Swiss Screw Machining
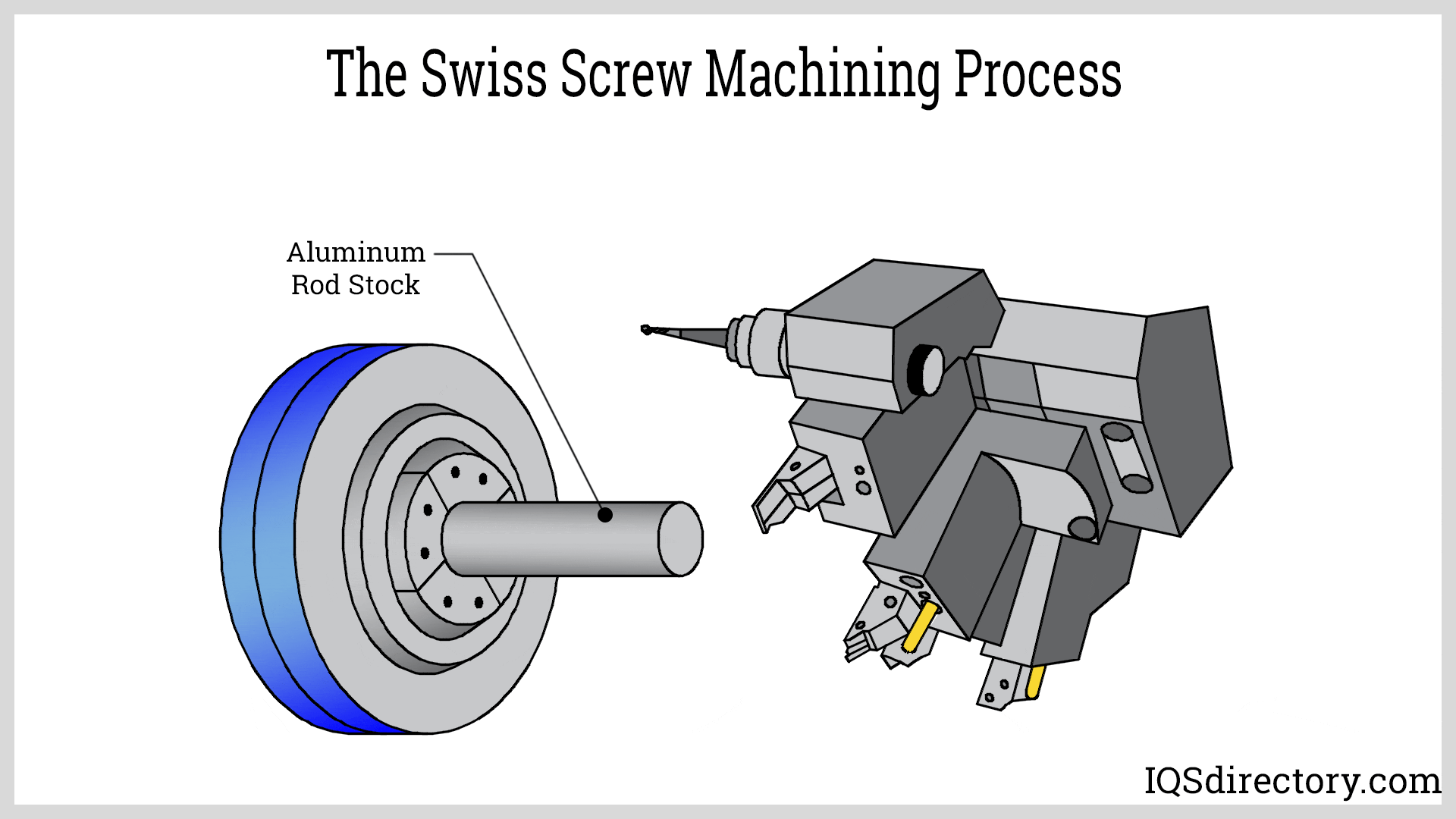
Swiss screw machining is a process for producing high precision parts in high volume using an automatic lathe that is programmed to perform every aspect of the cutting process. The method used for...
Please fill out the following form to submit a Request for Quote to any of the following companies listed on
This article will take an in-depth look at screw machined parts and products.
The article will bring more detail on topics such as:
This chapter delves into the world of screw machined parts and products, discussing their definitions and the range of machining techniques employed in their creation.
Screw machined parts are detailed components, generally cylindrical and threaded, crafted with specialized machinery. These parts are produced using automatic lathes for small to medium-sized items. Commonly manufactured with screw machines are items like screws, bolts, pins, fittings, bushings, rivets, fasteners, and studs. These components play a vital role in manufacturing numerous products and are extensively utilized in construction and maintenance sectors.
