RTD Sensors
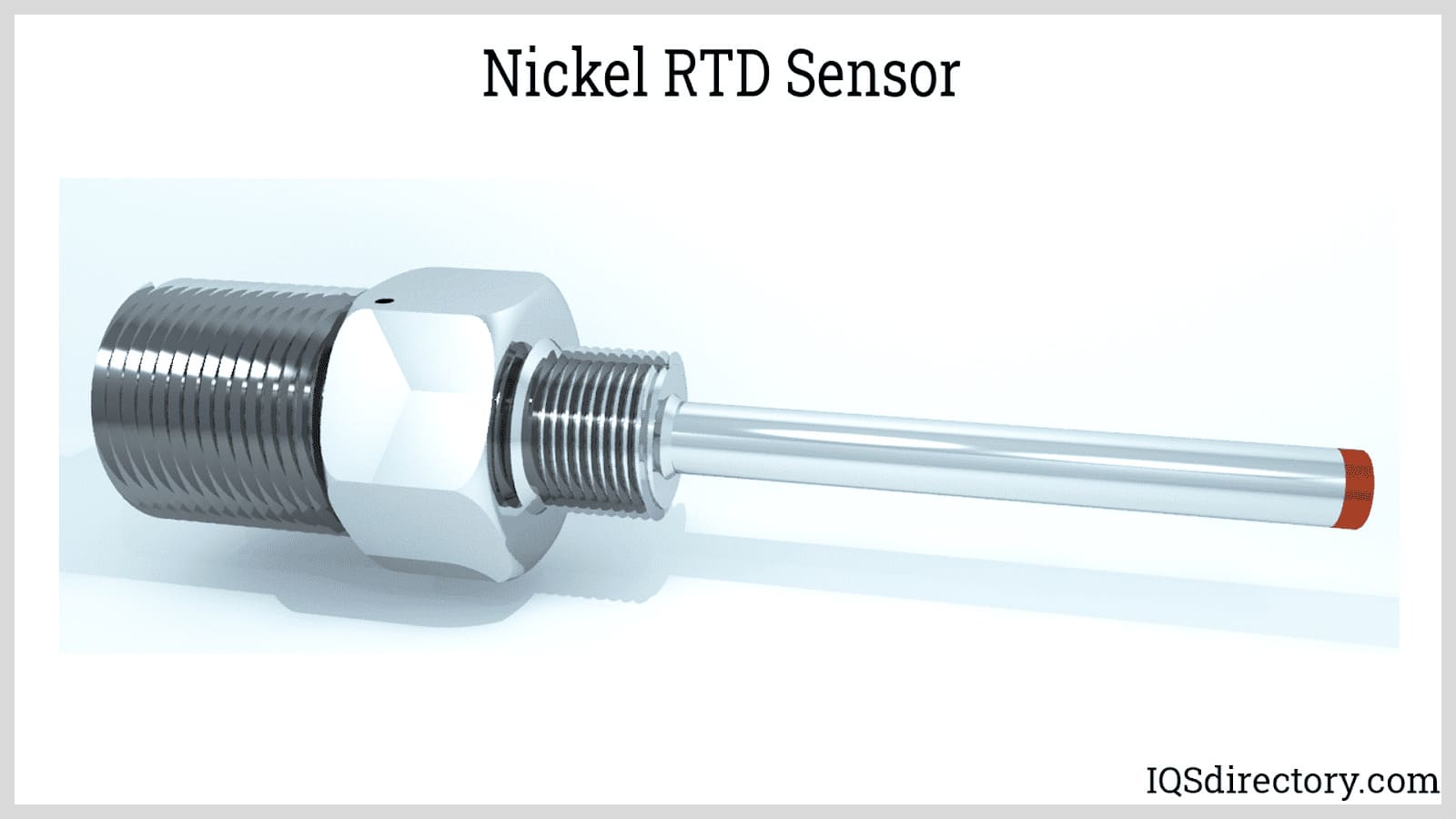
An RTD, resistance temperature detector, is a passive temperature sensing device that operates on the principle that the resistance of a metal changes as the temperature changes. The electrical current that passes through the element...
Please fill out the following form to submit a Request for Quote to any of the following companies listed on
This article will give more detailed information regarding thermowells on topics such as:
This chapter presents a comprehensive introduction to thermowells, covering their definition and function. It explores their operational process and highlights their essential contribution across varied industries. By grasping these factors, readers will recognize the pivotal role thermowells play in ensuring precise temperature readings and maintaining the integrity of systems.
