RTD Sensors
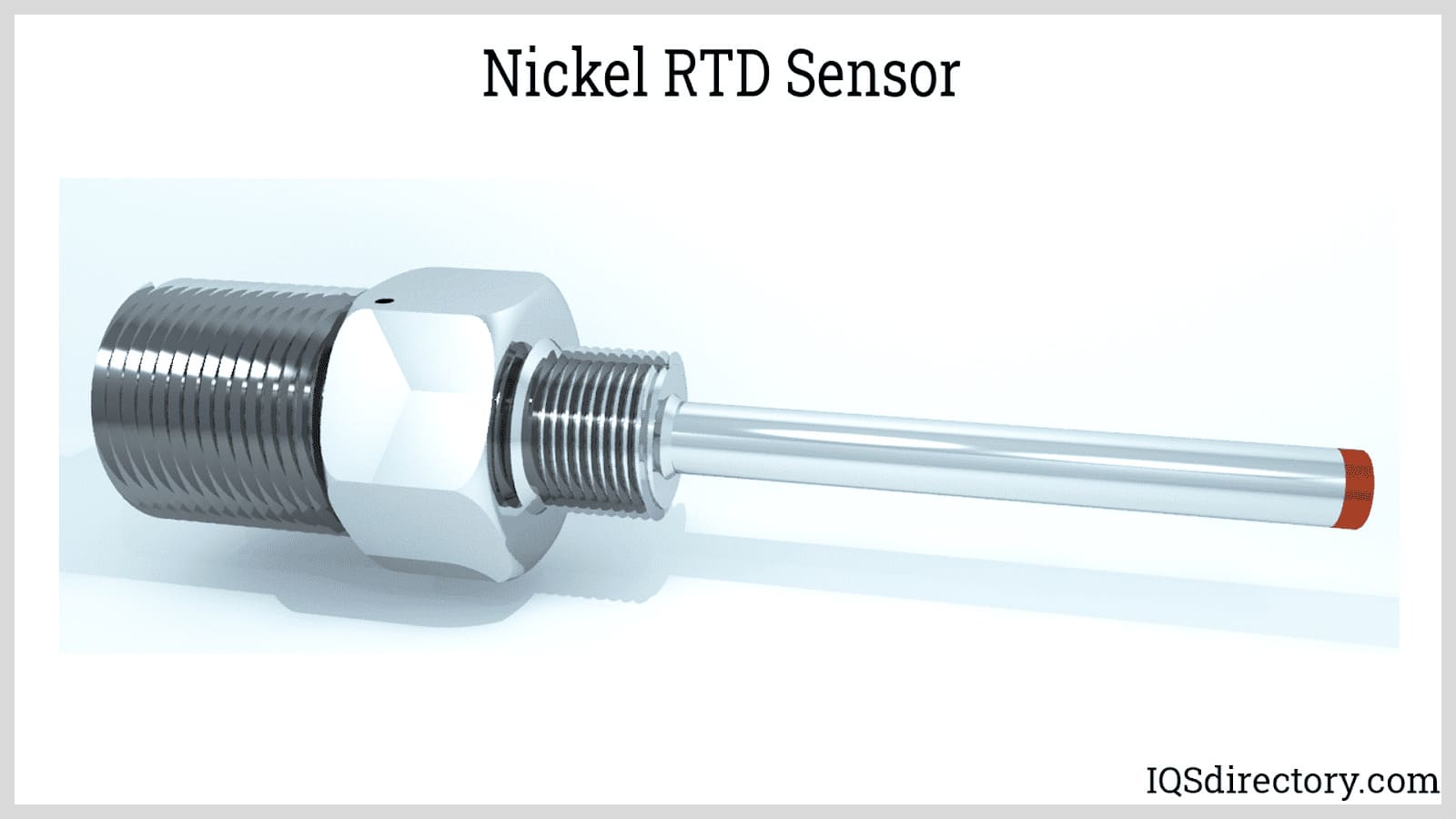
An RTD, resistance temperature detector, is a passive temperature sensing device that operates on the principle that the resistance of a metal changes as the temperature changes. The electrical current that passes through the element...
