Central Vacuum Systems
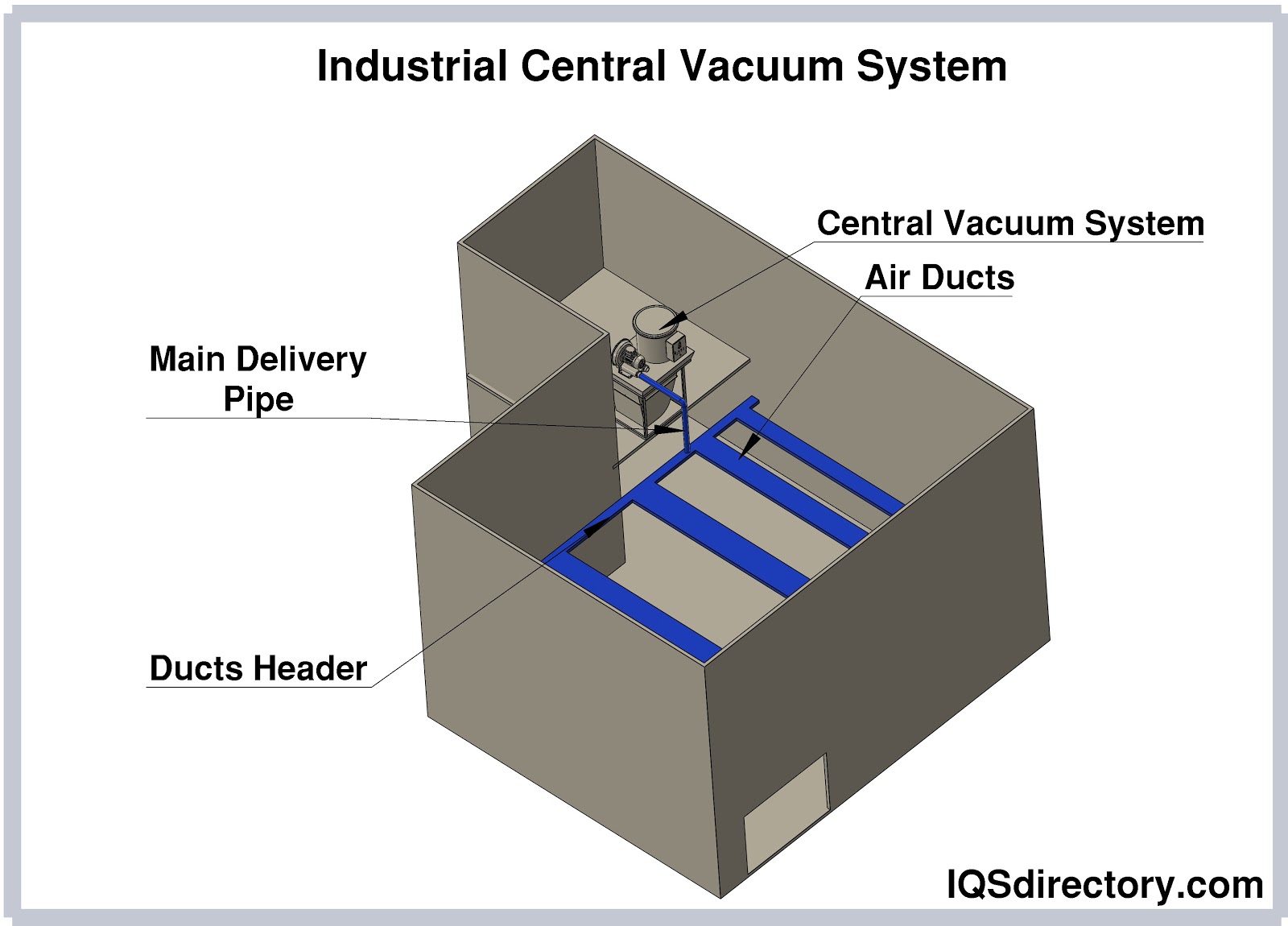
A central vacuum system is a cleaning mechanism that is built into a building for ease of use, access, and maintenance. Vacuum and pressure are created by a centrally located motor to remove dirt, dust, and debris...
Please fill out the following form to submit a Request for Quote to any of the following companies listed on
This article provides detailed information about Industrial Vacuum Cleaners.
