Storage Racks
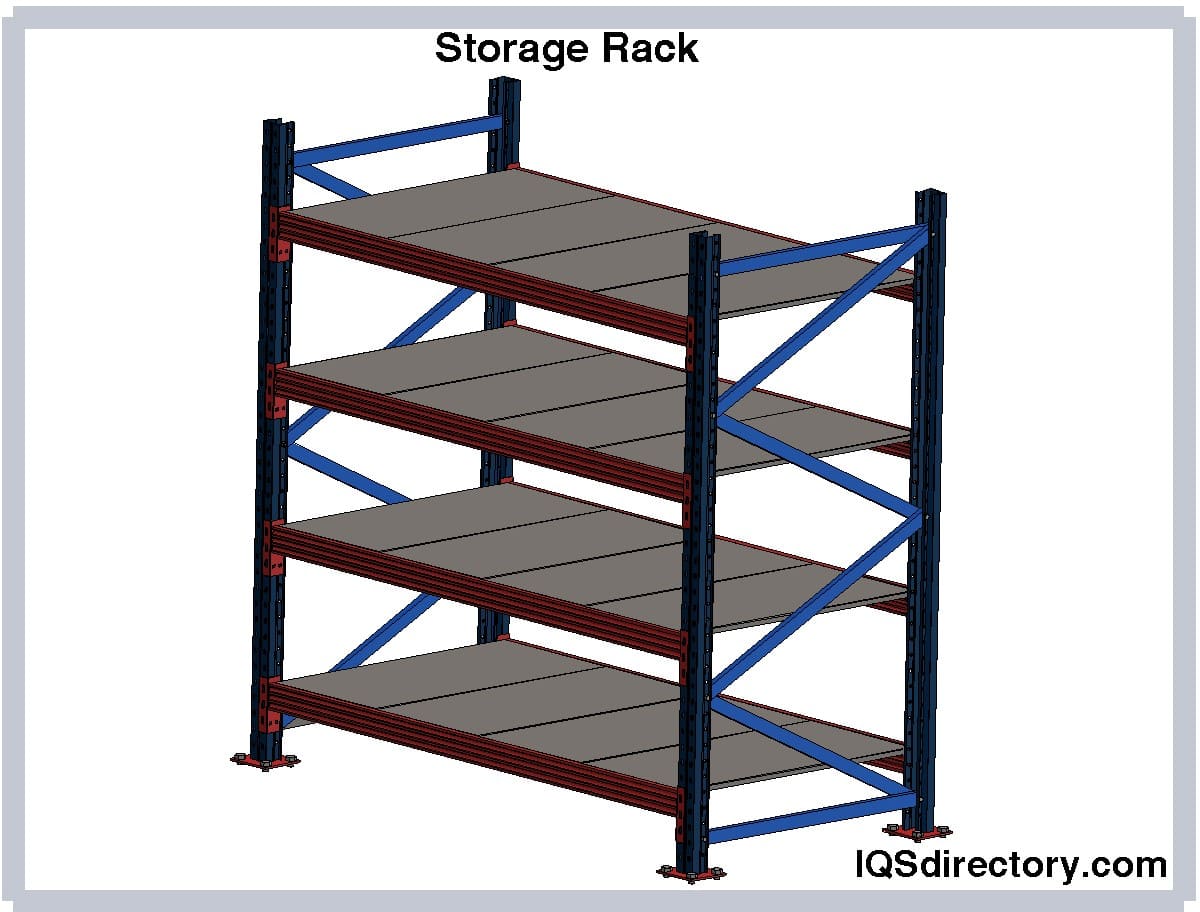
Storage rack, also known as racking, is a structure that stores items and materials and comprises at least two upright (vertical) frames, horizontal beams, and some sort of decking (bars, panels, meshes, or none)...
Please fill out the following form to submit a Request for Quote to any of the following companies listed on Pallet Racks .
List of pallet rack manufacturers with examples of their pallet racks.
