Autonomous Mobile Robots (AMR)
Autonomous mobile robots are rapidly becoming a fixture in manufacturing and industrial operations. Capable of completing a variety of tasks and activities, AMRs can move independently while receiving instructions from a central computer and making adjustments using SLAM algorithms. They can perform routine tasks and rescue operations and are the next step in automated guided vehicle (AGV) technology with expanded functions and capabilities.
AMRs use computer software and mapping technology to move around their environment with sensors to help them detect obstacles and avoid collisions. Initially, AMRs were implemented to perform menial, repetitive tasks that required constant movement by workers. However, this particular function has expanded into more complex, intricate, and essential activities.
Quick links to Autonomous Mobile Robots Information
How an Autonomous Mobile Robot Works
Unlike AGVs, autonomous mobile robots are able to navigate a facility without the use of tape, tracks, reflectors, or other forms of guidance systems. AMRs are completely independent and can operate on their own using information programmed into their system. They have a complex collection of technical instruments, including sensors, artificial intelligence, machine learning, and computer software, for planning their path and interpreting their environment.
AMRs can "see" where they are going through the use of light detection and ranging (LiDAR) scanners, ultra-wideband (UWB) scanners, and two- and three-dimensional cameras. These devices allow an AMR to observe its environment and make immediate adjustments. Furthermore, visualization tools make it possible for an AMR to create its own path. In addition, some AMRs are designed with sound identification software that enables them to have auditory navigation systems.
