Ultrasonic Cleaning
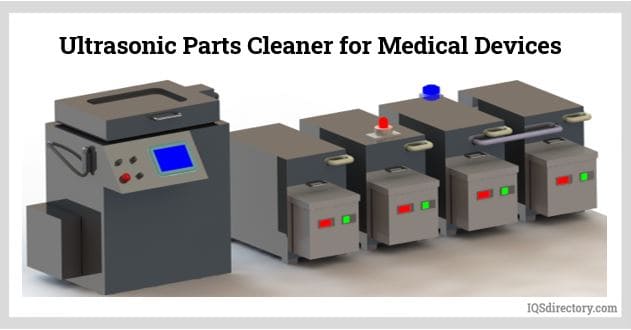
Ultrasonic cleaning is a type of cleaning process which uses cavitation induced by alternating compression and rarefaction cycles at ultrasonic frequencies. Ultrasonic frequencies are sound waves vibrating at 20 kHz or higher...
Please fill out the following form to submit a Request for Quote to any of the following companies listed on
This article takes an in depth look at ultrasonic cleaners.
Read further to learn more about topics such as:
Ultrasonic cleaners use mechanical vibrations to create sound waves in a liquid medium, initiating the rapid formation and collapse of microscopic bubbles. This phenomenon, called cavitation, results in a robust scrubbing motion that efficiently removes dirt and pollutants. By combining cavitation with sonic agitation and specialized cleaning agents, ultrasonic cleaners provide an extremely thorough cleaning method suitable for precision instruments, delicate objects, and sensitive devices. The ultrasonic waves induce compression and decompression cycles in the cleaning fluid, guaranteeing wide-ranging coverage and effective cleaning.
The effectiveness of ultrasonic cleaning is heavily influenced by the design of the system, as well as the frequency and power density at which it functions. These factors are vital when choosing an ultrasonic cleaner, as they greatly impact its overall performance and cleaning outcomes.
Cavitation is a physical phenomenon that occurs when alternating high-pressure zones rapidly change within a brief period. In an ultrasonic cleaner, these pressure shifts are triggered by the introduction of high-frequency sound waves into the cleaning medium. This leads to the creation of minute bubbles or cavities that quickly implode, generating small yet powerful shockwaves. Although these shockwaves are invisible, they are highly effective in clearing debris from the surfaces of items being cleaned, down to a microscopic level.
In many industrial applications, cavitation is recognized as a destructive process that can quickly deteriorate metal components like pump impellers and casings. Therefore, when implementing cavitation in cleaning, regulating the cleaning parameters is essential. Intense cavitation may potentially damage the objects being cleaned.
An ultrasonic cleaner is composed of three primary elements: the generator, transducer, and tank. The ultrasonic generator is pivotal as it transforms utility power into an electrical signal, which oscillates at the frequency necessary for the cleaning task. While standard utility power operates at 50 or 60 Hz, the generator elevates this to much higher ranges, typically between 20 kHz and 80 kHz. With technological advancements, even higher frequencies known as megasonic frequencies (100 kHz and beyond) are being used.
The subsequent component is the ultrasonic transducer, which converts the electrical signal into mechanical vibrations. This transformation occurs via either the inverse piezoelectric effect or the magnetostrictive effect. Upon application of an electric signal, piezoelectric or magnetostrictive materials undergo dimensional changes ranging from 1 to 0.1 microns.
A magnetostrictive transducer functions on the principle that ferrous metals expand and contract when exposed to a magnetic field. These changes cause the ultrasonic cleaner's container to vibrate, generating mechanical ultrasonic waves that follow an elliptical pattern.
Piezoelectric transducers contain crystals with unique electrical characteristics. When an electric current is applied to these crystals, they change their shape, leading to linear vibrations. Predominantly, piezoelectric transducers are utilized across Europe and Asia.
The selection of transducer significantly impacts the ultrasonic cleaning process. Initially, metal transducers were used to produce mechanical vibrations; however, they often created excessively strong vibrations that could harm instruments. Nowadays, ultrasonic cleaners generally employ ceramic transducers, offering more controlled and efficient cleaning action, reducing the risk of damage to delicate items.
The final fundamental component is the ultrasonic cleaner tank. The tank hosts the cleaning solution and the items to be cleaned. It is also the mounting base for the transducers. Most tanks are crafted from corrosion-resistant materials like stainless steel, but some are made from plastics and ceramics. Tanks vary in size based on the solvent capacity they hold and are designed for durability and longevity.
Additional features of ultrasonic cleaners include a heater and a strainer basket. The heater regulates the temperature of the cleaning solution, vital since the cavitation's effectiveness relies on the solution's vapor pressure and thus its temperature. Closely monitoring the temperature is crucial for optimizing cleaning efficiency and ensuring proper care of the items.