Please fill out the following form to submit a Request for Quote to any of the following companies listed on
This article will take an in-depth look at temperature sensors.
The article will bring more detail on topics such as:
This section delves into the fundamentals of temperature sensors, discussing their functions, main components, and how they operate.
Temperature sensors assess thermal conditions by converting thermal information into electrical outputs. These devices are prevalent in everyday items like thermometers, microwaves, refrigerators, and water heaters. They are also widely used in applications such as geotechnical monitoring.
A temperature sensor is a fundamental instrument that measures temperature, converting the data into a readable format. Certain sensors are tailored to specific needs, such as monitoring temperatures in structures like buildings, soil, large concrete formations, or boreholes.
Temperature sensors determine an object's thermal state, relying on a diode's voltage. This voltage changes as the resistance of the diode varies with temperature shifts.
As temperatures drop, diode resistance lessens, while rising temperatures cause the resistance to increase. This resistance is converted to a readable temperature value, shown numerically. In geotechnical monitoring, these sensors track internal temperatures of large infrastructure such as bridges, power plants, and dams.
Temperature sensors are varied, but they are primarily categorized by connection type: contact and non-contact sensors. Examples like thermistors and thermocouples involve direct contact with the objects they measure, unlike non-contact sensors that detect radiation from the heat source.
These meters are used in hazardous environments like nuclear and thermal power plants. They're also used for measuring hydration heat in sizable concrete constructions and in geotechnical monitoring to assess groundwater flow and seepage.
In concrete curing, temperature sensors play an essential role as they ensure proper setting by keeping the concrete warm. Seasonal temperature variations can induce expansion or contraction in structures, impacting their volume.
Temperature sensors work by monitoring voltage across a diode. An increase in temperature results in an increase in voltage and a corresponding reduction in voltage between a transistor's base and emitter terminals. Some sensors take advantage of stress variations due to temperature changes to function.
For vibrating wire temperature meters, different metals with distinct expansion coefficients are used. The sensor uses a magnetic wire under high tension between two metals, and temperature changes affect the wire's tension and its vibration frequency.
Among the metals, aluminum is commonly used due to its higher linear expansion coefficient compared to steel. The temperature-induced frequency changes can be monitored by the same read-out system used in other vibrating wire sensors.
The vibrating wire transducer senses temperature shifts, transforming them into electrical signals that are then translated into frequencies for read-out devices.
Temperature sensors consist of three categories of components. Essential components include elements such as thermocouple cables and sensing elements. Completing the sensor are items like insulating beads, connector heads, and protective tubes. Additional necessary components include controllers and converters for sensor operation.
To effectively integrate a temperature sensor into control or compensation circuits, the detection circuit must output data in usable formats. For analog systems, resistance typically serves as the output. For digital systems, this must be converted into a digital format using an analog-to-digital converter (ADC) to be processed by a microcontroller (MCU).
Semiconductor sensors with digital interfaces facilitate efficient communication with an MCU, which can read thermocouples due to their voltage-based outputs. RTDs and thermistors offer flexibility, allowing resistance or voltage outputs to adapt easily to compensation and control systems.
Both RTDs and thermistors provide variable resistance, which simplifies their inclusion in analog circuits. If voltage is required, resistance can be converted using a Wheatstone bridge with three other resistors, visualized below.
Non-linear sensors such as thermocouples or thermistors necessitate linearization of outputs. This can be managed simply in analog systems and through CPU lookup tables for digital systems, using the sensor's resistance and temperature specifications.
Engineers have multiple strategies for designing detection circuits to avoid overheating and achieve temperature control. Thermocouples are perfect for severe conditions, while platinum RTDs deliver precision. For applications involving PCBs where internal sensors are impractical, semiconductor types are adept at detecting temperature around sensitive electronics.