You will learn:
An industrial vacuum cleaner is a robust cleaning device crafted to effectively clear away debris, industrial waste, construction remnants, and byproducts from manufacturing settings or building activities. As an eco-friendly piece of machinery, industrial vacuum cleaners proficiently and securely remove and properly dispose of pollutants and hazardous substances.
Beyond tackling industrial debris, industrial vacuum cleaners play a crucial role as an environmental asset by filtering and purifying air within manufacturing facilities. Integrated with dust extraction systems, these vacuums collect, filter, and cleanse the air by extracting large particulate matter, resulting in a workspace that is both cleaner and safer.
Industrial vacuum cleaners use alternating current (AC) power to drive a high-pressure fan that generates negative pressure. This vacuum effect pulls in particulate matter and air, which then passes through a series of filters before being deposited into a bag or collection space.
The operation of an industrial vacuum cleaner is based on the principle of negative air pressure. The pressure outside the collection pipe is higher than the pressure inside, creating a vacuum that pulls particles and air into the system from the external environment.
The first step in an industrial vacuum cleaner's operation is the creation of negative pressure. Unlike household vacuums, which use a small motor to generate the necessary pressure change, industrial vacuum cleaners require significantly more energy to produce enough negative pressure to handle heavy materials and large volumes of debris.
The purpose of a vacuum pump, such as a centrifugal fan, is to use mechanical, physical, or chemical processes to remove air from a confined space, thereby creating a vacuum. In an industrial vacuum cleaner, the vacuum pump is designed to maintain a consistent vacuum over extended periods of operation.
Centrifugal exhausters deliver continuous airflow while ensuring quiet and clean operation. A heavy-duty, multi-stage centrifugal exhauster offers a broad range of volume and vacuum ratings, making it suitable for multiple operators. These exhausters are designed for large pipe systems, with horsepower ranging from 15 HP to 200 HP, depending on the number of operators and system requirements.
Multi-stage centrifugal exhausters are engineered for large industrial vacuum systems that utilize numerous vacuum hoses simultaneously. These exhausters can manage thousands of cubic feet per minute (CFM) of air and handle extensive lengths of vacuum tubing, making them ideal for complex and high-capacity vacuum applications.
The fan in a vacuum cleaner creates a change in air pressure by moving air towards the exhaust port. As air is forced through the fan, its density increases in front of the fan while decreasing behind it. This pressure drop generates suction, drawing in external particles. The diagram below illustrates how this pressure difference causes suction on one side of the fan.
Filtration systems in industrial vacuums vary based on the vacuum's design. Filters can be positioned where the vacuum tube connects to capture large particles, which then drop into a collection unit or bag. For handling toxic or hazardous materials, a high-efficiency particulate air (HEPA) filter is required. HEPA filters are highly efficient, with a 99.99% rating, and are used in cleanrooms or environments where superior air filtration is essential.
Hoses for industrial vacuum cleaners are crafted from durable, abrasion-resistant materials. A common type is steel wire reinforced with wear-resistant polyurethane, providing exceptional strength. Given that pressure is a critical factor in industrial vacuum cleaners, hose selection primarily focuses on ensuring it can handle the required pressure without compromising performance.
The pressure resistance of a hose is influenced by its wall thickness, with thicker walls able to withstand higher pressure gradients. Clear industrial vacuum cleaner hoses allow for visual inspection of the medium inside, helping to prevent and identify blockages.
The types of accessories for an industrial vacuum cleaner vary based on the characteristics of the materials and debris being handled. These accessories adapt the vacuum to different working conditions and include items such as battery packs, hand and wall brushes, squeegees, floor nozzles, bulk pickup nozzles, and various sizes of fittings and tubing.
Industrial vacuum cleaners are as diverse as the industries they serve, designed to handle a wide range of materials. Whether removing oil slicks, powders, sand, rocks, or other substances with varying consistencies and particulate sizes, these vacuums are engineered to meet the specific needs of different cleaning processes.
Traditionally, vacuum cleaners are often seen as canister models on wheels used by custodial staff. However, many industrial vacuum cleaners are much larger, sometimes occupying entire rooms or mounted on trucks. Operators are specially trained to handle these machines and manage potentially hazardous materials. When considering industrial vacuum cleaners, it’s crucial to account for the types of materials they are designed to handle, which can include heavy, bulky, hazardous, and toxic substances.
Truck-mounted industrial vacuum cleaners are designed for mobility, making them ideal for disaster sites and locations where materials like sludge, slurry, industrial waste, liquids, and sewage need to be removed. Despite their larger size compared to traditional industrial vacuum cleaners, they operate on the same principle: using a tank for collection and a pump to create negative pressure. The collected waste material is stored in the truck’s tank and then transported to a disposal site.
