Pressure Tanks
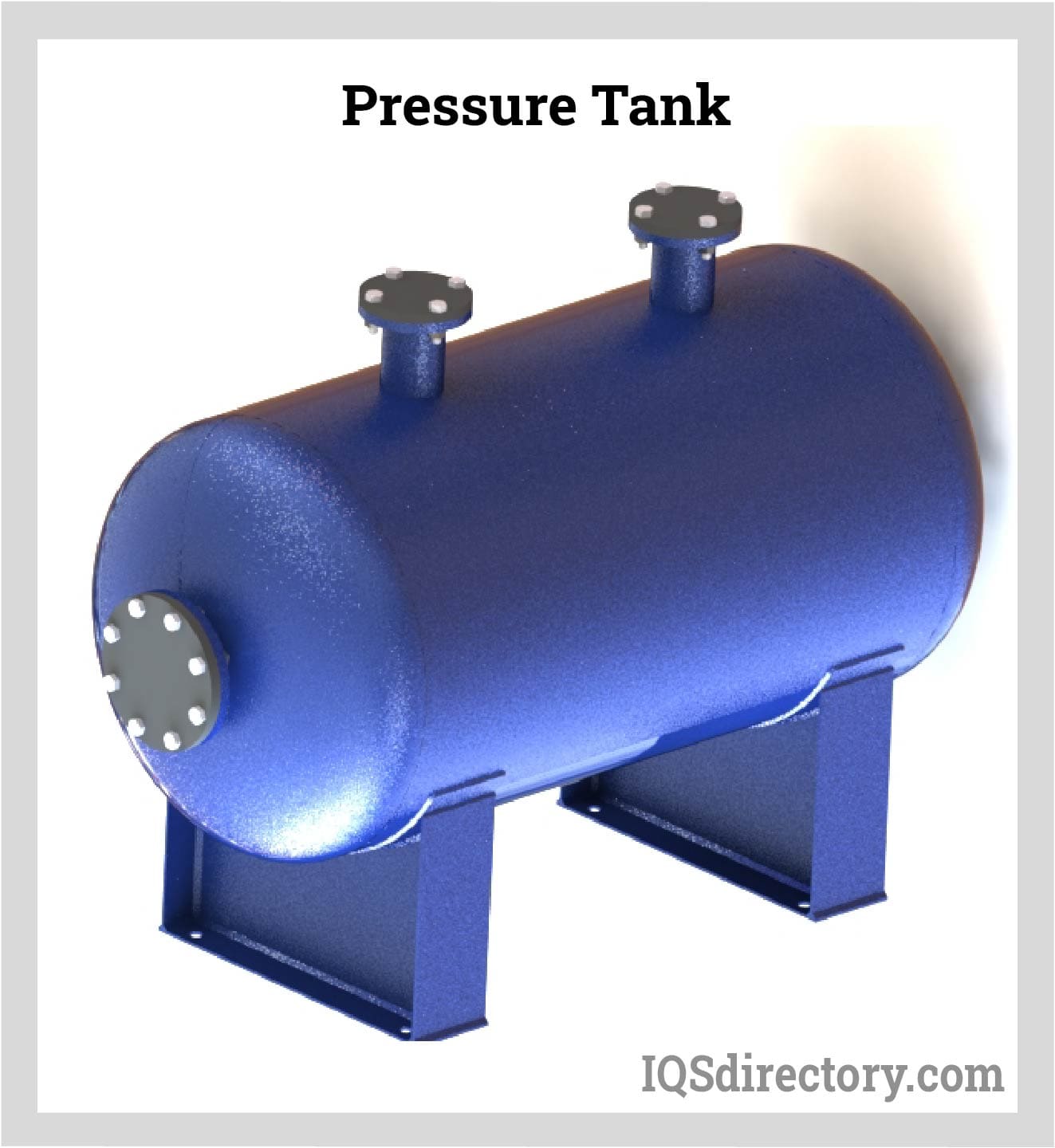
Pressure tanks are vessels that are used to store, hold, and/or convey gasses, vapors and fluids at pressures greater than atmospheric pressure, also known as high pressures...
