Aqueous Part Washers
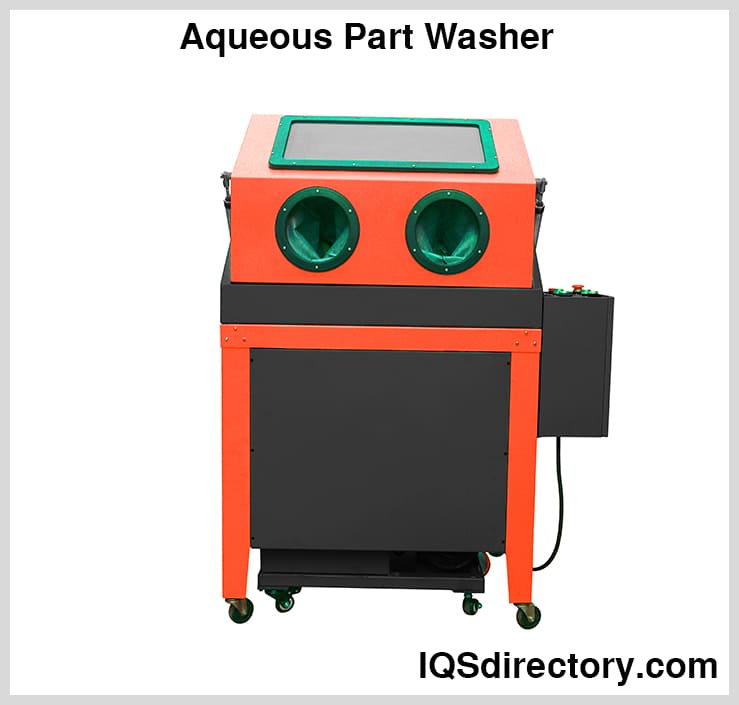
An aqueous part washer is an automated or semi-automated machine manufactured to clean, remove tough grease, and dry large or small parts before distribution or surface treatment. The washing is necessary since...
Please fill out the following form to submit a Request for Quote to any of the following companies listed on
Discover everything about wastewater evaporators available online. This comprehensive guide covers:
A wastewater evaporator functions by transforming water-based waste into vapor, effectively separating impurities and reducing the total volume of waste materials. This process plays a crucial role in efficient waste management.
The handling of wastewater falls under stringent regulations, ensuring careful oversight and management. Companies producing wastewater evaporators work closely with regulatory bodies to ensure the environmentally safe disposal of industrial waste materials.
A wastewater evaporator utilizes thermodynamics and mass transfer principles to eliminate water from waste materials. Thermodynamic evaporation involves heating the waste material sufficiently to vaporize water using various fuel sources.
Once water vaporizes, it is transferred as droplets via a blower without filtration.
Wastewater evaporation is an effective method for concentrating liquid waste and removing contaminants such as salts, heavy metals, and hazardous materials. Compared to solar evaporation ponds, which occupy large land areas and work slowly, wastewater evaporators are significantly more efficient.
Wastewater is introduced into the treatment tank from a holding tank in the required quantity.
The wastewater feed pump transfers wastewater into the wastewater evaporator, operating either manually with a toggle switch or automatically through an autofill system.
The wastewater evaporation process relies on heated steam generated by a heat exchanger, enhancing vaporization and concentration. Heat within the evaporator creates a uniform boil across the solution's surface.
As the temperature reaches optimal levels for waste concentration, the evaporator prompts the need for emptying.
The blower in a wastewater evaporator draws air into the evaporator tank to eliminate water vapors and aid in the heating process. In the unit below, the blower compartment is visible in the lower right corner.
Compressors play a crucial role in the vaporization process and can be categorized as positive displacement, centrifugal, or axial. Wastewater evaporators equipped with a compressor require an external steam source, such as a boiler or heater in the feed tank.
The mist eliminator, also known as a mist pad, removes contaminants from the process, which may include oils or other substances. Constructed from corrosion-resistant materials, these eliminators can be designed to be self-cleaning for enhanced efficiency.
