Wire Baskets
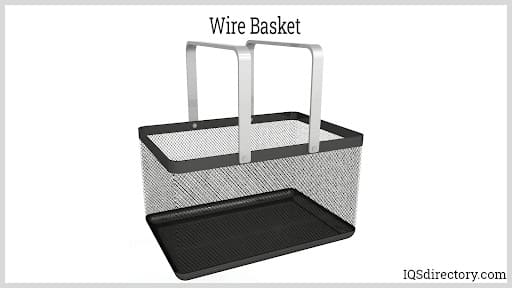
Wire baskets are made from a series of wires that are woven together or welded to form a shape of a basket. They can also be defined as containers that are made by use of an openwork pattern of metal...
Please fill out the following form to submit a Request for Quote to any of the following companies listed on
This article will take an in-depth look at wire racks.
The article will bring more detail on topics such as:
In this chapter, we delve into the nature of wire racks and the process behind their production.
A wire rack is a constructed wire platform used mainly in retail for displaying or storing different items. These racks are designed with interlaced metal wires, forming a resilient platform capable of supporting various objects. While resembling wire shelving intended to optimize space use, wire racks typically describe smaller shelving units that aren't standalone.
Wire racks enhance vertical storage space, making them particularly useful for displaying or holding retail and business products. Often structured with multiple layers or stackable parts, these racks are adaptable to numerous applications. Aside from their promotional uses, wire racks are widely employed in industrial settings. For instance, drying or cooling racks are often wire-based because they hold items in place while allowing necessary air flow, crucial for items such as baked goods.
Although storage racks are generally horizontal, designs for cooling and display racks may include a tilt to allow products to slide forward for accessibility. Additionally, some wire racks feature bent edges or lips at the front to prevent items from falling off entirely.
During manufacturing, racks may receive additional finishes like painting, coating, heat treatments, or electro-polishing according to specific requirements. To improve mobility, casters are often attached to the support bars of full rack units.
Wire racks are produced using a method known as wire forming. This involves transforming wire from its raw shape or a coiled spool into particular designs. The adaptability of wire forming accommodates a broad set of shapes and configurations, which is why it's ideal for crafting wire racks.
Wires can be manipulated into coils, angles, bends, or cuts, making them suitable for custom projects. From small springs used in machinery to large chains for carrying loads, or wire racks for retail storage, wire forming serves numerous purposes.
The creation of wire racks involves bending wires into precise shapes. This necessitates bending them past their yield strength but within tensile limits, ensuring the wire is reshaped without breaking or reverting. This precise bending retains both form and functionality in the finished rack.
As previously explained, wire forming involves bending wires into specific shapes, like interwoven racks. Specialized machines handle this wire bending to achieve the desired configurations.
These machines are capable of bending wires with a diameter up to 1 ½ inches, efficiently managing multiple wires in a brief period.
Optimizing wire forming and assembly for wire racks involves:
CNC bending, or "computer numerical control" bending, is prevalent in contemporary manufacturing, involving multiple integral parts.
These components cooperate to form intricate wire shapes, including:
The computer transmits design specifications to the CNC machine. Then, the CNC machine uncoils the wire, straightens it, and precisely bends it using a robotic arm and pins before cutting it to length. This facilitates customized wire shaping with consistency and precision across all axes.
Different wire benders offer varied capabilities. While 2D machines focus on simple, flat shapes, advanced 3D machines allow detailed 3D wire bending. These advanced machines deliver more flexibility and adaptability to complex designs, ensuring customized wire shaping.
Traditional wire forming relied on manual machines featuring spindles and levers for shaping, utilizing gears for controlled wire bending.
The four-slide stamping process, using cams with shafts, gears, and a motor-driven press, operates efficiently. The simultaneous action of four gears significantly speeds up production.
Roughly, 3,500 wire forms can be produced every hour. Cam systems dictate gear movement, enabling multidirectional actions.
Wire bending enables the creation of diverse wire configurations, accommodating thicknesses from 0.016 to 0.625 inches (0.41 to 16 mm). By forming before cutting, this technique reduces waste.