Please fill out the following form to submit a Request for Quote to any of the following companies listed on Stainless Steel Tanks .
This article gives you comprehensive information for selecting and specifying stainless steel tanks. Read further to learn more about:
Stainless steel tanks are widely used in various sectors, including food, beverage, dairy, pharmaceuticals, and cosmetics, where maintaining hygiene and purity is essential. These tanks are also crucial in industrial settings for storing chemicals and gases, demanding excellent durability against chemical breakdown. This resilience is attributed to its composition; stainless steel is an iron alloy containing chromium that enhances corrosion resistance. The formation of a thin oxide layer helps protect the metal from potentially harmful substances.
Stainless steel tanks come in diverse forms and dimensions, with configurations available in both vertical and horizontal orientations, tailored to space and logistical needs. They range from compact designs of just a few liters to expansive tanks capable of accommodating several thousand gallons. Basic water tanks made from stainless steel typically have an inlet, outlet, and a manhole often found in residential use. In industrial contexts, tanks are equipped with various nozzles to facilitate the blending of liquids and gases and to accommodate monitoring devices. Certain tanks function as reactors or mixers, equipped with agitators and mixing mechanisms to combine materials. Furthermore, they might feature cooling jackets and dual walls for insulation and temperature management. The adaptable nature of stainless steel tanks allows for easy customization to satisfy specific application requirements.
Stainless steel remains resistant to corrosion through a mechanism known as passivation, which makes the metal mostly "inert" to oxidation. This process occurs by forming a protective oxide coating on its exterior. The passive layer, primarily made of chromium oxides, protects stainless steel from aggressive outside influences and substances in processing fluids.
The main component of stainless steel is iron, augmented with at least 10.5% chromium, crucial for the formation of a protective film made of metal oxides. Additional alloy constituents include carbon, nickel, manganese, and molybdenum. Carbon transforms pure iron into steel, thereby improving its strength. Nickel and manganese provide stability to the austenitic structure, preventing it from hardening under heat while ensuring ductility at elevated temperatures. Compared to ferritic counterparts, austenitic stainless steel remains tough even when cold. Although manganese isn't as effective as nickel, it's a cost-efficient alternative. Molybdenum, akin to chromium, boosts resistance to corrosion and reinforces the steel at high temperatures, yet it can render stainless steel brittle, an issue alleviated by incorporating more nickel.
The process of passivation involves exposing stainless steel to air, enabling the creation of an oxide layer that shields the surface. To expedite this layer's formation, chemical treatment is applied, submerging the steel in acidic baths—commonly with nitric acid—that cleanse it thoroughly. This procedure removes contaminants like exogenous iron or free iron compounds that could obstruct the passive layer. After the acid bath, the metal is neutralized by treating it with aqueous sodium hydroxide. Furthermore, descaling eliminates other oxide formations that might form during high-temperature procedures such as hot-forming, welding, and heat treatment.
Stainless steel is a preferred material for manufacturing storage tanks, process tanks, mixing tanks, and chemical tanks because of its excellent corrosion resistance, longevity, and strength under demanding industrial conditions. Stainless steel tanks are engineered using a range of stainless steel grades, each offering different characteristics tailored for specific applications, chemical compatibilities, and performance requirements. Optimizing stainless steel selection ensures tank durability, hygiene, and maintenance efficiency in sectors such as pharmaceuticals, food and beverage processing, water treatment, dairy, and chemical manufacturing. In this section, we explore the most widely used stainless steel grades for tank fabrication: 304/304L, 316/316L, and duplex.
Stainless steel 304, aside from the steel forming alloys, is composed of 18-20% chromium, 8-11% nickel, and 2% manganese. This is the most common stainless steel since it has enough corrosion resistance for most applications and is less expensive than other grades. An austenitic metallurgical structure makes it ductile and well-suited for forming a wide range of products.
Stainless steel 304L contains similar amounts of chromium, nickel, and manganese as stainless steel 304. The key distinction lies in its reduced carbon content, which helps prevent sensitization. Sensitization occurs when chromium and carbon atoms in the steel react at elevated temperatures to form chromium carbides. This reaction depletes chromium that would otherwise contribute to the passive film, particularly at the grain boundaries of the steel, leading to increased susceptibility to intergranular corrosion. This issue is especially significant in high-temperature applications. By reducing the carbide content, the formation of chromium carbides is minimized, thereby preserving corrosion resistance even under high temperatures.
