from the reading through truck scale software, which provides a concise reading in regard to the weight of a truck.
Aside from axle scales, weigh-in-motion scales, and standard weighbridge platform scales, there are short term portable truck scales, which are flexible and adaptable to a wide variety of conditions. Portable truck scales have the same elements as all other forms of truck scales but can be positioned, moved, and adapted to a wide variety of conditions without diminishing accuracy.
The weighbridge of portable truck scales is securely locked down for safety and ensure top performance. They have a single unit construction using bulkhead assemblies, a design that allows for easy transport and avoids any need for disassembly. Once installed, each load cell is calibrated and checked.
Conveyor scales, also known as belt scales, measure the weight of materials as they move along a conveyor belt. They use load cell technology for bulk material measurements, inventory control, and process monitoring. Using a weighbridge, conveyor scales are installed on belt conveyors and measure loads as they move along a conveyor belt. They have one or more load cells and a speed sensor. As the load cell measures the weight of items, the speed sensor collects distance and speed data.
The systems for conveyor scales use the speed and weight data to determine material flow rates and the total amount of material moved during a specified time period, all of which is sent to a digital display. Conveyor belt scales are integrating weighing scales that use an integral calculus process to determine conveyed material quantities. The captured weight includes the weight of the belt, its idler, and the material on the belt. The weight of the material is the gross weight minus the belt and idler.
In addition to belt conveyor scales, there are roller conveyor scales that operate the same way as belt conveyors. Load cells are placed below the rollers. Adjustable feet make it easy to integrate the scale into a roller conveying system. As with conveyor belt scales, roller conveyor scales are designed to save time and material handling.
As with all forms of scales, conveyor and roller scales are custom adjusted to meet the requirements of a customer’s products and operation. Manufacturers work closely with their clients to ensure a perfect fit between client requirements and their conveyor scale. The majority of conveyor scales are manufactured with an IP rating of 67 for dust and liquid protection and a temperature range of 0°C to 70°C (32°F to 158°F).
Bench scales and compact balances and scales are similar in that both are portable and can be set on a bench, desk, or table. The difference between them is size with compact balances and scales being smaller while bench scales are normally larger and have a higher capacity. By comparison, bench scales have a capacity range of 1.5 kg up to 60 kg (3.3 lbs. up to 132.3 lbs.) while portable compact balances and scales have a capacity range of 0.001 g up to 0.05 kg (3.53 oz up to 1.76 oz).
The unique uses of bench scales have led to the development of several varieties of bench scales with each type having features and accessories that match the applications for which they are used. Some bench scales are used for a single application or operation and are designed specifically for the application. Other more gregarious bench scales are adaptable to a variety of applications, processes, and operations, which makes it possible to use the same scale for several different purposes.
The structure of bench scales varies depending on the conditions and environment where they are used. Less critical bench scales are made of plastic or light metals while more substantial bench scales are made of stainless steel or heavy metals. As the conditions for a bench scale become more hazardous, their durability, toughness, and resilience increase. Manufacturers work closely with their clients to define the conditions under which a bench scale is used in order to select the correct bench scale for an application.
The shape, size, and design of bench scales vary with some being very technical providing precision measurements while others supply rudimentary measurements or estimates. The data produced by a bench scale can be a critical and essential part of a process, such as a conveyor bench scale or roller top bench scale. A special feature that can be included in bench scales is a visual or audio signal to alert users to results and integration into other systems.
The eight scales described above is a small sampling of the thousands of scales scale manufacturers offer. In essence, there is a different type of scale or weighing device for every application, process, operation, and contingency. The key to the use of weighing scales is working with a manufacturer to choose the right scale for the application for which it is being used. Working closely with industry experts can avoid headaches and provide insight and guidance that leads to success.
The use of scales and devices for weighing have existed for thousands of years going back to the time of the ancient Egyptian empires. Until the middle of the first industrial revolution of the 19th century, a variety of mechanical processes were used to determine the weight of objects or materials.