A screw machine is a specialized, automated lathe for rapidly producing parts. These machines often boast multiple spindles, frequently a six-spindle configuration, allowing simultaneous processing of identical materials for efficient high-volume production. Screw machines work with diverse materials, including aluminum, plastic, wood, brass, and steel, producing various screw machine parts.
Screw machine products are significant to the automotive, agricultural, medical, electronic, and leisure industries. Multi-spindle screw machines, using several spindles, manufacture products with accurate tolerances, promoting quicker and more economical production, saving resources for manufacturers and reducing consumer costs.
Screw machine shops enhance efficiency by equipping staff with essential tools for precision screw machining. Depending on client demands, they select suitable designs, materials, and machining options for each item. Screw machines, whether single or multi-spindle, process bars up to 12 feet long, shaped in square, round, or hexagonal forms, often resembling the old Civil War-era Gatling guns in their setup.
Automated tools, including those for drilling, cutting, notching, and knurling, shape rotating stock into desired parts by making contact with the bar stock. These tools, integrated into the screw machine, drill, trim excess material, and smooth the stock. Manufacturers typically arrange these tools in stations along various axes, such as turret, horizontal, and vertical slides. Different screw machines execute multiple processes including, but not limited to:
Knurling is a method to add a textured pattern to metal surfaces, enhancing their grip. Specialized knurling tools are used to create distinct patterns. Typical knurled items include tool handles, metal flashlights, knurled nuts, and knobs—benefiting from superior grip. Knurling is widely applied across industries like electronics, automotive, construction, aerospace, telecommunications, fitness equipment, and maritime sectors. Performed on a lathe using automatic-feed mechanisms, it allows companies to serve extensive markets with precise efficiency.
Knurling tools, paired with a lathe, emboss patterns on materials, crafting three-dimensional designs. Four main knurl patterns exist: diamond, straight, angular, and circular rings. These can be used alone or combined for specific effects. Annular rings, for instance, are favored when working with plastic parts to boost grip and functionality.
While annular rings ease part coupling, they also complicate separation due to the ridges. Straight knurl patterns, composed of numerous parallel ridges, offer another design choice. Alternatively, turning straight ridges into helical grooves creates a helical knurl pattern.
Angular knurling, featuring single-direction angled ridges, enhances external handle traction. Among knurling patterns, diamond knurling is preferred for hand grips, offering maximum traction with ridges in a cross-hatch design, optimizing grip.
Screw heads are crafted using pressure application techniques with a die. Methods like thread rolling form metals cold, demanding workpieces with some ductility—metals must compress at low temperatures.
Thread formation in screw heads is often opted for lathes over screw machines due to time efficiency. Thread rolling uses hardened dies to create threads without material removal, promoting efficient production.
This method strengthens screws and other threaded parts. Preferred by manufacturers for producing robust components with consistent, accurate threads, the process uses two main die types: flat and cylindrical. Flat dies, rectangular with simple contours, are common for woodscrews and machined screws, while cylindrical dies come in two-feed and three-feed varieties. Two-feed dies fit large screws, while three-feed dies are typical for spark plugs and tube fittings.
Thread rolling offers benefits such as increased product strength and dimensional accuracy. However, limitations include the use of softer metals due to metal deformation and elevated tooling costs. The dies require durability and precision, and achieving the necessary hardness can be challenging. Die deformation can affect thread accuracy.
Turning involves a cutting tool, generally non-rotary, moving linearly as the workpiece spins, forming a helical toolpath. This process, typically employed for shaping external surfaces, is known as "turning," whereas for internal surfaces, it is termed "boring."
Lathing encompasses both "turning and boring." "Facing" cuts the workpiece faces using similar tools, falling within both categories.
Turning can be conducted manually on a traditional lathe, requiring constant operator presence, or on an automated lathe with minimal supervision. Modern lathes commonly employ computer numerical control (CNC).
During turning, for precise diameters and depths, the workpiece—be it wood, plastic, metal, or stone—spins while the cutting tool moves in multiple motion axes. This cutting action, including drilling, performed on workpiece interiors or exteriors, creates tubular parts with varied geometries.
This rotational machining allows manufacturers to perform diverse operations, such as drilling, slotting, knurling, threading, and milling, on a component.
Hard turning: This specialized turning is for materials with a Rockwell C hardness above 45, typically after heat treatment to reduce or replace grinding needs. Though hard turning competes with rough grinding in stock removal, grinding is commonly chosen for final operations demanding exact shapes and dimensions.
Tapered turning: Creating a form where diameter diminishes, producing a cone shape, is tapered turning.
Grooving: Involves a single-point turning tool cutting equally-wide grooves into a workpiece’s side as it progresses radially, with wider grooves made through multiple passes or form tools for varied geometries.