The combination of affordability and reliable performance makes 304 and 304L stainless steel tanks ideal for general-purpose storage applications, including potable water, breweries, distilleries, and many food-grade storage tank installations. Thanks to their ease of fabrication, these grades are popular for cylindrical tanks, jacketed tanks, and atmospheric tanks where aggressive chemical resistance is not a primary concern.
Stainless steel 316 contains 16-18% chromium, 10-14% nickel, 2-3% molybdenum, and 2% manganese. The added molybdenum makes this grade more corrosion-resistant than stainless steel 304. It has higher nickel content to counter the ferritic forming property of the added molybdenum. Stainless steel 316 is mostly used in highly corrosive environments such as chemical handling tanks and tanks near marine environments. Like stainless steel 304, stainless steel 316 has a lower carbon grade, 316L. Lower carbon content is also used for high-temperature applications to prevent sensitization.
316 and 316L stainless steel tanks are particularly valued for their superior resistance to pitting corrosion and crevice corrosion caused by chlorides, acids, and other harsh chemicals. As a result, they are the preferred choice for industrial process tanks, chemical storage tanks, offshore tanks, brine tanks, and tanks used in saltwater or caustic chemical processes. Industries relying on hygienic stainless steel tanks, such as pharmaceutical production, food processing, cosmetics, and biotechnology, often specify 316L stainless steel for its exceptional purity, cleanability, and resistance to contamination.
When evaluating 316 vs. 316L for tank manufacturing, consult with stainless steel tank suppliers for expert guidance. They will consider the intended application, temperature, chemical concentration, and relevant sanitary or industry standards (such as ASME, FDA, or 3-A) to recommend the most suitable grade.
This type of stainless steel is composed of both austenitic and ferritic metallurgical structures. Austenitic stainless steel offers superior corrosion resistance and mechanical properties compared to ferritic stainless steel, but it is more prone to stress corrosion cracking. Stress corrosion cracking occurs when a crack develops in a material exposed to a corrosive environment, potentially leading to sudden failure. On the other hand, ferritic stainless steel is resistant to stress corrosion cracking. By combining the ferritic phase with the austenitic phase, the material gains enhanced resistance to stress corrosion cracking. This makes it particularly suitable for tanks used in environments and processes involving chlorides, such as domestic water applications.
For demanding industrial applications, duplex stainless steel tanks deliver a unique balance of strength and resistance to a broad spectrum of corrosive substances, including aggressive chlorides and sulfides. Duplex alloys exhibit superior mechanical strength, enabling a reduction in tank wall thickness—and therefore material costs—without compromising performance. These tanks are ideal for wastewater treatment, desalination plants, oil and gas storage, pulp and paper processing, and chemical plant reactors. The duplex structure allows for a longer service life, reduced risk of corrosion-induced failures, and greater safety in chemically aggressive or high-stress environments.
Duplex stainless steel comprises 20-28% chromium, 2-5% molybdenum, and 5-8% nickel. The increased chromium and molybdenum content enhances the corrosion resistance and mechanical strength of duplex stainless steels. Compared to 316 stainless steel, duplex steel is more cost-effective due to its lower nickel content and higher strength at a given thickness, allowing for the use of thinner plates or sheets. The most commonly used grade of duplex stainless steel is the standard duplex, also known as 2205 stainless steel.
When selecting the best stainless steel tank material, consider factors such as required resistance to specific chemicals, temperature ranges, pressure ratings, and compliance with food-grade, pharmaceutical, or sanitary standards. Reputable stainless steel tank manufacturers can help evaluate the trade-offs between 304 vs. 316 stainless steel, or between duplex vs. austenitic grades, to ensure your tank investment meets your performance, safety, and regulatory needs. For a more detailed comparison of tank materials—including alloy composition, corrosion resistance, maintenance requirements, and life cycle costs—request specification sheets and consult with expert suppliers.