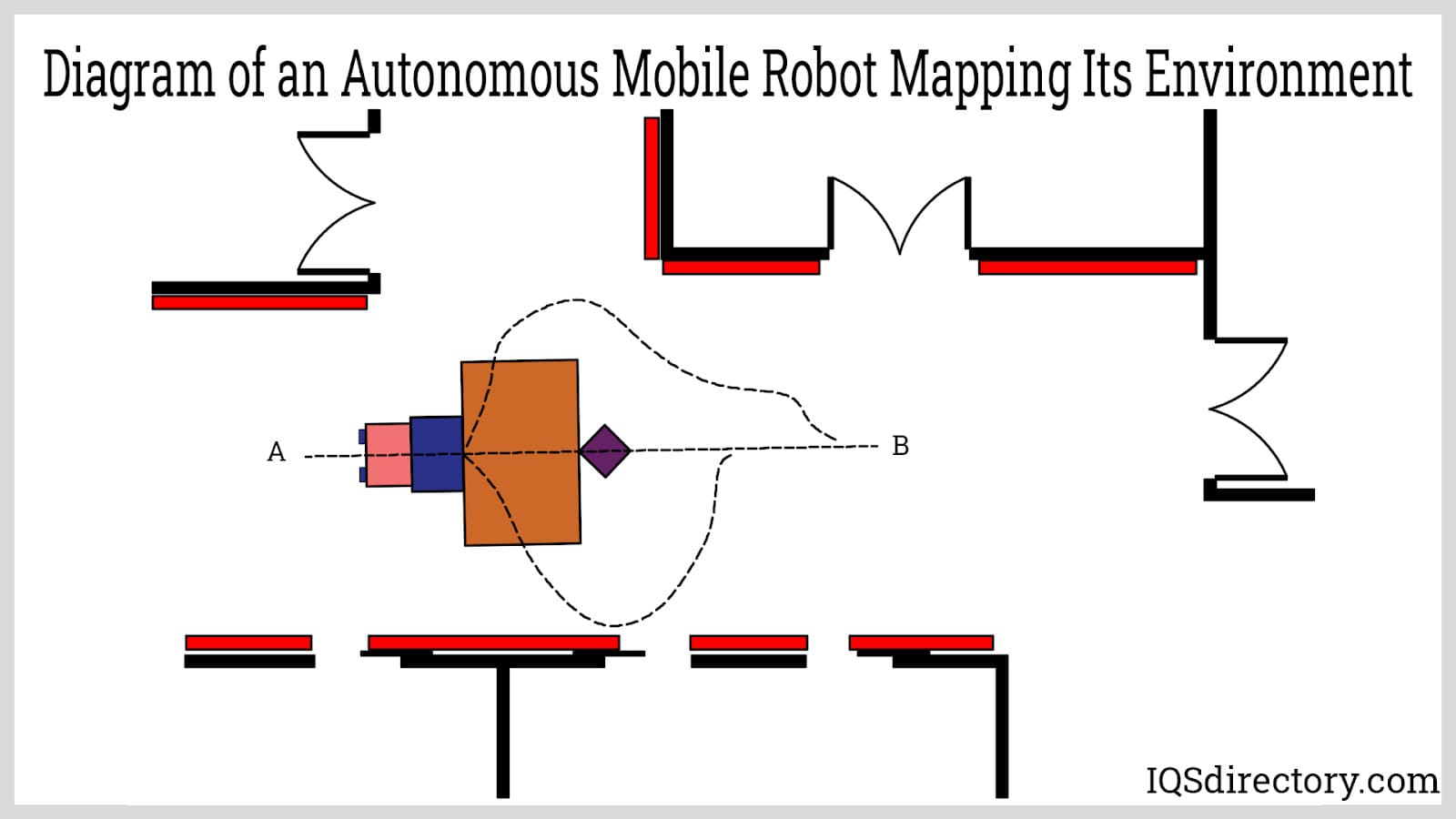
Mapping
A critical aspect of an AMR‘s navigation is its mapping software that provides an overview of the facility where they are being used. Aspects of a building that do not change are programmed into the mapping software, such as shelving, pillars, machines, entrances, and other obstacles.
In conjunction with the mapping software, sensing technology is used to detect possible obstructions that may become obstacles during the work of an AMR, such as workers, vehicles, and other AMRs. This aspect of AMRs makes it possible for them to "understand" their surroundings and efficiently perform their function.
Simultaneous Localization and Mapping (SLAM)
The mapping process uses the SLAM to build maps and place AMRs in the maps. The algorithms of SLAM assist AMRs in "seeing" the characteristics of their environment or new and unknown environments. SLAM has existed for many years and has been the subject of studies. It hasn‘t been until recent advances in computer processing speeds and sensors that SLAM has been put to practical use.
Visual SLAM
Visual SLAM uses images it receives from cameras and sensors. Although a single camera can be used for visual SLAM, additional sensors and cameras give an AMR depth perception and movement estimates. The cameras and sensors are not like those in television or photography. They provide an approximation of the environment and can calculate distances and depth. The data collected is used to estimate the position of the AMR in space and build a map of the features it has "seen."
