Cardboard Shredders
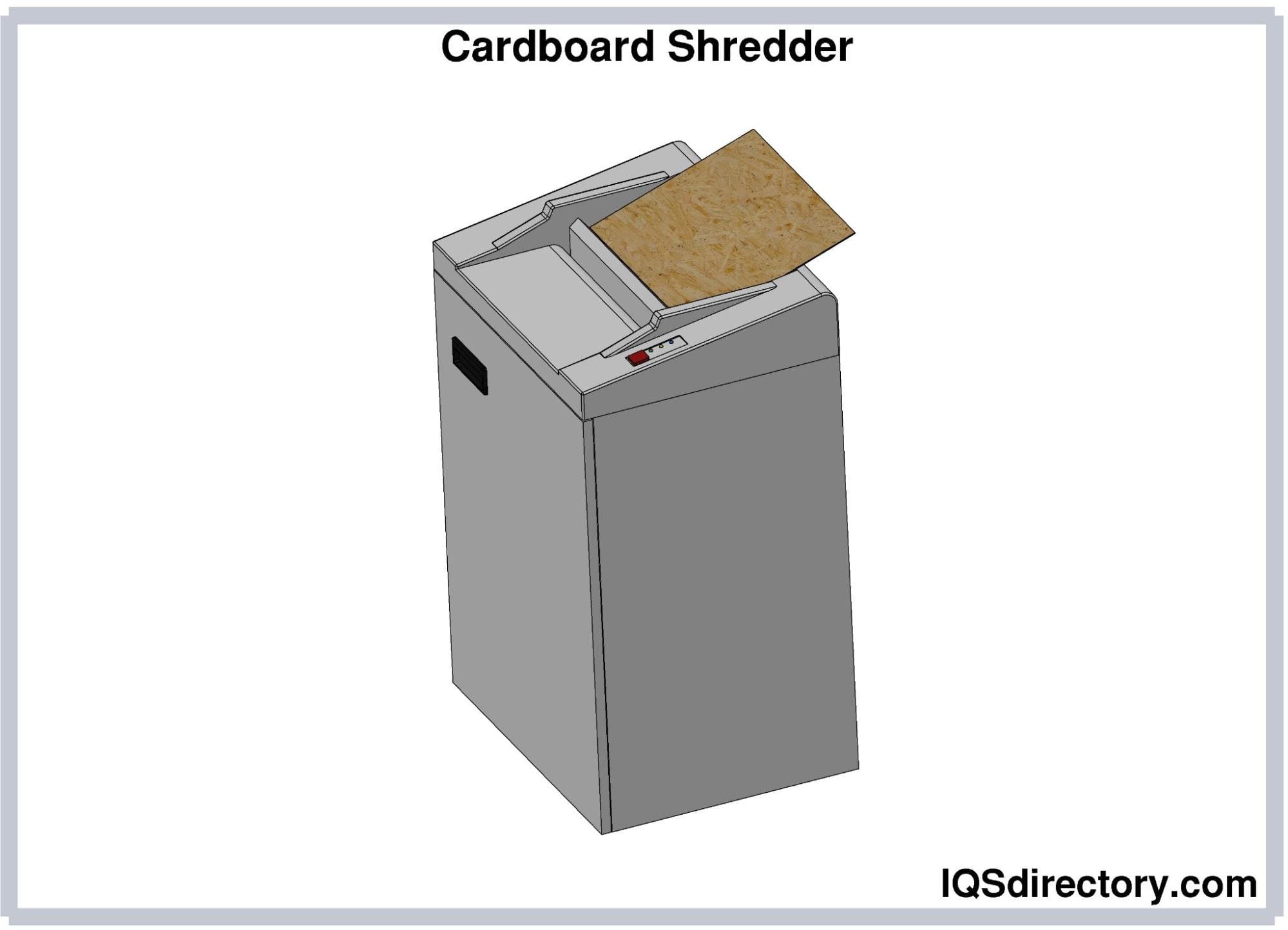
A cardboard shredder is a machine designed to turn cardboard boxes and sheets into small shards or strips. Specialty cardboard shredders are configured to convert cardboard into flexible perforated material for packaging...
