Pallet Racks
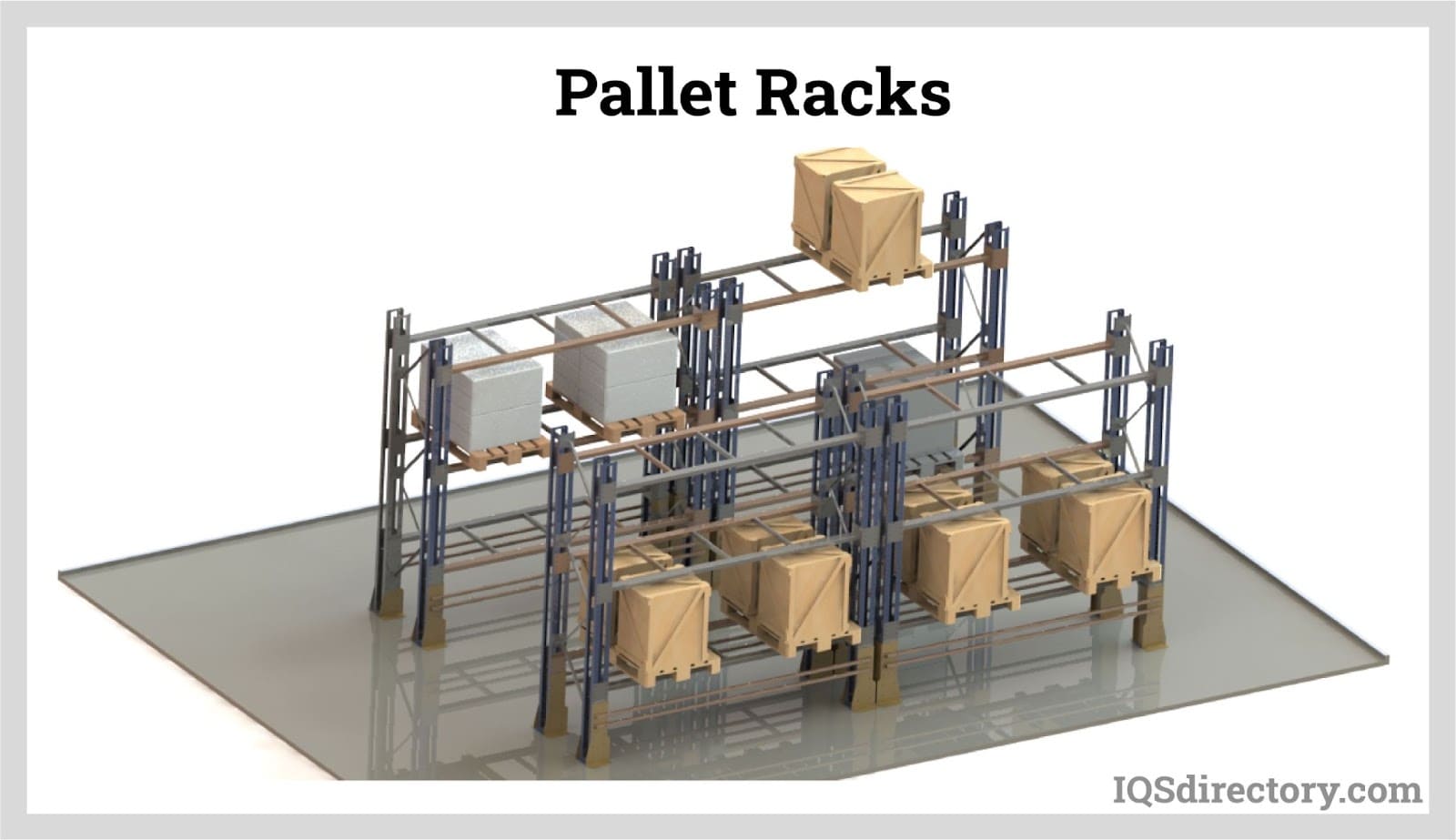
A pallet rack is an upright structure made of steel framing with beams and connectors that are bolted, welded, or clipped together to form a shelving unit to store inventory and equipment. In warehousing, pallet racks are...
Please fill out the following form to submit a Request for Quote to any of the following companies listed on
List of warehouse manufacturers, types of warehouse racking, and benefits of warehouse racking
You will learn:
Warehouse racking systems, often referred to as storage or pallet racking, are essential material handling solutions developed to facilitate the large-scale storage of goods placed on skids or pallets. These systems enhance space efficiency and provide easy access to stored materials, leading to better inventory management. Such systems are especially advantageous for manufacturers that need to store large volumes of non-perishable products due to limited storage availability. While conventionally, palletized goods are safely stacked up to three tiers, a racking system enables stacking these palletized goods five to seven tiers high, contingent on the facility's ceiling height, thereby significantly boosting storage capacity.