RTD elements act as resistance components in RTDs, typically not used alone but within assemblies designed to withstand various conditions. Each RTD has a set resistance at a known temperature, changing predictably. By assessing this resistance, calculations or instruments determine the temperature.
RTD elements are mass-produced through automated processes, layering platinum onto a ceramic base and using photolithography to carve a specified resistance path. Smaller than their wire-wound counterparts, thin film elements offer quicker responses, broader applications, and cost efficiency.
Ceramic elements in temperature sensors can be wound on ceramic or glass or use a partially supported platinum wire helix in a ceramic tube for ample temperature range and stability. Though other metals exist, platinum often pairs with ceramic or glass for optimal performance.
Using metals besides platinum can introduce linearity issues and drift at lower temperatures, affecting precision and necessitating frequent corrections, making platinum the preferred material.
Thermometrics can customize sensor elements with lead wires as specified, commonly using Teflon-coated nickel wires in 20 AWG size.
Wire-wound elements encased in glass or quartz are available to meet user-specific conditions.
This chapter explores the essential classes and types of temperature sensors commonly used in industrial automation, process control, HVAC systems, laboratory research, and compensation circuits. You’ll also learn about their sensor elements, measuring principles, applications, and advantages so you can choose the optimal temperature measurement device for your specific needs.
Temperature sensors come in numerous forms, including digital, analog, contact, and non-contact options, designed to suit a wide range of temperature monitoring and control applications. Broadly, these sensors are categorized into two main classes: contact temperature sensors and non-contact temperature sensors.
Contact-type temperature sensors measure heat or cold by physically touching or being immersed in the medium they are monitoring. These sensors directly sense temperature changes in liquids, solids, or gases. Common examples include thermocouples, RTDs, thermistors, and traditional glass thermometers. Contact sensors offer high accuracy and fast response times, making them suitable for environments where immediate, reliable measurements are critical.
Non-contact or remote temperature sensors determine temperature by detecting the infrared energy or thermal radiation emitted by an object or surface. These technologies are essential for temperature measurement when direct contact is impractical, unsafe, or could damage the target—such as in moving machinery, electrical equipment, or hazardous/contaminated environments. Infrared thermometers, thermal imaging cameras, and pyrometers fall under this category.
Both contact and non-contact classes encompass several types of temperature sensors, each engineered for specific use cases, accuracy levels, temperature ranges, and response time requirements. Below, we detail the most widely used temperature sensor types and highlight their operational principles and application areas.
A Resistance Temperature Detector (RTD), or resistance thermometer, measures temperature based on the change in electrical resistance of a metallic element as temperature fluctuates. RTDs are engineered from pure metals like nickel, platinum, and copper, with platinum RTDs (PT100 or PT1000) delivering the highest accuracy and long-term stability. These industrial temperature sensors are favored for calibration labs, process industries, and any application demanding precise and repeatable measurements across a temperature range of approximately -454°F to 1202°F (-270°C to 650°C).
RTDs are especially common in meteorological equipment, biotech labs, and the food industry due to their reliability, excellent linearity, minimal drift, and robust design for industrial temperature monitoring.
Thermocouple temperature sensors consist of two dissimilar metal wires joined at one end to create a measurement junction. The temperature difference between this junction and the reference end produces a voltage that is proportional to the temperature. Thermocouples are rugged, cost-effective, and capable of monitoring a vast temperature range from -328°F to 3182°F (-200°C to 1750°C), making them the preferred choice for high-temperature industrial process control, kilns, gas turbine exhaust, and furnaces, despite offering slightly lower accuracy compared to RTDs and thermistors.
Available in numerous types, thermocouples are selected based on calibration, temperature range, chemical resistance, vibration resistance, and installation requirements. Their flexibility makes them invaluable in industrial automation, manufacturing equipment, HVAC/R systems, and scientific instrumentation.
Thermocouple sensors are also favored for their fast response times, small size, and durability—even in harsh or corrosive environments. Regular calibration is important for maintaining measurement accuracy in thermocouple systems.
