Aircraft Cables
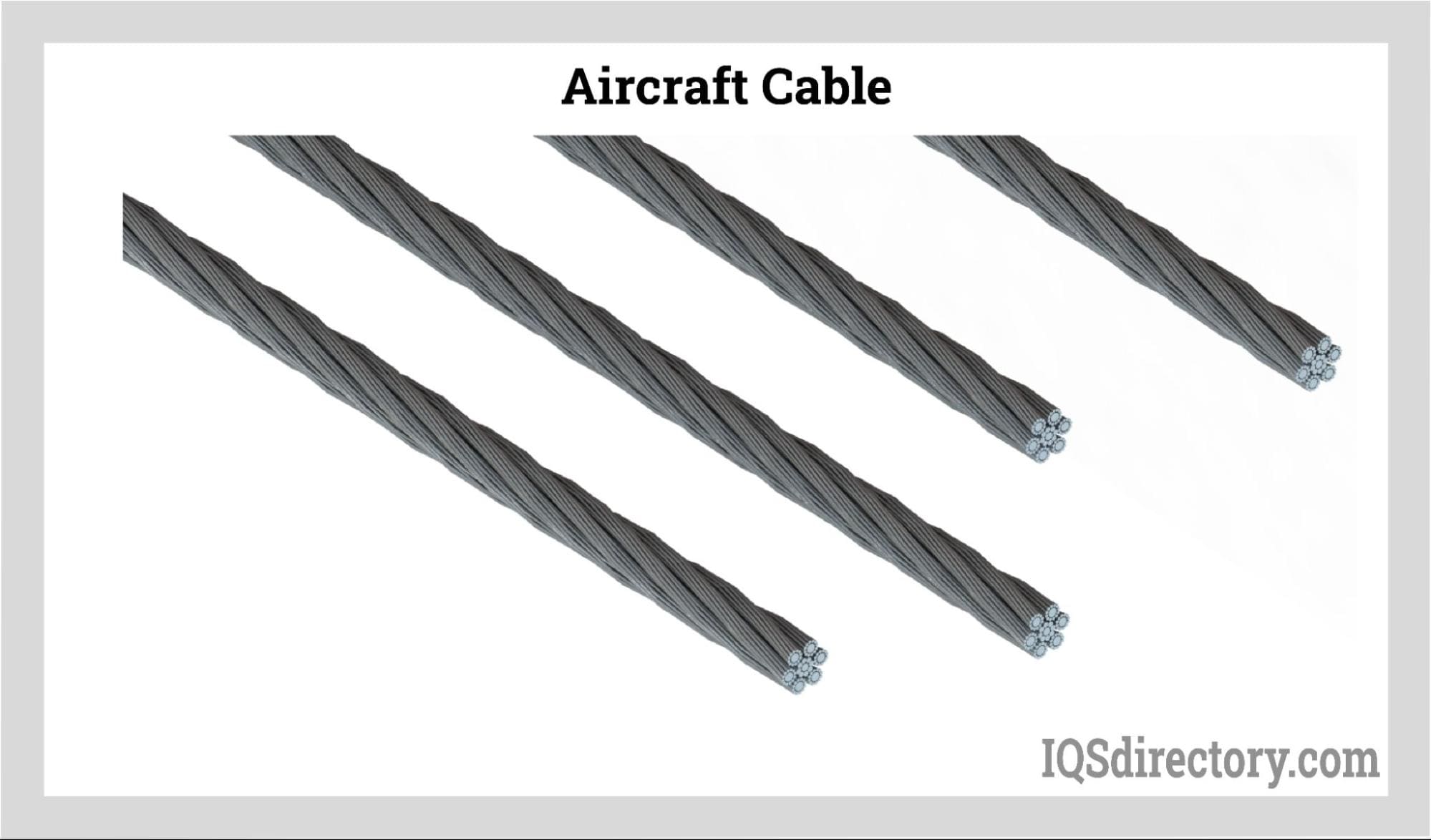
An aircraft cable is a style of highly durable cable that is used for aircraft flight controls and other applications and is differentiated from normal cables by its diameter, stranding, and wires, which provide...
Please fill out the following form to submit a Request for Quote to any of the following companies listed on Wire Rope .
This article takes an in depth look at Wire Rope.
You will learn more about topics such as:
Wire rope is formed by twisting metal strands into a helix, specifically engineered for lifting and carrying heavy weights. Frequently utilized in shipping docks, rigging, and various load-bearing apparatus, it connects to swivels, shackles, or hooks to ensure loads are lifted and managed safely with efficiency.
Wire rope also plays a critical role in supporting suspension bridges, lifting elevators, and reinforcing towers. Its design, characterized by multiple strands wrapping around a sturdy core, offers strength, flexibility, and easy manipulation in applications involving bending stresses.
The design of wire rope differs in terms of materials, types of wires, and strand arrangements, in order to effectively support lifting operations or other supportive duties.
