Stainless Steel 304
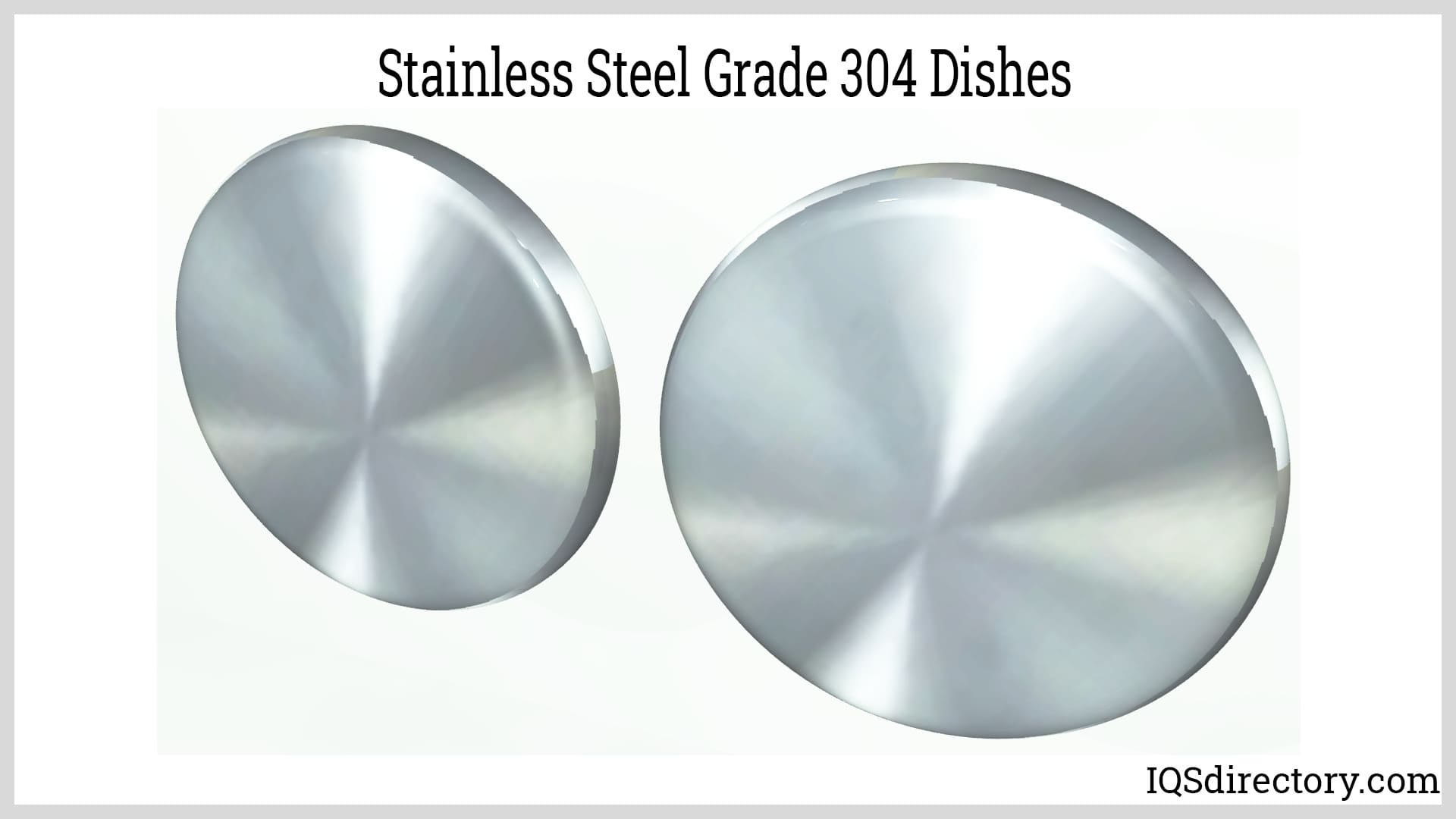
Stainless steel grade 304 is an austenite stainless steel that is the most widely used and versatile of the various grades of stainless steel. It is a part of the T300 series stainless steels with...
Please fill out the following form to submit a Request for Quote to any of the following companies listed on 400 Stainless Steel .
Describes uses for stainless steel series 400 grades 410, 416, and 420, how they are made, and where to purchase them.
You will learn:
The 400 series of stainless steels are distinguished by their significant carbon content, endowing them with remarkable strength and resistance to wear. In contrast to austenitic stainless steels, the 400 series offers less corrosion resistance but can undergo hardening via heat treatment, making it well-suited for a range of tough applications.
