Compression Springs
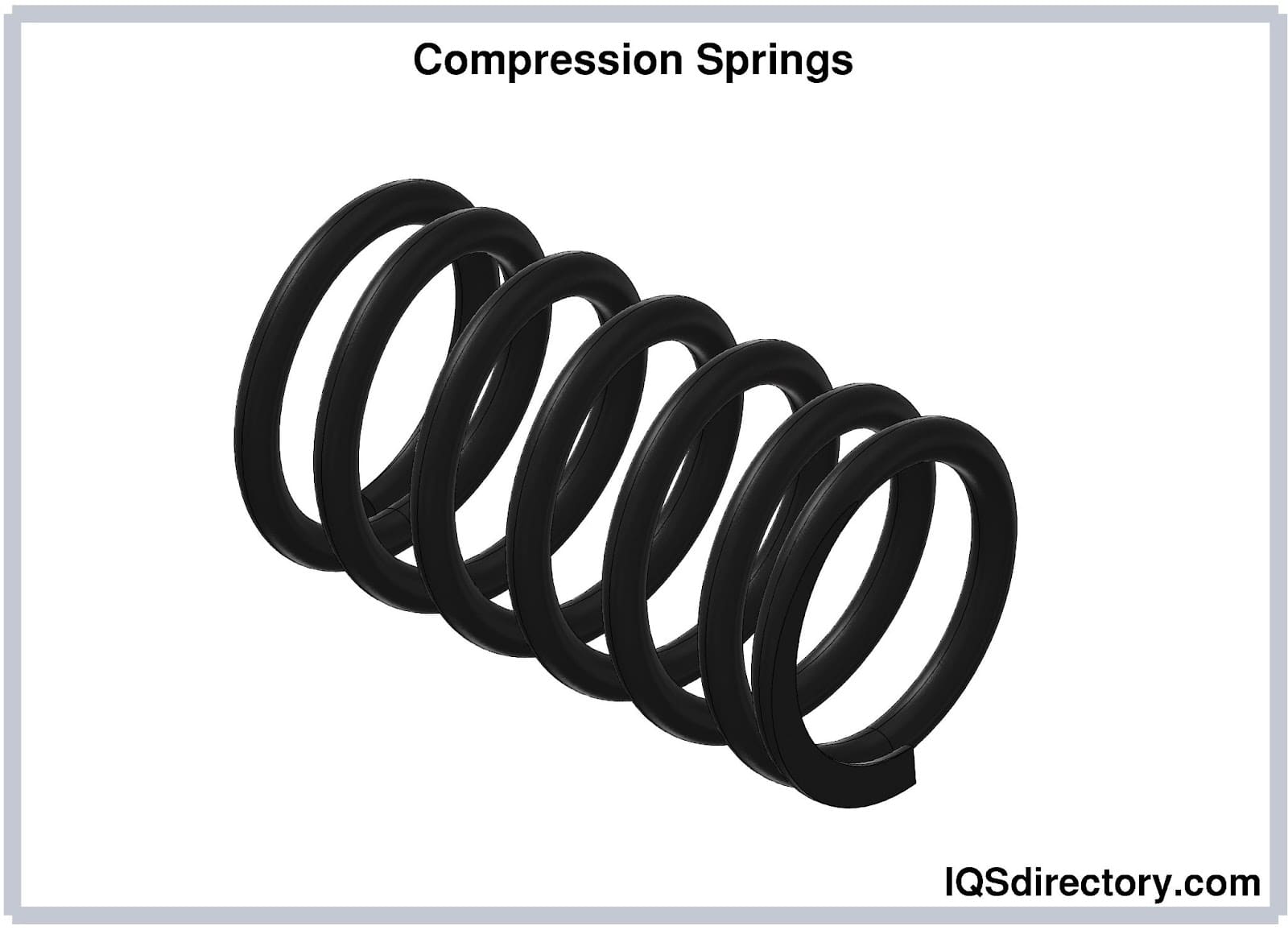
Coil springs called compression springs can store mechanical energy when they are compressed. These open-coiled, helical springs provide resistance to compressive loading. When these springs are...
Please fill out the following form to submit a Request for Quote to any of the following companies listed on
This article takes an in depth look at coil springs and their materials.