Cable and wire rope are distinct materials, each possessing unique traits and functionalities. Cable typically refers to a pliable assembly of one or more wires encased in a protective sheath. It is predominantly used for electrical connections, such as in power distribution and data transmission, where flexibility and conductivity are essential.
Wire rope, on the other hand, comprises a robust structure made from multiple intertwined steel strands, forming a durable cord. It’s perfect for scenarios demanding outstanding strength and load resistance, making it integral to construction, maritime, and industrial environments.
The main distinction between cable and wire rope lies in their construction and intended purpose. While cables are tailored for electrical or electronic transmission, focusing on flexibility and conductivity, wire ropes are crafted for mechanical strength and endurance, ideal for tasks like lifting, towing, or securing heavy items.
Despite their differences, both cable and wire rope serve crucial roles in today's technology and industry, each showcasing their unique design attributes and specialized uses.
Wire rope is a specialized mechanical assembly engineered for a range of heavy-duty lifting, rigging, hoisting, and tensioning applications. Compared to traditional wire or cable, wire rope features a complex construction—typically made up of several strands of high-strength steel, stainless steel, or other metal wires twisted around a central flexible core. Each strand in the rope contains multiple wires, providing strength, durability, and flexibility. For example, a 6x25 wire rope contains six strands with 25 wires each, resulting in 150 outer strands that move together but independently to enhance the rope's versatility, load distribution, and fatigue resistance in challenging environments.
A critical factor in wire rope design is the engineered clearance between strands, which allows each wire to shift slightly as the rope bends or flexes. This design feature improves performance under repeated bending cycles, making wire rope indispensable for construction cranes, elevators, winches, mining operations, bridge support cables, and many other industrial and maritime uses.
The essential components of wire rope are the individual wires, the strands (wires wound around a core), and the central core itself. The combination of these components—through a process known as wire rope fabrication or cable manufacturing—determines the final product's strength, resistance to crushing, flexibility, and suitability for various operating conditions.
The primary building block of wire rope is the wire, which can be made from several materials based on required mechanical properties such as tensile strength, ductility, abrasion resistance, and corrosion protection. Carbon steel, alloy steel, stainless steel, and galvanized wires are most commonly used in demanding environments due to their high breaking strength and durability. Other materials like aluminum, nickel alloy, bronze, copper, and titanium are selected for specialty applications where unique conductivity, flexibility, or environmental resistance is required.
Choosing the right type of wire is critical for performance—factors such as grade, diameter, finish (bright, galvanized, or coated), and fatigue resistance impact suitability for tasks like material handling, cable assemblies, support systems, and structural reinforcement.
Galvanized steel wire rope is coated with a protective layer of zinc to guard against oxidation, rust, and environmental corrosion. Galvanized wire rope offers long service life and lower maintenance costs, making it a popular choice for outdoor construction, marine, suspension bridges, tow cables, and general rigging applications where moisture is a concern.
Stainless steel wire rope provides all the mechanical benefits of galvanized rope with additional advantages—superior corrosion, rust, and chemical resistance. This makes it ideal for harsh environments such as offshore oil drilling, food processing, medical devices, and coastal or saltwater applications. Its low maintenance and long lifespan justify its higher initial cost for mission-critical duties.
General-purpose steel wire rope, available in multiple sizes, diameters, and strength grades, is the industry standard in manufacturing, transportation, forestry, and heavy equipment. Its balanced properties—combining strength, flexibility, and durability—make it the foundation for numerous wire rope slings, engineered cable systems, and architectural support structures.
To fully understand wire rope manufacturing, it's essential to recognize how different types are classified. Wire ropes are identified by strand construction, wire count per strand, lay pattern, and core type. For example, a common notation like 7x19 indicates seven strands with nineteen wires per strand. The rope's core may be a fiber core (FC), independent wire rope core (IWRC), or strand core (SC), each impacting flexibility, strength, and resistance to crushing or kinking.
Wire rope is also characterized by the arrangement, gauge (diameter), and tensile properties of the individual wires. A seven-wire rope (one central strand surrounded by six) offers simplicity and is suitable for light duty or flexible cable applications. Complex ropes—like 6x36 or 8x19 configurations—are engineered for maximum strength and resistance to fatigue, commonly used in cranes, elevators, and suspension applications.
Comprehension of wire rope nomenclature is fundamental for specifying ropes for critical uses in hoisting, rigging, load securement, or stay cables. The inner construction, specifically how wires, strands, and cores are layered, determines the rope’s overall mechanical properties and suitability for purposes like high-load lifting or abrasion-prone environments.
The foundation of wire rope manufacturing begins with wire strand production. Wires are helically wound around a central core wire to create a strand, with the number of wires determined by the required breaking strength, flexibility, and intended end use. Popular strand constructions—such as 1x7, 1x19, and 1x37—are tailored to provide the optimal balance of flexibility and abrasion resistance for various applications, including lifting slings, guy wires, and control cables. After forming, strands are precisely straightened to ensure consistent cable performance and to facilitate the next stage of wire rope fabrication.
