Belt Conveyors
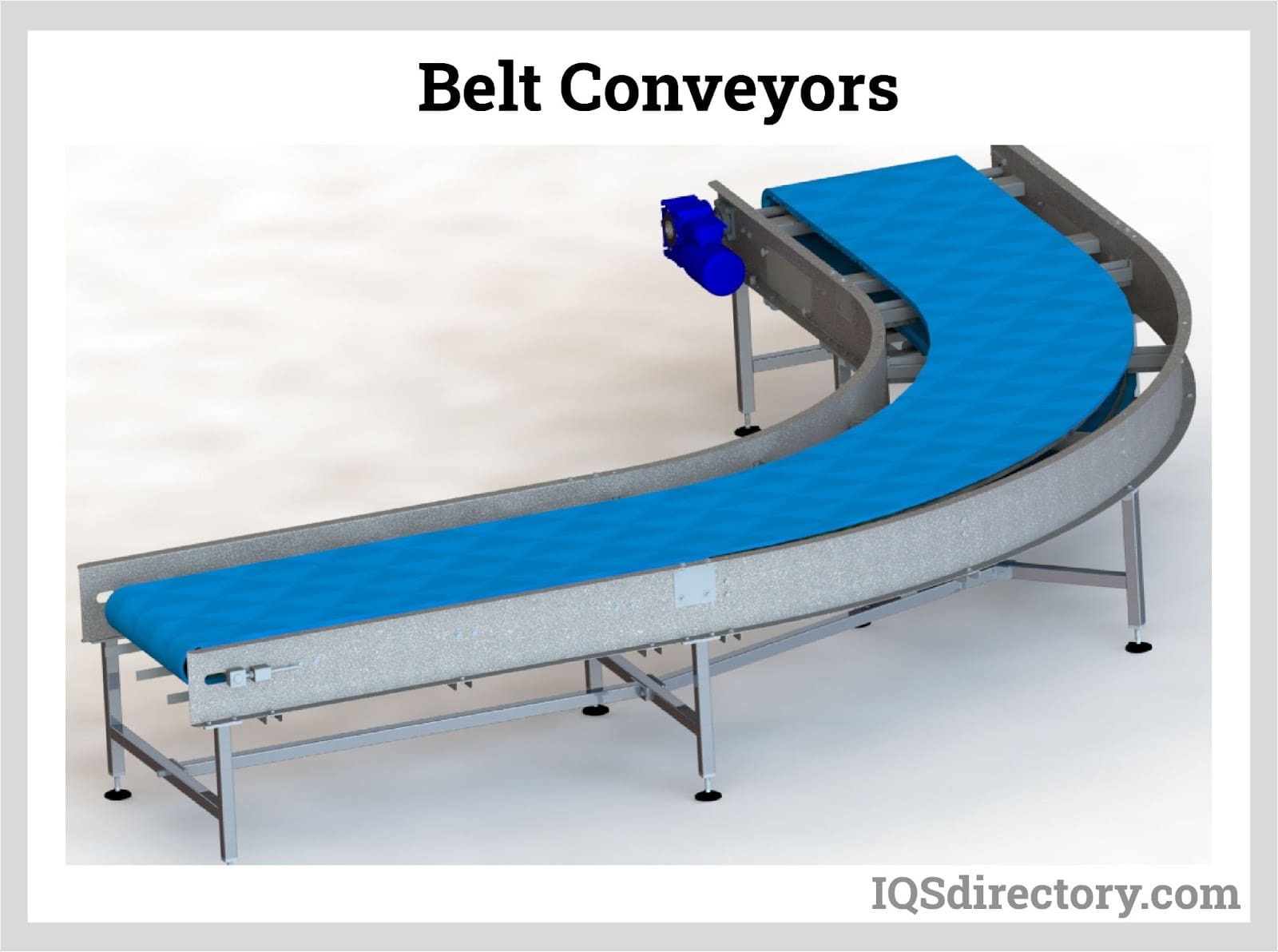
A belt conveyor is a system designed to transport or move physical items like materials, goods, even people from one point to another. Unlike other conveying means that employ chains, spirals, hydraulics, etc...
Please fill out the following form to submit a Request for Quote to any of the following companies listed on
This article takes an in depth look at screw conveyors.