A hydraulic motor drives rollers to shape wire, using CNC programming for specific designs. Post-formation, the wire is systematically retrieved from the machine.
In pneumatics, wires are fed and straightened before being cut to specific lengths using compressed air for accuracy.
In assembling wire racks, welding joins bent wires using techniques like MIG, TIG, or ERW. ERW combines electric currents and pressure for binding.
TIG, MIG, and ERW methods all employ inert gases to minimize contamination. TIG delivers top-notch results but requires skilled handling, making MIG a go-to for its speed. Some designs might still use weaving for grids and screens.
Post-welding, wire forms might be plated or coated, depending on design needs. Finishing eliminates sharp edges for a safe, polished product. Additional adjustments, such as grooves or swaging, help meet specific design requirements.
Wire racks act as an efficient storage option without needing construction modifications, holding items from books and toys to heavy goods. Choosing the right rack simplifies storage issues. Consider this approach:
Identify Purpose – Understand your storage requirements, whether for books, baked items, or retail goods, to select the most suitable wire rack.
Dimensions – Match the rack dimensions to your available space and item sizes, ensuring compatibility in terms of height, width, and length.
Appearance – If aesthetics are key, select racks with appealing designs.
Load Capacity – Ensure that the cumulative item weight doesn’t exceed rack strength, averting costly failures.
Openings – The gap between wires should be smaller than the smallest item to avoid storage issues.
With various options available, using these criteria will guide you to the best wire rack for your situation.
This chapter will explore the different types of wire racks and the materials commonly used in their construction. Understanding these aspects is crucial for businesses and consumers looking to purchase wire racks for specific commercial or industrial storage, retail display, or organizational needs.
There are several types of wire racks designed to serve different industries and applications. Below, we detail some of the most popular wire racking systems and their primary uses in various environments:
Literature stands, sometimes called magazine racks or brochure displays, are designed to hold various types of periodicals and can be used to display products for sale or organize a waiting room. Floor stands, featuring multiple levels or adjustable tiered pockets, can showcase numerous magazines or folded brochures for easy access and high visibility in reception areas, showrooms, and office lobbies.
Unlike wooden racks with pockets, metal wire frame constructions offer superior visibility from all angles and exceptional durability. Countertop styles are typically smaller versions of floor racks and come in both single and multiple pocket designs. Tabletop fixtures are ideal for displaying takeaway literature or keeping service centers and doctor’s offices organized. Additionally, rotating or revolving styles are available in both countertop and floor models, allowing for even greater display flexibility and maximized space utilization in busy settings.
Merchandising wire racks are popular among retailers and commercial businesses due to their durability, versatility, and affordability. These wire displays and rack systems come in various designs to accommodate almost any type of product, from packaged goods to bulk items. For example, rotating spinner stands, which can have up to 72 wire pockets, are ideal for displaying greeting cards, postcards, and other stationery. Conversely, bulk bins are perfect for storing and displaying items that are challenging to place on shelves, such as stuffed animals, beach balls, and pillows. The open-wire construction is desirable for both product visibility and airflow.
Racks with adjustable slant shelving are optimal for displaying bakery items, bottles, and various other products that benefit from tiered or angled presentation. Many models come equipped with rolling casters, making it easy to move them as needed for flexible floor layouts or seasonal promotions. Countertop racks are well-suited for holding small items such as blister packs, souvenirs, keychains, and other impulse-buy merchandise. Typically located at or near checkout counters (point-of-purchase displays), these versatile wire racks can significantly boost sales and encourage impulse shopping for retailers. Additionally, revolving racks are highly effective for showcasing postcards and small printed items.
In addition to industry-standard slat-wall fixtures, grid-wall wire racks and grid panels are also popular in retail stores for both display and storage purposes. They have a similar open-wire design to slat-wall but are typically more affordable, lighter in weight, and easier to reconfigure. Grid-wall racks can be securely mounted on walls or placed on the floor with sturdy bases. Once a wire rack is chosen, various add-ons such as baskets, hanging hooks, and shelves can be used to fully customize the layout, maximize product exposure, and create a modular display system. This adaptability makes grid-wall fixtures ideal for fast-changing inventory and visual merchandising requirements.
