Wire Baskets
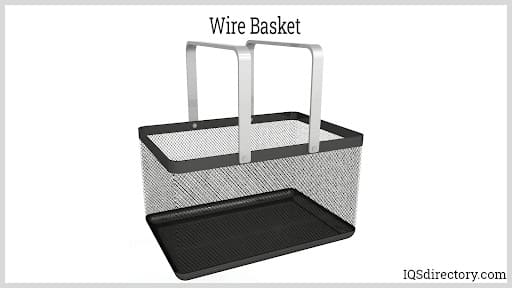
Wire baskets are made from a series of wires that are woven together or welded to form a shape of a basket. They can also be defined as containers that are made by use of an openwork pattern of metal...
Please fill out the following form to submit a Request for Quote to any of the following companies listed on
Here is the most complete guide on the internet to wire forming.
Wire forming refers to the process of reshaping wire by applying force through various techniques such as bending, swaging, piercing, chamfering, and shearing. Using these methods enables the creation of diverse shapes, configurations, and forms. The procedure commences with coiled wire, which is first straightened and then formed into the desired shape.
Commonly utilized metals in wire forming include steel, brass, stainless steel, copper, aluminum, along with assorted alloys. Wire diameters typically vary from 0.5 mm to 6.5 mm (1/64 inch to 0.25 inch) and can be molded into both two-dimensional and three-dimensional structures.
Wire forming equipment can range from basic handcraft tools to sophisticated CNC programmable machinery. Furthermore, the process includes options for finishing techniques like coating to protect and enhance the endurance of the final products against challenging environmental conditions.
Wire forming is an essential process in the metal fabrication and manufacturing industry, used to produce custom wire components, wire parts, and metal forms for a wide range of applications. There are various types of equipment used for wire forming, generally falling into manual or automatic categories. Manual machines include those operated by hand as well as semi-automatic models that, while electronic, require manual wire loading and adjustment. In modern industrial settings, automatic wire forming machines—often featuring advanced computer numerically controlled (CNC wire forming) programming—handle the entire production process without the need for direct human intervention, greatly increasing efficiency and precision. These automated systems are in high demand in high-volume production environments for creating precision wire forms, springs, fasteners, and intricate wire products.
Before wire forming can begin, the raw metal wire is processed using a wire drawing method to achieve the desired wire diameter, cross-section, and material properties for the final product. This critical wire drawing operation involves pulling the wire through a series of dies, which are typically funnel-shaped and crafted from hardened steel or carbide. As the wire passes through the die or multiple dies (known as multiple pass drawing), the pressure exerted by the die sides incrementally reduces the wire's diameter, while simultaneously increasing its tensile strength, hardness, material uniformity, and length. This tightly controlled process results in high-quality drawn wire suitable for subsequent forming, bending, coiling, or stamping operations.
Wire forming employs multiple specialized metal shaping processes, each tailored to produce specific shapes, wire patterns, custom wire forms, or complex configurations. While these methods overlap with other metal part manufacturing techniques, they have been optimized for continuous, high-precision wirework in industries such as electronics, automotive, medical device manufacturing, and custom metal fabrication.
The oldest method of wire forming utilizes manually operated wire bending machines, which use a hand lever and spindle for shaping. These manual machines may feature either draw or rotary dies and come equipped with high-torque gears that enhance the bending force applied to the steel wire or other metal, allowing operators to create simple or complex bends for prototypes and small batch production.
Coil or spring wire forming is fundamental to spring manufacturing, electrical coil production, and custom torsion applications. This method involves winding wire uniformly around a metal blank, mandrel, or ferromagnetic core. Electrical coil production requires high precision to achieve exact inductance and resistance, often using automated coiling machines for consistent results. The coiling process—critical in producing compression springs, extension springs, and torsion springs—varies based on end-use requirements such as load specifications and electrical properties.