Read further to learn more about topics such as:
Screw conveyors, also referred to as auger conveyors, are industrial machines meticulously engineered to efficiently move large quantities of granular materials like powders, grains, and granules. They can also transport semi-solids, liquids, and materials that do not flow easily. By eliminating the necessity of manual material handling, they significantly boost operational productivity. The fundamental parts of a screw conveyor include a rotating screw shaft placed inside a trough. When this screw shaft rotates, it propels the material forward in a straight path. Screw conveyors can be set up for transportation along horizontal, vertical, or inclined routes.
Diverse types of screw conveyors are crafted to manage different material properties. Materials in bulk can be abrasive, non-flowing, fluidizable, absorb moisture (hygroscopic), or pose hazards. Screw conveyors proficiently handle products such as cereals, fertilizers, animal feed, ash, gravel, cement, and solid waste.
The Archimedes screw, dating back to approximately 250 B.C., represents the earliest screw conveyor form. Originally devised as a primitive positive displacement pump, it was employed to lift water from lower levels to upper irrigation channels. Through the years, the design and driving mechanisms of Archimedes screws have been enhanced to improve their effectiveness, sturdiness, and speed, all while maintaining the foundational concept of the original invention.
The following are the components of screw conveyors and their various types based on design features:
The conveyor screw is a crucial element of a screw conveyor, tasked with moving solids along the length of the trough. It consists of a shaft with a broad blade that spirals helically around it. This spiral blade is known as the flight. Conveyor screws operate similarly to large screws, where material is displaced by one pitch with each full rotation of the screw. The pitch refers to the axial distance between consecutive flight crests. As the conveyor screw turns to transport the material, it remains stationary in the axial direction.
Here are the types of screw conveyors categorized by their flight and pitch design:
Standard pitch screw conveyors have a pitch that matches the diameter of the screw. The screw diameter refers to the radial distance between successive flight crests. These conveyors are typically used in horizontal applications and inclined conveyors with an angle of less than 10°. They are effective for handling a wide range of materials.
In variable pitch screw conveyors, the pitches increase variably across the screw flight. The pitch is longer at the inlet side to provide additional space for the fed materials as they are being discharged from hoppers, bins, or silos. Variable pitch screw conveyors are used in screw feeders for a controlled volumetric flow rate of materials.
In short pitch screw conveyors, the pitch is two-thirds of the screw diameter. These conveyors are often used in inclined and vertical applications, as well as for transporting free-flowing materials to avoid flushing.
In half pitch screw conveyors, the pitch is half of the screw diameter. These conveyors are utilized in inclined and vertical screw conveyor applications as well.
Long-pitch screw conveyors feature a pitch that is one and a half times the diameter of the screw. These conveyors are ideal for moving liquids and free-flowing materials, as well as for high-speed material handling operations. They are also effective in agitating the materials being transported.
Double flight screw conveyors feature two helical sets of flights along the length of the screw, which speeds up the conveying process. The flights are offset by 180°. Similar to standard pitch screw conveyors, the pitch in double flight screw conveyors matches the screw diameter. These conveyors provide a consistent material flow rate and smooth operation during transport.
Tapered flight screw conveyors feature a constant pitch while the flight width progressively expands from two-thirds of the screw diameter at the inlet to the full diameter at the discharge end. This design provides extra space for the material at the inlet, allowing for even material flow. Tapered flight conveyors are a cost-effective alternative to variable pitch screw conveyors and are particularly effective for handling lumpy solids.
Mass flow screw conveyors feature a conical screw with consistent flight pitches near the feed inlet. This conical section transitions into a variable pitch screw as it extends towards the discharge. They are designed to ensure consistent material withdrawal from hoppers, bins, or silos, promoting even material flow. The volume of material handled progressively increases with each flight as it moves through the conveyor.
Here are the different types of screw conveyors categorized by their flight construction:
Helicoid flight screw conveyors feature flights made from flat steel bars or strips that are cold-rolled into a helical shape. This process work-hardens and strengthens the material, resulting in a smooth flight surface. The flights have a thicker base that tapers to a thinner edge at the outer perimeter. These helicoid flights are attached to the central shaft by welding the short, individual flights together. The flights along the shaft are secured with intermittent welds at each end of the flights.
Helicoid flight screw conveyors are known for their durability and high load-bearing capacity while being cost-efficient. They are suitable for handling light to moderately abrasive materials, including limestone, cement, and fertilizers.
