Compression Molding
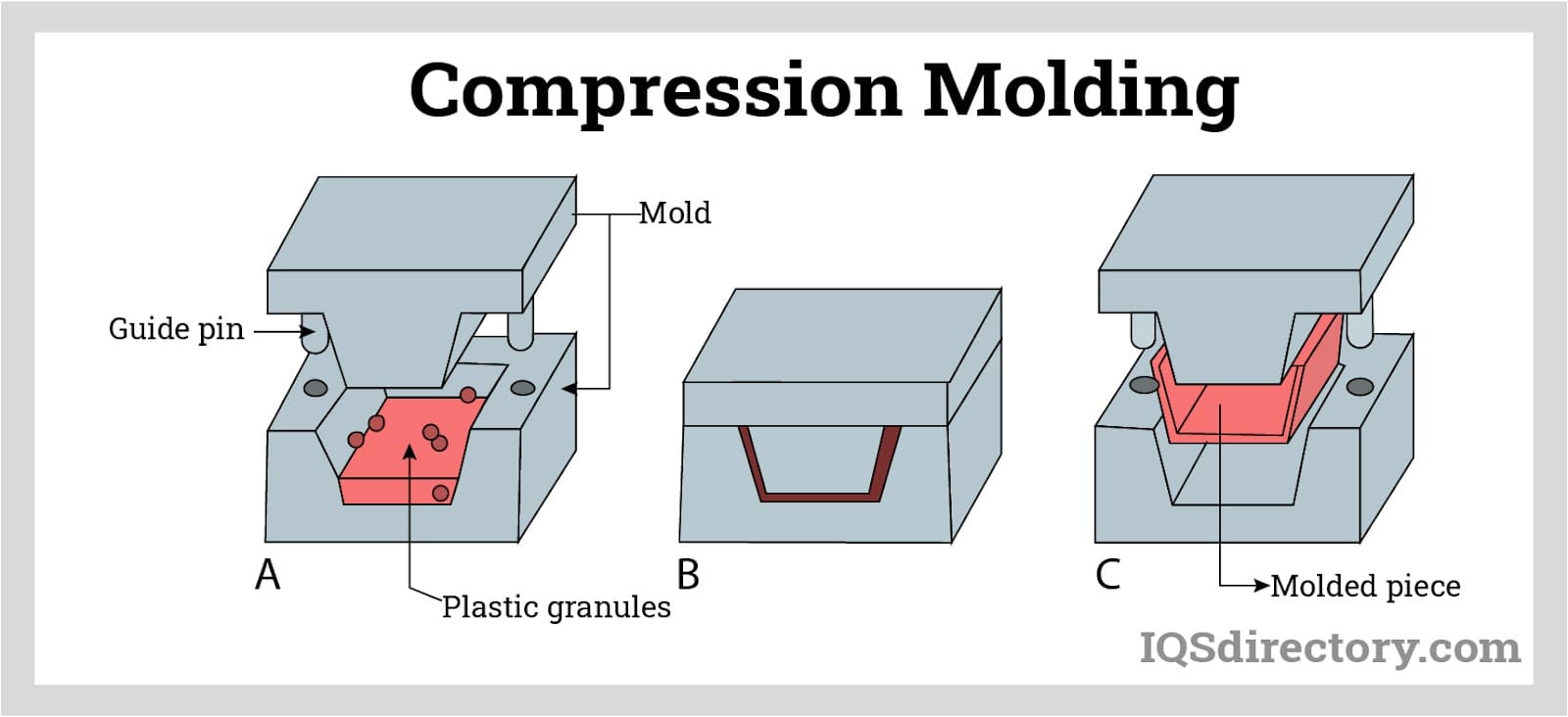
Molding is a manufacturing process that uses a mold - the latter being a solid container used to give shape to a piece of material. It is a forming process. The form is transferred from the mold to the material by...
Please fill out the following form to submit a Request for Quote to any of the following companies listed on
This article will take an in-depth look at vibration absorbers.
The article will bring more understanding on topics such as:
This section delves into vibration absorbers, exploring their terminology and operational mechanisms.
A vibration absorber is a spring-mass system with one degree of freedom (DOF) that deals with vibrations in systems affected by harmonic forces, such as engines, motors, and conveyors. Its primary purpose is to minimize or eliminate these vibrations, ensuring smoother and safer operation. Usually installed on vibrating systems, these devices create "anti-resonance" to counteract unwanted oscillations. An illustration of how a vibration absorber addresses these oscillations is provided below.
