Industrial Mills
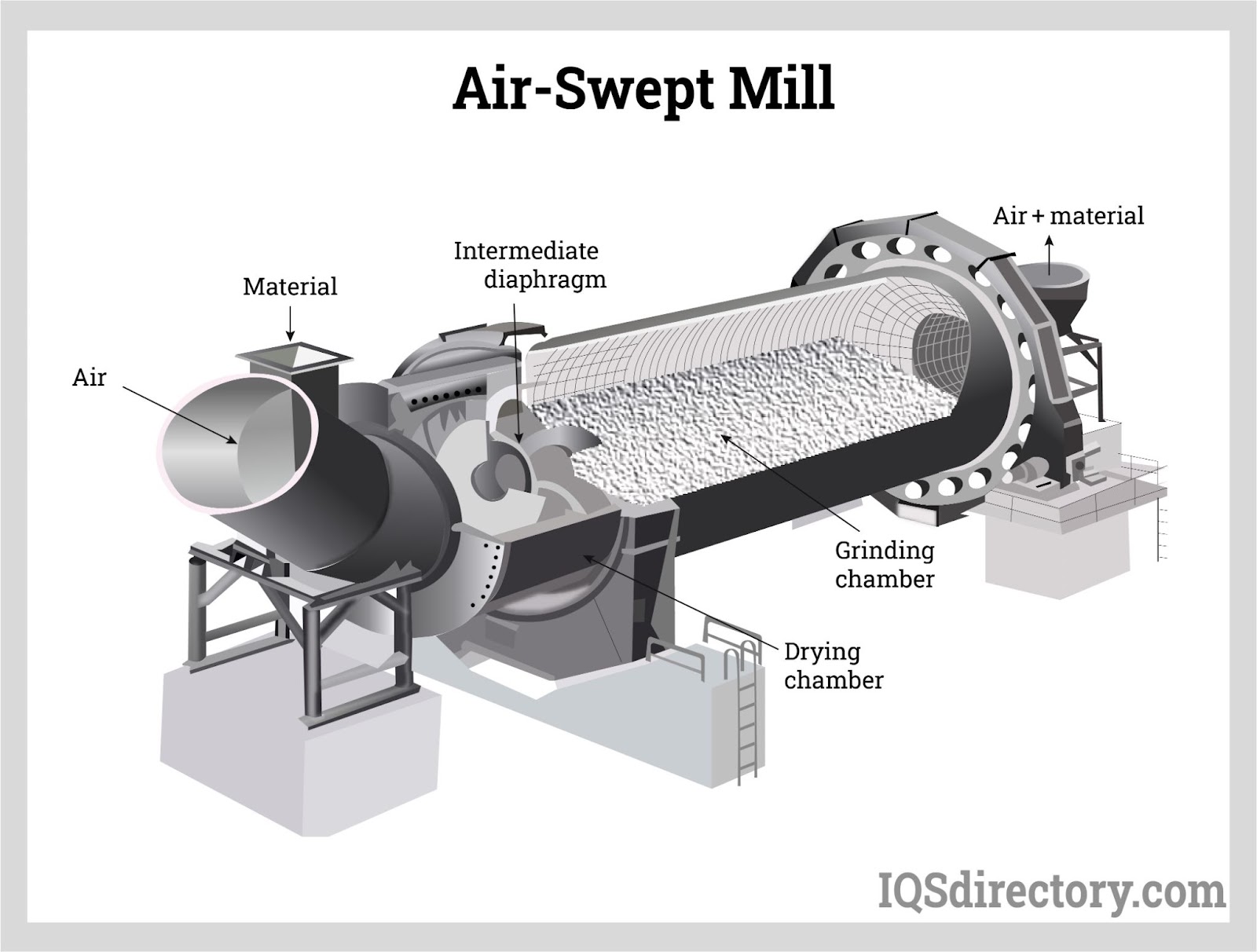
A mill is a mechanical device that is often a structure, appliance, or machine that is used to break down solid materials into smaller pieces by cutting, grinding, or crushing them. Many industrial processes involve...