Wire rope strands can be constructed with several distinct patterns—each designed to enhance specific rope properties, such as fatigue resistance, crushing resistance, or flexibility. Common strand patterns include centerless, single layer, multiple layer, Seale, Warrington, filler, and flattened strand designs. Understanding these patterns enables engineers and buyers to select the ideal strand construction for mining, marine, structural, and elevator applications, where operational demands vary significantly.
A centerless strand features all wires of identical diameter, twisted together into a helical shape. Centerless patterns are utilized in cable assemblies requiring maximum uniformity and surface contact between wires, maximizing fatigue resistance for repetitive bending or vibration exposure.
The single-layer strand design improves on the centerless pattern by wrapping wires around a single core wire, enhancing strength, structural integrity, and wear life. Suitable for overhead electrical conductors, suspension bridges, and broadcasting towers, this pattern provides even load distribution and improved flexibility.
Each wire in the single-layer strand maintains consistent diameter, ensuring predictable mechanical behavior under tensile and cyclic loads.
Multiple-layer strands consist of successive, concentric wire layers, with each tier precisely placed to achieve optimal contact and enhance crush resistance. This durable design is often chosen for heavy-duty winches, cranes, and hoisting applications, and is valued for its fatigue life and working load capacity.
In Seale pattern strands, smaller diameter wires wrap the central core, while the outer layer features the same number of wires but with larger diameters. This distribution provides a smooth exterior, enhances abrasion resistance, and is favored in elevator cables and applications subjected to drum winding or high-surface pressures.
The Warrington pattern resembles the multi-layered strand but utilizes alternating wire sizes—larger and smaller wires arranged to minimize gaps and improve load distribution. This pattern is commonly found in ropes used for cranes, hoists, and suspension cables, where balanced flexibility and durability are required.
Filler pattern strands use wires of identical size, with the distinguishing feature of small “filler” wires placed between the core and the outer layer. This maximizes metal cross-section and increases rope strength, making filler patterns ideal for tasks requiring enhanced load capacity and impact resistance.
Flattened strand, or triangular strand patterns, feature a core of three round wires and an outer surface pressed into a flat or oval shape. This design maximizes the metallic area, resulting in exceptionally strong ropes ideal for mining, structural suspension, and heavy lifting operations demanding minimal elongation and superior fatigue performance.
The core is the foundation of any wire rope, providing internal support, maintaining the shape of the rope, and assisting in load transfer. Cores are produced from a range of materials—synthetic fibers (like polypropylene and nylon), natural fibers (such as sisal or manila), a single strand, or an independent wire rope core (IWRC). The core’s material significantly impacts the rope’s strength, flexibility, resistance to crushing, and how well it absorbs and distributes lubricants.
Wire ropes with fiber cores offer increased flexibility but are typically used only for light loads and less severe conditions. Synthetic fiber cores, including polypropylene and nylon, deliver chemical resistance and consistent performance in environments exposed to moisture, chemicals, or moderate temperature changes. Natural fiber cores, while traditional, are best suited to dry environments where their tendency to absorb water won't lead to premature degradation.
Independent wire rope core (IWRC) constructions feature a wire rope core inside the main rope, maximizing resistance to compression, heat, and heavy dynamic loads. These wire rope assemblies are widely chosen for lifting and load-bearing in cranes, overhead hoists, and deep mining operations, where rope failure could have catastrophic consequences.
Wire rope with a strand core utilizes a solid strand—similar in size and construction to other strands in the rope—as the central support. Strand cores provide a blend of strength and flexibility, suited to general-purpose hoisting and support roles.
How wire ropes are twisted together—referred to as the “lay”—affects handling characteristics, resistance to abrasion, fatigue resistance, and ease of splicing or installation. The three main aspects of lay include direction (right or left), the relationship between wires and strands, and the linear pitch (the distance a strand covers in one revolution around the core). Lay is a key consideration when selecting lifting wire rope, winch lines, or structural cables to optimize safety, performance, and life span.
Right regular lay, left regular lay, Lang lay, and alternate lay are the primary constructions, each offering unique benefits for specific heavy equipment, crane cables, or marine rigging operations.
Regular lay wire rope, where wires and strands wind in opposite directions, is the go-to choice for general handling. Its construction simplifies splicing, reduces rotation under load, and ensures predictable behavior in lifting or pulling. However, the crowning wires are more exposed, increasing susceptibility to external wear in gritty or abrasive conditions.
Lang lay (or Albert lay) ropes feature wires and strands twisted in the same direction, producing a rope where the wires run nearly parallel to the axis. This design enhances wear life and lateral flexibility, ideal for draglines, shovel ropes, and applications involving repeated bending around drums or sheaves. Careful handling is necessary to avoid kinking or birdcaging (untwisting of wires).
Alternate lay wire ropes, combining both regular and Lang lays within the same rope, are used primarily for specialized and custom-engineered applications where unique load distribution or flexibility is needed. These are less common but essential for solving niche cable system challenges.