You will learn more about topics such as:
A coil spring is a helical mechanical element made by winding metal into a spiral form. It functions to store potential energy, which it then uses to mitigate shock. These springs are manufactured by twisting metal wire into a continuous helix, transforming the wire into an energy-storing component.
Available in various sizes, coil springs are engineered to reduce impact and stress on different surfaces. They achieve this by providing flexibility that allows them to deform under external stress and then bounce back to their original shape once the stress is lifted. During compression, the spring holds energy and releases it when returning to its initial form. The energy stored is proportional to the force applied.
When subjected to weight, coil springs compress, storing mechanical energy by reducing in size. After the weight is lifted, the spring expands, releasing the stored energy as it returns to its original state.
Coil springs can be classified into three main categories: compression, extension, and torsion, each serving a unique function. Among these, compression springs are the most prevalent. They are typically produced by hot or cold winding of spring steel and are engineered to absorb force and resist compression.
Coil springs may be prone to corrosion and environmental degradation, potentially causing early failure. To improve endurance, they are frequently coated with substances such as powder, epoxy, or polyester. Additionally, some springs are electroplated with zinc or nickel to enhance their protective capabilities.
Coil springs are elastic components designed to store and release mechanical energy, and they can be made from various materials selected based on the spring's design. They come in two main types: close wound, where the coils are tightly spaced and touch each other, and open wound, where the coils are spaced apart at the ends.
The choice of material and manufacturing process for coil springs varies depending on the production scale. Small production runs are typically completed using a lathe, while high-volume production is done with automated coiling machines or computer numerical control (CNC) equipment.
Coil springs are commonly made from various metals, including high and medium carbon steel, chromium vanadium steel, chromium silicon steel, various grades of stainless steel, copper alloys, and nickel. The selection of metal depends on the specific application of the coil spring. Additionally, since coil springs can be made from different forms of metal, the material used may vary to suit the type and design of the spring.
In some cases, metals are supplied as bars, which are then heated and drawn into wire of the required diameter for spring production.
Heat Treatment – Cold winding begins with heat treatment of the wire or working to reach its highest strength level. The process of cold winding can only work with wires that have a diameter of 0.75 inches or 18 mm or less.
Mandrel – A mandrel is one of the two primary methods for manufacturing coil springs. This process can be carried out using a lathe, winding machine, or hand crank machine. During production, a guide mechanism ensures that the wire is aligned correctly to achieve the desired pitch, which is the spacing between the coils as they are wrapped.
Computer Numerical Control (CNC) – CNC spring coiling machines are advanced and sophisticated compared to traditional mandrel systems. These machines use a series of components to precisely feed, wind, and shape the coils with high efficiency and accuracy.
The entire process and its components are illustrated in the diagram below.
Wire – For hot coil winding, the wire can be relatively thick, ranging from 3 inches (75 mm) to 6 inches (150 mm) in diameter. During hot winding, the wire is heated to around 1700°F, allowing manufacturers to work with larger diameter wire.
Mandrel – In the mandrel process, heated metal is coiled around a mandrel similarly to cold coiling, but with increased precision. The rotation of the mandrel and the pitch distance are controlled by a CNC machine.
Cooling – Following hot coil winding, the next critical step is to cool the wound coil rapidly through a process called quenching. Various methods are used for quenching steel parts, with oil being a common choice. This cooling process is essential for hardening the coil’s steel and preventing the development of thermal and transformational gradients that could cause cracking.
Quenching alters the crystalline structure of the metal, locking in changes and increasing hardness. Initially, a vapor blanket forms around the part as the first cooling stage. This blanket is then displaced by heating the quenching medium, followed by the convective stage, which continues to remove heat and cool the part.
Quenching oil is favored for its rapid cooling capabilities compared to other methods. The quenching process requires meticulous monitoring to ensure that the final coiled spring meets performance expectations.
During spring manufacturing, the wire is stretched and coiled under force to form the spring shape. This process disrupts the natural balance of the metal's molecules, leaving the spring with residual stress. If not properly managed, this residual stress can lead to defects, cracks, and a reduced lifespan. Stress relief is used to restore the equilibrium of the metal molecules in the spring.