Please fill out the following form to submit a Request for Quote to any of the following companies listed on
This article will take an in-depth look at size reduction equipment.
The article will bring more detail on topics such as:
In this opening chapter, we delve into the fundamentals of size reduction machinery, encompassing their design, construction, and operating principles.
Size reduction machinery encompasses devices engineered to crush and grind materials, effectively reducing their size. Pulverizers fall under this category, and these terms are often used synonymously. The size reduction process is pivotal in numerous industrial sectors, significantly contributing to various manufacturing and processing activities.
Manufacturers offer size reduction equipment capable of handling a wide range of materials, including coal, shale, brick, concrete, wood, limestone, and plastics. The diverse range of applications and material types necessitates a variety of configurations to efficiently address specific processing requirements.
Each size reduction apparatus is designed for a specific throughput or grinding capacity that aligns with a determined Hardgrove Grindability Index (HGI) value, considering elements such as raw coal volume, targeted particle size, and moisture content. These variables are essential in evaluating the capacity of size reduction equipment. For enhanced performance, pulverizers must maintain proper fuel fineness and airflow, among other critical metrics, to ensure effective boiler combustion. Despite different designs, all size reduction machines share fundamental components, such as grinding media, driven by a motor providing the necessary rotary motion for pulverization.
The frictional force generated within size reduction machinery predominantly arises from grinding media, which can include coarse substances like non-sparking lead, ceramics, brass, bronze, and flint. Moreover, crushers are often fabricated from materials such as steel, stainless steel, or stainless steel with wear-resistant coatings to augment durability and efficiency.
Ceramics are various brittle, hard, corrosion-resistant, and heat-resistant substances manufactured by molding and firing non-metallic, inorganic materials, such as clay, at high temperatures. Common examples include porcelain, earthenware, and brick.
Some elements, like silicon or carbon, can be classified as ceramics. Ceramic compounds resist chemical erosion, beneficial in settings where other materials might degrade due to caustic or acidic environments. They also endure extremely high temperatures, from about 1,832°F to 2,912°F (1,000°C to 1,600°C), making them well-suited for high-temperature grinding applications.
Modern advanced ceramics, such as tungsten carbide and silicon carbide, are prized for their outstanding abrasion resistance. These materials find frequent use in scenarios like wear plates in size reduction machinery, crucial in mining operations where durability against wear is vital.
Non-sparking lead is devoid of ferrous metals (iron and steel), meaning it does not produce sparks while grinding. Lead is renowned for its high ductility, density, and malleability. Despite being a poor conductor, it is highly corrosion-resistant, providing notable durability.
Brass, an alloy of zinc and copper, is engineered by altering the metal proportions to achieve specific electrical, chemical, and mechanical properties. It shares similarities with bronze, another copper alloy, but bronze incorporates tin instead of zinc. Both brass and bronze may contain traces of other elements like lead, arsenic, phosphorus, aluminum, silicon, and manganese. Brass is particularly used in applications necessitating corrosion resistance and minimized friction, especially where spark reduction is essential, such as milling machines.
Bronze, primarily containing copper and about 12 to 12.5% tin, might also include additional metals like aluminum, nickel, zinc, or manganese and metalloids or nonmetals like silicon, phosphorus, or arsenic. These alloying components enhance hardness, ductility, strength, and machinability compared to pure copper, making bronze ideal for size reduction equipment. Additionally, unlike steel, bronze does not generate sparks upon impact with other materials.
Flint, a type of sedimentary crystalline quartz, is categorized as a variant of chert, frequently found in marly limestone or chalk. It usually appears in colors like black, dark gray, green, brown, or white, often possessing a waxy or glassy surface. Flint pebbles serve as grinding media in ball milling in the ceramics industry. Hand selection of these pebbles based on color, such as blue-gray pebbles, is due to their low chromophoric oxide content, reducing influence on the color of ceramics after firing.
Steel, an iron alloy with slight carbon content, boosts strength and fracture resistance over pure iron. The added durability of steel results from decreased ductility. Steel is formed into various shapes, like balls or bars, for use as crushing media in size reduction scenarios.
