Wire Baskets
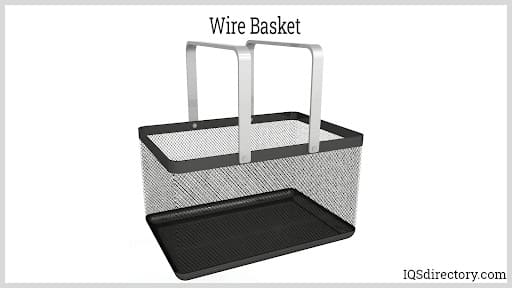
Wire baskets are made from a series of wires that are woven together or welded to form a shape of a basket. They can also be defined as containers that are made by use of an openwork pattern of metal...
Please fill out the following form to submit a Request for Quote to any of the following companies listed on
Here is the most complete guide on the internet about
You will learn:
This segment explores the concept of wire displays, detailing the processes of wire shaping, as well as the various techniques employed in their formation.
Wire shaping is a detailed process that accommodates a range of sizes, forms, and surface finishes. The creation of functional structures through wire bending and molding is known as custom wire forming.
Wires are crafted using low-carbon, medium-carbon, and high-carbon steels. Other suitable materials include stainless steel, copper, aluminum, brass, and a variety of alloyed metals.
The ultimate wire shapes can be modified with paint, plating, or coatings based on client specifications. Tools like the CFR Ring Forming and Welding Machine, BUW Butt Welder, K-70 Welder, and the CFM with a capacity for 17 mm wire are used in this process. CNC wire bending machines are prevalent in industries such as retail, manufacturing, construction, automotive, and OEM for shaping stainless steel and aluminum wire from sheet materials.
Skyscrapers owe their existence to rebar, produced by wire forming. Electric lamps need wire-made filaments. Basic furniture like beds and chairs relies on springs formed with wire. Additionally, wire displays are available in diverse sizes and alloys, ideal for merchants and newspaper vendors, aimed to meet specific display requirements.
Various wire rack display products, such as stainless steel wire shelves, sale display stands, wire baskets, wire shelving, and wire grid panels, can be tailored and designed using advanced computerized 2D and 3D wire forming and butt welding machines.
The wire forming process comprises the following stages:
The CAD design outlines the gauge, diameter, and type of wire for the forming procedure. Steel and stainless steel are preferred for robust and durable components, while more lightweight applications use materials like aluminum and copper. Wire is created from low, medium, and high-carbon steels, and alloyed metals like stainless steel, aluminum, and brass.
Wire, stored in coils, needs to be straightened before processing. Straightening eliminates stress irregularities from storage, done by machine rolling. Unchecked imperfections at this stage can affect the final wire form.
Forming wire involves applying force to alter its shape per specific needs, producing a variety of shapes and configurations. Force is applied using manual methods or automated equipment with dies and cutting tools. For mass production, CNC machines and fourslide machines are used.
Finishing might not always be necessary, depending on the design or wire product type. Some products might require additional procedures like cutting, grooving, heading, coining, or swaging. A critical part of finishing is removing burrs and sharp edges to ensure safety and functionality.
Wire shaping employs various techniques tailored to create distinct shapes, patterns, or configurations. These methods, similar to those in traditional part manufacturing, adapt to the unique requirements of wire forming. The techniques include:
Manual wire shaping, using hand levers and spindles, represents one of the oldest wire manufacturing methods. This includes manual machines with drawn or rotary dies, using gears to amplify bending force.
Coiling, or spring wire shaping, involves winding wire around a metal blank. It is also used to construct electrical coils by winding conductive wire evenly around a ferromagnetic core. Coil winding varies depending on the intended result. Electrical coils demand more precision and numerous windings compared to springs.
This cost-effective method produces wire components in flat, round, or various shapes, allowing features like undercuts, knurls, points, chamfers, grooves, surface finishes, collars, and threads. Once hardened, rounded, and prefinished, roll-formed wire parts gain increased strength.
The wire bending process molds wire into countless configurations for any application. Diameters from 0.016 to 0.635 inches (0.4 to 16 mm) can be easily produced. As bending occurs before cutting, no scraps or waste are generated, negating additional finishing needs.
Fourslide forming or stamping incorporates cams and uses a horizontal stamping press method. The machine includes shafts, an electric motor, a die, a press, and sliding tools, besides the cams. Fourslide tools shape the wire from four sides during the process.