Stress relief is achieved by heating the spring to a temperature below its deformation point, making the wire malleable without melting it. After heating, the spring is gradually cooled back to room temperature, allowing the molecules to realign.
Alloy steels like chrome silicon or chrome vanadium undergo stress relief between 700°F and 800°F (371°C and 426°C). Chrome silicon, due to its high tensile strength, requires a stress relief duration of one hour or more. Similarly, stainless steel 17-7 is stress relieved at 900°F (482°C) for over an hour. Stress relief at higher temperatures and for extended periods significantly reduces internal stress in the spring.
The finishing process for a coiled spring depends on its design requirements, including its shape, coating, pitch, and strength.
Grinding – Grinding is often needed to flatten the ends of a spring to meet its design specifications. This can be done either manually or automatically. In manual grinding, the spring is secured in a jig and ground with an abrasive tool. Automated grinding involves the spring being held in place while both ends are ground according to programmed settings. Lubrication is used during grinding to keep the metal cool and remove debris.
Grinding is frequently necessary to ensure the spring fits properly into its application and can sit flat. This process allows the spring to be positioned upright as required.
Shot Peening – Shot peening consists of impacting the surface of the coiled spring with shot, small round metal balls, glass, or ceramic particles. The impact of the many shots produces a compressive stress layer and changes the coil springs mechanical properties. The barrage of shots smooths the surface of the spring and compresses it.
Set Pitch and Length – To adjust the pitch and length of a spring, it is compressed until the coils make contact. This process may need to be repeated until the desired dimensions are achieved. Measuring the pitch can be challenging. A preliminary estimate can be made by measuring the distance between the spring's loops, but this method is less accurate. For a more precise measurement, a spring pitch formula, available through computer programs, should be used.
The length and pitch are illustrated in the diagram below. There are differing opinions on measuring pitch for coil springs. Some experts argue that specifying the number of active coils provides a more accurate representation than pitch alone.
Applying Coatings – Coatings are used to protect springs from corrosion, as the metals commonly used in spring manufacturing are susceptible to environmental damage. Various methods are employed to cover the entire surface of the spring, including spray painting, rubber dipping, or electroplating with zinc or chromium.
Coil spring ends come in four common forms: closed, open, square, and pigtail. Selecting the appropriate end type is crucial for fitting the spring to its specific application.
The closed end variant is the most prevalent. In this design, the spring’s end pitch is flat, with the tip making contact with the adjacent coil. This design ensures that the coil spring remains stable and can stand upright independently.
Square end coil springs are a subtype of closed end springs, where the end is ground to a square shape. These springs typically offer greater deflection compared to open end springs.
Open end coil springs feature a continuous pitch, extending to the end. Often called tangential coil springs, they are used in applications where the spring needs to rest on a surface, such as in automotive settings. For an open end coil spring to be functional, it must have a designated seat to support it.
A pigtail coil spring has a last coil with a smaller diameter than the other coils. This smaller diameter allows the pigtail end to be attached to mechanisms using screws or bolts.
The initial step in coil spring manufacturing is selecting the appropriate metal for fabrication. A key factor in this selection is the tensile strength of the metal, which must meet the application's requirements. Most springs are made from steel alloys due to their availability and cost-effectiveness, though copper and nickel alloys are used for certain specialized applications.
The chosen metal must be capable of holding and releasing mechanical energy over an extended period without failure. High-quality coil springs are characterized by their ability to exert force between surfaces and to effectively absorb shock and stress.
High carbon steel is widely used for manufacturing coil springs due to its strength, durability, and cost-effectiveness. This steel is available in 1045 and 1095 alloys and contains 1% carbon along with 0.9% manganese. Its very fine pearlite layer structure contributes to its hardness and brittleness, making it less ductile.
Music Wire – Also known as piano wire, music wire is regarded as the toughest material for coil springs. It is a high carbon spring steel characterized by its uniformity, high tensile strength, and ability to endure stress from repeated loadings. Music wire offers excellent temperature resistance and is commonly used in environments with extremely high temperatures, such as in foundries and refractories.
Chromium vanadium steel is known for its remarkable strength and flexibility. When utilized for coil springs, its medium carbon content imparts toughness and wear resistance. The inclusion of vanadium enhances its machinability, reducing the risk of breakage during shaping. Chromium vanadium steel is heat-treated during processing to improve its wear and fatigue resistance, making it suitable for high-stress environments with moderately elevated temperatures.
