Industrial Shredders
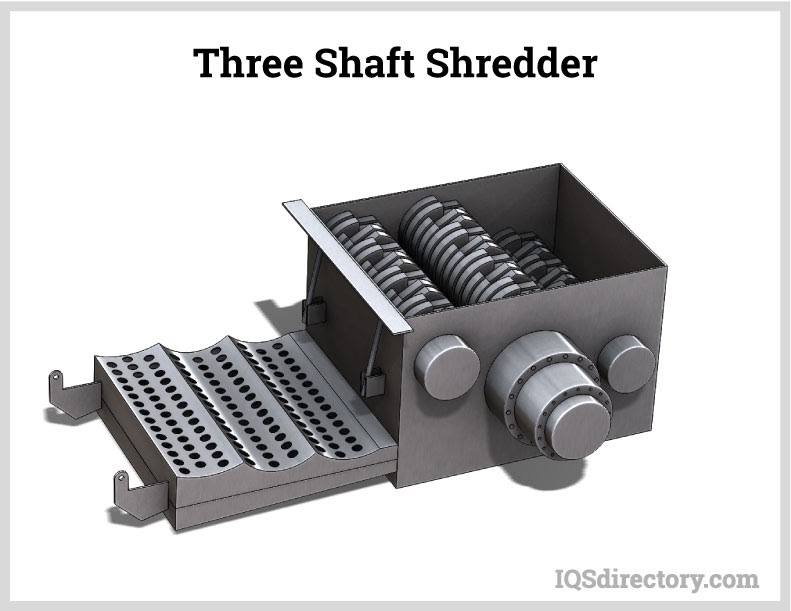
An industrial shredder is a piece of heavy duty equipment designed to shred dense and light materials to prepare them for recycling or for the destruction of unusable products. They are an environmentally sound device that...
Please fill out the following form to submit a Request for Quote to any of the following companies listed on Cardboard Shredders .
This article takes an in depth look at cardboard shredders.
You will learn more about topics such as:
A cardboard shredder is a piece of equipment engineered to transform cardboard boxes and sheets into small fragments or strips. Specialized cardboard shredders are specifically designed to convert cardboard into flexible, perforated materials suitable for packaging needs. These machines can produce cushioning, flat netting, chips, shreds, or strips. It is important not to mix them up with paper shredders, despite their similar designs.
The process of shredding cardboard involves breaking it down into various forms, such as tiny chips, elongated strips, perforated sheets, or other configurations, contingent on the shredder's design and functionality. This preparation is crucial for recycling, making it possible for cardboard to be repulped, processed, or repurposed into packaging materials for shipping purposes.
Cardboard plays a crucial role in packaging, shipping, and product presentation, offering essential protection for goods. As e-commerce and global logistics grow, the demand for robust cardboard packaging continues to rise. However, the widespread use of cardboard packaging also brings the challenge of proper disposal and avoiding landfill accumulation.
To address these sustainability concerns, efficient recycling and repurposing of cardboard are essential. This process heavily relies on specialized cardboard shredders and recycling equipment. Cardboard shredders are designed to break down cardboard materials—corrugated boxes, sheets, and packing inserts—into various forms for reuse, recycling, or compact waste management. These industrial shredders not only reduce the volume of cardboard waste, but also help companies save on disposal costs, support green initiatives, and comply with environmental regulations. Although many companies manufacture cardboard shredding machines, their primary functions are categorized into perforation and shredding for material processing and packaging reuse.
In addition to various shredding techniques, there are specialized machines designed for repurposing cardboard through perforation. Cardboard perforators use a cutting cylinder equipped with blades that create perforations or small holes in the cardboard, but do not fully sever it. This process produces an elongated, flexible, and cushioned form of paper—often called “cardboard matting”—which can be utilized as packing material, void fill, or protective cushioning for shipments.
Although perforators do not break cardboard into small pieces, they offer a valuable method for transforming used cardboard into a reusable packing material, enhancing its utility for sustainable packaging and product protection in transit. Many businesses use cardboard perforators to replace bubble wrap or foam, reducing reliance on single-use plastics.
While shredding paper typically generates minimal dust, this is not usually a significant issue except in large-scale industrial settings. In contrast, shredding cardboard produces substantial amounts of dust due to the size and fiber content of the material, necessitating effective dust capture and air filtration measures to protect worker health and equipment.
Cardboard shredders with dust control have a flanged outlet positioned above the cutting blades with ductwork that connects the shredder to a dust collector. To ensure smooth movement of dust-filled air, a fan inside the dust collector chamber pulls the cardboard dust through a high efficiency particulate air (HEPA) filter, which captures even fine particles from the air and forces the filtered air back into the environment.