High carbon steel bars can be employed as an alternative to balls in these machines, delivering consistent fine output and operating with low energy input. However, they are less suited to very hard materials, performing best with sticky substances that may cause ball clumping; the heavier bars help disperse these clumps and ensure effective grinding of granular materials.
Pulverizers process materials in a continuous or batch mode, receiving materials via conveyor belts, subsequently crushing and grinding them through rotating devices. Once processed, the materials exit through discharge outlets. Additionally, pulverizers might possess features to heat, cool, or ventilate materials during or subsequent to the grinding process.
Several considerations should be borne in mind when picking size reduction machinery:
If the initial sample particle size is coarse, employing two separate reduction machines may be necessary: one for primary reduction and another for fine grinding to attain the targeted analytical fineness.
The choice of proper grinding tools is critical when selecting size reduction machinery appropriate for a material. Considerations should encompass abrasion resistance, hardness, energy input, and the risk of contamination.
The different types of size reduction equipment are:
Pulverizers can be used in applications such as pulp creation in paper production, turning soil, crushing scrap, tire shredding, and recycling. The pulverizers are usually categorized as impactors, crushers, or grinding mills. Impactors, which are also known as impact crushers, use impaction, which is a force transmitted via a collision or two bodies striking each other. Crushers use pressure generated by two forces opposing each other. Crushers are used to reduce the size of large, dense materials like rocks into dust. Grinding mills break down materials using friction which is a result of grinding media. Such media can be coarse materials like ceramics, flint, non-sparking lead, and brass.
The following sections provide an overview of various types of pulverizers:
Ball mills are industrial crushing machines that are categorized by their usage of a loose crushing medium. Ball mills are one type of size reduction machine. Ball mills, together with impact crushers, grinding mills, and a range of other tools, are utilized for the reduction of all varieties of objects for all varieties of purposes.
Size reduction plays a crucial role in many industrial processes, making ball mills and similar mechanisms essential and highly sought after. In processes involving the mixing of materials, achieving smaller particle sizes simplifies and enhances the thoroughness of the mixing.
Ball mills are particularly useful in metal alloying processes, as they can grind and crush materials into very fine granules, facilitating easier combination. They are also employed for reducing the particulate size of cement, black powder, silicates, fertilizers, and various non-ferrous and ferrous metals. The operational concept and construction of ball mills are similar to rock tumblers, which use a milling medium to polish stones in a revolving cylinder.
Ball mill machinery generally consists of a motor, a cylinder, and a crushing medium. The crushing occurs within the cylinder, where the material to be ground is combined with the crushing media. This media can include materials such as steel, lead-antimony alloys, ceramics, or flint. As the cylinder rotates, the crushing medium is agitated, causing it to impact and break down the material.
Once the material is sufficiently reduced to fine particles, it can be discharged from the cylinder and replaced with new material for further processing. This process can be continuous or batch-wise. Continuous ball milling involves the automatic loading of materials and unloading of crushed products, while batch milling involves processing materials in discrete batches. Ball mills vary in size from small, bench-mounted units to large machines that occupy entire rooms, depending on the scale of the operation.
Crushers are tools constructed to reduce big waste materials for easy recycling or disposal. One of the most prevalent types of size reduction equipment, crushers are commonly utilized to reduce the size of big rocks, turning them into easily manageable rock dust, small rocks, or gravel. Crushers can break apart or compress soft objects such as gypsum, phosphate, and limestone to very hard objects such as asphalt and ore.
There are various types of crushers, including gyratory crushers, cone crushers, and jaw crushers. Gyratory and jaw crushers are effective for both hard and soft materials and are commonly used in mining to crush large quarried materials such as ore. In the construction industry, these crushers help reduce large building materials like concrete and stone. Additionally, they are used in industrial manufacturing for processing large, dense objects.
