Stainless Steel 304
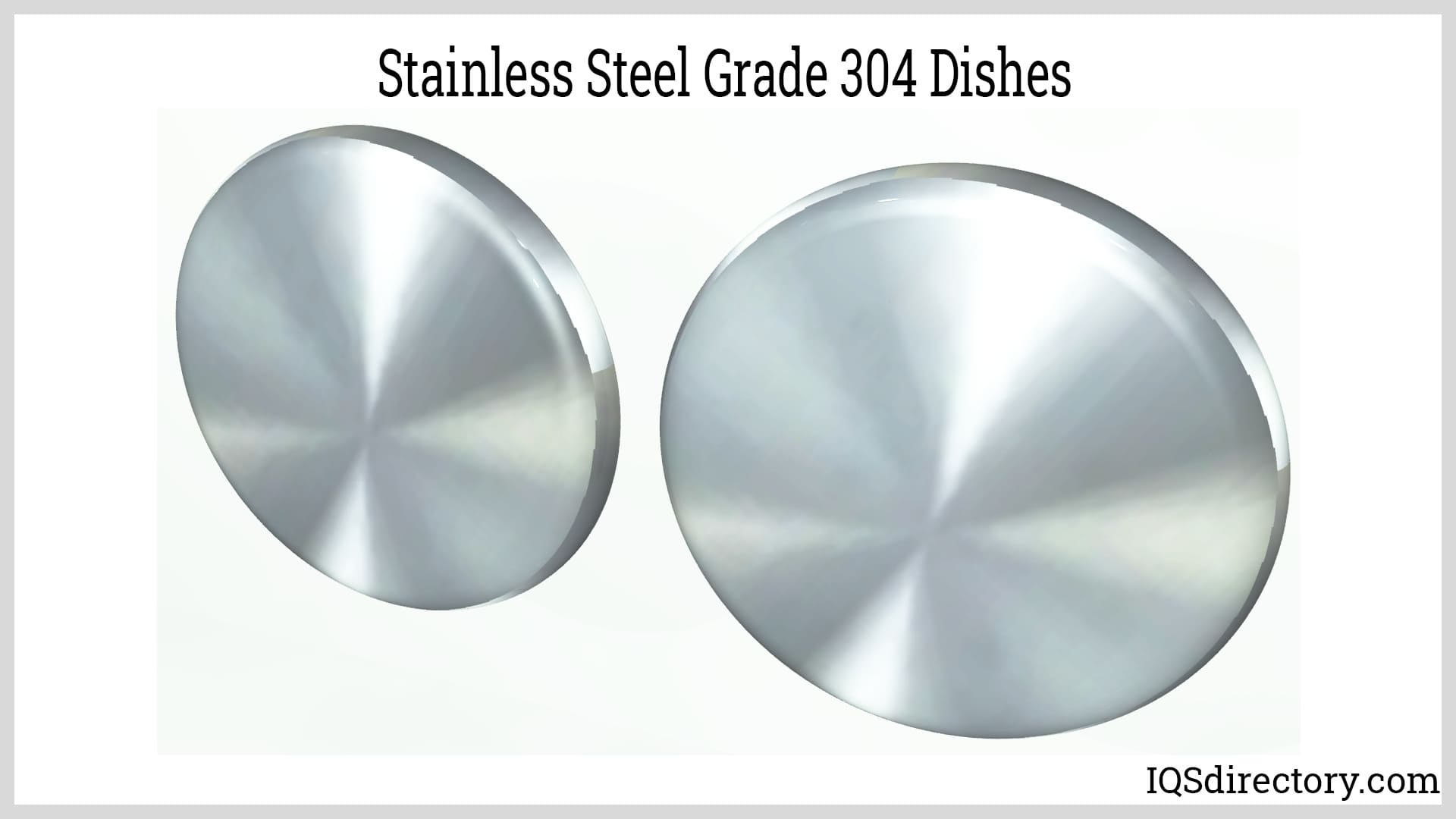
Stainless steel grade 304 is an austenite stainless steel that is the most widely used and versatile of the various grades of stainless steel. It is a part of the T300 series stainless steels with...
