PVC Ball Valves
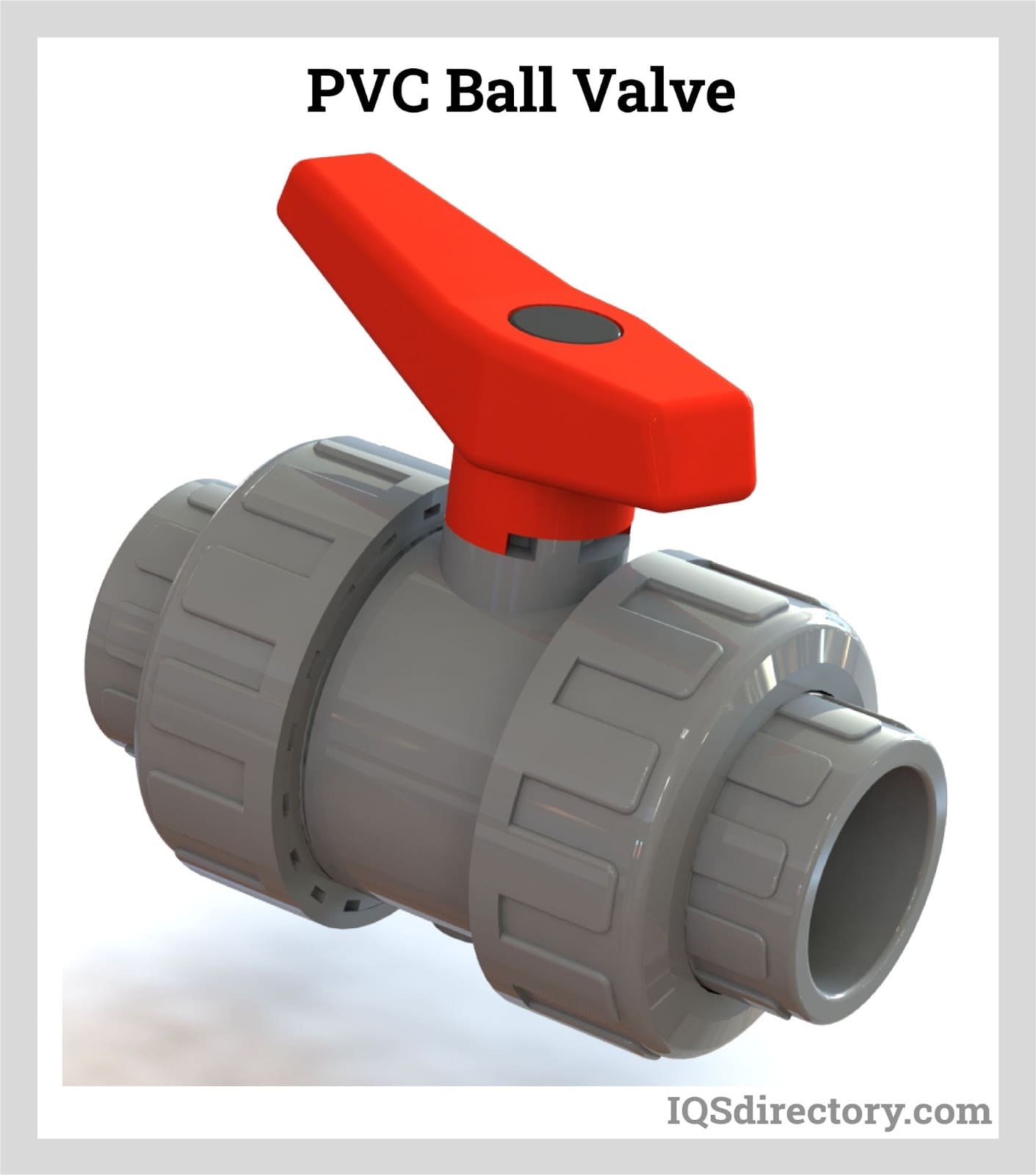
A PVC or polyvinyl chloride ball valve is a plastic on and off valve that has a rotary ball with a bore where turning the ball a quarter turn can stop the flow of a fluid. They are highly durable, cost effective and can be...