Besides managing finished goods, racking systems are also employed for storing raw materials and components. Selective racking systems are devised to optimize item accessibility, supporting a diverse array of products. Some distribution networks implement the FIFO (First-In, First-Out) inventory management strategy, ensuring the earliest-stocked items are the first to be accessed and shipped. This method aids in efficient inventory control and diminishes the risk of product obsolescence.
Aside from optimizing storage space, implementing advanced warehouse racking systems brings a wide array of advantages for inventory management and supply chain efficiency. The benefits of warehouse racking can be measured not only in terms of maximizing cubic storage, but also by reducing operational costs, improving warehouse layout, minimizing downtime, and supporting higher throughput. Companies installing modern industrial shelving, pallet racking, and storage rack systems often experience significant savings on leasing additional warehouse space, reduced workforce effort through improved accessibility, and a measurable increase in order processing speed. Additionally, ensuring compliance with OSHA safety standards and robust warehouse management protocols—while not always yielding immediate ROI—adds long-term reliability and value by reducing workplace accidents and product loss. Below are some of the key benefits of implementing a warehouse racking system:
Easy inventory organization: Racks can be addressed easily in comparison to stockpiling. Storing goods with many distinct varieties is virtually impossible with stockpiling without consuming large floor spaces. A type of racking system known as selective racking allows storing different types of goods while keeping the consumed space to a minimum. Inventory tracking via a Warehouse Management System (WMS) is also more accurate when items are systematically organized on shelves and racks, supporting better SKU control, batch management, and FIFO/LIFO picking strategies.
The evolution of racking systems was driven by the need to prevent damage to goods and products during storage and handling. Originally constructed from wood, today’s advanced metal warehouse racking—such as steel pallet racking and cantilever racks—are engineered for high stability and durability, enabling businesses to safely stack goods several feet high, limited only by building structure and local regulations.
Palletizing materials not only simplifies shipment organization and supply receipt, but when paired with a professionally engineered racking system, ensures each load is securely stored to prevent mishandling, accidental contact, or dropping. Strong metal frames stabilize pallets, minimizing risk of tipping or collapse, and many systems include load beams and decking for additional support. With options ranging from push-back racking and double-deep racking to highly automated AS/RS (Automated Storage and Retrieval Systems), businesses gain both damage protection and operational flexibility. Racking systems also allow for easy access to each SKU, reducing the risk of disrupting surrounding inventory during retrieval.
In a racking system, the location of empty or occupied pallets can be quickly identified and accessed thanks to improved labeling, barcoding, and digital inventory tracking systems. This streamlined process reduces unnecessary movements, such as excessive walking or searching, and promotes faster order picking and restocking. Over time, these incremental efficiency gains prevent minor inefficiencies from accumulating into substantial productivity losses, supporting higher workforce output and smoother warehouse operations. Additionally, clear aisle layouts and well-planned picking paths decrease congestion and enhance overall workflow, further optimizing labor costs.
Adapting a racking system is the first step to warehouse automation and scalable storage solutions. By integrating smart conveyor systems, automated guided vehicles (AGVs), and automated forklifts and cranes, companies can automate pallet handling, replenishment, and retrieval processes. These high-tech integrations can lead to significant savings in manpower costs, reduce manual errors, and streamline the business process, especially for large distribution centers and e-commerce fulfillment operations. With the adoption of technologies like RFID tracking and AI-driven inventory control, racking systems become the backbone of a smart warehouse infrastructure.
Warehouse racking systems are intentionally designed to maximize storage capacity while upholding strict safety standards. Properly engineered racking facilitates organized storage, efficient space allocation, and quick retrieval of items through effective product cataloging and order picking strategies. Warehouse safety measures are critical to maintaining operational efficiency and are embedded in quality racking system design. Essential safety features—including sensors and alarms, guard rails, rack end protectors, rack guards, and column guards—protect employees, products, and physical infrastructure from common hazards.
Racking systems improve access to all stored goods and create organized aisles for easier cleaning, dusting, and maintenance. This not only facilitates routine facility cleaning but also enhances product hygiene, which is crucial for food and pharmaceutical storage applications. Effective segregation of products allows for the separation of goods with different storage requirements, helping to prevent cross-contamination, spoilage, or damage to sensitive inventory. Moreover, elevated racks can aid in pest control by minimizing floor contact and exposure. Businesses seeking compliance with FDA or GMP warehouse standards can leverage advanced racking solutions to achieve sterility, traceability, and secure storage for regulated inventories.
