Central Vacuum Systems
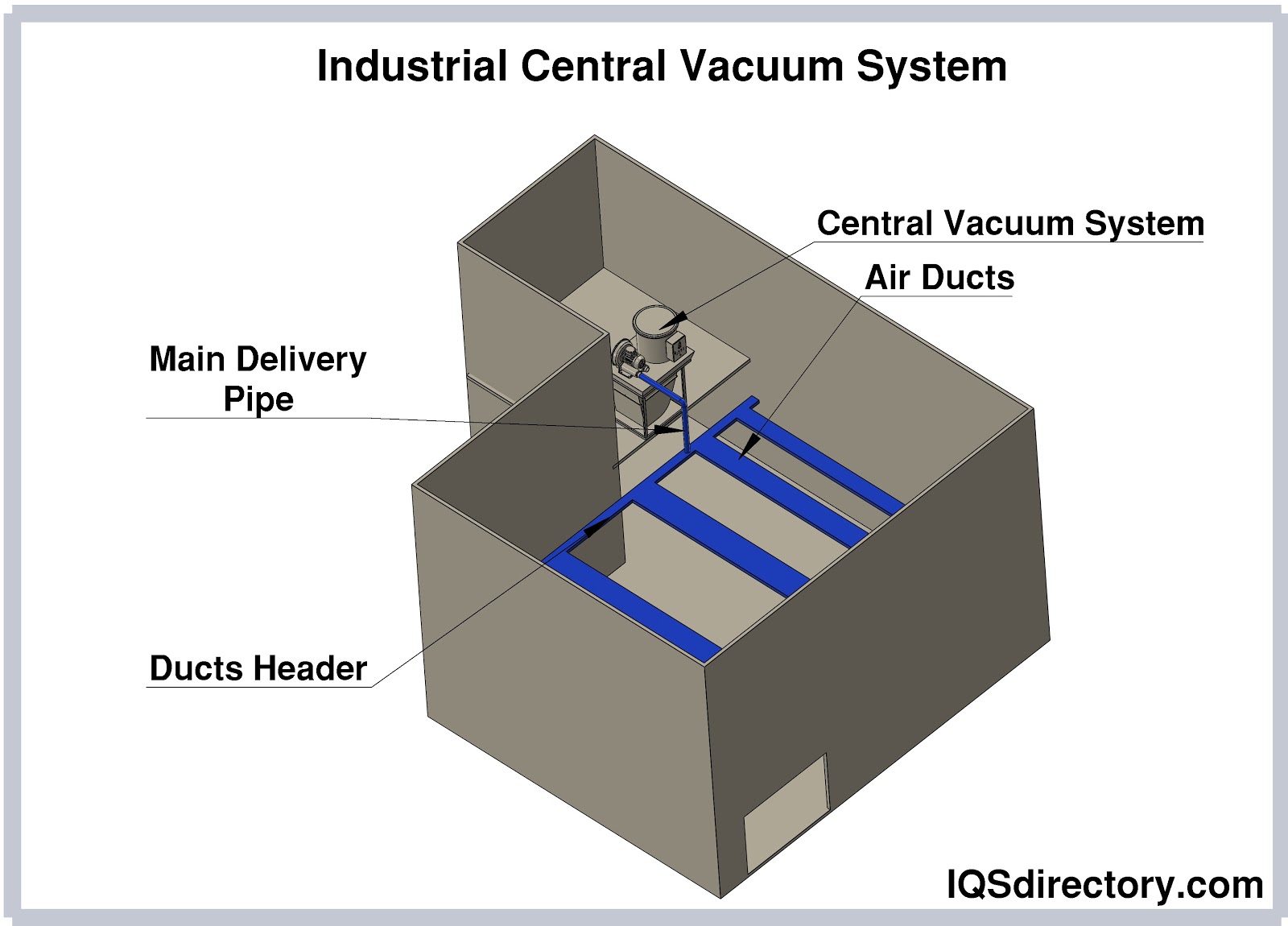
A central vacuum system is a cleaning mechanism that is built into a building for ease of use, access, and maintenance. Vacuum and pressure are created by a centrally located motor to remove dirt, dust, and debris...
Please fill out the following form to submit a Request for Quote to any of the following companies listed on
This article contains everything you need to know about industrial vacuum cleaners and their use.