In sectional flight screw conveyors, the flights are constructed from flat steel discs with uniform inside and outside diameters. The discs are cut to extend its length using a plasma, water jet, or laser cutter and pressed to form a helix or the individual flight which corresponds to one revolution. The sectional flight conveyor screw is assembled in the same manner as the helicoid conveyor screw.
Sectional flights maintain a uniform material thickness throughout. There are also thicker options available, making sectional flight screw conveyors well-suited for transporting highly abrasive substances like glass cullet and alumina.
There are special designs of conveyor screw flights that have different geometrical designs and serve other functions in addition to material transportation:
Cut flight screw conveyors feature notches cut into the outer edge of the screw flight at consistent intervals. These notches facilitate the mixing and agitation of the conveyed bulk material. This type of conveyor is effective for materials that are prone to packing, including hydrated lime, dried milk, and talc.
Cut and folded flight screw conveyors incorporate both notches and folds along the outer edge of the screw flight. The folds are elevated from the flight's surface, and together with the notches, they partially slow down the material flow, enhancing mixing. These features also aid in aerating lightweight materials and ensure even temperature distribution during heating and cooling processes.
Ribbon screw conveyors are designed with an open space between the inner edges of the flight and the central shaft. These conveyors can be built with either single or double flight configurations:
They are generally well-suited for moving sticky and viscous materials that have a tendency to accumulate around the conveyor screw shaft.
Double Flight Ribbon Screw Conveyors are effective for transporting sticky substances and offer more consistent material discharge. They can also be configured for blending dry materials. In this setup, the conveyor features an outer ribbon flight and an inner ribbon flight, each with a reduced diameter, and both flights rotate in opposite directions. This configuration facilitates thorough mixing by causing the material to move back and forth within the conveyor.
This screw conveyor design incorporates paddles placed between the screw flights to gently and effectively blend bulk materials.
This screw conveyor design features adjustable paddles arranged helically along the screw shaft. Each pitch can include up to four paddles, which intensify the mixing of bulk materials and manage their flow. While it offers the most vigorous mixing action, it is the least efficient of all types.
The direction in which a screw conveyor moves material is determined by its handedness, which refers to the rotation direction of the conveyor screw. A screw conveyor can be either right-handed or left-handed. A right-handed screw conveyor moves material towards the end of the screw when rotated clockwise, while a left-handed screw conveyor does so when rotated counterclockwise. Reversing the screw’s rotation direction also reverses the material flow, but it is generally not recommended as material should be managed on the carrying side of the flight.
Handedness is identified by looking at the end of the screw conveyor. For right-handed screw conveyors, the flighting wraps around the shaft in a clockwise direction, whereas for left-handed conveyors, it wraps in a counterclockwise direction. Right-handed screw conveyors are more commonly used than their left-handed counterparts.
The screw conveyor's trough encloses the conveyor screw and provides support for the bulk material as it is transported. It can be reinforced with saddles or flanged feet along its length. A durable, removable cover extends over the trough to safeguard the bulk material from contamination, dust, and potential hazards.
The trough also includes access points for feeding and extracting bulk material. Typically, the trough inlet connects to other equipment such as belt conveyors, rotary valves, and screw feeders that regulate or measure the material entering the screw conveyor. These components are often linked to hoppers, silos, and bins that store the bulk material. Alternatively, the trough inlet may be situated directly at the discharge side of upstream processing equipment.
There are several types of screw conveyor troughs:
The U-shaped trough is the most widely used and adaptable type of screw conveyor trough. It is economical and features a straightforward design.
Rectangular troughs are designed to handle abrasive materials during transport. The space between the conveyor screw and the trough walls becomes filled with the bulk material. This static layer of material helps shield the trough walls from wear and damage.
Tubular troughs are designed to handle larger screw diameters and offer protection for bulk materials from environmental factors such as dust and weather. They can operate at higher speeds and provide greater capacity per revolution, with conveying angles ranging from 1% to 2% based on minute-to-minute measurements. These troughs are also compatible with inclined screw conveyors.
The popularity of tubular troughs stems from their precise operation, which surpasses that of “U” shaped troughs due to the close fit of the screw within a defined volume tube. This design minimizes variations in density, air pockets, and material clumps, especially when the tube is vibrated.
Tubular troughs are categorized based on their construction into non-split and split tubular troughs. Non-split troughs are constructed as a single piece, whereas split tubular troughs consist of two halves joined by flanges.