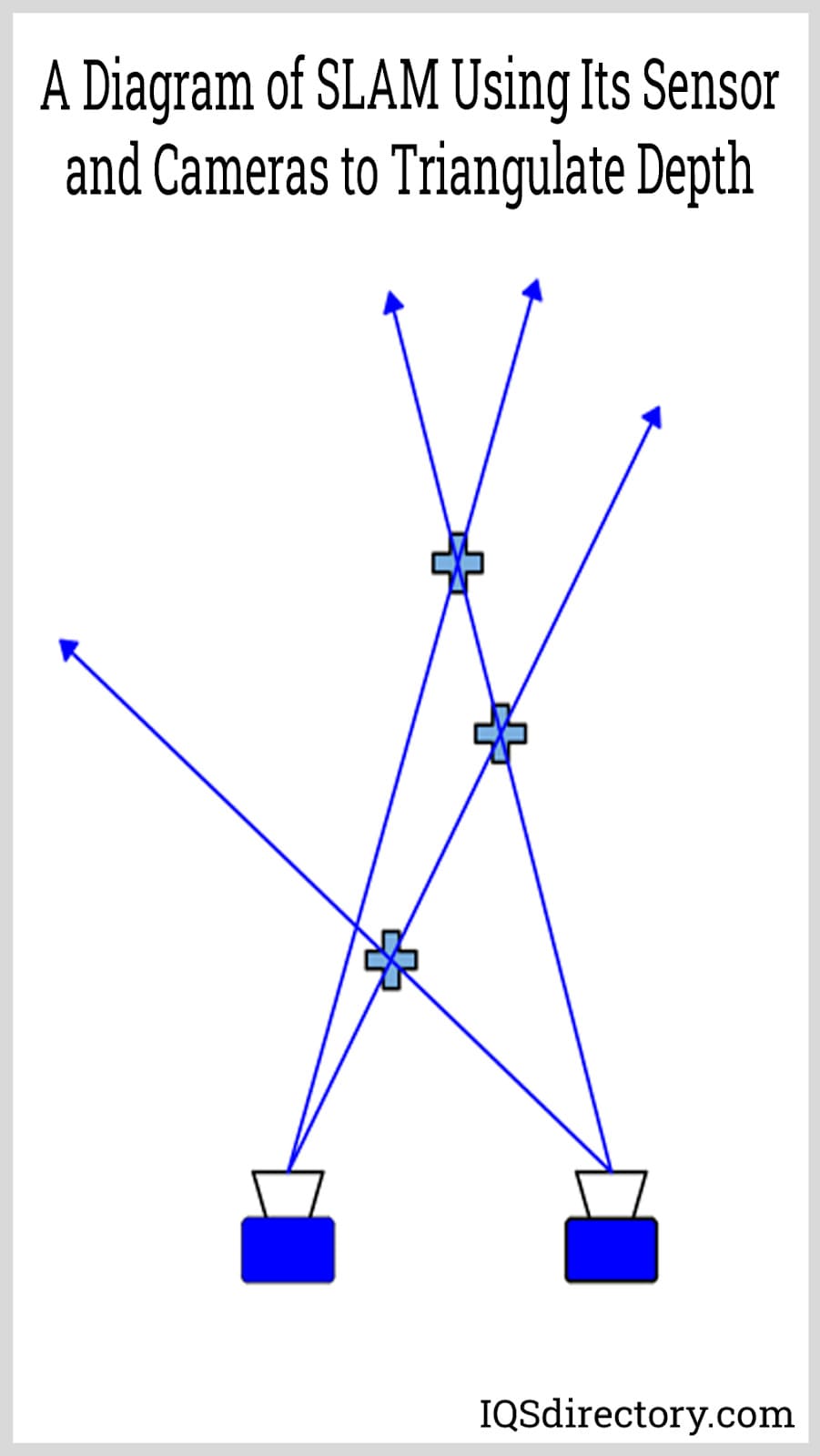
Light Detection and Ranging (LiDAR)
LiDAR uses pulsed laser light to measure distances and other data to create three-dimensional information. The components of LiDAR are a laser, scanner, and global positioning sensor (GPS). The laser sensor is the central component that provides precision distance measurements and works in combination with map constructions from SLAM. The calculated travel distance collected by LiDAR is used to localize an AMR.
An interesting aspect of LiDAR is its need for obstacles, without which it is unable to align and will lose track of an AMR‘s location. Additionally, high-speed processing is essential to improve AMR speed.
How AMRs are Used
AGVs have become a valuable tool for inventory movement and assisting assembly operations. However, their flexibility is limited by the track, tape, or reflectors they depend on to complete any task. Such limitations are removed from AMRs, which can go anywhere to perform a task.
The increased use of AMRs has added a new tool to industrial and commercial operations. Since AMRs automatically adjust and change with conditions, they can be instantly repurposed without having to make structural alterations.
Inventory Transport
The movement of inventory from one location to another is a low-level task that is one of the first jobs to be allocated to AMRs. The automation of inventory movement saves time and allows workers to do more important work.