Art display panels, sometimes referred to as artist display grids or art show panels, are similar to grid-wall racks but are specifically designed for showcasing artwork. With a comparable wire frame design, these panels are lightweight and ideal for outdoor art festivals, galleries, art fairs, and trade shows. They allow for quick and efficient hanging of mirrors, canvases, framed art, or other artwork using S-hooks and clips. The modular construction facilitates custom layouts, which can be easily assembled using cotter pins or connectors that lock the panels together. Portable and affordable, art display panels are also compatible with grid-wall hanging accessories, making them a highly versatile and indispensable tool for artists and exhibitors looking for professional, mobile display solutions.
A wire cooling rack, also known as a baking rack, is an essential piece of kitchen equipment for professional bakers and home cooks alike, allowing air to circulate completely around whatever is placed on it. This promotes much faster and more even cooling compared to placing items on a trivet or countertop. As a hot pan continues to cook the food inside it, using a wire rack helps prevent over-baking and ensures bakery goods maintain their intended texture and don’t become soggy.
Most recipes for cakes, cookies, breads, or muffins recommend placing the hot pan directly on a cooling wire rack for the initial cooldown. After this phase, baked goods are often transferred directly onto the rack. This final step encourages proper airflow on all sides—including the underside—preventing steam condensation from accumulating and ensuring that the freshly baked items retain their crispness and do not become soggy.
Cooling wire racks are typically constructed from stainless steel or chrome-plated steel, featuring a mesh of crisscrossed wires or closely aligned parallel wires. This sturdy design ensures that products can be securely placed without falling through, while still allowing ample air circulation to the base of the food to prevent excess moisture. Cooling racks can be single-layered, stackable, or multi-tiered, with two or three stackable rows to accommodate large batches of breads, cakes, cookies, or pies. They come in a variety of shapes and dimensions—including square, round, oval, and rectangular—and roasting racks can also serve as cooling racks in both residential and commercial kitchens. Look for nonstick coatings and dishwasher-safe options for added convenience and food safety.
A garment or clothes rack is a durable rail system made from metal wire, commonly used in retail clothing stores, warehouses, and backrooms for displaying and organizing clothing items such as shirts, coats, dresses, and outerwear. These racks are favored for their strength, portability, and ease of assembly. Folding garment wire racks are particularly convenient for retail settings because they facilitate quick changes to store layouts and simplify seasonal storage needs, making them a top choice for clothing retailers, boutiques, and pop-up shops.
In addition to retail use, heavy-duty garment wire racks serve vital roles in industrial laundry facilities, garment manufacturing, fashion showrooms, and even home organization for closets and laundry rooms. They often feature locking caster wheels for mobility and can include accessories like shelves, hanging bars, or additional storage bins to maximize organizational efficiency.
Wire racks are fabricated from several durable materials, each chosen for its strength, longevity, and suitability for the intended environment. The most common materials for wire racks include:
Choosing the appropriate wire rack material depends on factors like expected load-bearing requirements, environmental exposure (humidity, temperature), hygiene or food safety standards, and budget considerations. For high-humidity or food storage environments, opt for stainless or epoxy-coated racks. For general storage or dry retail spaces, chrome or powder-coated racks are often sufficient.
Wire racks can be custom fabricated to meet specific organizational and display needs, offering superior air flow, visibility, and ease of cleaning compared to many solid shelving alternatives. Whether for retail displays, commercial storage solutions, kitchen baking tools, or industrial shelving, selecting the right wire rack style and material enhances efficiency, safety, and visual appeal.