Products in the Stainless Steel 400 Series | |
---|---|
Stainless Steel Plate | Mill Plates and Coil Plates |
Stainless Steel Sheet | 2B/2D Finish, Polished Sheet, and Perforated Sheet |
Stainless Steel Structural | Includes Structural beams, tubes, and channels |
Stainless Steel Tubular | Available forms: rectangular, square, and circular tubing |
Choosing 400 series stainless steels hinges on various criteria. These steels, often with a martensitic structure, can be hardened through heat treatment and aging. Unlike other stainless steel series, the 400 series is known for its significant hardness, strength, and wear resistance, with Grade 410 as a general-use stainless steel, Grade 416 as the premier free machining option, and Grade 420 noted for its high hardness.
Grade 410 stainless steel includes 11.5% chromium, offering some corrosion resistance—a quality that can be further improved by polishing, tempering, and hardening. Recognized for its versatility, Grade 410 is commonly used in the manufacture of knife blades, scissors, culinary tools, and firearm parts.
The enhanced machinability of Grade 416 is partly attributed to its sulfur and phosphorus content. Its widespread use is also due to its lower cost and ease of availability. Grade 416’s tensile strength ranges from 510 MPa to 800 MPa, with a hardness rating between 230 HB and 320 HB.
Grade 420 stainless steel is lauded for its exceptional hardness and wear resistance compared to Grade 410, making it perfect for applications necessitating toughness. Its elevated carbon content enables its hardness to be increased to 55+ HRC through heat treatment. Grade 420 is widely used in the production of knife blades, scissors, surgical tools, firearm clips, hip implants, and industrial cutting implements. While its corrosion resistance is moderate, it can be enhanced through polishing and tempering to suit environments where strength and resistance to wear are crucial.
Each type of stainless steel is engineered to possess specific properties tailored for its ideal applications. Series 400 stainless steel is especially valued in industrial manufacturing for its higher carbon content, which increases strength and wear resistance compared to other stainless steel alloys. While it excels in durability, wear resistance, and machinability, it is somewhat less resistant to corrosion and rust than austenitic grades like Series 300. The composition for Series 400 stainless steel generally consists of iron with a chromium content ranging from 11% to 27%, up to 1% carbon, and approximately 2.5% nickel. The series primarily features a martensitic crystalline structure, though some ferritic grades also exist. This martensitic microstructure results in considerable variation in strength and hardness between different grades, making Series 400 ideal for engineering, cutlery, valves, and automotive components where mechanical performance is crucial.
The manufacturing of Series 400 stainless steel is a multi-stage process that ensures the final product achieves optimal performance, corrosion resistance, and formability for its intended industrial or commercial uses. Each element is carefully selected and measured to maintain precise chemical compositions, aligned with specific standards for grades 410, 416, and 420. Accurate formulation is crucial—variances in elemental purity can impact critical characteristics such as machinability, tensile strength, ductility, resistance to oxidation, and suitability for heat treatment.
Melting – After gathering the required raw materials, the blend is introduced into a melting furnace. These furnaces, including electric arc and coreless induction types, achieve temperatures required to melt high-alloy stainless steels. Consistent and uniform alloy mixing is vital—the process can last 8 to 12 hours, resulting in a homogeneous molten mixture. This step establishes the foundational structure and quality of the finished product, directly impacting metallurgical properties like microstructure and grain size.
Excess Carbon Removal – Precise control of carbon content is essential for achieving the right balance of hardness and corrosion resistance. During the refining stage, technologies like vacuum oxygen decarburization (VOD) and argon oxygen decarburization (AOD) are employed to remove excess carbon from the molten steel. This stage is carefully monitored and regulated, as even minor deviations in carbon content can dramatically affect the mechanical properties and weldability of Series 400 stainless steels, especially martensitic grades like 410, 416, and 420.
Forming Stainless Steel Series 400 – Once uniformity is ensured, the molten stainless steel is formed via continuous or ingot casting. Continuous casting allows for direct creation of semi-finished shapes such as billets, blooms, slabs, bars, tubes, and sheets, supporting various industries like automotive manufacturing, construction, and precision engineering. Proper cooling and solidification is performed, often with water-cooled molds, to minimize defects and ensure desirable mechanical characteristics.
Cutting and Shaping – To meet customer and application specifications, the cold or hot-worked billet is cut and shaped using advanced methods such as CNC machining, metal shearing, and laser cutting. These methods provide precise dimensional tolerances vital for industries like aerospace, defense, and energy, where Series 400 stainless steel is commonly used for gears, fasteners, and structural components.