Chromium silicon steel is recognized for its exceptional hardness and capacity to endure high stress. Its durability and heat resistance make it suitable for applications at temperatures above 275°F. Originally developed for coil springs in anti-aircraft weapons, chromium silicon steel is designed to handle significant shock loads.
When discussing stainless steel, it's essential to specify the grade, as each has distinct properties tailored for particular applications.
Stainless Steel 302 is the most widely used stainless steel for coil springs. It is particularly effective in environments exposed to moisture or corrosive elements. Stainless Steel 302 can withstand high temperatures up to 550°F or 228°C. Among the stainless steel grades, it is the softest and most flexible while still maintaining high tensile strength.
Stainless Steel 316 is one of the cleanest stainless steels and has all of the other properties of resistance to moisture and can resist the effects of high temperatures. Although it has positive qualities, it is the weakest of the three types of wire used to produce coil springs.
Stainless Steel 17-7 offers excellent resistance to moisture and corrosion, and it is stronger and harder compared to 302 and 316 grades. Its increased hardness allows for the production of coil springs with enhanced force and stiffness. Stainless Steel 17-7 can withstand temperatures up to 650°F or 343°C.
Silicon manganese steel enhances the steel's hardness, manages its decomposition during tempering, and strengthens its ferrite structure. Manganese further increases the steel's hardness and minimizes decarburization. Coil springs made from silicon manganese steel are hot-formed at 900°C, achieving a hardness of 225 BHN. These springs are commonly used in torsion bars, railway cars, automobile leaf springs, and stabilizers.
Copper-based spring alloys are valued for their excellent electrical conductivity and high resistance to corrosion. However, their additional beneficial properties make them more costly. These alloys are commonly used in electrical components and in environments with extremely low temperatures.
Beryllium Copper stands out for its electrical conductivity, corrosion resistance, and superior mechanical strength, offering higher tensile strength and good fatigue resistance compared to other copper alloys. It maintains its ductility even under cryogenic conditions. The non-magnetic nature of beryllium copper makes it particularly suitable for medical applications, such as MRI machines, and for industrial uses like directional drilling equipment.
Phosphorus Bronze is an alloy of copper, tin, and phosphorus that offers superior corrosion resistance and strength compared to other copper alloys, thanks to the addition of tin. The phosphorus enhances wear resistance and increases the stiffness of coil springs made from this material. Phosphorus bronze coil springs exhibit excellent strength, good fatigue resistance, and machinability. They are commonly used in marine fuel pumps, oil rigs, and oil pipeline valves.
Nickel-based alloys are favored for coil spring production due to nickel's exceptional corrosion resistance and its capacity to endure both extremely high and low temperatures. These alloys are non-magnetic, making them suitable for use in gyroscopes, chronometers, and various indicator instruments. Additionally, they resist the effects of electrical currents and are poor electrical conductors. Nickel-based spring alloys typically have a Rockwell Hardness ranging from C35 to C48.
Below are some common nickel-based spring alloys:
Inconel X750 is a nickel-chromium alloy known for its high strength at temperatures up to 1300°F (740°C) and its oxidation resistance at temperatures up to 1800°F (982°C). It also exhibits excellent resistance to relaxation.
Inconel 600 is a nickel-chromium-iron alloy known for its exceptional resistance to corrosion and oxidation. It maintains excellent strength at high temperatures and is particularly resistant to chloride stress cracking due to its high nickel content. Inconel 600 also withstands attacks from both inorganic and organic chemicals and performs effectively at temperatures as low as –300°F. This alloy is used in applications requiring a tensile strength of 220 Ksi, and the coil springs made from Inconel 600 are typically cold worked.
Inconel 625 is an alloy composed of nickel, chromium, molybdenum, and niobium, which impart exceptional corrosion and oxidation resistance, along with high strength at elevated temperatures. The strength of Inconel 625 is largely attributed to its molybdenum and niobium content. Similar to Inconel 600, it also resists chlorine stress corrosion cracking and pitting, making it suitable for marine and seawater applications.