You will learn:
Vacuum cleaners are robust machines designed to suction, or vacuum, dirt, debris, and other solid and liquid substances from floors and furnishings. They are commonly employed at construction sites, manufacturing plants, metalworking facilities, woodworking shops, warehouses, and similar environments where significant amounts of waste materials are produced.
In today's world, industrial vacuum cleaners are essential for operations such as recycling, material recovery, and spill management. Unlike typical home vacuum cleaners, these machines are engineered to tackle more demanding tasks. They efficiently collect a wide array of materials, including abrasive substances, coolant residues, oil mists, explosible dust, fine powders, metal shavings, debris, metalworking fluids, granular materials, and welding smoke.
An industrial vacuum cleaner operates using the fundamental principles of physics related to air pressure and suction. In basic terms, a vacuum refers to a space where air has been completely or partially evacuated, creating a pressure differential. On Earth, every object experiences the force of atmospheric pressure, and when the air pressure in a specific area drops, surrounding air with higher pressure rushes in to balance the pressure difference until equilibrium is restored. This core principle enables vacuum technology to effectively remove contaminants, including dust, debris, and even hazardous particles, from industrial environments.
Vacuum cleaners utilize this phenomenon to pick up and collect waste efficiently. The device uses a fan or a centrifugal air pump to artificially lower air pressure within its containment unit. Pressurized air from the outside rushes in, carrying dust, dirt, debris, or liquids, depending on how powerful the vacuum cleaner motor is. Motors for industrial vacuums are commonly available in single or three-phase configurations, with three-phase motors providing exceptional power suitable for the rigorous demands of heavy-duty cleaning in manufacturing plants, warehouses, and processing facilities.
The versatile design of industrial vacuum cleaners allows attachment of a wide range of cleaning accessories and specialized vacuum tools. For instance, carpet cleaning vacuums have an agitator that dislodges embedded dirt from carpet fibers, while auto detailing vacuums employ special attachments to clean tight, hard-to-reach areas like vehicle interiors. Continuous duty vacuums feature large-capacity collection chambers that can be emptied swiftly, minimizing downtime and supporting prolonged operation in commercial or industrial environments.
Industrial vacuum cleaners utilize a powerful air pump, such as a centrifugal fan, to create a partial vacuum that draws in dust, dirt, industrial debris, hazardous waste, or liquids from floors, machinery, and surfaces. These machines vary in their technical specifications—including airflow rate, filtration system, dirt or waste storage capacity, motor power, and energy source—allowing users to choose an industrial vacuum precisely suited for their application, whether in manufacturing, food processing, pharmaceutical plants, or cleanroom environments. Airflow, defined as the velocity and volume of air produced by the vacuum’s motor, is a crucial metric because certain industrial cleaning requirements demand a stronger suction power or increased air movement to tackle heavier or more abundant debris. To generate greater suction force and pick up larger or more hazardous materials, the vacuum motor must deliver increased air pressure and flow capacity. Selecting the right model often involves analyzing these factors alongside other critical features, such as noise level, portability, durability, and ease of maintenance.
Advanced air filtration systems represent another essential component of industrial vacuums. Filters are selected based on the type, consistency, and size of the contaminants to be collected. For example, water filters clean polluted air by forcing it through a water bath, trapping dust and preventing hazardous particulates from becoming airborne. High efficiency particulate air (HEPA) filters are especially effective for the removal of microscopic particles, including allergens, mold spores, bacteria, and fine dust as small as a micron, making them ideal for industries with stringent hygiene and safety requirements. Some units incorporate ULPA (ultra-low penetration air) filters for even finer particle retention. Activated charcoal filters are available to neutralize unpleasant odors, supporting applications in food production, recycling facilities, and waste management plants where air quality control is crucial.
The cyclonic separation principle uses centrifugal force to extract larger particles and debris from the incoming air stream, depositing them into a collection canister before they reach the finer filters. This multi-stage filtration design extends filter life, improves air purity, and ensures optimal suction performance. Furthermore, the rise of robotic industrial vacuum cleaners highlights the integration of automation and smart technology (AMR - Autonomous Mobile Robots) into industrial cleaning workflows. These robotic vacuums can be programmed to autonomously navigate complex facilities, provide consistent cleaning, and report on performance metrics in real time—streamlining operations and reducing labor costs. While some traditional industrial vacuums still use heavy-duty collection bags, many modern designs feature robust metal canisters or hoppers, enabling safe and efficient containment and disposal of large or hazardous debris collected in tough manufacturing environments.