Surface Finishes – High-performance finishing techniques such as rolling, polishing, and abrasive blasting are used to improve the final surface of Series 400 stainless steel. These finishes enhance durability, corrosion resistance, and aesthetics, while also reducing friction and increasing cleanliness. The proper surface finish improves performance in demanding environments, protects against oxidation, and can add value through mirror finishes or protective coatings for specialized markets.
The choice of surface finish is crucial for ensuring that Stainless Steel Series 400 meets the requirements of its target application. These ferritic and martensitic stainless steel grades are often selected for their superior strength, hardness, and wear resistance over visual appeal. Due to lower chromium content and limited nickel additions, corrosion resistance is not as high as austenitic grades; therefore, supplementary coatings or passivation treatments are applied to help resist rust and increase service life in aggressive environments.
Stainless Steel Grade 410, a martensitic stainless steel, is manufactured following the general steps outlined above, but with specifications finely tuned for performance in demanding environments. Melted and cast into ingots, Grade 410 is hot worked through forging, rolling, or extrusion to achieve optimal dimensional accuracy and mechanical performance. Subsequent annealing stages increase ductility and facilitate further processing such as machining, drilling, and forming. Industries often hot roll or cold roll Grade 410 for products like industrial blades, cutlery, fasteners, and pump shafts that require both strength and workability.
Specialized finishing techniques such as precision polishing and abrasive blasting are used to improve corrosion resistance and surface qualities. Heat treatment is a critical step: Grade 410 stainless steel is typically heated to 750°C up to 820°C (1382°F up to 1508°F), then rapidly quenched in oil, air, or water. Quenched metal is brittle, so tempering is necessary to restore mechanical balance—relieving internal stresses, increasing toughness, and enhancing ductility. This suite of manufacturing and treatment steps ensures that Stainless Steel 410 finds broad use in industries requiring durability, moderate corrosion resistance, and service in mildly aggressive environments.
If higher machinability or better surface finish is required, grades such as 416 stainless steel (sulfur-enhanced for machinability) and 420 stainless steel (higher carbon content for sharper hardness) may be specified. Each grade within the Series 400 family is selected based on required hardness, machinability, corrosion resistance, and ease of fabrication for tools, valves, surgical instruments, and cutlery.
Mechanical tests are essential to ensure that Series 400 stainless steels, including 410, 416, and 420, meet industry standards for strength, hardness, and toughness. These tests include tensile strength assessment, Brinell hardness tests, and Charpy V-notch impact testing, among others. By rigorously evaluating resistance to loads, bending, and impacts, manufacturers can guarantee that their stainless steel products will perform reliably in applications ranging from industrial tooling to automotive components. For critical use cases, additional fatigue, yield stress, and elongation tests are conducted to validate performance under cyclic and long-term loads.
Chemical testing is vital for verifying the chemical composition of 400 Series stainless steels, confirming compliance with ASTM or ISO standards. Non-destructive spectrochemical analysis is the preferred method for grade identification, detecting key alloying elements like chromium, carbon, sulfur, and nickel. Corrosion resistance, a defining property of stainless steel, is evaluated using rigorous salt spray testing as well as pitting and crevice corrosion tests. The longer a sample remains unmarred by salt spray, the higher its corrosion resistance—vital for automotive, food processing, petrochemical, and marine applications. These analytical results validate that the manufactured steel grade matches the specifications required for demanding industrial and commercial environments.
Stainless steel grade 410 is one of the most widely used martensitic stainless steels, valued for its versatility and balance of mechanical properties. As a general-purpose stainless steel, grade 410 is commonly chosen for its excellent hardness, high strength, and moderate resistance to corrosion, making it suitable for a diverse range of industrial and commercial applications. In addition to its easy availability and relatively low cost, stainless steel grade 410 is marginally machinable and formable compared to other grades. Its affordability is attributed to the limited amounts of expensive alloying elements, especially nickel, used in its composition and manufacturing process, resulting in cost-effective solutions for fabrication needs.
The manufacturing process for stainless steel 410 follows the standard steps typical of stainless steel production, beginning with melting and alloying, then casting into ingots. These ingots are heated and hot worked through forging, rolling, and extrusion methods. Subsequent shaping is often followed by annealing, which enhances the ductility and workability of the material. Finishing techniques such as hot rolling, cold rolling, and additional annealing or heat treatments are used to optimize the steel’s mechanical properties, surface quality, and corrosion resistance. Optional polishing can further improve the aesthetic appearance and resistance to oxidation of stainless steel 410 products.