To maintain both the cleanliness and efficiency of the dust filter, compressed air is used to send brief bursts of air against the filter, counteracting the flow of dust-laden air and keeping the filter free from clogging and blockages. Regular filter maintenance ensures optimal performance of industrial shredder systems.
A cross-cut cardboard shredder not only performs the same longitudinal cuts as a strip-cut shredder but also incorporates an additional crosscut. This dual-cutting action results in small, confetti-like pieces of cardboard, maximizing packing density and reducing waste volume. The specifics of the cross-cut shredding can vary, with particle sizes ranging from fractions of an inch to several inches, depending on the machine's configuration and settings. These industrial shredders are ideal for applications requiring uniform, easily processed shredded material.
Industrial cross cut shredders can be high volume shredders with conveyors as a feeding mechanism, allowing them to handle the continuous processing demands of warehouses, distribution centers, and recycling plants. To enhance the cutting process, some designs have integrated paddle wheel crushers that compress the cardboard before it enters the cutting blades. Cutters are made from high grade alloys capable of withstanding constant use and abrasive wear. Cross cut cardboard shredders are especially effective for secure destruction of branded packaging or confidential shipping labels, supporting data protection and compliance with privacy standards.
Dual-shaft cardboard shredders operate slowly and quietly, featuring two sets of counter-rotating blades mounted on opposing shafts. The twin-shaft configuration enables the shredder to handle thick, heavy-duty cardboard, including multi-wall (two- or three-ply) corrugated boards and laminated packaging. Dual-shaft shredders offer enhanced cutting power and versatility compared to standard shredders, and they are engineered to process various materials—ranging from dense cardboard to pallets and other bulky packaging waste—making them well-suited for demanding recycling applications.
Typically, dual-shaft cardboard shredders are equipped with a single motor, although some models include dual motors to boost shredding speed and power. The interlocking dual blades work in tandem to grip and shred material into very fine pieces, preventing jams and ensuring consistent throughput. Dual shaft shredders are known for their durability, low maintenance, and ability to handle contaminated or mixed packaging waste with minimal risk of damage.
One of the key advantages of four-shaft cardboard shredders is their superior reliability, high throughput, and minimal maintenance requirements, in addition to their unmatched capability to handle heavy-duty cardboard materials. These shredders are robust machines equipped with four sets of rotating blades, engineered for demanding environments such as recycling facilities, manufacturing plants, and distribution hubs.
Four-shaft cardboard shredders are known for their high processing speed and exceptional shredding power, allowing them to reduce large volumes of cardboard waste into shreds that are exceptionally small in size. This precise size reduction enables easy baling, compacting, or direct recycling. Advanced four-shaft shredders include smart control systems for customizable output, making them the preferred choice for businesses with high-volume packaging waste and sustainability goals.
The shredding of cardboards includes industrial box shredders that are capable of tearing cardboard boxes apart into smaller pieces or specific strip forms. This form of shredder is a preprocessing method used to prepare cardboard for baling, where the boxes are ripped apart before being baled and compacted for transport or recycling. There are various ways the boxes are fed into the shredding process, including automated conveyors, manual feeders, or hoppers where boxes are dropped in.
Shredding boxes involves using three or more shafts or rotors that draw in the material and tear it apart using high-torque, low-speed action. The spiral configuration of these rotors enhances the shredder's force and capacity, making them ideal for facilities with bulk packaging or large-scale cardboard waste. Given the thickness and density of the material, box shredders operate at a slower speed for added safety, which helps reduce both dust and noise. Some box shredders are also equipped with output sorting screens, dust suppression systems, and overload sensors for safe and efficient operation.
Single rotor cardboard shredders are compact and specifically designed for processing cardboard and other lightweight materials. These shredders feature various feeding mechanisms—such as infeed chutes or automatic conveyors—to guide the cardboard into the rotor cutting tool. Inside, a robust rotor with mounted cutting blades grinds the cardboard against a counter-knife. To achieve precise and consistent sizing, single rotor shredders include a perforated screen beneath the cutting rotor, which regulates the dimensions of the shredded material for downstream processing or baling.
Due to their small footprint and lower energy consumption, single rotor shredders are popular for commercial applications, mailrooms, and businesses seeking a cost-effective recycling solution. These machines offer controlled particle size output and are easy to maintain, contributing to efficient packing material creation and improved recycling rates.
Strip cut cardboard shredders have a similar function to the common paper shredder, but with higher capacity and more durable construction. A set of rotary blades cuts the cardboard into strips that are the same length as the cardboard sheets, creating easily compressed ribbons ideal for packing or cushioning. Strip cutting cardboard shredders destroy the structural integrity of the cardboard, leaving long slender strips or ribbons that are suitable for both shipping and packaging protection.