Vibration absorbers are prevalent in many machines and mechanical systems, making their terminology essential to comprehend. The following sections cover this information in detail.
Vibration is described as a mechanical phenomenon where oscillations occur around an equilibrium point. While vibrations are beneficial in some instances, such as mixing concrete with a concrete vibrator, they can also be detrimental by causing unwanted noise and energy wastage. In electric motors, engines, and numerous mechanical operations, vibrations are typically undesirable. When vibrations are not wanted, absorbers are implemented to diminish or eradicate them.
Resonance is a phenomenon where the amplitude of vibrations increases when the frequency of an externally applied force corresponds with the system's natural frequency. This effect can be either beneficial or harmful, depending on the situation. In construction, resonance is commonly adverse, potentially causing structural damage such as cracks or collapses in bridges, buildings, and walls due to intensified vibrations. On the other hand, in the music domain, resonance is advantageous, used to enrich sound production in musical instruments.
Amplitude represents the maximum distance achieved by a displaced object or point within a system. For vibrating or displaced objects, this measurement is taken from the system's equilibrium position. In terms of sound waves, amplitude is determined by assessing the volume or loudness of the sound produced.
Energy absorption describes the process where the magnitudes of random motion strengths (vibrations) are decreased.
The natural frequency is the number of vibration cycles completed by a body or object in a specified period of time when vibrating freely.
Shock refers to the disturbance or displacement of a body from its equilibrium position due to a sudden force application.
Vibration control involves utilizing various devices, such as isolators, dampers, pads, and mounts, to capture the kinetic energy produced by vibrating elements, thereby preventing it from transferring to nearby surfaces.
Vibration absorbers are typically used in machines and systems operating at a constant speed or under continuous exciting frequencies. The setup comprises both the main system and the absorber, as illustrated in the diagram below.
The following provides an arrangement for installing vibration absorbers:
The primary system is sometimes referred to as the payload and represents the component experiencing the unwanted frequencies needing management or mitigation. Examples include motors, engines, bridges, and machinery. Its natural elasticity allows it to return to its original shape after deformation.
The absorber, also known as the support, assists the primary system by reducing or eliminating encountered vibrations. This may involve elements like rubber mounts, springs, pads, and more. The absorber can also be hydraulic, where a hydraulic system is used for vibration absorption.
Vibrations from equipment signify a form of energy—kinetic energy—dissipating through random oscillations. Rubber effectively absorbs substantial amounts of kinetic energy due to its elasticity. Its durability and resistance to high temperatures make it suitable for environments like engines. Rubber's compatibility with various metals, alongside its high shear modulus and nonlinear stiffness, positions it as a preferred material. Typical natural and synthetic rubbers used in applications requiring heat and chemical resistance include silicone, butyl, fluoroelastomer, neoprene, and EPDM.
A hydraulic system features a hydraulic cylinder, piston rod, and hydraulic fluid. The diagram below displays the components of a basic hydraulic system. Vibrations influence the piston rod, causing fluid movement inside the cylinder. This liquid converts kinetic energy resulting from vibrations into heat. An image of hydraulic shock absorbers detailing their parts is shown below.
Effective vibration absorber designs involve several key considerations to ensure optimal functionality. Depending on system complexity, combining springs with rubber might be the most effective solution, while in other cases, a simple rubber mount suffices.
Rubber mounts are crafted to dampen system vibrations by positioning them between components, like metals. They help diminish wear and tear, reducing maintenance costs. These mounts come in diverse shapes, sizes, and materials for varying applications.
Rubber mounts can deform under machinery load, and without proper design, they may deform rapidly. Finite element analysis may be necessary to ensure effective vibration control before installation. Shock loading significantly influences rubber mount deformation, as deformation extent relates to the applied load. Shock loads can be particularly harmful, affecting general vibrations. If a device or mount can withstand these shock loads, it is more likely to endure longer under mechanical vibrations.
Rubber isolators, crucial for vibration absorption, typically combine springs and rubber. Both components contribute to dampening vibrations, enhancing performance. They are manufactured using various methods, like molding and extrusion. To boost isolator strength and performance, additives such as sulfur, urethane, peroxides, metallic oxides, and acetoxy silane may be added, depending on specific applications and manufacturer requirements.
This section will explore the concept of damping, including the different forms it can take. Additionally, it will cover the various methods used for vibration damping.