Please fill out the following form to submit a Request for Quote to any of the following companies listed on
This article takes an in-depth look at Stainless Steel Fabrication
You will learn:
Stainless steel fabrication involves various manufacturing techniques designed to manipulate, form, and transform metal into a variety of resilient stainless steel items. The primary aim of these fabrication methods is to harness the numerous beneficial traits of stainless steel, enhancing the durability, visual appeal, resilience, and life span of the finished products.
Although steel has been used for centuries for its strength and dependability, stainless steel is a relatively modern alloy, developed just over 100 years ago to solve problems like gun barrel wear. After its invention, the stainless steel industry rapidly progressed, innovating various production techniques.
The evolution of these production techniques has led to a wide spectrum of stainless steel alloys, each crafted for specific purposes. Depending on the alloy’s composition, stainless steel can range from extremely hard and corrosion-resistant to more pliable and soft. This has resulted in three principal classifications: austenitic, ferritic, and martensitic, alongside five main families: austenitic, ferritic, martensitic, duplex, and precipitation hardening.
The broad array of stainless steel families and classifications can be quite intricate, potentially confounding those new to the material.
Additionally, each stainless steel family boasts numerous grades, identifiable by numbers that indicate their attributes and caliber. In the U.S., two primary grading systems are employed: the Society of Automotive Engineers (SAE), utilizing a three-digit code, and the American Society for Testing and Materials (ASTM), using a six-digit code for categorizing more than 200 stainless steel alloys.
Beyond these U.S. grading systems, there are other international standards set by organizations like the International Organization for Standardization (ISO) and in countries such as Japan, Germany, the United Kingdom, Sweden, and China, each with distinct grading mechanisms. This multitude of standards can make finding explicit information on stainless steel alloys quite difficult.
Under the SAE system, Grade 304 stainless steel is categorized as follows:
EN numbers represent a European standard for categorizing metal specifications, grades, and chemical compositions, specifically for steel varieties, initially devised by the British during World War II for streamlined standardization of products. The German equivalent is called the Deutsches Institut für Normung.
Stainless steel is widely recognized for its use in manufacturing a broad range of products, appearing in both everyday items and industrial applications. Its appeal goes beyond its attractive appearance; its durability and resistance to corrosion contribute significantly to its popularity. As a result, stainless steel fabrication has become an essential process in various industries, from construction and architecture to food processing and medical equipment manufacturing. Its non-reactive nature, strength-to-weight ratio, and ability to withstand harsh environmental conditions make stainless steel a top choice for demanding engineering projects.
Various grades of stainless steel can be shaped and processed, with austenitic grades being the most commonly worked. Stainless steel fabrication encompasses a range of traditional techniques used to shape and form metals into various components, tools, and products. The specific fabrication method selected depends on the grade of stainless steel, its alloy composition, and the end-use requirements. Key factors such as machinability, weldability, formability, and heat resistance influence the choice of fabrication method, ensuring the final product meets the desired mechanical properties and functional attributes.
Each stainless steel grade possesses unique properties tailored to meet specific application requirements. While choosing the right grade for fabrication may seem complex, different grading systems, such as the AISI (American Iron and Steel Institute) and ASTM (American Society for Testing and Materials) standards, provide detailed descriptions of each grade’s attributes, simplifying the selection process for engineers and fabricators.
Stainless steel is adaptable to many traditional forming techniques, including machining, punching, cutting, bending, and welding. Despite its significant strength and high hardening ability, it remains highly ductile, allowing for cold forming in both custom and high-volume manufacturing settings. Fabricators adjust their methods based on the stainless steel grade being processed—a crucial factor since the varying combinations of elements in each grade alter the metal’s properties, influencing the fabrication approach, tooling selection, and post-processing treatments.
The extent of work hardening, also known as strain hardening, varies by the stainless steel grade. Austenitic stainless steels (such as grades 304 and 316) experience rapid hardening, an important consideration during processes like cold rolling or forming. Meanwhile, 400 series stainless steels, such as ferritic and martensitic varieties, harden at a rate slightly higher than carbon steel. This work-hardening characteristic is beneficial in applications requiring increased strength, wear resistance, and improved fatigue life.
