Central Vacuum Systems
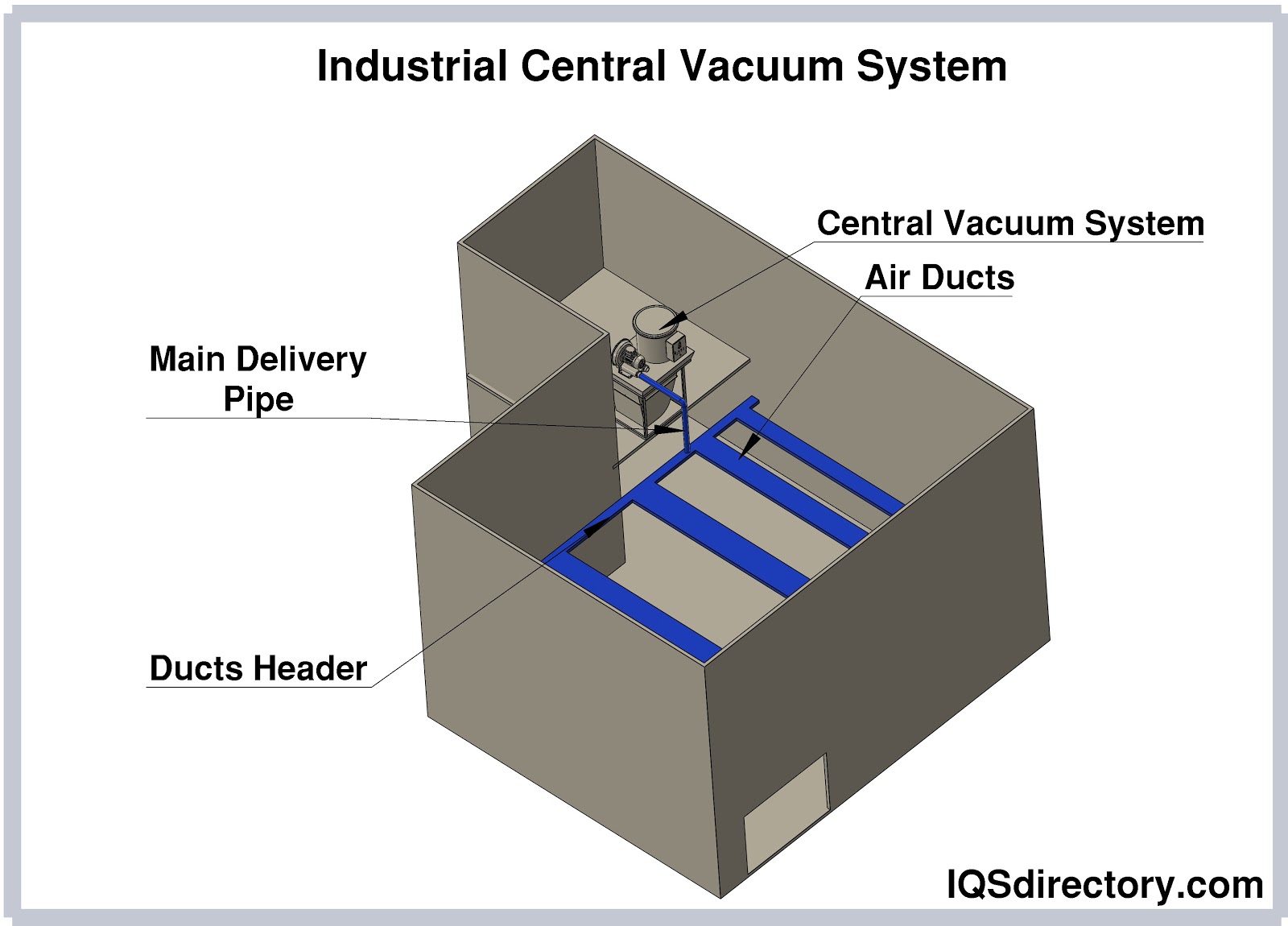
A central vacuum system is a cleaning mechanism that is built into a building for ease of use, access, and maintenance. Vacuum and pressure are created by a centrally located motor to remove dirt, dust, and debris...
Please fill out the following form to submit a Request for Quote to any of the following companies listed on Explosion Proof Vacuums .