The burner ignites within the combustion chamber, directing hot gases through a chimney into the evaporator tank. This process heats the wastewater to its boiling point.
Electrically powered units feature a heat exchanger located within the wastewater evaporator tank to generate heat for the wastewater.
Wastewater evaporators powered by oil operate similarly to gas models but use oil as their fuel source. The oil combusts within a combustion chamber, then travels through tubes in the heat exchanger before entering the chimney, where it mixes with air to heat the evaporation tank.
Steam heats the coils of the heat exchanger. Upon condensation, heat transfers to the wastewater and is discharged, releasing vapors through the mist eliminator.
One of the primary applications of wastewater evaporators is the removal of oily waste from water used in parts washers. However, this is just one of many uses for wastewater evaporators, which are widely employed across various industries ranging from food processing to power generation.
Wastewater from metal finishing processes, such as tumbling, stamping, die casting, and polishing, poses challenges due to the presence of difficult-to-treat chelating agents. Instead of costly chemical treatments or filtration, some companies opt to have this wastewater hauled away, which can be prohibitively expensive. While wastewater evaporators do not entirely eliminate these challenges, they significantly reduce disposal costs.
Wastewater evaporators find numerous applications in the food industry. While wastewater from food production is non-toxic and biodegradable, it does contain biochemical oxygen demand (BOD) and solids from various processed foods. Activities like vegetable washing and animal slaughter introduce dissolved organic materials that must be eliminated from water before it can be reused or discharged.
The pharmaceutical industry demands clean water as chemists require pure water for drug manufacturing processes. Regulatory agencies establish stringent purity standards for water used in drug production. Contaminants generated during pharmaceutical manufacturing are hazardous and pose risks, underscoring the necessity of wastewater evaporation equipment.
Water plays a crucial role in paint manufacturing, used in both water-based paints and for cooling ball mills in oil-based paint production. Wastewater from paint production typically contains elevated levels of alkaline substances from cleaning processes and cooling towers. Although the volume of wastewater from paint production is small, it is highly concentrated with pollutants.
Water-based parts cleaning processes produce wastewater that appears brownish-gray or clear with a soapy appearance, containing settled solids and oil residues. Parts used in automotive and other manufacturing applications undergo washing before assembly, and the water used in this process contains pollutants that require removal.
Wastewater in the graphic arts industry originates from processes involving offset and flexo plates, ink, and cylinder etchings.
Machine coolants are essential for cooling tools and parts during machining processes to prevent overheating. Coolants include water-soluble oils, water-soluble synthetics, and pure oils. During normal operations, coolant continuously circulates through the machinery until it requires cleaning. Evaporators are then used to evaporate the water, leaving metals and oil in the evaporator tank.
Landfills contain dissolved organic and inorganic substances, heavy metals, and other compounds. The amount of leachate, which is liquid draining from or through the landfill, depends on the landfill type and age. Leachate wastewater poses significant environmental risks and requires specialized treatment. Treatment methods vary based on location, and wastewater evaporators are particularly suitable for this application due to their ability to adapt to varying wastewater compositions.
The purpose of vaporization is to convert a liquid into vapor. Unlike gas, vapor originates from a liquid and undergoes transformation into a vapor state. When a liquid transforms into vapor below its boiling point, this process is known as evaporation.
Factors influencing evaporation include:
Boiler blow-off evaporators do not collect or remove suspended solids. Instead, solids are dissolved as vapor at 212°F and released into the atmosphere.
Boiling water evaporation involves heating water to its boiling point and releasing the resulting steam through an exhaust pipe. This method does not effectively remove dried solids.
A forced-air evaporator includes a feed pump, an evaporation tank equipped with a heater, a circulation pump, blower, mixing tube, mist eliminator, and air outlet. Wastewater is pumped into the evaporator tank and heated. The air and wastewater mixture flows through the evaporator tank, passes through the mist eliminator, and exits via the air outlet.