Please fill out the following form to submit a Request for Quote to any of the following companies listed on
This article contains all the information you need to know about Ball Valves.
Read further and learn more about:
A ball valve is a form of shut-off valve designed to control the flow of gases, liquids, and vapors in a piping network. It functions by rotating a ball with a central hole that allows or obstructs flow. This ball is placed between two seats and is linked to an operating mechanism through a shaft. When the cross-section of the bore is perpendicular to the direction of flow, the valve halts fluid passage. Conversely, when the bore is aligned with the flow direction, it permits the fluid to pass through, with the flow rate determined by the exposed bore area.
Ball valves belong to a category of quarter-turn valves, which also includes plug valves and butterfly valves. These valves can be operated manually or through an actuator. The most basic method of operating a ball valve involves using a wrench or lever that an operator manually turns. Applying torque rotates the lever arm 90 degrees, either clockwise or counterclockwise, to open or shut the valve. A lever arm parallel to the pipe denotes that the valve is open, while a lever arm perpendicular to the pipe indicates that the valve is shut.
Ball valves come in numerous designs and with various features, catering to a wide range of industrial needs. The standards and specifications for these valves vary depending on the particular industry they serve.
The essential components of a ball valve are as follows:
The valve housing, or body, encloses all internal components of the ball valve. It provides a secure, sealed environment for the ball, ensuring accurate control of fluid flow through the valve. Typically, the housing includes inlet and outlet ports for pipe connections. It is constructed from durable materials like metal, thermoplastic, or thermoplastic-lined metal to safeguard the internal parts, guaranteeing the valve’s longevity and reliability in various industrial settings.
The ball within a ball valve is a sphere with a central hole known as the bore. The bore serves as the passage for fluid flow when it aligns with the valve's flow path. If the bore is perpendicular to the flow direction, it restricts the flow. Ball valves may feature either solid or hollow balls. A solid ball maintains a consistent opening diameter, promoting smooth and constant fluid flow. Conversely, a hollow ball, with its internal cavity, allows for higher flow rates but can create turbulence and increased velocities. Hollow balls are typically lighter and more cost-effective than solid ones.
The shaft connects the ball to the control mechanism, enabling rotation of the ball. This rotation aligns the ball with the flow path to allow fluid passage or positions it perpendicular to block the flow. The shaft includes seals like O-rings and packing rings to prevent fluid leakage around the shaft. It must be robust enough to handle the system's pressure and temperature conditions. The shaft can be manually operated via a lever or handwheel, or it may be actuated electrically, pneumatically, or hydraulically.
The bonnet extends from the valve housing and encases the shaft and its packing, especially in high-pressure and high-temperature applications. It may be welded or bolted to the body and is typically constructed from sturdy metal. The bonnet provides a cover for the shaft connection to the external control mechanism and can be either removable or integral to the valve body, depending on the design.
Ball valves have two seats, usually made from soft materials such as PTFE (Teflon) or elastomers. These seats create a tight seal around the ball when the valve is closed, preventing leaks by forming a barrier between the ball and the valve body. The upstream seat seals against pressure, while the downstream seat prevents leakage to the atmosphere.
Electric actuators, or motorized actuators, enable remote control of ball valves and are ideal for situations where manual operation isn't feasible. These actuators can be designed as either quarter-turn or multi-turn units. Quarter-turn actuators are suited for valves that can be fully opened or closed, while multi-turn actuators provide multiple rotations for more nuanced control.
At the core of an electric actuator is its electric motor, which drives a gear system available in various torque ranges. This gear drive connects to an output drive that operates the valve. All components are housed in a sealed, waterproof enclosure. Electric actuators are remotely controlled and can include features such as adjustable cycle times, duty cycles, and even network or databus connectivity for enhanced functionality.
In addition to electric actuators, pneumatic actuators are available and perform similar functions. These rely on an air supply, which can limit their applicability compared to electric actuators. While electric actuators tend to be more expensive, they offer greater versatility and can be adapted to a wider range of applications.
Motorized ball valves provide automated control by using an electric motor to open or close the valve. These valves feature an electric actuator mounted to the valve body, which rotates 90° to control the valve's position. The actuator responds to electrical signals that dictate whether the valve should be opened or closed.