Roll forming is a continuous, cost-effective manufacturing method for producing flat, round, or complex-shaped wire parts. Using sets of precisely aligned rollers, this process forms the wire into desired profiles, including wire undercuts, knurls, points, chamfers, grooves, specialized surface finishes, collars, and threads. Roll-formed wire components often exhibit increased tensile strength and springback resistance after hardening, along with smooth, rounded edges and prefinished surfaces, making them ideal for high-strength applications such as automotive clips, clamps, and metal brackets.
In the wire bending process, wire can be shaped into a wide variety of custom configurations—including 2D and 3D forms—to suit nearly any industrial or commercial application. Wire diameters ranging from 0.016 inches to 0.635 inches (0.4 mm to 16 mm) can be easily formed. Because the bends are made before the wire is cut, this process generates virtually no scrap or waste and eliminates the need for secondary finishing. Advanced wire bending equipment—from simple hand tools to sophisticated servo-driven CNC wire benders—deliver precision and speed for forming intricate assemblies, wire racks, display hooks, safety pins, and more.
Fourslide forming (also known as multi-slide stamping) utilizes a horizontal stamping press equipped with additional cams to create complex, multi-plane wire shapes. The fourslide machine includes shafts, an electric motor, a die, a press, and four sliding tools. The cams precisely control the movement of these sliding tools, enabling both vertical actions such as punching and horizontal wire manipulation in synchrony. This multi-directional forming capability provides immense versatility for creating intricate wire forms, terminals, electrical connectors, and clips for mass production.
The fourslide process offers a high-speed alternative to traditional stamping by rapidly producing small, complex forms with minimal material waste. Unlike conventional unidirectional stamping, it can shape metal strips or wires from four sides simultaneously, resulting in enhanced component uniformity and cost efficiency in high-volume manufacturing.
In a hydraulic wire forming machine, powerful hydraulic motors drive the shaping rollers and tooling assemblies. The machine, often integrated with a servo motor and CNC controls, is capable of high-torque forming of heavy-gauge wire and custom metal rods for demanding applications such as automotive suspension, construction reinforcement, or industrial enclosures. Once the programmed operation is complete, formed wire parts are automatically ejected for high productivity.
In the pneumatic wire forming process, wire is efficiently fed into a straightening machine, shaped to the desired form through pneumatic (compressed air-powered) mechanisms, and cut to length. This method is preferred in environments where rapid, repetitive forming of uniform wire parts is required, such as in the production of fasteners, hooks, hangers, and wire supports. Pneumatic systems offer high-speed throughput and low maintenance requirements.
CNC wire bending machines—available in pneumatic, hydraulic, and electric servo-driven configurations—provide unmatched efficiency and precision for rapid production of custom wire forms and prototypes. These automated machines are engineered to accurately bend and shape wire, including rebar, up to 180° in single or double wire operations and are capable of straightening the bar prior to the forming process for optimal results.
Advanced CNC wire forming machines feature programmable logic controls for exceptional accuracy and consistent, repeatable results, precisely cutting and shaping wire to exact dimensions. While sometimes slower than dedicated high-speed formers for large production runs, CNC systems excel in flexibility, ideal for low-volume production, prototyping, or manufacturing complex geometries that would otherwise require expensive tooling. Modern CNC benders can be programmed for a broad range of materials, including music wire, hard-drawn steel, galvanized or coated metals, 300 series stainless steel, brass, copper, and even exotic alloys such as titanium or beryllium copper. The supported diameter range typically spans 0.008 inches to 0.250 inches (0.0203 mm to 6.35 mm), covering most wire forming requirements for industrial and custom use.
The finishing of wire ends and formation of specialized geometries are critical steps in custom wire forming, directly impacting a part's fit, function, safety, and usability. Accurate end finishing and interior shaping often enhance the wire's performance in assembly operations or as a finished component in a larger system.
Wire ends can be cut straight with minimal burrs or finished with a clean, burr-free cut. Other options include quill or angle cut ends, where a single angle or opposing angles are applied for specific assembly and penetration applications.
Chamfered ends have a smooth, flat slope machined around the wire tip to remove sharp edges. This process is commonly used for safety-critical parts and to facilitate easier insertion into mating components.