Inconel 718 is a high-strength, age-hardened alloy made from nickel, chromium, niobium, and molybdenum, known for its excellent corrosion resistance. It performs well in extreme temperature conditions, both high and low. Inconel 718 is particularly well-suited for spring manufacturing due to its superior fatigue, creep, and rupture strength, making it ideal for various industrial applications and operations.
The metals mentioned above represent just a selection of materials used in coil spring production. Researchers and engineers are continually exploring new materials, such as aluminum, for potential use in coil springs.
Springs are classified into coil and non-coil types based on their design. Coil springs have a helical shape and are made from a single metal strand wound into a coil. The typical manufacturing process involves wrapping or winding the spring material around an arbor and coiling point.
Different types of coil springs have distinct characteristics that set them apart. Generally, coil springs are engineered to withstand various types of stress, such as compression or extension.
Volute springs are created from flat material coiled around an arbor to form a spiral scroll shape, known as a volute. These springs often resemble a tube with a smaller end, and some designs feature small ends at both extremities. After coiling, the material sheets are heated, which affects the spring's gap, shape, dimensions, and load characteristics. During compression, the overlapping flat sheets guide each other radially, enhancing the stability of the volute spring.
Arc coil springs, or bow springs, feature a curved shape resembling the arch of a bow. Unlike traditional springs that run straight from end to end, these springs have a central curve. Initially designed for use in dual mass flywheels within drive trains, arc coil springs apply force from both ends to bring objects closer together.
Variable coil springs feature varying distances between their turns, which affects how the spring compresses at different points. As the spring is compressed, the energy required changes with each turn, often following an exponential curve. This design enhances performance in several areas, including easier unlocking, better recoil energy storage, improved dampening, and more effective feeding, breaching, and lockup.
Torsion coil springs are a flat spiral coil that is used to apply torque or store rotational energy. They store and release rotational energy via torque, which causes the spring to rotate on its axis to apply or resist a load. Torsion springs are attached to components that will rotate around their axis. In most cases, they are very tightly wound but also have versions that have pitch to reduce friction between the coils.
Torsion springs, like many other springs, can be oriented at various angles, either horizontally or vertically, and can rotate along or against their axis. When a torsion spring rotates, its coil tightens to either store or release energy. They are commonly used in applications such as mouse traps and self-closing screen doors.
Compression coil springs are designed with a helical shape to resist forces applied along their axis. They are highly versatile and come in various sizes, ranging from those used in retractable pens to those found in automobile suspension systems. Compression springs come in different forms, including helical, conical, volute, barrel, and hourglass types.
Straight Coil compression springs feature coils that maintain a consistent diameter throughout their length. This type is the most commonly used compression spring.
Hourglass compression springs feature a tapered middle that narrows to a smaller diameter compared to the rest of the coils. This design ensures that the spring remains centered within a larger diameter hole. Hourglass springs combine some benefits of conical springs while offering symmetrical characteristics.
Barrel compression springs feature smaller diameters at the ends and a larger diameter in the middle. This design addresses a common issue with standard compression springs, which can buckle or bow under pressure. The barrel shape enhances flexibility, allows the spring to fit various designs, and distributes pressure more evenly due to its wider middle section, resulting in improved stability.
Extension springs are like compression springs but are tightly wound and loaded with tension. They have hooks or loops at either end to apply pull force. Extension springs are attached at both ends to components. When the components move apart, the extension spring attempts to bring them back together. The initial tension in the spring determines how tightly coiled it is and can be changed to meet the needs of an application. The tight winding of extension springs is designed to oppose extension. In essence, they provide return force for components that have extended to the actuated position.
Coil springs are extensively utilized in a vast range of components, machines, devices, instruments, and vehicles. They play a crucial role in medical equipment, automobiles, heavy lifting machinery, and small delicate tools. Their capacity to store and release energy is essential for supporting and ensuring the efficient operation of these applications.
In trucks and cars, coil springs are a vital component of the suspension system, working in conjunction with struts and shocks. They absorb road impacts, support the vehicle’s weight, ensure a smooth ride, and maintain wheel contact with the road. In smaller applications, coil springs hold the hood open and regulate engine valve movement. Additionally, they contribute to the comfort of car seats.