Stainless steels that exhibit the highest work hardening rates typically have elevated magnetic permeability, such as certain austenitic grades after cold working. Cold working enhances the tensile strength of different grades, potentially reaching up to 2000 MPa. However, as the size of the stainless steel components increases, the feasibility and efficiency of cold working decrease, making it less practical for larger pieces. Proper annealing between forming steps can help mitigate excessive work hardening, ensuring optimal ductility and performance throughout the fabrication process.
Stainless steel grades vary significantly in their welding properties, with each type exhibiting unique characteristics that influence process selection and weld quality. Among these, austenitic stainless steels are known for their superior weldability and are frequently used in pressure vessels, piping, and food industry applications. Martensitic stainless steels, due to their higher carbon content, require careful handling during welding to prevent issues such as thermal cracking and loss of corrosion resistance. Ferritic grades, when welded under the right conditions, also offer excellent weldability, although brittleness and grain growth can be concerns if not managed properly.
Weld quality and the selection of proper shielding gases and filler metals are critical for maintaining the corrosion resistance and structural integrity of stainless steel welds. Choosing an experienced stainless steel fabricator ensures optimal results for both standard and custom stainless steel fabrication projects.
The deep drawing technique is a cold working method performed at ambient temperatures, though post-processing heat treatment can enhance the material's strength. This method is primarily used for drawing complex, deep shapes from 400 series ferritic and 300 series austenitic stainless steels. The 300 series, especially grade 304, is generally preferred for deep drawing applications due to its superior ductility, forming stability, and corrosion resistance, making it ideal for kitchen sinks, cookware, and automotive components.
Due to its tendency to work harden more quickly than carbon steel, stainless steel demands approximately double the pressure for effective stretching and forming. The process is carefully controlled to prevent metal breakage, galling, and surface pitting. The protective chromium oxide layer on stainless steel increases friction during deep drawing, requiring the use of specialized coated and lubricated tools to reduce wear and achieve high-quality finishes.
The efficiency of the deep drawing process is influenced by factors such as lubrication, tool geometry, friction, pressure, and the depth of the draw. Improper speed calibration can result in defects like tearing, breakage, and wrinkles. It is advisable to proceed slowly, particularly as the severity of the draw increases, and to choose stainless steel grades specifically engineered for formability in deep drawing applications to improve productivity and product quality.
Punching involves positioning a stainless steel sheet between a punch and die, both made from hardened tool steel or tungsten carbide, which are highly durable metals designed for precision, abrasion resistance, and longevity. The punch press descends on the sheet, cutting through to create a hole with exact dimensions and shape according to the design. Besides creating holes, punching can also be used to emboss patterns and dimples without fully penetrating the material, offering decorative and functional possibilities for stainless steel components in automotive, electronics, and appliance industries.
Computer Numerical Control (CNC) machining is frequently utilized for punching, blanking, and embossing stainless steel due to its high precision, automation, and efficiency. The flexibility of CNC technology allows for complex, multi-stage punching operations in a single setup and enables a broad spectrum of fabrication tasks—such as notching, louvering, and perforating—to be executed in one cycle, reducing production time and labor costs.
When it comes to cutting stainless steel, methods such as shearing, sawing, waterjet cutting, and both plasma and laser cutting are employed to achieve precise cuts and complex shapes. Although the techniques used are similar to those for cutting carbon steel, the key difference lies in the force required and the potential for work hardening, especially in austenitic grades. Ferritic stainless steel can be cut similarly to carbon steel due to its comparable strength, while austenitic stainless steel requires a lower punch clearance to reduce burr formation and edge distortion.
A major challenge in cutting stainless steel is the wear and potential chipping that cutting tools experience, which affects the tool's edge quality. Utilizing high-speed steel or carbide-tipped blades, along with optimized coolant and lubrication systems, helps extend tool life and enhance cut finishes. To minimize burrs, it is essential to adjust factors such as tool clearance, cutting force, and speed. For thermal cutting processes, such as plasma or laser cutting, both the type of shielding gas (such as nitrogen or argon) and the energy input play significant roles in controlling the amount of burr formation and heat-affected zones.