Winging, also called swaging, involves placing the end of the wire in a special die that forms a wing shape. This configuration improves component retention or engagement for fasteners, clips, and specialty hardware.
In pierced swaging, wire ends are first swaged to create an expanded geometry, after which a hole is precisely punched in the center. This method is popular when producing wire lugs, electrical contacts, or custom fittings where mechanical or electrical connections are required.
For parts needing specialized connections or unique mounting requirements, a custom-shaped hole can be created. The end of the wire is trimmed by a die and then a shaped punch is used to form the desired opening.
In this process, specialized dies create a jagged or pointed end by cutting the wire on a precise diagonal. Chisel points are common in pins, stakes, and probes for easy penetration into other materials.
A lathe or automatic turning machine forms the end of the wire into a smooth, rounded ball—often used for decorative elements, electrical contacts, and mechanical detents.
In the groove end process, a controlled circumferential groove is machined or pressed into the wire's end, which can help with locking, assembly, or securing components in hardware systems.
Cold heading is a forging process in which the wire is subjected to a series of high-force blows that flatten or round the end. This results in robust button, carriage, or collar-head styles, often seen in screws, rivets, or fasteners where strong, uniform heads are required.
Adhering to precise wire forming tolerances is crucial in all metal fabrication and manufacturing processes—especially in wire forming where even small dimensional deviations can affect product fit, function, and quality. Wire forming tolerances are typically ±0.01 per bend or ±0.06 on an assembly. More stringent tolerances may require advanced CNC machines, specialized tool and die setups, additional secondary operations, and extensive engineering review. Meeting or exceeding industry standards for dimensional accuracy is vital in sectors like aerospace, automotive, medical device assembly, and custom metal part production, ensuring components function reliably as part of larger assemblies. See the chart below for standard wire diameter tolerance values across metric and imperial units.
Wire Diameter Tolerances | ||||||
---|---|---|---|---|---|---|
(mm) | (inch) | |||||
Wire Diameter | Up To But Excluding | Tolerance | Wire Diameter | Up To But Excluding | Tolerance | |
0.0254 | 0.203 | ±0.0051 | .001 | .008 | ±.0002 | |
0.203 | 0.376 | ±0.0076 | .008 | .015 | ±.0003 | |
0.376 | 0.813 | ±0.0100 | .015 | .032 | ±.0004 | |
0.813 | 1.220 | ±0.0127 | .032 | .048 | ±.005 | |
1.220 | 2.030 | ±0.0152 | .048 | .080 | ±.0006 | |
2.030 | 3.250 | ±0.0254 | .128 | .176 | ±.0010 | |
4.470 | 5.890 | ±0.0381 | .176 | .232 | ±.0015 | |
5.890 | 8.000 | ±0.0510 | .232 | .315 | ±.0020 | |
8.000 | 10.00 | ±0.0635 | .315 | .395 | ±.0025 | |
10.00 | 21.00 | ±0.0762 | .395 | .827 | ±.0030 |
When seeking a wire forming partner or sourcing custom wire forms, buyers should also consider factors such as material selection (e.g., stainless steel, carbon steel, copper, titanium), surface finishing, secondary processing (such as threading, welding, or assembly), production capabilities (including short-run vs. high-volume), in-house engineering support, quality certifications (e.g., ISO 9001), and lead time. Leading wire forming companies invest in advanced automation, state-of-the-art tooling, and stringent quality control measures to meet the diverse needs of industries like aerospace, medical, electronics, and industrial equipment manufacturing.
The range of wire shapes, configurations, and forms is virtually limitless, with new wire form designs continually being developed to meet evolving industrial needs. Wire forming is an advanced manufacturing process that can create anything from complex, intricate three-dimensional components for automotive assemblies and medical devices to simple hooks and springs for everyday applications. Many of the products and hardware we use daily—ranging from storage solutions and display racks to safety fasteners and mechanical linkages—incorporate some type of precision wire forming.