Please fill out the following form to submit a Request for Quote to any of the following companies listed on
This article contains everything you need to know about tire shredders and their use.
You will learn:
Tire shredders are specialized machines in the recycling industry, designed to diminish the volume of tires by employing high-torque shredding mechanisms. Available in various models, they are capable of processing substantial volumes of tires of diverse sizes. By cutting, slicing, and crushing end-of-life tires (ELTs), these shredders transform them into rubber chips. Tire shredding serves as an essential technique for recycling, reprocessing, and transforming waste tires into valuable products.
Although applying new treads to tires is possible, shredding them simplifies repurposing and recycling efforts. Tires are commonly shredded due to their weather-resistant nature and slow breakdown, making them ideal for numerous recycling applications. A significant part of a tire is hollow, meaning landfilling is inefficient and expensive. Shredding enhances disposal efficiency and environmental responsibility.
To optimize shredding outcomes and safeguard the shredder, tires often undergo preliminary preparation. A vital component of this preparation involves removing the bead, a thick rubber or steel band located on the tire's inner edge. When tires are cut open, they form a U shape, with beads situated at the U's tips.
Tire shredding requires robust, heavy-duty equipment capable of handling significant torque due to the toughness and thickness of tires. This is particularly important when shredding large truck tires, earthmover tires, and mining equipment tires.
The first step in tire shredding is to gather the tires for processing. The most responsible way to dispose of tires is to deliver them to a tire shredding facility, as throwing them in the trash is illegal. Tire dealers often collect large volumes of end-of-life tires (ELTs) and usually have arrangements with recycling companies to pick up and process these tires.
Tire bead removal is a mechanized process conducted using a specialized machine. This step is crucial to reduce wear on the tire shredder. The tire is placed on the machine and rotated against a cutter that slices the beads from both sides. The removed beads, like the shredded tire chips, are recyclable materials.
Although often called tire shredding, this step is just the start of tire recycling. Shredding primarily cuts tires into strips, which are then processed into granules or fine powder. The shredding process is completed through either mechanical or cryogenic methods.
The constant crushing and tearing of the rubber produce a form of recycled rubber referred to as crumb rubber, which is rubber in a variety of shapes and sizes. The different forms of crumb rubber can take the form of a dust like material to particles that are 0.05 inch (0.127 cm) in size. Internationally, crumb rubber is referred to as 10:20 mesh or the size of sand particles, which is a reference to the number of holes per inch in the screens used for sizing materials.
Tires are made up of more than rubber. They have steel belts, fibers, and beading that have been used to reinforce and strengthen the tire. As with the rubber, these other components are saved for recycling. During the shredding process, tires are repeatedly ground to remove the fibers and steel, a process that is referred to as ambient grinding. The constant grinding in the shredding process increases the mesh size to produce smaller crumb rubber.
Cryogenic shredding has gained a great deal of tracking in recent years due to the limited amount of energy it requires and the lack of pollutants. The process makes it easier to remove the steel and fiber from the rubber, which are cleaner for recycling.
Some companies use the cryogenic process in conjunction with mechanical shredding to produce fine rubber powder. Cryogenic shredding is a devulcanization process where the mechanical properties of the vulcanized rubber are broken. The result of the process is the production of an extremely fine powder.
Cryogenic shredding separates the components of ELTs and transforms the rubber into a manageable form. The difficulty with the process is its cost, which is prohibitive due to the expense of the refrigerants such as the liquid nitrogen.
Sorting involves collecting the fibers and steel from the shredded rubber material and is completed using various processes. Magnets are used to pull the steel fibers out of the shredded mass while other methods are used to remove the fibers. Larger fibers are easier to separate and remove.