Many fabricators also use advanced CNC laser cutting and waterjet cutting for intricate shapes, reduced heat distortion, and superior edge quality—making these techniques particularly well-suited for custom stainless steel parts, signage, and high-precision architectural components.
Bending stainless steel allows for the formation of various shapes by manipulating the bend's angle and radius. The techniques employed for bending include V-bending, roll bending, U-bending, edge bending, and wipe bending, each offering unique advantages depending on project requirements, sheet thickness, and material grade. Accurate stainless steel bending depends on factors like bend allowance, springback, and minimum bend radius, which vary across stainless steel grades.
Stainless steel fabricators optimize the bending process by using advanced CAD/CAM software and CNC press brakes to ensure consistent results across both prototyping and large-volume production runs.
Stainless steel undergoes various surface treatments to leverage its strength and durability while enhancing its appearance and performance. These treatments not only serve protective and enhancing purposes but also contribute to the metal's corrosion resistance, cleanability, and aesthetic appeal in architectural, medical, and food-grade applications. Techniques such as cold rolling, electropolishing, passivation, and pickling create a matte, durable finish suitable for architectural use, resulting in a smooth, semi-reflective surface that resists staining and retains hygiene standards.
The fabrication techniques for stainless steel mentioned earlier represent just a subset of the numerous methods available to manufacturers for producing everything from precision medical devices to large architectural panels, industrial piping, and structural supports. When choosing a stainless steel fabrication approach, it is recommended to consult with a skilled fabricator who can offer both standard and custom techniques such as laser cutting, robotic welding, or specialized surface treatments tailored to your project's requirements. Working with experienced stainless steel fabrication companies ensures that finished components meet rigorous industry standards for strength, hygiene, functionality, and longevity.
For buyers and engineers evaluating fabrication solutions, considering factors such as required tolerances, surface finishes, joining methods, and intended application environments can help narrow supplier selection. Leading stainless steel fabricators often provide value-added services such as design assistance, prototyping, finishing, and quality testing, streamlining the process from concept to finished product.
Stainless steel is renowned for its durability, corrosion resistance, and versatility in manufacturing and industrial applications. Each grade, series, and category of stainless steel is designed to fulfill specific application needs, offering unique mechanical and chemical properties. The extensive range of stainless steel types contributes to its widespread use across industries such as construction, automotive, food processing, medical device manufacturing, and chemical processing. Selecting the appropriate stainless steel for fabrication can appear intricate and daunting, given the broad spectrum of alloys and finishing options. To assist users in choosing the optimal type for products and components, stainless steel manufacturers have developed detailed classification systems based on global standards.
Stainless steel types and grades are suited to various applications, from structural components and pressure vessels to cookware, surgical instruments, and marine equipment. When selecting a grade for a fabrication project, it is essential to consider factors such as the end-use environment (indoors or outdoors), the product type, forming and machining methods, temperature requirements, corrosion resistance, and the fabrication equipment involved. Careful material selection ensures enhanced performance, longevity, and cost-effectiveness.
Choosing the right stainless steel involves understanding the different grades, which are categorized into five main families: austenitic, ferritic, martensitic, duplex, and precipitation hardening. The austenitic stainless steel family is the largest group, composed of steel combined with nickel or manganese and nitrogen, known for exceptional corrosion resistance and excellent weldability.
Ferritic stainless steel primarily consists of carbon steel and chromium, whereas martensitic stainless steels vary in their mix of iron, chromium, and carbon. The specific properties of martensitic stainless steel depend on the exact composition and additional alloying elements used to achieve targeted performance, such as increased hardness, tensile strength, or improved machinability. Duplex stainless steel blends austenite and ferrite in varying proportions and ratios, resulting in hybrid properties suitable for demanding environments.