This article will take an in-depth look at explosion-proof vacuums and dust collectors.
You will understand more about topics such as:
Explosion-proof vacuums are designed to operate safely in environments where there is a risk of igniting flammable gases or vapors. These systems use compressed air, electricity, and cyclonic motion to ensure that they do not generate conditions that could ignite a potentially hazardous atmosphere. By replacing traditional motors with compressed air systems, explosion-proof vacuums eliminate the risk of sparks from motors, friction, or heat from moving parts. In contrast, conventional electric vacuum cleaners can create sparks from plugs, switches, or arcing motors, which could trigger an explosion.
To ensure safety, explosion-proof vacuums are constructed with components that are securely grounded to discharge any static electricity and prevent sparks or other explosion risks. These vacuums avoid the use of direct electrical connections that could potentially create hazardous conditions.
Explosion-resistant vacuums feature metal drums to collect dust and contain it securely to prevent any potential explosions. When these drums are full, they are sealed and properly disposed of. The metal drums act as containment units for hazardous materials, ensuring safe handling and disposal.
Industrial explosion-proof vacuums utilize electricity, the Venturi effect (refer to chapter 3 for details), and cyclonic action to perform their cleaning tasks. The method of dust, dirt, and debris collection varies based on the material's type and its classification and division. Each explosion-proof vacuum is designed to handle specific materials according to its rating. Thus, it is crucial to understand these classifications and divisions when selecting an explosion-proof vacuum to ensure it is suitable for the intended conditions and types of waste. Incorrectly choosing a vacuum for volatile materials can pose significant hazards and dangers.
Explosion-proof dust collectors are specialized air purification devices designed to remove combustible gases and improve air quality in commercial and industrial environments. They effectively trap gas vapors and particulates, filtering out both solid pollutants and hazardous substances regulated by environmental standards. The process begins when raw gas enters the dust collector, where it passes through filters that separate dust and other contaminants, resulting in clean air being released. These systems are essential in manufacturing and industrial operations, where dangerous particles can be released, posing health risks to workers. By employing a network of filters and separators, dust collection systems clean the polluted air, enhancing workplace safety and air quality.
Dust collecting systems are combustible gas removers and air cleaning systems used to remove particulate matter, gas vapors, and prevent ambient air pollution and explosions. They collect dust using ducting, air purifiers, pleated filters, and containers. The various systems have different configurations, designs, and components depending on the manufacturer and the types of dust being collected.
Ductwork for explosion-proof dust collectors is meticulously designed to ensure safe and effective operation of the system. The design considerations include the size of the ducts, the volume of air required, the length of the piping, the number of machines served, and the types of particles being extracted. Fans draw air into the dust collector, and each type of collector is tailored to meet the specific needs of the air cleaning process and the type of combustible material involved. Proper ductwork design is crucial for optimizing system performance and maintaining safety standards.
Blowers, or fans, are responsible for directing contaminated air from the workspace into the ductwork and filtration systems. Despite their seemingly simple design, several factors need to be considered when installing these components in a dust collection system.
The first consideration is the quantity of air that needs to be moved. It is expressed as a cubic foot per minute (CFM). Static pressure across the entire system is the next factor with the composition of the air, its temperature, combustibility, and moisture content being other factors. Blowers can be centrifugal or axial, where an axial blower is like a standard fan, and a centrifugal blower pulls in air at an angle.
The effectiveness of a dust collection system hinges on its dust filters. A blower draws air from the work area through the filter, which captures airborne particles. The efficiency of the filtration system is often evaluated by the air-to-cloth ratio, which measures the amount of air passing through each square foot of filter material; a lower ratio indicates higher efficiency. Once gases are filtered out, particulate matter is collected in a container or receptacle. The choice of filter material and its loading rate influence the design of the receptacle, with all explosion-proof dust collectors utilizing HEPA or ULPA filters to ensure thorough filtration.
For a vacuum to be classified as explosion-proof, its various components must comply with specific government standards. This includes ensuring that the housing, filters, hoses, and other parts are constructed from robust and durable materials capable of withstanding harsh and hazardous conditions.
Heavy Duty Housing: The housing can contain any explosion and has a stainless steel outer shell that does not crack or dent. Anti-sparking substances reduce the possibility of electrical discharge. In addition to stainless steel, explosion-proof housings may be made of reinforced fiberglass.