Parting: Mimicking the grooving tool's operation, a cut-off tool advances radially into the workpiece, eventually reaching the center to cut off a section.
Screw machining not only shapes metal items but also refines surface finishes, achieving either knurled or polished finishes through turning. For secondary operations often replacing manual tasks, a twin spindle CNC Swiss screw machine might engage its second spindle.
Rotary broaching, distinct from traditional broaching, achieves desired internal shapes in a single corner-cutting pass, unlike the successive shape increases in conventional methods. Effective on horizontally or vertically spindle-equipped machines like lathes and mills, it often negates further operations.
Rotary broaching quickly and accurately forms internal polygonal shapes, achieving at least 0.0005-inch precision within seconds. Praised for efficiency and precision, it thrives in plumbing, automotive, aerospace, and medical industries.
The method’s success hinges on the broach’s 1-inch angle to the workpiece’s midline, and the broach tool-held live spindle's free rotation, driven by engagement with a lathe's rotating workpiece. As the broach penetrates the material, it cuts with a scalloping or chiseling effect.
This chapter provides an in-depth overview of the various types of screw machined parts and products, exploring the precision manufacturing processes involved in their production and their extensive industrial applications. By understanding the full spectrum of capabilities and advantages offered by screw machining, you can make informed decisions when specifying, sourcing, or purchasing custom machined components for your projects.
Manufacturers of screw machined products utilize advanced CNC screw machines and Swiss machining technology to create high-precision components for clients across a wide array of mission-critical and specialized sectors. These industries include home appliances, industrial construction, general and precision manufacturing, automotive, aerospace, medical device manufacturing, electronics and semiconductor production, laboratories, military and defense, telecommunications, and the fast-growing healthcare and life sciences markets.
The results of screw machining are commonly referred to as precision-turned parts, custom fasteners, CNC-turned components, or screw machine parts. Screw machining is responsible for the production of a diverse selection of critical parts and assemblies, including but not limited to button machine screws, hex machine screws, pan head screws, truss machine screws, cap screws, set screws, shoulder screws, dowel pins, bushings, custom spacers, and many other specialty fasteners and engineered metal parts. High-tolerance military, aerospace, and defense components—such as firearm accessories, mounting hardware, and flight control components—depend heavily on reliable screw machined parts. In addition, screw machining encompasses the precise fabrication of complex items such as metal knobs, bio-implants, miniature surgical instruments, tire gauges, threaded rods, splines, keyways, and specialized spindles, each produced to exacting specifications for demanding environments.
Two core methods in modern screw machining are traditional CNC lathes and Swiss CNC lathes. Unlike standard CNC lathes, Swiss lathes can move along the third Z-axis, enabling the manufacture of ultra-precise, elongated, or concentric parts with intricate and tight tolerances. Swiss screw machining provides outstanding dimensional accuracy and is favored for making small, complex parts in industries such as medical device manufacturing, aerospace, dental implants, watchmaking, and precision electronics. The increased control and flexibility of Swiss-type automatic lathes empower engineers and product designers to specify components with detailed geometries and micro-features that are simply not possible with conventional machining methods.
The versatility of screw machine tooling processes extends well beyond traditional fasteners. Screw machined parts are integral to the design and function of a huge variety of products, including precision medical instruments, automotive assemblies, laboratory testing equipment, consumer and industrial electronics, IT network infrastructure, appliance components, sensors, instrumentation, and military-grade hardware. Swiss screw machines and automated turning centers are capable of processing an array of materials, from common and exotic metals like stainless steel, titanium, aluminum, and brass, to high-performance engineering plastics such as PEEK, Delrin, and nylon. This adaptability makes screw machining indispensable for manufacturers seeking high-precision, custom-engineered components for innovative applications.
Importantly, screw machines aren’t just for producing industry-standard screws—they deliver a vast array of parts and custom metal products using cost-effective, repeatable mechanical and CNC operations. Examples of screw machined products include custom and conventional bio-implants, intricate fittings, surgical pins, miniaturized medical devices, metal knobs, precision-engineered fasteners, spindles, splines, keyways, threaded rods, tire pressure gauges, and other high-tolerance machined parts. Reputable automatic screw machining services can provide the following parts to meet your unique specifications:
For procurement professionals, engineers, and product managers, working with an experienced screw machining supplier ensures access to high-quality, ISO-certified components that meet strict regulatory and safety standards for your specific industry.
High precision screw machined products are engineered to extremely tight tolerances—a necessity for industries requiring unwavering part consistency and reliability in high-volume production runs. State-of-the-art quality assurance measures, including automated optical inspection and statistical process controls, are commonly employed to guarantee that each part conforms to exact engineering specifications. The use of high-grade alloys and advanced production controls delivers components ideally suited for critical functions in medical devices, aerospace assemblies, and semiconductor manufacturing where failure is not an option.