Damping involves minimizing or removing undesired oscillations or vibrations from a system. This can be achieved using methods such as overdamping, underdamping, and critical damping.
Light damping is characterized by oscillations that decay slowly over time rather than decreasing in a linear or exponential manner until they reach a minimal amplitude. An example of light damping can be seen in a child playing on a swing or a pendulum. Over time, the swing's amplitude diminishes gradually until it eventually comes to a stop. This effect is illustrated in the displacement-time graph provided below.
Heavy damping results in oscillations taking a longer period to settle back to the equilibrium position. An example of a heavily damped system is a door that gradually closes rather than slamming shut, which helps avoid potential damage. The graph below demonstrates the gradual return to equilibrium observed in heavily damped systems.
In a critically damped system, the oscillator returns to its equilibrium position as swiftly as possible without oscillating. A typical example is a car's suspension system navigating over uneven terrain; if the system is critically damped, it will stabilize and return to its normal position quickly, minimizing the time spent in motion after hitting a bump.
The following graph demonstrates the behavior of a critically damped system over time.
Vibration damping involves absorbing kinetic energy from various sources of vibrations, including noise, mechanical oscillations, and alternating currents, to decrease the overall energy generated by a system.
There are several methods of vibration damping, including:
This damping method involves placing a cushioning pad between moving or vibrating parts, such as metal plates. The pad adjusts to the movement of these parts and absorbs the vibrations, which are then slowly dissipated as heat. This simple yet effective technique helps in protecting materials and preventing damage.
Constrained damping utilizes viscoelastic materials like Sorbothane to manage vibrations within systems. It operates similarly to unconstrained damping, where the material is positioned between components. However, constrained damping is employed in scenarios requiring more precise vibration control and greater attention to detail.
This method of vibration damping employs targeted control techniques to manage vibrations more precisely. Sorbothane is commonly used in this approach to address specific wavelength ranges that could cause damage. Tuned viscoelastic damping is frequently highlighted as a highly effective means of managing vibrations within specific frequency ranges.
Vibration isolation involves separating machinery from the primary source of vibrations. When vibrations are excessively strong, it is often necessary to isolate systems from these high levels of vibrations to prevent potential damage and reduce noise. To achieve this separation, vibration isolators are employed. These devices are positioned between the vibration source and the components that need protection.
Vibration isolation is categorized into the following types:
Passive vibration isolation systems typically consist of springs, masses, and damping materials. Mechanical springs and rubber pads are common examples of components used in this passive control method. The combination of spring and mass establishes a natural frequency, which is influenced by damping. During vibrations, energy is transferred at this natural frequency, and damping helps to minimize the amplification of these vibrations at the natural frequency.
Active vibration isolation systems, similar to many other active control systems, incorporate electronic components such as circuits, feedback mechanisms, controllers, sensors, actuators, and springs. Typically, these systems utilize processor-based actuators for precise control. Vibrations are detected and transmitted to the control system, which processes the input and sends corrective signals to an electromagnetic actuator. This setup allows for greater accuracy compared to passive isolation and prevents resonance issues. The CAD model of an active vibration isolation system is illustrated in the image below.
Considerations for installing vibration isolators include:
Vibration isolators are widely used in industries to protect equipment such as:
This section will explore the different categories of vibration absorbers and highlight the most commonly used types.
The following are some of the most frequently utilized types of vibration absorbers.
An air spring consists of air enclosed within a fabric and rubber envelope, often shaped like a bellows. Designed to enhance vehicle comfort, air springs adjust the vehicle’s height, lowering it at high speeds and raising it when driving on uneven terrain. They offer an effective stroke-to-compressed-height ratio, especially compared to air cylinders. Due to their adaptability, air springs are suitable for various vibration isolation applications and can work with different actuation mediums such as water, air, and nitrogen.
Bushings are vibration isolators designed to cushion the interface between two components, effectively absorbing vibrations at the contact surfaces. These inserts come in various metals, including stainless steel, brass, copper, bronze, and plated options. Typically, the steel used is case-hardened and may feature end serrations for improved grip in torsional applications. The outer bushing often has a centerless ground diameter and is press-fitted into the receiving bore. The choice of elastomer for the bushing is based on the environmental conditions of the application, such as exposure to oils, ozone, and extreme temperatures.
The diagram below illustrates the principle of vibration absorption using bushings.
A cam follower is a mechanical component that tracks the motion of a camshaft. It helps minimize vibrations caused by high-speed cam movement and aids in identifying any misalignments that might occur on the camshaft. Additionally, cam followers play a role in reducing vehicle skidding.