Explosion-proof industrial vacuum cleaners are engineered to safely handle flammable substances, dangerous solids, and hazardous liquids that could be ignited by sparks or friction. They are constructed from non-flammable materials and designed to minimize the risk of sparks from material friction or static electricity. These vacuums are equipped with features to ensure safe operation in environments where explosive atmospheres are a concern.
The construction of explosion-proof industrial vacuum cleaners involves careful consideration of static dissipation, electrical insulation, and chemical neutrality. Manufacturers select materials for the housing, inlets, casters, and nozzles to meet these requirements. These materials are chosen to ensure that static electricity is effectively managed, electrical components are well-insulated, and the equipment remains chemically neutral, reducing the risk of ignition in hazardous environments.
Central vacuum systems are integrated into the design and construction of a building. Powered by the building's electricity, they operate similarly to heating or air conditioning systems. These systems consist of a central unit connected to various rooms through a network of tubes, which can be installed in ceilings or walls.
The performance of a central vacuum system largely depends on its motor type. Brush motors, while useful, have limitations in their capacity for central vacuum systems. In contrast, centrifugal exhausts can provide powerful suction for multiple hose units simultaneously. Generally, centrifugal systems are the most powerful and robust, offering superior performance for larger or more demanding cleaning applications.
The collected waste in central vacuum systems is transported through a network of tubing to a central enclosure. This enclosure is equipped with filters, bags, and storage compartments to manage the debris. Central vacuum systems are designed to provide an efficient and integrated method for cleanup, tailored to the specific needs and layout of the building or structure where they are installed.
Each stationary vacuum system, similar to central systems, is customized to meet the specific demands of the industry it serves. These systems can be installed indoors or outdoors and are designed for ultra-heavy duty use. They are equipped to handle a range of materials including wet or dry heavy abrasive substances, fine powders, and granular particulates. Operating continuously, stationary vacuum systems feature various filtration mechanisms, such as shake-out designs or centrifugal filters, to efficiently manage and process debris.
Much like truck-mounted industrial vacuum cleaners, portable industrial vacuum cleaners provide the flexibility to be used in isolated locations, such as disaster sites, liquid spills, or construction areas, as well as in places that are difficult to access with conventional equipment. Portable industrial vacuums range from models that can be carried on the back of a worker to larger units mounted on wheels for easier mobility.
The central design parameter for portable industrial vacuum cleaners is ease of mobility. These units are designed and engineered to meet the specific needs of the industry and handle the materials being cleaned. Their design often focuses on balancing portability with the necessary capacity and power to effectively manage various types of debris and contaminants.
ESD industrial vacuum cleaners are designed specifically for the electronics market to clean, remove, and collect dust and debris from sensitive electronic components. They feature permanent dissipative and grounded rubber nozzles to prevent electrostatic discharge (ESD), which can damage delicate electronic systems. Unlike other industrial vacuum cleaners, ESD models are precision-engineered for applications involving sensitive electrical systems, such as circuit boards or electrical panels.
Air-powered industrial vacuums operate on compressed air and are used in hazardous environments where electricity is not available. They have no moving parts, making them suitable for handling both wet and dry materials. These vacuums are ideal for industries that need to comply with National Fire Protection Association (NFPA) and Occupational Safety and Health Administration (OSHA) regulations concerning the handling of toxic and harmful debris and waste materials.
The operation of an air-powered industrial vacuum cleaner involves a compressed air line connected to a Venturi box. This box contains a constriction in the airflow that creates the negative air pressure needed to draw in debris and waste materials through a vacuum hose inlet. For instance, the model from Vac-U-Max features a twin Venturi suction source, enhancing its efficiency and suction power.
One of the key distinguishing features of industrial vacuum cleaners is their motor type, which can be either single-phase or three-phase. Both motor types operate on the principle of creating a magnetic field. The main difference lies in the movement of this magnetic field: a single-phase motor produces a stationary magnetic field, while a three-phase motor generates a rotating magnetic field due to the 120° phase offset between each phase of the power supply. This rotating magnetic field in a three-phase motor contributes to greater efficiency and power for heavy-duty applications.
A single-phase motor generates an oscillating magnetic field that moves back and forth. This motor typically has zero starting torque, requiring the use of an additional phase to start the motor. In contrast, three-phase motors produce a rotating magnetic field, leading to higher power output and efficiency. Three-phase motors are generally more powerful and suitable for heavy-duty industrial applications compared to single-phase motors.