For applications requiring precise valve positioning based on flow conditions, a digital position sensor may be employed. This sensor, coupled with a microprocessor, compares the actual valve position with the desired position using feedback from an output system. The actuator adjusts accordingly to align with the input signals.
Motorized ball valves are commonly used in remote locations to control the flow of materials. They are designed to accommodate various applications and can be located at significant distances from the control point. These valves offer a practical and efficient solution for valve control, significantly reducing labor and enhancing material handling processes.
Pneumatic actuators function similarly to electric actuators but use compressed air to control ball valves. These actuators feature a housing with horizontal pistons connected to a rack and pinion mechanism, which converts the pistons' linear motion into rotary motion. The pistons are driven by compressed air, making the system straightforward, reliable, and more cost-effective compared to electric actuators.
Like electric actuator systems, pneumatic actuators have specialized mounts for easy valve installation. They operate by receiving controlled bursts of air. A solenoid, mounted on the actuator and connected via an air line, is energized by an electric current. This current moves a plunger that opens ports on the actuator, allowing air to actuate the valve.
Air actuated ball valves come with features similar to those found in electric actuated valves, including positioners, limit switches, gear operations, and speed control. While pneumatic actuators are robust and dependable, they require proximity to an air supply, making them suitable for environments where access to compressed air is readily available.
Ball valves can be categorized based on their housing assembly, ball design, and bore profile.
A one-piece ball valve features a single, cast body that encases all internal components, minimizing the risk of fluid leakage. These valves are the most cost-effective and typically have a reduced bore. Welded one-piece ball valves are common but are not designed for disassembly, making them unsuitable for applications where cleaning or repair might be necessary. They are best used in environments where particle accumulation is minimal and sanitation is not a primary concern. In contrast, screwed one-piece ball valves can be cleaned, serviced, and repaired, though disassembly requires specialized tools.
Split body ball valves are designed with their bodies assembled around the ball. These valves can be categorized as either two-piece or three-piece configurations:
A two-piece ball valve features a housing divided into two sections that are assembled together. One section houses the ball and provides a connection at one end, while the other section contains the internal components and connects at the opposite end. This design is the most prevalent among ball valves. Although the two sections can be separated for cleaning, maintenance, and inspection, this process requires removing the valve from the pipe.
A three-piece ball valve comprises a housing that encloses the internal components, with the housing sections connected and secured by bolts at each end. These ends are typically threaded or welded to the main pipe.
Three-piece ball valves are ideal for applications requiring easy cleaning and maintenance. The design allows for the replacement of seats and seals without removing the entire valve from the pipeline, which is particularly beneficial in industries such as food and beverage and pharmaceuticals, where cleanliness and product safety are critical.
A top entry ball valve provides access to its internal components by removing the bonnet from the top of the valve. This design facilitates in-line maintenance activities—such as disassembly, cleaning, inspection, and repair—without the need to remove the valve from the pipeline.
The floating ball is a prevalent design used in ball valves. In this design, the ball is suspended within the valve and can move laterally when the valve is closed. It is positioned between two seats that secure and support the ball. The ball is connected to the shaft at one end via a slot, while the other end remains free. When the valve is open, the shaft’s connection at the top of the ball keeps it from moving laterally.
Sealing in a floating ball valve relies solely on fluid pressure. When the valve operates, the inlet fluid pressure pushes the ball against the outlet seat, preventing any leakage from the valve body. The fluid pressure exerted on the ball and seats is higher when the valve is closed.
Floating ball valves are known for their simple design and are typically used in smaller diameters for handling liquids and gases under low to moderate pressures. Their application is constrained by the pressure tolerance of the seats. At higher pressures, the seats may deform due to the force exerted by the ball, potentially compromising the valve’s sealing ability at lower pressures. Additionally, the torque required to turn the shaft is influenced by the force needed to overcome the fluid pressure acting on the ball and seats.
In a trunnion ball valve, the ball is supported by an additional shaft at the bottom known as the trunnion. This design stabilizes the ball and restricts its movement to the axis of the valve. The ball’s movement is controlled by the rotation of the valve shaft. Trunnion ball valves also include spring-loaded seats. The inlet fluid pressure compresses the springs towards the ball, creating a secure seal.