Dashpots are vibration-damping devices that utilize fluid to generate resistance. Commonly found in small devices and instruments, they are extensively employed in manufacturing industries for precision applications.
A helical isolator is a type of multidirectional wire rope assembly engineered to absorb both shock and vibration. These isolators are often utilized to protect sensitive or fragile materials during transport, especially in challenging weather or environmental conditions.
Rubber pads are also known as anti-vibration pads or vibration isolators are rubber materials that are used to absorb vibrations in materials by placing them between materials or moving parts. In some instances, these pads are made of ribbed patterns so that they avoid slippage of materials on their surfaces. Rubber pads can be grouped into many types based on the pattern formed and the common types include the KHL. KH, KHS, RHS, etc.
Shock absorbers are components designed to absorb vibrations and impacts, primarily found in vehicles.
Vibration absorbers are classified into two primary categories: passive and active absorbers.
Active vibration absorbers operate using electrical power and consist of electronic components such as switches, sensors, actuators, and controllers. These devices detect the frequencies and forces impacting the system and, based on their programming, respond by absorbing or eliminating unwanted noise.
Passive vibration absorbers operate without active components like switches, electrical circuits, or sensors. They typically consist of rubber mounts and mechanical springs designed to absorb energy. Common types of passive absorbers made from rubber include base isolators, pads, and elastomers. These materials, such as dense cork foam, are frequently used to isolate vibrations from machinery, home appliances, and vehicles. They are particularly effective for managing medium to high-frequency noise and vibrations in heavy machinery. Passive absorbers generally have a natural frequency range between 3 and 40 Hertz.
Vibration absorbers are highly useful in various mechanical systems, helping to prevent damage and reduce wear and tear on materials. They are generally cost-effective, making it advisable to use them in equipment subjected to vibrations and shaking. Below is a list of some common applications for vibration absorbers.
A machine tool, such as a milling machine, lathe, grinder, or drilling machine, operates using power to shape, drill, or finish materials. These tools generate significant vibrations due to their rotating and moving components, including spindles, gears, motors, and accelerometers. Without adequate vibration absorption, these machines could potentially cause accidents or damage. The diagram below illustrates the parts of a lathe machine that are subject to high levels of vibration.
Overhead power transmission lines are electric cables suspended from poles or towers. These lines can experience vibrations due to various factors, including weather conditions like wind, storms, and rain, as well as the movement of electrical charge. The vibrations may sometimes be audible, resulting from the discharge of energy when the electric field strength on the conductors exceeds the breakdown strength of the surrounding air.
Torsional vibration in engines occurs due to the combined effect of angular oscillations, primarily resulting from components like the gearbox, crankshaft, and propeller shaft. To counteract these vibrations and ensure smoother operation, vibration absorbers such as engine mounts, rubber bumpers, and transmission mounts are employed. Without these absorbers, engines would be significantly less comfortable and practical to use.
Rubber bumpers, also referred to as rubber mounts, are designed to absorb vibrations from machinery and equipment. They protect equipment by damping vibrations and typically come in various shapes, with the most common being circular with a central hole. Some bumpers feature adhesive on one side for easy attachment to surfaces. These bumpers are widely used in applications such as between metal surfaces on doors and between floors and equipment. The selection of a rubber bumper depends on factors like environmental conditions, material type, equipment weight, and durability. For environments with moisture, silicon bumpers are recommended due to their water resistance, while nitrile bumpers are ideal for oily environments as they resist chemical reactions.
Engine mounts are vibration absorbers that are used to hold the engine together. They are made of rubber because rubber absorbs impact and vibrations. They are put between metals to avoid wear and tear between them. Some engine mounts are filled with liquid inside to enhance strength and in case they wear out, the liquid will start to leak. If they start leaking, it means maintenance or replacement should be done to them.
Similar to engine mounts, transmission mounts are designed to support and secure a vehicle's transmission system. They typically feature a metal plate for durability and a rubber bushing to absorb vibrations produced by the transmission during operation. The image below displays a basic transmission mount commonly used in vehicles.
Pillow blocks consist of an oil-resistant neoprene flexing medium combined with a continuously lubricated sleeve bearing, all housed in a welded steel mounting bracket that is stamped and coated with durable zinc trivalent plating. These pillow blocks can be used in various applications to:
This shear mount made of rubber has a dual function: it minimizes noise and vibration transmission and supports precise machine leveling. Vibro-leveler mounts include:
Vibro-levelers feature a straightforward design and are generally built to be durable. They include a stud fixed to the inner cylinder and are insulated with rubber that is mechanically bonded.