SSince magnets can't separate fibers, they are removed using size differential or weight. The processing equipment fluffs or enlarges the fibers, which are then extracted with a scalping screen. The tiny size of the crumb rubber facilitates its separation from steel and fibers. Any remaining fibers can be removed using a vacuum gravity separator.
Vacuum gravity separators remove fibers based on their density, size, shape, and weight, distinguishing them from crumb rubber. These separators feature a vibrating porous deck where particles make contact. Low-pressure air lifts lighter materials off the deck, and at the discharge, particles are sorted from least to most dense and smallest to largest.
Screening ensures that crumb rubber is free from any residual steel or fibers and is crucial for producing clean, usable material. This process involves carefully checking for contaminants that could affect the rubber's quality. During screening, crumb rubber is further separated based on size and other characteristics to ensure it meets the required specifications.
Screening crumb rubber presents challenges due to its flowability, which can cause it to move away from the screening surface. To address this, various screening methods have been developed. One effective technique is tumbler screening, where the material undergoes a tumbler motion. This motion adjusts the axial propagation to meridional and tangential angles, altering the trajectory of the processed material to improve screening efficiency.
Another effective screening method is the vibratory removal screen. This screen vibrates to separate crumb rubber from the fibers, allowing the rubber to fall through while leaving the fiber fluff behind. Additionally, vacuum systems positioned along the vibratory lines help to remove the fiber fluff efficiently.
After screening, the crumb rubber undergoes a thorough cleaning process using water and solvents. This step ensures that each form of crumb rubber is free from contaminants and impurities, making it ready for shipment to manufacturers. Proper cleaning is crucial to avoid any interference or contamination in the production of new rubber products.
Pyrolysis is a thermal decomposition technique used to convert end-of-life tires (ELTs) into valuable materials. This process involves heating tires to high temperatures in the absence of oxygen, which decomposes the rubber into gas and liquid fuels. These by-products can then be utilized by the chemical, energy, and transportation industries. Pyrolysis is a versatile thermochemical process applicable to any carbon-based material, leveraging extreme heat to chemically and physically separate the crumb rubber into distinct molecules.
In pyrolysis, the decomposition of crumb rubber occurs due to the limited thermal stability of its chemical bonds. This thermal decomposition creates new molecules. The process is endothermic, meaning it absorbs heat and occurs in the absence of air. Pyrolysis produces solid, liquid, and non-condensable gases such as hydrogen (H₂), methane (CH₄), ethane (C₂H₆), ethene (C₂H₄), propane (C₃H₈), propene (C₃H₆), butane (C₄H₁₀), and butene (C₄H₈). The specific types and quantities of gases generated depend on the type of crumb rubber and the operating temperature of the process.
Tire shredders are available in various sizes, configurations, and shredding methods. The choice of shredder depends on the manufacturer's needs and the specific requirements of the recycling operation. Additionally, the volume of material to be processed plays a role in selecting the appropriate shredder, with some operations necessitating larger and more robust equipment for high-volume shredding.
Tire shredders are essential to the rubber and tire recycling industry, serving a crucial role in the safe, efficient, and eco-friendly processing and disposal of used tires.
A dual shaft tire shredder features two interlocking shafts that cut into each other. The size of the shredded rubber depends on the thickness of the blades and the number of teeth on them. Thinner blades produce smaller pieces, while a higher number of teeth results in shorter shredded material.
As a low-speed, high-torque tire shredder, dual shaft tire shredders produce minimal heat and generate only a small amount of dust. The design of the two shafts helps prevent jams, ensuring smooth and continuous shredding.
Chipping tire shredders utilize multi-stack and double-stack knife systems to generate clean-cut chips. These knives are designed for sharpening, rotating, and reusing, which makes them a cost-effective choice for whole tire processing. A notable advantage of chipping tire shredders is the easy blade replacement feature in both double and multi-stack knife setups, helping to minimize labor costs.