When evaluating which industrial vacuum cleaner to purchase, consider key factors such as intended usage (wet/dry, hazardous material removal, or general debris collection), required suction power, portability, type of filtration, regulatory compliance (OSHA, EPA, or ATEX for combustible dust), noise levels, energy efficiency, and total cost of ownership. Proper selection and regular maintenance of an industrial vacuum system ensure optimal cleaning efficiency, reduced downtime, longer equipment life, and a safer, cleaner workspace for employees. For large-scale or specialized needs, partnering with a reputable industrial vacuum manufacturer or supplier can help tailor solutions that meet specific industry requirements and operational challenges.
Industrial vacuum cleaners are engineered for challenging environments, handling a broad spectrum of waste and debris ranging from oil spills and fine dust particles to hazardous liquids and combustible dust. These heavy-duty cleaning machines are tailored to suit demanding tasks found in industries such as manufacturing, mining, food processing, pharmaceuticals, paper mills, fabrication shops, and metalworking facilities. Whether you need continuous high-capacity cleaning or portable targeted solutions, industrial vacuums play a critical role in workplace safety, compliance, and efficient waste management for all types of facilities where stringent cleanliness standards are required.
Industrial vacuum systems are distinct from residential vacuums by their higher suction power, filtration efficiency, and robust construction. While both suction devices may appear similar on the surface, industrial models are explicitly designed for demanding commercial and industrial cleaning jobs. For example, cleaning heavy materials like sawdust and paper dust at lumber mills requires industrial vacuum equipment capable of sustaining high static lift and airflow. To pick up industrial dust and particulate matter, significant vacuum pressure and advanced filtration systems are essential, especially for facilities regulated under OSHA and EPA standards for air quality control.
Each type of industrial vacuum is optimized for specific materials—removal of toxic substances, heavy debris, fine powders, chemicals, liquids, and hazardous waste. The cleaning process, suction strength, filtration method, and build material are all chosen based on the industry and contaminants involved. Explosion-proof and hazardous-duty vacuums, for example, meet strict pollution control and hazardous waste removal regulations, achieving compliance for safe handling in environments with flammable dust or chemicals.
Central vacuum systems (CVS) are built-in industrial cleaning solutions that use ductwork and a stationary power unit to provide facility-wide vacuum coverage. These permanent installations utilize powerful motors, strategically placed tubing, and large waste collection canisters, enabling efficient cleaning of commercial and industrial buildings. Multiple inlet valves allow attachment of hoses and tools throughout the facility for dust, debris, and liquid extraction.
Strategically located in a facility’s lower level or utility area, the central vacuum system’s continuous-duty motor ensures exceptionally high static vacuum and airflow capabilities. Motor selection and system design are based on factors such as debris type, tubing distance, and required cleaning coverage. Motors typically range from 6 to 30 horsepower, providing broad application for facilities demanding industrial strength cleaning over extended periods.
Central vacuum systems offer superior dust control, noise reduction, and minimal operator labor. Designed for low-maintenance operation, these high-efficiency vacuum cleaners feature cyclone filtration or multi-stage particle separation to optimize air quality. Their advanced engineering distinguishes them from portable floor vacuums—making them a preferred choice for expansive industrial environments, warehouses, and large multi-floor office complexes.
Commercial vacuum cleaners are designed for regular cleaning of non-industrial environments such as offices, hotels, schools, and retail spaces. Commercial vacuums bridge the gap between lightweight residential vacuums and more robust industrial floor cleaning machines, offering greater durability and higher debris capacity for daily use.
These machines come in a range of forms—including upright, canister, handheld, backpack, and cordless vacuums—providing versatile spot cleaning, detail work, and carpet care in light- to medium-traffic areas. Some commercial models are wet/dry types suitable for small-scale liquid recovery. Facility cleaning services often choose commercial-grade machines for their portability and ease of use in environments where industrial contaminant levels and cleanup requirements are minimal.
Continuous duty vacuums are heavy-duty cleaning systems engineered to run 24/7, supporting nonstop industrial cleaning on manufacturing lines, logistics facilities, conveyor systems, production floors, and public transit platforms. Built for high durability and minimal downtime, these vacuums utilize rugged materials, slow-speed, brushless motors, and advanced filtration to withstand round-the-clock operation.