The following diagram provides an overview of every major step in wire rope manufacturing—covering material selection, wire drawing, strand formation, core integration, and final assembly of cable or rope products built to precise industry standards and quality-control specifications.
Wire rope coatings play a vital role in extending the service life of lifting wire ropes, control cables, and marine cable systems. Protective coatings shield the base wire from abrasion, corrosive chemicals, saltwater, UV rays, and impacts. Advances in coating technologies have led to high-performance solutions that optimize safety, reduce friction, and minimize maintenance for critical infrastructure and industrial machinery.
The industry's three primary wire rope coating options are polyvinyl chloride (PVC), polypropylene, and nylon—selected based on application requirements, temperature ranges, and exposure to chemicals or physical stresses.
PVC. or polyvinyl chloride, is the most widely used coating for general-purpose wire ropes and cable assemblies. It is cost-effective, water-resistant, provides good flexibility, and offers protection in temperatures ranging from -30°F (-35°C) up to 180°F (80°C). PVC coatings are chosen for a variety of industrial, automotive, and marine wire rope applications due to their reliable insulation and abrasion protection.
Polypropylene-coated wire rope is engineered for harsh and hazardous environments, offering exceptional chemical resistance, low moisture absorption, and high impact strength. This coating is ideal for ropes used in water treatment facilities, chemical processing plants, marine settings, and safety cable applications, where both abrasion and chemical exposure are significant concerns.
Nylon-coated wire rope offers the highest abrasion resistance, excellent flexibility at sub-freezing temperatures, and substantial protection against corrosion, impact, and harsh chemicals. With an operating temperature window of -65°F (-54°C) to 230°F (110°C), nylon coatings are frequently used in military, aerospace, and critical transportation cable systems, as well as color-coded cable assemblies for identification and enhanced safety.
Braided wires are electrical conductors and structural cable solutions produced by intertwining fine strands of copper, tinned copper, stainless steel, or other alloys to create a flexible, durable, and vibration-resistant wire braid. The braiding process results in a round tubular or flat tape configuration, each suited for unique application requirements. Braided conductors are critical in shielding for electronics, battery cables, ground straps, EMI/RFI suppression, and as flexible connections in high-vibration settings like the aerospace, defense, medical, and automotive industries.
Round tubular braided wire is chosen when spatial constraints demand a compact, high current-carrying cable that resists fatigue and breakage under mechanical stress. Flat braided wire—formed by flattening a round braid—provides greater surface area, flexibility, and is easily integrated as grounding straps, bonding leads, or shielded grounding in sensitive electronic assemblies. Experts recommend specifying the braid pattern, material, number of carriers, and construction for optimal electrical and mechanical performance.
For sourcing, design, or installation advice related to wire rope, lifting slings, control cables, and braided wiring solutions, always consult with reputable manufacturers or certified distributors. Selection should be based on a thorough understanding of safety standards, load requirements, environmental exposure, and the life cycle costs associated with each rope or cable system.
Wire rope, also referred to as steel cable or metal wire rope, is typically manufactured from various specialized alloys and metal grades to deliver optimal performance in demanding applications. The most commonly used metals include various grades of stainless steel wire rope, bright steel (carbon steel), and galvanized steel wire. These three materials are industry standards due to their balance of strength, flexibility, and resistance to harsh environments. However, some manufacturers also produce wire ropes and cable assemblies using specialty metals such as copper, aluminum, bronze, and Monel, which are utilized in specific industry niches such as marine, electrical, and aerospace sectors.
The most crucial aspect of wire rope design is the composition and quality of the underlying metal wire. The tensile strength, fatigue resistance, corrosion resistance, and flexibility of a wire rope largely depend on the type and grade of metal used during production. For this reason, choosing the appropriate wire rope material is essential for maximizing safety, load-bearing capabilities, and longevity, especially when evaluating wire rope for lifting, hoisting, rigging, marine, or construction applications. Always consult performance specifications and material compatibility requirements when purchasing wire rope products.
Bright steel wire rope is manufactured from high-strength carbon steel wires drawn from hot-rolled steel rods. Unlike galvanized steel wire or stainless steel, bright steel wire lacks a protective coating—resulting in a “bright” finish with a smooth surface. Designed to be rotation-resistant, bright steel cables are engineered to maintain load stability and minimize spin when lifting or hoisting heavy weights. The absence of a coating allows for precision processing through dies, achieving tight dimensional tolerances and excellent mechanical properties for demanding industrial operations. Common applications for bright steel wire rope include overhead cranes, winches, elevators, and material handling equipment where internal environments minimize the risk of corrosion, and where high tensile strength and resistance to cabling (twisting) are required.
Galvanized steel wire rope is characterized by a zinc coating applied through a galvanization process. This technique creates a rust-resistant barrier while maintaining strength and durability consistent with bright steel wire. Galvanized steel is widely used for its ability to withstand moderate outdoor exposure, making it ideal for construction, marine, and utility applications. In environments subject to moisture, humidity, or intermittent harsh weather, galvanized wire rope provides enhanced corrosion resistance over plain carbon steel—making it a reliable and cost-effective alternative to stainless steel in many scenarios.