Medical screw machined products are vital for the healthcare and scientific sectors, demanding flawless quality and biocompatibility. Applications include precision dental implants, orthopedic bone screws, pedicle and spinal implants, cardiac pacemaker housings, surgical tool components, and micro-miniature device elements. All medical-grade parts are manufactured according to stringent regulatory requirements such as ISO 13485, with full traceability, validation, and sterilization compatibility to ensure patient safety and effective clinical use.
Stainless steel screw machined components are the cornerstone of industrial and commercial engineering, prized for their superior resistance to corrosion, oxidation, and chemical exposure. These parts perform reliably in demanding environments such as marine applications, chemical processing plants, food and beverage production, and outdoor electronic housings. The inherent strength and durability of stainless steel, combined with its hygienic properties, make it the alloy of choice for critical applications where long-term performance and regulatory compliance are paramount.
Screw machined parts are available in countless styles, configurations, and head designs to match an extensive range of application requirements. Machined screws are customized with various driver heads for efficient use and reliable torque transfer. Common options include Phillips® heads (cross-shaped for compatibility with Phillips screwdrivers), slotted heads (single flat groove for use with flathead drivers), hex socket heads (for use with Allen wrenches and hex keys), and Torx™ heads (six-pointed star pattern for improved grip and security). Specialty security screws, tamper-proof designs, and custom drive profiles are often used in high-security settings, electronics, and public infrastructure to prevent unauthorized removal.
The manufacturing processes employed to create screw machined parts are tailored to optimize strength, surface finish, and geometric accuracy. Methods include subtractive machining such as turning, milling, and drilling, die-cutting for forming threads and grooves, and thread rolling to produce robust, fatigue-resistant threads. To ensure the best possible result, it is crucial to supply detailed blueprints, CAD drawings, and quality standards to your chosen precision screw machining service provider. Clear communication of your requirements guarantees parts that fit, function, and perform to the highest standards in your assembly or product.
User considerations when specifying precision screw machine parts include selection of proper thread size and pitch, tolerance requirements, material compatibility, environmental resistance, and compliance with industry certifications (such as RoHS, REACH, or FDA). Options such as recessed, countersunk, flanged, captive, and shoulder-style machine screws are available in both imperial (inch) and metric (mm) systems, offering versatility for designers integrating these components into global platforms and products.
Screw machines are engineered to process a comprehensive selection of metallurgical and polymer materials, each offering unique benefits in mechanical properties, machinability, and end-use performance. Among the most popular screw machining materials are the following:
Aluminum: Lightweight, corrosion-resistant, and highly ductile, aluminum and its alloys (such as 6061 and 7075) are favored for their ease of machining and excellent strength-to-weight ratio. Aerospace, automotive, consumer electronics, and transportation sectors rely on aluminum screw machined parts for applications where both weight reduction and strength are crucial. Anodizing further enhances aluminum’s surface hardness and corrosion resistance.
Brass: An alloy of copper and zinc, brass is celebrated for its low friction coefficient, excellent machinability, smooth surface finish, and natural antibacterial properties. Brass screw machine products—such as nuts, inserts, washers, connectors, and decorative hardware—are widely used in plumbing, instrumentation, custom architectural components, and aesthetic product design due to their attractive gold-like appearance and overall durability.
Steel and Stainless Steel: Steel alloys (primarily iron and carbon) are prevalent in the production of structural and load-bearing screw machined parts because of their high tensile and yield strength. Stainless steel, containing at least 10.5% chromium by mass, is the material of choice for harsh and sanitary environments, delivering outstanding corrosion resistance, easy cleanability, and long service life. Both are essential in construction, manufacturing, medical equipment, and consumer goods.
Titanium: Symbolized as Ti, titanium is a high-performance transition metal chosen for its impressive strength-to-weight ratio, very high corrosion resistance (including to seawater and chemicals), and biocompatibility. Titanium screw machined components find extensive use in aerospace, orthopedics, dental implants, surgical tools, and high-end racing and sports equipment, where low weight and absolute reliability are mandatory.
Engineering Plastics: In addition to metals, advanced polymers such as PEEK, Delrin (acetal), nylon, and PTFE are also processed on Swiss and CNC screw machines. These plastics are used in medical components, food-grade parts, electronics insulation, and lightweight mechanical assemblies where metal alternatives may be inappropriate due to weight, magnetism, or sterilization constraints.
Secondary operations encompass a range of post-machining processes essential for enhancing the performance, surface finish, appearance, and longevity of screw machined parts. While the primary machining stage—whether via CNC or mechanical screw machining—shapes the base geometry, secondary operations deliver the critical finishing touches and functional improvements demanded by modern industries. These processes add value, enabling manufacturers to achieve precise dimensional tolerances, specialized properties, and compliance with customer specifications.