One of the essential elements of any air cleaning system is HEPA filters, which can remove 99.9% of particulate matter. They are used in all cleanrooms and hygienic environments. Specially designed HEPA and ultra low particulate air (ULPA) filters are used with explosion-proof vacuums. They are a critical component that enhances the safe use of explosion-proof vacuums. With the capability of capturing 0.2 microns (µ) sized particles, HEPA filters clean and capture hazardous dust to ensure safe, clean air is exhausted from an explosion-proof vacuum.
Explosion-proof vacuum cleaners are categorized based on classes, divisions, and power ratings, with specialized models designed for specific work environments. Understanding these classifications is essential for selecting the appropriate vacuum for particular conditions.
The National Electrical Code provides a classification system that details the specific capabilities needed for explosion-proof vacuums. Additionally, the Occupational Safety and Health Administration (OSHA) sets standards that outline the essential safety features for operating these vacuums.
According to OSHA standards, operators must exercise additional precautions when using explosion-proof vacuums in areas with flammable gases, vapors, or liquids. Risks such as metal-to-metal contact, hot surfaces, static electricity, sparks, and flames can potentially ignite these substances, leading to explosions.
Area classification involves categorizing rooms, sections, and specific areas based on their potential hazards and the presence of dangerous substances. This method provides critical information about potential risks and the necessary safety equipment and practices required for each area.
The North American classification system is detailed in the National Fire Protection Association (NFPA) Publication 70, as well as in the National Electrical Code (NEC) and the Canadian Electrical Code (CEC). These guidelines specify the types and quantities of hazardous materials that could act as ignition sources for fires or explosions.
Class is the first of the three categories used to define an area’s hazard level. The three classes—Class I, Class II, and Class III—are outlined in NFPA Publication 70, NEC, and CEC. Each class specifies different types of hazardous materials present in the environment.
The explosive characteristics of a substance can vary depending on its use. These characteristics include ignition temperature, safety clearance, and maximum explosive pressure. Flammable and combustible gases are further classified into additional categories based on their specific properties.
The temperature class indicates the lowest ignition temperature of hazardous materials, representing the minimum temperature at which a material can ignite. This classification describes the thermal energy levels that an explosion-proof vacuum can generate. Temperature classes are denoted as T classes, ranging from T1 to T6.
Each class is further divided into two divisions to assess the likelihood of the presence of hazardous materials with explosive potential:
Division I: Indicates a high likelihood of ignitable substances being present.
Division II: Indicates a lower likelihood of ignitable materials being present.
The group classification addresses atmospheric hazards, focusing on flammable and combustible substances. There are seven groups, from Group A to Group G, each specifying different types of atmospheric contaminants.
Single-phase electric explosion-proof vacuums are designed for cleaning dry, explosive dusts such as aluminum, magnesium, titanium, and gunpowder. They are suitable for use in environments classified as Class I, Division 1, Group D, as well as Class II, Division 1, Groups E, F, and G. These vacuums are built to withstand harsh and hazardous conditions, featuring multiple HEPA filters and an explosion-proof pressure switch with filter status indicators. Most single-phase explosion-proof vacuums are equipped with automatic shut-off mechanisms that activate when the filters become full or clogged.
Three-phase electric explosion-proof vacuums are designed to handle combustible dust and come equipped with one or more HEPA filters rated for use with combustible materials. They feature stainless steel chambers and containers, meeting electrical standards for Class II, Division 2 environments, and are capable of managing Group E metal dust. Like single-phase models, three-phase vacuums include a filter cleaning indicator, and some models offer a manual dust filter shaker to assist with filter maintenance and dedusting.
A Venturi explosion-proof vacuum utilizes a Venturi tube to generate suction. The design of the Venturi tube accelerates and decelerates the air flow. As air moves through the constricted section of the tube, it creates a low-pressure area that generates a vacuum. This method produces a stronger suction compared to traditional electric vacuums.
In a Venturi explosion-proof vacuum, compressed air is directed through a nozzle into a chamber. The air speeds up through the nozzle and then rapidly slows down upon entering the mixing chamber. This reduction in air velocity creates a negative pressure that generates suction in the vacuum line. The mixture of vacuumed air and debris is then filtered. The use of compressed air results in negative pressure within the metal drum, which facilitates suction through an attached hose.