During the wire rope manufacturing process, each steel strand is galvanized to deliver exceptional resistance to rust, abrasion, and mechanical wear. These properties make galvanized wire rope flexible and long-lasting, well-suited to applications such as guy wires, fencing, rigging, cable railings, and support strands in infrastructure projects. For extended outdoor use or coastal environments, however, evaluating higher grades of zinc or specialized coatings may be necessary for optimal service life.
Stainless steel wire rope is a top choice where superior resistance to rust, corrosion, staining, and chemical exposure is essential. While stainless steel may offer slightly lower tensile strength than bright steel or galvanized options, its non-corrosive nature ensures exceptional performance in marine, architectural, food processing, pharmaceuticals, and corrosive industrial settings. The most common alloys include 304 and 316 stainless, with 316 stainless steel delivering enhanced corrosion protection in saltwater, acidic, or chloride-laden environments.
Although stainless steel is generally more expensive, its benefits—such as extended lifespan, low maintenance requirements, clean appearance, and reliability in both indoor and outdoor environments—far outweigh the initial investment for critical projects. This makes it highly suitable for cable rail systems, balustrades, boat rigging, suspension bridges, and any application where both durability and aesthetics are priorities.
Copper wire rope is primarily used in specialized electrical and electromagnetic applications due to its outstanding electrical conductivity and moderate corrosion resistance. It delivers unique benefits such as excellent flexibility, durability under vibration, and resilience against fatigue, which often surpass those of standard copper wire. As a result, copper wire rope is ideal for use in environments subject to continual shaking, bending, or movement—such as electrical grounding, flexible current-carrying cables, and telecommunications. While less common than steel alternatives, copper and copper alloy rope find critical roles in industries like aerospace, zero-interference grounding, and specialty electronics, where electromagnetic shielding and conductivity are paramount considerations.
When sourcing wire rope for your next project, consider key performance factors such as strength, corrosion resistance, flexibility, environmental exposure, and compliance with industry standards. Selecting the right metal alloy and wire rope construction ensures the optimal combination of safety, service life, and value to best suit your specific use case.
The lubrication of wire rope starts during its fabrication and continues throughout its use. The purpose of lubrication is to reduce friction and provide protection against corrosion. Ongoing lubrication helps extend the lifespan of wire rope by preventing it from drying out, rusting, and breaking.
There are two main types of lubricants for wire rope: penetrating and coating. Coating lubricants cover and seal the exterior of the rope, while penetrating lubricants penetrate deeply into the rope, reaching the core. Once inside, penetrating lubricants evaporate to form a thick coating or film.
The method of applying lubricant depends on the type of core used in the wire rope. For fiber cores, the lubricant is absorbed and acts as a reservoir, maintaining lubrication over a long period. In contrast, with metal cores, the lubricant is applied during the twisting process of the wire into strands, ensuring thorough saturation and coverage of the wires.
Petrolatum compounds are translucent and offer excellent resistance to corrosion and water. While they may drip off at high temperatures, they maintain their consistency in cold conditions. Petrolatum is a hydrocarbon mixture derived from the distillation of petroleum and belongs to the methane family of hydrocarbons. It can be used in both semi-solid and liquid forms, with the semi-solid form taking on a jelly-like consistency.
Asphaltic compounds are made by combining mineral-based oil with bitumen to produce a tacky, high-viscosity lubricant with an undiluted consistency. These lubricants create an oil film that separates the mating surfaces and are typically applied as a spray. When applied, the solvent evaporates due to the meshing of surfaces, leaving behind a thick, viscous coating of lubricant.
Several types of greases are used as lubricants for wire rope, consisting of oil, a thickener, and additives. The key components are the base oil and additives, which determine the grease's performance. The thickener keeps the base oil and additives combined. Typically, grease contains between 70% and 95% base oil, with about 10% additives.
Additives in grease enhance the positive properties of the oil while mitigating its negative aspects. Common additives include oxidation and rust inhibitors, as well as agents that reduce pressure, wear, and friction.
Greases used for wire rope are typically soft and semifluid. When applied with a pressure lubricator, they form a coating that partially penetrates the rope.
Among various lubricant options, vegetable oil is the easiest to use and offers the deepest penetration. The additives in vegetable oils are specifically designed to provide the qualities needed for deep penetration into wire rope. This exceptional penetration helps protect against wear and corrosion. Additionally, because vegetable oil is fluid, it effectively washes the wire rope, removing external abrasive contaminants.
Wire rope is extensively used in machinery, structural applications, and various lifting tasks. The type, size, and specifications of wire rope are tailored to its intended use. Regardless of the application, wire rope ensures exceptional strength, high quality, and outstanding performance.