As with other grades in the 400 series stainless steel family, grade 410 offers reliable corrosion resistance, which can be significantly enhanced through specialized hardening, tempering, and polishing treatments. These heat treatments alter the microstructure, increasing both hardness and resistance to corrosion and wear—crucial factors in applications demanding durability and longevity. When properly treated, stainless steel 410 demonstrates strong corrosion resistance in moist and wet environments as well as settings with mild chemicals. However, it is important to note that this grade is not recommended for use in saltwater or highly acidic environments, where the alloy’s corrosion resistance could be compromised.
The increased carbon content of stainless steel 410, typically around 0.1%, imparts substantial strength and hardenability while moderately reducing ductility compared to austenitic stainless steels. Its 12% chromium content facilitates the formation of chromium carbide compounds, which contribute to the alloy’s wear resistance, edge retention, and ability to maintain structural integrity under thermal stress. The carefully balanced composition of elements—including iron, chromium, and carbon—gives stainless steel 410 resistance to high temperature oxidation, scaling, and stress corrosion cracking, making it an outstanding choice for heat-treated components, valves, pumps, bolts, and machinery parts.
Composition of Stainless Steel Grade 410 | ||||
---|---|---|---|---|
Alloy | Alloy | |||
Iron | 85% or Higher | Manganese | 1.0% or Less | |
Carbon | 0.08-0.15% | Silicon | 1.0% or Less | |
Chromium | 11.5 to 13.5% | Sulfur | 0.03% or Less | |
Nickel | 0.75% or Less | Phosphorus | 0.04% or Less |
Stainless steel 410 grades can be reliably cut, shaped, and formed by being worked, quench hardened, and tempered, which allows for high flexibility in manufacturing various industrial components. However, compared to austenitic grades such as stainless steel 304 and 316—well-known for their superior machinability and formability—grade 410 presents more challenges in machining and forming processes. As a result, grade 304 or grade 316 stainless steel is sometimes preferred for intricate or high-precision fabrication, especially where enhanced corrosion resistance or ductility is needed.
Grade 410 is classified as air-hardening martensitic stainless steel and requires preheating before welding, as well as annealing prior to cooling, to prevent unwanted hardening and potential cracking. It supports limited cold forming when annealed and may be hot formed at elevated temperatures ranging from 750°C to 1150°C (1382°F – 2102°F). For lighter forming processes, such as bending or light stamping, preheating temperatures may be lower. Although grade 410 is machinable, it is commonly annealed before the process, followed by decontamination and passivation to restore corrosion resistance disrupted during machining. This makes stainless steel 410 ideal for precision-engineered parts, fasteners, cutlery, surgical instruments, and structural applications where toughness and wear resistance are critical.
The melting point of stainless steel 410 is 1495°C (2729°F). It offers a density of 7.65 g/cm³ (0.276 lb/in³), specific gravity of 7.65, and a modulus of elasticity in tension of 29x10⁶ psi or approximately 200 GPa. Mechanical properties include a tensile strength of approximately 65,000 psi and a yield strength of 30,000 psi. On the Rockwell hardness scale, stainless steel 410 typically measures HRB80 when annealed, aligning with the requirements for low-carbon structural steel applications. These physical and mechanical properties make grade 410 suitable for environments where moderate corrosion resistance, high hardness, and wear resistance are priorities.
The martensitic microstructure of grade 410 stainless steel provides ferromagnetic properties, distinguishing it from non-magnetic austenitic alloys. During heat treatment, the transition from austenitic to martensitic crystalline structure dramatically increases strength and hardness, while introducing magnetic capabilities. These characteristics make stainless steel 410 a preferred choice for applications requiring both structural robustness and magnetic responsiveness—such as magnetic assemblies, sensors, separators, and industrial cutting tools.
When selecting stainless steel grade 410 for a project, it’s important to carefully consider the intended application, environmental exposure, and required mechanical properties. Users frequently evaluate stainless steel 410 for its balance of affordability, machinability, and corrosion resistance compared to other stainless steel alloys. Grade 410 excels in oil and gas, automotive, aerospace, and food processing industries where durability and moderate corrosion resistance are vital. For buyers seeking to source stainless steel 410, ensure the supplier can deliver the required heat treatment, surface finish, and certification to meet industry standards such as ASTM A240/A276. Understanding these variables will help you determine if grade 410 is the optimal alloy for your application or if an alternative stainless steel, such as grade 420 or duplex stainless, would be more suitable for aggressive chemical environments or highly corrosive service conditions.