Wire hose clamps are made from heavy-duty wire bent into a U shape and then formed into a continuous ring, with one end overlapping the other. The ends are bent upward to allow for easy opening and secure installation. When the ends are pushed apart, the clamp tightens around the hose, applying uniform compression and ensuring a leak-proof seal—an essential feature in plumbing, automotive, and industrial hose applications. To loosen the clamp, the ends are simply pressed together, allowing for fast adjustment or removal. Stainless steel and galvanized steel are often used for corrosion-resistant hose clamps in demanding environments.
There are many types of J hooks, which are essential hardware in construction, electrical wiring installation, and material handling. The fishhook is one of the most common variants. J hooks can be coated with rubber or vinyl to protect the surfaces of the items they hold and often feature notched design elements for easy, secure hanging. Heavy-duty double J hooks, when attached to webbing or straps, are engineered to support substantial loads, making them ideal for cargo control and transportation applications.
Linchpins are precision wire fasteners that are inserted into the end of an axle or shaft to prevent wheels or rotating parts from coming off. These critical components are fabricated from materials such as aluminum, zinc, brass, and stainless steel for enhanced durability and resistance to wear in agricultural machinery, trailers, and automotive assemblies.
R-clips—commonly referred to as retaining clips, hairpin cotters, or spring cotter pins—are versatile metal wire fasteners shaped like the letter R. They function similarly to linchpins, securing the end of an axle, pin, or rod with a wheel. The long, straight portion of the R clip fits through a pre-drilled hole at the end of the shaft, while the springy loop snaps snugly around the shaft, ensuring a secure hold. The semi-circular, bent section of the clip facilitates easy installation and removal, making them a preferred choice for quick assembly and maintenance in machinery, equipment, and vehicle applications.
Both ends of an S hook are precisely bent to form the characteristic S shape, enabling effortless hanging and lifting. S hooks are widely used for hanging storage, organizing cables, hoses, chains, and cords, and enhancing workplace or home safety. They are preferred in retail, industrial, and commercial environments for their simplicity, strength, and versatility.
Among the various categories of wire forms, springs are the most common and widely utilized components in countless industries. These mechanical devices consist of a coiled wire wound into a tightly wrapped spiral to achieve precise tension, compression, or torsion requirements. Types of springs include compression springs, extension springs, torsion springs, and wire coil springs, each engineered for a specific function. The selection of a spring depends on factors such as load capacity, deflection, fatigue resistance, and environmental conditions, which are critical for achieving optimal performance in industrial machinery, electronics, automotive suspensions, and aerospace devices.
In the wire form threading process, a metal rod is passed through a set of threading dies that shape the threads with precisely engineered peaks and valleys, producing high-strength screw threads rapidly. There are two primary thread forming techniques: rolled threading, where threads are created by displacing the metal, and cut threading, where material is removed to form the thread profile. Cut threading allows for a wider range of diameters, customized thread lengths, and tailored pitch combinations, making it especially useful for unique fastener applications in manufacturing, construction, and repair industries.
Utility hooks feature a threaded end and a hook, allowing for straightforward installation into wood, metal, and masonry surfaces. The manufacturing process involves multiple bends—including offset bends on both sides of the loop—followed by a final bend at the end of the loop that secures the hook on the opposite side. Utility hooks are frequently used in garages, warehouses, and storage systems for organizing tools, hoses, bicycles, and heavy equipment securely.
Wire baskets are essential for bulk storage and material handling of parts, equipment, and product components in industrial, medical, and commercial facilities. They are fabricated from heavy-gauge welded wire mesh, which provides excellent strength, ventilation, and visibility for inventory control. Some models feature a rust-resistant electrogalvanized or powder-coated finish to prevent corrosion and ensure a long service life. The open mesh design allows for easy identification and forklift access, streamlining lean manufacturing and just-in-time inventory systems. In production facilities, wire baskets can be used for washing, dipping, and transporting components with maximum efficiency and durability.
Wire displays are a durable and cost-effective solution for showcasing retail products, promotional items, and merchandise in stores, trade shows, and showrooms. These displays are manufactured by bending, shaping, and forming wire—typically from low, medium, or high carbon steel, as well as stainless steel, copper, or aluminum brass. After forming, wire displays can be powder coated, plated, or painted for enhanced appearance, durability, and resistance to scratching and corrosion. Custom wire display racks offer flexibility in design and can be engineered to meet specific branding and merchandising requirements.