Precipitation hardening (PH) stainless steel is a specialized type that undergoes a heat treatment process to enhance its yield strength, making it ideal for high-temperature applications and precision components. This process involves heating the stainless steel to a very high temperature, rapidly cooling it (quenching), and then reheating it to an intermediate temperature to achieve exceptional mechanical performance.
Grades of stainless steel are identified by a numbering system, which varies between Great Britain, the International Organization of Standardization (ISO), Japan, Europe, the United States, Germany, and China. Regardless of the system, all organizations base their system on the properties, characteristics, and standards for stainless steel. Understanding stainless steel grade numbers, such as 304 or 316, helps users compare performance characteristics and select materials that meet regulatory or industry requirements for strength, corrosion resistance, temperature tolerance, and weldability.
Stainless steel alloys are classified into five broad categories according to the specific alloy compositions used in their production. Among these categories, ferritic, martensitic, and austenitic are the most commonly utilized, with austenitic stainless steel being the most widely used grade in manufacturing. Each category presents a unique balance of ductility, toughness, hardness, and corrosion resistance, making the proper selection crucial for fabricators and engineers seeking the right steel for their projects.
Ferritic stainless steel has over 12% chromium content with low carbon content, which makes it non-hardenable and imparts natural high corrosion resistance. It differs from other stainless steels in its molecular grain structure and chemical makeup. Ferritic stainless steel is magnetic due to its body centered cubic (BCC) lattice structure, contributing to its performance in certain design applications. In addition to chromium and carbon, ferritic stainless steel incorporates small quantities of manganese, molybdenum, niobium, and titanium—elements that enhance stabilization, strength, and weldability.
Ferritic stainless steel is designated by the series number 400, which is further divided into five distinct groups:
Ferritic stainless steel cannot be hardened through thermal methods but is amenable to shaping through cold working processes, such as cold rolling, which improve its formability and structural integrity. It is characterized by its magnetic properties, excellent ductility, and inherent resistance to stress corrosion cracking. The most widely used grade is type 430, which contains 16 percent chromium and is commonly found in kitchen appliances, automotive trim, heat exchangers, and architectural applications. Ferritic stainless steels are generally more cost-effective compared to austenitic and duplex grades, making them a practical solution for large-scale manufacturing where corrosion resistance and moderate strength are required.
Austenitic stainless steel is the most commonly used type of stainless steel worldwide, thanks to its superior corrosion resistance, high tensile strength, and remarkable formability. It can be welded, formed, shaped, and reconfigured for a variety of purposes, including hygienic applications, architectural panels, and pressure vessels. It is a face centered cubic (FCC) iron or steel alloy, typically containing 10.5% chromium, 5% to 12% nickel, and small percentages of nitrogen and carbon. Austenitic stainless steel can be cold worked to improve its hardness, strength, and resistance to stress, making it suitable for food service, medical instruments, and chemical storage tanks. It can also be heat treated to be shaped, returning to its original strength upon cooling. Austenitic stainless steel is classified in the 200 and 300 series of stainless steel.
The 300 series of austenitic stainless steel features grade 304, the most widely used stainless steel alloy, containing 18 percent chromium and 8 percent nickel; and grade 316, which includes 16 percent chromium, 10 percent nickel, and 2 percent molybdenum for enhanced pitting resistance in chloride environments. While most austenitic stainless steels can be hardened through cold working, they do not respond to heat treatment. Key properties of austenitic grades crucial for industrial and commercial fabricators include:
Austenitic stainless steel is divided into series 200 and series 300, with nickel being the dominant alloy in series 300 (e.g., 304, 316). Series 200 primarily uses manganese and nitrogen as partial substitutes for nickel, providing a lower-cost option with good general corrosion resistance and high strength, although typically less corrosion resistant than the 300 series. Both series support cleanroom use, marine hardware, kitchenware, and pharmaceutical equipment, where hygiene and resistance to corrosive agents are essential.
Notable grades in the 300 series include:
If you are evaluating stainless steel for your fabrication projects, austenitic grades are often the default choice for high-performance, corrosion-resistant components that require strength, ductility, and ease of manufacture.