After initial machining, components may undergo various finishing, testing, and quality assurance steps to meet the desired surface characteristics and performance standards. Secondary operations, such as the ones listed below, help tailor parts to unique application requirements and end-use conditions:
Plating: This advanced surface finishing technique involves depositing a thin, protective metal layer on the substrate. Common plating metals include copper, silver, nickel, gold, tin, and chromium. Plating serves to enhance aspects such as conductivity, corrosion resistance, solderability, and aesthetic appeal—crucial qualities for connector pins, electronic contacts, and decorative hardware. Specialized types of plating used across industries:
Electroplating—Through the electroplating process, ionic metal in solution is reduced onto the substrate via an electric current, resulting in a durable, non-ionic metal coating. Used extensively in electronics, precision bearings, and the automotive industry.
Electroless plating—Achieves uniform coatings without electricity via chemical reduction in an aqueous solution, often employed for nickel plating on complex geometries and hard-to-reach surfaces.
Grinding: Utilized to achieve ultra-smooth surface finishes and tight dimensional tolerances, grinding removes minute imperfections and sharpens cutting tools to exacting standards. Precision thread grinding and cylindrical grinding are critical in manufacturing threaded parts, lead screws, gears, and precision shafts.
Hard materials and tooling are brought to precise dimensions in multiple grinding stages, often beginning with rough grinding and followed by fine or finish grinding to reach the targeted particle size and surface condition. As needed, dry or wet grinding methods are selected based on material type and desired outcome, with pre-drying steps for moisture-sensitive workpieces.
Heat Treating: Applied to both ferrous and non-ferrous metals, heat treatment is a vital metallurgical process for optimizing physical properties such as strength, hardness, ductility, and resistance to fatigue. Controlled heating and cooling cycles allow manufacturers to achieve desired performance characteristics for demanding mechanical or structural use.
Modern heat treating facilities leverage computer-controlled ovens and custom process schedules for full traceability, ensuring compliance with aerospace, automotive, and medical device standards.
Partnering with a top screw machining manufacturer gives you access to these value-added secondary operations, allowing seamless one-stop production from raw material selection and high-precision CNC turning through to customized finishing, assembly, and logistics support. This ensures you receive fully compliant, ready-to-use screw machined parts tailored to your manufacturing and assembly line requirements.
Screw machines are highly specialized, automated metalworking lathes designed to efficiently manufacture high-precision components. By definition, lathes are industrial machines that rotate a workpiece about an axis to shape, cut, or drill it to specification. While both traditional lathes and screw machines are utilized to produce screw-machined products, screw machines—especially when equipped with advanced technology like multi-spindle configurations and computerized controls—dramatically increase productivity and accuracy. Their ability to automate complex turning and threading operations makes them an optimal choice for high-volume and high-precision production in the fields of medical device manufacturing, aerospace, electronics, automotive, and industrial equipment. As demand grows for tighter tolerances and shorter lead times, screw machining solutions play an essential role in modern manufacturing environments.
CNC screw machines feature multiple spindles and advanced software controls, allowing manufacturers to produce numerous identical parts simultaneously—often up to six pieces at once. This multi-spindle capability is invaluable for precision machining, enabling mass production of complex, intricately machined parts with remarkable speed and repeatability. Industries leveraging CNC screw machining benefit from reduced cycle times and exceptional accuracy, using CNC turning centers and live tooling to achieve complex geometries, threading, knurling, and drilling in a single setup. With computer numerical control, these machines streamline prototyping and full-scale production, offering rapid changeover between part specifications for diverse high-volume applications in sectors such as medical, aerospace, and automotive manufacturing.
CNC lathes can perform precision machining and turning functions, processing up to six pieces at once in optimal conditions. Compared to CNC screw machines, however, they generally offer fewer spindles and are not purpose-built for the highest volume screw machining jobs. As a result, CNC lathes are better suited for flexible manufacturing and lower production runs where part complexity is required but overall quantities are moderate. When choosing between CNC lathes and screw machines, manufacturers consider variables such as spindle capacity, part geometry, cycle time, and operational costs. Additionally, there are several important types of screw machines in the industry, including mechanical screw machines, multi-spindle CNC screw machines, Swiss-type screw machines, and roll thread machines. Mechanical screw machines are legacy systems prized for their robust, non-CNC mechanisms and suitability for mass-producing simple, precision parts. Multi-spindle CNC screw machines enhance throughput for repetitive high-precision production. Swiss-type lathes and roll machines further expand the versatility of screw machining, each excelling in unique manufacturing scenarios such as medical device components and threaded fasteners.