Footbridges often have slender designs, making them susceptible to damage from wind or vibrations caused by pedestrians. To prevent issues such as shaking or resonance-induced damage, these structures typically incorporate vibration absorbers to mitigate such effects.
Machines with rotating shafts, such as pumps and generators, generate vibrations that can impact other components or the surfaces they rest on, such as tables, floors, or bases. To address and mitigate these potential damages, vibration absorbers are installed to reduce or eliminate these disruptive effects.
Several factors should be considered when choosing a vibration absorber, including:
The size of the machine affects the vibration absorption requirements. Larger machines may need multiple mounts to handle vibrations effectively, while smaller machinery might only require a single mount to manage all vibrations. It is important to consider the weight of the equipment as a key factor before sourcing vibration absorbers.
Understanding the installation environment for a vibration absorber is crucial, as different materials respond differently to various conditions. For instance, absorbers designed for laboratory settings differ from those used in industrial applications. Some absorbers, intended for indoor use, may deteriorate when exposed to UV rays, compromising their effectiveness. Many rubber-based products, such as rubber pads and bumpers, are not resistant to chemicals and can be prone to damage.
Understanding the nature of vibrations is essential. Key aspects include analyzing the frequency, amplitude, and direction of the vibrations. To measure these parameters accurately, tools like accelerometers are used, and it's recommended to consult a specialist for precise data. The amplitude's magnitude will indicate whether vibration isolation is needed. Additionally, knowing the vibration’s direction helps in positioning absorbers correctly. Incorrectly identifying the direction may result in ineffective vibration control, even if appropriate mounts are utilized.
Similar to other mechanical systems, vibration absorbers will need maintenance over time due to wear and tear. Additionally, expenses related to shipping, site surveys, and installation should also be factored into the overall cost.
Considerations should address questions such as: What will the maintenance costs be for the system with the chosen absorber? How straightforward is the replacement process for this absorber? Are there trained technicians available to service and maintain both the absorber and the overall system?
This considers how the system will handle modifications if needed. An optimal system should offer enough flexibility to accommodate changes in absorber installation. However, if the absorber is designed perfectly, flexibility may not be a major concern.
Determining which services or parts will interact is crucial for choosing the correct absorber for specific vibrations. Without detailed information about these contact points, there's a risk of causing damage to the system. Additionally, understanding the nature of these contact surfaces can help predict the lifespan and effectiveness of the absorber.
The lifespan of absorbers is influenced by a variety of factors, as outlined earlier. This is closely tied to cost considerations because typically, absorbers of higher quality are more durable and have a longer service life, assuming the system is well-designed.
It's crucial to understand the load that will be placed on the absorber before making a purchase. Heavier loads require more robust absorbers, while lighter loads can be managed with less substantial ones.
A vibration absorber is a single degree of freedom (DOF) spring-mass system that eliminates or reduces the vibration of a harmonically excited system such as the rotation of engines, motors, generators, belts, etc. to create a comfortable and safe environment. In selecting a vibration absorber for a particular use, it is critical to understand the type and application of the different vibration absorbers.
Molding is a manufacturing process that uses a mold - the latter being a solid container used to give shape to a piece of material. It is a forming process. The form is transferred from the mold to the material by...
A gas spring is a hydro-pneumatic element that stores potential energy by compressing gas contained inside an enclosed cylinder sealed by a sliding piston. A gas spring does not rely on elastic deformation...
Rubber injection molding is when uncured rubber is transformed into a usable product by injecting raw rubber material into a mold cavity made of metal. The applied pressure produces a chemical reaction like...
Rubber molding is a process of transforming uncured rubber or an elastomer into a usable product by transferring, compressing, or injecting raw rubber material into a metal mold cavity...
There are several methods to perform rubber overmolding, and each method has its own unique advantages and disadvantages. The choice of method typically depends on the design and material requirements of the product being...
Silicone rubber molding is a method for shaping, forming, and fabricating silicone rubber parts and products using a heated mold. The process involves compressing or injecting silicone rubber into a mold...
A grommet edging is a flexible rubber or plastic strip that covers rough and sharp surfaces found in openings and edges of panel walls to protect the passing electrical cables, wires, and other sensitive components...