Push Pull Cable Controls
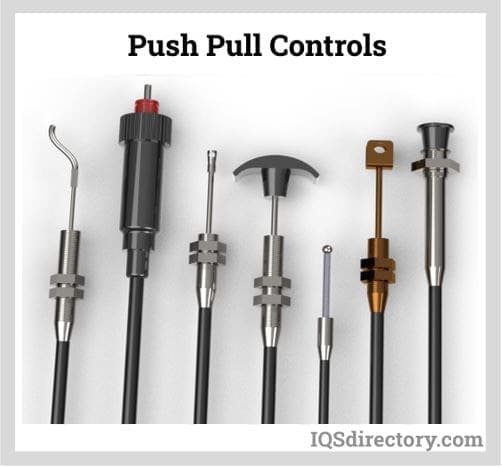
A push pull cable control is used for the transmission of multi directional precision control of mechanical motion. The many varieties of push pull cables or controls are adaptable to a wide range of applications and...
Please fill out the following form to submit a Request for Quote to any of the following companies listed on
The content of this article is everything you need to know about aircraft cables and their use.
You will learn:
Aircraft cable is a specialized, robust wire frequently employed in aviation to manage flight systems and other high-demand applications. What sets it apart from standard cables is its unique design, which encompasses factors such as thickness, material makeup, and the arrangement of strands. These characteristics endow the cable with both durability and flexibility. The term "aircraft cable" generally describes cables that are under 0.375 inches in diameter, typically constructed in either a 7x7 or 7x19 configuration using galvanized or stainless steel. The hallmark of this cable is its high tensile strength, ranging from 120 pounds to as much as 14,400 pounds (54 kg to 6532 kg).
Aircraft cables are crafted using techniques similar to those used for standard cables or wire ropes. They are made by twisting individual wires in a precise helical pattern to form strands. Adding more strands and increasing the number of wires per strand results in enhanced flexibility of the cable. Additionally, as the cable's diameter increases, the thickness of individual wires also grows, leading to a greater overall breaking strength.
Aircraft cables find applications across various sectors, including industry, shipping, commercial use, and even residential settings. Their strength is derived from the individual strands and wires that make up the cable. The most commonly used materials for creating these strands are galvanized high-carbon steel such as A1S1 C1050 and C1070, along with stainless steel from the A1S1 302 and 304 series.
What sets aircraft cables apart from other cable types is the number of strands and wires per strand they contain. Typically, aircraft cable diameters range from 0.03125 inches to 0.375 inches (0.79 mm to 9.5 mm) and are built using a 7x7 or 7x19 pattern. The wire core is usually identical to the outer strands. These cables are composed of strands of wire wrapped around a central core, with each strand consisting of wires twisted around a central filament.
The resulting strands are wound helically around a central core. The classification system for aircraft cables involves two numbers: the first represents the number of strands, and the second indicates the number of wires per strand. A common example is a 7x19 aircraft cable, which means it consists of 7 strands with 19 wires in each strand.
Another type of aircraft cable is the 7x7 variety, consisting of seven strands twisted around a core made of seven wires, with each strand also containing seven wires. The variation in wire count between 7x7 cables gives them distinct characteristics. Despite the difference in wire numbers, both 7x7 and 7x19 cables are flexible, as higher wire counts enhance their ability to bend, making them suitable for various cable systems. The 7x19 cable, with its higher wire count, is ideal for applications requiring frequent movement, while the stiffer 7x7 cable is preferred for aircraft installations.
The initial stage in constructing aircraft cables involves twisting galvanized or stainless steel wires into strands. For these cables, 6 or 18 wires are coiled in a helical shape around a central wire to form a strand. The flexibility and axial stiffness of the strand are influenced by the pitch of this helical winding. Aircraft cable strands can be wound in either a left or right direction, which refers to the orientation of the stranding.
The spiral or helix formed during the winding of wires to create strands is known as the "lay." Aircraft cables with 7x7 or 7x19 constructions are typically wound with a right-hand lay. If the wires twist in a clockwise direction, it is called a right lay; if twisted counterclockwise, it is a left lay. The term "lay length" measures the linear distance a wire covers during one complete rotation.
The core of an aircraft cable serves as its backbone, consisting of a single strand constructed in the same way as the outer strands. This core bears the compressive forces applied to the cable and runs through its center. It plays a crucial role in supporting the outer strands, helping them stay in place when the cable is bent or subjected to tension.