Mechanical screw machines utilize robust cam-driven automation and feature two front camshafts, an integrated motor, and eight or more synchronized spindles. Metal bar stock is securely clamped by spring collets, which allows for highly repeatable, precise machining of components such as fittings, bushings, fasteners, and shafts. Power from the main drive shaft synchronizes every aspect of the machine, efficiently coordinating the bed lead work shaft and camshafts. This classic setup enables continuous operation for the high-speed production of small, precision-machined components, particularly in industries demanding cost-effective, large-scale part manufacturing.
Multi-spindle CNC screw machines integrate the reliability of mechanical automation with cutting-edge CNC programming and CAD modeling. These advanced machines excel at high-volume, multi-axis machining, allowing simultaneous operation on several workpieces and maximizing throughput. Although the initial setup, including detailed part programming and system configuration, can be intensive, multi-spindle CNC machines offer significant long-term cost savings and productivity gains for extended production runs. Their precision, speed, and automation are especially invaluable in automotive, aerospace, and electronics sectors that demand scalable production of precise, repeatable components such as connectors, medical implant parts, and custom fasteners.
Swiss screw machines, also known as Swiss automatic lathes or Swiss turning centers, originated in Switzerland to fulfill the demand for precise watch components. Modern Swiss-style screw machines are now widely adopted for producing complex, miniature components with exacting tolerances, making them an industry standard in sectors such as medical, electronics, aerospace, and micro-manufacturing. Their hallmark is the ability to produce long, slender, and intricate parts efficiently and with remarkable dimensional stability.
These machines hold bar stock firmly in a rotating collet and feed it through a guide bushing, limiting deflection and enhancing precision. The unique engineering of Swiss-type machines enables simultaneous movement of both workpiece and multiple cutting tools, facilitating expertly controlled operations such as micro-turning, cross-drilling, grooving, and milling. This allows for rapid, single-pass completion of intricate parts that demand true concentricity and fine surface finishes—benefiting industries focused on medical implants, dental hardware, and precision instrumentation.
Unlike traditional lathes, which move the tool across stationary bar stock, Swiss screw machines maneuver the workpiece in a five-axis system (X, Y, Z, A, B axes) to achieve ultra-tight tolerances. This multi-axis versatility enables machining of highly complex components—such as bone screws, electronic contacts, and intricate sensor housings—without multiple setups. Additionally, the use of disc cams and integrated guide bushings gives Swiss screw machines an edge for producing long, thin, and challenging geometries while minimizing material waste and secondary operations.
Swiss screw machines utilize headstocks that dynamically reposition the workpiece and sophisticated slide mechanisms for fully automated machining cycles. With closed spindle collets, these machines efficiently manage debris, maintaining a pristine environment for high-precision cutting. The advancement of CNC Swiss screw machines, also referred to as CNC Swiss lathes or CNC turning machines, further elevates performance, combining rapid RPM operation (up to 10,000+ revolutions per minute), exceptional repeatability (precision ranges from 0.0002 to 0.0005 inches), and seamless automation of tool changes. Modern CNC Swiss screw machines execute multi-operation cycles—milling, drilling, threading, and finishing—in a single run, accelerating lead times while ensuring stringent quality standards.
CNC Swiss lathes are especially cost-effective in high-production runs where minimized labor costs, reduced setup times, and reliable, unmanned operation are key. The modern designs often include advanced live tooling stations, integrated bar feeders, and programmable tool offsets, supporting rapid production changeovers. The superior surface finishes achieved often eliminate the need for post-processing like grinding or polishing, saving both time and operational expense.
The optimized spacing, modularity, and tooling density of modern Swiss screw machines further enhances their adaptability for diverse project requirements, including rapid prototyping, contract manufacturing, and complex medical device production. In summary, Swiss-type lathes, and especially CNC Swiss machines, are unrivaled for projects requiring micro-machining, superior quality, and efficient, unattended high-volume manufacturing.
Thread rolling machines serve a crucial function in modern screw machining operations—they produce high-strength, rolled threads by plastically deforming material, as opposed to conventional cutting. Using advanced thread rolling dies, these machines create both external and internal screw threads with exceptional speed and uniformity, making them ideal for high-volume runs of fasteners, bolts, and threaded rods. Thread rolling not only improves the finished thread’s strength and fatigue resistance but also ensures superior surface finish and dimensional repeatability. Manufacturers increasingly turn to thread rolling machines in automotive, aerospace, energy, and construction applications, where reliability and high output are paramount. This process produces consistent, defect-free threads that comply with strict industry standards for fastener performance and durability.