Cone crushers are best suited for medium to very hard materials and are valuable in several industries. In the metallurgical sector, they process large, inert granular materials from mining operations involving metals like copper and iron ore. They are also employed in road construction for crushing building materials such as concrete and asphalt. In the chemical industry, cone crushers help break down minerals like silicic acid and phosphate. Beyond these, crushers are utilized in automotive, demolition, smelting, and manufacturing industries.
Crushers function by breaking apart or compressing materials through the application of mechanical force. This force is exerted by surfaces stronger than the material being crushed, which are kept between parallel plates. The crushers apply sufficient force to these surfaces to deform or fracture the material. While all crushers rely on the principle of compression, they operate differently. Jaw crushers are easily recognizable due to their vertical "jaws," with one fixed and the other movable, generating the compressive force needed.
Gyratory crushers are similar to jaw crushers but feature a conical head and concave surface. Their operation is based on an eccentric motion. Cone crushers resemble gyratory crushers but have a more pronounced conical shape, with a large top inlet for large materials and a small bottom outlet for the crushed material. Cone crushers work by crushing materials between a concave hopper and an eccentrically rotating spindle, which are both lined with wear-resistant material.
Grinding mills are designed to reduce large quantities of solid materials into finer particles. These mills can handle a variety of substances and operate using different methods. Historically, grinding mills were powered by animals, windmills, and waterwheels. However, modern industrial grinding mills are highly advanced, capable of performing more demanding and intensive tasks.
Grinding mills are utilized across various industries. For example, in gristmills, they are used to grind grains such as maize. Ball mills are commonly employed in power plants to mill coal or to produce black powder for fireworks. Similar grinding methods are used for crushing ceramic materials and paint pigments.
Grinding mills operate with a rotating cylinder in which the materials to be ground are loaded. This cylinder is equipped with a grinding medium that crushes the materials as the cylinder turns. Grinding mills come in various sizes, from compact models suitable for workbenches to large units that can occupy entire rooms. Different types of grinding mills include hammermills, ball mills, roll crushers, and jaw crushers.
An impactor is a type of size reduction machine that utilizes impact forces to break or deform materials, rather than relying solely on shear pressure. Impact involves the force generated by the collision or striking of one object against another. Crushing occurs due to the pressure exerted by these opposing forces during the impact process.
Impalers, often referred to as impact crushers, are commonly used for secondary size reduction rather than primary. They can process a wide range of materials but are particularly effective for non-abrasive, soft substances like gypsum, phosphate, soft metallic cores, seeds, and coal. They can also handle abrasive, hard materials such as gravel, basalt, asphalt, and concrete, though they perform best with materials of medium hardness.
Impactors are utilized across various industries. In bridge and road construction, they are used for crushing building materials. In mining, they process quarried and mined materials. They are also employed in industrial manufacturing for processing different materials before further use. Additionally, in water conservancy, impactors are used to handle inert granular materials for various applications.
There are two main types of impactors: vertical shaft impactors (VSIs) and horizontal shaft impactors (HSIs). HSIs are equipped with curtain liners, adjustable liner plates, and impeller bars. The impact process begins when materials reach the breaker plate, where fixed hammers on the outer edge of a rotating rotor apply force. All impactors feature a metal cage to contain the materials and outlets at the base to release the crushed particles once they reach the desired size. HSIs are less suitable for abrasive, hard materials and are more effective for softer materials like dolomite, aluminum, weathered rock, and clay. VSIs, while similar in design to HSIs, include a crushing chamber designed to throw materials against a surface and a high-speed rotor that uses velocity to impact the materials. This design results in higher efficiency and power, making VSIs better suited for harder materials such as metallurgical slag, quartz, magnesium sand, bauxite, and limestone.
Jaw crushers are size reduction machines that utilize a combination of crushing jaws and gravity to break down materials. Named for their jaw-like structure, these crushers are crucial in various industrial processes. They play a significant role in recycling and waste management by compressing trash, in mining operations for breaking down large boulders, and in demolition or construction projects for managing and disposing of materials.
Pulverizer manufacturers have developed a variety of crushing and pulverizing equipment to meet the diverse needs of different industries. Jaw crushers, which come in various sizes and capacities, generally occupy a mid-range position among crushers. Some models are designed for portability, such as those commonly used in mining, and are typically about the size of a storage shed.