Martensitic stainless steel falls under the 400 series and is composed mainly of iron and chromium alloys. Unique among stainless steel families, martensitic types can be hardened and tempered through controlled heat treatment processes and are well-suited where both wear resistance and moderate corrosion resistance are required—such as in cutlery, surgical instruments, fasteners, and pump shafts. This family exhibits good ductility, magnetism, and increased strength, with Type 410 particularly favored for withstanding mechanical stress under harsh conditions.
The chromium content in martensitic stainless steel ranges from 11.5% to 18%, with about 1.2% maximum carbon and a small amount of nickel. The high carbon content provides a robust molecular structure for improved hardness and tensile properties, while the limited nickel content reduces general corrosion resistance compared to austenitic or duplex grades. Additional alloying elements may include manganese, molybdenum, and vanadium to further enhance specific properties such as toughness and resistance to brittle fracture.
Martensitic stainless steel is categorized into low carbon and high carbon types. Low carbon martensitic stainless steel contains 0.05% to 0.25% carbon, whereas high carbon types feature 0.61% to 1.5% carbon. Higher carbon levels yield greater mechanical strength and edge retention but can reduce weldability and increase brittleness. Martensitic stainless steels are engineered to withstand cyclic mechanical stresses, abrasive forces, and both wet and dry environments.
Key grades of martensitic stainless steel include:
Understanding the balance between hardness, machinability, and corrosion resistance offered by martensitic stainless steels is essential for engineers designing components exposed to high friction, repeated mechanical loads, or corrosive industrial environments.
Duplex stainless steel (DSS) alloys feature high chromium content (18%–28%) and moderate nickel content (1.5%–8%). The term "duplex" denotes its dual-phase microstructure, consisting of approximately equal volumes of austenite and ferrite, resulting in a combination of strength, toughness, and enhanced stress corrosion cracking resistance. This hybrid microstructure is valuable in industries such as oil and gas, petrochemical, pulp and paper, and desalination, where both mechanical and corrosive challenges are severe.
Duplex stainless steel is divided into several subgroups: lean, standard, super, and hyper duplex. These alloys offer greater toughness than ferritic grades and approximately double the strength compared to common austenitic stainless steels. Their corrosion resistance is superior to standard austenitics (such as grades 304 and 316), particularly against chloride-induced pitting and crevice corrosion—making them ideal for marine, chemical processing, and coastal construction uses. Grades of duplex stainless steel are typically numbered in the 2000s.
Subgroups of duplex stainless steel include:
For users evaluating stainless steel in projects requiring both high mechanical strength and top-tier resistance to corrosion or stress corrosion cracking, duplex stainless grades offer an optimal solution—helping to expand lifetime, reduce maintenance intervals, and lower total cost of ownership in harsh industrial conditions.
A distinctive family within stainless steels is precipitation hardening (PH) stainless steel, renowned for its remarkable combination of strength and corrosion resistance. This alloy category boasts yield strengths three to four times greater than that of standard austenitic stainless steel while maintaining comparable corrosion resistance. PH stainless steels are engineered by integrating elements such as copper, molybdenum, aluminum, and titanium. The key advantage stems from a specialized heat treatment (aging or precipitation process), which improves crystal structure for superior mechanical performance. These steels are available in low carbon martensitic, semi-austenitic, and fully austenitic forms, supporting applications from aerospace components and turbine blades to high-performance valves and precision fasteners.
Among PH stainless steels, the martensitic 17-4PH is particularly common, featuring 17% chromium and 4% nickel. Precipitation hardening treatments enable this alloy to achieve tensile strengths from 850 MPa to 1700 MPa, and yield strengths between 520 MPa and over 1500 MPa—outperforming austenitic grades like 304 and 316 for components where dimensional stability, wear resistance, and load-bearing capacity are critical.
Categories of precipitation hardening stainless steel include:
When selecting stainless steel for high-performance, precision-fabricated products, understanding how precipitation hardening can dramatically enhance strength, fatigue life, and wear resistance will help you achieve superior results in demanding environments.
