Canopies
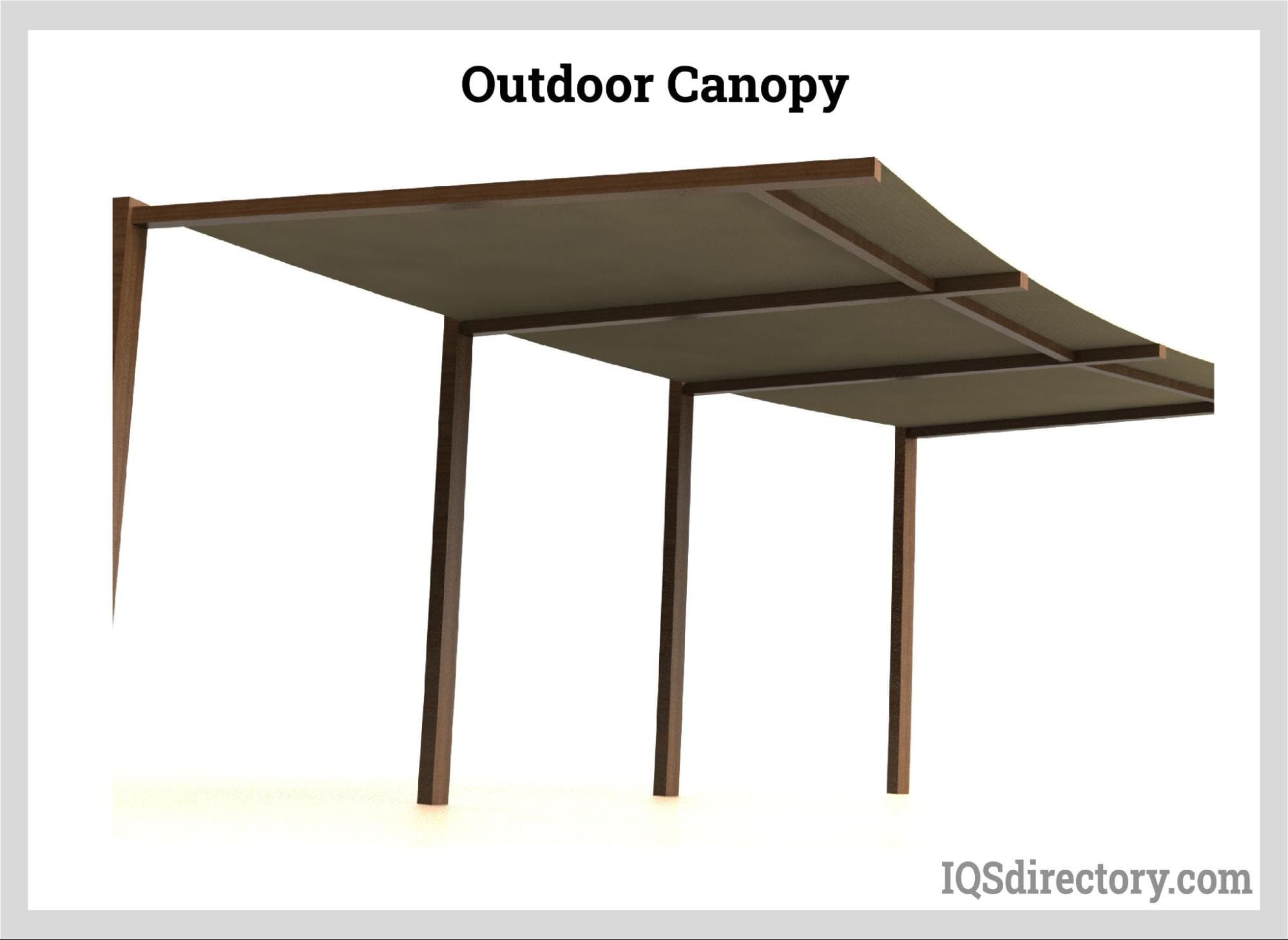
A canopy is a structure with a connected fabric or metal covering that can give shade or shelter from weather elements such as the sun, hail, snow, and rain. For example, a tent with no floor can be...