A thermowell is a pressure-resistant enclosure crafted to safeguard and prolong the life of temperature sensors in processing environments, especially where direct placement of sensors is unfeasible due to mechanical or chemical limitations. Thermowells are installed directly into piping systems, allowing sensor replacement within high-pressure pipelines without disrupting process operations or necessitating system drainage. Furthermore, standardized thermowells aid in the easy removal and maintenance of sensors across the plant, enhancing process efficiency.
Thermowells protect temperature sensors—such as bimetal thermometers, thermocouples, and thermistors—from corrosion, high velocities, and extreme pressures. This protection not only increases sensor longevity but also facilitates their replacement without draining the system, reducing contamination risks. In high-pressure scenarios, thermowells are precision-machined from bar stock to ensure durability, whereas those for lower-pressure settings may be made from tubing with a welded end.
A thermowell serves as a barrier between the temperature sensor's sensing element and the process medium being handled. It provides protection from corrosive materials, pressurized substances, and rapid movement. Additionally, a thermowell allows for the sensing component's removal from an application while keeping the system sealed. Thermowells find usage both in simple applications like cooking pots in the food industry and more complex setups such as boilers in the brewing industry, where precise temperature control is vital.
In industrial settings where exact temperature measurement is essential, thermowells are vital. They offer indispensable protection to temperature sensors from harsh conditions, including corrosion, high speeds, and extreme pressures, thereby ensuring dependable and accurate readings.
To select the optimal thermowell for industrial temperature measurement, it is vital to assess a comprehensive set of specifications. Key factors include material compatibility (e.g., stainless steel, carbon steel, Inconel, Monel, Hastelloy), pressure and temperature ratings, mechanical strength, length and diameter, insertion depth, and end connection type. It is also essential to ensure compliance with industry standards such as ASME PTC 19.3 TW, DIN, and other relevant codes, as well as to verify the thermowell is robust and suitable for the process environment (including corrosive media or high-velocity flow applications). Specifying the proper thermowell dimensions and confirming its vibration resistance and wake frequency calculation performance are crucial for long-term durability and safety.
Thermowell Root Dimension (Q): This refers to the thickest part of the thermowell that is inserted into the pipe wall. It is crucial because it correlates with both the size of the process connection and the diameter of the thermowell bore.
Thermowell Immersion Length (U): The thermowell immersion length is the distance from the tip of the thermowell to the base of the process connection. Proper immersion ensures reliable process temperature readings and reduces thermal lag.
Thermowell Bore Size (V): The thermowell bore size refers to the internal diameter of the thermowell. Standard bore diameters are typically 0.260" and 0.385", which are designed to fit sensors with corresponding diameters of 0.25” or 0.38”. Ensuring the correct bore size allows seamless insertion of temperature sensors such as thermocouples or RTD probes.
Thermowell Lagging (or Trailing) Extension Length (T): The thermowell lagging extension length is the portion of the thermowell that extends beyond the pipe wall after installation. This length is typically an extension of the thermowell's hex length and is defined by the cold head of the process connection. Lagging extensions are essential for processes using insulation or heat tracing.
The Hex Length (P): The hex length measurement is the distance from the top of the mounting threads to the tip of the stem. Proper hex length allows for convenient installation using standard tools.
Thermocouple Probe: A thermocouple probe consists of a metallic tube housing thermocouple wire. Due to the lagging extension length, the probe and thermowell can extend through insulation or walls. The tube wall of the probe is referred to as the sheath, which is commonly made from steel or other corrosion-resistant materials. The close fit between the probe sheath and thermowell interior is important for maximizing heat transfer and accurate sensor performance.
Proper thermowell installation is critical to achieving accurate temperature measurement and ensuring long service life in process instrumentation systems. When installing a thermowell through insulation on a pipeline or equipment, lagging (heat-insulating material for pipes) is used to minimize heat loss and prevent measurement errors. To help avoid common installation failures in industrial and commercial applications, consider the following:
It's also crucial that the gap between the thermowell's internal diameter (ID) and the thermocouple sheath's outer diameter (OD) is minimal to ensure accurate temperature measurements and avoid potential inaccuracies. Additionally, the thermowell's bore should be uniform and smooth to facilitate the easy insertion of the thermocouple during installation.