Thermocouple Types | |||||
---|---|---|---|---|---|
Thermocouple Type | Temperature Range (°C) | ||||
Short Term Use | Continuous Use | Class 1 Tolerance | Class 2 Tolerance | Class 3 Tolerance | |
Type E | -40 to 900 | 0 to 800 | -40 to 800 | -40 to 900 | -40 to 904 |
Type J | -180 to 800 | 0 to 750 | -40 to 750 | -40 to 750 | N/A |
Type K | -180 to 1300 | 0 to 1100 | -40 to 1000 | -40 to 1200 | -180 to 1300 |
Type N | -270 to 1300 | 0 to 1100 | -40 to 1000 | -40 to 1200 | -270 to 1304 |
Type R | -50 to 1700 | 0 to 1600 | 0 to 1600 | 0 to 1600 | N/A |
Type S | -50 to 1750 | 0 to 1600 | 0 to 1600 | 0 to 1600 | N/A |
Type T | -250 to 400 | -185 to 300 | -40 to 350 | -40 to 350 | -250 to 404 |
Type B | 0 to 1820 | 200 to 1700 | N/A | 600 to 1700 | 4 to 1820 |
Uses for Thermocouple Types:
Type E Thermocouples - Type E thermocouples use a combination of chromel (a nickel-chromium alloy) and constantan. They have a temperature range of -330°F to 1600°F (-200°C to 870°C) and provide excellent EMF (electromotive force) versus temperature characteristics. These thermocouples are suitable for use in sub-zero temperatures and inert environments but need protection when used in sulfurous conditions.
Type J Thermocouples - Type J thermocouples, similar to Type K, are general-purpose sensors made from iron and constantan, with the iron leg being positive and the constantan leg negative. They can be used either exposed or with a protective tube, which is recommended for durability. Type J thermocouples are suitable for use in vacuum, inert, and reducing environments. Like Type K thermocouples, Type J thermocouples require careful calibration and may be sensitive to electrical noise.
Type K Thermocouples - Type K thermocouples are made of Chromel®–Alumel® with small percentages of manganese and silicone. They are a general purpose thermocouple with a temperature range of -328°F up to 2462°F (-200°C up to 1350°C). Type K thermocouples need to be carefully calibrated and have small output signals. They are used in an assortment of environments including water, mild chemicals, gasses, and dry conditions. Common industries that use type K thermocouples are hospitals and food preparation. Regardless of their wide temperature range, type K thermocouples are mostly used for temperatures over 1004°F (540°C).
Type N Thermocouples: These thermocouples are composed of nicrosil (a nickel-chromium alloy) and nisil (an alloy of nickel, silicon, and magnesium). They operate within a temperature range of 32°F to 2300°F (650°C to 1260°C) and are known for their resistance to green rot and hysteresis. Common applications include use in refineries and the petrochemical sector.
Type R Thermocouples: Constructed from a combination of platinum and rhodium, Type R thermocouples can measure temperatures up to 2700°F (1480°C). They require protection through a gas-tight ceramic tube and an additional outer tube. These thermocouples offer enhanced stability and a broader temperature range compared to Type S. They are utilized in fields such as heat treatment, control sensors, semiconductor manufacturing, glass production, and metal processing.
Type S Thermocouples: Known for their precision and stability, Type S thermocouples are ideal for both high-temperature applications in the BioTech and Pharmaceutical industries as well as low-temperature scenarios. They cover a temperature range of -58°F to 2700°F (980°C to 1450°C).
Type T Thermocouples: Featuring copper and constantan, Type T thermocouples are suitable for temperatures ranging from -330°F to 700°F (-200°C to 370°C). They are used in inert atmospheres and are resistant to decomposition even in the presence of moisture. Typical applications include food production and cryogenic environments.