Please fill out the following form to submit a Request for Quote to any of the following companies listed on
This article contains information and an explanation of the cut and sew process.
You will learn more about topics such as:
The cut and sew method is a production technique used to create a wide array of fabric products, ranging from dust covers and tents to guitar cases and foam cushions. The sheer variety of items that can be produced using this technique underscores the importance of the cut and sew industry in manufacturing and advancing fabric goods.
The procedure begins with a pattern printed onto fabric, which becomes the basis for assembling the final product. Ensuring that the pattern is accurately cut to adhere to specific design and color standards is crucial. Cut and sew involves a highly detailed process that guarantees the precision and superior quality of fabric items. Each piece is fashioned with painstaking detail and is thoroughly inspected to meet the expectations of clients, designers, and manufacturers alike.
This production model boosts creativity by permitting direct printing on raw fabric, thus avoiding the limitations that seams and predefined sizes generally impose. Moreover, this method allows for a vast spectrum of colors since it circumvents the need for pre-stocked colored materials.
The versatility of cut and sew makes it applicable across a multitude of products, as nearly every industry requires fabric components within their production operations. Despite its widespread application, the contribution of the cut and sew industry to the enhancement of product quality and success often remains underappreciated.
Focused on delivering thousands of premium quality products at competitive rates, the cut and sew industry empowers its clients to attain profitability and success. Indeed, cut and sew remains at the heart of fabric-based product creation.
Cut and sew manufacturing is a specialized apparel production process that brings custom clothing designs to life by transforming creative concepts into finished products. The cut and sew method is favored by designers and apparel brands seeking flexibility, quality, and the ability to produce unique, small-batch or private label garments. Through collaboration with experienced cut and sew suppliers, individuals and businesses can receive expert support on everything from fabric sourcing and garment construction to technical pattern creation and sample development. Whether you’re launching a new fashion line or introducing innovative custom apparel, professional cut and sew contractors are essential partners for navigating clothing manufacturing from design through production.
While the process of custom cut and sew manufacturing is accessible to anyone interested in mass-producing apparel or soft goods, reputable apparel manufacturers typically maintain a thorough vetting system to ensure project feasibility. This screening protects resources and ensures only viable designs move forward. Although fashion garments—including streetwear, activewear, hoodies, outerwear, and designer dresses—are the most commonly requested products, cut and sew production is remarkably versatile. The process can also be applied to a wide range of textile products, such as home furnishings, accessories, or promotional items.
Popular cut and sew manufactured items include hoodies, sweatshirts, custom t-shirts, fashion-forward jackets, bespoke dresses, leggings, uniforms, and sportswear. The methodology extends beyond apparel to include products such as textile wall art, curtains, decorative rugs, soft toys like teddy bears, tote bags, and even custom upholstery. Essentially, any product made from cut fabric panels can be expertly crafted with cut and sew production services tailored to industry specifications.
The first step in cut and sew manufacturing is digital pattern design, which forms the blueprint for apparel production. Pattern making is performed using advanced software such as Adobe Photoshop, Illustrator, and Computer-Aided Design (CAD) programs—industry standards for both digital and print pattern creation. Many cut and sew designers begin with hand-drawn sketches or patterns, which are then scanned into a computer at a high resolution (typically 300 dpi or above) for precise digital manipulation. Using bold, dark lines enhances the clarity and editability of original designs.
Once imported, the scanned image is saved in a file format compatible with professional design software. The designer then rasterizes the layers, allowing for targeted edits, vector tracing, and easy color modifications. This meticulous process ensures every detail of the pattern aligns with the desired fit, construction, and style, while maximizing print clarity and fabric utilization.
During this stage, individual design elements are separated from the background and layered for detailed color editing and arrangement. Key motifs or graphics are repositioned at design edges to keep repeat patterns seamless—a critical step for all-over print garments and textile applications. Designers also refine patterns for scale, colorway, and placement, ensuring both creative vision and technical feasibility are maintained throughout the apparel prototype and sampling phase.