Wire racks can be fabricated from various metals and coating materials, with each offering unique performance characteristics suited for specific uses in commercial, industrial, and residential storage. Selecting the right wire rack material is essential for maximizing strength, durability, and resistance to environmental stressors. Below is a comprehensive overview of the best materials for manufacturing wire racks, shelving units, baskets, and custom storage solutions:
Grade 304 stainless steel, an austenitic alloy, offers exceptional corrosion resistance and a high tensile strength of 621 MPa (90 ksi). This makes it ideal for supporting heavier loads and performing well in mildly corrosive environments. Grade 304 is the industry standard for wire shelving in food service, medical equipment, kitchen storage racks, and laboratory racks due to its sanitary properties and ease of cleaning. Compared to iron or plain carbon steel, grade 304 stainless steel also exhibits superior resistance to oxidation, rust, and wear.
Grade 316 stainless steel is more resistant to corrosion than grade 304 stainless steel. In essence, 316 stainless steel is good at resisting chlorides, like salt, making this stainless steel grade perfect for applications having caustic conditions too hostile for grade 304 stainless steel. Typically used in marine environments, pharmaceutical processing, and chemical storage solutions, grade 316 wire racks provide unmatched durability, even under exposure to aggressive cleaning agents or saltwater. This makes it a top choice where wire storage solutions face extreme corrosion or sanitary conditions.
Grade 434 stainless steel, a ferritic alloy, is known for its excellent resistance to pitting. While it is less resistant to chemicals compared to grade 304 stainless steel, it still offers superior protection against corrosion, pitting, and oxidation compared to plain steel. Grade 434 is often selected for indoor wire shelving, cabinet racks, and moderate-demand industrial applications where cost efficiency and moderate corrosion resistance are priorities.
Polyester (triglycidyl isocyanurate, or TGIC) is a specialized powder coating used to protect wire forms from harsh chemicals and high temperatures. This industrial-grade coating is highly resistant to chlorides, scratches, and abrasions, making it an excellent choice for enhancing durability and longevity in demanding environments. Polyester TGIC coatings are common for retail display racks, laundry shelving, outdoor storage solutions, and any wire rack exposed to frequent handling or chemical cleaning agents.
Similar to polyester TGIC powder coating, epoxy solid coating provides strong resistance to staining, marring, humidity, chipping, and various solvents. This makes it an excellent protective layer for metal wire forms, ensuring enhanced durability and longevity. Epoxy coatings are especially popular in healthcare environments, walk-in cooler shelving, laboratory wire racks, and food storage applications due to their antimicrobial and moisture-resistant properties. They help prevent metal corrosion, prolonging the life of the wire rack under heavy use and variable temperatures.
Plastisol is a flexible coating material with properties that can vary based on the plasticizers and application methods used. It is particularly effective at protecting wire forms from chemical exposure, offering a durable shield against harsh environments. Plastisol-coated wire racks are preferred for dish racks, food processing, beverage storage, and applications involving regular contact with moisture or direct food handling since the PVC surface is non-porous, easily cleaned, and provides excellent insulation. This coating also helps prevent scratching and impact damage, increasing service life in both commercial and industrial settings.
Another alloy specifically designed for high-temperature applications is grade 330 stainless steel. It can withstand extended exposure to temperatures up to 1,037°C (1,900°F). Grade 330 wire racks are routinely chosen for specialized industrial environments such as heat-treating processes, baking ovens, and annealing furnace shelving. Their temperature resilience combined with corrosion resistance makes them suitable for applications where wire baskets must endure repeated heating or direct flame exposure.
When selecting materials for your wire rack project, be sure to assess the environmental conditions, weight capacities, and regulatory requirements specific to your intended storage solution. In addition to considering different metals and coatings, reviewing key attributes such as load-bearing capability, maintenance needs, life expectancy, and suitability for hygienic or caustic environments will ensure optimal performance for your shelving or organizational system. By matching the right wire rack material to your unique needs, you can achieve balance between durability, safety, and long-term value—whether you’re outfitting a commercial kitchen, hospital cleanroom, warehouse, or retail space. For additional guidance on choosing the best wire rack materials and comparing available options, industry professionals recommend consulting with a reputable wire rack manufacturer or installer (nofollow) to discuss custom specifications, cost-effective solutions, and ongoing maintenance best practices.
This chapter will explore the applications and benefits of wire racks, as well as the maintenance required to keep them in optimal condition.