Turret machines, while not as precise as Swiss-type screw machines due to differences in tool-to-workpiece alignment, offer tremendous flexibility and power. These machines are equipped with robust live tool stations, larger tool shank capacities, and superior rigid construction, making them ideal for heavy-duty machining and secondary operations on larger components. Turret-style lathes are often chosen for their ability to automatically transfer parts, thereby supporting efficient workflow and accommodating larger workpieces that would exceed the capabilities of Swiss-type lathes. Their adaptability and endurance make them a staple in job shops and general-purpose machine shops focused on custom or medium-batch runs.
Turret-style screw machines provide greater tool variety and allow for the installation of numerous cutting tools on a single machine, making them highly versatile. However, Swiss-style screw machines—particularly CNC models—excel in automated, multi-axis high-precision machining, effectively minimizing operator intervention and maximizing throughput for complex, small, and intricate components. The CNC controller on a Swiss machine leverages real-time data and adaptive tooling adjustments, ensuring superior process control and output quality over traditional turret lathes. For industries where micron-level tolerances and high repeatability are mission-critical, such as medical device, electronics, and watchmaking sectors, CNC Swiss screw machines deliver clear advantages in accuracy and efficiency.
Cam-driven screw machines use a series of engineered cams and mechanical linkages to automate the movement of cutting tools, delivering rapid, repeatable, and highly accurate production of small components. Synchronized by a drum cam system, these machines precisely coordinate each cycle—indexing the headstock and actuating the cam bank to control the various spindle operations. The result is reliable, cost-effective, and efficient screw machining, ideal for producing high volumes of simple, precision-machined parts such as spacers, washers, nuts, and pins.
Each cam is carefully designed to manage the speed, depth, and force of cutting tools for specific operations. This mechanically driven automation regulates every segment of the screw machining process, ensuring tight tolerances and consistent quality. The high-speed, synchronized operation of cam-driven screw machines makes them a go-to choice where accuracy, repeatability, and affordability are required, even as CNC-driven alternatives rise in popularity.
Despite the rapid evolution of automated CNC technologies, cam-driven screw machines remain indispensable in many manufacturing settings because of their lower capital investment, ease of maintenance, and simple operation. They continue to provide an efficient solution for long production runs, offering economical machining where part complexity and customization are moderate but cycle times are critical.
Since their introduction during the industrial revolution, cam-driven screw machines have held a strong presence in the manufacture of precision small parts used in automotive, aerospace, electronics, and consumer products. Their robust performance and ability to deliver consistent, high-quality parts reinforce their ongoing relevance in today’s competitive manufacturing landscape.
This chapter will explore the diverse applications and advantages of screw machined parts and products. We will delve into how these precision-engineered components are utilized across various industries, highlighting their critical roles in sectors such as automotive, aerospace, electronics, and medical fields. Additionally, the discussion will cover the benefits of screw machining, including enhanced accuracy, efficiency, and the ability to produce complex and intricate parts to tight tolerances. By understanding these aspects, readers will gain insight into the significance and versatility of screw machined products in modern manufacturing.
Screw machined products, also known as turned components, are frequently parts with tight tolerances and are used in a variety of delicate and important applications, including:
Due to a variety of considerations, screw machining is regarded as one of the most efficient and affordable methods for manufacturing small rotary parts. The efficiency of CNC machining and turning equipment is well-established, with the capability to produce high-quality components quickly and cost-effectively. For instance, some CNC screw machines can handle up to six components simultaneously, significantly increasing production efficiency. Additionally, the tooling area of these machines can accommodate up to 20 different tools, allowing for complex operations and reducing the need for frequent tool changes. This high level of automation and versatility contributes to the overall cost-effectiveness and precision of screw machining, making it a preferred choice for producing intricate and high-tolerance parts in various industries.
Screw machines excel at producing multiple components simultaneously, leading to high production rates and significantly reduced cycle times. This efficiency not only shortens production times but also ensures that parts are highly uniform. By utilizing several screw machines, manufacturers can minimize labor costs associated with large workforces, as a single operator can manage multiple machines and oversee secondary tasks. Swiss screw machining, in particular, offers substantial cost savings for bulk production of high-quality metal parts, making it a crucial technology for industries where precision and efficiency are paramount.
No other production process matches the cost-effectiveness and structural advantages offered by screw machining. The precision achieved with screw machining is unparalleled compared to many other metal forming and manufacturing techniques. This high level of accuracy makes precision turning and machining essential for producing components where exact tolerances are critical, such as customized fasteners. Consequently, screw machining remains a preferred method for crafting parts that require meticulous detail and reliability in various applications.
However, for items such as tiny precision tools used in critical medical applications, screw machining remains the only practical manufacturing method. While some types of metal stamping can achieve tolerances comparable to screw-machined products, screw machining does have its drawbacks. One notable disadvantage is the setup time required before machine operation can commence. This setup period can be considerable, potentially affecting overall production efficiency.