Continuous duty vacuum systems are engineered for extended operation, offering exceptional durability and high performance. These systems are highly efficient and designed to operate continuously or intermittently, depending on the application. They typically feature robust, long-lasting motors, with many being central systems that utilize centrifugal exhauster motors for optimal performance.
The range of continuous duty vacuums includes various types, such as high-efficiency portable vacuums and specialized process vacuums. Portable continuous duty vacuums typically offer airflow rates between 150 to 300 CFM (cubic feet per minute), while process vacuums generally provide airflow rates ranging from 50 to 200 CFM. Each type is designed to meet specific needs based on application requirements and operational efficiency.
Industrial vacuum cleaners offer an efficient and safe solution for cleaning spills, dust, dirt, and debris. They can complete tasks that would otherwise take several hours or even days using traditional methods in a fraction of the time. By reducing the need for manual labor, these vacuum cleaners help lower labor costs and contribute to safer, cleaner, and more organized work environments.
Traditionally, vacuum cleaners are associated with household use for cleaning carpets and floors. However, in manufacturing and industrial settings, industrial vacuum cleaners play a crucial role in maintaining safety and productivity. They are essential tools for managing and removing debris, dust, and hazardous materials, helping to ensure a safe and efficient work environment.
Farmers have faced the challenge of dust from grain and livestock feed cultivation for centuries. Although it may appear harmless, this dust is highly flammable and volatile, posing significant ignition risks. Explosion-proof industrial vacuums, whether air or electrically powered, are specifically designed to safely collect and remove this dust, mitigating the threat of fires and explosions in agricultural settings.
In the automotive industry, paints and coatings are essential for protecting products during production. When changing over paint types or finishing processes, it's crucial to manage the residue and overspray left in the paint booths. To effectively handle this, industrial vacuum cleaners equipped with highly efficient filtration systems are used to recover and manage these materials, ensuring a clean and safe environment while minimizing waste and contamination.
Similar to the automotive industry, the aviation industry also involves the extensive use of powders and paints in aircraft assembly. Aircraft production often takes place in clean rooms, which necessitate the use of HEPA filters and high-performance industrial vacuum cleaners to maintain stringent cleanliness standards. Additionally, before an aircraft is delivered, it undergoes a thorough cleaning process, frequently utilizing backpack portable industrial vacuum cleaners to ensure every surface is pristine and free of contaminants.
In the baking industry, flour is a key ingredient that is very fine and prone to spreading during processing. To address the issue of clogging, industrial vacuum cleaners used in this sector are specially designed to handle such materials. These vacuums often feature multi-stage filtration systems and filter shakers that keep the filters clean and clear, preventing blockages and ensuring efficient collection and removal of flour and other fine particles.
In the chemical industry, hazardous conditions frequently pose risks to workers due to exposure to toxic and harmful substances. Industrial vacuum cleaners play a crucial role in this sector by aiding in product recovery, maintenance, and packaging. They are also essential for safely transferring products and maintaining a clean and safe work environment. These vacuums are designed to handle and contain hazardous materials effectively, helping to prevent accidents and ensure compliance with safety regulations.
In the healthcare industry, maintaining exceptional cleanliness and contaminant-free environments is crucial for patient safety and staff well-being. Industrial vacuum cleaners equipped with HEPA filters are essential for achieving these high standards. They effectively clean and remove harmful dirt, bacteria, and other contaminants, minimizing the risk of infection. Unlike common vacuum cleaners, industrial models with HEPA filters prevent the spread of airborne infectious substances, ensuring a safer and more sterile environment.
The mining industry faces significant challenges with dust, which is flammable, volatile, and highly concentrated in enclosed environments. To address these issues, industrial vacuum cleaners with high static lift are essential. These vacuums are designed to effectively recover dust and manage liquids used in mining operations, ensuring a safer and cleaner working environment.
In plastics production, small round resin pellets are the primary ingredient. These pellets are melted and shaped into plastic products. During manufacturing, the pellets are fed into the production process through hoppers. Effective recovery of spilled pellets is crucial for cost efficiency and inventory management.
Specially designed industrial vacuums are employed to remove dust and waste in the plastics production industry. These vacuums are tailored to ensure smooth and uninterrupted production, and they can clean floors, machinery, or be integrated directly into the production processes.