A jaw crusher operates by moving a movable plate towards and away from a fixed plate. These plates are positioned at an angle within a vertical channel. As materials are fed into the channel, the movable plate oscillates, crushing the materials against the fixed plate. The crushed materials are then released from the channel as the movable plate retracts. Jaw crushing is a multi-stage process because of the angled plates: larger objects are initially crushed at the top of the channel and progressively broken down as they move downward. Although jaw crushing is less precise compared to other methods, such as grinding or hammer mills, which repeatedly grind materials to produce finer particles, it remains an effective and valuable method for certain applications when matched appropriately with the desired outcome.
A stone crusher is a type of size reduction equipment designed to break down or compress large stones. Known for their high output and significant crushing capacity, stone crushers are used both as primary crushers and in secondary or tertiary stages of crushing. They are employed across various industries, including energy, transportation, petrochemical refining, and industrial manufacturing.
Stone crushers are designed to handle a diverse range of materials, from soft minerals to very hard stones. These materials include limestone, slag, quartz, granite, sandstone, copper ore, iron ore, cement, marble, and more. Given their versatility, stone crushers are widely used in industries such as mining, where they crush quarried and mined stones. In metallurgy, they break down large stones into smaller sizes for further processing. Stone crushers are also employed in processing chemicals and recycling construction rubble. Additionally, they help in clearing debris from demolished structures like roadways, buildings, canals, and bridges.
Several types of crushers are used for stone crushing, including cone crushers, jaw crushers, impact crushers, and hammer crushers. Jaw crushers operate by using two "jaw-like" surfaces: a mobile jaw and a fixed jaw. The mobile jaw moves to crush stones against the fixed jaw, facilitating size reduction through compression. Cone crushers, with their conical shape, crush stones by squeezing them between a concave hopper and a rotating spindle, which is powered by an eccentric mechanism. Both components are protected by wear-resistant materials to handle the impact of crushed stones.
Hammer crushers, often used as secondary crushers, feature swinging arms mounted on a rotating shaft that strike the stones against an iron cage. A screen below the crusher allows finer pieces to pass through. Another type of hammer crusher, known as a hammermill, operates with reversible hammers and can run in both directions. Impact crushers break stones through impact forces and come in two main varieties: vertical shaft impactors (VSIs) and horizontal shaft impactors (HSIs).
A grinder, commonly referred to as a grinding machine, is a power tool designed for grinding materials. This machine utilizes an abrasive wheel to cut and shape materials. As the wheel rotates, each abrasive grain on its surface removes small amounts of material through a process of shear deformation.
Grinding is employed to achieve a high level of surface quality and precision in materials, providing a smooth surface with minimal roughness and accurate dimensions. With grinders capable of achieving size tolerances on the order of 25 × 10-6 mm, they are primarily used as finishing tools, removing very small amounts of material, typically between 250 µm and 500 µm. However, grinders are also used for more aggressive material removal in roughing applications, demonstrating the versatility of grinding processes.
A grinder consists of a bed that supports and guides the material, along with a power-driven wheel that spins at the required speed for grinding. The wheel's speed is determined by its manufacturer’s specifications and diameter. The grinder’s head can either move across a stationary object or allow the object to move while the grinder remains fixed in place.
Granulators are specialized machines designed to break down materials into granular form. Unlike grinders or shredders, which handle smaller reductions, granulators are capable of reducing larger materials to a finer size, often smaller than what grinders can achieve. They typically feature an open rotor design, allowing air to circulate freely and cool the material. In contrast, closed rotor granulators operate at high speeds, producing particles that can be as fine as maize meal or even smaller, with sizes ranging from 0.008 to 0.16 inches (0.2 to 4 mm).
There are two main types of granulation: wet and dry. Wet granulation involves adding a liquid to a powder mixture, which is then combined using screws, impellers, or air to form granules. Common liquids used include ethanol, water, and isopropanol, with water-based solutions being preferred for their safety. Dry granulation, on the other hand, forms granules without the use of liquids, making it suitable for materials sensitive to heat and moisture. This process often involves compactors to achieve the desired granule size.