The strength, flexibility, and resilience of an aircraft cable rely on the combined efforts of the core and outer strands to withstand the stress of loads and continuous bending. While various core types can include materials like rods or fabrics, aircraft cable cores are always made from a strand identical to the outer strands to ensure the cable’s strength and longevity.
The construction process of an aircraft cable follows the same steps as those used for creating the individual strands, incorporating either right or left lays. Just as with strand winding, the direction of the lay in the strands is essential to the cable's overall strength.
During the manufacturing process, each strand is preformed into its helical shape, ensuring that it fits properly when assembled into the final cable. This preforming technique enhances the cable's flexibility and helps reduce tension as the strands are woven together. Additionally, as the strands are twisted into the cable, they are lubricated to minimize friction and protect against corrosion.
There are two main types of lubricants used for aircraft cables: penetrating and coating. Penetrating lubricants, which contain a petroleum solvent, reach the cable's core, evaporating after application and leaving a protective layer on each strand. Coating lubricants, on the other hand, create a protective barrier around the outer strands, shielding them from moisture, wear, and rust. Typically, both types are applied to ensure the core is fully lubricated and protected
The last stage in the production of aircraft cable involves winding it onto a spool for distribution. Depending on the manufacturing process, assemblies or terminations may be attached to the cable ends in anticipation of its final application. Given the diverse range of uses and customizations, most manufacturers typically do not include these assemblies unless the cable is specifically tailored for a particular purpose.
The robustness and longevity of aircraft cables make them suitable for numerous applications. An important aspect of their functionality is how they are connected to their specific use. Given the diverse and unique applications of aircraft cables, the terminals and assemblies used can vary significantly in form, shape, and size.
There are two primary types of terminations: loops (or eyes) and fittings. Loops are created through methods such as splicing with a swaged sleeve, hand-tucked splices, or wire cable clips. Fittings are attached to the cable using techniques like swaging, bonding with molten zinc or resin, or employing a wedge. Aircraft cable terminations and assemblies come in many different shapes, sizes, and materials, including button stops, thimbles, shank balls, spelter sockets, and turnbuckles.
Loop sleeves, also known as cable crimp sleeves, are the most commonly used components for creating cable loops. These sleeves are specifically engineered for cable assemblies, allowing for the formation of loops of various sizes or the attachment of separate sections of aircraft cable. Available in a wide range of sizes, shapes, and materials, loop sleeves cater to diverse applications. They come in designs such as cylindrical or figure-eight and can be applied using manual hand tools or industrial presses. Typically made from stainless steel, loop sleeves are crimped or pressed onto the cable to create the loop.
Ball and shank end fittings feature a spherical design and are crimped onto the end of an aircraft cable to fit into a corresponding socket. These fittings have a central hole passing through the ball and are typically made from stainless steel. The shank portion, which is attached to the ball, is crimped onto the cable. Ball and shank end fittings are utilized in applications where the strength of the cable termination exceeds that of the cable itself.
Strap fork terminations are used alongside ball and shank end fittings, allowing the forks to swivel freely. This design helps to accommodate end loads that twist, reducing unnecessary stress on the cable. The spherical part of the ball and shank end fitting enables the strap fork to rotate, while a shoulder on the fitting provides added protection for the cable.
A strap eye termination functions similarly to a strap fork, as it attaches to a shank ball rather than being directly connected to the cable, which permits rotation without placing undue stress on the cable. However, unlike strap forks, strap eyes feature their forks welded together to create a slimmer profile, allowing them to fit into tighter spaces.
Cable thimbles are used in conjunction with loops to support and protect the cable, particularly around the inner lining of the loop. They reinforce the loop or eye by providing a solid metal barrier that helps prevent fraying due to friction and load pressure. The cable is wrapped around the thimble's groove, and once positioned securely, the loop is crimped near the bottom of the thimble. With the extensive use of cable loops, thimbles are available in a range of sizes to accommodate various sizes of aircraft cable.
Threaded terminals are designed to enhance tension on an aircraft cable through the use of a locking nut, rigging screw, or turnbuckle. These terminals are either swaged or pressed onto the cable and feature either left-hand or right-hand threads. They are frequently employed to achieve precise tension in aircraft assemblies. When paired with a turnbuckle, threaded terminals allow for adjustments to the cable's length and tension.