Stainless steel grade 416 has the highest machinability of all of the different stainless steels with a rating of 85%. The rating scale for machinability was established by the American Iron and Steel Institute (AISI) and is expressed as a percentage with carbon steel having a 100% rating, which means it is easy to machine. As the percentage for a metal moves below 100%, it is determined to be difficult to machine. Most stainless steels are in the 40% to 80% range.
The manufacture of stainless steel grade 416 follows the same process as that which is used for grade 410 and is a variation of grade 410 with a higher sulfur content to increase its machinability. Once grade 416 is formed into sheets, bars, rods, and pipes, it is hardened and polished to increase its resistance to corrosion. To increase its resistance to oxidation, it is heat treated at 760°C (1400°F).
Grade 416 is resistant to acids, alkalis, fresh water, and dry air but is less corrosion resistant than non-machinable stainless steels. In order to enhance the corrosion resistance of grade 416, it is hardened, which gives it a smooth surface. The hardening process for grade 416 involves heating the metal to 925°C up to 1010°C (1742°F up to 1850°F) followed by oil quenching and tempering.
In order to weld grade 416, the metal has to be preheated to 200°C up to 300°C (392°F up to 572°F), which is followed by annealing or stress relief. Grade 410 electrodes are ideal for the grade 416 welding process, and grade 309 filler rods can be used, as well.
Stainless steel grade 416 is the grade of stainless steel that is most often used for machining. The reason for the high machinability of grade 416 is its high sulfur content. In addition, grade 416 can be heat treated to further enhance its machinability, which gives it an improved machinability performance over austenitic 300 series stainless steels.
The machinability of all stainless steels is dependent on the elements and materials that are added to it. Many of the elements that are added increase stainless steel’s strength but make it difficult to machine, such as chromium, nickel, and molybdenum. The addition of sulfur increases the metal's machinability since it lowers the shear strength of inclusions that act as stress risers and weaken the steel. The lowered shear strength makes it possible for machined chips to break away from the work area more efficiently and helps avoid the build up of waste on the cutting tool, known as bird nesting. In addition to sulfur, other additives used to enhance machinability include selenium and calcium.
Composition of Stainless Steel Grade 416 | ||||
---|---|---|---|---|
Alloy | Alloy | |||
Iron | 85% | Manganese | 1.25% | |
Carbon | 0.15% | Silicon | 1.0% | |
Chromium | 12 to 14% | Sulfur | 0.15% | |
Phosphorus | 0.06% |
Stainless steel grade 420 is a modified version of grade 410 with a higher carbon content, which increases its hardness and improves the metal’s strength and wear resistance. In annealed condition, it has good ductility and can be hardened up to 50 RHC. The corrosion resistance for grade 420 improves after the metal has been hardened and surface ground or polished.
In a hardened condition, stainless steel grade 420 has corrosion resistance against the atmosphere, foods, fresh water, alkalies, acids, steam, and crude oil. The strength and durability of grade 420 is due to its high carbon content, which also gives it higher hardness than grades 410 and 416. Stainless steel grade 420 has the highest hardness level of all of the low chromium stainless steels.
The ability to machine stainless steel grade 420 varies and depends on its level of hardness. When it is hardened to under 30 RHC, it is relatively easy to machine. If the hardness is over 30 RHC, the ability to machine it becomes difficult and challenging. If grade 420 is used above 427°C (800.6°F), it softens and loses its corrosion resistance.
The physical properties of stainless steel grade 420 depend on how it is tempered. In many cases, customers discuss with manufacturers how the metal is to be used, which allows manufacturers to temper it appropriately.
The introduction of stainless steel 420 was due to the demand for a stainless steel with superior hardness and exceptional wear resistance for the manufacture of tools, medical instruments, and cutlery. A unique feature of stainless steel grade 420 is its edge retention, which was the main reason for its development, as well as its toughness.
Stainless steel grade 420 can be welded using welding rods made of stainless steel grade 309. For purposes of welding, grade 420 is heated to 150°C up to 320°C (302°F up to 608°F). After which, welded parts are post heated.
As with grades 410 and 416, stainless steel grade 420 is used for a variety of applications. It is designed for applications that require a stainless steel with high hardness. The edge retention of stainless steel 420 makes it ideal for the manufacture of cutlery, surgical tools, scissors, shear blades, and knives.