Granulators play a crucial role in recycling processes, especially for lighter materials like rubber and plastics that are difficult to grind effectively. They are essential for transforming these materials into a form suitable for further processing or reuse.
Rotor mills are employed for the fine reduction of various materials across multiple applications. They are effective for processing a range of substances, including hard, soft, and fibrous materials, as well as temperature-sensitive samples like those cooled with liquid nitrogen. In agriculture, rotor mills are used to reduce the size of plant materials, fertilizers, wood, seeds, tobacco, and straw. Additionally, in the plastics and chemical industries, rotor mills handle materials such as synthetic resins, super-absorbent polymers, rubber granulates, powder coatings, activated charcoals, and various plastics.
Rotor mills are typically powered by motors and can operate at various speeds. They are equipped with safety casings to protect the electrical components and motor from material and dust infiltration. The sieves used in rotor mills often feature round or trapezoidal holes of varying sizes, typically ranging from 0.003 to 0.4 inches (0.08 mm to 10 mm). Additionally, options are available for rings and rotors with reinforced rims, which enhance the stability of the sieve during operation.
Briquette machines use pressure and force to convert metal waste and powder into compact bricks or blocks, making them easier to transport or use as raw materials in manufacturing and production. A briquette system can handle various materials, provided they have the appropriate size, moisture content, and compatibility.
Central to the briquetting process is the binder, which binds the raw particles together and ensures sufficient strength when formed into bricks or blocks. The type of binder used must be compatible with the chemical properties and characteristics of the material being processed.
Different types of machines generate the pressure required for briquetting. Screw-type briquette machines use an auger to press the raw material and may include a heating element. Hydraulic briquette systems, known for producing high pressure, are versatile and can handle a wide range of materials.
Other briquette machines include piston types and roller types. Piston-type briquette systems use a piston driven by rotary or hydraulic power to compress the material into briquettes. Roller-type briquette systems press the raw material between two rollers with slots or holes, shaping the material into briquettes as the rollers rotate.
Briquette machinery provides an effective solution for managing and recycling various types of waste that are difficult to handle in their original form. By applying force and pressure, briquette machines transform materials into solid masses that are easier to manipulate and store.
Draining presses are used to empty beverage containers, milk cartons, and food cans of their leftover contents. These presses compact the containers into discs for easier recycling, while the extracted liquid is either disposed of or saved for reuse. Draining presses have been employed for many years by wastewater treatment facilities to separate solid waste from liquid waste. In industrial settings, they are used to remove impurities and solid waste from industrial wastewater.
The draining press process involves applying pressure to waste containers with liquids or to wastewater containing solid matter. Dewatering, or the removal of liquid, is achieved by exerting pressure on the water or containers. Traditional draining presses use plate and frame systems to squeeze out fluids.
Draining presses are capable of compressing and draining a variety of liquid-containing materials, such as boxes, cans, plastic bottles, and food containers. They efficiently empty containers of liquid waste, making the contents available for reuse or compressing them for disposal.
This chapter will explore the applications and benefits of size reduction equipment.
Stone crushers are built on a robust foundation, allowing for scalability. They are ideal for mines with high processing capacities due to their long service life. These machines offer high surface finishes and can handle hard materials with minimal pressure during operation, achieving precise measurements even at elevated temperatures.
Jaw crushers feature a straightforward structure that simplifies operation and maintenance. They are equipped with an efficient lubrication mechanism and offer a cost-effective solution compared to other stone crushers.
Rotor mills are well-suited for fine batch milling of large quantities, with adjustable speeds for various applications. They are easy to clean, thanks to removable components such as rotors, grinding inserts, and cassettes. Made of stainless steel, their feed hoppers, grinding chambers, and material inlets and outlets ensure the production of very fine powders. Rotor mills are also ideal for milling toxic substances in a fully enclosed environment.