For centuries, lifting heavy loads relied on hemp rope or chains, neither of which provided a consistently reliable method. In the early 19th century, between 1824 and 1838, Wilhelm Albert, a German mining engineer, combined the twisting of hemp with the strength of chains to develop the modern wire rope.
Since its inception, wire rope has undergone significant advancements, resulting in the diverse range of varieties used in industrial applications today.
The most common use of wire rope is as a part of a crane hoist (*Discover Hoist Crane Manufacturers) wherein it is attached to the hook of the hoist and wrapped around a grooved drum. The tensile strength and durability of wire rope makes an ideal tool for lifting and keeping loads secure. Though it is used in several industries, it is very popular for production environments wherein materials need to be lifted quickly and efficiently.
Beyond its numerous lifting applications, wire rope's strength and stability make it valuable in other fields, particularly in the aerospace industry. In aircraft cockpits, wire rope connects pedals, levers, and connectors, facilitating the transmission of power between systems and mechanisms to control the aircraft. It is used to manage propeller pitch, cowl flaps, and throttle operations, and it also helps in reducing and dampening vibrations.
Wire rope is used to reinforce tires, enhancing their durability and strength. In automotive production, wire rope plays a crucial role in supplying materials, moving heavy loads, and positioning equipment. It is also integral to the manufacturing of various components, including steering wheels, cables, exhaust systems, springs, sunroofs, doors, and seating elements.
It might be surprising, but wire rope is most widely used in the home, where its strength, durability, and resilience offer reliable protection and performance. One of the main reasons for its popularity in residential settings is its cost-effectiveness.
Inexpensive, readily available, easy to install, and simple to maintain, wire ropes offer a practical solution for home repairs and structural support. Their flexibility and durability, coupled with their discreet appearance, make wire rope ideal for various home maintenance tasks. It is commonly used to support staircases, fences, decks, and to hang plants.
For centuries, wire ropes have been essential in the search and production of crude oil, used for lifting drill bits, inserting shafts, and supporting oil rigs both on land and at sea. Wire ropes are crucial for lowering equipment, machinery, and tools into the depths of the earth and ocean, making them indispensable to the oil industry.
Oil production tasks often involve tools that must endure severe and harsh conditions. Wire ropes are designed to withstand immense pressure, extreme stress, and a broad range of temperatures. They play a crucial role in maintaining the stability of oil rigs and securing moorings for offshore platforms.
Wire rope has been a fundamental element in the transportation industry for many years, from the iconic cable cars of San Francisco to lift chairs at ski resorts. Heavy-duty wire ropes are used in cable cars, where they are pulled by a central motor from various locations. This method of transportation has been in use for centuries.
In Europe, funiculars use cables suspended from supports to move cars up and down mountains, with cables operating in opposite directions. The term "funicular" derives from the French word "funiculaire," which means "railway by cable." The term "funicular" itself comes from the Latin word "funis," meaning rope. In professional contexts, the terms "wire rope" and "cable" are often used interchangeably.
The major use for wire ropes in the food and beverage industries is as a means for lifting and moving heavy loads. Wine barrels and containers full of ingredients are lifted and placed through use of cranes and wire ropes. They are also part of conveyor systems (*Discover Conveyor System Manufacturers) that move products from one station to another.
From the early days of amusement rides to modern attractions, wire ropes have been crucial in both construction and safety. They are used to pull roller coaster cars, support swinging cabins, and move carriages through haunted houses. Ensuring safety is a primary concern for amusement parks, and the strength, stability, and reliable performance of wire ropes play a key role in providing a safe and enjoyable experience for visitors.
In modern movies, wire rope is essential for safely executing stunts. These strong steel cables, composed of multiple smaller strands, are used to suspend actors, create dynamic car chases, and perform thrilling aerial maneuvers. Their strength and ability to handle heavy loads make stunts both safe and reliable. Experts meticulously calculate the tension and angles of the cables to ensure performers' safety. Often hidden from view, these cables play a crucial role in making dangerous scenes appear realistic.
In live theater, wire ropes are essential for raising and lowering curtains, supporting overhead rigging, and securing backdrops and scenery. They provide strong, reliable support for various aspects of a performance, ensuring that actors, scenery, and equipment are lifted smoothly and securely. Whether used for aerial stunts or set changes, wire ropes contribute to the seamless execution of productions. Their durability and flexibility allow creative directors to push the boundaries of their designs while maintaining safety. In live theater, wire ropes play a vital yet discreet role in making stage performances both magical and secure.
Wire rope is often perceived as indestructible and immune to damage due to its exceptional strength and durability. However, despite its robustness and ability to withstand constant use, it is still susceptible to wear and breakdown like any other tool.
To prevent serious harm and damage, wire ropes should be regularly inspected. Understanding the potential situations that can cause damage or breakage is crucial to addressing issues before they arise.
Guide rollers can cause damage and abrasions to wire rope if they become rough or uneven. Since guide rollers have the most contact with the wire rope in a crane or lift, regular inspections are essential to ensure they are not harming the rope or causing abrasions.