Turnbuckles are used in conjunction with threaded terminals to adjust the length and tension of aircraft cables. They facilitate the connection of multiple cable segments to form a longer cable. Turnbuckles feature threads at both ends for attaching threaded terminals. Rotating the turnbuckle increases the tension in the connected terminals and their respective cables.
Turnbuckles are versatile and can be adapted for various applications, available with hooks, eyes, and different types of fittings. They are designed with threading that is typically left-handed to ensure smooth and easy engagement with right-handed threads.
Eyelets feature a round end with a central hole designed for connecting screws, bolts, or clevis pins. They serve as attachment points and are commonly made from aluminum, stainless steel, or carbon steel. Like other aircraft cable terminations, eyelets come in various sizes. They are typically produced through stamping and have a sleeve attached to their round, O-shaped section, allowing them to be swaged onto aircraft cable.
Cable clips serve a function similar to loop sleeves, being used to form cable loops and connect cables. A cable clip consists of a U-shaped bolt with threaded ends, a saddle, and two bolts. To secure an aircraft cable, the U-bolt is positioned over the cable, usually near the end, with the saddle placed over the bolt ends. The bolts are then tightened to ensure the cable remains fixed in place and does not shift or twist.
Among the various cable and wire rope products, aircraft cable stands out for its combination of thinness, strength, and flexibility, making it exceptionally reliable and versatile. The cable’s construction of fine steel wires provides the durability needed for a wide range of applications. Stainless steel aircraft cable is particularly suited for demanding environments due to its corrosion resistance and ability to endure extreme temperatures. In contrast, galvanized steel aircraft cable, while less costly, offers comparable strength and is typically used in less severe conditions.
Aircraft cable lanyards, crafted from galvanized or stainless steel, are valued for their exceptional strength, durability, and longevity. These lanyards are commonly used to secure pins and fasteners, prevent loss, and act as tethers for components and door restraint cables. Their resistance to wear makes them particularly suitable for lanyard applications, and they are frequently utilized in military and marine settings. Like other aircraft cables, lanyards can be equipped with various terminations, including hooks, loops, and eyelets.
Aircraft cable is essential in aviation for securing aircraft and cargo due to its remarkable durability. It is commonly used to control various aircraft components and connections, including the rudder, engine systems, and emergency systems. Additionally, aircraft cable plays a crucial role in the operation of landing gear, enabling it to be raised and lowered as needed.
Ensuring cargo stability during transport is crucial for shipping companies, as damaged goods can lead to significant financial losses. Aircraft cables are employed to secure and restrain cargo, preventing it from shifting. Their suitability for this purpose is due to their manageable size, which facilitates easy handling, installation, maintenance, and shaping.
Wires and cables used in maritime environments need special protection against the corrosive effects of salt water. Stainless steel series 316 is typically preferred for these applications due to its excellent resistance to pitting corrosion, which is common in marine settings. Aircraft cable is widely used for various maritime purposes, including hoisting, securing boats and docks, rigging for sailboats and fishing boats, and operating winches and pulleys.
Pulleys and winches are subjected to significant stress, torque, and tension while in operation. Designed to lift and move heavy loads, these mechanisms require cables that are exceptionally strong and rigid. Aircraft cable, with its remarkable strength, is ideally suited for use with pulleys and winches. It withstands constant strain and tension with great resilience and durability.
In the entertainment industry, the lifting of heavy backdrops, scenery, and curtains is essential for the presentation of shows and plays. To ensure both performance and safety, the equipment used for hoisting and moving these bulky items must be secure, strong, and capable of handling substantial loads. Aircraft cable is therefore a preferred choice for stage managers and crew members, providing reliable and efficient movement of props and other heavy elements during performances.
While not classified as dramatic performances, zip lines have become a popular form of entertainment in recent years. They transport tourists across caverns, canyons, valleys, and between mountain points. Due to safety concerns, including insurance requirements, zip lines must be exceptionally secure and durable. During peak tourist seasons, they are in constant use and undergo daily inspections and maintenance. Aircraft cable is often chosen for zip lines not primarily for its weight capacity but for its durability under frequent use, which helps it withstand wear better than many other types of cable.