For critical applications—such as steam lines, chemical processing, or offshore oil and gas facilities—following wake frequency calculations and adhering to engineered installation practices will help minimize vibration-induced failures. Periodic inspection and maintenance are recommended for reliable performance.
Thermowells must be designed to handle specific process media and varying conditions such as pressures, temperatures, velocities, and specific gravities. Additionally, a well-functioning thermowell design should consider the following factors to optimize process safety and measurement accuracy:
Thermowells come in various types, classified by their end connectors—the parts that interface with a measuring sensor's connector. The choice of thermowell depends on the connector type used by the measuring sensor. Below is a list of end connector types, which will be explained in more detail:
Threaded Thermowells: As the name implies, threaded thermowells are screwed directly into the wall of a tapped pipe. These thermowells are generally the most cost-effective and versatile option, commonly used in non-corrosive or general-purpose process temperature measurement, such as measuring the temperature of molten iron, water, or air, where protecting the thermowell threads from rust is crucial. Due to their material properties and design, threaded thermowells can also be brazed or welded to enhance strength and durability.
Socket-Welded Thermowells: Socket-welded thermowells offer a robust and permanent connection, making them ideal for applications involving extremely high temperatures and pressures. The socket-welded joint provides a secure connection that resists pressure and withstands high temperatures. Additionally, in industries such as food, beverage, and pharmaceuticals, where thread impurities must be avoided, socket-welded thermowells are preferred. This is because the welded socket joint eliminates the risk of impurities or air entering the process, ensuring the integrity of the food or medicine being produced. This style is compliant with many sanitary and CIP (Clean-In-Place) requirements.
Van Stone Thermowells: Van Stone thermowells are well-suited for high-pressure applications due to their robust construction, which allows them to withstand significant forces. Typically, a Van Stone thermowell is secured between a cover flange and nozzle, and is machined from solid bars. The flange surface features a phonographic or continuous spiral serration, which provides multiple grades of surface polish. This design not only enhances the thermowell's strength and durability but also ensures a precise and reliable fit in high-pressure environments often found in refineries and power plants.
Scruton Thermowells: To mitigate damage from mechanical loads and address process criticality—based on a company’s risk matrix study—a Scruton thermowell is designed using the ScrutonWell® design. This design incorporates a helix on the outside of the thermowell, facilitating quick and easy installation without the need for a support collar. This approach not only prevents costly and time-consuming site rework but also reduces oscillation amplitude by over 90%. Additionally, the ScrutonWell® design allows for various grades of surface polish, saving both time and money on site rework. Scruton thermowells are especially recognized in the petrochemical industry for reducing risk of catastrophic vibration-induced failure.
Sanitary Thermowell: A sanitary thermowell isolates and protects the sensing element of a temperature sensor. These thermowells are designed with hygienic connections such as tri-clamp or sanitary flanges to prevent microbial growth and meet FDA and 3-A sanitary standards. Sanitary thermowells are essential in food processing, pharmaceutical, and biotech manufacturing to ensure contamination-free measurement.
Various methods are used to connect thermowells to piping systems, and these connections can help identify the type of thermowell as well as their potential industrial application. Here are some common types of thermowell connections:
Flanged Thermowells: A flanged thermowell features an extended "collar" that offers enhanced support by securing the thermowell firmly to the pipe. These are commonly specified for high-pressure, high-velocity, or hazardous process media because they provide reliable sealing and simplify maintenance or replacement in critical service areas.
Weld-in thermowells: Weld-in thermowells are directly welded into a pipe or process vessel, providing the highest quality and permanent connection available. This installation method guarantees robust performance and is ideal for continuous process systems exposed to high temperatures, pressures, or dynamic loads—such as refineries, chemical plants, or power generation. Since maintenance requires cutting or grinding, welded thermowells are best suited for applications with infrequent sensor removal or replacement. Weld-in thermowells are commonly used in systems handling non-corrosive media.
Threaded Thermowells: Threaded thermowells are commonly used in smaller pipelines carrying non-corrosive fluids. They are screwed into the pipe and are not intended for frequent replacement. Below are some typical applications where threaded thermowells are frequently employed:
Threaded thermowells are favored in these applications because they ensure a tight fit, preventing air or water from entering and causing corrosion inside pipes or equipment. This also helps avoid contamination in manufacturing processes. These connections are also suitable for both temperature transmitters and digital temperature sensors in automation and process control systems.