Cyclone explosion-proof vacuums use a cyclone separation method to remove dust from the airflow, directing dust particles into a collection drum. This technique prevents dust from clogging the filtration system and effectively clears the environment of particulate matter. The vacuum generates a vortex that directs waste material downward, with the cyclone's design and dimensions ensuring that particles are kept out of the main airflow.
This cyclone separation process extends the vacuum's operating time and reduces the frequency of filter maintenance, enhancing overall efficiency.
Pneumatic explosion-proof vacuums operate without electricity, motors, or any moving parts, making them ideal for handling explosive materials like flour, carbon dust, titanium powder, and aluminum powder. These vacuums are equipped with static-dissipating components to mitigate concerns related to static electricity.
Powered by portable air compressors, pneumatic explosion-proof vacuums utilize a Venturi system to generate suction and draw in debris. They are known for being quiet and lightweight, enhancing ease of use. Additionally, they offer versatility by efficiently handling both wet and dry waste, and are available with drum capacities ranging from 18 to 55 gallons.
Single, dual, and quad Venturi explosion-proof vacuums and pneumatic vacuums are powered by compressed air. They are the most used type of explosion-proof vacuum because they do not use any electrical motor that could create static electricity. An air powered explosion-proof vacuum is attached to an airline to generate vacuum power. All air-powered explosion-proof vacuums depend on Venturi tubes to create their vacuum using portable air compressors.
Explosion-proof dust collectors are designed to capture and filter dust while ensuring safety from explosive or combustible dust particles. These dust collectors can range from large, stationary units with advanced filtration systems to smaller, portable models with castors. They are equipped with features to manage, suppress, and control combustible dust effectively.
While explosion-proof dust collectors are engineered to prevent explosions, their selection depends on the specific type of dust they need to handle. All organic dust is considered explosive, making the use of explosion-proof dust collectors essential.
The process begins with "Go or no-go" testing when dealing with potentially explosive or flammable dust. This initial assessment is followed by evaluating the collected dust at the site using various methods, with further examination conducted by OSHA. These procedures help determine the most appropriate dust collection approach.
The initial phase of combustible dust analysis is a Dust Hazard Analysis (DHA), which assesses combustion risks, environmental factors, and potential damage. This analysis can be performed at the facility and is not governed by specific regulations.
A more comprehensive analysis is conducted by OSHA, known as Process Hazards Analysis (PHA). This detailed assessment evaluates the potential hazards of combustible dust more broadly. Additionally, NFPA standards 61, 484, 654, 655, and 664 provide guidelines on dust characteristics and methods to control and prevent dust explosions.
Pulse jet dust collectors are a type of baghouse dust collector that utilizes pulsed jet air to clean dust-covered cloth bag filters. These systems use differential pressure sensors to monitor the pressure difference between clean and contaminated air. The filter cleaning process is triggered when the pressure differential exceeds a set threshold.
Pulse jet dust collectors are highly favored for their low maintenance requirements, effective handling of high-density dust, and excellent filter performance. Despite their advantages, they are quite large, need to be installed externally, and occupy more space compared to other dust collection systems. They are particularly well-suited for applications such as product recovery, dust collection, separating and filtering explosive materials, metalworking chips, hazardous media, central vacuum cleaning, and pneumatic conveying.
Industrial dust collectors are essential for maintaining clean and safe environments in workplaces, plants, manufacturing facilities, and commercial spaces. They effectively remove pollutants such as volatile organic compounds, hydrocarbon fumes, and solvent vapors, which can be harmful to both the environment and biological systems. Explosion-proof dust collectors utilize advanced filtration systems to capture and neutralize these harmful gases and dust particles.
Regulatory agencies and insurance companies often mandate the use of dust collectors to ensure a healthy work environment, addressing potential health risks and air quality concerns. Additionally, some regulations require specific levels of soundproofing to mitigate noise from machinery and further protect workers.
An electrostatic precipitator captures pollutants through electrostatic forces generated by a network of charged wires. As air flows through these wires, it becomes electrically charged and ionized. The charged particles are then attracted to and adhere to collection plates within an electrostatic field. The cleaned air, free of contaminants, continues to exit the system while the pollutants remain on the plates.