Aircraft cable is frequently used in the operation of garage doors, offering a time-saving solution for their lifting and opening. Garage door openers utilize a chain drive system that gradually pulls or releases a cable connected to the door. Despite the smooth and gradual operation of the mechanism, the weight and angle of the garage door place significant tension and strain on the lifting cable. Aircraft cables are ideally suited for this application due to their ability to handle such stress effectively.
The exercise and fitness industries have experienced significant growth in recent years due to increased focus on health and physical activity. Unlike the past, when exercising mainly involved lifting weights, jogging, and stretching, today's gyms and home fitness setups feature a diverse array of equipment that has evolved beyond traditional barbells and medicine balls. Modern exercise machines often use adjustable cables to change weights and lifting angles. Aircraft cables are integral to these mechanisms, providing reliable connections in weightlifting equipment and other commercially available fitness devices found in gyms.
While all aircraft cables share fundamental characteristics, variations in their manufacturing process distinguish one type from another. Differences can include the type of metal used, coatings, lubricants, and other factors that contribute to the uniqueness of each cable. When selecting aircraft cable, it's crucial to understand these distinctions to ensure that the cable chosen is suited to the specific application for which it is intended.
Aircraft cable is available in both galvanized steel and stainless steel, with the choice of metal depending on the intended use and cost considerations, as stainless steel is more expensive than galvanized steel. Stainless steel cables are preferred for harsh and hazardous environments where exposure to chemicals and moisture is a concern. In contrast, galvanized steel cables are suitable for less severe conditions without such exposure. Both types are manufactured using similar winding processes, including 7x7 and 7x19 constructions.
Push-pull aircraft cables are designed to control movement in both directions and are built to withstand wear and various weather conditions. They operate equipment through mechanical force and are tailored to meet specific application requirements. The design of push-pull cables allows them to transmit motion and force effectively over any distance. Due to their strength, reliability, and durability, push-pull aircraft cables are used in a wide range of applications.
Connector cables represent a prevalent application of aircraft cables, offering robust, reliable, and durable connections. The effectiveness of these cables is determined by the tension they withstand and their ability to handle linear movement. Aircraft cables are designed to be compatible with most standard terminals and are built to perform reliably in various environments.
Aircraft cables, regardless of the metal used, can be coated with materials such as polyvinyl chloride (PVC), nylon, or high-density polyethylene (HDPE) for added protection. These coatings help maintain the shape of the cable strands and modify its external profile. Coatings serve several purposes, including enhancing protection, improving ergonomics, providing aesthetic appeal, and increasing visibility.
The coating process involves extrusion, where resin pellets are melted in an extruder. The melted resin coats the aircraft cable as it is fed through the extruder. To ensure uniform coverage, a pulley system maintains tension on the cable as it passes through the liquid resin.
Aircraft cable stands out from other types of cable primarily due to its remarkable strength and durability under extreme conditions. In addition to this exceptional quality, aircraft cable possesses other attributes that make it highly suitable for demanding applications.
Since its inception, aircraft cable has withstood a variety of demanding conditions, including tension, acceleration, load shocks, bending, and various external forces. Despite these intense stresses, aircraft cable has consistently demonstrated exceptional durability and performance.
The safety factors of aircraft cable are determined by comparing its strength to the workload it is subjected to. This ratio indicates the cable's safety margin. Typically, aircraft cable can withstand several times its rated workload, ensuring a high level of safety and reliability.
A frequent issue with wire rope and cable is fatigue, which manifests as cracks from repeated bending. This problem usually arises when cables are flexed over surfaces and subsequently straightened. As fatigue progresses, the bending of the cable’s wires eventually leads to breakage. In contrast, aircraft cables feature a flexible construction with smaller wires, which helps mitigate the effects of fatigue and enhances their durability.
The durability of aircraft cable against abrasive wear is largely attributed to the quality of the wires used in its construction. Despite its inherent flexibility, which can make it more susceptible to abrasion, proper use and maintenance significantly impact its resistance to wear. Higher-grade galvanized and stainless steel wires provide the necessary strength and resistance to effectively counteract abrasive forces.
The terms "wire rope" and "cable" are often used interchangeably, but they actually refer to distinct types of wound wire products. The primary difference between them is their size. Aircraft wire is smaller in diameter and is typically classified as cable, cord, or aircraft cable by experts.