Secondary tire shredders are used to further process pre-shredded tire material into smaller chips. They take the rough shreds produced by primary shredding and reduce them to pieces that are one inch (2.54 cm) or smaller. During this process, any wire remaining from the end-of-life tires (ELTs) is also removed and collected for recycling.
A rubber granulator is the third step in the tire shredding process. It grinds the wire-free rubber material into pieces ranging from 0.039 to 0.2 inches (1 mm to 5 mm). The granulator's knives further reduce the material from secondary processing into crumb rubber. During this stage, any remaining fibrous material is removed using cyclonic blowers, a screening system, and filter bags. This granulation process prepares the recycled rubber for further manufacturing and processing.
Granulators, like other components of the tire shredding process, come in various sizes and designs, with different loading hopper capacities. Depending on their design, granulating tire shredders can handle an hourly capacity ranging from two tons to nine tons.
Portable tire shredders come in various forms, including those mounted on four wheels for easy mobility and others mounted on semi-trucks, similar in size to shredders found in recycling plants. The primary purpose of portable or mobile tire shredders is to bring the shredding equipment directly to the location of end-of-life tires (ELTs), eliminating the need to transport the tires to a recycling facility.
Portable tire shredders offer the same features as stationary models but in a mobile and accessible format. While each type has distinct features that set it apart, they all share basic components such as blades and grinding shafts. Despite variations in blade design, portable shredders perform just as efficiently as their non-portable counterparts.
Ultrasonic tire shredding utilizes high-frequency vibrations to ease the cutting process by reducing material resistance. The cutting edge of an ultrasonic shredder vibrates at 20,000 times per second, enhancing efficiency, cooling, and minimizing debris. This method also devulcanizes rubber by breaking down sulfur-to-sulfur and carbon-to-sulfur bonds, allowing the rubber melt to be repurposed for new tire production.
Ultrasonic tire shredding uses rapidly moving sound waves to disintegrate tires by applying pressure to the rubber. This non-contact method reduces mechanical stress on equipment, lowers energy consumption, and is more eco-friendly compared to traditional mechanical shredding methods.
Tire shredders are complex heavy-duty pieces of equipment capable of producing high torque in the shafts of the shredder. Although shredders have the single function of changing whole tires into tiny fragments, their engineering and design is carefully planned to ensure efficiency and protection for shredder operators.
The components of a tire shredder are similar to those found in other shredding equipment but are designed with added strength, durability, and toughness needed for processing tires. A basic tire shredder consists of a rotor, cutting blades, housing, motor, transmission system, power supply, and controls.
The cutting blades are the most crucial component of a shredder, particularly for tire shredders, as they are responsible for breaking down tires into small pieces. While various shredders are designed for materials like paper, plastics, and metals, tire shredders are specifically engineered to handle the toughness of tires. To achieve optimal performance, these shredders require high-quality blades capable of efficiently tearing tires apart.
Double shaft tire shredder blades are the most commonly used type and must be installed correctly to ensure effective cutting and long-term durability. Proper installation is crucial for optimal performance and blade lifespan. These blades are spiral-mounted with a spacer sleeve to keep them separated in the middle. Their design is such that the blades do not collide during the shredding process. Typically made from tool steel, these blades are specifically designed to handle the toughness of rubber.
The motor powers the shredder blades, driving them to cut through tires. Tire shredders use either electrical or hydraulic motors, depending on the shredder's size and capacity. These motors must be exceptionally powerful to handle the combined strength of fabric, rubber, and metal within the tires.
For high-capacity shredders, the motor operates at low speed and high torque, enabling it to process up to 40 tons of tires per hour. Some models are equipped with dual motors to enhance efficiency and increase shredding force. Shredder motors feature a range of reduced drive gear ratios and may include single or dual electric motors. The key is ensuring the motor can meet the intense demands of tire shredding efficiently while being durable, robust, and long-lasting.
Tires for a tire shredder are loaded into the shredder through the feed hopper. Since the majority of shredders are designed for high capacity and volume, the hopper is configured to meet the demand and can be connected to a conveyor belt or hydraulic ram to control and move the volume of tires. The need for high capacity requires that feed hoppers be exceptionally sturdy and strong.