Most stationary continuous duty vacuum cleaners incorporate primary and secondary filters (including HEPA), pre-separators, and robust housing to ensure reliable performance and maximum worker safety. These vacuums are essential for safe removal of combustible dust, food waste, or hazardous materials, supporting industrial hygiene objectives and compliance with safety codes—including the prevention of dust explosions in high-risk industries.
High-capacity positive displacement blowers, anti-static components, vacuum relief valves, and dust collection buckets are standard features, alongside specialty filter options like PTFE and industrial-grade cloth. These systems foster automated cleaning and dust collection, minimizing facility downtime for preventive maintenance and air quality management.
Explosion proof vacuums are specifically engineered for explosive or hazardous dust and vapor environments, including chemical processing, food production, plastics, and petrochemical facilities. Built from non-sparking, corrosion-resistant materials like stainless steel and reinforced fiber, these vacuums safely remove flammable dust, fine powders, metal shavings, and volatile chemical residues—lowering risk of combustion or fire.
Facilities managing magnesium dust, aluminum shavings, chemical powders, and combustible organic byproducts utilize explosion-proof HEPA vacuums for safe contaminant removal. Critical factors in these industrial vacuums include static dissipation, grounded electrical systems, and chemical-neutral construction to avoid sparking and static charge generation. Specialized water filtration—such as immersion separators—may be used to eliminate the risk of dust ignition and enable compliant hazardous waste disposal.
Explosion-proof commercial vacuums must meet NFPA and National Electrical Code (NEC) standards (NEC 500 and NEC 505) for operation in classified hazardous locations. Typical features include bronze or static-dissipative inlets, non-electric operation, and thorough system grounding, with designations for handling Class 1 and Class 2 hazardous material environments.
High Efficiency Particulate Air (HEPA) vacuum cleaners are essential filtration systems for the removal of ultrafine particulate contamination. Industrial HEPA vacuums are used in environments where workplace air quality, hygiene, and health standards are paramount—such as cleanrooms, electronics manufacturing, pharmaceutical production, mold remediation, hazardous material abatement, and biomedical labs. With certified HEPA filters that trap 99.97% of particles as small as 0.3 microns, these vacuums excel at capturing allergens, microbial spores, lead dust, and toxic particles, ensuring compliance with occupational exposure limits.
HEPA vacuum cleaners provide advanced dust and contamination removal in critical facilities. Popular with the medical sector, food processors, and semiconductor assembly, their ability to handle both wet and dry particulate has broader benefits for facility health and safety. HEPA vacuums may include pre-filters, ULPA filters, and redundant filtration stages for maximum containment of hazardous fine particles.
Portable vacuums are flexible cleaning tools ideal for diverse job sites, from temporary industrial setups and mobile disaster response to routine shop cleanup. With models spanning backpack vacuums, canister units, and compact hand-held industrial cleaners, these machines are engineered to handle heavy debris, abrasive dust, and fine powders in hard-to-reach areas where fixed cleaning systems are unavailable.
The core components—intake and exhaust ports, high-efficiency motors, industrial filtration, and durable housing—deliver exceptional portability and reliable suction power. Many portable units feature interchangeable attachments for tasks such as standing water removal, dust extraction, and dry debris cleaning, making them essential maintenance equipment for both regular facility cleaning and emergency cleanup efforts.
Portable vacuums often deliver near-industrial cleaning performance in an easy-to-transport package. Rugged, abrasion-resistant tanks and efficient multi-stage filtration systems ensure worker safety and regulatory compliance, even for specialized applications such as chemical plant spill cleanup or construction dust management.
Portable industrial vacuums blend heavy-duty extraction performance with on-site flexibility. These rugged cleaning systems—ranging from compact canister-style cleaners to forklift-movable tanks—are trusted by diverse sectors, from electronics assembly to plastics and injection molding.
Industrial portable vacuum cleaners integrate advanced features such as multi-stage high-performance filtration (often including HEPA, ULPA, or ASHRAE-compliant filters), corrosion-resistant stainless steel housings, and robust fans driven by powerful AC motors to achieve high airflow and static pressure. This allows safe handling of hazardous, combustible, or toxic materials, supporting strict occupational health and safety protocols.
Customizable hoses and accessories—such as floor wands, water extractor heads, and anti-static tubing—ensure these portable models adapt seamlessly to a variety of industrial processes and specialized cleaning requirements, from fine dust containment to the removal of oil, sludge, metal filings, or pharmaceutical powders from sensitive production zones.