Strip cut cardboard shredders are known for their operational efficiency and high-speed throughput. With fewer moving components, these shredders generally require less maintenance and operate with greater simplicity. Their easy-to-use design makes them a favorite among businesses with low to medium cardboard disposal needs, while also supporting sustainability by turning waste into eco-friendly packaging alternatives.
Choosing the Right Cardboard Shredder for Your Operation
When selecting a cardboard shredder for your packaging, recycling, or waste management needs, consider several key factors: throughput requirements, cut style (strip cut, cross cut, perforated), material thickness, dust control needs, safety features, and available floor space. High-volume warehouses and recycling centers may benefit from robust dual-shaft or four-shaft models with advanced feeding and dust collection systems, while small businesses may find single rotor or strip cut models sufficient for their needs. Many industrial shredders can be customized with add-ons such as automatic oilers, energy-saving modes, and noise reduction panels.
Investing in the right cardboard shredding equipment allows your business to reduce waste-hauling costs, create sustainable packing materials, and promote a circular economy. For optimal performance and return on investment, partner with reputable manufacturers who offer technical support, warranty coverage, and replacement parts availability.
All shredders operate using a combination of key components, including a housing, rotor, blades, motor or motors, feed system, and an efficient power supply. The strength, industrial design, and configuration of different shredders—such as industrial shredders, commercial shredders, and paper shredders—vary according to the types of material they are engineered to process. Paper shredders, for example, typically have lower power and endurance compared to heavy-duty units designed for thicker materials like cardboard, packaging waste, or corrugated fiberboard.
Cardboard shredders are specialized equipment built for recycling and repurposing cardboard boxes, shipping cartons, and corrugated packaging. These machines come in various types, including dedicated cardboard shredders for warehouses and versatile shredders capable of handling mixed waste streams (including plastics and foam). Models designed exclusively for cardboard feature reinforced construction, high-torque motors, and precision cutting blades capable of handling cardboard up to one inch thick or more. Their robust design enables them to efficiently process packaging material—turning cardboard waste into eco-friendly packing material or void fill alternatives—making them an integral part of sustainable recycling solutions for businesses.
Cardboard shredders feature a variety of feeding mechanisms that influence both ease of use and throughput capacity. Simple entry-level shredders employ a manual feed system, where operators insert cardboard sheets and used boxes directly into a hopper. This design is suitable for smaller operations or occasional shredding needs. Larger, industrial-grade shredders are equipped with automated conveyor feeders, which deliver bulk cardboard continuously and at a controlled pace into the cutting chamber. Automated feeding not only increases productivity but also ensures consistent shredding performance, helping facilities manage high volumes of packaging waste efficiently. Some advanced models offer safety sensors, auto-reverse functions, and adjustable feed rates for optimal workflow and protection.
The rotor assembly is the heart of a cardboard shredder, containing the sharp cutting blades that interlock and slice through tough materials. Rotors in shredders can range from single-shaft to dual-shaft and multi-shaft designs. Multi-shaft shredders are particularly effective in high-volume environments, boosting efficiency and enabling the machine to handle thick and heavy cardboard pieces, sheet stock, or whole boxes with reinforced seams.
Manufacturers offer diverse rotor configurations and cutting methods, allowing users to choose between strip-cut, cross-cut, and particle-cut options. The type of cut impacts the size and shape of the shredded output—ranging from thin strips and rough chunks to finely shredded confetti. This versatility makes it easy to tailor the end product to its intended use, such as creating cushioning, packaging filler, or compressed recyclable material.
Overfeeding cardboard that exceeds the designed rotor capacity may result in jams or potential mechanical strain, decreasing operational life. For optimal performance, it is essential to select a shredder that matches rotors’ size, number, and cutting power to the types and amounts of cardboard processed. This consideration ensures reliability, low maintenance costs, and long-term durability for industrial and commercial cardboard recycling applications.
The motor in a cardboard shredder is responsible for powering the rotors and generating the torque required to cut through thick, corrugated material. Motor specifications—such as horsepower (HP), voltage, torque, and revolutions per minute (RPM)—vary depending on the shredder’s rotor size, throughput requirements, and the density of cardboard being processed. Industrial cardboard shredders typically feature high-torque, energy-efficient motors ranging from 200 volts for compact models to powerful, multi-horsepower motors for continuous-duty operation.