The significant pressure and force involved in industrial pulverizers increase the risk of operator injury if safety precautions are not strictly followed. To mitigate this risk, safety measures such as shields, guard rails, automatic shut-off controls, and sensors should be employed. When these safety features are properly implemented, regularly maintained, and operated by trained personnel, size reduction machines can perform effectively and safely, playing a crucial role in many industrial processes.
Key safety standards for handling size reduction equipment include:
Maintenance of size reduction equipment includes:
Preventive maintenance involves scheduling regular checks, inspections, and servicing according to the equipment manufacturer’s recommendations. Regular inspections and adjustments should be performed, and worn-out parts replaced before major breakdowns occur. This proactive approach is crucial for maximizing the equipment’s lifespan and ensuring reliable operation.
Predictive maintenance monitors the conditions of reduction while the equipment is running. This is achieved by using predictive maintenance tools like lubricating oil thermometers or temperature sensors, gauges or lubricating oil pressure sensors, lubricating oil filter condition indicators, lubricating oil tank return screen, and downtime.
Size reduction equipment is machinery that crushes and grinds materials to reduce their size. Size reduction equipment typically falls into three main types: impactors, crushers, and grinding mills. The grinding and crushing media in this equipment is usually steel, bronze, and brass. All such equipment must be operated by trained personnel. Preventative and predictive maintenance goes a long way in prolonging the life of size reduction equipment.
A mill is a mechanical device that is often a structure, appliance, or machine that is used to break down solid materials into smaller pieces by cutting, grinding, or crushing them. Many industrial processes involve...
Agitators are equipment used in homogenizing media inside a tank. It works by rotating the impeller at its immersed end at a controlled speed or revolutions per minute (rpm). The work exerted by...
A belt conveyor is a system designed to transport or move physical items like materials, goods, even people from one point to another. Unlike other conveying means that employ chains, spirals, hydraulics, etc...
A cardboard shredder is a machine designed to turn cardboard boxes and sheets into small shards or strips. Specialty cardboard shredders are configured to convert cardboard into flexible perforated material for packaging...
A conveyor system is a method for moving packages, products, supplies, parts, and equipment for production, shipping, or relocation. The different types of conveying systems include pneumatic, screw, belt, and roller. The construction of individual systems depends on the materials...
High shear mixers, also known as high shear reactors (HSRs), rotor-stator mixers, and high shear homogenizers, are used to emulsify, homogenize, disperse, grind and/or dissolve immiscible mixtures with components of the same or different phases...
A homogenizer is a type of mixing equipment used to create a uniform and consistent mixture. It works by breaking the components and evenly distributing them throughout the solution. The components are either immiscible, have varying sizes, or are in different phases from each other...
An industrial blender is a machine for large-scale production that consists of a large tank capable of mixing and blending batches of manufacturing materials to create a reaction between the materials. The many uses for industrial blenders are due to their capacity and...
An industrial shredder is a piece of heavy duty equipment designed to shred dense and light materials to prepare them for recycling or for the destruction of unusable products. They are an environmentally sound device that...
Pneumatic conveying is a method for transferring bulk materials, like powders and granules, using compressed gas or air, from one processing center to another. Material is moved through an enclosed conveying line or tube using a combination of pressure differential and airflow from a blower or fan...
Roller conveyors are a type of conveyor belt that allows objects to skate on its surface by using rollers, which are equally spaced revolving cylinders. They transport stuff from one location to another...
Screw conveyors, or auger conveyors, are industrial equipment used in transporting bulk quantities of granular solids (e.g., powder, grains, granules), semi-solids, liquids, and even non-flowing materials from one point to another...
A shredding machine is equipment utilized for shredding. Shredding machines are used to reduce the size of materials. While most online sources define the shredding machine as...
A vertical conveyor is an engineered mechanical method for moving goods, products, supplies, parts, and components from a lower level to a higher level or from a higher level to a lower level. They are...
A mixer is a complex and precise tool that is used in combining and mixing of substances and chemicals for manufacturing, production, and industrial use. There are many types of industrial mixers including...