There are four distinct stem design shapes for thermowells, each suited to specific applications and process conditions:
The diameter of a straight thermowell remains uniform along its entire length, making it straightforward to manufacture. This design provides excellent stiffness and protection against erosion and corrosion, and is preferred for low-velocity or less demanding applications. In contrast, stepped thermowells feature a graduated diameter, typically with a larger diameter at the top (often 3/4") and a smaller diameter at the tip (commonly 1/2"). This design facilitates smoother flow and faster temperature response due to reduced thermal inertia at the process end. Stepped thermowells are often specified for general processing where both accuracy and cost-efficiency are required.
A tapered thermowell features a gradually changing diameter along its entire insertion length, providing a smooth, continuous taper. This design enhances response time and vibration resistance, making it ideal for heavy-duty applications where quick temperature measurements are needed due to its reduced wall thickness. Tapered thermowells are industry-standard for use in power plants and high-velocity pipelines. On the other hand, built-up thermowells are designed for applications requiring long insertion lengths, such as in large boilers or deep tanks. These thermowells incorporate a pipe section welded between the tip and process connection, allowing for deeper insertion into vessels with larger liquid volumes. This construction is particularly useful for thermocouples and RTDs that need to measure temperatures in extended or deep vessels where installation flexibility is crucial.
In addition to classifying thermowells by their end connections, they can also be categorized based on the materials used in their construction, their shank design, and their intended use. The thermowell material selection affects corrosion resistance, mechanical integrity, and thermal response—key to a reliable temperature measurement system. Stainless steel, carbon steel, brass, and exotic alloys are chosen based on process compatibility and cost considerations. The shank design—such as solid, tapered, or stepped—directly influences strength, vibration resistance, and sensor response speed. Choosing between these options often involves computational analysis of process conditions and wake frequency compliance, ensuring plant safety and regulatory adherence.
Bar Stock Thermowells: These thermowells are crafted from bar stock, a raw, purified metal that is machined and drilled without the need for welding. Bar stock thermowells are preferred for high-stress or corrosive applications and provide maximum strength and metallurgical integrity, often specified in refinery and power plant environments.
Thermowell Classification by Type of Shank: The shank of a thermowell is the part that is inserted into a process piping system or vessel. Common types of shanks include straight, stepped, and tapered designs. A straight-shank thermowell maintains a constant diameter along its immersion length. Step-shank thermowells feature varying diameters along the immersion length, which allows for quicker reaction times. Tapered thermowells have a diameter that gradually decreases along their immersion length. Historically, the ASME PTC 19.3 standard (1974) provided outdated definitions for tapered thermowells, leading to the development of the heavy-duty tapered thermowell for more demanding applications. This type is specifically designed for high-pressure and high-temperature environments and is commonly used in heavy-duty settings where thermowells are threaded into or welded to flanges, or welded directly into pipes or process vessels. For applications where resistance to velocity-induced resonance is crucial, and the inner nozzle diameter is a design constraint, the straight shank thermowell is often the most suitable choice.
Lagging extension is another category of shank thermowells. As detailed in Chapter Two, lagging extension refers to the length of a thermowell that remains exposed after it has been inserted into a piping system. These thermowells are specifically designed for use in conjunction with insulation, allowing them to extend through the insulating material that covers the vessel or piping system. Lagging extension thermowells are important in chilled water, HVAC, and cryogenic applications, as well as in process facilities with significant thermal insulation. They prevent heat loss and ensure that temperature measurements reflect the actual process conditions, not the temperature of the insulation or surrounding ambient air.
Proper thermowell design is critical to ensuring reliable temperature measurement and process safety in harsh industrial environments. To guarantee that a thermowell can endure operational hydrostatic pressure limits, dynamic static stress, and fluid-induced vibration from process conditions, several essential engineering calculations are required. One pivotal assessment is the wake frequency calculation, which determines the risk of resonance due to vortex shedding. This calculation evaluates the ratio of the Strouhal frequency (the natural oscillation frequency induced by turbulent flow) to the natural frequency of the thermowell itself. According to the widely adopted ASME PTC 19.3 standard—a benchmark for thermowell design and mechanical integrity evaluations—this ratio must not exceed 0.8 to minimize the risk of resonance and subsequent fatigue failure.