Bending is a typical aspect of wire rope usage, occurring repeatedly as the rope passes through a sheave. This constant bending can lead to the development of cracks or breaks in the rope. The damage is worsened by the rope's movement on and off the drum groove. Initially, the breakage usually appears on the surface and is visible. Once surface cracks form, they can quickly progress to the core of the rope.
A birdcage break refers to a specific pattern of wire rope damage that resembles a birdcage or mesh structure. This type of damage is characterized by wires unraveling or fanning out from the main body of the rope, creating a cage-like appearance.
This type of break is a major concern in industries that rely on wire ropes for lifting, rigging, and other critical applications. It can severely compromise the structural integrity of the rope and present a significant safety hazard.
Localized wear occurs due to contact with the sheave and is often hard to detect without a thorough inspection of the rope. This wear can be caused by friction, abrasion, corrosion, or other forms of mechanical stress. It is a significant concern because it can weaken the wire rope and potentially lead to failure if not identified and addressed promptly.
Regular inspections, maintenance, and proper lubrication are essential for identifying and addressing localized wear issues. If significant localized wear is found, replacing the affected section of the wire rope may be necessary to ensure safe operation.
Drum crushing, also referred to as drum compression or drum bulging, occurs when wire ropes are wound or spooled onto a drum or reel, especially under high tension. This typically happens when the rope is wound onto a drum with a diameter smaller than the minimum recommended bending diameter for the rope. Drum crushing can damage the wire rope, potentially compromising its strength and integrity.
Wire ropes are designed with multiple layers, providing flexibility and torque balance. This layering enhances both flexibility and wear resistance. However, the relative motion between the wires can cause wear over time, leading to internal breakage. To detect these internal breaks, an electromagnetic inspection can be used, which measures the diameter of the rope and identifies potential issues.
Kinks in wire rope can occur when the rope is subjected to excessive twisting, bending, or torque forces beyond its design limits. They can also result from improper handling, coiling, or spooling of the wire rope.
Kinks in a wire rope are a serious concern because they can weaken the rope and diminish its load-bearing capacity. The sharp bends created by kinks lead to stress concentrations, making the rope more vulnerable to breaking or failing under load. Additionally, kinked wire ropes are more susceptible to abrasion and wear, as the kinks can cause the rope to rub against itself or other surfaces.
Regular inspections should be carried out to detect any signs of kinking or other damage. Damaged wire ropes should be replaced promptly to ensure safety and maintain optimal performance.
Corrosion damage is one of the most challenging types of wire rope damage to identify, making it particularly dangerous. It is a persistent issue in industries such as maritime and construction. Corrosion occurs when the metal wires in the rope react with environmental factors like moisture, saltwater, or chemicals, causing gradual material degradation. Over time, this weakening reduces the rope's load-bearing capacity and compromises safety.
Rust and pitting are common visual signs of corrosion, highlighting the importance of routine inspection and maintenance. To mitigate the impact of corrosion, preventive measures such as galvanization, protective coatings, and proper storage are employed. These measures help ensure the longevity and reliability of wire ropes in critical applications.
The types of damage and problems mentioned are just a small fraction of the issues that can arise from insufficient lubrication and inspection of wire ropes. Various regulatory agencies mandate that wire ropes be inspected on a weekly or monthly basis and provide detailed guidelines on the factors to examine.
Like any heavy-duty equipment, wire rope must comply with specific regulations and standards to ensure safety and quality. The American Society of Mechanical Engineers (ASME) and the Occupational Safety and Health Administration (OSHA) are the primary organizations that set guidelines for wire rope use.
ASME is a professional association that establishes guidelines to advance the engineering profession. OSHA is a government agency dedicated to protecting workers and ensuring their safety.
Wire rope manufacturers and users closely adhere to the standards and guidelines established by OSHA and ASME. Typically, they specify the particular standards they follow concerning their products.
OSHA's regulations for wire rope are detailed in sections 1910, 1915, and 1926, with the majority of the requirements found in section 1926, which covers material handling, storage, use, and disposal.
Covered in 1926 are:
Guidelines for wire rope inspection are outlined in the B30.30 Ropes Standard.
ASME B30.30-1.8.1(b) specifies the requirements for frequent inspections of wire ropes.
ASME B30.30-1.8.1(b) states: "Running rope in service shall be visually inspected daily, unless a qualified person determines it should be inspected more frequently. The visual inspection should cover all sections of the rope that are likely to be in use during the day's operations, with a focus on identifying any gross damage that could pose an immediate hazard."
According to ASME B30.30 guidelines, inspectors should check for:
ASME B30.30-1.8.1(c) outlines the requirements for periodic inspections.
ASME B30.30-1.8.1(c) states:The frequency of periodic inspections should be determined by factors such as the rope's service life in the specific installation or similar installations, the severity of the environment, the percentage of capacity lifts, the frequency of operation, and exposure to shock loads. Inspections do not need to be at equal calendar intervals and should be conducted more frequently as the rope nears the end of its useful life. A close visual inspection of the entire length of the rope is required to assess its condition and determine whether it should be removed from service.