You will learn:
A pallet rack is a vertical steel structure designed for the storage of pallets. It features beams and connectors that are either bolted, welded, or clipped together, forming a sturdy system for holding inventory and equipment. In warehouse environments, pallet racks are essential for providing a safe and dependable method to organize and retrieve materials. This design accommodates a diverse array of products, ranging from food and clothing to heavy machinery and tools.
The widespread use of pallet racks is attributed to their adaptability and the capacity to meet varied warehousing demands. They are designed for easy access, making them a leading option for storage solutions.
In a well-structured pallet racking system, pallets are placed in horizontal rows spanning several levels. The number of levels typically ranges from three to seven, depending on content and specific needs. Pallet racks effectively utilize vertical space that might otherwise go unused, providing a smart, safe, and well-organized way to store valuable inventory.
Pallet racking comes in numerous styles, designs, and capacities, tailored to accommodate the types of products stored and the building’s capacity. The materials used in manufacturing pallet racks, typically steel, dictate their strength and functionality, allowing them to support several tons of products, merchandise, and materials.
In the material handling industry, a diverse range of pallet racking types is essential to meet varying customer needs and specifications. While there are different varieties suited to specific applications, all pallet racking systems must feature essential attributes such as forklift accessibility and structural components designed to support palletized goods.
Cantilever pallet racking can store pallets if designed properly. They are used to store longer products that cannot be stored on traditional racks. The key to cantilever racks is their weight capacity, which can vary to meet the needs of a particular product. They are made using upright columns, arms to secure the product, and horizontal braces between the storage bays.
In a selective pallet racking system, each pallet rack position is directly accessible from the aisle. This system is widely used because it allows for the retrieval of a pallet without the need to move others. The easy access ensures that every item is visible for both loading and unloading. During inventory checks, there is no need to remove items from their pallets, making counting and calculations more efficient.
Double deep pallet racking is designed for warehouses with limited space that need efficient handling. It is well-suited for the first in, last out (FILO) inventory system. Unlike selective racking, where only one pallet per shelf is stored, double deep racking holds two pallets per shelf—one directly behind the other. The configuration involves placing one rack closely behind another, so the first pallet placed is pushed back behind the second pallet.
To access the second pallet, a specialized forklift is required, as it is positioned a full rack's width back. This system reduces the number of aisles needed and optimizes the use of available space.
Push back pallet racking is well-suited for high-density storage in spaces with limited room. It operates similarly to the double deep system but accommodates more than two pallets per shelf. In this system, pallets are placed on carts or shelf trays that travel along rails within the rack frame, allowing them to be pushed back as new pallets are loaded.
This system supports multiple pallet sizes and can store pallets up to six deep on a single shelf. It is particularly effective for the last in, first out (LIFO) inventory management system.
Drive-in and drive-through racking systems are designed for warehouses with frequently shifting inventory. Unlike static systems with defined rows and aisles, these systems offer denser placement and optimize available space.
In a drive-in or drive-through system, forklifts operate within the racks, which lack designated lanes between rows. The forklift enters and exits through the same opening. This setup is particularly suited for cold storage environments where only one entry point is permitted.
Pallet flow racking, also known as gravity flow racking, employs roller tracks arranged at a slope to create a gravity flow lane. This incline allows pallets to move smoothly from the rear to the front of the rack. The system includes brakes to regulate the movement speed of the pallets, ensuring safe handling. Pallet flow racking systems can accommodate between two to twenty pallets on the tracks.
Similar to other systems, pallet flow racking is ideal for warehouses with limited space and operates on a FIFO (first in, first out) basis. It is particularly suited for handling time-sensitive or perishable products.
Multi-tier pallet racks are similar to mezzanines in that they take advantage of the space below the ceiling in very tall or high facilities. The structure of multi-tier pallet racks consists of a series of levels that have shelving and walking platforms that are connected by stairs. Such systems are ideal for storing small items such as parts, medicines, and documents. In some ways, the multiple levels resemble a very large library with identification codes and labels.