These calculations utilize the Strouhal number (\( \text{St} \)), calculated with the formula \( \text{St} = \frac{f_{st}D}{U} \), where \(f_{st}\) is the vortex shedding frequency, \(D\) is the diameter of the thermowell stem (circular cylinder), and \(U\) is the ambient flow velocity. The accuracy of this formula is vital for predicting and mitigating vortex-induced vibration. In addition to wake frequency analysis, it's crucial to apply steady-state stress analysis in the final design phase, considering the thermowell's length, stem design, and mounting configuration. This holistic approach helps validate the thermowell's structural integrity for both startup and operating conditions, increasing operational reliability and preventing unscheduled downtime caused by thermowell failures. Furthermore, finite element analysis (FEA) and computational fluid dynamics (CFD) simulations are powerful tools often used for advanced validation of thermowell performance in challenging process fluids such as steam, oil, or corrosive environments.
When selecting a thermowell for your application, considering these calculations ensures the design will not only meet safety codes but also optimize your process for longevity and performance.
As process fluids flow past a thermowell, a turbulent wake is produced downstream, resulting from changes in fluid momentum at the well surface. This phenomenon causes the formation and shedding of vortices from alternating sides of the thermowell, leading to vibration. The vortex shedding frequency (wake frequency) is inversely proportional to the tip diameter and directly proportional to the fluid velocity, critical for industries such as power plants, refineries, chemical processing plants, and other applications involving high-velocity or high-density media.
Vortex-induced forces on the thermowell include:
The ASME PTC 19.3 standard specifically addresses thermowell vibration by requiring the wake-to-natural frequency ratio to remain below 0.8. It also highlights the importance of the oscillating lift force in vibration analysis and warns against potential underestimation of risk when using simplified models such as the Murdock analysis, which may lead to velocity ratings up to 50% lower in high-density, high-pressure fluids. Engineers must leverage these calculations as design guidelines rather than absolute determinants. Best practices include reviewing historical process data, consulting manufacturer-provided tools or charts, and considering the full range of expected process fluid dynamics. Advanced vibration analysis may also incorporate span-to-tip ratios, mounting style considerations, and other parameters to ensure the selected thermowell both meets regulatory requirements and enhances operational lifespan.
For critical applications, ongoing monitoring for excessive vibration and routine inspection can prevent premature failure and maintain system integrity.
The relationship between fluid velocity and thermowell vibration is fundamental to robust thermowell design. As process fluids sweep past a thermowell, swirling eddies and low-pressure zones—collectively known as vortex streets—form downstream. This dynamic flow pattern generates two predominant periodic forces on the thermowell:
Vortex shedding frequencies typically range from 50 Hz to 1500 Hz and can be accurately modeled using industry-standard formulas. The force exerted on the thermowell due to vortex shedding scales with the square of the fluid velocity, while the shedding frequency increases linearly with velocity. If the Strouhal frequency approaches the natural frequency of a thermowell, or matches its harmonic (2fs), resonance may arise, culminating in severe amplification of dynamic forces and raising the risk of fatigue failure or cracking.
To mitigate vibration damage, it's essential to keep the thermowell's natural frequency outside critical resonance ranges for both in-line (drag) and transverse (lift) vibration responses. Two key parameters—critical velocity for transverse response and for in-line response—must be considered for each thermowell configuration. The critical velocity for transverse resonance is roughly twice that of the in-line resonance due to the frequency relationship of the acting forces.
For engineering teams, monitoring fluid velocity setpoints and verifying against calculated critical velocities is extremely important to ensure long-term reliability and safety. Acceptable operation at in-line resonance is possible provided cyclic stress is kept within allowable safety limits, and proper damping techniques or specialized thermowell designs (such as helical strakes or shortened immersion lengths) are implemented to suppress vibration. These approaches, often validated through laboratory or in-line testing, can substantially reduce risk in demanding process environments.
Resonance-induced fatigue remains one of the leading causes of thermowell failure. By employing vigilant design, continuous vibration monitoring, and adherence to standards such as ASME PTC 19.3, facilities can maximize equipment longevity, enhance sensor accuracy, and maintain plant safety. For additional technical resources, see the ASME Thermowell Design Standard.