Trunnion ball valves come in a range of sizes from small to large but are generally more costly than floating ball valves. They are well-suited for high-pressure applications because they efficiently handle a wide range of pressures. The fluid pressure is distributed to both the trunnion and the seat springs, resulting in lower operating torque and enabling the use of smaller actuators.
A vented ball valve operates similarly to a standard ball valve, with the key difference being that the vented ball has small orifices drilled into its side. When the valve is closed, these orifices align with the outlet side of the valve. The purpose of these drilled holes is to release trapped gases that can accumulate and build up internal pressure. This feature helps prevent leaks, valve failure, and potential explosions.
Vented ball valves are commonly used in applications involving compressed air systems, cryogenic processing, and the handling of volatile liquids. They are sometimes referred to as "cryogenic valves" due to their effectiveness in cryogenic environments.
A full bore ball valve features a bore diameter that matches the pipe diameter, ensuring that the flow area remains consistent. This design results in minimal flow resistance and low frictional losses, which translates to a lower pressure drop. Such low pressure drop reduces the difficulty of pumping within the system. However, because the bore diameter must match the pipe size, full bore valves require larger ball sizes and housings, making them more expensive than reduced bore valves.
Full bore ball valves are also easier to maintain and clean. In pipeline systems, a process called pigging is used for maintenance and inspection. This involves using spherical or cylindrical devices known as pigs to travel through the pipes, detecting and removing build-ups without disrupting the fluid flow. This process is facilitated by the larger diameter of full bore ball valves.
Additionally, full bore ball valves are well-suited for handling liquids with mixed solids. They help prevent the accumulation of particles that could otherwise cause blockages or separation of the mixture as it flows through the system.
A reduced bore ball valve features a bore diameter that is smaller than the pipe diameter by one pipe size. The exact reduction is specified based on the agreement between the manufacturer and the customer. This design narrows the flow area at the outlet, which introduces frictional losses and results in a pressure drop. As the flow area decreases, the velocity of the fluid increases to maintain the same flow rate.
Reduced bore ball valves are more commonly used than full bore ball valves, particularly in applications where flow rate and turbulence are not critical concerns, and where particle build-up is unlikely. They are generally less expensive than full bore valves due to the smaller ball size and housing required. Additionally, reduced bore ball valves typically experience a smaller pressure drop compared to other types of valves.
A segmented ball valve features a V-shaped notch on the ball, which provides precise flow rate control based on the ball's rotation. This design also ensures effective shut-off capability. The flow characteristics of a segmented ball valve are designed to approximate an equal percentage flow curve, meaning that the flow rate increases exponentially as the ball nears the fully open position.
A cavity-filled ball valve features a seat design that fills the gap between the ball and the valve body, preventing the accumulation of trapped media or particles that could lead to contamination or blockages. This design makes cavity-filled ball valves easier to clean and maintain.
These valves are particularly valuable in industries where hygiene is critical, such as the food, pharmaceutical, and bioprocessing sectors. They are well-suited for handling solid-liquid mixtures, such as slurries, due to their effective design.
Multi-port ball valves are designed to manage multiple fluid streams, allowing for diversion, combination, splitting, or shutting off of flows. They achieve this through a ball with either an L-shaped or T-shaped bore. While these valves can direct flow from a single inlet to multiple outlets, they do not regulate the flow rates to each outlet stream. Multi-port ball valves are versatile in combining several streams into one or redirecting flow as needed. The schematic diagram below illustrates the various flow configurations for L-shaped and T-shaped multi-port ball valves.
Three-way ball valves feature three ports for capturing and directing fluid flow. The valve's core component is a metal ball with internal passages that regulate the flow of fluid or gas. As the fluid enters the valve, a mechanism rotates the ball to direct the flow through the desired port. Three-way ball valves are available in designs with either two outlet ports and one inlet port or two inlet ports and one outlet port.
These valves can be configured in L or T shapes and are capable of various functions such as switching flow direction, mixing flows, diverting streams, and stopping flow while allowing other flows to continue. When used for mixing, the valve allows fluid to enter from multiple directions and combine within the valve body.