Type B Thermocouples: Type B thermocouples are designed for high-temperature applications and offer the highest temperature range among thermocouples, with remarkable accuracy and stability. Their construction includes platinum with 6% rhodium and platinum with 30% rhodium, operating between 2500°F and 3100°F (1370°C to 1700°C).
Type C Thermocouples: These thermocouples use tungsten and rhenium and are capable of measuring temperatures up to 4200°F (2315°C). They are suitable for use in hydrogen, inert, or vacuum environments to avoid oxidation failure. Type C thermocouples are equipped with protective sheaths made from molybdenum, tantalum, or inconel, and feature insulators such as alumina, hafnia, or magnesium oxide.
Thermistors are temperature-sensitive resistors that exhibit substantial and predictable changes in resistance corresponding to temperature shifts. Thermistors are widely used for their high sensitivity, rapid response, and excellent repeatability, making them ideal in medical temperature sensors, environmental monitoring, battery management systems, and precision electronic control circuits. They are cost-effective, but typically operate over a narrower range than thermocouples or RTDs, making them well suited for tighter temperature control in moderate ranges.
Traditional thermometer temperature sensors employ a calibrated glass tube filled with a liquid such as mercury or ethanol. The expansion or contraction of the fluid delivers a visual indication of temperature. Glass thermometers are still referenced as industry standards in scientific laboratories, pharmaceutical manufacturing, and meteorological monitoring, but are increasingly replaced by digital or electronic sensor technologies for safety and environmental reasons.
Bi-metal thermometers use two bonded metal strips with different coefficients of expansion. As temperature shifts, the coil bends or unbends, moving a needle to indicate the temperature. These mechanical dial thermometers are commonly installed in HVAC systems, industrial boilers, Petrochemical plants, and food service equipment for real-time temperature display without requiring external power sources. Their robustness and simplicity make them a mainstay for both field and in-process measurement.
When heat is applied to the sensing coil, it causes the coil to move. This movement translates into needle movement on the gauge, thereby indicating the temperature.
These thermometers, also known as filled system temperature sensors, utilize a sealed bulb and capillary containing gas or liquid that expands with temperature changes. They are valued for remote temperature monitoring, pipeline and storage tank applications, chemical processing, and outdoor weather stations. Gas and liquid thermometers are inherently stable and require minimal maintenance, providing years of dependable operation.
Digital thermometers employ electronic temperature sensing elements, such as thermocouples, RTDs, or thermistors, and output an easy-to-read temperature value on a digital display. These instruments are embedded throughout industrial, commercial, and medical devices—including laboratory freezers, cold chain monitoring, and food safety inspections—where precise digital temperature readings and memory logging are required. The integration of microprocessors enables advanced features such as data storage, programmable alarms, and wireless connectivity.
Infrared temperature sensors, also referred to as IR sensors or pyrometers, offer reliable non-contact temperature measurement by analyzing IR energy emitted from objects. These sensors are vital for monitoring surface temperatures of moving machinery, electrical panels, high-voltage components, and objects that are too hot, hazardous, or inaccessible for contact temperature probes. Infrared sensors support rapid response times and are widely used in predictive maintenance, food safety monitoring, motor winding protection, and thermal inspection across many industries.
By enabling temperature readings at a distance, infrared thermometers improve safety, streamline quality control, and enable real-time process adjustments in critical environments.
Thermal imaging sensors, also known as thermal cameras or thermographic cameras, are advanced non-contact instruments that convert infrared radiated energy into visible images. This technology allows for two-dimensional temperature mapping, highlighting hot and cold spots in complex assemblies, buildings, electronics, or live electrical panels. Thermal imaging is indispensable in predictive maintenance, medical diagnostics, security, fire prevention, and process optimization, offering comprehensive situational awareness in environments where traditional point sensors would fall short.
NTC thermistors decrease in resistance as temperature rises, showing a highly nonlinear yet sensitive response. Thanks to their rapid response and cost-efficiency across the -58°F to 482°F (-50°C to 250°C) range, NTC thermistors are ideal for automotive temperature sensors, HVAC systems, 3D printing, household appliances, and medical diagnostics. Their high sensitivity at narrow intervals enables pinpoint temperature control and circuit protection features.