The lifespan of a thermowell is heavily influenced by the material used in its construction. Key factors to consider when selecting a material include the operating temperature, the types of chemicals the thermowell will be exposed to, and the flow rate it will encounter. Chemicals can accelerate corrosion, particularly at elevated temperatures and concentrations, while suspended particles in the fluid can cause erosion. Here is a list of some of the most commonly used materials for thermowell construction:/p>
Carbon steels can only be used in low-temperature, low-pressure applications because of their low resistance to corrosive chemicals. The most-common material used to create thermowells is stainless steel. Thermowells made from stainless steel are affordable and have high heat and corrosion resistance. One high-strength steel used for pressurized vessels is chromium/molybdenum steel. Molybdenum increases corrosion resistance when added to chromium. The elements cobalt, nickel, chromium, and tungsten make up the Haynes alloy®. It is most frequently utilized during carburizing heat treatment, and in chlorine or sulfide conditions.
Insertion Length: The distance from the thermowell's connection point to the tip is known as the insertion length. The insertion length should be long enough to allow the entire temperature-sensitive section of the measuring device to extend into the measured medium in order to attain the highest level of accuracy. A minimum of one inch should be added to the length of the temperature-sensitive part when using a temperature sensor to measure the temperature of liquids. When the length of the temperature-sensitive segment will be submerged in gas or air, an additional three inches should be added. A thermocouple or thermistor can use a thermowell with a lower insertion length since its temperature-sensitive region is shorter. For acceptable accuracy, the temperature-sensitive portion of bimetal thermometers, RTDs, and liquid-in-glass thermometers must be submerged at least 2½ " in liquids.
In which industrial fields are thermowells used, and what benefits do they provide? Thermowells are employed in industries such as petrochemical, food processing, refining, cosmetics, chemicals, power generation, and pharmaceuticals. They protect equipment from external forces and disturbances, including pressure, abrasion, vibration, and corrosion from the processed medium. Additionally, thermowells allow for the removal and replacement of sensors without causing disruptions to the manufacturing environment.
How do thermowells enhance temperature measurement processes and contribute to cost savings? Thermowells offer significant benefits by protecting against corrosion, high material velocities, and extreme pressure damage. They also facilitate the replacement of temperature sensors without needing to drain the system. In summary, thermowells are designed to provide cost savings in various industries. Below is a summary of factors to consider regarding a thermowell’s cost-saving potential.
Longevity: How are thermocouples and RTDs typically protected, and what role do thermowells play in extending their lifespan? Thermocouples and RTDs are often housed in 1/4" diameter stainless steel probes, which provide adequate protection in relatively inert environments. However, in more hostile conditions, such as those involving temperatures above 1000°C (1832°F), the stainless steel can become stressed and the sensor probe may warp. The process medium itself can also be harsh, with corrosive substances like acids or seawater, or solid particles in gases, further challenging the probe's durability. High pressures can exacerbate the negative effects of high temperatures and corrosive environments. Thermowells significantly extend the lifespan of temperature sensors by absorbing and mitigating these harsh conditions.
Sensor Replacement Cost Analysis: How does the cost of temperature sensors and the protection offered by thermowells impact their overall value? The cost of RTDs, thermocouples, or thermistors can vary widely based on the sensor type and its susceptibility to degradation under harsh conditions. The protection provided by a thermowell becomes particularly valuable if the sensors are expensive or operate in demanding environments. Although thermowells represent an additional expense, this cost is often outweighed by the savings achieved through reduced sensor replacement frequency. Conducting a cost-benefit analysis can help determine when investing in a thermowell shifts from being a discretionary expense to a necessary investment, similar to other manufacturing decisions.
Labor Costs: Even if a temperature sensor is inexpensive, adding a thermowell can still be practical. Frequent replacement of sensors incurs labor costs, as sensors will eventually need to be replaced. Replacing sensors is more straightforward when they are housed in a thermowell. Furthermore, a thermowell seals the process, preventing outside contamination during sensor replacement, and eliminating the need for additional protective equipment or measures for workers.
No Shut-Downs: One significant benefit of thermowells is their ability to keep the temperature-monitoring process independent from the temperature sensor itself. Since temperature sensors eventually need to be removed and replaced, the thermowell ensures that the process remains contained during this maintenance. As a result, other than a temporary lapse in temperature measurement, the operation is unaffected by the sensor swap. Without a thermowell, there is a risk of partial or complete disruption of the process during sensor replacement. When deciding whether to use a thermowell, it's important to consider the cost or impact of such disruptions. Additionally, thermowells can be coated with FEP (fluorinated ethylene propylene) for added protection.