A jacketed trough is a specialized screw conveyor trough designed to control the temperature of the bulk material during transport. It achieves this by either heating or cooling the material as it moves through the conveyor. Jacketed troughs are constructed with concentric layers, allowing a utility fluid to circulate between them to regulate temperature effectively.
The material chosen for constructing the trough depends on the specific application, the type of screw conveyor, and the level of corrosion or abrasion resistance required.
Hanger bearings provide support for the various sections of the conveyor screw and offer a bearing surface. These components feature a plain linear bearing that is suspended and enclosed in a frame designed to fit within the conveyor screw trough.
Couplings enable the transfer of torque between different sections of the screw by accommodating any misalignment between the screw shafts. They enhance the operational efficiency of the screw conveyor. Both couplings and hanger bearings are essential when extending the length of the screw conveyor.
The internal collar is a continuous tube fitted at the end of the screw shaft. It serves to narrow the internal diameter of the shaft to match standard-sized fittings.
End lugs are positioned on the non-carrying side of both the initial and final flights of the conveyor screw. They help to prevent material accumulation at the ends of the screw, ensuring unobstructed flow and offering extra support to the screw.
Screw conveyors are driven by an electric motor situated close to the trough's discharge end. This setup facilitates the natural movement of bulk material towards the drive end, reducing tension on the screw flights and minimizing wear and tear on the conveyor components.
Screw conveyors can utilize a variety of drive assemblies. A common configuration includes a single or double shaft-mounted speed reducer paired with a V-belt drive and motor, all mounted on the conveyor housing. The drive assembly can be installed either vertically or horizontally.
Gear motor drives may involve direct low-speed couplings attached to the conveyor shaft or roller chain drives with couplings positioned at the trough ends and chains running along the top of the conveyor. Gear drives are favored for their ability to deliver high horsepower and offer variable speed options.
Screw conveyors can be categorized based on the different flow paths they provide for transporting bulk materials:
Horizontal screw conveyors represent the most straightforward type of screw conveyors. They can accommodate a diverse range of bulk material types and efficiently distribute materials to different locations through multiple inlets and discharge points. These conveyors are typically designed to have a trough loading capacity ranging from 15-45%.
Trough loading denotes the maximum depth at which the trough can be filled without causing excessive wear or stress on the screw conveyor components. This capacity depends on the characteristics of the bulk material being transported and is crucial for proper sizing of the screw conveyor. Generally, the trough loading can be higher for lightweight, free-flowing, and non-abrasive materials, while it needs to be lower for thick, heavy, and abrasive substances.
Inclined screw conveyors offer an inclined path that eliminates the need for additional conveying equipment for transporting bulk materials to or from an elevated surface. An alternative to this type is the use of two pieces of conveying equipment: one piece of equipment for horizontal transportation and one for vertical transportation. However, this setup is expensive and consumes more space.
An inclined screw conveyor can have an angle of inclination ranging from 0° to 45° above the horizontal. As this angle increases, both the efficiency and load capacity of the screw conveyor tend to decrease, and the power requirement rises due to gravitational pull and material fallback. To mitigate these negative effects, a reduced pitch conveyor screw (such as one-half or two-thirds of the screw diameter) is used, which offers a better conveying surface and minimizes material fallback. Additionally, tubular troughs help in reducing material fallback.
Vertical screw conveyors transport bulk materials on vertical paths and very steep inclines with an angle of inclination greater than 45° above the horizontal. They are also space- and cost-efficient in transporting bulk materials. Controlling the amount of bulk material fed to the screw conveyor is critical for vertical screw conveyors to maintain a constant speed, reduce wear and power consumption, and increase the conveyor efficiency. Hence, bulk metering devices such as screw feeders are necessary.
Here are the other types of screw conveyors:
Shaftless screw conveyors eliminate the need for a conveyor shaft screw and internal bearings, reducing material build-up and flow obstruction. This makes them ideal for conveying sticky, viscous, and sluggish materials. These conveyors simplify the conveying process and enhance efficiency, and they are often used to move products from mixers, centrifuges, and filters.
The shaftless spiral in these conveyors allows for higher filling rates and lower RPMs, resulting in less wear and reduced maintenance needs. Spirals can be constructed from various materials, including a special Swedish steel known for its exceptional mechanical properties and high tensile strength.