The cam mechanism orchestrates the movement of four tools, executing vertical actions like punching and horizontal motions in multiple directions. The fourslide method offers a versatile alternative to conventional stamping. It efficiently creates complex small forms by shaping metal strips from four directions at once, unlike unidirectional traditional stamping.
A hydraulic wire forming machine uses shaping rollers driven by a hydraulic motor. It is configured to the desired shape using a servo motor and CNC programming. Post-formation, wire shapes are automatically ejected.
In pneumatic wire forming, the wire feeds into the straightening machine, adopts the desired configuration, and is cut to length using a pneumatic cutting procedure.
CNC wire bending machines, whether pneumatic or hydraulic, offer fast, efficient manufacturing. Capable of bending rebar to 180 degrees with single or double wire use, the CNC machine straightens the bar before bending.
CNC machines boast high accuracy, cutting wire to exact dimensions, albeit slower than other techniques. They require minimal tooling, ideal for low-volume production or prototyping. Different wire types formable include music, hard-drawn, basic or coated metals, 300 series stainless steel, brass, and beryllium copper, with diameters from 0.008 to 0.250 inches (0.0203 to 6.35 mm).
This chapter will explore the different types of wire displays and the materials employed in their construction.
The different categories of wire displays are as follows:
Floor wire displays are units positioned on the ground that offer shelving space. They come in various shapes and designs, including the following:
This wire display features five shelving racks and can be used to store a variety of items, such as consumables in retail settings, tools, or books.
This is a wire rack that is used to store wine bottles. The display shelves are made out of wood, and the vertical supporting bars are made out of steel.
This type of wire display unit is designed specifically for hanging cables. It features hooks at the top for suspending the cables securely.
A 4-shelf wire display includes four shelving racks, providing versatile storage for a wide range of items, from snacks to tools.
These wire displays feature built-in hooks along the top and down the sides, allowing for the hanging of bags and other items.
This wire display unit is constructed entirely from wire and features six storage racks. Designed for snack storage, the six-tier tabletop wire rack also effectively organizes pamphlets, maps, and brochures, offering a combination of durability and lightweight design.
These wire display units are wall-mounted and ideal for storing items such as chocolates.
These display units are typically placed on countertops rather than the floor. They are designed to hang various snack items, providing easy access and visibility.
Metal grid racks are lightweight yet made from durable steel due to the manufacturing process used. The wire bending technique allows these stands to hold various sizes of tabloid newspapers and magazines, making it easy for customers to view the headlines. These metal grid display racks are well-suited for displaying literature, making them ideal for use by newspaper vendors in street settings, lobbies, and convenience stores. The newspaper wire display racks measure 37 inches in height, 16 inches in width, and 15 inches in depth (94 x 41.6 x 38.1 cm).
Wire Point of Purchase (POP) displays, also referred to as wire Point of Sale (POS) displays, are commonly used in retail settings to highlight fast-selling products. These displays enhance the visibility of goods, and a well-crafted wire POP display can boost sales for retail business owners. Many companies provide branded wire POP displays to enhance brand recognition and emphasize the uniqueness of their products.
Wire point-of-purchase displays are designed to showcase lightweight and medium-weight consumer goods, including food, snacks, compact discs, and gift cards. These displays feature adjustable shelves spaced at 3-inch (7.6 cm) intervals. The wire shelves can be angled forward or set in a balanced position, measuring 18 inches wide by 15 inches deep (45.7 x 38.1 cm). The overall dimensions of a display stand with five shelves, excluding any lettering, can reach 50 inches in height, 20 inches in width, and 16 inches in depth (127 x 50.8 x 40.6 cm).
Wire counter brochure displays, also known as wire brochure displays, are perfect for showcasing reading materials such as brochures and pamphlets in retail and commercial settings. Designed for use at checkout counters, these displays feature multiple pockets to hold a variety of periodicals. They help businesses distribute important information to customers, attract new clientele, and keep existing customers engaged and satisfied.
These displays are highly durable, with wire-forming technology ensuring their longevity despite changes in the retail environment. Merchandisers often need to be innovative and efficient to maximize the use of counter space. Counter displays play a crucial role in the success of a business, offering various types that can be beneficial. Placing products near the cash register can entice shoppers to examine them while waiting for their purchases to be packed and payment to be processed.
Establishing a strong brand presence is essential for many organizations, especially those new to the market. Counter brochure displays are particularly valuable in retail settings, such as bookstores and convenience stores, where they help showcase catalogs, bulletins, and brochures. These displays often feature pockets to organize materials and may include rotating elements for an elegant, eye-catching look. This design allows customers to easily browse and select items, potentially increasing transaction conversion rates. A standard 16-pocket revolving counter display typically measures 10 inches wide by 21 inches tall (25.4 x 53.3 cm).