Shop vacuum cleaners (commonly called Shop-Vac® or shop vacs) are robust, bagless cleaning units ideal for workshop, machine shop, and industrial maintenance tasks. Available in drum, cylinder, or canister configurations, shop vacs deliver powerful wet/dry suction and are well-suited for construction debris, metal shavings, liquid spills, dust, and routine facility cleaning.
Shop vacuum cleaners are engineered for quick emptying and easy maintenance, featuring removable, impact-resistant collection tanks that can be dumped, blown out, or lined as needed. Additional accessories such as detachable blowers make shop vacs adaptable for clearing clogs, blowing dust away from machinery, or cleaning equipment after flooding or property damage.
Precision industrial vacuum solutions—such as small vacuum cleaners—are designed for detail cleaning, vehicle interior restoration, spot-cleaning electronics, or servicing hard-to-access machinery. Their agile, compact designs are ideal for light-duty collection of dust, crumbs, and residues in spaces where larger vacuums are cumbersome or impractical.
Variations include handheld or cordless versions, some equipped with casters or ergonomic carrying handles. Industrial-grade batteries provide workplace flexibility; however, users should be aware of trade-offs between runtime and maximum suction power when considering battery-operated small vacuums for critical tasks.
Stationary vacuum systems are permanent, automated cleaning solutions for industrial or commercial facilities. These high-capacity, centralized vacuum systems run 24 hours a day to maintain continuous cleanliness, combining bulk waste removal, dust collection, and hazardous material management in a single integrated network. Automated sensors, variable waste collector sizes, and multi-inlet configurations enhance efficiency, while robust steel construction and noise reduction technology minimize disruption in busy environments.
These systems offer a broad array of features: from HEPA or ULPA filtration for hazardous dust, to vibratory discharges for bulk waste flow, and pressure ratings for heavy-duty cleaning. Large stationary vacuums are often specified for compliance with EPA, OSHA, and local workplace airborne contaminant limits.
Additionally, advanced stationary vacuums are equipped to handle multiple cleaning points simultaneously, making them well-suited for processing plants, chemical manufacturing, and other facilities where safety-critical dust capture and centralized waste management are priorities.
Truck mounted vacuum cleaners—often called vacuum trucks or hydro-excavators—serve applications demanding remote, high-volume waste extraction and conveyance. These mobile industrial vacuums are deployed outdoors or at job sites for removal of soil, hazardous material, sewer cleaning, liquid sludge recovery, and large-scale excavation. Equipped with industrial vacuum pumps, reinforced tanks, and self-contained power sources, these units can collect, transport, and safely discharge waste collection materials into preassigned containment systems.
Truck-mounted systems are indispensable in oil and gas, utilities, environmental remediation, and construction. Their integrated water jetting (hydro-excavation) capabilities allow loosening and recovery of embedded materials for safe, non-destructive digging and soil removal at utility installation sites or when exposing underground infrastructure. Vacuum trailers provide similar performance and are valued for flexibility and deployability on remote worksites.
Upright industrial vacuums are built for robust everyday commercial cleaning—combining durable housings, reinforced handles, and heavy-duty waste collection with powerful suction. Used in offices, retail, hotels, and hospitality settings, they offer redundancy and reliability for frequent floor, carpet, and rug cleaning.
Key differences from residential vacuums include significantly larger brushes, extended power cords, and advanced, multi-stage filtration systems (often including HEPA filters) for superior particulate control and extended operational lifespan. Industrial upright vacuums deliver efficient, large-area coverage for demanding, high-traffic environments.
Today, many commercial upright models utilize advanced allergen filtration, sealing, and multi-speed motor systems for tailored cleaning performance and optimized dust control.
Canister vacuum cleaners offer industrial users exceptional versatility and ergonomic operation. With hoses and wands designed for maneuverability, these machines facilitate effortless cleaning of large floor spaces, under equipment, and in narrow gaps. Larger, industrial-grade canisters with robust casters support heavy loads and endure frequent, high-volume waste removal.
Many industrial canister vacuums are specified with flexible hoses, onboard accessory holders, anti-static wiring, and advanced filtration (including HEPA or ULPA options) for effective particulate management and worker safety. Their adaptability makes them ideal for cleaning contracts, janitorial services, and facilities with varied floor types and cleanliness requirements.