Multi-spindle CNC screw machines involve a labor-intensive setup process that includes part design, system programming, and CAD design, which can sometimes take one to two hours for a Swiss machine. This setup time can be a drawback, making extended production runs more economical. Despite this, even short-run screw machines offer a relatively cost-effective method for precision production since they don’t require custom dies or hardware. Another disadvantage of screw machining is the significant production of scrap, with each bar potentially generating up to a foot of waste material.
Screw machines, first introduced during the first industrial revolution, are often considered older technology. The latest versions of these machines, despite advancements, still require a manual setup process that can take between six to nine hours. Once set up, however, they are capable of producing between 200 to 400 parts per hour, demonstrating their efficiency in high-volume production.
If you're considering purchasing highly-customized screw machined parts, working with a reliable manufacturer is crucial. It’s advisable to invest the time and resources needed to select a supplier with the expertise and transparency to create a tailored solution for your specific needs. When evaluating screw machining suppliers, several factors should be considered: the quality and source of the materials used, the extent of product customization available, the supplier's reputation for turnaround times, and their ability to meet delivery schedules to ensure your business deadlines are met.
Similar considerations apply when evaluating your own operations as a manufacturer or provider of screw machining services. Flexibility is a crucial, yet often undervalued, quality in equipment investment. The ability to adapt to varying production needs, handle diverse materials, and accommodate different part designs can significantly impact your operational efficiency and ability to meet customer demands.
Investing in advanced machinery, such as CNC machines with versatile tooling options, is recommended for staying adaptable to future developments in Swiss screw machining. This proactive approach contrasts with a more conservative strategy that depends on consistent high production runs and is less flexible in accommodating changes. Generally, turret screw machines offer less accuracy compared to Swiss screw machines, while CNC Swiss screw machines provide superior speed and precision over automated Swiss screw machines. Investing in state-of-the-art CNC technology can help ensure that your operations remain competitive and adaptable to evolving industry demands.
A screw machined product refers to a range of automatic lathes designed for producing small to medium-sized components. These screw machined parts are typically cylindrical and threaded, encompassing items such as screws, bolts, pins, fittings, bushings, rivets, fasteners, and studs. Various types of screw machinery include Swiss-type screw machines, roll machines, mechanical screw machines, multi-spindle CNC screw machines, and CNC lathes. These turned components, or screw machine items, are known for their tight tolerances and are utilized in a range of delicate and critical applications, such as laboratory equipment, automotive tools, and military parts.
Swiss screw machining is a process for producing high precision parts in high volume using an automatic lathe that is programmed to perform every aspect of the cutting process. The method used for...
Thread rolling is a type of threading process which involves deforming a metal stock by rolling it through dies. This process forms external threads along the surface of the metal stock...
The normal functioning of CNC machines is done along the three Z, X, and Y axes. The five axes machines have two more axes accessible, which are namely A and B. The addition of the two extra axes makes it easy to cut complex and intricate parts...
CNC machining is an electromechanical process that manipulates tools around three to five axes, with high precision and accuracy, cutting away excess material to produce parts and components. The initial designs to be machined by CNC machining are created in CAD...
The CNC process was developed in the 1950‘s and took a leap forward in the 1980‘s with the addition of computerization. Unlike other production processes, CNC begins with a rendering by a computer, which creates a two or three dimensional representation of the part to be produced...
Contract manufacturing is a business model in which a company hires a contract manufacturer to produce its products or components of its products. It is a strategic action widely adopted by companies to save extensive resources and...
EDM machining is a contemporary machining method based on the removal of material from a part using thermal energy. The material is removed by local melting or vaporizing small areas on the surface of the part being machined...
G-code is the name of a plain text language that is used to guide and direct CNC machines. For most modern CNC machines, it isn‘t necessary to know the meaning of G-codes since CAD and CAM software is translated into G or M codes to instruct a CNC machine on how to complete a process...
Computer numerical control (CNC) is a fundamental part of modern manufacturing. The majority of machines operate using instructions and guidelines that have been downloaded using a CNC program controller...
Sinker Electrical Discharge Machining (EDM) is a metal machining process used to create molds, dies, and parts using electrical sparks to erode material from a workpiece. It is preferred over other machining processes due to...
A method of precision machining called electrical discharge machining (EDM) removes material from a workpiece using thermal energy rather than mechanical force. A thin, single-strand metal wire and deionized water used to...
Machining is a manufacturing process used to produce products, parts, and designs by removing layers from a workpiece. There are several types of machining that include the use of a power driven set of machining tools to chip, cut, and grind to alter a workpiece to meet specific requirements...
The CNC process, computer numerical control, is a method of manufacturing where programmed software directs the operation of factory tools and machinery. It is designed to manage a wide range of complex machines from grinders and lathes to mills and routers...