Each wire grid display features a panel equipped with multiple hooks and shelves. These displays offer a cost-effective, durable, and versatile solution for maximizing display space. They can be used to create both wall-mounted and freestanding display systems. Seasonal businesses, dollar stores, mall kiosks, tourist shops, and pop-up stores often use wire grid systems due to their ease of setup and takedown.
Wire grid displays are mounted to walls using 3-inch brackets and can be customized with various accessories such as hooks, shelves, shelf brackets, lights, waterfalls, and wire baskets. They are commonly used in shoe and clothing stores to showcase merchandise. A standard wire grid display system features 0.4-inch (1 cm) diameter wire arranged in 3-inch (7.6 cm) squares. For added stability, the wire is reinforced with double 0.4-inch wire on both sides. Panel sizes for these systems typically range from 12 inches by 70 inches (30.5 x 177.8 cm) to 24 inches by 97 inches (61 x 246.4 cm).
The materials used in the construction of wire displays include:
Stainless steel grade 304 is known for its excellent corrosion resistance and tensile strength of 621 MPa, making it suitable for environments with moderate corrosive elements or heavy load requirements. This high-quality material is durable and long-lasting, with a temperature range of up to 1500°F (815.5°C) to 2500°F (1371°C). Additionally, stainless steel grade 304 is non-magnetic, which can be a crucial feature for certain applications.
Grade 316 stainless steel offers superior corrosion resistance, particularly against chloride environments, and can handle exceptionally heavy loads with a tensile strength of 579 MPa. It is suitable for use in temperatures up to 1400°F (760°C). Its ability to withstand harsh and highly corrosive conditions makes it a highly valuable material in demanding applications.
Grade 434 stainless steel is a ferritic alloy that is resistant to pitting and does not contain nickel, making it a more cost-effective option. Although it is limited to temperatures below 1500°F (815.5°C), which restricts its use in heat treatment applications, it offers excellent resistance to oxidation, corrosion, and pitting. This makes it well-suited for manufacturing industrial baskets and other similar applications.
Galvanized wire is carbon steel wire coated with zinc through electroplating or hot-dipping processes. This coating makes it rust-resistant and highly durable, and it is available in various gauges. In the hot-dipping process, carbon steel wire is immersed in a zinc bath. As the wire cools after being removed from the bath, the zinc reacts with the air, forming a strong bond with the carbon steel.
The benefits of using galvanized wire include:
Comprehensive Shielding: Hot-dip galvanizing coats every surface of the steel it touches, ensuring that even the most inaccessible areas receive protection that other rust prevention methods might miss. This galvanization technique significantly enhances the steel's longevity, and its effectiveness can be improved over time.
Electrochemical Safeguarding: Galvanizing steel imparts cathodic protection through its coating. In the galvanization process, the metal undergoes microscopic changes that enhance its resilience. This means that small exposed areas are less prone to harm compared to those on components covered with natural materials, reducing the need for frequent maintenance or repairs.
Easy to Clean and Maintain: Galvanized materials are resistant to various metals, salts, and both corrosive and synthetic substances present in the environment. To maximize their durability, it's advisable to clean them annually.
Aesthetic Finish: Galvanized steel boasts a refined look due to its zinc oxide coating and sophisticated chemical treatment, resulting in a sleek and polished surface.
Extended Durability: Galvanized coatings typically last over 50 years in standard environments and between 20 to 25 years in more demanding public and waterfront conditions.
Bright Basic Wire (BBW) is a low carbon steel wire that features a shiny, smooth surface. It is cold-drawn to enhance its tensile strength and mechanical properties. This wire is versatile, allowing it to be bent, straightened, welded, and coated with epoxy, plastic, galvanized layers, or powder coatings. The BBW grades most frequently utilized in wire forming are 1008C and 1018C.
Steel is an alloy of iron and carbon, designed to enhance its strength and resistance to breakage. Due to its high tensile strength and affordability, steel is a key material in manufacturing. The fundamental metal in steel is iron, and its properties are shaped by the interaction between iron's various forms and its carbon content. Adding carbon and other alloying elements increases the hardness, strength, and durability of iron, which in its pure form is relatively soft and pliable.