The final pattern is examined for print repeatability and adjusted to the correct size for garment construction and fabric printing. Before moving forward to sampling, pattern files are thoroughly reviewed against tech pack specifications to ensure alignment with fit, grading, and production requirements. This attention to detail allows clothing brands and designers to confidently move to the next stage in cut and sew manufacturing.
These essential steps result in a production-ready file that can be transferred directly onto fabric through various advanced textile printing methods. Whether for limited runs or large-scale cut and sew clothing lines, efficient pattern development is the foundation for high-quality, custom apparel manufacturing.
Once your design and technical pattern are finalized and approved, the next step is to select an experienced cut and sew manufacturer to bring your product to market. Choosing the right apparel manufacturer is critical for ensuring high quality, cost efficiency, and timely delivery. Reputable cut and sew facilities—whether boutique shops, contract sewing companies, or full-service production houses—have the skilled workforce and infrastructure to scale garment manufacturing to your brand’s needs.
Leading cut and sew partners focus on apparel production by digitally placing approved patterns onto fabric, skillfully cutting textiles, and assembling garments according to detailed specifications. While many specialize in clothing, some sewing contractors expand their offerings to custom accessories, branded merchandise, and soft goods. It’s worth noting, however, that most do not manufacture seamless knits, technical footwear, or structured bags—these categories typically require specialized equipment and production processes.
One significant advantage of the cut and sew model is its accommodation of low minimum order quantities (MOQs), making it ideal for startups, emerging brands, and promotional lines that prefer small-batch production without the constraints of traditional large-volume apparel manufacturers. This flexibility empowers entrepreneurs and independent designers to prototype, refine, and scale unique products while minimizing upfront costs and inventory risk.
When evaluating a cut and sew partner for your apparel line, keep the following critical stages in mind, as each stage directly impacts the finished garment’s quality and consistency:
To identify trustworthy cut and sew contractors, leverage apparel industry directories, manufacturer databases, and verified reviews. Look for transparent communication, comprehensive sample portfolios, and evidence of compliance with ethical labor standards. Offshore manufacturing may be tempting for its lower costs, but can pose risks with longer lead times, reduced oversight, and potential quality control issues. Many apparel brands prefer domestic, onshore sewing manufacturers for their responsiveness, proximity, and ability to facilitate direct designer collaboration.
Professional sewing contractors not only execute your production vision, but can support with apparel development services such as technical design consulting, complex pattern grading, and small-batch prototyping. This partnership provides fashion entrepreneurs with creative freedom while ensuring manufacturability, consistency, and brand quality across every production run. For best results, build a collaborative relationship by requesting samples, reviewing certifications, and discussing your long-term garment production goals.
Although online design submissions are common, initiating direct conversations and factory audits with your chosen apparel manufacturer helps you evaluate their reliability, production capacity, and quality management systems. This hands-on diligence is crucial for launching successful private label or custom apparel collections.
For decades, offshore apparel production has appealed to brands seeking reduced manufacturing costs on bulk garment orders. International cut and sew factories—located in regions such as Asia, Central America, and Eastern Europe—often operate with lower labor costs and less stringent regulatory oversight. This lower-cost environment allows fashion brands to maximize margins, particularly when mass-producing wholesale clothing lines.
However, relying on offshore sewing contractors can introduce challenges, including communication barriers, variable lead times, logistics complications, and increased risk to product quality. Distant time zones and potential language differences can delay feedback, impacting tech pack accuracy and delivery schedules. Quality concerns and labor rights issues have also driven brands to reconsider overseas manufacturing for ethical and branding reasons.
In response, many emerging designers and established apparel companies are choosing domestic, US-based cut and sew manufacturers for their consistent quality, transparent processes, and direct access for sample review or factory visits. Onshore production offers sophisticated quality assurance systems, faster turnaround times, and a collaborative environment—advantages vital for limited-edition clothing drops, direct-to-consumer (DTC) brands, and responsible fashion initiatives.
Ultimately, selecting between offshore and onshore cut and sew manufacturing depends on your brand’s values, production volumes, and target market. A careful risk-benefit analysis ensures your apparel products meet quality standards, align with operational goals, and satisfy consumer expectations for ethical and prompt manufacturing.