The ancient processes of weighing involved the manual placing of objects on a scale and using pen and paper to record weights and measures. The readings that were collected varied by culture, country, and society, which made it impossible for weights to be the same when shipped. Accuracy, efficiency, and information were limited. In the latter part of the 19th century, things began to change and have continued to change.
Mechanical scales are one of the oldest types of scales. They have been used for centuries to determine the weight of objects and materials. The fundamental process of mechanical scales is in regard to the force of gravity that pulls an object toward the center of the earth. The systems for mechanical scales include springs and balances.
When a load is placed on a scale using a coiled spring system of weight measurement, the load compresses the spring as the force of gravity pulls the load toward the center of the earth. As the load forces the compression of the spring, an incremental numbered dial rotates to a number that indicates the weight of the load.
Spring scales are based on Hooke’s Law that says the amount of force that pulls on a spring is proportional to the length that the spring extends. When something is hung from a spring, its weight can be calculated as the distance the spring extends and the pulling force.
The other form of mechanical scale is a balance scale, which is a comparative scale. Balance scales are very ancient and harken back to thousands of years ago. Unlike spring scales, balance scales use free weights that are compared to the weight of the object being monitored. In most cases, balance scales consist of a beam with a cross bar that holds two containers suspended from either end. The object to be weighed is placed in one end and weights are added to the container at the other end until they balance and the cross beam is perpendicular to the support beam.
Regardless of the simplicity and inaccuracy of these weighing methods, they are still used today for certain applications. Both methods are easy to access and do not require any form of power. Their use is limited to simple weighing applications such as home projects and cooking.
The modern era has led to an increase in the requirements of accuracy and precision. From the beginning of the 20th century up to the present, technological advancements have led to the development of weighing methods that are precise and exact using various electronic tools.
The introduction of load cells into weight measurement was a huge leap forward in the accuracy and reliability of recording the weight of objects. A type of transducer that converts force into electrical signals, load cells have become a central part of a wide range of weight measuring devices. When force is applied to a load cell, it generates an electrical signal that is measured and digitized. Load cells are precision measurement instruments designed to measure weight with exceptional accuracy.
When a load is placed on a load cell, the load cell bends slightly, which creates an electrical signal that runs through the load cell indicating a change. The generated signal is caused by electrical resistance from the bending, which affects a strain gauge located in the load cell. The signal is read by a digital weight indicator and changed into a digital weight value that appears on a digital display.
The distinction between scales is due to the different types of load cells used to make them. Load cells are classified by their output signal, such as pneumatic, hydraulic, strain gauge, and capacitance, and how they detect weight, which includes bending, shear, compression, and tension.
Hydraulic load cells use a fluid, under pressure, and a piston to measure weight. When a load is placed on the platform of a hydraulic load cell scale, the piston applies pressure to the liquid. The increase in pressure is proportional to the amount of applied weight. After the pressure is calibrated, it is used as a reading for an analogue gauge or is converted into an electrical signal. Accuracy for hydraulic load cell scales can be within 0.25% or better. Since hydraulic load cells do not require electricity, they are used in hazardous conditions.
The popularity of hydraulic load cells is due to their accuracy and reliability. They can measure a wide range of weights and are easy to install and maintain. The different types of hydraulic load cells include single ended, double ended, and cantilever, which are chosen in accordance with the type of application and system requirements.
Pneumatic load cells use air pressure to measure weight and have an elastic diaphragm that is attached to the weighing platform. As with hydraulic load cells, pneumatic load cells operate on the force balance principle and have an air regulator to control air flow pressure and a pressure gauge. Pressurized air is used to balance the weight of the item being weighed. The amount of air required to achieve balance is the weight of the object being weighed. A pressure gauge converts the reading into an electrical signal.
Strain gauge load cells, known as single point load cells, parallelogram sensors, and shear beam load cells, measure tension and compression. When tension is applied to a strain gauge load cell, it gets longer and thinner, increasing resistance. Compression forces cause a strain gauge to get thicker and shorter, decreasing resistance. When a load is applied to a strain gauge, it produces an electrical signal that provides a weight reading. Most scales have more than one strain gauge to increase the accuracy of readings. The structure of a strain gauge includes fine wire or foil arranged in a grid pattern to measure linear changes in resistance.