The control system manages the operation of a tire shredder and monitors its performance. Often integrated into automated shredding setups, it regulates the feed rate in relation to the main drive motor and includes safety interlocks for protection. PLC (Programmable Logic Controller) systems typically feature power on/off controls, overload protection, and reverse controls, along with input and output monitoring to ensure smooth and safe operation.
High-performance shredder control systems feature advanced controls such as lighted buttons, keyed power switches, lockable disconnects, and hour meters. They also include programmable functions like knife reversal for overloads. These systems enhance both the ease of operation and safety of tire shredders, offering exceptional control over the shredding process while being user-friendly and efficient.
The rotor is a crucial component of a tire shredder, driving tires into the cutting zone between the blades. Mounted on the rotor are cutting knives, which are secured to discs. While single-rotor shredders exist, tire shredders typically feature two to four rotors with blades. Operating at 750 revolutions per minute, the rotor is protected by coifs and end disks, which are further shielded by protective caps or hard facings to ensure durability and efficiency in the shredding process.
While standard tire shredders can be installed as complete units, there are various features that can be added to enhance their efficiency and performance. Each manufacturer offers a range of addons designed to improve the shredder's functionality and output. These enhancements help optimize the shredding process and increase overall effectiveness.
Tires are composed of various materials designed to enhance their strength and durability. While early vehicle tires were primarily made of rubber, modern tires now incorporate additional materials to extend their lifespan and improve their toughness.
Tires are primarily made from synthetic rubber, natural rubber, steel, various fibers, and chemicals.
Rubber, steel, fibers, and chemicals significantly impact the tire shredding process. To produce usable crumb rubber for manufacturing, the steel and fibers must be separated from the rubber.
The term tire is a generic term that covers a wide range of tires from ones for family vehicles to ones for construction equipment, loaders, fork lifts, and many other types of heavy equipment including different sizes of trucks.
Farm equipment tires present a unique challenge in tire shredding due to their specific construction. These tires are classified based on their width and diameter ratio, with the width measured from sidewall to sidewall and the diameter corresponding to the rim size. There are two primary types of farm tires: bias and radial, which refer to the tire's construction method. Additionally, farm tires often feature lugs integrated into the tread design to enhance traction, making them more complex to shred.
Common passenger tires are generally categorized into three groups: summer tires, winter tires, and all-season tires. Summer tires are engineered to perform optimally in warm weather, offering strong traction on both dry and wet roads. Winter tires are built to handle cold temperatures and provide excellent grip on icy or snowy surfaces. All-season tires are designed to deliver reliable performance across a wide range of weather conditions.
Additional types of passenger tires include those for recreational vehicles like off-road all-terrain vehicles (ATVs) and sports cars. Off-road tires are built to be durable and tough, suitable for challenging terrains such as dirt roads, sand, and rocky surfaces. While they aren't as robust as farm tires, they share some similar characteristics. Sports car tires, on the other hand, are specifically designed for pavement use, offering exceptional grip and high performance for enhanced driving experiences.
Truck tires vary significantly based on the size and capacity of the truck. Tires for pickup trucks, vans, and mobile homes are quite similar to passenger tires. However, tires for semis, mining trucks, and excavation trucks are much more durable, featuring additional reinforcements to enhance their strength and extend their lifespan.
Shredding truck tires presents a unique challenge due to their inner liner, which is significantly thicker and contains a high halobutyl content to prevent pressurized air from entering the inner chamber and causing degradation. Additionally, truck tires feature much more tread than passenger tires, which is thicker and contributes to the tire's overall strength. To extend their lifespan, heavy-duty truck tires often undergo a process called retreading, where the original worn tread is removed and replaced with new tread. While this process saves on costs, it also increases the difficulty of shredding these tires.