Stainless steel tanks are integral to a wide range of industries, valued for their durability, corrosion resistance, and sanitary properties. These tanks offer extensive customization options to meet specific operational and regulatory requirements for sectors such as food and beverage, pharmaceutical manufacturing, chemical processing, dairy, and water treatment. Design variations include single or double walls, horizontal or vertical orientation, and insulation or heating capabilities. Choosing the right type of stainless steel tank is essential based on application-specific factors like storage medium, temperature control, pressure ratings, and hygienic requirements. Below are the primary classifications of stainless steel tanks based on function, construction, and typical industrial uses.
These are the simplest stainless steel tanks, usually cylindrical in construction. These vessels can be oriented vertically or horizontally depending on the application and size restrictions. Having a single wall provides basic protection from corrosive compounds on both the internal and external surfaces of the tank, leveraging stainless steel's excellent corrosion resistance. Single-walled tanks are commonly used for storing potable water, processing liquids, and bulk raw materials in water treatment facilities, food production, chemical plants, and manufacturing environments where product purity and tank cleanliness are priorities.
Double-walled stainless steel tanks are utilized for applications requiring secondary containment to minimize environmental risk in the event of leaks or spills. These tanks comply with EPA regulations such as SPCC (Spill Prevention, Control, and Countermeasure) for hazardous materials and oil storage. The inner and outer walls, often both stainless steel but sometimes combining with carbon steel, enhance structural integrity and corrosion protection. Some models feature insulation between walls, supporting thermal management—ideal for temperature-sensitive products in breweries, distilleries, and chemical storage. Double-wall designs are also vital for storing fuel, acids, and caustic chemicals in compliance with industry safety standards.
For storage of corrosive chemicals or large-volume liquids, stainless steel clad tanks combine the strength and cost-effectiveness of carbon steel with the superior corrosion resistance of stainless steel. Constructing large stainless steel tanks with thick walls can be prohibitively expensive; using carbon steel plates for structure, clad with a thin layer of stainless steel, resolves this challenge. Cladding processes—such as hot roll bonding, cold roll bonding, or explosive bonding—create a durable metallurgical bond that protects contents and extends service life in aggressive environments. Clad tanks are widely used where high strength and chemical inertness must be balanced, such as in biofuel storage, wastewater treatment, and pulp & paper processing.
Jacketed stainless steel tanks are engineered for precise temperature control, essential in applications such as fermentation, pasteurization, and chemical reactions. Heating or cooling mediums flow between two walls, allowing controlled heat transfer via the inner stainless steel shell. After the process, the thermal medium typically circulates back to utility systems. These tanks are indispensable in industries requiring strict process temperatures—like breweries, food processing, biopharma manufacturing, and cosmetics. The three principal jacket types are:
This classic design features an outer shell welded to the inner tank, with baffles to direct thermal medium. The resulting annular space is best for low-pressure heating or cooling applications, ideal for gentle temperature maintenance in food and beverage processing or pharmaceutical production. For higher pressures, wall thickness—and associated cost—increases.
Dimple-jacketed stainless steel tanks employ spot- or plug-welded patterns that produce external dimples, maximizing the effective heat exchange surface area. This configuration permits the use of thinner stainless steel sheets and is favored for moderate pressures and efficient thermal conductivity. Dimple jackets are prevalent in brewing, dairy, and wine production, though not suitable for rapid thermal cycling processes, as repeated expansion and contraction can stress weld points.
This type uses a split (half-pipe) coil wound and welded directly onto the tank exterior, forming a robust jacket ideal for high-pressure heating or cooling media. Half-pipe coil jacketed tanks withstand higher thermal stress and pressure, making them optimal for chemical processing industries and large-scale fermenters. They offer a balance of cost, efficiency, and durability for operations requiring extensive heating or cooling capacity.
This stainless steel tank category is crucial for processing steps involving mixing, blending, dissolution, or homogenizing of ingredients—common in chemical, pharmaceutical, and food industries. A defining feature is the integrated agitator or mixing apparatus, which may include high-shear mixers, impellers, paddles, or helical agitators to optimize process performance. Advanced process tanks integrate temperature, pressure, and level monitoring for precise control, often including features such as steam jackets or insulation for thermal management. Custom process tanks are tailored to hygiene requirements for sanitary processing (CIP/SIP-ready) or hazardous material handling, ensuring compliance with FDA, cGMP, and industry standards.
