Stainless Steel 304
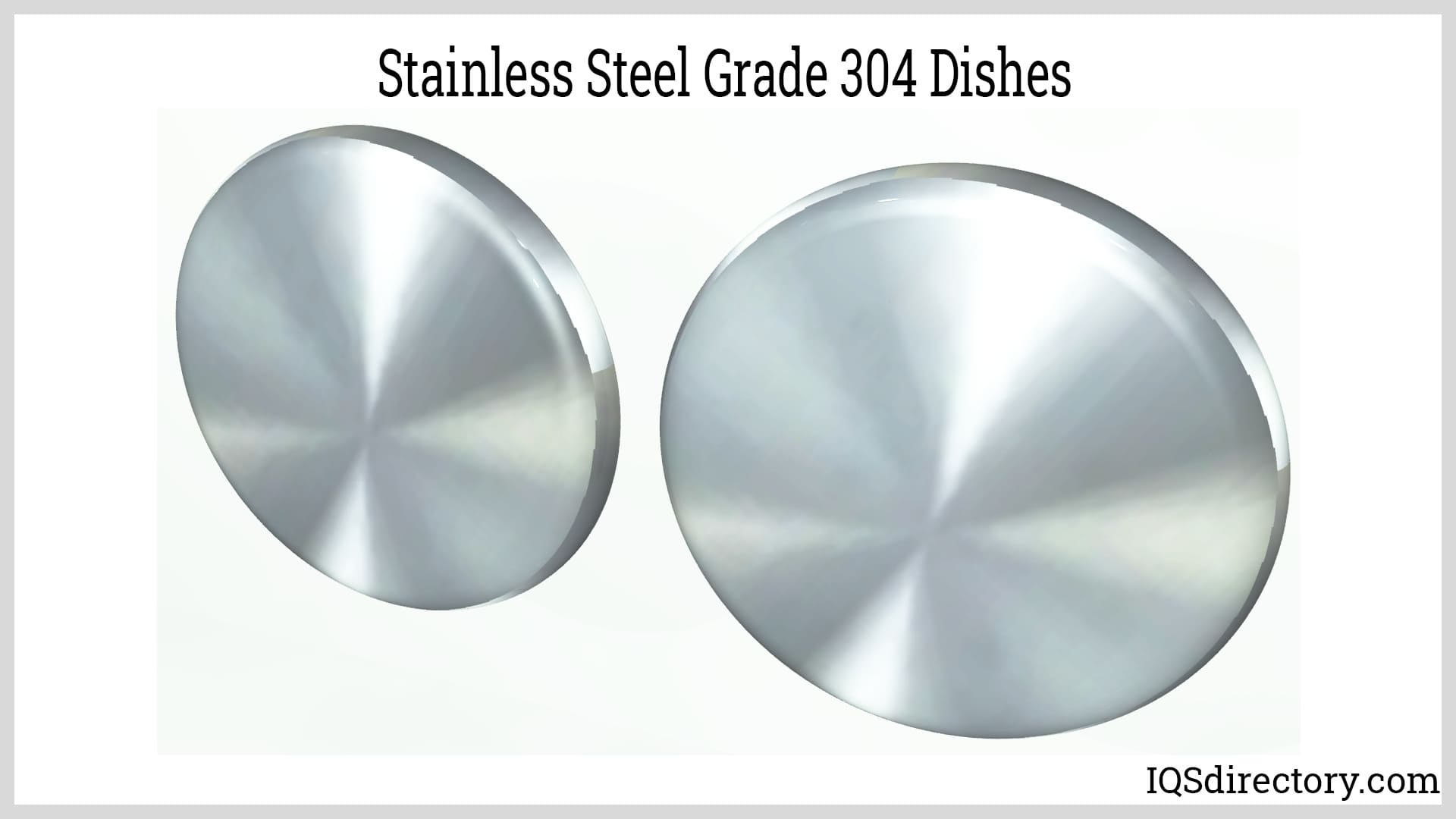
Stainless steel grade 304 is an austenite stainless steel that is the most widely used and versatile of the various grades of stainless steel. It is a part of the T300 series stainless steels with...
Please fill out the following form to submit a Request for Quote to any of the following companies listed on
This article offers detailed information about stainless steel 316.