Before investing in a warehouse racking system, it’s crucial to evaluate a comprehensive range of factors to ensure the solution meets your operational needs and aligns with best practices in warehouse management. Although storage racks are engineered to maximize available space and improve inventory control, they do inherently occupy some square footage with their steel frames and necessary accessories. One significant limitation to consider is the potential difficulty and cost involved in modifying or reconfiguring commercial racking systems once installed. To maximize your return on investment (ROI) and create a scalable, efficient storage solution, keep the following key considerations in mind:
Vertical Clearance: Optimize not only horizontal floor space but also the available vertical clearance to improve storage density and cubic utilization. Rack-supported mezzanines can make use of vertical space, but must be planned with awareness of fire suppression system clearances, adequate lighting, and HVAC system airflow. High-density racking, such as drive-in racking or gravity flow rack systems, can exploit vertical room, but may require sacrificing a layer for necessary slopes or operational clearances. Overextending stack heights could impact critical warehouse infrastructure and may incur additional costs for compliance modifications.
Load: Select racking materials and construction methods that match your operational requirements. Most industrial shelving is engineered from robust steel—cold-rolled for lighter loads, and hot-rolled or structural steel for heavy-duty warehouse pallet racks. Always verify the maximum load capacity per bay and per shelf to prevent overloading and to comply with OSHA and local building code regulations. For specialized inventory such as cantilever racks for long materials, or push-back racks for deep lane storage, choose structural components scaled to expected weights.
Number of SKUs: Identify the total number of stock keeping units (SKUs) your warehouse must accommodate. Higher SKU counts call for greater selectivity—such as selective pallet racks or carton flow racks—to ensure fast access, accurate inventory tracking, and efficient order picking. If the facility manages lower SKU diversity with larger volumes per SKU, systems like push-back or drive-in racks may deliver higher storage efficiency. Evaluate your WMS (warehouse management system) integration needs for real-time tracking and optimization of inventory locations.
When planning your warehouse racking system, also weigh secondary considerations, such as seismic zone requirements, forklift aisle widths for optimized material handling, future scalability of storage solutions, and environmental factors like temperature or humidity needed for climate-controlled storage. Choosing the right type of racks—such as selective racking, carton flow racks, cantilever racks, or automated storage and retrieval systems (AS/RS)—with a reputable racking supplier is vital for long-term operational efficiency.
Ultimately, investing in the correct warehouse racking system helps increase inventory turnover, enhance workplace safety, and optimize material handling processes—all cornerstones of modern supply chain management. Careful planning and strategic selection deliver tangible cost savings and keep your warehouse operations competitive within the logistics industry.
Racking systems come in various designs and configurations tailored to specific applications. Generally, storage racks are categorized into high-selectivity, low-density or low-selectivity, high-density applications. High-selectivity, low-density racks include selective, double-deep, and very-narrow-aisle systems. Conversely, high-density applications encompass push-back, drive-in, and pallet flow systems. Additionally, there are specialized systems, which are essentially adaptations or modifications of these standard configurations.
Selective pallet racking is designed for high SKU counts but offers lower storage density. It is often visualized as large shelves with space for a single row of items. Although racks can be arranged back-to-back to enhance storage density, the overall density remains low due to the space occupied by aisles. This type of racking is commonly used in warehouses for raw materials, parts storage, and distribution centers where there is a wide variety of products in low volumes. Selective pallet racking can be combined with other racking types to handle SKUs with higher volumes. Key benefits include flexibility for FIFO and LIFO inventory management, compatibility with standard forklifts, ease of cleaning and inventory management, and straightforward construction that allows for easy reconfiguration. Selective racking also features various frame and beam connection designs, including teardrop and slotted racks.
Teardrop Racks: Teardrop racking is a type of selective racking with modified frame and beam attachments that can be reconfigured and expanded easily without the use of machine tools. Upside down teardrop-shaped holes are punched along the upright frames, where pins attached to the beams are inserted. As the pin falls into the tapered opening, friction secures it in place without requiring additional fasteners. This connection has enough strength to be comparable with permanent joints. Adding heavier loads causes more friction to fix the beam in place. Wire decks are placed above the beams that become shelves for the pallets. Appurtenances such as pallet supports, crossbars, ties, and anchors are added to further strengthen the structure. Teardrop pallet racks are usually produced by roll forming in which metal sheets are cold-rolled into rectangular frames and beams.