Manufacturers often linearize the exponential output of NTC thermistors for improved integration with microcontrollers, PLCs, and analog-to-digital converters. Their adaptability, stability, and ease of installation make them one of the most common types of sensors in modern electronics and embedded systems.
Semiconductor-based temperature sensors, often implemented as integrated circuits (ICs), employ matched diode junctions to detect temperature-driven voltage changes. These sensors provide linear output and digital signal compatibility, making them ideal for embedded temperature sensing in consumer electronics, smart sensors, data loggers, and microcontroller-based systems.
Suitable for applications requiring on-board diagnostics, environmental monitoring, and over-temperature protection, these sensors operate reliably within a -94°F to 302°F (-70°C to 150°C) range. Their ease of integration and low power consumption make them a mainstay of modern IoT devices, automotive electronics, wearables, and wireless sensor networks.
Vibrating wire temperature sensors are specialized devices used for precise internal temperature measurement in civil engineering, geotechnical projects, and structural health monitoring, such as within concrete dams, tunnels, and water containment systems. By leveraging frequency shifts in a tensioned wire, these sensors offer outstanding long-term stability and high accuracy (resolution better than 0.1°C) over the -4°F to 176°F (-20°C to 80°C) range, making them crucial for real-time safety and durability assessments in large-scale infrastructure.
Selecting the most appropriate temperature sensor depends on key factors such as target temperature range, required measurement accuracy, environmental conditions (humidity, vibration, chemical exposure), response time, installation constraints, and connectivity or compatibility with control systems (e.g., PLCs, SCADA, or IoT platforms). Digital temperature sensors and wireless temperature monitoring systems are increasingly favored for their flexibility, remote access, and seamless data logging.
In industrial automation, RTDs and thermocouples are preferred for high-precision process control and harsh environments, whereas thermistors and IC-based sensors are optimal for portable devices, electronics, and applications needing frequent calibration in moderate environments. Non-contact methods, like infrared thermometers or thermal imaging systems, are essential for safety compliance, machine diagnostics, or fast-moving objects. Consulting a reputable temperature sensor manufacturer, system integrator, or engineering partner ensures proper sensor selection, specification, installation, and ongoing support, maximizing performance and reducing downtime.
For more extensive information or to browse and compare leading temperature sensor suppliers and manufacturers, visit our product directory, where you can request technical datasheets, quote prices, and learn about industry certifications, calibration services, and after-sales support.
This chapter will discuss the applications and benefits of temperature sensors. It will also discuss temperature control using temperature sensors.
Temperature sensors play a crucial role in measuring temperature across diverse applications and industries. They are ubiquitous, found in both industrial environments and daily life. Here are some examples of how temperature sensors are used:
Temperature sensors are employed to monitor a range of environments and equipment, including power plants and manufacturing processes. They measure water temperatures in reservoirs and boreholes, assess temperature-induced stress and volume changes in dams, and study the impact of temperature on other installed instruments.
Temperature sensors are used in scientific research and biotechnology monitoring.
Temperature sensors are employed in various medical applications, including patient monitoring, medical devices, thermodilution, humidifiers, gas analysis, cardiac catheters, ventilator flow tubes, and dialysis fluid temperature management.
Temperature sensors are used to measure inlet air temperature, exhaust gas temperature, engine temperature, and oil temperature.
Temperature sensors are employed in kitchen appliances such as ovens and kettles, as well as in various white goods.
Temperature sensors are used in air conditioning and heating ventilation systems, whether for residential or commercial applications.
Temperature sensors are employed in refrigerated vans and trucks to monitor and control temperature during transport.