Air-operated or pneumatic industrial vacuums utilize compressed air (through venturi systems) instead of electric motors to generate vacuum power. Free of moving mechanical components, these vacuums present unmatched safety for combustible dust applications, ATEX-compliant facilities, and areas with strict electrical hazard controls.
Their silent, spark-free operation makes them the cleaning system of choice in explosive environments, hazardous materials recovery, pharmaceutical plants, and labs. Typically, air-operated vacuums meet rigorous NFPA certification requirements, providing anti-static grounding and multi-stage filtration. They are frequently used for dry and wet substance containment in sensitive production zones lacking reliable electrical infrastructure.
Wet-dry industrial vacuums are multi-purpose cleaning systems equipped to extract both solid debris and liquid waste. Combining dynamic suction, filtration versatility, and squeegee attachments, these vacuums address commercial and industrial cleaning challenges—ranging from coolant spills and flood restoration to fine dust and general workshop clean-up.
Wet-dry vacuums feature airtight canisters designed for safe containment of water, chemicals, and solid particles. Their efficient, dual-mode design eliminates the need for separate wet and dry cleaning equipment, saving on labor and reducing facility downtime. They are widely adopted in facilities with frequent liquid hazards, such as automotive shops, food processing, or labs, ensuring OSHA and hygiene compliance by enabling quick response to spills and leaks as well as effective removal of workplace dust and debris.
Advanced filtration ensures that particles are separated from the collected liquid, protecting both vacuum performance and air quality. Wet-dry vacuums are also complemented by a range of nozzles and accessories suitable for tile, carpet, and hard-surface cleaning.
Robotic industrial vacuum cleaners represent the cutting edge of automated facility maintenance. These intelligent autonomous systems use mapping, sensors, and programmable navigation to provide consistent, operator-free cleaning. Well-suited for distribution centers, warehouses, cleanrooms, and environments prioritizing employee productivity, robotic vacuums efficiently manage dust and debris removal across expansive floor areas.
Featuring high suction power, advanced filtration, obstacle avoidance, and automated charging, these machines align with industries seeking to reduce labor costs and human exposure to hazardous contaminants. Robotic models are ideal for repeatable cleaning tasks and hard-to-reach or hazardous locations. Their deployment supports Industry 4.0 initiatives and the integration of smart, connected facility management solutions.
Industrial vacuum cleaners are available with single-phase motors, operating on the standard 115V power supply found in most commercial and industrial buildings. Single-phase industrial vacuums offer flexibility for light-to-medium duty cleaning tasks, including machine shop maintenance, temporary work zone cleanup, and critical area contamination control.
These vacuums deliver up to 3 HP—making them suitable for spot cleaning and intermittent use rather than facility-wide central vacuum installations. Available in wet, dry, or wet/dry configurations, single-phase models are portable, easy to deploy, and can be equipped with specialty filters for hazardous or combustible dust, as well as accessories tailored to industry-specific cleaning needs.
Three-phase industrial vacuum systems set the standard for continuous-duty cleaning in large-scale production plants, CNC machining centers, conveyor operations, and bulk material handling. Powered by motors ranging from 3 to 25 HP, these vacuums are engineered for maximum performance, longevity, and minimal maintenance demands—delivering high static pressure and airflow for demanding applications such as bulk powder transfer, central dust collection, regulated hazardous waste removal, and large-scale cleanup.
Three-phase motors provide stable, efficient power, enabling non-stop operation and compatibility with automated facility cleaning systems. Available with customizable filtration (HEPA H14, Class L/M/H filters), side channel blowers, and heavy-duty construction, three-phase vacuums excel in environments with persistent, heavy debris or hazardous material volumes. Integration with centralized cleaning infrastructure ensures compliance with workplace safety, regulatory standards, and process requirements in modern industrial facilities.
Vacuum cleaners use suction to collect dirt, dust, and waste products from industrial processes for disposal, recycling, or reuse. Commercial vacuums have the same purpose but are less efficient and are used for light duty cleaning. The cleaning power of an industrial vacuum can be configured to pick up fine powders, abrasives, explosive media, litter, non-free flowing media, metalworking chips, toxic media, coolant, oil mist, and welding fumes. They have enough power to remove fine powders, large chunks of debris, and various types of fluids and liquids. Engineers design industrial vacuums that are capable of performing general and precision cleaning.