According to ASME B30.30 guidelines, inspectors should look for:
Repetitive Wear Sections
Known Wear Areas Based on Previous Experience with the Machine Being Inspected
Locations Where Rope Vibrations are Damped
AASTM A1023 outlines the requirements for steel wire ropes, specifying various grades and constructions ranging from ¼ inch (6 mm) to 3½ inches (89 mm), and includes options for both uncoated and metallic-coated wire. The standard also covers cord products from 1/32 inch (0.8 mm) to 3/8 inch (10 mm) made from metallic-coated wire.
ASTM A1023 covers:
United States Federal Specification RR-W-410 addresses wire ropes and wire seizing strands but does not encompass all available types, classes, constructions, and sizes. Its purpose is to cover the more common types, classes, constructions, and sizes that are suitable for federal government use.
The wire rope and wire seizing strands specified in United States Federal Specification RR-W-410 are intended for general applications such as hauling, hoisting, lifting, transporting, well drilling, and use in passenger and freight elevators, as well as for marine mooring, towing, trawling, and similar tasks. These specifications do not cover applications involving aircraft.
API 9A specifies the minimum standards for wire ropes used in the petroleum and natural gas industries. It covers a wide range of applications including tubing lines, rod hanger lines, sand lines, cable-tool drilling and clean-out lines, cable tool casing lines, rotary drilling lines, winch lines, horse head pumping unit lines, torpedo lines, mast-raising lines, guideline tensioner lines, riser tensioner lines, and mooring and anchor lines. Additionally, API 9A includes standards for well servicing wire ropes, such as lifting slings and well measuring ropes.
Additional specifications for wire rope can be obtained from the Wire Rope Technical Board and Associated Wire Rope Fabricators.
An aircraft cable is a style of highly durable cable that is used for aircraft flight controls and other applications and is differentiated from normal cables by its diameter, stranding, and wires, which provide...
A push pull cable control is used for the transmission of multi directional precision control of mechanical motion. The many varieties of push pull cables or controls are adaptable to a wide range of applications and...
Stranded wire refers to thin bundled up wires that are compressed and covered up in insulating material. Stranded wires are more flexible thus making them very ideal for joining electronic circuit components in confined spaces where their bending...
A wire rope assembly is composed of wire rope and end fittings, terminals, or lanyards that are attached to various parts of the wire rope such that the assembly can be used to lift, hoist, and move loads. The various types of...
Wire rope is constructed of multiple strands of wire that are twisted and braided together to form a spiral design or helix. Once the separate wires are shaped into a solid form, they become a single wire with greater strength because...
A bungee cord is a rope that is composed of two or more elastic strands coated with a woven fabric. It has hooks that are placed on both ends. A bungee cord is also known as shock cord and elastic cord...
Cordage is a series of intertwined fibers, strands, strings, or fabric that are joined by twisting or braiding to form a larger more formidable whole. The combination of the materials makes the final, larger strand stronger than its individual pieces...
Electric hoists are material handling equipment used for lifting, lowering, and transporting materials and products. They are powered by an electric motor and have a controller to adjust the lifting parameters...
A gantry crane is an overhead crane that has an overhead beam supported by freestanding legs and moves on wheels, a track, or rail system carrying a bridge, trolley, and hoist. Workshops, warehouses, freight yards, railroads, and shipyards use gantry cranes as their lifting solution as a variation of overhead or bridge cranes...
Rope is a collection of strands, fibers, piles and yarns joined together to form a strong and a large structure. These strands or fibers are either twisted or braided with one another to give high tensile strength to the rope...
A hydraulic lift is a device for moving objects using force created by pressure on a liquid inside a cylinder that moves a piston upward. Incompressible oil is pumped into the cylinder, which forces the piston upward. When a valve opens to release the oil, the piston lowers by gravitational force...
A jib crane is a lifting device with an arm or boom that extends off the main body of the crane to provide extra reach and has a lattice design to lower the weight added to a load. The design of jib cranes allows them to work...
A lift table is a platform capable of holding materials and raising, lowering, and adjusting them to any height to meet the needs of an application and the user’s requirements. Lift tables are supported by a strong, rigid, and stable base frame placed flat on the floor, in a pit, or equipped with casters or wheels...
An overhead crane is a type of heavy duty machinery that is capable of moving extremely heavy loads and equipment from one location to another in a safe and precise manner using the overhead space of a manufacturing facility. Due to the nature of the work they perform...
Scissor lifts are a type of manlift that is commonly used in construction and facility maintenance to raise employees and their tools to working heights. A power system and a control system make up the scissor lift...
A hydraulic system is based on Pascal‘s principle of fluid pressure, which hypothesizes that a change in pressure in a fluid is transmitted to all points of the fluid in all directions. With a hydraulic lift, an electrically powered pump pushes fluid into a cylinder at the base of a lifting jack system that lifts the platform up and down...