The printing process used to transfer your custom patterns and graphics onto fabric is a pivotal factor in determining garment vibrancy, durability, and tactile feel. State-of-the-art digital textile printing enables complex, high-resolution prints for apparel and soft goods, supporting vibrant colorways, detailed illustrations, and photographic designs. The primary methods for textile pattern printing include:
Digital Printing – The leading technology for modern cut and sew applications, digital printing delivers photo-quality color and pattern accuracy by transferring computer-generated files directly onto uncut fabric (also known as “fabric panels”).
Digital textile printing processes—including both sublimation and direct-to-fabric methods—use inkjet technology to deliver precise, full-color graphics. The difference between the two methods lies in fabric compatibility and how the dyes are absorbed.
Following printing, the prepared fabric undergoes a series of finishing treatments—steaming, washing, drying, and ironing—tailored for the specific textile to lock in color, improve hand feel, and ensure print longevity. The right printing technology, paired with high-quality fabric, sets the stage for standout custom apparel and soft goods.
The cutting process is a cornerstone of apparel manufacturing, as precision cutting determines garment fit, structural integrity, and waste minimization. In cut and sew production, the cutting stage involves extracting pattern pieces from fabric rolls according to the approved tech pack and graded size sets. Two main cutting phases are employed: rough cutting (separating fabric into larger panels) and precision cutting (trimming to the exact pattern shapes).
Cut and sew manufacturers utilize three principal cutting methods: traditional manual cutting with heavy-duty shears, semi-automated powered knife cutting, and advanced computerized cutting with automated knife or laser systems. Modern apparel facilities often use computer-aided cutting to ensure perfect consistency across large batch production, reduce fabric waste, and optimize marker layout. Standard operating procedures (SOPs) are strictly adhered to for safety and quality control throughout this process.
By leveraging expert pattern marking and precision cutting technology, top cut and sew manufacturers deliver the accuracy, speed, and repeatability demanded by premium apparel brands, promotional product lines, and custom batch orders. These processes are foundational to scalable, high-quality garment production and long-term manufacturing success.
In the cut and sew industry, a wide variety of sewing machines are utilized, each engineered to perform specific garment construction functions and boost manufacturing efficiency. These machines are robust, power-driven, and capable of operating at high speeds to meet the demands of commercial garment production. Industrial sewing machines are classified based on the types of seams they create, their stitch classes, and their use in different fabric and apparel applications. Understanding the different types of industrial sewing machines and their features is essential for apparel manufacturers, fashion designers, and sewing contractors who are evaluating equipment for mass production, custom clothing, or specialty sewn products.
Lock Stitch Machines – Lock stitch machines are among the most commonly used industrial sewing machines. Featuring a single needle and bobbin, lock stitch sewing machines efficiently join two or more layers of fabric with precision. They are versatile and can handle multiple fabric weights, making them ideal for high-volume sewing and apparel manufacturing. The resulting seam is strong and durable, suitable for garment assembly, dressmaking, and even upholstery applications.
Overlock Machines – Overlock sewing machines, also known as sergers, use three, four, or five threads to create clean, finished edges on fabric panels. These machines excel at serging garment edges, attaching elastic, and performing overedge stitching, making them indispensable in both cut and sew production and knitwear manufacturing. While overlock sewing machines are essential for creating durable, stretchable seams in T-shirts, sportswear, and underwear, they are also used in finishing raw edges to prevent fraying and unraveling in various textile products.
Flatlock Sewing Machines – Flatlock sewing machines utilize two or three needles, threading through materials and interlooping with a looper thread to set secure, flat seams. These machines are pivotal in hemming sleeves, producing seamless decorative accents, and reducing seam bulk in sportswear, activewear, and underwear manufacturing. Flatlock technology creates comfortable, flat-finished seams that enhance garment appearance and wearer comfort—a key advantage in performance clothing production.
Feed Off the Arm Machine – Feed off the arm sewing machines are designed for fast and accurate assembly of tubular and flat-felled seams using two needle threads to produce chain stitches. These specialized machines are ideally suited for constructing shirt side seams, underarm seams, jean inseams, and other continuous seams found in jeans, workwear, and outerwear. Their unique configuration allows garment factories to sew long, straight seams more efficiently, increasing productivity in bulk apparel manufacturing.