Both aircraft cables and wire ropes are constructed by twisting wires into strands, with multiple strands twisted together to form the final product. Aircraft cables commonly feature configurations such as 1x7, 1x19, 7x7, and 7x19. In contrast, wire ropes come in a broader range of configurations and sizes, with some types having strands of varying widths and diameters.
The fundamental distinction between wire rope and aircraft cable lies in their diameter. Wire rope generally has a diameter greater than 0.375 inches (9.5 mm), whereas aircraft cable has a diameter less than 0.375 inches. This size difference limits the wire sizes used in aircraft cables, while wire ropes can accommodate a variety of wire sizes and configurations within the same strand.
Wire ropes are significantly stronger than cables and are designed for heavy-duty and demanding applications.
Cables are thinner, more flexible, and remarkably strong. Their flexibility makes them ideal for a diverse range of applications.
As flexibility increases in both wire rope and aircraft cable, so does their susceptibility to abrasions. Wire rope is generally less vulnerable to abrasion, while aircraft cables, being more flexible, are more prone to wear and tear from abrasive conditions.
Breakage from fatigue is a common issue for both wire rope and aircraft cable, though cables are generally less prone to this problem due to their flexibility. The longevity of wire rope or aircraft cable largely depends on the specific application and how they are used.
A push pull cable control is used for the transmission of multi directional precision control of mechanical motion. The many varieties of push pull cables or controls are adaptable to a wide range of applications and...
Stranded wire refers to thin bundled up wires that are compressed and covered up in insulating material. Stranded wires are more flexible thus making them very ideal for joining electronic circuit components in confined spaces where their bending...
Wire rope is a collection of metal strands that have been twisted and wound to form the shape of a helix with the purpose of supporting and lifting heavy loads and performing tasks that are too rigorous for standard wire...
A wire rope assembly is composed of wire rope and end fittings, terminals, or lanyards that are attached to various parts of the wire rope such that the assembly can be used to lift, hoist, and move loads. The various types of...
Wire rope is constructed of multiple strands of wire that are twisted and braided together to form a spiral design or helix. Once the separate wires are shaped into a solid form, they become a single wire with greater strength because...
A bungee cord is a rope that is composed of two or more elastic strands coated with a woven fabric. It has hooks that are placed on both ends. A bungee cord is also known as shock cord and elastic cord...
Cordage is a series of intertwined fibers, strands, strings, or fabric that are joined by twisting or braiding to form a larger more formidable whole. The combination of the materials makes the final, larger strand stronger than its individual pieces...
Electric hoists are material handling equipment used for lifting, lowering, and transporting materials and products. They are powered by an electric motor and have a controller to adjust the lifting parameters...
A gantry crane is an overhead crane that has an overhead beam supported by freestanding legs and moves on wheels, a track, or rail system carrying a bridge, trolley, and hoist. Workshops, warehouses, freight yards, railroads, and shipyards use gantry cranes as their lifting solution as a variation of overhead or bridge cranes...
Rope is a collection of strands, fibers, piles and yarns joined together to form a strong and a large structure. These strands or fibers are either twisted or braided with one another to give high tensile strength to the rope...
A hydraulic lift is a device for moving objects using force created by pressure on a liquid inside a cylinder that moves a piston upward. Incompressible oil is pumped into the cylinder, which forces the piston upward. When a valve opens to release the oil, the piston lowers by gravitational force...
A jib crane is a lifting device with an arm or boom that extends off the main body of the crane to provide extra reach and has a lattice design to lower the weight added to a load. The design of jib cranes allows them to work...
A lift table is a platform capable of holding materials and raising, lowering, and adjusting them to any height to meet the needs of an application and the user’s requirements. Lift tables are supported by a strong, rigid, and stable base frame placed flat on the floor, in a pit, or equipped with casters or wheels...
An overhead crane is a type of heavy duty machinery that is capable of moving extremely heavy loads and equipment from one location to another in a safe and precise manner using the overhead space of a manufacturing facility. Due to the nature of the work they perform...
Scissor lifts are a type of manlift that is commonly used in construction and facility maintenance to raise employees and their tools to working heights. A power system and a control system make up the scissor lift...
A hydraulic system is based on Pascal‘s principle of fluid pressure, which hypothesizes that a change in pressure in a fluid is transmitted to all points of the fluid in all directions. With a hydraulic lift, an electrically powered pump pushes fluid into a cylinder at the base of a lifting jack system that lifts the platform up and down...