Steel is renowned for its reliability due to its consistent and uniform quality. It benefits from superior quality control during manufacturing, high elasticity, and excellent ductility. Laboratory tests of different samples of the same steel type show much less variation in yield stress, ultimate strength, and elongation compared to materials like concrete and wood. Additionally, because steel is a genuinely uniform and elastic material, it aligns well with the assumptions used in structural analysis and design, resulting in precise and reliable outcomes.
Steel is prone to corrosion when exposed to air and moisture, necessitating regular coatings to prevent deterioration. This process can be costly and requires careful attention. Weathering steels are often used in stable design scenarios to mitigate these costs. Without proper maintenance, steel components can lose between 0.04 to 0.06 inches (1 to 1.5 mm) of thickness annually, potentially reducing their weight by up to 35% over their lifespan and compromising their ability to withstand external loads.
Copper (Cu) is a flexible, malleable metal with a reddish-orange color and excellent conductivity for both electricity and heat. Its ease of bending and shaping makes it ideal for producing wires. Over time, copper develops a green patina when exposed to the elements, which protects it against rust and corrosion.
Copper is highly valued for various electrical and thermal applications due to its heat resistance and high melting point. Its excellent thermal conductivity also makes it a popular choice for corrosion-resistant coatings.
Flexibility is required to provide a suitable form and dimension. The elasticity of copper is a component of its high degree of flexibility. Copper is widely utilized in electrical applications because it can be pounded or hammered into thin wires of any shape, size, or form to fit into any area.
Aluminum (Al) is the third most abundant metal on Earth, known for its softness, non-magnetic properties, and ductility. Extracted from bauxite, it appears in various forms, including over 270 different minerals. Key attributes of aluminum include its low density and resistance to corrosion. To enhance its strength and prevent distortion, aluminum is often alloyed with other metals. Common alloying elements include copper, zinc, magnesium, manganese, and silicon.
Aluminum is the most abundant metal in the Earth's crust, characterized by its softness, strength, light weight, ductility, and malleability. It offers excellent thermal and electrical conductivity and is resistant to corrosion. Additionally, aluminum can be fully recycled without losing its inherent properties and is considered very safe. However, it is not as strong as some other metals and tends to be more costly compared to steel of equivalent strength.
Brass is an alloy composed of 67% copper and 33% zinc. It combines the electrical and thermal conductivity of copper with the malleability of zinc. Compared to pure copper, brass offers enhanced corrosion resistance, making it suitable for various applications, including wire production. To improve properties such as hardness, strength, and appearance, some brass formulations include additional elements like antimony, arsenic, iron, and tin.
Brass is cost-effective and easier to work with compared to other metals. It is commonly used in casting for large-scale jewelry projects, where substantial amounts of metal are required. With proper anti-oxidation treatment, brass maintains a good level of shine. Additionally, brass is frequently utilized in jewelry repair due to its favorable properties.
However, brass can undergo color changes over time. Regular cleaning may lead to discoloration in brass jewelry, primarily due to its copper content, which affects the color.
Wire displays are used in a variety of applications, including:
Wire displays are an essential marketing asset that can enhance product visibility and encourage consumer interest, leading to higher sales. These displays offer a significant advantage by featuring multiple shelves, enabling the placement of various pamphlets or brochures. By using a wire display stand, business owners can organize different types of instructional materials on each shelf, targeting specific audiences more effectively.
A wire display stand featuring two pockets per column and four rows typically measures about 18 inches wide, 20 inches tall, and 14 inches deep (45.7 x 50.8 x 35.6 cm). These displays are often placed at checkout counters in retail stores, where customers are likely to grab additional items like candy bars, chocolate, or gum while waiting in line. Positioned strategically, these stands serve both as advertising tools and points of sale. Customers are drawn to displays with prominent branding, which increases the likelihood of them picking up a product just before leaving the store.
Wire display shelving is a common feature in the production of wire rack displays. These shelves are frequently used in retail merchandising, home organization, and commercial storage. Wire display shelves are favored by newspaper vendors and retail stores because they can support substantial weight, making them ideal for displaying a variety of newspapers, magazines, and other products.
Shelving is commonly utilized in retail settings to organize various products, such as snacks, confectioneries, and chocolates, into a single display for customer selection. Wire display shelves are easy to set up with minimal tools and can be quickly adjusted to change the spacing between shelves as storage needs evolve. Made from high-quality materials, these shelves are both durable and long-lasting.
During the construction of wire shelves, the wire rungs are reinforced with a central truss to support a specified weight capacity based on the intended use. Wire shelves come in various sizes, from as small as 8 inches wide by 8 inches deep (20.3 x 20.3 cm) to as large as 72 inches wide by 36 inches deep (182.9 x 91.4 cm). Wire shelving is versatile and offers numerous benefits, making it a popular choice for various applications. It is commonly used in every room of residential properties managed by property management companies.