Motor efficiency, reliability, and advanced features like overload protection or variable speed control are crucial for heavy-duty environments. When evaluating a cardboard shredder, consider the type of material, desired output capacity, and available electrical infrastructure to select the right motor configuration for your facility’s recycling needs.
Electric power systems are the most prevalent among cardboard shredders due to their widespread availability, low maintenance, and compact installation requirements. The specific power supply needed depends on the shredder’s rated capacity and operational demands. Heavy-duty industrial cardboard shredders typically require more substantial electrical input, while smaller, commercial units may operate efficiently on standard power sources. For businesses with high throughput, continuous cycling, or 24/7-operation, energy efficiency and optimized power consumption are vital for minimizing utility costs and reducing environmental footprint.
Modern shredders often incorporate advanced power management systems, such as smart sensors and automatic shutoff features, to conserve energy and enhance operational safety. When purchasing a cardboard shredder, be sure to assess the building’s electrical capabilities and select a model with the right power rating and efficiency features for maximum return on investment and sustainability goals.
Cardboard is extensively used for packaging, shipping, storing, and presenting products. It has become an integral part of daily life and business. However, eventually, all cardboard reaches the end of its functional life. Historically, such cardboard was simply discarded in landfills.
With growing environmental awareness and a focus on recycling, various methods have been developed to manage used cardboard. It can be compacted into bales for repulping into new boxes, or it can be processed into packing material through perforation and slitting.
Cardboard shredders, designed similarly to paper shredders but with greater durability and capacity, are used to process cardboard. This shredding not only helps manage waste but also plays a role in environmental conservation.
Cardboard shredders facilitate the processing of large quantities of cardboard by breaking it down for use in reshipping products. Rather than letting bundles of cardboard accumulate while waiting for collection, shredding allows it to be repurposed for packaging. This reduces waste and eliminates disposal costs.
Businesses today are increasingly committed to environmental sustainability and green practices. Manufacturers and producers are continuously exploring ways to demonstrate their dedication to eco-friendly methods. Shredding cardboard is one way companies can showcase their commitment to responsible material disposal, reducing landfill waste and supporting recycling efforts.
In manufacturing and production, managing large quantities of cardboard is essential. Whether it’s in its complete form or disassembled, cardboard takes up significant storage space. Cardboard shredders help alleviate this issue by compressing the material into smaller, more manageable pieces. Shredding reduces the bulk of cardboard piles, making them much more space-efficient and easier to handle.
Debris and clutter in the workspace can significantly hinder operations and obstruct workflow. Accumulated piles of cardboard not only create obstacles for workers but also pose a fire risk. Utilizing a cardboard shredder to swiftly process and remove these piles helps eliminate tripping hazards and reduces the potential for fire hazards.
Numerous waste management firms buy used cardboard for resale to manufacturers. These companies handle the collection, transportation, and disposal of shredded cardboard, which is then repurposed for recycling and producing new boxes.
Recycling cardboard plays a crucial role in forest conservation by decreasing the demand for new paper, thereby reducing the number of trees needed. Annually, the production of paper products leads to the cutting down of approximately 15 billion trees. By shredding and recycling cardboard, this demand is significantly reduced.
The paper used in cardboard is primarily sourced from birch and pine trees. These species are not only fast-growing but also highly recyclable, making them ideal for sustainable paper production. Their efficient management and harvesting contribute to the environmental goals of the cardboard industry.
Air pollution and its environmental impact have long been significant concerns. To address these issues, air filtration systems have been developed to comply with the standards set by the Environmental Protection Agency (EPA). Incineration of cardboard is one aspect of pollution, as the coatings and adhesives used in cardboard production are not intended for burning.
Cardboard shredders play a crucial role in mitigating this problem by minimizing the amount of cardboard that needs to be incinerated. By breaking down cardboard into small chips and strips, shredders make it easier to either dispose of or repurpose the material, reducing the need for incineration.
The papermaking process consumes a significant amount of water, particularly during the pulping stage. Utilizing shredded cardboard for the production of new cardboard products helps conserve water. Recycled cardboard requires 80% less water in the repulping process, resulting in a savings of approximately 7,000 gallons (or 25,000 liters) of water per ton of recycled material.
Among recyclable materials, cardboard boasts the highest recycling rate, significantly reducing the energy needed for its production. Recycling cardboard uses 75% less energy compared to creating new cardboard from raw materials, and it consumes 50% less electricity.
Recycling and repurposing shredded cardboard offer substantial resource savings. For every ton of corrugated containers recycled, it is estimated that one barrel of oil, six million Btus of energy, 3902 kWh of electricity, and five cubic feet of landfill space are conserved. The recycling process can provide approximately 70% of the raw materials needed for the cardboard manufacturing sector.