Composition of Stainless Steel Grade 420 | ||||
---|---|---|---|---|
Alloy | Alloy | |||
Carbon | 0.41% | Vanadium | 0.046% | |
Chromium | 12.69% | Copper | 0.05% | |
Manganese | 0.74% | Phosphorus | 0.025% | |
Silicone | 0.33% | Sulfur | 0.001% | |
Nickel | 0.16% | Aluminum | 0.017% | |
Molybdenum | 0.05% |
The applications for which stainless steel grade 410 is used require mild corrosion resistance, heat resistance, and strength. It is supplied to fabricators and manufacturers in sheets, bars, plates, rolled, coils, and drawn. The forms used by product producers are dependent on the dimensions and specifications of their product. As with all series and grades of stainless steel, there are specialized types of stainless steel grade 410 that are engineered for certain types of applications.
AWS E410-16 are coated electrodes with a titania flux coating, which are used for welding and repairing stainless steel grades 410, 416, 420, and 431. It is a coated electrode with hardenability with exceptional strength and moderate resistance to corrosion with a tensile range of 700 Mpa up to 850 Mpa. AWS E410-16 has excellent rust resistance and can be hardened to a Rockwell hardness of 40 depending on the amount of carbon it contains. There is a wide assortment of applications for which AWS E410-16 is used including bolts, bushings, and various types of fasteners.
Stainless steel grade 410 round bars are used for aerospace, automotive, medical, natural gas, and petroleum applications. It is ideal for use in the manufacture of high stress parts due to its good corrosion resistance and exceptional strength, a characteristic of most series 400 stainless steels. Stainless steel grade 410 round bars are available in several configurations with diameters that range from less than an inch up to close to a foot.
ER410, like AWSE410-16, is used to weld stainless steels and to weld overlays on carbon steels. For it to be used for welding, ER410 has to match the chemical composition of the material to be welded. As an overlay for carbon steels, ER410 gives carbon steel resistance against corrosion and abrasion. It is a hardening filler metal that requires joints to be preheated to 176.7°C (350°F) prior to welding the joint.
The various types of kitchen cutlery require a knife blade with strength, durability, and some resistance to corrosion. These factors are the reason that stainless steel grade 410 is used for the manufacturing of knives and flatware and for use in industrial food processing. The chromium content of grade 410 protects knife blades from the effects of the acidity of food and the corrosiveness of water. The heating process in the manufacture of grade 410 gives the knife blades their hardness and edge retention, which helps in their durability and longevity.
Stainless steel 410S is a low carbon modification of stainless steel 410. The low carbon content and some alloy additions reduces austenite formations at high temperatures, which restricts the ability of stainless steel 410S from hardening. It remains soft and ductile after being rapidly cooled. The non-hardening characteristic prevents the steel from cracking when exposed to excessively high temperatures or welding. The ductility of stainless steel 410S makes it easy to form and shape and increases its viability for a wide range of applications from ore processing to plates and valves.
Gate valves are used for fluids that flow in a straight line and require minimal restrictions. The composition and properties of the gate valve material is very important, since the range of liquids or gases widely vary and can affect the performance of the valve. High volume liquid and gas flow requires a gate valve with exceptional strength and corrosion resistance, which is the reason that stainless steel 410 is used in gate valve construction and the manufacture of different types of gate valves. The mechanical and physical properties of stainless steel 410 make it an ideal material for gate valves for the oil and gas, pharmaceutical, and waste water treatment industries.
Stainless steel grade 416 is a free machining stainless steel, which is a metal that allows small chips to break evenly during machining. The machining process can be completed continuously since the machined chips do not need to be removed, a factor that allows for longer run times and machining cycle times. Stainless steel 416 is normally used for parts and components that require extensive machining and corrosion resistance, such as electric motors, pumps, valves, screw machines, studs, and gears.
Many of the uses for stainless steel grade 416 are the same as those for grade 410 with the difference between the two being 416’s strength and toughness. A common use for stainless steel 416 is as fasteners due to its strength. In addition, it is used for the manufacture of cutlery and kitchenware, like grade 410. A unique use of grade 416 is as components for firearms.
The use of grade 416 in the manufacture of firearms is due to its strength, resistance to rust, and resistance to heat. The main part of a firearm that is made of stainless steel is the barrel through which the fired projectile travels. It is included in the barrels of rifles, pistols, competitive rifles, and military weapons. In order to be approved for use in firearms, grade 416 is tested ultrasonically under the American Society of Testing and Materials (ASTM) stipulation 2375, which outlines the parameters for the ultrasonic test.
In addition to the barrels of firearms, grade 416 has been found to have the strength, endurance, and stability to perform as other aspects of firearms, such as triggers and firing pins. Any aspect of a weapon that requires constant and repetitive use is made of grade 416 stainless steel to ensure the safety of a weapon and its performance. The barrels of firearms made with grade 416 stainless steel have greater accuracy and are the reason competitive and target shooters prefer grade 416 barrels.