Three-way ball valves are equipped with three ports for controlling fluid flow. They feature a central metal ball with internal passages designed to manage the direction of the fluid. As fluid or gas flows into the valve, a rotating mechanism adjusts the ball to direct the flow through the appropriate port. Three-way ball valves come in configurations with either two outlet ports and one inlet port or two inlet ports and one outlet port.
Similar to multi-port valves, three-way ball valves can be configured in either an L-shaped or T-shaped arrangement. They are versatile and can perform various functions such as switching the direction of flow, mixing different flows, diverting flow, and blocking flow from multiple directions. When mixing materials, the valve allows fluids to enter from multiple directions and blend within the valve body.
Sanitary ball valves are designed to adhere to stringent cleanliness and hygiene standards, making them suitable for applications in the food, beverage, medical, and pharmaceutical industries. These valves are engineered to meet health and safety regulations that require strict control over microbial contamination, ensuring the purity of substances during processing.
The body of sanitary ball valves is typically constructed from series 304 or series 316 stainless steel. Series 304 is commonly used in hospitals and food processing due to its smooth surface and durability, which allows for repeated cleaning without significant wear. Sanitary ball valves are designed for frequent assembly, disassembly, cleaning, and reassembly to prevent microbial growth and contamination.
These valves are engineered to mitigate risks associated with biological, chemical, or physical hazards. To ensure easy cleaning and avoid contamination, sanitary ball valves avoid threaded connections. Instead, they use seals, O-rings, and seats made from inert, abrasion-resistant materials such as polytetrafluoroethylene (PTFE or Teflon).
Sanitary ball valves address the typical issue of dead spots between the ball and the seat where bacteria can grow by employing cavity-filled ball seats. These seats fill the dead space with PTFE, reducing the risk of contamination. Additionally, the surfaces of sanitary ball valves are polished to a high finish with roughness average (Ra) values ranging from 8 to 32 to eliminate peaks and imperfections that could harbor contaminants.
Ball valves are typically made from a range of materials for both the ball and the housing, including:
Brass, an alloy primarily composed of copper and zinc, is easily recognized by its dull yellowish to reddish hue, which varies based on zinc content. It is a popular choice for ball valves due to its strength, durability, and ability to handle high temperatures and pressures. Brass also boasts antimicrobial properties thanks to its copper content, which helps prevent microbial growth on its surface. It offers good resistance to chemicals, corrosion, and biofouling. However, brass can be susceptible to dezincification when exposed to high chlorine levels, which can lead to the loss of zinc and weaken the alloy's structure.
Brass ball valves are not difficult to fabricate because of their malleability, and they are also easy to cast and weld. They are lighter and cheaper than steel ball valves. They are also easy to assemble in the piping system. Common applications of brass ball valves are in food, chemical, and oil and gas processing, and in conveying gaseous fluids. It is also safe to use in the delivery of potable drinking water.
Stainless steel is a high-strength alloy known for its excellent corrosion resistance, achieved through its high chromium content and, in many cases, nickel. It maintains its strength and durability even under high temperatures and pressures, making it a reliable material for demanding applications.
Common grades of stainless steel used in ball valves are 304 and 316. Type 304 stainless steel contains 18% chromium and 8% nickel, while 316 stainless steel includes 18% chromium, 10% nickel, and trace amounts of molybdenum. The addition of molybdenum in 316 stainless steel enhances its resistance to chlorides and other corrosive agents.
Stainless steel ball valves are particularly advantageous in several applications. They are commonly used in swimming pools to manage chlorinated water, in industrial settings such as desalination and petroleum refining where they handle corrosive chemicals at high temperatures and pressures, and in breweries for processing wort, a reactive liquid produced during mashing.
PVC (Polyvinyl Chloride) is a tough, rigid plastic material known for its durability and affordability compared to brass and stainless steel. While it generally has lower strength and a lower temperature and pressure rating (up to 150 psi and 140°F, respectively), PVC is resistant to corrosion and most acids, bases, and salt solutions. However, it is not resistant to aromatic compounds and hydrocarbons. PVC ball valves are commonly used in plumbing, irrigation, and water distribution systems.