In multi-tier pallet rack systems, locations are identified by the shelf number and the level of its placement. Although such systems are ideal for small parts, they can be palletized for storing items on pallets. The various levels of a multi-tier pallet racking system are very sturdy and durable but are not capable of holding forklifts or pallet jacks. Their main benefit is taking advantage of unused space.
A variety of add-ons can be integrated into a pallet racking system, including those tailored to specific product requirements. While pallet racks are versatile and can store various types of products, some items necessitate racks designed to accommodate their unique characteristics.
Wire Mesh Decking – Wire mesh decking sits on the racking beams and acts as shelving material. Though it is lightweight and easy to install, it is sturdy and durable enough to hold any type of material. Wire mesh is made from solid galvanized steel and allows the racking of small cartons.
Barrel Supports – Several industries store their raw materials in barrels, which can be stored upright on a rack or in a horizontal position. To prevent barrels from rolling on a pallet rack and to maintain the stability of their contents, barrel supports can be attached to the horizontal supports of the racking.
The accessories mentioned above represent just a small selection of those available from pallet rack suppliers. Engineers and designers collaborate with customers to create custom accessories tailored to the needs of specific applications.
The identification of pallet racking is based on how the horizontal beams connect to the vertical uprights. There are various connection types, primarily determined by the manufacturer. These connections are designed to join the main components of the pallet rack securely, ensuring the structure remains stable and well-supported.
The pallet rack identification system describes the types of connections, including bolts, screws, clips, and fasteners.
The term "teardrop" describes the shape of the holes in the racking's upright frame and is one of the most common and popular racking designs. The punched holes ensure a secure fit between the horizontal beams and the uprights. The teardrop design facilitates easy and quick assembly. A rivet with a flat head is inserted into the top of the teardrop hole, and its shaft slides into the narrower part of the teardrop, locking the horizontal support in place.
Structural pallet racking is designed for environments prone to seismic activity, offering enhanced security compared to other types. It uses nuts and bolts to connect the vertical and horizontal beams, providing a more stable structure. Although its dimensions are consistent with other pallet racking systems, structural racking is constructed from heavier materials to ensure greater durability.
Hiline pallet racking, similar to structural racking, is utilized in seismic activity zones and is constructed from heavier gauge steel. Distinctively, Hiline racking features one-inch hole spacing from center to center. The horizontal and vertical beams are secured with clip pins or j-bolts. Its beams are typically orange, complemented by grey framing.
The slide and lock version of pallet racking uses rectangular slots to allow hook-like brackets to slide into place, with the option of adding cotter pins for enhanced security. This style has become as prevalent as the teardrop design. The lengths of the frames and beams in slide and lock pallet racking are standardized, making them adaptable to various racking configurations.
Keystone pallet racking features symmetric channels with punched lips and a single row of keystone slots at the front where beam clips' lugs fit. The frame is equipped with holes punched on both sides, offset from the keystones, allowing safety clips to securely snap into place.
Ridg-U-Rak slotted pallet racking offers an optional feature: a pinch clip that locks the beams in place. Unlike traditional rivets, this design utilizes a hook material that fits into slots in the column. The hook and slot configuration ensures automatic beam locking. Additionally, the slotted columns feature a 6-bend design section that enhances stiffness in the return flanges, thereby improving overall section stability.
Speedrack pallet racking connections employ a handle hook and J-hook safety pin to firmly secure the beam to the frame, preventing accidental detachment. The uprights are constructed from closed rectangular or square tubing, which enhances the stability and strength of the racking, resulting in a higher weight capacity.
Sturdi-bilt pallet racking utilizes a wedge lock clip system to secure the beams and uprights. The beams are equipped with clips that fit into slots on the frame, simplifying assembly and configuration. Initially, Sturdi-bilt pallet racking lacked the additional clip for securing the wedge clips, which was later introduced as a safety enhancement.