Springs are various sizes of wires that are wound in a helical fashion with each type of spring having a different and unique form to fit the requirements of an application. They have to be exceptionally durable and able to easily recover after being stressed or deformed. Stainless steel grade 416 is an ideal material that is used to form springs due to its strength, durability, machinability, and rust and corrosion resistance. The types of springs manufactured using stainless steel 416 include the full spectrum of springs with larger springs being the most common.
Stainless steel grade 416 bars are available in round bars, flat bars, and square bars. The unique machining characteristics of stainless steel grade 416 makes it ideal for use in agriculture, gas turbines, and motor shafts. The popularity of stainless steel 416 bars is due to the steel's free machining properties even though it has low corrosion resistance. Bars of stainless steel 416 are available annealed and T conditioned.
Stainless steel grade 420 was developed for use in the manufacture of knives. The quality of knives produced using grade 420 varies in accordance with the amount of carbon it contains, which can range from 0.15% up to 0.38%. Grade 420 with high end carbon can have a hardness rating of 57 RHC up to 58 RHC. Its toughness is due to its low carbide content.
Stainless steel grade 420 is referred to as a surgical grade stainless steel and capable of being used for biomedical applications. Although the term medical grade stainless steel is used to describe grade 420, there isn’t a formal definition for what surgical stainless steel is. In most cases, any stainless steel with sufficient corrosion resistance is referred to as surgical stainless steel. In the case of grade 420, its edge retention, strength, hardness, and toughness makes it ideal for the manufacture of surgical tools.
Stainless steel grade 420 has many of the mechanical properties of carbon steel, which makes it ideal for the shaping and forming of tools with the mechanical characteristics of industrial tools. In some cases, grade 420 is used in place of grades 304 and 316 due to its exceptional tensile strength and hardness. Tools made using grade 420 have a longer useful life due to the metal's high wear resistance.
Needle valves are used for accurate control of the flow of clean gases and liquids. They are designed for even and smooth control of flow for fluids or gases with a low flow rate and significant pressure drop between their inlet and outlet. The strength and durability of stainless steel grade 420 as well as its corrosion resistance and hardness make grade 420 an ideal material for needle valve applications.
Stainless steel grade 420 HC has a high carbon content of 0.44% up to 0.60%, which is unlike grade 420 with a carbon content of 0.12% up to 0.14%. In addition, stainless steel grade 420 HC has an increased chromium content of 14%, a factor that gives the metal increased corrosion resistance. Grade 420 HC sharpens easily and can endure constant use as well as being rust resistant. It is commonly used to manufacture knives and is popular in the manufacture of machetes.
Stainless steel grades 420J1 and 420J2 are a low cost stainless steel that is used for the manufacture of knives. They are differentiated by their carbon content with grade 420J1 having a low carbon content while grade 420J2 has a medium carbon content.
The various forms of stainless steel grades 410, 416, and 420 are produced to meet the requirements of manufacturers and take several different shapes. During the manufacturing process, the molten stainless steel is formed into different shapes for shipment. Common forms used in the production of grades 410, 416, and 420 are sheets, bars, plates, billets and ingots, coils, or being cold drawn through a die to form a specialized shape.
Stainless steel plates have a similar structure to that of sheets with a greater thickness. Although both forms of stainless steel are in the form of thick flat pieces of metal, the differentiating factor between the two forms is their thickness with flat forms that have a thickness of 2 to 3 mm (0.079 in up to 0.12 in) being defined as plates. Plates are produced in the same way as sheets by having the material rolled through a mill.
Rods have a cylindrical shape and are used in their manufactured form as supports. They come in different diameters in accordance with the purpose for which they are manufactured. Rods also come in different lengths, a factor that makes them flexible enough to be used for the CNC process for producing screws and fasteners.
Of the various forms of stainless steel series 400, coils are one of the most common due to their versatility. They are thin sheets of stainless steel that are rolled into a coil shape and cut to the desired size and configuration required by an application. Coils are available as flat strips and have thicknesses that vary from 0.02 mm up to 6 mm (0.0008 in up to 0.24 in).
Coils are typically used in applications requiring high strength and durability, especially where the material needs to be processed further, such as cutting, slitting, or rolling into more specialized shapes. The wide use of stainless steel series 400 coils includes kitchen appliances, automotive parts, and materials for construction. Series 400 coils are due rust resistant, which gives them an advantage over other types of metal coils.