Temperature sensors offer several advantages, including:
When choosing a temperature sensor for a specific application, several factors need to be taken into account. Consider the following aspects when selecting a temperature sensor:
Various types of temperature sensors are designed to measure different temperature ranges and may offer higher accuracy within specific ranges. Before purchasing, ensure that the sensor's temperature range matches the requirements of your application. This information is typically detailed in the sensor's datasheet.
Applications may have specific accuracy requirements. Note that thermocouples generally exhibit greater long-term stability variance compared to thermistors and RTDs.
The choice of temperature sensor depends on the available space within the application. A smaller device may be necessary if space is limited. Additionally, the package style of the sensor affects how it connects to the application and measures temperature, making it a crucial factor to consider.
The placement and selection of a temperature sensor are significantly influenced by the environmental conditions in which it will operate. Factors such as humidity, vibrations, and other environmental elements can impact the sensor's stability and accuracy. Additionally, electrical noise can affect readings, particularly when detecting small temperature changes. Ensuring that the sensor is used in a low-noise environment is essential for obtaining accurate measurements.
To ensure optimal performance, it is crucial to thoroughly assess the conditions and environment where a temperature sensor will be installed. In addition to evaluating the sensor's structure, it is important to protect any connections, such as lead wires, from harsh and unstable conditions.
To safeguard a temperature sensor and its wiring from environmental conditions, protective measures such as durable metal sheaths that resist wear and corrosion can be employed. While these sheaths enhance protection, they can also increase the sensor's cost and impact its sensitivity. Moreover, some sensor configurations require specific mounting considerations to ensure a reliable thermal connection.
Temperature sensors play a crucial role in effective temperature control. Below are five key factors for achieving efficient temperature management:
In system design, selecting a temperature sensor is often one of the final decisions. This choice is typically influenced by the compatibility with the system's process controller, as well as factors like availability and cost. However, essential selection criteria such as sensor mass, operating temperature, signal strength, reading sensitivity, and ambient conditions are frequently overlooked.
In commercial temperature control, three primary types of sensors are commonly used: thermistors, thermocouples, and resistive thermal devices (RTDs). Each sensor type has distinct characteristics, and within each category, different styles are designed to meet specific temperature ranges, output signals, and process compatibility based on their construction materials.
The sensor should be chosen to align with the specific parameters of the design application. Sensor mass is a critical characteristic to consider: heavier sensors generally have a slower and more dampened response to temperature changes, while lighter sensors respond more quickly. For applications requiring precise temperature control, a lighter sensor is often preferred due to its faster response time.
The placement of the temperature sensor is critical, even if it seems straightforward. In some cases, physical obstacles during field installation may necessitate modifications to the initial design location. If placing the sensor in the ideal position proves challenging, it's important to consider potential compromises and alternative solutions.
Nevertheless, the sensor's placement is crucial to the overall success of the system. It is essential not to sacrifice system efficiency for the sake of easier sensor installation. Below are some tips to avoid common pitfalls:
The primary objective of any temperature control system is to achieve a balance between heating and cooling capabilities. Mismanagement of this energy balance can lead to temperature instability. The two fundamental types of controls used are proportional output control and on/off output control.
The on/off control is the simplest type of temperature control to understand. It operates based on the system's temperature setpoint, activating the full capacity of the heating or cooling system when the temperature deviates from this setpoint. The system continues to operate at full capacity until the temperature reaches the setpoint, at which point the equipment is turned off. On/off control can be a cost-effective method, especially when the mass of the process is larger than the heating or cooling capacity and when a wide temperature fluctuation is acceptable.
However, there are practical limitations to this approach. Since a system's capabilities often exceed the load requirements in various situations, simply turning the heating or cooling equipment on and off is usually impractical.
To improve the control capacity of on/off systems, one approach is to incorporate multiple levels or stages of capacity into the heating or cooling system.
Process control becomes more manageable when all equipment subsystem functions are predictable. However, energy-saving measures and management improvements can sometimes destabilize temperature control. Many modern systems are designed to automatically adjust several variables in response to changes in load, helping to maintain stability despite these fluctuations.