Using a wire rack to create a folder counter in the laundry room for sorting purposes is one innovative way to address storage issues. Wire shelves are also commonly used in businesses for storing frequently rotated and inventoried items. An open shelf system allows for loading from the back and retrieving from the front, enhancing storage efficiency, visibility, and accessibility in stock rooms. Additionally, stainless steel wire shelves can be utilized in merchandising stands and point-of-sale displays to drive sales. They are also employed by office designers to organize and store important offline records, such as tax codes and employee information.
Wire display racks are an effective way for businesses to showcase informational materials about their products or services. Placing a wire rack display at the store entrance, inside the store, or on the counter allows customers to easily access leaflets and brochures. These materials can include marketing content or any essential information that the business owner deems important for customers to know.
Wire racks come in various designs, including rotating models that turn on a stand and stationary ones that require customers to navigate around to find what they need. The size of the wire rack display is typically based on the brochure sizes it accommodates, such as A4, A5, or DL. The height of the rack depends on the number of pockets and their dimensions. For example, a wire display rack with three standard pockets, each 1.25 inches (3.1 cm) deep, and a base diameter of approximately 2.2 inches (5.6 cm) can have a total height of about 7 inches (17.8 cm).
Wire shaping is a complex method that encompasses a wide range of dimensions, forms, and textures. The technique of creating a usable product by wire bending and shaping is known as custom wire forms. Low-carbon steel, medium-carbon steel, and high-carbon steel can all be used to make the wire, in addition to stainless steel, copper, aluminum brass, and a variety of other alloyed materials. It is essential to make the right choice of wire display and remain cognizant of the material and design best suited for you.
Wire baskets are made from a series of wires that are woven together or welded to form a shape of a basket. They can also be defined as containers that are made by use of an openwork pattern of metal...
Wire forming is a method for applying force to change the contour of wire by bending, swaging, piercing, chamfering, shearing, or other techniques. The various techniques for wire forming can produce any type of shape, form, or configuration...
A wire handle is attached to a bucket, pail, or other type of container to make it easy to lift the container and transport it. They are made of durable and sturdy metals capable of lifting several pounds...
A wire rack is a level wire form utilized to stock and exhibit a number of products, usually retail. The bottom surface on which such goods are stored is made of several latticed or interlaced metal strands...
Wire mesh is fabricated by the intertwining, weaving, or welding of wires of various thicknesses to create proportionally equal parallel rows and intersecting columns. Also known as wire fabric, wire cloth, or...
A coil spring is an elastic element made of metal or heavy plastic in the form of curls or ringlets of round wire or cord that is wrapped around a cylinder. The winding of a coil spring can be loose or tight in a helical shape depending on the application for which it is made...
Coil springs called compression springs can store mechanical energy when they are compressed. These open-coiled, helical springs provide resistance to compressive loading. When these springs are...
Contract manufacturing is a business model in which a company hires a contract manufacturer to produce its products or components of its products. It is a strategic action widely adopted by companies to save extensive resources and...
Extension springs are helical wound springs that are so closely coiled together to create initial tension in the coils. This initial tension creates resistance against the force applied to its ends for extension. The initial tension helps determine how closely and...
Hardware cloth is a woven mesh made by interlacing various sizes of wire to form a metal fabric that can be used for animal cages, fence material, strainers, and filtering screens. The differences between the various types of hardware cloth...
The phrase "wire mesh" describes two- or three-dimensional structures constructed of two or more metallic wires connected by various techniques. In a wide range of settings, wire mesh products are...
Springs are a flexible machine element that store mechanical energy when subjected to tensile, compressive, bending, or torsional forces. When the spring is deflected, it stores energy and at the same time exerts an opposing force...
A torsion spring is a mechanical device that stores and releases rotational energy. Each end of the torsion spring is connected to a mechanical component. As the spring is rotated around its axis on one end, the winding of the spring is tightened and stores potential energy...
Welded wire mesh is a series of wires that are welded where the individual wires cross. The openings of the mesh varies depending on the type of wire used and the function of the mesh. Regardless of size and wire, welded wire mesh is permanent and...
Wire cloth is a woven (or nonwoven) sheet or web material with a series of openings across the surface. Wire cloth is also known as: Metal Fabric or Metal Cloth; Wire Mesh, Metal Mesh, or Alloy Mesh...