Button Hole and Attaching – Button hole and button attaching sewing machines are highly specialized, automating the process of creating buttonholes and securely attaching buttons of various sizes and styles to garments. These machines offer multiple buttonhole configurations—such as keyhole and straight buttonholes—and are indispensable for dress shirt, blouse, and jacket manufacturing. By automating repetitive tasks, they increase production speed, ensure consistency, and reduce labor costs in mass garment production.
Bartack Machine – A bartack sewing machine is utilized to reinforce high-stress areas and secure attached components on a garment, such as belt loops, pocket openings, and zipper ends. By creating a tight, densely stitched bar, bartack machines enhance garment durability and prolong the lifespan of apparel items. They are essential in denim manufacturing, work uniforms, and any application where garments encounter frequent tension or pulling.
Zigzag Stitching – Zigzag sewing machines produce a wide spectrum of zigzag stitch patterns, which provide stretchability and flexibility in seam construction. Commonly used for sewing garment edges, attaching lace, elastics, or for decorative topstitching, zigzag stitching is essential in swimwear, lingerie, and jacket manufacturing. These machines enable designers to incorporate both structural integrity and decorative detail in a single operation.
The cut and sew manufacturing process is highly efficient and flexible, enabling the rapid creation and scalable production of intricate fashion designs and custom sewn products—from small-batch clothing lines to large-scale uniform manufacturing. Leveraging advanced industrial sewing machines, apparel manufacturers can quickly transform digital patterns and computer-rendered visuals into finished products, offering endless opportunities for creativity, precision, and innovation in the textile and fashion industry. Whether you are a start-up clothing brand, an established garment producer, or a specialty textile contractor, understanding the capabilities and advantages of each type of industrial sewing machine ensures you can select the right equipment for your project needs, streamline your workflow, and achieve the highest standards in quality apparel manufacturing.
When choosing the best sewing machine for your production requirements, consider factors such as fabric type (woven, knit, synthetic), volume of production, desired stitch quality, ease of maintenance, machine automation levels, and available technical support. Investing in the appropriate sewing machinery not only increases operational efficiency, but also empowers your business to adapt to trending designs and rapidly evolving fashion industry demands, enhancing your ability to bring unique, high-quality garments to market.
The cut and sew process has significantly improved garment manufacturing by removing the need for traditional patterns when developing new brands or unique clothing designs. This method offers greater flexibility and creativity in producing high-quality, fashionable apparel.
The primary advantage of cut and sew manufacturing is the enhanced control it provides over every stage of production—from design creation and printing to cutting, sewing, and finishing. Unlike relying on pre-made garments that require adjustments, cut and sew enables designers to efficiently and effectively produce their own original creations.
The fashion industry is increasingly embracing the benefits of cut and sew manufacturing, as it provides a valuable platform for independent designers from diverse backgrounds to showcase and create their designs.
Collaborating with a cut and sew company offers designers access to extensive experience, which can be crucial for refining a product to meet manufacturing standards. An experienced cut and sew partner can assist in transforming a conceptual design into a perfected, production-ready product.
A tech pack, or technical packet, serves as a comprehensive blueprint for a clothing brand. It includes all specifications required to guide manufacturers through the initial stages of developing a clothing line. Tech packs allow designers to monitor, adjust, and oversee their product throughout the production process.
Tech packs provide detailed measurements, patterns, and technical specifications that help workers, supervisors, and managers convert these details into marketable garments. They act as a crucial communication tool to prevent errors and misunderstandings.
Throughout the garment's journey from concept to final product, it is handled by various workers, developers, and managers. To ensure the original design maintains its intended form and quality, a tech pack functions as a manual or standard operating procedure (SOP), guiding each step of the process and keeping everything consistent and on track.
Contents typically included in a tech pack are:
The detail and depth of the tech pack's contents depend on the expertise of the cut and sew manufacturer, which should have been evaluated during the selection process.