The pharmaceutical industry deals with a diverse array of chemicals and powders during drug and medicine production. To ensure product safety and protect workers, strict controls and monitoring are in place. Like in healthcare facilities, HEPA-filtered industrial vacuum cleaners are essential for maintaining cleanliness and recovering residue, adhering to high standards of cleanliness and safety.
In the pharmaceutical industry, there is often confusion between dust collectors and industrial vacuum cleaners. While they might seem similar, their functions are quite different. A dust collector primarily uses high air flow to manage airborne dust, without relying on suction or water lift. It's designed to capture dust that's already airborne. In contrast, an industrial vacuum cleaner is equipped with superior air flow, suction, and water lift capabilities, making it effective at picking up a variety of debris, dust, and contaminants directly from surfaces. This makes industrial vacuums more versatile and effective for comprehensive cleanup in pharmaceutical settings.
In the beverage industry, spill recovery is crucial for maintaining safety and hygiene standards. Industrial vacuum cleaners with high static lift capabilities are specifically designed to handle a wide range of liquids, ensuring effective spill management. The industry's strict government regulations concerning safety, hygiene, and cleanliness have driven the need for highly efficient and reliable vacuum cleaners to manage spills and maintain a clean production environment.
In the beverage industry, industrial vacuum cleaners play a crucial role in various aspects of production. They are used for cleaning and transporting raw materials, controlling waste, and managing scraps and cutouts from packaging. One of their most important functions is preventing food contamination by removing microbes and other harmful substances, which is essential for maintaining the safety and quality of the final product.
Vacuum cleaners are engineered to remove dirt, dust, waste, and unwanted materials using negative pressure. The collected debris is directed into a bag or collection unit for later disposal. While the basic cleaning process is straightforward, industrial vacuum cleaners have become essential in production and manufacturing environments due to their efficiency and ability to handle large volumes of debris.
Industrial vacuum cleaners are efficient, fast, and reliable. Their usefulness extends beyond mere cleaning, contributing significantly to the creation of safe and secure workspaces by managing debris and maintaining cleanliness in various industrial environments.
Initially, the cost of purchasing a reliable and high-quality industrial vacuum cleaner may seem prohibitive. However, this investment is quickly justified by their long lifespan and exceptional reliability. Jobs that previously took hours can be completed in significantly less time, enhancing overall efficiency. Industrial vacuum cleaners can be customized and adapted to meet any type of cleaning conditions or requirements, regardless of the complexity of the task.
Cleaning is a time-consuming and labor-intensive task. Investing in an industrial vacuum cleaner significantly reduces the time and energy required for cleaning, leading to increased efficiency and effectiveness in maintaining a clean environment.
Every industry is increasingly concerned about their environmental footprint and continually seeks methods to reduce their impact. Industrial vacuum cleaners are equipped with mechanisms for trapping dirt, dust, mites, allergens, and other contaminants, contributing to the creation of a healthier, safer, and more environmentally friendly workplace.
For many years, companies relied on traditional cleaning methods such as mops, brooms, and inefficient vacuums. While these methods created a surface-level appearance of cleanliness, they often failed to remove harmful and toxic materials effectively. Mops and brooms, in particular, have not proven sufficient for thorough cleaning, often leaving behind dirt and dust residue.
A major investment for a company is its buildings and facilities. Protecting these assets is essential to a company's business plan and necessary for its continuity and longevity. Investing in an industrial vacuum cleaner system is a crucial step in asset protection and stability. With various designs available, industrial vacuum cleaners can be easily adapted to fit any cleaning situation or set of parameters.
High-quality industrial vacuum cleaners are equipped with HEPA filters to enhance the removal of air contaminants. Work environments are often polluted with allergens, bacteria, and microbial contaminants that are dispersed through the airflow system or are part of production operations. Efficient, safe, and reliable industrial vacuum cleaners are designed to trap and capture these harmful airborne pollutants and effectively remove them.
Industrial vacuum cleaners are categorized as heavy-duty industrial equipment, engineered for outstanding performance in critical sectors such as healthcare, pharmaceuticals, and food production. Their use across various industries has led to the development of stringent regulations concerning their design, structure, and application. Key agencies overseeing industrial vacuum cleaners include the Occupational Safety and Health Administration (OSHA), National Fire Protection Association (NFPA), ATEX, and Environmental Protection Agency (EPA).