In a heat exchanger, high-temperature oil from an oil-filled coil is pumped into a coil inside a tank containing contaminated waste.
Leachate wastewater evaporators are engineered to decrease leachate volume by extracting water from the leachate and expelling the purified vapors, while retaining sludge and solids.
The liquid thermal oxidation method entails spraying liquid waste under pressure near a flame. At 1250°F, all volatile organic compounds (VOCs) are oxidized and dissolved, while solids are transformed into ash. Contaminants are converted into inorganic ash.
Water placed in an outdoor pond naturally evaporates due to solar heat and wind. Natural evaporation requires significant space.
The steam tube evaporator operates on a principle similar to that of the boiling tank evaporator. The key difference lies in passing heated exhaust gases through the wastewater, enhancing heat transfer efficiency.
Vacuum wastewater evaporators reduce the pressure inside the evaporation tank below atmospheric pressure, thereby lowering the boiling point of the wastewater. This method eliminates the requirement for high heat and can handle liquids with elevated boiling points. Vacuum wastewater evaporators are recognized as a safe and efficient means of removing contaminants.
Despite various methods for wastewater disposal, wastewater evaporators are steadily gaining popularity due to their environmental friendliness and effectiveness in removing salts, heavy metals, and hazardous materials during water purification processes.
Advancements in technology have heightened the demand for proper wastewater disposal, particularly concerning water-mixed chemicals used in manufacturing sophisticated instruments.
Energy Efficiency: Wastewater evaporators operate on a 1:1 ratio, meaning the energy used to extract water equals the water extracted. Efficiency can be further enhanced by employing multiple effects, such as utilizing steam from one operation for another.
Zero Liquid Discharge: Stringent regulations at national, state, and local levels necessitate minimal industrial wastewater discharge. Wastewater evaporators can achieve zero liquid discharge, exceeding regulatory requirements.
Total Dissolved Solids (TDS): Wastewater processed by evaporators typically yields TDS levels below 10 mg/L, often as low as 2 mg/L. This purity allows the treated water to be reused in manufacturing processes.
Cost Effectiveness: Compared to chemical precipitation systems processing 395 liters per minute (L/m), wastewater evaporators are more efficient at 190 L/m, offering significant cost savings.
Flexibility: Wastewater evaporators are adaptable to diverse industry needs and wastewater conditions. They can be customized to handle various contaminants effectively.
Volume Reduction: A key advantage of wastewater evaporators is their capability to drastically reduce waste volume by removing moisture from materials. This addresses challenges in waste management by minimizing required disposal space.
Integration: Wastewater evaporators can operate independently or integrate seamlessly into existing systems, enhancing operational efficiency and reducing costs in wastewater disposal processes.
Natural Evaporation: Natural evaporation has traditionally been employed to remove water from ponds, leaving hazardous materials behind. While environmentally sound, this method is slow and can potentially contaminate the surrounding environment.
Sewage Discharge: Historically, dirty water was disposed of directly into rivers and streams without full awareness of the environmental consequences. As environmental awareness has grown, regulations now strictly govern the discharge of wastewater into sewers and public waters.
Dumping: Still practiced today, waste disposal involves sending waste to landfills or regulated disposal sites. This method is costly and overlooks the fact that over 70% of waste contains water that could be removed to reduce waste volume.
Filtration: Advances in technology have led to the development of highly refined filters capable of removing even minute particulates. While effective for water purification, filtration systems require constant monitoring and can be labor-intensive.
Reverse Osmosis (RO): Reverse osmosis, an early method for removing contaminants from water, forces wastewater through a semi-permeable membrane. This process traps large particles while allowing small ones to pass through. However, managing the water left behind by the RO process remains a challenge.
Chemical Treatment: Chemical methods for wastewater treatment have been used for over 70 years but have become less effective as regulations for clean water have tightened. Chemical treatments may not safely remove all contaminants and can leave residual chemicals.
Evaporation: Wastewater evaporation is a straightforward, efficient, and cost-effective solution. It requires minimal installation time and can be operational immediately. Manufacturers' engineers assess a company's wastewater samples and program wastewater evaporators to suit specific applications.