The T-bolt pallet racking style is widely favored for its durability and strength. It incorporates T-bolts that are fastened to the uprights with large bolts, ensuring the racking system achieves optimal capacity strength.
A tab at the end of the beam connector secures the beam, while the T-bolt, attached at the front of the beam, locks into place at a 90-degree angle to keep everything firmly in position.
The ten pallet rack identifiers mentioned above represent just a fraction of the numerous styles, designs, configurations, and support systems utilized by pallet rack manufacturers. Below is a list of additional manufacturers, each with its own unique designs and methods for pallet rack beams, frames, and connections.
As with all industrial equipment and materials, pallet racks require careful planning to support the materials they store and for the safety of personnel. Several key components are used in the construction of pallet racks, which are normally made of steel, galvanized steel, or an aluminum alloy. The construction of all pallet racks begins with the frame and horizontal beams.
A pallet rack system is a storage method for storing pallets loaded with materials that are aligned in rows on metal shelves. The multiple levels of beam elevations are accessible by forklifts and are designed to increase storage density.
The upright frame is composed of vertical columns that sit on the floor and rise up to the level of the top shelf. These columns feature a series of holes for connecting the cross beams. To determine the frame's height, you need to account for the height of a loaded pallet, plus the depth of the beam, and add some extra space for clearance. This calculation helps establish the number of levels that can be accommodated on the pallet rack.
Cross beams have dual functions: they connect the frame and provide support for the pallets. Each end of the beams features a connective bracket that securely attaches them to the frame's holes. At each beam level, there are two cross beams: one positioned at the front of the rack and the other at the back. Essentially, these cross beams create the platform for the shelf and support the weight of the pallets.
Concrete anchor bolts are used to anchor the feet of a pallet rack’s upright frame. For support, the upright frame of a pallet rack has feet welded to the bottom. Holes are drilled in the feet to place the anchor bolts to hold the pallet rack and frame securely in place. The purpose of the anchor bolts is to serve as an extra source of security and reinforcement.
The base plate, or foot, is welded to the base of the vertical support frame, serving as the anchor for the racking system. Its dimensions are specifically designed to evenly distribute the weight of the rack and support the column’s load.
The dimensions of the base plate are influenced by various factors such as soil-bearing capacity, concrete strength (psi), rack height, seismic activity, and the load-bearing requirements of the rack. The thickness can vary based on the materials used. Larger base plates offer enhanced stability and reduce the risk of the rack tipping over.
Crossbars enhance the safety of pallet racks by redistributing part of the beam load, thus improving overall stability. They play a critical role in securing the pallet rack and reducing the risk of failure. Crossbars can be installed either horizontally or diagonally, connecting the front and rear columns.
Designed to reinforce the rack's frame and provide additional support to the columns, crossbars are essential for maintaining the rack's alignment. Proper placement of crossbars and horizontal supports ensures that the rack remains upright and stable, regardless of its height.
Pallet rack decking enhances the safety of pallet racks by providing a stable surface for pallets and ensuring they remain securely in place. This feature helps prevent items from falling due to poorly stacked pallets and offers extra support. It also accommodates lightweight and irregularly shaped pallets.
While the advantages of pallet rack decking are straightforward, choosing the right type can be complex. There are various decking options available, such as solid, wire mesh, wire, bar, wood, metal, and punched sheets, each offering different benefits and applications.
Pallet racking systems offer significant convenience and organizational advantages, making them a crucial component in warehousing and storage design. In manufacturing and production environments, large spaces often remain underutilized due to improper layout or insufficient tools. Pallet racking effectively optimizes these underused areas, enhancing overall space utilization.
Efficiency is a key focus in modern manufacturing, directly impacting time savings and profitability. Established organizations recognize the importance of leveraging their resources, including implementing cost-effective and well-designed storage solutions.
Significant warehouse space is dedicated to ensuring safe passage and access for forklifts. When materials are scattered across the floor, they become inaccessible and contribute to disorganization. Installing pallet racks allows for optimal use of vertical space, freeing up floor area and improving organization. With various pallet racking options available, you can adjust and configure the racks to reduce the number of aisles and maximize pallet storage capacity.