The regulations established by these various agencies address the handling of potentially flammable, toxic, hazardous, and harmful substances by industrial vacuum cleaners. These regulations ensure that industrial vacuum cleaners are designed and operated in a manner that mitigates risks and enhances safety in environments where such substances are present.
OSHA, established in the 1970s as part of the United States Department of Labor, is a regulatory agency focused on ensuring the safety, health, and welfare of workers and their working conditions. The General Industry standard 29 CFR 1910 outlines criteria relevant to the cleaning industry, including the handling of hazardous substances.
Silica dust, found in materials like bricks, tiles, roof slate, concrete, glass, and ceramics, has become a significant concern due to its harmful effects and widespread use. The dangerous nature of silica dust necessitates effective control and removal from worksites, a task typically managed by industrial vacuums. In 2016, OSHA updated its regulations concerning the handling of silica dust and human exposure. The previous rules were deemed insufficiently stringent and required adjustment to address the increased use of materials that produce silica dust.
The NFPA (National Fire Protection Association) is an international organization focused on fire prevention, aiming to reduce death, economic loss, and injury caused by fire. NFPA standards 652 and 654 specifically address the design requirements for vacuum systems that handle flammable, combustible, or volatile particulate matter.
The EPA (Environmental Protection Agency) continually develops standards for filtration systems used in various equipment, including industrial vacuum cleaners. The recent implementation of the Renovation, Repair, and Painting (RRP) rule has increased the need for modifications to the filtration systems of industrial vacuum cleaners to ensure compliance and effectiveness.
The ATEX directives are European Union (EU) regulations concerning potentially explosive environments and substances. Industrial vacuum cleaners with ATEX certification are approved for use in areas where there is a risk of explosive atmospheres or the presence of combustible dust.
The ATEX directives outline the minimum health and safety requirements for equipment intended to handle potentially explosive substances. Industrial vacuum cleaners with ATEX certification provide an added layer of safety for such environments.
A central vacuum system is a cleaning mechanism that is built into a building for ease of use, access, and maintenance. Vacuum and pressure are created by a centrally located motor to remove dirt, dust, and debris...
Explosion-proof vacuums are vacuum systems that use compressed air, electricity, and cyclonic motion to prevent the ignition of gasses or vapors and operate at temperatures that will not ignite a possibly flammable atmosphere. Replacing motors with...
A HEPA vacuum cleaner is a vacuum cleaner that accepts high efficiency particulate air (HEPA) filters, is tightly sealed, and allows air to only pass through the HEPA filter. They are designed to capture particles of dust, dirt, and...
Vacuum cleaners use suction to collect dirt, dust, waste products from industrial processes, and other debris for disposal, recycling, or reuse. They are mainly used for building maintenance and cleaning of industrial space...
Air filters are devices used to remove airborne particles, pollutants, and microorganisms hazardous to health and the ecosystem. In industrial facilities, air filters preserve the quality of products and materials and protect critical equipment from damage...
A baghouse is a pollution control device that uses tubes, envelopes, or cartridges to remove, capture, and separate dirt, particulate matter, and dust from the air of a manufacturing or processing facility. The main components of a baghouse are the media or bags used to filter the particles from the air as it passes through the system...
A centrifugal blower is an air moving device that uses an impeller to pull air into a tube like structure and release it at a 90o angle. The impeller is a set of blades inside the blower that rotates at a high rate to pressurize and move air...
A dust collection system is a system that removes particulate contaminants from the air in production facilities, workshops, and industrial complexes. The system cleans air by forcing it through a series of airtight filters...
A HEPA filter is a high efficiency pleated air filter capable of capturing extremely small particulate matter down to particles that are the size of a micron (µ), or a micrometer, which is 1/1000th of a meter...
An industrial blower is a device that enhances the air flow in a workspace effectively and efficiently using an electric motor, impeller, and airfoils. The purpose and function of industrial blowers is to be a permanent addition to a workspace to increase airflow and...
An industrial fan is a highly efficient, heavy duty air flow device that is constructed from exceptionally durable materials and components to withstand stringent environments and operate longer to provide constant air flow and pressure. The strength of industrial fans is due to the materials used...
A jet dust collector is a suction filtration unit that pulls dust ladened air into a filtration system that collects particulate matter and releases clean air. The filters of jet dust collectors are cleaned by compressed air that uses...
During the Industrial Revolution, when companies began producing high volumes of industrial waste like fine dust, wood dust, and other particles, an American, in 1852, S.T. Jones, applied for the first dust collector patents, a single bag filter...