Modern appliances and industrial products are made of stainless steel due to its ability to adapt to extreme temperatures, corrosion and rust resistance, and superior strength. The main stipulations for stainless steel products are that they require limited care and can endure all forms of use. The popularity of stainless steel rests in its ability to meet stringent and exacting requirements, especially its ability to maintain its appearance in stressful conditions.
Stainless steel is non-porous, scratch resistant, and sturdy enough to make it ideal for sanitary and antiseptically clean conditions, such as large kitchens, where it is used as cutlery, and cookware. Counter tops, cookware, and utensils in the food processing industries are made from stainless steel to meet the exacting requirements of the Food and Drug Administration (FDA) and local health inspectors.
In the oil and gas industries, corrosion-resistant pipes are crucial for withstanding the severe conditions found at offshore drilling sites. The corrosive environment can lead to pipe failures and pose significant risks. Robust stainless steel pipes are essential to maintaining safety and reliability in these operations.
Desalination is the process of extracting salt and minerals from seawater to produce fresh water suitable for drinking or irrigation. This technique is employed in submarines and ships and is crucial for providing potable water to regions with scarce fresh water resources. Given that saltwater can corrode and damage standard pipes, stainless steel pipes are highly effective and durable for use in desalination systems.
Chemical plants handle highly corrosive and toxic substances like acids and oxidizers, which can damage standard piping and materials. To ensure thorough removal of hazardous residues, storage tanks and pipes are often cleaned with bleach, a process that many metals cannot withstand.
By the late 20th century, duplex stainless steel became a popular choice in the chemical industry due to its superior strength and resistance. Advances in chemical processing demanded more robust and durable materials, and duplex stainless steel's remarkable resistance to chloride-induced stress corrosion cracking has led to its increased adoption in the sector.
Duplex stainless steel is also becoming increasingly popular in the construction of bridges and other structures due to its strength, which is twice that of ferritic stainless steel. Its superior strength allows for the use of less material to achieve the same structural integrity, making duplex stainless steel both cost-effective and weight-efficient.
The medical field demands that all instruments, equipment, and tools be both antiseptically clean and sterile. Only a few metals can endure the rigorous cleaning processes necessary to meet these standards. Stainless steel is preferred for manufacturing medical instruments and equipment due to its ability to withstand the intensive disinfecting treatments required by healthcare professionals.
The chromium in stainless steel enhances its resistance to scratches and corrosion, which is crucial for cleaning and sterilization. Nickel contributes to a smooth, even surface, while molybdenum adds hardness, helping medical tools retain their strength and shape. Stainless steel is used for surgical cutting tools because it maintains its sharp edge and cleanliness after sterilization.
Stainless steel's numerous advantageous properties make it an excellent choice for structural load-bearing applications. Austenitic and duplex grades are often hot rolled and welded into sheets, plates, bars, and tubes for use in structural sections, while other sections may be cold-formed. Additionally, bolts, screws, and various fasteners are manufactured from stainless steel due to its exceptional strength and durability.
Common stainless steels utilized in structural applications include austenitic grades such as series 304 and series 316, as well as duplex stainless steel grades 321, 322, and 323. For specific structural uses, ferritic stainless steels with a thickness of 3 mm and a nickel content ranging from 2% to 4% are also employed.
Duplex stainless steel is commonly used for constructing storage and cargo tanks on ships, while austenitic grades are preferred for navigation tankers. Stainless steel is employed in various ship components, including piping, pulpits, hinges, propeller shafts, railings, accents, fasteners, and shackles. Despite its high cost preventing its use for ship hulls, stainless steel is extensively utilized in other parts of ships due to its excellent resistance to corrosion and rust, making it particularly valuable for crucial ship components.
Power generation plants need materials that can withstand high temperatures and intense pressure. Stainless steel has been a material of choice for traditional coal-fired plants due to its durability. In contemporary power plants, it is used in various applications including cooling systems, heat exchangers, combustion components, boiler superheaters, reheater tubing, and water panels. Additionally, stainless steel is in high demand for nuclear power plants, where it is utilized for tanks, chimneys, and containment canisters.
Stainless steel is widely used for manufacturing storage tanks due to its excellent resistance to corrosion and rust. These tanks are ideal for holding corrosive substances such as chemicals, gases, and bulk materials like food and water, as stainless steel does not impart any flavor or odor to the contents.