Cut and sew manufacturers possess the expertise needed to help new designers turn their concepts into reality. This aspect of cut and sew manufacturing is crucial for the successful development, creation, and production of garment designs. Choosing the right manufacturer is fundamental to building a successful business.
The professionalism of a cut and sew manufacturer can often be gauged by their track record of helping new designers bring their products to market. This is typically reflected in how the company presents itself and supports its clients.
New designers often face challenges finding companies willing to produce small quantities, as many large producers only handle high-volume runs. Cut and sew manufacturers, however, are generally more flexible and open to working with designers on limited orders, within certain constraints.
Low MOQs make it easier to launch a new clothing line, as they allow time for adjustments and corrections during production. This flexibility ensures that any issues can be addressed and resolved as needed.
Cut and sew manufacturers take pride in providing extensive service and guidance to their clients. The relationship between a designer and a cut and sew manufacturer often evolves into a partnership based on mutual trust and confidence, with both parties having a collaborative role.
There is a notable distinction between cut and sew operations and sew factories. In a sew factory, the designer is responsible for all aspects of the tech pack, including preparation for the factory's production line.
In contrast, cut and sew operations offer comprehensive services and support, including managing outsourcing for large production runs. This level of service distinguishes cut and sew manufacturing from other clothing production methods.
When selecting a cut and sew manufacturer, several key factors need to be carefully considered. Reviewing the track record of various manufacturers is a critical part of this process. Although it can be daunting and frustrating to sift through numerous options after investing significant time in developing a design, this step is crucial for turning a vision into reality.
A full-service cut and sew manufacturer offers a comprehensive range of services, from design assistance to garment completion, all under one roof. Typically, designers pay a flat rate for these services, allowing them to focus on overseeing the process rather than managing multiple aspects individually.
This streamlined approach helps control and minimize costs. Opting for a lower-priced, less comprehensive service can sometimes result in a lower-quality final product, making it important to balance cost with the quality of service provided.
Cut and sew specialists are equipped to handle a wide range of batch sizes, unlike many garment manufacturers that may have minimum quantity requirements due to production and equipment costs. Cut and sew professionals are designed to accommodate various production runs, making them versatile and adaptable to different needs.
Among the most critical factors in choosing a cut and sew company are their knowledge, expertise, and experience. As the saying goes, experience is invaluable. A company’s website should provide information about their successful projects and satisfied clients, which can help verify their credentials.
It’s often surprising to learn that many well-known brands began their journey with cut and sew services. These companies, which have played a role in the success of established designers, are also open to working with newcomers. This openness is a testament to the supportive nature of the cut and sew industry.
A canopy is a structure with a connected fabric or metal covering that can give shade or shelter from weather elements such as the sun, hail, snow, and rain. For example, a tent with no floor can be...
Contract sewing is a specialized industry that provides services to manufacturers for production of a wide range of products using highly skilled workers and technologically advanced sewing machines. The strength of the contract sewing industry is its ability to perform any type of sewing services...
A protective cover is a sewn fabric that is specifically designed and used for protecting equipment, people, surfaces, and enclosures. Protective covers provide protection from the elements, UV rays, dirt, dust, moisture, and...
A carrying case is a way of conveniently organizing and transporting a collection of similar or dissimilar items for future use. There is a type and kind of carrying case to fit every possible application from protecting and storing cell phones to cases for speaking systems and technical equipment...
Contract manufacturing is a business model in which a company hires a contract manufacturer to produce its products or components of its products. It is a strategic action widely adopted by companies to save extensive resources and...
A hard case is a type of carrying case that is made from molded plastic, aluminum, veneered or laminated wood, or different types of metals. They are the most secure and durable forms of carrying cases and...
A road case is a ruggedly built, highly functional protective container with varying wall thicknesses that is capable of withstanding the riggers and handling of shipping. They are designed to meet...
A tool case is a portable case designed to organize and protect tools and allow easy access and convenient availability. Standard tool cases can be used when working on a project. In addition, specialty and custom-designed tool cases are...
Cases designed to carry special valuables have been part of society throughout history back to the time of the Egyptians and before. Carrying cases are commonly found in any house stored in a garage, tucked away in a basement, or setting on a shelf...