High-pressure stainless steel tanks are engineered for applications where internal pressures exceed 1 barg, requiring adherence to stringent safety and engineering codes such as the ASME Boiler and Pressure Vessel Code. Typical uses include energy, petrochemical, and industrial gas storage. These pressure vessels are built with reinforced weld seams, secure manways, and pressure relief devices, with tank specifications often bearing certification marks to indicate compliance. Design parameters—such as material thickness, head geometry, weld integrity, and corrosion allowances—are critical to maintain workplace safety and minimize environmental risk. High-pressure tanks are also instrumental in process optimization in industries handling compressed gases, refrigerants, or autoclaving operations.
Compressed air tanks—also called air receivers—are specialized stainless steel pressure vessels designed for use in pneumatic systems within manufacturing, automotive, and processing facilities. Governed by the ASME Boiler and Pressure Vessel Code, these tanks safely store air at pressures commonly ranging from 5 to 6 barg. Air receivers function as air storage, pressure stabilization, and moisture separation units, crucial for improving overall system efficiency and protecting downstream equipment. Cleanliness and corrosion resistance are paramount, as water vapor condenses and collects at the bottom, necessitating regular drainage. Stainless steel’s inert properties ensure longevity and hygiene, making these vessels ideal for applications demanding high purity or where aggressive cleaning agents are used.
When selecting a stainless steel tank type, consider factors such as chemical compatibility, temperature and pressure requirements, hygienic design, maintenance, and applicable industry certifications. Features such as access ports, level indicators, CIP/SIP systems, and custom fittings further enhance tank performance and operational efficiency. For tailored recommendations and sourcing guidance, consult a stainless steel tank manufacturer with expertise in your specific application under current industry regulations.
Stainless steel typically features a smooth and slightly reflective surface, though it can also have a grainy or brushed texture in certain applications. These different profiles are known as surface finishes. Surface roughness is a key characteristic, representing the deviation of microscopic peaks and valleys from the ideal surface. The choice of surface finish and roughness is crucial for stainless steel tanks as it influences moisture retention and material adhesion on the tank's surface.
This is the basic supply condition of stainless steel sheets or plates after manufacture from the steel mill. Thus, a mill finish is not yet altered by mechanical or chemical means to suit a specific purpose. Manufacturing is usually through hot and cold rolling. Secondary milling operations such as pickling are done to enhance the stainless steel corrosion resistance. The most popular type of mill finish used for stainless steel tanks is No. 2B. No. 2B, as designated by ASTM, is characterized by a smooth and slightly reflective surface. The average surface roughness, Ra, is typically in the range of 0.30 – 0.50 µm. The process used to achieve this smoothness is skin pass rolling. Other types of mill finishes are No. 1D, No. 2D, and BA (bright annealed).
From a standard mill finish, additional processes are applied to achieve the desired surface smoothness. Mill finish grade is chosen closest to the surface characteristics desired to lessen polishing effort. Polishing and brushing are achieved by using fine, abrasive materials bonded on belts and disks that cut in a unidirectional manner. The average roughness for this finishing varies depending on the application. This is usually done on stainless steel process tanks where a specific surface roughness for the inner walls is required to achieve the proper flow of materials as they are mixed or agitated. Popular mechanical finishes are No. 3 and No. 4.
Electropolishing is an electrochemical process that removes or levels microscopic peaks on the surface of the metal. This is done by submerging the metal into a heated electrolyte bath. The metal is then connected to a DC power supply together with a cathode submerged into the electrolyte as well. As the current passes through the metal, the surface dissolves into the electrolyte solution. The microscopic surface peaks dissolve faster than the flatter regions. Eventually, the surface becomes smoother in the order of less than 0.2 µm. Electropolished stainless steel tanks are used in food and pharmaceutical industries where product contamination is an issue. The surface of the tank must be smooth enough so that no moisture can linger since moisture promotes the growth of microbes. Also, for tanks featuring clean-in-place (CIP) capabilities, having a very smooth surface prevents any product from adhering to the surface, making the rinse phases easier.