Commonly adjusted variables in temperature control systems include supply fluid temperature, process fluid volume, and heating or cooling capacities. Modifying subsystems such as supply temperatures, process pressures, and fluid flow can alter the system’s characteristics, potentially leading to temperature instability and control issues. For example, in a plant chiller system, changing the rate of flow of the process fluid can impact overall performance.
A reduced flow rate can significantly alter heat-transfer characteristics in some system components and heat exchangers. This loss in heat transfer efficiency may lead to temperature instability at critical points and could potentially cause the compressor or other components to malfunction.
Proportional controllers typically come in three design types: (PID) proportional plus integral plus derivative, (PI) proportional plus integral, and (P) proportional only. Advances in small process controllers have given engineers greater flexibility in their designs.
Advancements in controller technology have enhanced their ability to compensate for system design flaws and unpredictable characteristics. The simplest type of controller is the proportional controller, which forms the basis for many small electronic devices. A proportional controller operates by responding to temperature deviations, generating an output signal based on a linear calculation where changes in deviation result in a proportional change in output.
A temperature sensor can also be defined as a simple instrument that measures the degree of coldness or hotness and then converts it into a readable unit. There are different types of temperature sensors, including thermocouples, thermistors, RTDs, etc. Each temperature sensor has its own unique characteristics, which makes it suitable in specific types of applications. However it is important to consider the temperature range, accuracy, size, and stability of a temperature sensor for optimal performance within a specific application.
An RTD, resistance temperature detector, is a passive temperature sensing device that operates on the principle that the resistance of a metal changes as the temperature changes. The electrical current that passes through the element...
A thermistor, a shortened version of the term thermal resistor, is a passive component whose resistance changes as the temperature in a system changes. Thus they serve as an inexpensive, accurate, and dynamic method for measuring temperature...
A thermocouple is a transducer that converts thermal energy into electrical energy and is constructed by joining wires made from dissimilar metals to form a junction. Voltage is produced when the temperature at the junction changes...
A thermowell is a pressure-tight vessel that safeguards and increases the lifespan of temperature sensors in processing plants in cases where a measuring sensor is not otherwise mechanically or chemically useful in...
A band heater is a heating device that clamps onto objects to provide external heat using radiant and conductive heating. The different mounting methods of band heaters makes it possible to secure them tightly and...
A cartridge heater is a cylindrical tubular heating device that provides concise and precise heating for various forms of materials, machinery, and equipment. Unlike an immersion heater, a cartridge heater is inserted into a hole in the item to be heated to furnish internal radiant heat...
Ceramic heaters are electric heaters that utilize a positive temperature coefficient (PTC) ceramic heating element and generate heat through the principle of resistive heating. Ceramic materials possess sufficient electrical resistance and...
Electric heating is produced by using a known resistance in an electric circuit. This placed resistance has very few free electrons in it so it does not conduct electric current easily through it. When there is resistance in...
A flexible heater is a heater made of material that can bend, stretch, and conform to a surface that requires heating. The various forms of flexible heaters include polyimide film, silicone rubber, tape...
A heating element is a material or device that directly converts electrical energy into heat or thermal energy through a principle known as Joule heating. Joule heating is the phenomenon where a conductor generates heat due to the flow of electric current...
An immersion heater is a fast, economical, and efficient method for heating liquids in tanks, vats, or equipment. Known as bayonet heaters, they have heating elements that can be directly inserted into a container of water, oil, or other material in order to heat the entire contents...
Infrared heating is a heating method used to warm surrounding bodies by infrared radiation. Thermal energy is transferred directly to a body with a lower temperature through electromagnetic waves in the infrared region...
Radiant heaters are systems that generate heat internally and then radiate it to the nearby objects and people. The sun is a basic example of a radiant heater. When we feel warm on our bodies on a sunny day...
The idea of an electric heater seems to be out of place in modern society since most buildings have a sophisticated central heating system. That may be true, but electric heaters can be a helpful way of saving energy while providing efficient heating...