Slotted Racks: These are sometimes referred to as structural racks. Instead of using upside-down teardrop-shaped holes, slotted racks have a pair of rectangular openings milled along with the upright frame. The frame and beam can be attached by hooks protruding from the beam or by bolts. The main advantage of using slotted racks over teardrop racks are their higher durability and strength. Slotted racks are produced from hot-rolled structural steel, making them more robust than teardrop racks. Higher gauges of sheet metal are used to allow a higher load-bearing capacity. The downside of using slotted racks is their higher cost and weight.
Double-deep pallet racking is an enhancement of standard selective racking, where each pallet shelf holds two rows of pallets instead of one. This modification increases storage capacity by 40-60% while retaining many of the benefits of traditional selective racking. For FIFO inventory management, adjacent rows must contain the same SKU, which improves storage density but reduces selectivity. A notable disadvantage is the requirement for specialized forklifts or standard forklifts equipped with double-deep handling attachments, leading to higher operating costs and the need for well-trained operators.
The concept of very narrow aisle (VNA) racking is to enhance space utilization while maintaining 100% selectivity, building upon the standard selective racking system. This is achieved by using a side-loading forklift, which allows pallets to be loaded and unloaded without the need for wide aisles. By minimizing aisle space, VNA racking can reduce the aisle width by up to 40%. However, a drawback of this system is the requirement for two types of equipment: a side-loading forklift for accessing the racks and a standard forklift for transporting pallets between the palletizing station and staging area.
Push-back racking involves loading pallets onto carts that rest on rails within each lane of the racking system. These carts are positioned at the front of the aisle and are designed to nest together. To load a pallet, a forklift pushes the pallet into the lane, causing the existing pallets to move further back. This dynamic system enables higher storage density compared to single or double deep racking. Each lane typically holds one SKU and can be configured to accommodate three to six pallets deep. Because the pallet being accessed is always at the front of the lane, specialized deep-handling forklifts are not necessary. The lanes are inclined to facilitate the rolling of carts towards the aisle. Note that this system operates on a Last-In, First-Out (LIFO) basis, as only the most recently loaded pallet is directly accessible.
In this racking system, pallets are supported by a pair of rails specifically designed to match the dimensions of the pallets. These rails enable the forklift mast and forks to access the pallet as it moves along the bay. Loading is performed by driving the forklift into the last available position within the bay. Once in position, the pallet is carefully lowered onto the rails. After loading, the forklift mast is retracted, and the forklift exits the bay. Each bay is dedicated to a single SKU and can hold multiple units deep, making this system suitable for high-density storage with lower selectivity. There are two primary configurations: drive-in and drive-through. In a drive-in system, there is only one access point for both entrance and exit, which supports Last-In, First-Out (LIFO) inventory management. Conversely, a drive-through system features two access points—one for loading and one for unloading—facilitating First-In, First-Out (FIFO) inventory management.
This racking design uses roller beds to move pallets into the last available position within a lane. The lane features two openings, one at the front and one at the rear, similar to a drive-through system. Pallets are loaded from the rear and roll towards the front of the lane due to the rearward incline of the lane. Off-loading occurs at the front side of the racks. Like drive-in and drive-through racking systems, pallet flow racks are ideal for high-volume, low-SKU applications. This system supports First-In, First-Out (FIFO) inventory management. Although it offers similar storage density to drive-through racks, it does not achieve the same density as drive-in racks due to the use of two lanes. Additionally, the pallet flow system is less susceptible to damage from forklifts, reducing the risk of structural collapse compared to other racking systems.
This type of racking system is ideal for storing long products such as roofing materials, pipes, tubes, and lumber. It features upright columns with cantilever arms extending from one or both sides. The vertical spacing between the arms can be adjusted to accommodate the size and bulkiness of the products, and the angle of the arms can be adjusted to ensure secure load retention. Unlike standard selective racking, cantilever racks do not have front upright frames that obstruct loading, making them particularly suitable for storing long or irregularly shaped items such as appliances and furniture.
This racking system operates on a principle similar to pallet flow racking. It features two access points: one for loading and another for off-loading. Manual loading and off-loading can be done without the use of forklifts, making it ideal for high-volume piece-pick applications, such as in cold storage and food warehouses. Carton flow lanes can also accommodate non-standard-sized items, enhancing flexibility and efficiency in storage.
This method requires shifting an entire rack assembly sideways to open up an aisle. This shifting is typically done using electric motors, though smaller racks might be moved manually or through mechanical means like handwheels. This system offers high-density storage and great selectivity but requires moving the racks to access stored items, making it ideal for warehouses with minimal traffic.