Wire guards exist in various configurations, all engineered to provide reliable protection and prevent unauthorized access to sensitive equipment, passageways, instruments, and electronic devices. Hinged wire guards, also known as wire cages, are used to protect sensitive machinery and components in high-traffic industrial locations, athletic facilities, and public spaces. Open-face wire guards safeguard fire alarms, emergency stop switches, and safety controls against accidental damage or activation. Additionally, wire guards are often used to enclose automated machinery, robotic systems, vibration-sensitive equipment, tanks, heavy motors, and spiral HVAC fans—enhancing workplace safety and facility security by minimizing risk and meeting regulatory standards.
Wire screens are fabricated by weaving or welding thin metal wires both horizontally and vertically to create open protective barriers, ideal for filtering, sieving, and controlling the flow of materials. These screens are constructed from stainless steel, galvanized steel, copper, or specialty alloys to provide high tensile strength, chemical resistance, and thermal stability. The intersecting wires are welded or woven with precision for consistent mesh size and reliable performance. Advanced wire-forming techniques are used to shape the mesh to precise diameters. In industrial manufacturing, wire screens are used in filtration systems, mining operations, food processing, and architectural applications, providing durability and versatility in demanding environments.
Z clips are innovative wire fastening components engineered to securely lock panels, signage, or assemblies in place in commercial, industrial, and electronic applications. The extended portion of the Z clip slips over the part to be secured and is anchored at both ends, ensuring a firm and stable hold. Available in a wide range of thicknesses and diameters, Z clips are used for everything from mounting wall panels and architectural elements to holding delicate electronic components in place within devices. Z clips are valued for their strength, adaptability, and corrosion resistance, contributing to maintenance efficiency and structural integrity.
Choosing the Right Wire Form for Your Application
Selecting a wire form that best meets your project requirements involves considering key factors such as material composition, wire diameter, load-bearing capacity, corrosion resistance, finishing options (e.g., powder coating, plating), and intended application environment. Industries such as automotive, aerospace, electronics, medical device manufacturing, and construction rely on custom wire forming for parts and assemblies that demand precision, reliability, and durability. When researching wire form manufacturers or suppliers, evaluate design flexibility, prototyping capabilities, production lead time, and the ability to meet strict quality standards. For more guidance on high-precision custom wire forms—including wire bending, cutting, stamping, and advanced form technologies—consult an experienced fabricator with a proven track record in your specific industry.
Wire forms can be fabricated from a wide variety of metals, including aluminum, copper, steel, brass, stainless steel grades 304, 316, and 434, as well as various types of alloys.
Bright basic wire (BBW) is a low carbon steel wire with a bright polished finish. It is cold drawn to enhance its tensile strength and mechanical properties. BBW possesses the essential physical properties for bending, straightening, welding, and finishing with epoxy, plastic, galvanization, or powder coating. The common grades of BBW used for wire forming are 1008C and 1018C.
Galvanized wire is carbon steel wire coated with zinc through electroplating or hot-dipping. This process makes it rust-resistant and exceptionally strong, and it is available in various gauges. In the hot-dipping process, the carbon steel wire is submerged in a zinc bath. Upon removal, the wire cools and reacts with the surrounding oxygen, binding the zinc to the carbon steel.
Stainless steel grade 304 has high resistance to corrosion with a tensile strength of 621 MPa and can be used in conditions with mild corrosive elements or where handling of heavy loads is required. The quality of grade 304 makes it durable and long-lasting. It can be used in conditions that have temperatures that exceed 1500° F (815.5° C) less than 2500° F (1371 ° C). It may be important for some applications that none of the 300 grade stainless steels are magnetic.
Grade 316 stainless steel is more resistant to corrosion and can withstand the effects of chlorides. It has a tensile strength of 579 MPa and can handle extremely heavy loads. Grade 316 can be used in environments with temperatures that do not exceed 1400° F (760 ° C). Its ability to withstand caustic or highly corrosive environments has made it extremely useful.