Coils, like other forms of stainless steel 400, can be heat treated and finished in a variety of ways to meet specific requirements. Grade 420 coils, in particular, are used in applications where high hardness and wear resistance are critical, such as cutlery and heavy duty industrial components.
Bars are a unique form of stainless steel and take a wide assortment of shapes that include round, hexagonal, strips, and specialized ones for specific applications. They are hot or cold rolled to achieve the necessary hardness for an application. Bars can have complex profiles that have different cross-sectional shapes. This aspect of bars is one of the reasons for their wide use.
Sheets are one of the more common forms of stainless steel that are used for shipping since they fit easily on pallets and can be loaded in stacks. Like the other forms of stainless steel, sheets come in a wide variety of sizes. They can be rectangular or square depending on the preference of the manufacturer. In the manufacturing process, sheets can be laser cut, stamped, bent, and deformed to fit the requirements of a product or application. They are seldom used in their original form and are normally reengineered by a mechanical process.
Billets and ingots are another common form of stainless steel that are used for shipping and manufacturing. They are used in a wide array of manufacturing processes from casting to extrusion. The shapes of stainless steel billets are easy to manipulate and handle. They can be easily placed in furnaces to melt the metal for being injected into a casting mold.
The factor that differentiates stainless steel 420 strips from coils is their width that range from 1.5 mm up to 600 mm (0.059 in up to 23 in). Although stainless steel 420 strips fall into the category of coils, their small widths distinguish them. Regardless of their widths, the thickness of 420 strips is the same as that of coils. The wide use of stainless steel 420 strips is due to their exceptional strength, corrosion resistance, and durability. They are used to manufacture cutlery, medical instrumentation, scissors, springs, and blades. As with other forms of stainless steel 420, the shape and appearance of strips are changed and altered by grinding and polishing.
Stainless steel series 400 is known for its strength, hardness, and wear resistance and is used in applications by several industries. The list of uses for series 400 stainless steels includes simple cutlery and kitchen tools, industrial machinery, medical instruments, and petrochemical equipment. It has the necessary quality and performance that is demanded by manufacturers.
Alloys in the 400 series, such as grades 410, 416, and 420, are versatile, dependable, and resilient and provide a cost effective and reliable metal to meet the needs of high stress applications. The wear and tear resistance of stainless steels series 400 makes it applicable for specialized and unique applications.
The lower nickel content of series 400 stainless steels significantly affects its cost compared to other types of stainless steel. It is one of the reasons that series 400 is selected for so many applications.
The ease of forming and shaping of series 400 makes it possible to quickly produce the metal products and components. It is one of the easiest steels to produce compared to other forms of steel. The ability to form and shape series 400 is part of the reason for its wide usage.
Series 400 has similar strength compared to carbon steel but with rust and corrosion resistance, which makes it easier to maintain compared to carbon steels. While carbon steel requires the applications of coatings for protection from rust and corrosion, series 400 is naturally resistant.
One of the outstanding characteristics of series 400 stainless steels is their ability to endure wear and tear, which is unlike other forms of stainless steel. This aspect makes series 400 stainless steels long lasting and highly durable and makes it an option for applications that require strength and endurance.
Stainless steel grade 304 is an austenite stainless steel that is the most widely used and versatile of the various grades of stainless steel. It is a part of the T300 series stainless steels with...
Stainless steel is a type of steel alloy containing a minimum of 10.5% chromium. Chromium imparts corrosion resistance to the metal. Corrosion resistance is achieved by creating a thin film of metal...
Stainless steel can be fabricated using any of the traditional forming and shaping methods. Austenitic stainless steel can be rolled, spun, deep drawn, cold forged, hot forged, or stippled using force and stress...
Stainless steel tubing is a multifaceted product that is commonly utilized in structural applications. Stainless steel tubing diameters and variations vary greatly based on the application requirements and are...
Perforated stainless steel is cut, punched, or stamped to produce a precise pattern of holes or apertures. It is used for functional reasons, such as filtration or ventilation, and aesthetic ones, such as architectural accents...
Stainless steel hinges connect two components while allowing them to move in relation to one another. They can have various leafs shaped like rectangles and other forms depending on the type of stainless steel hinge. Stainless steel hinge leafs are...
Stainless steel tanks are widely used in food, beverage, dairy, medicine, cosmetics, and other manufacturing processes where cleanliness and purity are important. These are also used in industrial plants for storing chemicals and gases where strong resistance from chemical degradation is required...
Titanium metal, with the symbol Ti, is the ninth most abundant element in the earth‘s crust. It does not occur in large deposits, yet small amounts of titanium are found in almost every rock...