A wire rack is an excellent tool for businesses to display informational materials about their products or services. Placing a wire rack at the store entrance, on the counter, or inside the store allows customers to easily access and take pamphlets. These pamphlets can include marketing content, important business information, or anything else the business owners deem essential for customer awareness.
Wire racks come in various designs, including rotational and circular stands, as well as immovable ones where customers need to navigate around to find what they need. The dimensions of the wire rack depend on the size of the brochures it holds, such as A5, A4, or DL. The height of the stand is influenced by the number and size of pockets it has. For example, a wire rack with three standard pockets, each 1.25 inches deep, might measure approximately 7 inches in height with a base radius of about 1.1 inches.
Some advantages of wire racks include:
Wire racks can feature interchangeable panels that can be added or removed as needed. This flexibility allows the racks to adapt to changing space requirements and inventory needs. By rearranging or updating these fixed components, businesses can efficiently reflect new or additional inventory, ensuring that the display or storage setup remains functional and relevant.
This versatility enhances efficiency, especially when preparing for professional shows. The point-of-purchase (POP) display pieces can be quickly and easily assembled or disassembled as needed, streamlining the setup and takedown process.
Wire Rack Durability – Wire racks are highly durable, crafted from top-quality materials that ensure they withstand extensive use without breaking or bending. They can support significant weight, making them ideal for displaying heavy items like mirrors and tools. Despite their strength, they remain lightweight, which makes them easy to store and relocate as needed.
Beautiful Designs and Customization – Customized wire racks offer flexibility in design, allowing for a variety of shapes and features tailored to specific needs. Their sleek, open designs ensure products are showcased effectively, while new fittings can be created to accommodate any display item. Powder coating can be applied to match exact color requirements, ensuring a perfect fit for customer preferences. Manufacturers can collaborate with clients to bring their vision to life, leveraging the unique advantages of wire racks for optimal results.
Economics of Wire Racks – Wire racks offer exceptional value and high quality. Their durability ensures they are a wise investment, providing efficient and long-lasting solutions for storage and display needs.
Easy Product Access – Similar to shelving, wire racks are accessible from all four sides. This feature of customer psychology suggests that if clients "connect" with an item, they are more likely to make a purchase.
Wire Racks are Portable – Wire racks, despite being made from durable metals, are lighter compared to other storage options. This allows them to be easily mounted on rolling casters, making them mobile. Increased mobility helps maximize storage space and facilitates changing the layout of a business or office as needed.
Easy to Clean – A wire rack offers a safe environment for products by protecting them from damage. Its open design allows for easy airflow, preventing dust and debris accumulation. Additionally, the rack can be easily wiped down and disinfected when needed, ensuring a clean and hygienic display.
Food Safe – In addition to their ease of cleaning, wire racks are ideal for cold storage in butcheries and restaurants, as the mesh design allows for optimal airflow around products, enhancing quality and extending shelf life. They can also be coated with antifungal and antimicrobial epoxy to further improve hygiene and prevent contamination.
Selecting the appropriate wire forming product can significantly enhance efficiency, reduce costs associated with damaged equipment, and minimize the risk of employee injury.
Increased Efficiency – High-quality wire forming products equip manufacturers with the right tools to complete operations swiftly and efficiently, thereby boosting overall productivity.
Decreased Costs – High-quality wire forms are designed to endure years of repeated use without breaking. This durability minimizes the risk of stoppages, which can lead to increased costs and potential damage to products.
One issue with wire racks is their potential for deterioration. They can buckle and break if mishandled and may rust over time, requiring regular maintenance. For instance, chrome wire racks are prone to rust, making them more suitable for indoor use. In contrast, stainless steel or epoxy-coated racks are better choices for outdoor environments or for storing goods that need to be kept cool, as they offer enhanced durability and resistance to rust.
Wire racks are ideal for storing small items and lightweight products, but they may not be suitable for high-volume, heavy items that require more robust shelving solutions.