You will learn:
Stainless Steel Grade 316 Spec Sheet | |
---|---|
316 | 316L |
ASTM A240 | ASTM A240 |
ASTM A666 | ASTM A666 |
ASME SA240 | ASME SA240 |
AMS 5524 | AMS 5507 |
Stainless steel is a type of alloy composed of at least 10% chromium, a key element that gives it corrosion resistance. The chromium develops a protective oxide film on the metal's surface, shielding it from corrosive factors.
Among the various grades, stainless steel 316 is quite prevalent. It generally consists of 16 to 18% chromium, 10 to 14% nickel, 2 to 3% molybdenum, and traces of carbon. The inclusion of molybdenum enhances the corrosion resistance of stainless steel 316 when compared to other grades, with additional alloying improving its overall attributes.
The characteristics and advantages of stainless steel 316 make it the second most frequently used grade, right behind stainless steel 304. It is especially suitable for corrosive settings like chemical plants, refineries, and marine applications.
Stainless steel 316L, a low-carbon variant, is favored in cases where sensitization could be a problem. In contrast, stainless steel 316H has an increased carbon content, offering better thermal stability and creep resistance. Another variant, stainless steel 316Ti, is stabilized for enhanced resistance to intergranular corrosion.
Stainless steel benefits significantly from passivation, a process that makes the metal "passive" or resistant to oxidation in corrosive environments and process fluids. This is accomplished by exposing the stainless steel to air, allowing the formation of a protective layer of chromium oxides on its surface.
To bolster the formation of the passive film, stainless steel is treated chemically in acidic passivation baths, which typically include nitric acid. This cleaning process eradicates impurities such as free iron or iron compounds that could compromise the passive layer.
After the acidic treatment, the metal is neutralized in a sodium hydroxide bath. Furthermore, a descaling procedure is used to remove oxide films that develop during high-temperature operations like hot-forming, welding, and heat treatment.
The key feature of stainless steel 316 is its molybdenum content, which significantly improves its resistance to corrosion. It is the second most widely used austenitic stainless steel, following grade 304. Austenitic stainless steels are distinguished by their nickel or nitrogen content, which imparts a unique crystalline structure to these materials.
Stainless steels are categorized based on their chemical composition, physical properties, metallographic structure, and functional characteristics. They are classified into four main families: ferritic, martensitic, austenitic, and duplex, with duplex stainless steels being combinations of the first three types, such as martensitic-ferritic or austenitic-martensitic. The matrix structure of these stainless steels defines their classification into these families.
The families of stainless steel are further divided into grades describing the properties of the alloys used to produce them. Older grades are designated by three-digit numbers established by the Society of Automotive Engineers (SAE). Although three-digit identifiers are common, many countries have their own systems, with North America using a six-digit system established by the American Society for Testing and Materials (ASTM).
Regardless of the numbering system, each grade of stainless steel must adhere to its specified alloy composition. Any modification or addition to the alloy can significantly affect the performance of the stainless steel grade. When different families and grades are combined and identified, they are expected to exhibit a specific set of characteristics, properties, and performance traits.
Stainless steel grades vary in their levels of corrosion resistance, strength, toughness, and performance at high and low temperatures. The defining factor for each grade is its microstructure, which can be examined under a microscope at 25x magnification. The microstructure affects the material's physical properties, including strength, toughness, ductility, hardness, corrosion resistance, temperature stability, and wear resistance.
The microstructure of stainless steel 316 features cell structures with boundaries enriched with elements such as chromium, manganese, molybdenum, and niobium, which contribute to its enhanced corrosion resistance. This improved resistance results from the densification and fine cellular structures, as well as the enrichment of chromium and molybdenum at the boundaries of these structures.
Austenitic Stainless Steels: Austenitic stainless steels are non-magnetic with high levels of chromium and nickel and low levels of carbon. They are the largest and most used group of stainless steels.
Austenitic stainless steels have a face-centered cubic (FCC) crystal structure with one atom at each corner of the cube and one in the center of each face, a grain structure formed due to nickel being added as an alloy. The microstructure of austenitic stainless steel makes it tougher and more ductile, even at cryogenic temperatures.
When subjected to high temperatures, austenitic stainless steels do not lose their strength, which gives them excellent formability and weldability. Since the austenitic structure is maintained at all temperatures, they do not respond to heat treatment. Instead, they are cold-worked to improve their toughness, strength, hardness, and stress resistance.
The principle alloy for all austenitic stainless steels is nickel, which is used for all series 300 austenitic stainless steels, including grades 316 and 316L. When a stainless steel has a low nickel and high nitrogen content, it is no longer a 300 series stainless steel. The presence of nitrogen in stainless steels is limited since it can have very negative effects. Stainless steels with a low nickel and nitrogen content are classified as series 200 stainless steels.