Legislation governing wastewater evaporators is shaped by clean water regulations. The initial Clean Water Act (CWA) of 1972, originally the Federal Water Pollution Control Act, entrusted oversight to the Environmental Protection Agency (EPA).
The CWA's objective is to cease untreated water discharge from urban and industrial sources. Over time, EPA jurisdiction expanded beyond cities and factories to encompass sectors like agriculture, logging, paper production, and fertilizer manufacturing.
Administered by the EPA, NPDES issues permits dictating allowable water purity levels from wastewater treatment plants. These permits authorize facilities to release regulated pollutant amounts under strict conditions.
States seeking authority over wastewater management must apply to the EPA through NPDES for regulatory control. Approval necessitates submitting a program report outlining state wastewater management initiatives.
Various states have enacted legislation imposing specific requirements on wastewater processing, varying in stringency.
A wastewater evaporator functions by converting water in water-based waste into vapor, thereby leaving contaminants behind. Utilizing principles of thermodynamics and mass transfer, it efficiently removes water from waste materials. Wastewater evaporators are pivotal in addressing challenges such as removing oily waste from parts washer water, aligning operations with evolving clean water regulations.
An aqueous part washer is an automated or semi-automated machine manufactured to clean, remove tough grease, and dry large or small parts before distribution or surface treatment. The washing is necessary since...
Automated parts washers are mechanical devices designed to efficiently remove grit, oil, grime, dirt, paint and other contaminating substances from parts with minimum manual supervision. These substances are removed...
A parts cleaner is a cleaning device that uses various types of solvents, cleaning agents, and processes to remove grease, grime, and contaminating materials from manufactured parts prior to shipment or movement for further processing...
A parts washer is a mechanical device designed to remove grit, grime, oil, miscellaneous debris, dirt, paint, and other contaminating substances from parts in preparation for their use in assembly operations, packaging, or coating...
Parts washers are designed for cleaning, degreasing of equipment, and drying of mass quantities of small or large parts in preparation for surface treatment, assembly, inspection, or shipment...
Industries worldwide utilize abrasive blasting for various purposes, including cleaning rust and oil, removing surface coatings like paint and pollutants, preparing surfaces for paint and coatings, reinforcing metal surfaces and...
Deburring is a secondary operation of a machining process that enhances the final quality of the product by removing raised edges and unwanted pieces of material, known as burrs, left by the initial...
Finishing machines are machines used for metal finishing, which is the last stage of the metal fabrication process; the stage encompasses the use of machines in finishing the metal surface...
Sandblast cabinets include systems or machinery and components for projecting blast media against a part‘s surface to abrade, clean, or modify the surface. Sand, abrasive, metal shot, and other blast media are driven or propelled using pressurized water, compressed air, or a blast wheel...
Sandblasting equipment includes systems or machinery, and components for projecting blast media against a part‘s surface to abrade, clean, or modify the surface. Sand, abrasive, metal shot, and other blast media are driven or propelled using pressurized water, compressed air, or a blast wheel...
Shot peening equipment includes systems or machinery and components for projecting shot peening media against a part‘s surface to modify the surface or surface engineer the part...
A tumbling machine is a durable deburring and metal-polishing machine designed for finishing large parts or batches of smaller parts. A tumbling machine is also known as a barreling machine or a mass-finishing...
An ultrasonic cleaner is a type of sonic cleaner or sonic cleaning machine that uses cavitation to remove unwanted material. The cleaning effect is created by the compression and refraction of a cleaning medium. Miniscule vibrations propagate throughout the...
Ultrasonic cleaning is a type of cleaning process which uses cavitation induced by alternating compression and rarefaction cycles at ultrasonic frequencies. Ultrasonic frequencies are sound waves vibrating at 20 kHz or higher...
Vibratory tumbler is the equipment used in a vibratory finishing process, one of the most common methods in mass finishing. But how does a vibratory tumbler work...