Stainless steel grade 434 is a ferritic alloy that is resistant to pitting and does not have any nickel content, which makes it less expensive. A restriction on stainless steel grade 434 is the temperatures at which it can be used, less than 1500° F (815.5° C), limiting its use for heat treatment applications. It is highly resistant to oxidation, corrosion, and pitting and is very useful in the production of industrial baskets.
Brass is an alloy consisting of 67% copper and 33% zinc, retaining the electrical and heat conductivity and malleability of copper. It is stronger than copper, making it suitable for a wider range of applications, including wire forming. Certain brass alloys include elements like antimony, arsenic, iron, and tin to enhance mechanical and physical properties such as hardness, formability, strength, and appearance.
Copper (Cu) is a soft, malleable, and ductile metal with high electrical and thermal conductivity and a reddish-orange hue. Its excellent conductivity and ease of shaping make it ideal for wire forming. Copper is resistant to rust and corrosion, and over time, it develops a green patina when exposed to the atmosphere.
Aluminum (Al) is a soft, non-magnetic, and ductile metal, making it the third most abundant metal on Earth. It is derived from bauxite and often occurs in combination with over 270 other minerals. Aluminum is known for its low density and resistance to corrosion. For wire forming applications, aluminum is alloyed with other metals because it is prone to deformation in its pure form. Key alloying metals include copper, zinc, magnesium, manganese, and silicon.
Steel is an alloy of iron with added carbon to enhance its strength and resistance to fracturing. Its primary appeal in manufacturing lies in its high tensile strength combined with affordability. The base metal of steel is iron, and the interaction between iron's allotropes and its alloying elements, primarily carbon, imparts the steel's properties. Since pure iron is soft and ductile, the addition of carbon and other alloys increases its hardness, strength, and durability.
Wire forming is a key process in industries that utilize wire to create components and parts. This technique encompasses both standard shapes and custom-designed forms, making it highly adaptable to various conditions, materials, and engineering requirements.
Parts for the medical industry must be durable, smooth, and exceptionally clean. Stainless steel is the primary metal used for manufacturing medical components because it can endure high temperatures, repeated cleanings, and sterilization. Its smooth surface helps prevent nicks, cuts, and punctures to medical workers' gloves and garments.
Industrial operations demand fast and precise methods for assembly and manufacturing. Wire-formed baskets play a crucial role in the efficient and organized delivery of parts to production areas, ensuring convenience and speed in handling.
In the automotive industry, wire forming encompasses a range of components including wire springs, compression coils, and volute springs for suspension systems. Delicate springs, such as torsion and tension springs, serve various functions, including supporting swing-down tailgates. Additionally, conical springs are used in manufacturing battery contacts.
Masks used in contact sports are wire-formed for protection and are designed to meet the standards set by the National Operating Committee on Standards for Athletic Equipment (NOCSAE).
Steel wire is utilized for guides and trays due to its smooth surface. The open design facilitates easy access for cable installation, inspection, and upgrades. Routing rings can be attached to frames to manage various types of wire, thanks to the strength of the wire frame. Trays, troughs, and support hardware are designed for efficient cable management, incorporating routing rings and tie bars for optimal organization.
A common use of wire forming in retail is product display racks that are lightweight but sturdy enough to hold products for customer inspection. They can be placed at cash registers as point of purchase displays or in multiple locations throughout the store. Their light weight makes it easy to relocate them to high-traffic aisles. Wire racks are also a convenient way for storing merchandise for future sales and conducting inventory.
The food industry must adhere to numerous regulations to comply with FDA requirements and specifications. Wire storage and processing racks must meet stringent standards for sanitation and cleanliness. They are constructed from high-grade stainless steel, which is corrosion- and rust-resistant, and capable of being continuously sanitized and washed.
Wire forms play a crucial role in building construction, serving various functions such as holding wires, supporting hooks, springs, pins, wire guards, equipment frames, and wire screens. They are used not only as essential construction materials but also in decorative applications, including guardrails and accent pieces.