The strainer basket keeps items in place while submerged in the cleaning solution. Most systems are designed to avoid contact between items and the tank's bottom or sides, as this can adversely affect the vibration quality transmitted to the cleaning solution.
Ultrasonic cleaners have increasingly gained recognition as a versatile cleaning solution across numerous industries. Commonly used in fields such as healthcare, dental care, electronics, plastics, metalworking, and machinery manufacturing, these devices offer a range of benefits. Here are some of the advantages of utilizing ultrasonic cleaning equipment.
Highly Suitable for Delicate Parts: Unlike traditional cleaning methods such as brushing, polishing, scrubbing, water jet or spray cleaning, compressed air cleaning, and chemical cleaning, ultrasonic cleaning does not damage the part being cleaned. Aside from dirt and debris, mechanical and chemical tools can remove some surface material from the part being cleaned. This can cause unpleasant surface defects, scratches, corrosion, and discoloration. This makes ultrasonic cleaners highly suitable for cleaning delicate and sensitive items such as jewelry, dental and surgical equipment, microelectronics, and intricate machine parts.
Faster and More Thorough Cleaning: Ultrasonic cleaners are both quick and effective. The usual time of cleaning is only 10 to 15 minutes, even for the most delicate of parts. Cleaning only takes one cycle. More cycles are usually not needed to increase cleaning effectiveness. Its speed is also attributed to multi-tank setups where multiple parts can be cleaned at the same time. The parts are submerged in several tanks which comprise only one ultrasonic cleaner unit.
Relatively High Power Efficiency: Compared to other mechanical cleaning methods, an ultrasonic cleaning process takes less power. Other methods use motors, pumps, and compressors, which consume a lot of power while converting only a small amount into actual cleaning action. Ultrasonic cleaning, on the other hand, can easily convert electrical energy into vibrations. The ultrasonic generator has an efficiency of 95%, while the transducer has 65% to 70%. The overall efficiency of ultrasonic cleaners, particularly the piezoelectric types, can reach around 70% or higher.
Various types of ultrasonic cleaners are available, each tailored to clean specific parts or materials. They are designed with unique features to address particular cleaning needs, ensuring optimal performance for different applications.
Medical and Dental Ultrasonic Cleaners: Ultrasonic cleaners can remove blood, tissue, and protein-based contaminants, which is achieved while maintaining the delicate surface of the instrument. They are used to prepare instruments for the sterilization process since they can attack most contaminants. Common medical and dental items prepared for sterilization are surgical instruments, implants, surgical screws and fasteners, needles, blades, cutters, labware, and more.
Jewelry Ultrasonic Cleaners: Ultrasonic cleaning is a popular method involved in jewelry crafting. The process takes advantage of the gentle and precise cleaning of ultrasonic cleaners. Ultrasonic cleaners can create cavitation in hard-to-reach areas. It also does not scratch or damage the intricate surface of the jewelry which is particularly important in the crafting process. On top of that, ultrasonic cleaning can be coupled with ultrasonic polishing to create a luster far better than that of other cleaning methods.
Ultrasonic Gun Cleaners: Guns have many hollow areas, cavities, and crevices in their assembly that brushes and polishers cannot reach. Even in the gun’s disassembled state, there are still areas inaccessible to hand washing or brushing. Moreover, traditional cleaning for guns uses solvents that are usually harmful to the environment. This is not the case with ultrasonic gun cleaners. Ultrasonic gun cleaners, also known as ultrasonic firearm cleaners, can reach all areas as long as they are properly wetted with the cleaning solution. Ultrasonic gun cleaners can also be used with ultrasonic gun lubrication. Both processes are similar: they use cavitation. The complete ultrasonic cleaning and lubricating process eliminates the need to have the gun dismantled every time it needs maintenance.
Electronics Ultrasonic Cleaner: Because of its simple operation, high throughput, and precise cleaning, ultrasonic cleaners are employed in circuit boards and electronics cleaning. Electronics ultrasonic cleaners can remove different types of debris usually found in semiconductors and electronics manufacturing processes. Small metal chips and burrs can be removed while keeping the small features of the electronic components unharmed. This ensures a defect-free product that performs reliably.
Industrial Ultrasonic Cleaners: Industrial ultrasonic cleaners clean different machine elements and automobile and aircraft components. These are large cleaning machines designed to contain parts such as compressors, radiators, pumps, valves, and gear assemblies. They are highly effective in removing oil and grease. Also, despite the large size of the component being cleaned, the cycle time is only a few minutes more than that of the smaller types. However, cleaning is done uniformly throughout the wetted surfaces of the component.