Designed for handling challenging materials, shaftless spiral conveyors are effective for transporting municipal dewatered sludge, wastewater screenings, grit, industrial sludges, and sticky, viscous, and stringy materials.
One advantage of shaftless spiral conveyors is their ability to transfer materials efficiently and directly – whether horizontally, on an incline, or vertically – into another conveyor. Their durability can be extended with liners, such as Duraflo SPX®, which feature a wear indicator and can be easily replaced.
Shaftless screw conveyors can be fully enclosed to prevent spillage and control odors. Moreover, their direct drive mechanism ensures clean and efficient material movement.
Live bottom screw conveyors are designed to regulate and control the volume of bulk material being discharged from hoppers, bins, and silos. Typically installed at the bottom of these containers, they feature multiple tapered, variable pitch, or mass flow conveyor screws to manage fluctuations in material volume at the inlet. These conveyors can also function as a screw feeder to supply another screw conveyor.
Flexible screw conveyors are made up of a shaftless conveyor screw and a flexible tubular trough made from UHMW polyethylene. Since both conveyor screw and trough are made from flexible and bendable materials, flexible screw conveyors can transport bulk materials over a wide range of distances, angles, and elevations.
Flexible screw conveyors feature a unique design that saves space by allowing the bulk material path to be easily routed, and enabling convenient placement of the electric motor and discharge outlet. The conveyor screw can be fitted with either a round or flat spiral profile, offering added flexibility and strength. For higher feed rates, a flat spiral profile is used.
When selecting and designing a screw conveyor, it is essential to consider the characteristics of the bulk material to be handled.
It is important to know additional properties of the bulk material, such as density and particle size. Estimating the volumetric and mass feed rate is also crucial. This information helps determine the structural and strength requirements and the appropriate sizing for the screw conveyor.
Finally, the distance and environmental conditions along the material's path must be taken into account.
A belt conveyor is a system designed to transport or move physical items like materials, goods, even people from one point to another. Unlike other conveying means that employ chains, spirals, hydraulics, etc...
A bucket elevator or grain leg is used to move items in bulk. The usage of bucket elevators is widespread, notably in commercial agriculture and mining, and several specialized businesses manufacture bucket elevators and...
Processing equipment for holding and moving bulk bags is known as bulk bag equipment. This bulk bag equipment is typically used at the front end of the production process to hand off product to...
A conveyor belt is a material handling system designed to move supplies, materials, and components using an efficient and effortless process that saves on time, energy, and cost. The design of conveyor belts includes two motorized pulleys with the conveyor material looped over them...
A conveyor system is a method for moving packages, products, supplies, parts, and equipment for production, shipping, or relocation. The different types of conveying systems include pneumatic, screw, belt, and roller. The construction of individual systems depends on the materials...
Flat belts are power transmission belts that are flat and made of rubber, synthetic composites, or leather. They are used to transfer rotational power in industrial equipment and conveyor systems. Flat belts have a low profile with a positive grip, which...
A metal conveyor belt is a conveyor belt that uses metal in the form of flat sheets or woven wire mesh as its belt surface. The use of a metal surface enhances the ability of a conveyor to handle parts and...
Pneumatic conveying is a method for transferring bulk materials, like powders and granules, using compressed gas or air, from one processing center to another. Material is moved through an enclosed conveying line or tube using a combination of pressure differential and airflow from a blower or fan...
Roller conveyors are a type of conveyor belt that allows objects to skate on its surface by using rollers, which are equally spaced revolving cylinders. They transport stuff from one location to another...
A vertical conveyor is an engineered mechanical method for moving goods, products, supplies, parts, and components from a lower level to a higher level or from a higher level to a lower level. They are...
Vibratory conveyors are material-handling equipment used to transport fine to coarse-grained bulk materials. These vibratory conveyors are strong conveying equipment utilized for bulk commodities with fine to coarse graininess...
A timing belt is made of rubber with hard teeth capable of interlocking with camshafts and crankshafts cogwheels. It is an integral component of an internal combustion engine responsible for...
A v-belt is a flexible machine element used to transmit power between a set of grooved pulleys or sheaves. They are characterized as belts having a trapezium cross-section...
Vacuum conveyors are suctioning machines that utilize air pressure in order to move materials through an enclosed pipeline. Vacuum conveyors have broad applications throughout the industrial and...