Shredded cardboard simplifies storage, transportation, and recycling. By breaking down solid cardboard into smaller fragments, the material becomes more manageable and easier to handle. The reduced weight of these smaller pieces not only makes storage more efficient but also decreases the fuel required for transportation.
Cardboard shredders streamline the disposal of large cartons and bulky packing materials that consume valuable storage space. Selecting the right shredder requires careful evaluation to ensure it meets the specific needs of the materials, employees, and the scale of the operation.
When purchasing a cardboard shredder, several factors should be considered. It is crucial to choose a shredder that aligns with the organization's current requirements and remains adaptable to future growth and changes.
The capacity of a cardboard shredder indicates how many layers of cardboard it can process in a single operation and the maximum thickness it can handle. Industrial-grade shredders are capable of managing multiple thicknesses simultaneously and can even shred entire boxes.
Run time is a crucial aspect, particularly for operations running multiple shifts, where the equipment is expected to function for extended hours. The duration a shredder can operate is impacted by the volume of cardboard it needs to handle. In shipping environments, dealing with cardboard waste efficiently is essential to maintain productivity and create space.
Manufacturing settings also require a solution for cardboard disposal, though the demands may be less intense compared to material handling facilities.
Cardboard shredders are equipped with motors that drive the rotors and blades to slice through the cardboard. The effective run time of a shredder depends on how long it can function before the motor reaches its temperature limit and how quickly the motor cools down afterward.
When deciding on a cardboard shredder, opting for a less expensive model might seem like a cost-effective choice. However, this can be a mistake if the lower-cost shredder lacks the necessary power and durability to handle the demands of your operation. It's crucial that the shredder's size and capabilities align with the volume of work it will perform. While higher-powered shredders might have a higher initial cost, their superior endurance, capacity, and efficiency can provide greater long-term value and performance.
Choosing a cardboard shredder with a jam-resistant feature is crucial to avoid frequent interruptions and delays in operations. Jams can lead to repeated shutdowns and slow down workflow. Most cardboard shredders are equipped with mechanisms designed to prevent jamming, thereby improving their overall efficiency and reliability.
Most industrial cardboard shredders are equipped with overload detectors as a safety measure. These detectors alert users when the machine is being fed too much cardboard or if the material is excessively thick. This feature works alongside the jam prevention system, both of which contribute to prolonging the shredder's lifespan and ensuring optimal performance.
An industrial shredder is a piece of heavy duty equipment designed to shred dense and light materials to prepare them for recycling or for the destruction of unusable products. They are an environmentally sound device that...
Scrap metal must be processed to be effectively recycled and ready for reuse. Metal shredders are machines used to process a variety of metal scraps. Metal shredders are frequently used to reduce metal debris to...
A shredding machine is equipment utilized for shredding. Shredding machines are used to reduce the size of materials. While most online sources define the shredding machine as...
Tire shredders are a type of recycling equipment used to reduce the volume of tires to scrap using high torque shredding systems. The various types of tire shredders are capable of handling large loads of...
A baler is a piece of equipment used to compress solid industrial waste or recyclable materials (e.g., paper, plastic, foam, cans, etc.) to achieve better material handling and storage. Eliminating empty space between individual items of these bulk products is a great way to save costs attributed to storage and transport...
A bowl feeder is a mechanism for supplying small parts and components to a production line or for sorting bulk items for rapid use. A self contained bowl feeder system has a bowl that sets on a spring loaded base that moves vertically...
A cardboard baler is a mechanism that uses a metal plate driven by a hydraulic ram to apply tremendous pressure and force to crush, compact, and compress pieces of cardboard into tightly formed and easy to transport cubes and...
A Trash compactor is a machine or device designed to compress, reduce, and compact a variety of materials through hydraulic, mechanical, or pneumatic force. The initial steps in the compacting process are the collection of the material to be compacted...
Vibratory conveyors are material-handling equipment used to transport fine to coarse-grained bulk materials. These vibratory conveyors are strong conveying equipment utilized for bulk commodities with fine to coarse graininess...
Vibratory feeders are short conveyors used to transport bulk materials utilizing a controlled vibratory force system and gravity. The vibrations impart a combination of horizontal and vertical acceleration through tossing, hopping, or sliding-type of action to the materials being handled...
A vibratory screening is a process that separates bulk solid materials from solids and slurries using inertial vibration that causes various sizes of particles to pass through openings in a screen or...
Modern balers are descendants of hay presses, invented in the mid-nineteenth century, that made it easier to gather and stack hay. The earliest hay presses were stationary units built into a barn and extending two to three stories into the hayloft...