Benefits of FEP (Fluorinated Ethylene Propylene) Coated Thermowells: A thermowell can be constructed from various materials. However, to ensure optimal protection, the following factors should be considered during the decision-making process:
FEP (fluorinated ethylene propylene) offers several beneficial properties, making it an ideal material for encasing a thermowell. The advantages of FEP include:
FDA-approved FEP-coated thermowells are versatile and available in lengths of any size with diameters ranging from 1mm to 50mm. For applications that require faster temperature response or involve complex shapes, spray coatings such as PVDF (polyvinylidene fluoride) and PTFE (polytetrafluoroethylene) are effective. These coatings are particularly suitable for instruments exposed to environmental conditions, as they have a low thermal expansion coefficient (0.000122 mm per degree Celsius) and absorb minimal moisture (less than 0.01%). Additionally, coated thermowells are resistant to ultraviolet radiation, providing added protection to the sensor element inside.
Thermowells are designed to meet recognized standards based on established process conditions, but processes are often subject to unexpected changes. For instance, when working with gases or oils, initial assumptions about the source material might evolve due to various external factors. For example, if sand inadvertently enters a piping system, it can start to degrade the thermowell from within the pipe. Additionally, the sensor housed within the thermowell may not always detect or measure the specific materials flowing through, potentially leading to severe failures. Despite careful planning and engineering, thermowells might not always adapt to all process changes. Another limitation is that some thermowells are only compatible with specific types of sensors.
All temperature-monitoring equipment is prone to degradation from flow, heat, and pressure exposure. A severe processing environment will impact a sensor's structural integrity and performance over time. For instance, the metals used to construct thermocouple probes are susceptible to the corrosive conditions where they are typically employed. Under such harmful conditions sensors often begin to deteriorate quickly and, also, may report false readings while they begin to fail. Thermowells protect a sensor’s lifespan and, by doing so, lower overall production costs for the industries they are employed by eliminating the need for regular sensor replacements and the associated material (sensor replacement), labor, and operational costs.
An RTD, resistance temperature detector, is a passive temperature sensing device that operates on the principle that the resistance of a metal changes as the temperature changes. The electrical current that passes through the element...
Temperature sensors are devices that detect and measure coolness and hotness and convert it into an electrical signal. Temperature sensors are utilized in our daily lives, be it in the form of domestic water heaters...
A thermistor, a shortened version of the term thermal resistor, is a passive component whose resistance changes as the temperature in a system changes. Thus they serve as an inexpensive, accurate, and dynamic method for measuring temperature...
A thermocouple is a transducer that converts thermal energy into electrical energy and is constructed by joining wires made from dissimilar metals to form a junction. Voltage is produced when the temperature at the junction changes...
A band heater is a heating device that clamps onto objects to provide external heat using radiant and conductive heating. The different mounting methods of band heaters makes it possible to secure them tightly and...
A cartridge heater is a cylindrical tubular heating device that provides concise and precise heating for various forms of materials, machinery, and equipment. Unlike an immersion heater, a cartridge heater is inserted into a hole in the item to be heated to furnish internal radiant heat...
Ceramic heaters are electric heaters that utilize a positive temperature coefficient (PTC) ceramic heating element and generate heat through the principle of resistive heating. Ceramic materials possess sufficient electrical resistance and...
Electric heating is produced by using a known resistance in an electric circuit. This placed resistance has very few free electrons in it so it does not conduct electric current easily through it. When there is resistance in...
A flexible heater is a heater made of material that can bend, stretch, and conform to a surface that requires heating. The various forms of flexible heaters include polyimide film, silicone rubber, tape...
A heating element is a material or device that directly converts electrical energy into heat or thermal energy through a principle known as Joule heating. Joule heating is the phenomenon where a conductor generates heat due to the flow of electric current...
An immersion heater is a fast, economical, and efficient method for heating liquids in tanks, vats, or equipment. Known as bayonet heaters, they have heating elements that can be directly inserted into a container of water, oil, or other material in order to heat the entire contents...
Infrared heating is a heating method used to warm surrounding bodies by infrared radiation. Thermal energy is transferred directly to a body with a lower temperature through electromagnetic waves in the infrared region...
Radiant heaters are systems that generate heat internally and then radiate it to the nearby objects and people. The sun is a basic example of a radiant heater. When we feel warm on our bodies on a sunny day...
The idea of an electric heater seems to be out of place in modern society since most buildings have a sophisticated central heating system. That may be true, but electric heaters can be a helpful way of saving energy while providing efficient heating...