Industrial vacuum cleaners facilitate the collection of waste materials from industrial processes that can be reclaimed and reused. They employ specialized filters to ensure that reusable materials are not contaminated by unwanted substances. After collection, these reclaimed materials are cleaned and reprocessed. In environments where fine dust or waste shavings are present, high-efficiency particulate air (HEPA) filters are utilized. These filters effectively capture both large particles and microscopic particulates, ensuring high standards of cleanliness and material purity.
Every vacuum configuration is different, which makes it possible to engineer an industrial vacuum for every industrial environment. Small, portable vacuum cleaners can collect debris in fabric filter bags or removable plastic containers. Disposable filters can be lined with a larger, removable filter to provide extra filtration. Backpack vacuum cleaners, canister vacuums, rider or walk-behind vacuum cleaners, robotic vacuum cleaners, and vacuum cleaner trucks are a few of the available industrial vacuum cleaner configurations with the majority of vacuum cleaners being portable. Continuous vacuum cleaners, which can be large and are used for constant use, are equipped with wheels .
Central vacuum systems are ideal for large buildings requiring frequent cleaning due to their efficiency and ease of use. These systems feature inlets installed throughout the building's ductwork, allowing maintenance staff to connect hoses and vacuum attachments to a single central unit. By being concealed, central vacuum systems reduce noise associated with vacuuming. Instead of managing multiple vacuums with separate filters, maintenance teams benefit from a single machine with multiple outlets.
As Automated Mobile Robots (AMRs) and robotics technology advance, robotic industrial vacuum systems are gaining popularity for their efficiency and cost-effectiveness. These vacuums can be programmed to clean specific areas using an uploaded map and a series of sensors. While they may not be suited for heavy-duty cleaning tasks, robotic vacuums are effective for various cleaning operations, offering significant labor savings.
A central vacuum system is a cleaning mechanism that is built into a building for ease of use, access, and maintenance. Vacuum and pressure are created by a centrally located motor to remove dirt, dust, and debris...
Explosion-proof vacuums are vacuum systems that use compressed air, electricity, and cyclonic motion to prevent the ignition of gasses or vapors and operate at temperatures that will not ignite a possibly flammable atmosphere. Replacing motors with...
A HEPA vacuum cleaner is a vacuum cleaner that accepts high efficiency particulate air (HEPA) filters, is tightly sealed, and allows air to only pass through the HEPA filter. They are designed to capture particles of dust, dirt, and...
An industrial vacuum cleaner is a heavy duty piece of cleaning equipment designed to remove debris, industrial waste, construction refuse, and matter that remains after a manufacturing process or construction project...
Air filters are devices used to remove airborne particles, pollutants, and microorganisms hazardous to health and the ecosystem. In industrial facilities, air filters preserve the quality of products and materials and protect critical equipment from damage...
A baghouse is a pollution control device that uses tubes, envelopes, or cartridges to remove, capture, and separate dirt, particulate matter, and dust from the air of a manufacturing or processing facility. The main components of a baghouse are the media or bags used to filter the particles from the air as it passes through the system...
A centrifugal blower is an air moving device that uses an impeller to pull air into a tube like structure and release it at a 90o angle. The impeller is a set of blades inside the blower that rotates at a high rate to pressurize and move air...
A dust collection system is a system that removes particulate contaminants from the air in production facilities, workshops, and industrial complexes. The system cleans air by forcing it through a series of airtight filters...
A HEPA filter is a high efficiency pleated air filter capable of capturing extremely small particulate matter down to particles that are the size of a micron (µ), or a micrometer, which is 1/1000th of a meter...
An industrial blower is a device that enhances the air flow in a workspace effectively and efficiently using an electric motor, impeller, and airfoils. The purpose and function of industrial blowers is to be a permanent addition to a workspace to increase airflow and...
An industrial fan is a highly efficient, heavy duty air flow device that is constructed from exceptionally durable materials and components to withstand stringent environments and operate longer to provide constant air flow and pressure. The strength of industrial fans is due to the materials used...
A jet dust collector is a suction filtration unit that pulls dust ladened air into a filtration system that collects particulate matter and releases clean air. The filters of jet dust collectors are cleaned by compressed air that uses...
During the Industrial Revolution, when companies began producing high volumes of industrial waste like fine dust, wood dust, and other particles, an American, in 1852, S.T. Jones, applied for the first dust collector patents, a single bag filter...