Medical Parts Cleaning During Manufacturing:Sanitation and sterilization are vital to eliminating potentially harmful microorganisms from medical devices. Additionally, the component parts of medical instruments need to be cleaned prior to assembly and sterilization.
The purpose of cleaning medical devices prior to sterilization is to remove contaminants such as particulates and fluids that may have accumulated during machining and assembly. For example, devices made of stainless steel and titanium, such as joint implants, may have metal shavings stuck in holes or connecting points. The fluids used to cut and shape implants must be removed prior to the next steps of production. Medical instruments products are cleaned multiple times during assembly and before the product is sterilized.
Ultrasonic precision-cleaning is the industry standard for cleaning medical devices during manufacture. It is particularly effective in cleaning intricately designed parts and hard-to-reach crevices or blind holes and in further improving subsequent surface treatment processes. It has proven to be the ideal solution for the precision cleaning of everything from surgical instruments, implants, surgical screws and fasteners, needles, blades, and cannulas to catheters, stents, hospital and labware, and test instruments.
Ultrasonic Mold Cleaners:Ultrasonic cleaners are used for cleaning molds for plastics and other materials due to the noncontact aspect of their system that does not change, damage, modify, or alter the design of mold cavity details. A critical part of mold geometry is strict adherence to mold tolerances, which is necessary to guarantee the quality of formed products. Unlike other cleaning methods that use harsh toxic chemicals, ultrasonic cleaning does not touch the surface of a mold but is still capable of precision cleaning of a mold's most intricate and detailed sections.
The turbulence of ultrasonic cavitation increases cleaning action, exposing surfaces to fresh chemical cleaning. When combined with heat and cleaning solvents, the process creates cleaning action that penetrates blind holes, tiny crevices, and the complex design features of molds. Residual burnt polymers and mold releases from mold components are removed, extending the useful life of a mold without harming or damaging its surface. Buildup from cooling ports and channels are removed, which assists in improving polymer flow.
Side mounted immersible transducers are a recent innovation in ultrasonic cleaning and provide more intense and focused cavitation, compared to transducers mounted on the bottom of the tank. Plastic injection molds are rectangular with design details on their surface that face the side of the tank. Side mounted transducers provide a more effective and concentrated cleaning process for the position of a mold’s most complex details.
The turbulence of ultrasonic cavitation increases cleaning action, exposing surfaces to fresh chemical cleaning. When combined with heat and cleaning solvents, the process creates cleaning action that penetrates blind holes, tiny crevices, and the complex design features of molds. Residual burnt polymers and mold releases from mold components are removed, extending the useful life of a mold without harming or damaging its surface. Buildup from cooling ports and channels are removed, which assists in improving polymer flow.
Side mounted immersible transducers are a recent innovation in ultrasonic cleaning and provide more intense and focused cavitation, compared to transducers mounted on the bottom of the tank. Plastic injection molds are rectangular with design details on their surface that face the side of the tank. Side mounted transducers provide a more effective and concentrated cleaning process for the position of a mold’s most complex details.
Immersible Ultrasonic Cleaners: Immersible ultrasonic cleaners, sometimes referred to as submersible cleaners, are machines composed of only two parts: the ultrasonic generator and transducer. The transducer is connected to the generator by a cable and is immersed into the cleaning bath. Any container can act as a tank as long as it can hold a sufficient amount of solution. These types are designed to be portable. However, this advantage is offset by the machine’s poor cleaning quality.
The effectiveness of cleaning relies not just on the ultrasonic machine's power and accuracy but also on the type of cleaning solution employed. Simply using water is insufficient for optimal results. It is crucial that cleaning solutions:
Ultrasonic cleaning solutions are typically composed of alkaline detergents, surfactants, acids, and enzymes, which are diluted in deionized water. The composition of the cleaning solution depends on the type of debris or contaminant to be removed.
Alkaline Detergents: Alkaline detergents are used for removing organic and petroleum-based contaminants such as oil, grease, and waxes. They generally have a pH number of 10 and above. Alkaline detergents are almost synonymous with caustic solutions and surfactants. Their main action is to reduce the surface tension of water. This allows oils to dissolve easily into the solution. Moreover, lowering surface tension enhances the wettability of the part, which then helps in its immersion to the solution.
Enzymes: Enzymes are particularly used in medical and dental ultrasonic cleaners. These are catalysts made from active strings of proteins that break down biological matter. They are safe to use since they are biodegradable and pH neutral. They are used to remove blood, bone, tissue, fats, and other soils that cannot be easily removed using typical detergents. Enzymatic cleaning agents are available in concentrated solutions or dissolvable powder and tablets.