Pallet racking systems, including push back and flow racking, offer a stable and secure framework for loading and storing pallets and bulk materials. These high-density storage solutions allow for efficient storage and easy access to products without requiring changes to the warehouse layout.
Among the various facets of business operations, inventory control often proves to be the most challenging. Despite advancements in computerization and technology, inventory still requires adjustments every three to six months. Accurate inventory control is crucial for maximizing profits and delivering effective customer service.
Implementing a well-structured and meticulously planned pallet racking system significantly enhances inventory control. With a range of add-ons and accessories available, pallet racking systems can be tailored to meet detailed inventory management needs.
Each pallet racking system is custom-designed and engineered to address the unique requirements of every warehouse. Although businesses might sell similar products, their approaches to organizing storage space and picking patterns can differ. The versatility of pallet racking allows for the creation of a warehousing system that perfectly aligns with the specific needs of any storage plan.
Among the numerous advantages of pallet racking, safety is the most critical. In manufacturing environments, disorganization and unmanaged storage can result in various hazards that are both dangerous and expensive. A properly secured pallet racking system offers a reliable foundation for safeguarding workers and protecting materials.
In today’s fast-paced marketing and manufacturing environments, the ability to quickly adapt to changes in supply and demand is crucial. Products previously considered ineffective or unnecessary may suddenly become essential. Pallet racking systems are well-suited to handle these fluctuations, offering flexible storage solutions that allow for rapid adjustments in product movement and availability.
Timely service is crucial to a business’s success, necessitating meticulous planning, efficiency, and attention to detail. A well-designed pallet racking system enables businesses to deliver streamlined and cost-effective service, fostering more opportunities and increased profitability.
Storage rack, also known as racking, is a structure that stores items and materials and comprises at least two upright (vertical) frames, horizontal beams, and some sort of decking (bars, panels, meshes, or none)...
Warehouse racking, also known as storage or pallet racking, is a material handling system suitable for mass storage of goods unitized on skids or pallets. It allows efficient utilization of space while providing easy access to stockpiled items for better inventory control...
An adjustable work bench is a tool that allows the user to adjust and regulate the height of the work surface to a more ergonomic and comfortable position for the safe and effortless performance of work...
An AGV forklift is a driverless self-operating robotic device that has the ability to carry, lift, retrieve, and place loads for easy transfer from one location to another. An automatic guided vehicle (AGV) forklift is a computer controlled mechanism that...
Automated guided vehicles (AGV) or mobile robots are types of guided robotic systems that are not bounded by a fixed range of motion. Rather, it is self-contained and can move along a line, surface, or space...
An autonomous mobile robot (AMR) is a self-propelled self-powered mechanism designed to perform repetitive tasks or organizational functions using an internal guidance system. They are able to navigate their...
A forklift truck is an electrical or gas powered industrial piece of equipment with a metal fork platform attached to its front that can be used to lift heavy loads by inserting the fork platform under cargo, pallets, or...
A lab bench is a specially designed bench or table that is able to assist in the performance of laboratory experiments and tasks, including the handling of reagents and test samples. Part of the design process for...
A pallet stacker is a machine designed to assist the user in lifting, moving and handling palletized materials with ease. A pallet itself is a flat and horizontal structure used to support goods in a sturdy fashion...
A portable workbench is a flexible and mobile work surface that is designed to function in multiple environments for the purpose of preparing, constructing, or servicing a wide variety of industrial and commercial applications...
A workbench is a sturdy flat, smooth, molded surface that comes in a variety of sizes designed for specific tasks. They can be very complex for engineering design work, complicated machining, and intricate precision tooling or be a highly finished wood table for woodworking, metal work, and project design...
In 1954, when Arthur "Mac" Barrett, of Barrett Electronics Corporation, unveiled the first AGV, he named it Guide-o-Matic and described it as a driverless vehicle...