Various methods are used to remove collected debris from the collection plates in an electrostatic precipitator, including shaking, scraping, or manual cleaning. Additionally, the electrostatic precipitator can be adapted to handle larger particles, such as ash, or particles that require more energy to effectively remove.
Cyclone dust collectors utilize centrifugal force to remove particles from the air through cyclonic motion within a hopper chamber. The spinning action drives larger particles toward the chamber's outer wall, where they then fall into a collection chamber for removal.
Cyclone dust collectors range in size from large, outdoor units designed for cement production to smaller models suited for laboratory environments. They are available in various configurations to optimize performance for different applications. In addition to enhancing operational efficiency, cyclone dust collectors help ensure worker safety and extend the lifespan of equipment.
Downdraft tables are designed to either automatically remove dust from a work area or be manually activated by the user. Prior to the advent of these tables, workers traditionally managed dust and debris by sweeping it into a hole in the work surface.
Downdraft tables are primarily used to capture various types of airborne contaminants, including powders, fumes, and both fine and coarse particulates. They feature perforated grilles that ensure even airflow distribution. Air is drawn through the perforated surface and into an exhaust chamber located beneath the table. The exhaust chamber is equipped with filters capable of trapping dust particles as small as 0.5 microns (µ).
Shaker dust collection systems are ideal for handling large particulate matter, such as wood dust or plastic chips. In these systems, a filter bag suspended inside the dirty air plenum collects dust on its exterior. The connection duct for a shaker dust collector is positioned below the hopper. As air velocity decreases upon entering the dust collector, larger particles settle into the hopper, while smaller particles adhere to the outside of the filter bags.
The collected particles are dislodged from the filters by a shaking mechanism and fall into the collection bin or hopper.
Shaker dust collectors can feature a segmented system or an interrupted airflow system. These designs allow for continuous operation without needing to take the system offline. They are commonly used in environments such as foundries, steel mills, mines, and smelting plants, where compressed air is not available for filter cleaning.
Wet scrubbers are also known as wet dust collectors and use a scouring fluid to gather gasses and particulates, with water being the most popular solvent. Contaminated air enters the bottom of the scrubber and passes through the packed bed with a downward-flowing water solvent that collects the pollutants.
For effective operation of wet scrubbers, the choice of liquid is crucial and depends on its chemical composition and compatibility with the contaminants being treated. Liquids used in wet scrubbers must be selected based on their ability to interact with pollutants, whether they are positively, negatively, or neutrally charged. The chemical properties of the liquid must ensure it can effectively absorb or bind the contaminants present.
Portable dust collectors are designed for small-scale dust collection in repair shops, commercial facilities, and for small projects. They effectively manage debris from processes such as welding, cutting, and grinding. Unlike traditional vacuums, portable dust collectors operate at lower pressures, enabling continuous operation.
These collectors are equipped with self-cleaning filters and an auger for dust discharge. Despite their smaller size, portable dust collectors, typically featuring a baghouse design, offer efficiency comparable to larger models. They are constructed from heavy-duty materials and are tightly sealed to ensure optimal performance.
Cartridge dust collectors are equipped with specialized cloth filters designed for specific applications. They offer the advantage of requiring less space while maintaining airflow comparable to larger baghouse systems. By incorporating fewer filters and maximizing fabric surface area in a compact design, cartridge dust collectors reduce safety risks and minimize the time and labor needed for filter changes. Additionally, these units allow for external filter replacements, further streamlining maintenance.
The compact size of cartridge dust collectors makes them well-suited for commercial and industrial environments where fine, light, or moderate dust is present, such as in pharmaceutical manufacturing, powder coating, metalworking, woodworking, fume collection, and thermal spray operations.
Laser Plasma Cutting: Laser cutting employs a focused laser beam for precise cuts, while plasma cutting, used for stainless steel, combines gases to cut through material. Both processes generate fumes, smoke, dust, and oxides, making it essential to use a laser fume extractor to ensure worker safety and machinery efficiency. Many laser cutting systems are equipped with built-in duct ports for dust collection. Key features of laser dust collectors include the air-to-cloth ratio and total draw.