Corrosion Inhibitors: Corrosion inhibitors are chemical additives that significantly reduce the oxidative attack on the material. These are commonly used in cleaning metallic objects such as jewelry, electronics, automotive, and aerospace parts. Since some ultrasonic cleaning solutions contain acids, a rinsing bath with corrosion inhibitors can be applied to protect the material. These added chemicals protect and maintain the cleaner tank from corrosion as well.
Ultrasonic cleaning is a straightforward procedure that primarily consists of setting up the cleaning bath and machine. The cleaning itself requires minimal operator involvement. After the cleaning, additional steps can be carried out if needed. Here is an overview of the typical ultrasonic cleaning process.
Setting the Bath Temperature: Most ultrasonic cleaners, especially in industrial setups, have a mounted heater for controlling the temperature. The temperature directly affects the machine’s efficiency in generating cavitation. On top of that, other fluid properties such as surface tension, viscosity, and density are affected by temperature. Higher temperature also results in more chemical activity in the solution.
Solution Degassing: Dissolved gases in the cleaning solution decreases the intensity of cavitation. Gases are dissolved in the solution through minuscule bubbles. Upon applying the positive and negative pressure phases, the cavitation voids migrate into the gas bubbles. The extra volume prevents the voids from collapsing, which severely muffles the shockwaves produced by the cavitation.
To degas the solution, the ultrasonic cleaner is first operated without load for a few minutes. Most of the dissolved gases will eventually rise to the surface of the fluid. The rising of gases can be observed by the naked eye since the gases collect at the surface creating larger bubbles.
Secondary Processes: Secondary processes are optional steps that may include polishing and lubricating. These processes use different solvents, which add desirable surface properties to the material. The additional polishing step is usually done in cleaning pieces of jewelry, while the lubricating step is performed in servicing firearms.
To ensure ultrasonic cleaners remain effective and reliable, it is essential to follow proper maintenance procedures. Effective upkeep not only boosts the system’s performance but also ensures consistent cleaning results. Below are some recommendations for successful maintenance.
Ultrasonic cleaning is a type of cleaning process which uses cavitation induced by alternating compression and rarefaction cycles at ultrasonic frequencies. Ultrasonic frequencies are sound waves vibrating at 20 kHz or higher...
Industries worldwide utilize abrasive blasting for various purposes, including cleaning rust and oil, removing surface coatings like paint and pollutants, preparing surfaces for paint and coatings, reinforcing metal surfaces and...
An aqueous part washer is an automated or semi-automated machine manufactured to clean, remove tough grease, and dry large or small parts before distribution or surface treatment. The washing is necessary since...
Automated parts washers are mechanical devices designed to efficiently remove grit, oil, grime, dirt, paint and other contaminating substances from parts with minimum manual supervision. These substances are removed...
Deburring is a secondary operation of a machining process that enhances the final quality of the product by removing raised edges and unwanted pieces of material, known as burrs, left by the initial...
Finishing machines are machines used for metal finishing, which is the last stage of the metal fabrication process; the stage encompasses the use of machines in finishing the metal surface...
A parts cleaner is a cleaning device that uses various types of solvents, cleaning agents, and processes to remove grease, grime, and contaminating materials from manufactured parts prior to shipment or movement for further processing...
A parts washer is a mechanical device designed to remove grit, grime, oil, miscellaneous debris, dirt, paint, and other contaminating substances from parts in preparation for their use in assembly operations, packaging, or coating...
Sandblast cabinets include systems or machinery and components for projecting blast media against a part‘s surface to abrade, clean, or modify the surface. Sand, abrasive, metal shot, and other blast media are driven or propelled using pressurized water, compressed air, or a blast wheel...
Sandblasting equipment includes systems or machinery, and components for projecting blast media against a part‘s surface to abrade, clean, or modify the surface. Sand, abrasive, metal shot, and other blast media are driven or propelled using pressurized water, compressed air, or a blast wheel...
Shot peening equipment includes systems or machinery and components for projecting shot peening media against a part‘s surface to modify the surface or surface engineer the part...
A tumbling machine is a durable deburring and metal-polishing machine designed for finishing large parts or batches of smaller parts. A tumbling machine is also known as a barreling machine or a mass-finishing...
Vibratory tumbler is the equipment used in a vibratory finishing process, one of the most common methods in mass finishing. But how does a vibratory tumbler work...
A wastewater evaporator is a method of removing water from water-based waste by converting the water in the waste to a vapor and leaving contaminants. The function of a wastewater evaporator is to reduce the volume of waste materials...
Parts washers are designed for cleaning, degreasing of equipment, and drying of mass quantities of small or large parts in preparation for surface treatment, assembly, inspection, or shipment...