Industries such as agriculture, fire protection, and fuel transport and storage rely on stainless steel for their storage tanks because of the material’s strength and durability. This is particularly crucial in the chemical industry, where tanks must not react with the substances they contain.
Stainless steel is commonly used to produce drawn wire, a process that involves pulling or pushing the metal through a die under significant stress and force. The diameter of the wire affects its tensile strength and hardness. Only certain grades of stainless steel, capable of being drawn into wire, are used for this purpose. The most frequently used grades are from the 300 series, including 302, 304, and 316. Cold drawing further enhances the strength of these grades.
The many grades and families of stainless steel can make selecting the right grade for a project difficult. There are several factors to consider when designing a stainless steel product, such as the required strength and necessary work hardening as well as other characteristics that play a part in the fabrication process.
While stainless steel is renowned for its strength and resistance to corrosion, not all types and grades possess these properties to the same extent. Each grade and type of stainless steel offers varying levels of corrosion resistance, strength, and durability. Therefore, it is important to understand the specific properties of each type and grade before choosing stainless steel for manufacturing a product.
Stainless steel is widely used in construction projects due to its aesthetic appeal and strength. It is commonly found in exterior features such as railings, siding, fixtures, countertops, and backsplashes. Its durability and resilience, combined with its attractive appearance, contribute to its long-lasting performance in various applications.
Since the 1930‘s, stainless steel has played a major part in the production of automobiles. Initially, it was used for exhaust systems, trim, and other non-structural purposes. With the advent of increased emissions standards, stainless steel has become an important component in the structure and design of automobiles.
Stainless steel has profoundly influenced the medical instrument industry because of its ease of sterilization and resistance to corrosion. In addition to surgical tools, stainless steel is used in medical implants like hip joints. It is also essential for pins and plates used in the repair of broken bones.
High carbon grades of stainless steel are popular and widely used in a variety of industries from the chemical processing of paper to the production of foods and beverages. Depending on the product and industry, the 400 series, with less corrosion resistance, may be used while the 300 series with good corrosion resistance may be preferred due to its lower cost and surface finishes.
Stainless steel grade 304 is an austenite stainless steel that is the most widely used and versatile of the various grades of stainless steel. It is a part of the T300 series stainless steels with...
Stainless steel is a type of steel alloy containing a minimum of 10.5% chromium. Chromium imparts corrosion resistance to the metal. Corrosion resistance is achieved by creating a thin film of metal...
Stainless steel grades each consist of carbon, iron, 10.5%-30% chromium, nickel, molybdenum, and other alloying elements. It is a popular metal used in various products, tools, equipment, and structures that serve in many industrial, commercial, and domestic applications...
Stainless steel tanks are widely used in food, beverage, dairy, medicine, cosmetics, and other manufacturing processes where cleanliness and purity are important. These are also used in industrial plants for storing chemicals and gases where strong resistance from chemical degradation is required...
Stainless steel tubing is a multifaceted product that is commonly utilized in structural applications. Stainless steel tubing diameters and variations vary greatly based on the application requirements and are...
Precision sheet metal fabrication is a common manufacturing process where the structure of a metal workpiece is cut, bent, and assembled by machining. There are any number of operations that are performed in the creation of a finished sheet metal product...
Perforated stainless steel is cut, punched, or stamped to produce a precise pattern of holes or apertures. It is used for functional reasons, such as filtration or ventilation, and aesthetic ones, such as architectural accents...
Sheet metal fabrication is metal that has been formed into thin and flat sheets which is then cut and bent into various shapes. Different metals, brass, steel, copper, tin, titanium, aluminium, etc., can be made into sheet metal...
Secondary manufacturing processes, or fabrication, work on products from primary processes to create a metal part or structure that is suitable for end-use. In these processes, semi-finished metal products are reshaped and joined...
Titanium metal, with the symbol Ti, is the ninth most abundant element in the earth‘s crust. It does not occur in large deposits, yet small amounts of titanium are found in almost every rock...