The wire forming process involves four key steps that should be considered when deciding to wire-form a part or component. These steps include selecting the appropriate type of wire for the application, straightening the wire before processing, applying force to shape the design, and determining if secondary processing is required.
The gauge, diameter, and type of wire used in the wire forming process are determined by the initial CAD design. Steel and stainless steel are commonly used for applications requiring durable and long-lasting components, while lightweight wires like aluminum and copper are suitable for less demanding conditions. Wire can be made from low, medium, and high carbon steel, as well as stainless steel, aluminum, copper, brass, and various alloys.
Wire is stored in coils and must be straightened before processing. This step removes stress deformities that may have developed during storage. Machine rolling is used for straightening the wire. Uncontrolled irregularities in this process can result in poor wire form.
Wire forming involves applying force to alter the contour and shape of the wire into the desired form. This shaping process is designed to create a diverse range of shapes and configurations. Force can be applied manually or using various automated equipment, including dies and cutting tools. For high-volume production, CNC machines and four-slide machines are commonly used.
The need for finishing in wire forming depends on the type of product and its design. While some wire-formed products may not require additional finishing, others might need post-production adjustments such as cuts, grooves, heading, coining, or swaging. The primary focus of finishing is to ensure that burrs and sharp edges are smoothed out and removed.
Wire baskets are made from a series of wires that are woven together or welded to form a shape of a basket. They can also be defined as containers that are made by use of an openwork pattern of metal...
Wire shaping is a complex method that encompasses a wide range of dimensions, forms, and textures. The technique of creating a usable product by wire bending and shaping is known as custom wire forms...
A wire handle is attached to a bucket, pail, or other type of container to make it easy to lift the container and transport it. They are made of durable and sturdy metals capable of lifting several pounds...
A wire rack is a level wire form utilized to stock and exhibit a number of products, usually retail. The bottom surface on which such goods are stored is made of several latticed or interlaced metal strands...
Wire mesh is fabricated by the intertwining, weaving, or welding of wires of various thicknesses to create proportionally equal parallel rows and intersecting columns. Also known as wire fabric, wire cloth, or...
A coil spring is an elastic element made of metal or heavy plastic in the form of curls or ringlets of round wire or cord that is wrapped around a cylinder. The winding of a coil spring can be loose or tight in a helical shape depending on the application for which it is made...
Coil springs called compression springs can store mechanical energy when they are compressed. These open-coiled, helical springs provide resistance to compressive loading. When these springs are...
Contract manufacturing is a business model in which a company hires a contract manufacturer to produce its products or components of its products. It is a strategic action widely adopted by companies to save extensive resources and...
Extension springs are helical wound springs that are so closely coiled together to create initial tension in the coils. This initial tension creates resistance against the force applied to its ends for extension. The initial tension helps determine how closely and...
Hardware cloth is a woven mesh made by interlacing various sizes of wire to form a metal fabric that can be used for animal cages, fence material, strainers, and filtering screens. The differences between the various types of hardware cloth...
The phrase "wire mesh" describes two- or three-dimensional structures constructed of two or more metallic wires connected by various techniques. In a wide range of settings, wire mesh products are...
Springs are a flexible machine element that store mechanical energy when subjected to tensile, compressive, bending, or torsional forces. When the spring is deflected, it stores energy and at the same time exerts an opposing force...
A torsion spring is a mechanical device that stores and releases rotational energy. Each end of the torsion spring is connected to a mechanical component. As the spring is rotated around its axis on one end, the winding of the spring is tightened and stores potential energy...
Welded wire mesh is a series of wires that are welded where the individual wires cross. The openings of the mesh varies depending on the type of wire used and the function of the mesh. Regardless of size and wire, welded wire mesh is permanent and...
Wire cloth is a woven (or nonwoven) sheet or web material with a series of openings across the surface. Wire cloth is also known as: Metal Fabric or Metal Cloth; Wire Mesh, Metal Mesh, or Alloy Mesh...