The different types of strain gauge arrangements include quarter bridge with one strain gauge, half bridge with two strain gauges, and full bridge with four strain gauges, which is referred to as a Wheatstone Bridge. With a linear strain gauge wire is attached to the backing and runs parallel to the strain gauge’s edge. Shear strain gauges have the wire laid out at a 45o angle to the sides of the strain gauge.
Strain gauges are available in a wide range of sizes, types, and shapes. They are popular due to their accuracy, reliability, and adaptability.
Capacitive load cells have two parallel plates with a gap between them. Electric current is applied to the plates until a stable charge is reached, one positive and one negative. The area between the plates is filled with a dielectric material. When a load is applied to one of the plates, the gap between the plates and the dielectric material narrows creating a stored capacitance. The charge or capacitance is the output of the load cell, which is converted into a measurement of weight.
The capacitance factor of a capacitive load cell is the ability to store an electrical charge. For capacitive load cells, capacitance is proportional to the dielectric material between the plates. Capacitors for capacitive load cells can take several shapes including flat, cylindrical, and spherical, and is referred to as the capacitive strain gauge.
Load cell technology is ever changing with new types of load cells being produced to meet the needs of a wide range of applications and processes. The four load cells described above are a sampling of the many types of load cells. In some cases, the names of the types of load cells varies between manufacturers even though the processing method of the load cells may be the same.
The process for EMFR weigh cells is based on the simple balance beam mechanism. Its basic structure includes a position indicator, controller, and an electromagnetic drive. When a load is placed on one side of the platform, the opposite side works to move out of the field of the magnet. The position indicator detects the change and transmits the current necessary to create a balance. The current that is required is measured and converted into a digital signal.
The principle behind electromagnetic force restoration is the same as that of a simple beam balance where an item to be weighed is placed in one container as weights are added to another container on the other side of the balance beam until the item and weights are at the same level. In the case of EMFR weigh balances, electrical force is applied instead of weights. The amount of electricity changes in accordance with the weight of the item being sampled. The change is transmitted to a display as an item’s numerical weight.
EMFR weigh cells are used as part of in motion weighing systems. The speed of EMFR weigh cells enables them to weigh products as the products move over the cells. The accuracy of the weights increases production efficiency and speed.
Scales provide accurate measurements for enhancing product quality and ensuring proper pricing. Their use covers a wide spectrum of industrial, commercial, and residential applications, from weighing flour for food production to counting parts for inventory control. Scales for laboratories, manufacturing, and industrial operations are carefully selected in conjunction with scale manufacturers, whose expertise, knowledge, and experience ensure a selected scale meets the needs of an application.
Analytical scales are scientific instruments that provide precision weighing for research and laboratories. They are accurate up to 0.0001 grams (3.52 oz) and are used for chemical testing, drug manufacturing, and various scientific processes. Designed to measure materials in extremely small increments, analytical scales are reliable and exceptionally accurate. To prevent outside interference, analytical scales have enclosures for items being measured.
Commercial scales are used for a variety of applications from piece counting to computing prices. They provide packaging information and product counts for retail pricing and are regulated by the National Bureau of Standards, which stipulates accuracy requirements and how labels are to be printed. The regulations are for the protection of consumers. The types of commercial scales include bench or table top, pricing, counting, platform, application indicators, hanging, and industrial scales for large orders.
Medical scales are used to measure body weight and health related factors. There are many varieties of medical industry scales each of which is designed for a specific function and patient group. Some of the common forms of medical industry scales include infant scales, adult scales, growth monitoring scales, and body mass index (BMI) scales for comparative analysis.
Modern medical scales offer a wide variety of features and technological advancements that improve the accuracy of readings and provide more accurate data. Some forms of digital medical scales are capable of transferring data to a computer system and patient records. An important feature of medical scales is patient safety, which includes non-slip mats and baby cradles.