Chlorinated PVC (CPVC) is a modified form of PVC that has been chlorinated through a free radical reaction initiated by UV light. This chlorination enhances CPVC's temperature resistance, allowing CPVC ball valves to handle temperatures up to 200°F. CPVC ball valves are suitable for applications requiring higher temperature tolerance than standard PVC.
Polypropylene (PP) is a versatile, resilient, and lightweight thermoplastic derived from propylene monomer. It is known for its high resistance to many acids and bases, although its compatibility with organic compounds and solvents is somewhat limited. The material's chemical resistance diminishes at elevated temperatures, with a maximum service temperature of 82°C. PP ball valves are effective for managing the flow of various fluids, including those with different viscosities. These valves are commonly utilized in industries such as sugar production, fertilizers, chemicals, and paper manufacturing.
Glass-fiber-reinforced polypropylene (GFPP) incorporates glass fibers into polypropylene to enhance its dimensional stability, rigidity, and chemical resistance, while also reducing its thermal expansion coefficient. With a 40% glass fiber composition, the heat deflection temperature can reach up to 150°C at 264 psi. The addition of glass fibers improves the material's cost-effectiveness and enables it to withstand more demanding and severe applications.
PVDF (Polyvinylidene Fluoride) is a high-purity, robust thermoplastic fluoropolymer with a high molecular weight. It is produced through the free-radical polymerization of vinylidene fluoride gas. Additionally, PVDF is known for its resistance to abrasion.
This polymer offers exceptional chemical resistance, making it ideal for handling aggressive liquids and gases such as sulfuric acid, hydrochloric acid, nitric acid, hydrocarbons, fuels, and both aromatic and aliphatic halogenated solvents. It is widely used in ball valves across various industries, including water purification, wastewater treatment, and food and pharmaceutical processing, due to its resistance to biofouling and microbial film growth. PVDF is also stable when exposed to sunlight and UV radiation. The maximum operational temperature for PVDF is approximately 115°C.
Polyethylene (PE) is a versatile, resilient, and lightweight thermoplastic that is the most widely used plastic. It exhibits compatibility with a range of substances, including strong acids and bases, as well as some organic compounds like oils and alcohols. As PE's crystallinity and density increase, its chemical resistance improves. PE ball valves are utilized in various manufacturing processes and are also effective in water purification and wastewater treatment. The maximum operational temperature for PE is about 60°C.
The seat in a valve is typically made from elastomeric materials, plastics, or metals to ensure a secure seal with the ball. An ideal seat material should also exhibit the following qualities:
Common materials used for ball valve seats include:
Metal-seated ball valves are capable of enduring higher temperatures and hydraulic pressures. They are also more resistant to abrasive and corrosive fluids.
Ball valves provide numerous advantages in a range of applications, thanks to their design and operational features. Key benefits of using ball valves include:
Users should be aware of certain limitations to maintain the optimal performance of ball valves:
Standard ball valves may be used in throttling low pressure gases. Segmented ball valves may be used in limited throttling applications.
However, advanced ball valves with modified designs or seats made from engineered materials that are suitable for throttling applications are commercially available.
A PVC or polyvinyl chloride ball valve is a plastic on and off valve that has a rotary ball with a bore where turning the ball a quarter turn can stop the flow of a fluid. They are highly durable, cost effective and can be...
A butterfly valve is a quarter-turn rotational motion device that utilizes a rotary disc to allow, obstruct, or control the flow of fluids in a piping system. It features a rotating disc that is situated on the passageway of the flowing media...
A check valve is a safety device designed to allow fluids and gases to flow in one direction. Under pressure, fluids enter the valve at the inlet and exit through the outlet. Uninterrupted flow continues until the pressure drops, or the pump is shut down...
Diaphragm valves utilize a flexible diaphragm to obstruct, control, or isolate the flow of fluids. The diaphragm acts as the flow control element that flexes up or down to increase or decrease the fluid flow rate, respectively...
A spring check valve is a valve that ensures unidirectional flow and prevents reverse flow. They have a single inlet and outlet and must be placed in proper orientation to function correctly. On the side of a spring check valve, and all...