Food Processing: The production of common ingredients like sugar, flour, and spices involves processes that generate explosive dust. As materials are mixed and packaged, fine particles are released into the air. Dust collectors are employed to capture and gather these dust particles, ensuring a safer environment.
Plastics Industry: Plastics are prevalent in many everyday items, from office supplies and vehicles to communication devices and entertainment products. The manufacturing of these items involves polymers and various additives, which can generate harmful dust and debris. To prevent contamination and protect workers' health, dust collectors are essential for capturing and removing these particles from the air.
Processes such as extrusion, blow molding, injection molding, and 3D printing shape and produce plastic products, all of which can release dust particles. Whether the dust is from sanding, deburring, or processing recycled plastics, it must be effectively collected to maintain a clean and safe working environment. Industrial dust collection systems are crucial for managing airborne particles and ensuring a healthy workspace.
A central vacuum system is a cleaning mechanism that is built into a building for ease of use, access, and maintenance. Vacuum and pressure are created by a centrally located motor to remove dirt, dust, and debris...
A HEPA vacuum cleaner is a vacuum cleaner that accepts high efficiency particulate air (HEPA) filters, is tightly sealed, and allows air to only pass through the HEPA filter. They are designed to capture particles of dust, dirt, and...
An industrial vacuum cleaner is a heavy duty piece of cleaning equipment designed to remove debris, industrial waste, construction refuse, and matter that remains after a manufacturing process or construction project...
Vacuum cleaners use suction to collect dirt, dust, waste products from industrial processes, and other debris for disposal, recycling, or reuse. They are mainly used for building maintenance and cleaning of industrial space...
Air filters are devices used to remove airborne particles, pollutants, and microorganisms hazardous to health and the ecosystem. In industrial facilities, air filters preserve the quality of products and materials and protect critical equipment from damage...
An automatic screwdriver is a piece of equipment that automatically inserts screws into a product during assembly and production. Since every production operation is unique and requires a...
An automation system is an integration of sensors, controls, and actuators designed to perform a function with minimal or no human intervention. The field concerned in this subject is called Mechatronics which is an...
A baghouse is a pollution control device that uses tubes, envelopes, or cartridges to remove, capture, and separate dirt, particulate matter, and dust from the air of a manufacturing or processing facility. The main components of a baghouse are the media or bags used to filter the particles from the air as it passes through the system...
A centrifugal blower is an air moving device that uses an impeller to pull air into a tube like structure and release it at a 90o angle. The impeller is a set of blades inside the blower that rotates at a high rate to pressurize and move air...
Collaborative robots, also abbreviated as Cobots, are the newest technology in robotics. They have changed the automation world significantly. These robots can work safely together with workers, hence are...
A dust collection system is a system that removes particulate contaminants from the air in production facilities, workshops, and industrial complexes. The system cleans air by forcing it through a series of airtight filters...
A HEPA filter is a high efficiency pleated air filter capable of capturing extremely small particulate matter down to particles that are the size of a micron (µ), or a micrometer, which is 1/1000th of a meter...
An industrial blower is a device that enhances the air flow in a workspace effectively and efficiently using an electric motor, impeller, and airfoils. The purpose and function of industrial blowers is to be a permanent addition to a workspace to increase airflow and...
An industrial fan is a highly efficient, heavy duty air flow device that is constructed from exceptionally durable materials and components to withstand stringent environments and operate longer to provide constant air flow and pressure. The strength of industrial fans is due to the materials used...
An industrial robot is an autonomous system of sensors, controllers, and actuators that executes specific functions and operations in a manufacturing or processing line. They operate continuously through repetitive...
A jet dust collector is a suction filtration unit that pulls dust ladened air into a filtration system that collects particulate matter and releases clean air. The filters of jet dust collectors are cleaned by compressed air that uses...
Robotic system integrators are companies that provide assistance in automating a wide range of applications. They help design robotic technologies that best suit the needs of an operation for a company and solutions as...
Warehouse automation is the process of replacing repetitive tasks with systems that are automated. The main goal is to remove labor-intensive duties that consume time. As a result, the workers can focus more on...
During the Industrial Revolution, when companies began producing high volumes of industrial waste like fine dust, wood dust, and other particles, an American, in 1852, S.T. Jones, applied for the first dust collector patents, a single bag filter...