Specifications, or ordering information, are design details provided to the manufacturer that depend on the intended application. Before proceeding with an order, it is crucial to confirm that the supplier can produce the required features. Below is the essential information needed for specifying a stainless steel tank.
This is one of the most important design considerations, as determined by the process owners. This is the nominal volume of the tank usable for storage or processing. Note that this is different than the overall or gross volume, which accounts for space reserved for vapors and expansion.
Aside from the capacity, pressure rating is an important design parameter that affects the thickness of the metal sheet or plate to be used. Additional specifications such as welding processes and inspection methods are required according to the experienced pressure of the tank.
This is the process owner‘s preferred dimensions of the tank. Still, this depends on the manufacturer‘s capability and governing standards. It is best to start from commercially available or standard sizes and tweak them accordingly.
As discussed earlier, there are three stainless steel grades commonly used for tanks. These are 304/304L, 316/316L, and duplex. Stainless steel 304/304L is the cheapest and suited for mildly-corrosive environments and chemicals. 316/316L has superior properties than 304/304L but is significantly more expensive. Duplex stainless steel has comparable properties (better for more expensive grades) than 316/316L. Duplex is more expensive; however, technological advances bring lower costs.
The usual stainless steel tank finishes are standard mill finish and electropolished. Mechanical polishing is employed to achieve a specific surface roughness for agitation and mixing processes.
Nozzles are stub-in connections welded into the stainless steel tank for joining, coupling, or bolting inlet, outlet, and instrument pipes. Manholes provide access to tank internals for cleaning and maintenance. Nozzle and manhole sizes are usually specified by the process owner.
These are safeguards in the event of emergencies such as equipment failure or process upsets. Excessive pressure and flow can exceed the limits of the tank, causing explosion and spillage. This is particularly relevant to high throughput process tanks and pressurized tanks.
For tanks utilized in food, beverage, pharmaceutical, and dairy industries, there can be no regions where the product can stagnate. Weld caps can prevent liquid from flowing. Microbes can grow in these areas, causing contamination. Process owners may opt to specify ground flush welds. However, this process significantly weakens the joints and should be considered in designing the thickness of the sheet walls.
These include cooling jackets, insulation, connections for agitators and mixers, brackets, supports, lifting lugs, and internal structures such as baffles, trays, and ladders.
Stainless steel tanks offer limitless applications due to their durability and strength. Every sector of society benefits from the positive properties of stainless steel, ensuring high-quality performance and protection for stored materials. While stainless steel is often associated with antiseptic and sterile environments, these tanks are also widely used in various industrial storage and containment applications.
The five uses for stainless steel tanks mentioned above represent just a small sample of their diverse applications in everyday life. Their strength and durability ensure that stored or protected materials are kept safe and secure. The different varieties and grades of stainless steel provide a wide range of solutions for manufacturing these tanks.
Pressure tanks are vessels that are used to store, hold, and/or convey gasses, vapors and fluids at pressures greater than atmospheric pressure, also known as high pressures...
Pressure vessels are enclosed containers used to hold liquids, vapors, and gases at a pressure significantly higher or lower than the ambient pressure. They are widely used in various industries such as...
Stainless steel grade 304 is an austenite stainless steel that is the most widely used and versatile of the various grades of stainless steel. It is a part of the T300 series stainless steels with...
Stainless steel is a type of steel alloy containing a minimum of 10.5% chromium. Chromium imparts corrosion resistance to the metal. Corrosion resistance is achieved by creating a thin film of metal...
Stainless steel can be fabricated using any of the traditional forming and shaping methods. Austenitic stainless steel can be rolled, spun, deep drawn, cold forged, hot forged, or stippled using force and stress...
Stainless steel grades each consist of carbon, iron, 10.5%-30% chromium, nickel, molybdenum, and other alloying elements. It is a popular metal used in various products, tools, equipment, and structures that serve in many industrial, commercial, and domestic applications...
Stainless steel tubing is a multifaceted product that is commonly utilized in structural applications. Stainless steel tubing diameters and variations vary greatly based on the application requirements and are...