Aside from its resistance to chlorides, the main difference between series 304 and series 316 is the presence of molybdenum in series 316 at percentages of 2% to 3%, which identifies series 316 as a Cr-Ni-Mo system. Adding molybdenum makes series 316 resistant to pitting caused by phosphoric acid, acetic acid, and dilute chloride solutions. The strength and toughness of molybdenum increase series 316’s heat and wear resistance.
Comparison of the Elements of Series 304 Stainless Steel and Series 316 Stainless Steel | ||
---|---|---|
Type 304 | Type 316 | |
Carbon | 0.08% Max | 0.08% Max |
Manganese | 2.00% Max | 2.00% Max |
Phophorus | 0.045% Max | 0.045% Max |
Sulfer | 0.030% Max | 0.030% Max |
Silicon | 1.00% Max | 1.00% Max |
Chromium | 18.00 - 20.00 | 16.00 - 18.00 |
Nickel | 8.00 - 10.50% | 10.00 - 14.00 |
Molybdenum | - | 2.00 - 3.00% |
Ferritic Stainless Steels: As the name suggests, these stainless steels that have a ferritic microstructure. Its ferritic microstructure is present at all temperatures due to the addition of chromium with little or no austenite forming elements such as nickel. Because of this constant microstructure, like the austenitic stainless steel, they do not respond to heat treatment. They are more difficult to weld due to excessive grain growth and intermetallic phase precipitation, especially at higher chromium content. The result is lower toughness after welding which makes them unsuitable for structural materials. Ferritic stainless steels are designated as AISI 400 series. This designation is shared with martensitic stainless steels.
Martensitic Unit Cell: These stainless steels have higher amounts of carbon that promotes a martensitic microstructure. Martensitic stainless steels are hardenable by heat treatment. When heated above its curie temperature, they have an austenitic microstructure. From an austenitic state, heating rapidly results in martensite, while cooling slowly promotes the formation of ferrites and cementite. Varying the carbon content results in a wide range of mechanical properties, making them suitable for engineering and tool steels. Increasing the carbon content makes the stainless steel harder and stronger, while decreasing it makes the alloy more ductile and formable. However, adding more carbon results in lower chromium to maintain a martensitic microstructure. Thus, higher strength is attained at the expense of corrosion resistance. They generally have lower corrosion resistance than ferritic and austenitic stainless steels.
Duplex Stainless Steels: This type of stainless steel consists of a combination of austenitic and ferritic metallurgical structures, usually in equal amounts. It is created by adding more chromium and nickel to a standard martensitic stainless steel, promoting a duplex ferritic-austenitic microstructure. Since they do not have a constant ferritic and austenitic microstructure, they respond to heat treatment. Austenitic stainless steel is far superior to ferritic in terms of corrosion resistance and mechanical properties. However, they are highly susceptible to stress corrosion cracking. Stress corrosion cracking happens when a crack propagates when the material is subjected to a highly corrosive environment. This can lead to the sudden failure of ductile materials. A ferritic microstructure is resistant to stress corrosion cracking. By combining the ferritic phase with the austenitic phase, added resistance to stress corrosion cracking is obtained. Aside from improved corrosion resistance and mechanical properties, the price of duplex stainless steels is more stable than austenitic. This is attributed to the lower nickel content. The most common grade is the standard duplex 2205. Duplex stainless steels are not covered by AISI designation.
Precipitation Hardening Stainless Steels: These are stainless steels that can further be modified by precipitation hardening. Initially, precipitation hardening stainless steels are supplied in a solution annealed condition. Manufacturers can perform an additional aging process to attain the desired mechanical properties. Note that this heat treatment has a different mechanism than hardening martensitic stainless steels. In precipitation hardening, precipitates or secondary phase particles are allowed to form at elevated temperatures usually lower than the curie temperature. The formation of these secondary phase particles is promoted by alloying elements such as copper, niobium, aluminum, and titanium. Their growth rate, size, and dispersion are controlled by temperature and time. These secondary phase particles act as dislocation sites to the crystal structure, improving the metal's overall toughness and strength. Moreover, unlike the martensitic varieties, they have comparable corrosion resistance with austenitic and ferritic stainless steels.