Regular maintenance steps are crucial for extending the lifespan of wire racking units. These include:
Dust Daily – Whether a shop has air conditioning or not, dust will accumulate over time. Dusty racks are unattractive to customers and can negatively impact business. Regular dusting prevents stale odors and promotes a healthier environment for everyone..
Organized Display – An organized product display transforms the store's appearance, making it easier for customers to find what they need and enhancing their impression of the store's spaciousness and neatness.
Sanitize Often – Sanitization is crucial as racks are frequently touched by both customers and employees throughout the day. Implement a regular cleaning routine that includes thoroughly wiping down all racks within the retail setup. Use high-quality wipes, sprays, or disinfectants to ensure a thorough and effective clean.
Doing Maintenance Checks – Most types of racks experience wear and tear over time. Conducting a biannual service ensures that all critical components of the racking units remain in good condition, helping them to withstand use and last for many more years.
Wire racks are level wire forms for storing and showing a number of products, usually retail. Although they’re similar to wire shelving since they are both designed for taking full advantage of horizontal and vertical space, the term ‘wire rack’ more frequently refers to miniature units or those ledges not made to stand alone.
Wire racks come from wire forming which is a process of acquiring a wire, from either a blank length or spooled coil, and bending it into definite forms. Wire forms are particularly flexible, enabling them to be changed into a vast variety of shapes and particular configurations. They are applied mostly in retail to encourage consumers with impulse buying as they provide easy access to products.
Wire baskets are made from a series of wires that are woven together or welded to form a shape of a basket. They can also be defined as containers that are made by use of an openwork pattern of metal...
Wire shaping is a complex method that encompasses a wide range of dimensions, forms, and textures. The technique of creating a usable product by wire bending and shaping is known as custom wire forms...
Wire forming is a method for applying force to change the contour of wire by bending, swaging, piercing, chamfering, shearing, or other techniques. The various techniques for wire forming can produce any type of shape, form, or configuration...
A wire handle is attached to a bucket, pail, or other type of container to make it easy to lift the container and transport it. They are made of durable and sturdy metals capable of lifting several pounds...
Wire mesh is fabricated by the intertwining, weaving, or welding of wires of various thicknesses to create proportionally equal parallel rows and intersecting columns. Also known as wire fabric, wire cloth, or...
A coil spring is an elastic element made of metal or heavy plastic in the form of curls or ringlets of round wire or cord that is wrapped around a cylinder. The winding of a coil spring can be loose or tight in a helical shape depending on the application for which it is made...
Coil springs called compression springs can store mechanical energy when they are compressed. These open-coiled, helical springs provide resistance to compressive loading. When these springs are...
Contract manufacturing is a business model in which a company hires a contract manufacturer to produce its products or components of its products. It is a strategic action widely adopted by companies to save extensive resources and...
Extension springs are helical wound springs that are so closely coiled together to create initial tension in the coils. This initial tension creates resistance against the force applied to its ends for extension. The initial tension helps determine how closely and...
Hardware cloth is a woven mesh made by interlacing various sizes of wire to form a metal fabric that can be used for animal cages, fence material, strainers, and filtering screens. The differences between the various types of hardware cloth...
The phrase "wire mesh" describes two- or three-dimensional structures constructed of two or more metallic wires connected by various techniques. In a wide range of settings, wire mesh products are...
Springs are a flexible machine element that store mechanical energy when subjected to tensile, compressive, bending, or torsional forces. When the spring is deflected, it stores energy and at the same time exerts an opposing force...
A torsion spring is a mechanical device that stores and releases rotational energy. Each end of the torsion spring is connected to a mechanical component. As the spring is rotated around its axis on one end, the winding of the spring is tightened and stores potential energy...
Welded wire mesh is a series of wires that are welded where the individual wires cross. The openings of the mesh varies depending on the type of wire used and the function of the mesh. Regardless of size and wire, welded wire mesh is permanent and...
Wire cloth is a woven (or nonwoven) sheet or web material with a series of openings across the surface. Wire cloth is also known as: Metal Fabric or Metal Cloth; Wire Mesh, Metal Mesh, or Alloy Mesh...