Coil springs are extensively used in doors to facilitate opening and closing mechanisms. In garage doors, they are crucial for bearing the door's weight and keeping it in place until it is manually moved or closed. The design of coil springs for doors is tailored to the weight and size of the door to ensure reliability and prevent failure. For automatic doors, coil springs apply resistance to keep the doors closed but release their tension when the opening sensor is triggered.
Coil springs play a crucial role in construction projects, from anchoring new constructions to reinforcing existing foundations. They provide essential support for sidewalks, managing movement and motion. Additionally, coil springs are integral to safety release valves, facilitating the opening and closing of pipelines and pressure release systems. They also support railroad cars and engines, and are used in bridges and overpasses. In environments prone to vibrations or motion, coil springs function as dampeners and sound-absorbing devices to protect and enhance the durability of applications.
Coil springs are essential components in firearms, found in magazine springs, trigger springs, and recoil springs. In detonators, they are compressed and held in a flattened state until activation. Their reliability and durability make them suitable for the constant use demanded by loaded weapons.
The average home contains a multitude of coil springs in nearly every room. They are found in mattresses, chairs, and couches to provide support and absorb impact. Modern children’s toys use springs to activate their functions and keep them operational. Coil springs are also crucial in switches, garage door openers, cabinets, appliances, and countless other applications. In many ways, homes rely heavily on coil springs for smooth and effortless living.
Compression coil springs are employed to extend and retract the ballpoint of a pen. These springs need to be elastic enough to compress to a solid height. For proper functionality, the spring must have a suitable index and an adequate number of coils relative to its free length and wire diameter. Generally, a larger diameter and more coils result in a lighter spring.
Coil springs called compression springs can store mechanical energy when they are compressed. These open-coiled, helical springs provide resistance to compressive loading. When these springs are...
Extension springs are helical wound springs that are so closely coiled together to create initial tension in the coils. This initial tension creates resistance against the force applied to its ends for extension. The initial tension helps determine how closely and...
Springs are a flexible machine element that store mechanical energy when subjected to tensile, compressive, bending, or torsional forces. When the spring is deflected, it stores energy and at the same time exerts an opposing force...
A torsion spring is a mechanical device that stores and releases rotational energy. Each end of the torsion spring is connected to a mechanical component. As the spring is rotated around its axis on one end, the winding of the spring is tightened and stores potential energy...
Wire mesh is fabricated by the intertwining, weaving, or welding of wires of various thicknesses to create proportionally equal parallel rows and intersecting columns. Also known as wire fabric, wire cloth, or...
Contract manufacturing is a business model in which a company hires a contract manufacturer to produce its products or components of its products. It is a strategic action widely adopted by companies to save extensive resources and...
Hardware cloth is a woven mesh made by interlacing various sizes of wire to form a metal fabric that can be used for animal cages, fence material, strainers, and filtering screens. The differences between the various types of hardware cloth...
The phrase "wire mesh" describes two- or three-dimensional structures constructed of two or more metallic wires connected by various techniques. In a wide range of settings, wire mesh products are...
Welded wire mesh is a series of wires that are welded where the individual wires cross. The openings of the mesh varies depending on the type of wire used and the function of the mesh. Regardless of size and wire, welded wire mesh is permanent and...
Wire baskets are made from a series of wires that are woven together or welded to form a shape of a basket. They can also be defined as containers that are made by use of an openwork pattern of metal...
Wire cloth is a woven (or nonwoven) sheet or web material with a series of openings across the surface. Wire cloth is also known as: Metal Fabric or Metal Cloth; Wire Mesh, Metal Mesh, or Alloy Mesh...
Wire shaping is a complex method that encompasses a wide range of dimensions, forms, and textures. The technique of creating a usable product by wire bending and shaping is known as custom wire forms...
Wire forming is a method for applying force to change the contour of wire by bending, swaging, piercing, chamfering, shearing, or other techniques. The various techniques for wire forming can produce any type of shape, form, or configuration...
A wire handle is attached to a bucket, pail, or other type of container to make it easy to lift the container and transport it. They are made of durable and sturdy metals capable of lifting several pounds...
A wire rack is a level wire form utilized to stock and exhibit a number of products, usually retail. The bottom surface on which such goods are stored is made of several latticed or interlaced metal strands...