Source 21 is a supplier of stainless steel in coils and strips, offering various grades including 316 and 316L. Their processing services for stainless steel coils include cutting to length, polishing, masking, and tempering. The finished products are available in custom boxes, export crates, or specialty skid mounts. Source 21 serves multiple industries, such as aerospace, roll forming, automotive manufacturing, and food processing. The company is committed to providing stainless steel solutions that meet the diverse needs of their customers, whether they require standard grades or specialized alloys.
Cleveland-Cliffs is a leading producer of flat-rolled stainless steel in North America, with iron ore mining operations in Michigan and Minnesota. The company supplies stainless steel to the automotive industry and is committed to steel recycling and sustainability. Cleveland-Cliffs manufactures all five main types of stainless steel, including grades 304 and 304L, and caters to both the automotive sector and other manufacturing industries.
Allegheny Technologies is a manufacturer of a diverse array of metals and specialty metals, including various grades of stainless steel. The company provides a comprehensive range of stainless steels, including specialized forms such as superaustenitic and superferritic stainless steels. ATI produces stainless steel through hot rolling, offering a wide range of product sizes and thicknesses. The company is known for its ability to meet customer orders efficiently with short lead times.
Acerinox is a Spanish manufacturer specializing in various forms of stainless steel for industries including transportation, industrial equipment manufacturing, food processing, and environmental technology. The company produces stainless steel plates, hot and cold coils, sheets, strips, and discs. With a global presence, Acerinox provides its diverse range of stainless steel products to a broad spectrum of industries and customers worldwide.
Aperam, based in Luxembourg, delivers a wide range of stainless steel products to 40 countries, with a production capacity of 2.5 million tons across five global facilities. The company offers stainless steel coils, sheets, tubes, discs, flat bars, strips, and heavy plates, and operates a service center in Sterling Heights, Michigan, specializing in flat stainless steel. Aperam is committed to innovation and high-performance solutions for technological and manufacturing challenges. All of its stainless steel products are recyclable and produced with a notably low CO2 footprint.
As discussed earlier, stainless steel 316 is part of the austenitic family, where nickel acts as a stabilizer for the austenitic structure. The typical composition of stainless steel 316 includes 16–18% chromium, 10–14% nickel, 2–3% molybdenum, up to 2% manganese, up to 0.75% silicon, up to 0.10% nitrogen, up to 0.08% carbon, up to 0.045% phosphorus, up to 0.03% sulfur, with iron making up the remainder. Additional alloying elements like titanium and niobium may be included to produce other grades. The compositions of various stainless steel grades are summarized below.
Grade | Alloying Elements (Percent) | |||||||||
---|---|---|---|---|---|---|---|---|---|---|
C | Cr | Ni | Mo | Mn | Si | N | P | S | Others | |
316 | 0.08 | 16-18 | 10-14 | 2-3 | 2.0 | 0.75 | 0.10 | 0.045 | 0.03 | |
316L | 0.03 | 16-18 | 10-14 | 2-3 | 2.0 | 0.75 | 0.10 | 0.045 | 0.03 | |
316H | 0.04 - 0.10 | 16-18 | 10-14 | 2-3 | 2.0 | 0.75 | 0.045 | 0.03 | ||
316Ti | 0.08 | 16-18 | 10-14 | 2-3 | 2.0 | 0.75 | 0.10 | 0.045 | 0.03 | Ti¹ |
316Cb | 0.08 | 16-18 | 10-14 | 2-3 | 2.0 | 0.75 | 0.10 | 0.045 | 0.03 | Cb² |
316N | 0.03 | 16-18 | 10-14 | 2-3 | 2.0 | 0.75 | 0.10 - 0.16 | 0.045 | 0.03 | |
316LN | 0.03 | 16-18 | 10-14 | 2-3 | 2.0 | 0.75 | 0.10 - 0.16 | 0.045 | 0.03 |
Notes:
The alloying elements of stainless steel 316 and their effects on the properties of the alloy are listed below.
Carbon: This is the main alloying element of steel. Iron alone has poor mechanical properties, but when alloyed with varying amounts of carbon imparts a wide range of hardness and strength. Adding carbon makes the steel harder and stronger but more brittle. Decreasing it improves ductility. Also, adding sufficient amounts of carbon allows the steel to respond to heat treatment. However, there is a certain limit to how much carbon can be added. For austenitic stainless steels, adding too much carbon promotes sensitization. Sensitization is the precipitation of chromium carbides at the grain boundaries that consumes the chromium from the adjacent regions. This makes the stainless steel susceptible to intergranular corrosion.