Truck tires contain more steel reinforcement for added durability and protection. The steel cord in truck tires is 8% denser than that in passenger tires, providing additional strength. Additionally, steel ply is incorporated to enhance load-bearing capacity and offer puncture resistance, making truck tires more robust and resilient.
Earthmover tires, unlike passenger and truck tires, are so large that they are measured in feet or meters rather than inches, often standing as tall or taller than a person. These tires come in various sizes to accommodate the heavy equipment they support and feature rugged casings made with cut-resistant compounds and deep treads for enhanced durability and performance.
The primary challenge in shredding earthmover tires lies in their massive size, which demands the use of long rotors, heavy-duty blades, and a hopper large enough to accommodate these enormous tires. Before being placed in the tire shredder, the tires must first be debeaded to remove the steel beading. Due to their size and weight, earthmover tires are typically fed into the shredder using a forklift or other heavy machinery capable of lifting them.
Mining tires, classified as off-the-road (OTR) tires, are engineered to withstand harsh conditions. Unlike standard tires, they are constructed with more durable rubber compounds and advanced manufacturing techniques to handle rugged terrain. A key feature of OTR and mining tires is the increased use of steel in their construction, combined with tougher rubber formulations, making them highly resistant to shredding and wear.
The additional steel in OTR tires can quickly dull or seize shredding equipment, necessitating that these tires be sent to specialized recycling facilities. Mining tires, which can be several meters or feet in diameter and weigh several tons, undergo a preliminary size reduction process before being shredded. Once reduced in size, the pieces are forwarded to shredding plants for further processing.
The PD1000 is a high-torque shear shredder that utilizes solid-state electronics for efficient operation. It is designed for easy transport and can be moved with a one-ton pickup truck. The shredder features a straightforward mechanism for safely and easily replacing used shredder heads with new ones. Paired with the PD1000IO feeder, which rapidly introduces tires into the shredder, the PD1000 is capable of handling automotive tires, light-duty truck tires, and semi-truck treads with the sidewalls removed.
The STQ-100 shredder offers a throughput of up to 5,055 lbs. (2,293 kg) per hour and features an infeed size of 41 inches by 59 inches (1 m by 1.5 m). Its cutting chamber is triple-sealed with abrasion-resistant components and high cutting force knives, reducing noise and vibrations. The design facilitates easy maintenance and repair, with robust bulkhead walls and labyrinth barriers protecting bearings and seals. The heavy-duty shredding knives enable the STQ-100 to maintain high-capacity operation.
The Green Giant is a two-shaft shredder optimized for rubber with low operating and maintenance costs. It processes up to 30 tons (27 t) per hour, producing outputs ranging from 2 inches to 6 inches (5 cm to 15 cm). Powered by two electric motors, it features blade and knife-filled rotors. The shredder includes easily replaceable knife inserts with six cutting edges each, offering an estimated wear life of 2,500 tons per edge. It can handle whole tires up to 48 inches (1,220 mm), debeaded chopped mining tires, and debeaded OTR rough shreds.
TThe HT 250 Hybrid Primary Shredder, the largest model from CM Shredders, excels with a processing capacity of 30 tons per hour. It features high throughput, substantial torque, and knives that are both replaceable and resharpenable. As a primary shredder, it efficiently handles large volumes of tires at high speeds. The knives are bolted directly to a hardened steel rotor, which is easily removable or replaceable. Powered by a 480 V, 3-phase, 60 Hz power source with twin 125 hp drives, the HT 250 is equipped with cameras and sensors that interface with the shredder and conveyance system, allowing operators to monitor and manage the shredding process effectively.
The Grizzly is a medium-speed grinder designed for efficient steel and rubber separation during the grinding process. It features a single rotor for size reduction and an adjustable screen for flexible final product sizing. By producing smaller, consistent rubber sizes, the Grizzly enhances the performance of downstream equipment and allows for the use of the ground rubber in extrusion or molding. It can process various tire types, including car, truck, agricultural, OTR, and mining tires.