Accuracy in manufacturing has become a critical issue in the modern era. Industrial scales ensure that the right amount of materials is being used such that the final product meets design parameters. Over the years, the accuracy of industrial scales has radically improved to meet customer standards and government requirements. Some of the types of industrial scales include platform, bench, portion, counting, and crane scales. Industrial scales are used for their efficiency, accuracy, real time data, productivity, and cost savings. The high quality of scales manufactured for industrial use has benefited the meat, food, pharmaceutical, and chemical industries. Industrial users work closely with scale manufacturers who provide scales that match the requirements of a user’s industry.
Accuracy in weighing materials has become a necessity for modern manufacturing. Technological advances and innovations have significantly improved the mechanisms used to weigh and assess quantities and amounts of materials. These developments have revolutionized manufacturing and industrial operations.
The technology of weighing has made processes more precise with the use of load cell technology and various sensing devices. Load cells use strain gauges to convert force into electrical signals, which enhances the accuracy of weighing systems. Many industries rely on weighing precision where the slightest deviation can have catastrophic consequences.
Weighing scales are now integrated into production to streamline processes, eliminate human errors, and increase productivity. Automated weighing technologies enable seamless weighing, labelling, and packaging, which eliminates bottlenecks and removes the need for manual labor. Data monitoring has been improved with wireless connectivity and internet of things (IoT) integration that provide real time data, makes workflow more efficient, and assists with decision making. Additionally, the data collected from scales improves inventory management and helps maintain proper stock levels and fulfillment processes.
The interconnection of modern weighing scales with devices and cloud platforms makes access to real time data easier, provides quick notifications, and makes it possible to control operations from off site locations. Access to these assets provides convenience, predictive maintenance, and rapid response to negative issues.
Modern industrial operations rely on accurate and up to date data in order to make decisions and adjustments. Data analytics, artificial intelligence (AI), and machine learning provide information coordinated with weighing data. These instruments help in noticing patterns, improve processes, enhance planning, and help with decisions that are profitable and efficient.
Modern society is a technology driven culture that has opened a world of analytics for the weighing scale industry. The integration of weighing systems with other technologies improves the efficiency of processes and enables accurate identification of products using error free methods for product identification.
The best technology in the world relies on users to input data, check status, and oversee operations. Modern weighing systems have been significantly upgraded to include intuitive interfaces with touchscreens and other features to simplify and enhance operations. Users can quickly complete weighing tasks to help improve productivity and efficiency.
Regardless of the era, the key to a business’ success is high quality products that perform according to their description. The integration of weighing systems makes it possible to monitor production processes in real time to ensure adherence to product parameters and compliance with industry regulations.
As with quality control, the supply chain is an old business function that is crucial to the success of a business. With modern methods, weighing data is passed to the supply chain from which it flows to suppliers for retailers, manufacturers, and distributors. The integration of the different factors improves visibility, logistics, and leads to better inventory management, reduction of waste, and improved billing. Having easily available weighing data enables better demand forecasting, making it possible to manage production that is in line with market changes.
The simple process of product weighing has moved far beyond the old days of balance scales using rocks. Modern weighing scales are capable of a wide range of technological and innovative advancements that enhance manufacturing operations and improve profitability. The transformation of the weighing industry from mechanical scales to high tech load cells has made it possible to integrate weighing systems into modern data sharing devices.
A data acquisition system is a system that comprises sensors, measurement devices, and a computer. A data acquisition system is used for processing acquired data, which involves collecting the information...
Force sensors are transducers that transform mechanical input forces like weight, tension, compression, torque, strain, stress, or pressure into an electrical output signal whose value can be used to...
A load cell is a transducer which converts mechanical energy (tensile and compressive forces) into electrical signals. There are different transducer operating principles that can be utilized to convert forces...
A load pin is a sensor utilized to measure force or weight in various research, control, measurement and testing applications. The load pin force sensor converts a force into an electrical signal. The load pins provide...
A strain gauge, or strain gage, is a sensing device used for measuring strain experienced by an object. It is made from a long, thin piece of conductor bonded to an elastic backing material called a carrier...
At the heart of every weighing device is a sensor called a load cell. When an item is put on a load cell, it senses the force of the gravitational pull of the weight, which an electronic circuit processes to display...