Nickel: Nickel is added to stainless steel to form or retain an austenitic microstructure at room and low temperatures. The minimum amount required to stabilize an austenitic microstructure is around 8 to 9%. In austenitic stainless steels, 10 to 14% is required due to the addition of molybdenum, another ferrite former aside from chromium.
Titanium: Titanium is a stabilizer added to standard or straight 316 stainless steels to form the 316Ti variant. Titanium is a stronger carbide-former than chromium. At high temperatures, chromium tends to react with carbon and precipitate at grain boundaries. In stainless steel 316Ti, titanium reacts with carbon instead of chromium. This maintains the amount of chromium present within the austenite, resulting in the high-temperature stability of 316Ti. By lessening the formation of precipitates, intergranular corrosion resistance is improved.
Stainless steel 316 is the second most commonly used stainless steel grade after 304. It is favored for its addition of molybdenum, which enhances its resistance to chemical attacks, particularly from chloride solutions. Beyond the role of molybdenum, many of its beneficial properties are due to its austenitic microstructure.
Below is a summary of the general properties of stainless steel 316 and its variants. These properties highlight its advantages compared to other types of stainless steel.
Corrosion Resistance: All stainless steel 316 grades have molybdenum as an alloying element that further improves corrosion resistance, particularly pitting corrosion. Pitting is a highly localized type of corrosion that creates shallow holes on the surface of the metal. This takes place in the presence of solutions containing chloride ions, such as seawater. High resistance to pitting corrosion makes stainless steel 316 recommended for marine applications. Molybdenum, together with chromium and nitrogen, is one of the factors in determining the pitting index or pitting resistance equivalence number.
Weldability: Austenitic stainless steels experience fewer negative effects from welding. They can retain their toughness and impact strength since they do not transform to martensite. They are less susceptible to cold cracking as encountered in martensitic stainless steels. Because of these, they are suitable for welding fillers even in welding different stainless steel groups.
Listed below are the various grades of stainless steel 316. These grades are modified versions of the standard 316 composition, where the carbon content is reduced or stabilizing alloying elements are added. These modifications enhance or maintain mechanical properties and corrosion resistance, particularly after welding. Variants with higher carbon and nitrogen contents are utilized for their improved hardness and creep resistance.
316L: As of now, this is perhaps the most widely used variant compared to the standard and the 316Ti grade. Originally, low carbon grades were more expensive and difficult to produce until the introduction of the production process known as Argon Oxygen Decarburization (AOD). This grade of stainless steel 316 has a lower carbon content to reduce the effects of sensitization.
Lower carbon content means less formation of chromium carbide precipitates and less depletion of chromium in regions near the grain boundaries. This improves the retention of toughness and corrosion resistance of the stainless steel after welding.
316H: This grade contains higher amounts of carbon, improving its thermal stability and creep resistance. Its corrosion resistance is comparable to 316L. However, due to the high carbon content, it is prone to sensitization which makes welding joints vulnerable to corrosion.
Stainless steel grade 304 is an austenite stainless steel that is the most widely used and versatile of the various grades of stainless steel. It is a part of the T300 series stainless steels with...
Stainless steel grades each consist of carbon, iron, 10.5%-30% chromium, nickel, molybdenum, and other alloying elements. It is a popular metal used in various products, tools, equipment, and structures that serve in many industrial, commercial, and domestic applications...
Stainless steel can be fabricated using any of the traditional forming and shaping methods. Austenitic stainless steel can be rolled, spun, deep drawn, cold forged, hot forged, or stippled using force and stress...
Stainless steel tubing is a multifaceted product that is commonly utilized in structural applications. Stainless steel tubing diameters and variations vary greatly based on the application requirements and are...
Perforated stainless steel is cut, punched, or stamped to produce a precise pattern of holes or apertures. It is used for functional reasons, such as filtration or ventilation, and aesthetic ones, such as architectural accents...
Stainless steel hinges connect two components while allowing them to move in relation to one another. They can have various leafs shaped like rectangles and other forms depending on the type of stainless steel hinge. Stainless steel hinge leafs are...
Stainless steel tanks are widely used in food, beverage, dairy, medicine, cosmetics, and other manufacturing processes where cleanliness and purity are important. These are also used in industrial plants for storing chemicals and gases where strong resistance from chemical degradation is required...
Titanium metal, with the symbol Ti, is the ninth most abundant element in the earth‘s crust. It does not occur in large deposits, yet small amounts of titanium are found in almost every rock...