As the name suggests, this type takes advantage of having high bays. They are most suitable for automated distribution centers for high density, high selectivity, and high throughput storage. The racks can be single, double, or in some instances, multi-deep rows. Automatic cranes with telescopic forks or order-picking trucks stabilized by rails and supports move along the aisle. The crane picks up a pallet from the conveyor system and places it on its designated rack. Due to the complexity and high cost of this system, it is only viable for warehousing that hedges profits on efficient storage.
Chrome wire shelving offers great versatility and affordability while matching the strength of stainless steel. It boasts a sleek appearance and is suitable for storing various items, including trays, cartons, boxes, and storage containers, thanks to its robust durability.
Multi-tier pallet racks take advantage of unused space in facilities that have high ceilings. Shelves are placed at different levels with aisles and stairs that make the picking process easier. Multi-tier pallet racks resemble mezzanines in that they take advantage of unused space and have different levels above the floor. The use of multi-tier pallet racks makes it possible to increase storage space while providing direct access to products. The typical use of multi-tier pallet racking is operations that store small items, such as auto parts, pharmaceuticals, and document storage.
The forms of multi-tier pallet racking are pallet racking, shelving racks, and mezzanines. Of the three, pallet racking is the most common. It allows for palletizing at multiple levels. While multi-tier pallet racks can store palletized products, shelving racks are designed for smaller items arranged in multiple tiers. Mezzanine floors are usually additional work space. In the case of multi-tier racking, areas on a mezzanine can be used for storage racking.
Epoxy-coated shelving, available in colors like gray, black, or green, is perfect for damp and humid settings. Certain epoxy shelves come with antimicrobial properties to inhibit bacterial growth, making them particularly suitable for use in the food industry and healthcare environments.
ASRS (Automated Storage and Retrieval Systems) leverage software, computers, and robotics to streamline and enhance the efficiency of handling, storage, and picking processes. These systems can be tailored to accommodate various warehouse sizes and rely on a range of technologies to automate warehousing functions.
Numerous types of ASRS systems are available, each designed to address different warehousing requirements. The most frequently used systems include:
Horizontal Carousels - Horizontal carousels are a form of sorting device used with small parts and products. They can be activated by a computer program or an electronic switch.
Vertical Carousels - Vertical carousels operate like horizontal carousels and have the same activation mechanisms but complete their function vertically rather than horizontally.
Instead of carts or roller beds, this system employs remote-controlled shuttles for lifting, lowering, and transporting pallets. The lane length is not constrained by inclines, allowing shuttles to accommodate a large number of pallet positions per lane. This system supports both FIFO (First In, First Out) and LIFO (Last In, First Out) inventory management methods.
A pallet rack is an upright structure made of steel framing with beams and connectors that are bolted, welded, or clipped together to form a shelving unit to store inventory and equipment. In warehousing, pallet racks are...
Storage rack, also known as racking, is a structure that stores items and materials and comprises at least two upright (vertical) frames, horizontal beams, and some sort of decking (bars, panels, meshes, or none)...
An adjustable work bench is a tool that allows the user to adjust and regulate the height of the work surface to a more ergonomic and comfortable position for the safe and effortless performance of work...
An AGV forklift is a driverless self-operating robotic device that has the ability to carry, lift, retrieve, and place loads for easy transfer from one location to another. An automatic guided vehicle (AGV) forklift is a computer controlled mechanism that...
Automated guided vehicles (AGV) or mobile robots are types of guided robotic systems that are not bounded by a fixed range of motion. Rather, it is self-contained and can move along a line, surface, or space...
An autonomous mobile robot (AMR) is a self-propelled self-powered mechanism designed to perform repetitive tasks or organizational functions using an internal guidance system. They are able to navigate their...
A forklift truck is an electrical or gas powered industrial piece of equipment with a metal fork platform attached to its front that can be used to lift heavy loads by inserting the fork platform under cargo, pallets, or...
A lab bench is a specially designed bench or table that is able to assist in the performance of laboratory experiments and tasks, including the handling of reagents and test samples. Part of the design process for...
A pallet stacker is a machine designed to assist the user in lifting, moving and handling palletized materials with ease. A pallet itself is a flat and horizontal structure used to support goods in a sturdy fashion...
A portable workbench is a flexible and mobile work surface that is designed to function in multiple environments for the purpose of preparing, constructing, or servicing a wide variety of industrial and commercial applications...
A workbench is a sturdy flat, smooth, molded surface that comes in a variety of sizes designed for specific tasks. They can be very complex for engineering design work, complicated machining, and intricate precision tooling or be a highly finished wood table for woodworking, metal work, and project design...
In 1954, when Arthur "Mac" Barrett, of Barrett Electronics Corporation, unveiled the first AGV, he named it Guide-o-Matic and described it as a driverless vehicle...