Shredded tire rubber is now a valuable resource with various applications in construction, road maintenance, and playground surfaces. Environmental concerns, sustainability efforts, and eco-friendly programs have driven the development of numerous strategies for utilizing this recycled material.
Shredded rubber serves as an alternative to gravel in drainage ditches and highway embankments. The small tire chips help limit frost penetration and are three times lighter than gravel, which reduces labor, equipment, and time costs.
Crumb rubber is utilized in various applications, including the production of asphalt, playground surfaces, mats, and vehicle mud guards. It is also sold as feedstock for chemical devulcanization and the creation of rubber-containing products. In the automotive industry, crumb rubber is used to manufacture bumpers, floor mats, and fender guards.
The pyrolysis process converts shredded rubber into energy, producing oil and gas for heating and electricity generation. This thermal decomposition method uses high temperatures to break down the long-chain molecules in the rubber.
Shredded tires are utilized as liners and covers for landfills, providing thermal insulation between primary and secondary liners to reduce the temperature of waste material. Additionally, this material serves as a cost-effective landscaping tool for landfills.
Shredded tire chips can be cut to uniform sizes for use as filters in wastewater treatment and wetlands. Their easy shapeability and lower porosity compared to organic materials make them a more effective filtering medium.
Shredded tires are used as garden mulch because of their durability and longevity. Unlike wood mulch, shredded tire chips maintain their appearance over time, do not wash away during rainstorms, and do not decompose. Additionally, they are resistant to pests and insects.
The primary goal of tire shredders is to minimize landfill waste and extend the lifespan of valuable rubber, contributing to efforts to reduce pollution and protect the environment. However, despite their ecological benefits, selecting the right tire shredder requires careful consideration to ensure it meets the specific needs of its intended use.
A cardboard shredder is a machine designed to turn cardboard boxes and sheets into small shards or strips. Specialty cardboard shredders are configured to convert cardboard into flexible perforated material for packaging...
An industrial shredder is a piece of heavy duty equipment designed to shred dense and light materials to prepare them for recycling or for the destruction of unusable products. They are an environmentally sound device that...
Scrap metal must be processed to be effectively recycled and ready for reuse. Metal shredders are machines used to process a variety of metal scraps. Metal shredders are frequently used to reduce metal debris to...
A shredding machine is equipment utilized for shredding. Shredding machines are used to reduce the size of materials. While most online sources define the shredding machine as...
A baler is a piece of equipment used to compress solid industrial waste or recyclable materials (e.g., paper, plastic, foam, cans, etc.) to achieve better material handling and storage. Eliminating empty space between individual items of these bulk products is a great way to save costs attributed to storage and transport...
A bowl feeder is a mechanism for supplying small parts and components to a production line or for sorting bulk items for rapid use. A self contained bowl feeder system has a bowl that sets on a spring loaded base that moves vertically...
A cardboard baler is a mechanism that uses a metal plate driven by a hydraulic ram to apply tremendous pressure and force to crush, compact, and compress pieces of cardboard into tightly formed and easy to transport cubes and...
A Trash compactor is a machine or device designed to compress, reduce, and compact a variety of materials through hydraulic, mechanical, or pneumatic force. The initial steps in the compacting process are the collection of the material to be compacted...
Vibratory conveyors are material-handling equipment used to transport fine to coarse-grained bulk materials. These vibratory conveyors are strong conveying equipment utilized for bulk commodities with fine to coarse graininess...
Vibratory feeders are short conveyors used to transport bulk materials utilizing a controlled vibratory force system and gravity. The vibrations impart a combination of horizontal and vertical acceleration through tossing, hopping, or sliding-type of action to the materials being handled...
A vibratory screening is a process that separates bulk solid materials from solids and slurries using inertial vibration that causes various sizes of particles to pass through openings in a screen or...
Modern balers are descendants of hay presses, invented in the mid-nineteenth century, that made it easier to gather and stack hay. The earliest hay presses were stationary units built into a barn and extending two to three stories into the hayloft...