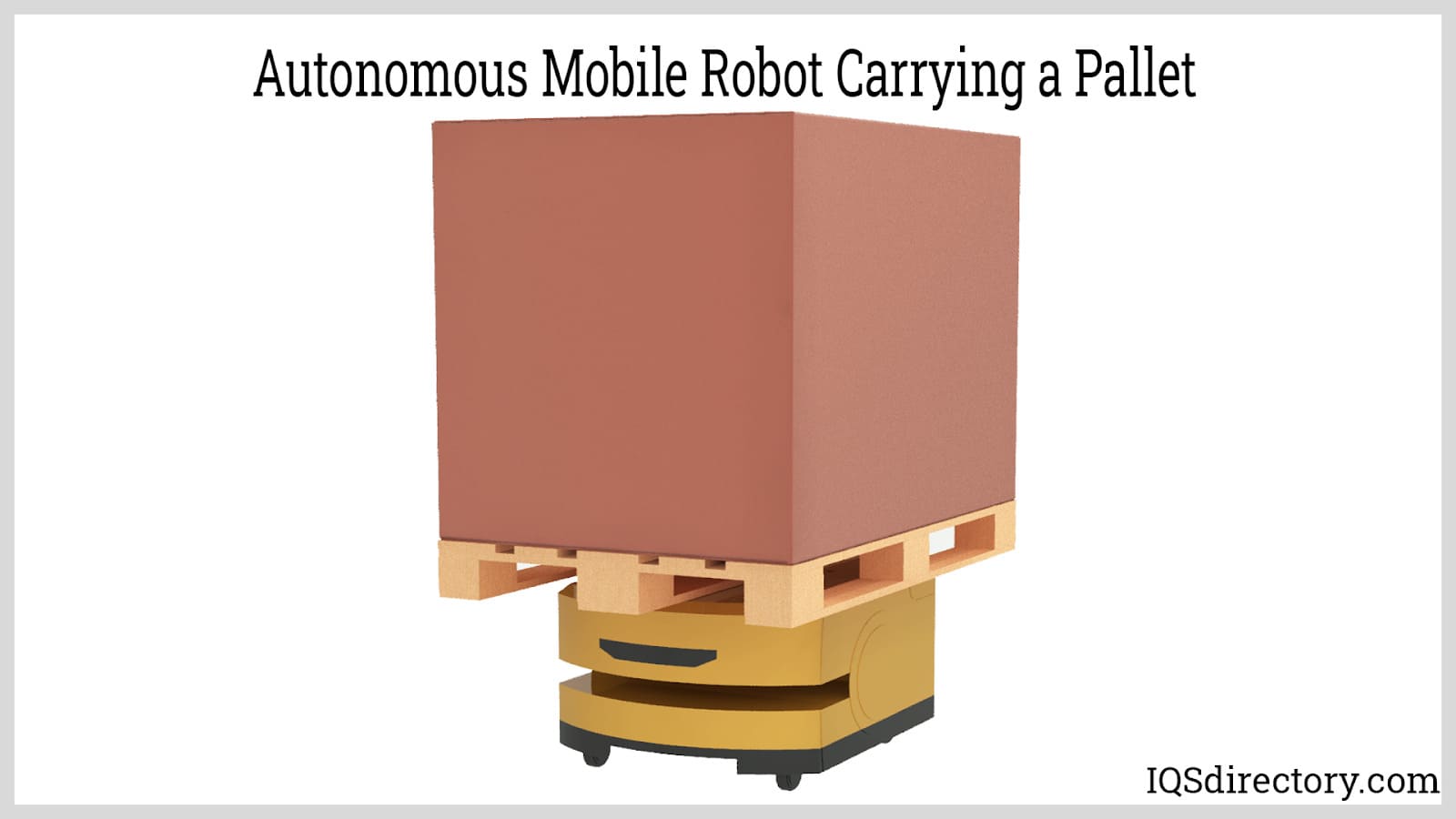
Order Picking
A tedious task that has been the function of warehouse workers for centuries is picking and assembling inventory for shipment, production, and delivery. It is an exceptionally expensive function that requires significant training, experience, and skill. Additionally, order picking is one of the most time-consuming jobs of any organization because it requires multiple trips, correction of errors, and constant searching. Simply walking from one part of a facility to another consumes time.
The effortless work of AMRs makes it possible to efficiently complete order picking at low cost and increase inventory visibility. They assist in eliminating errors, remove the need for multiple trips, and operate with precision and accuracy.
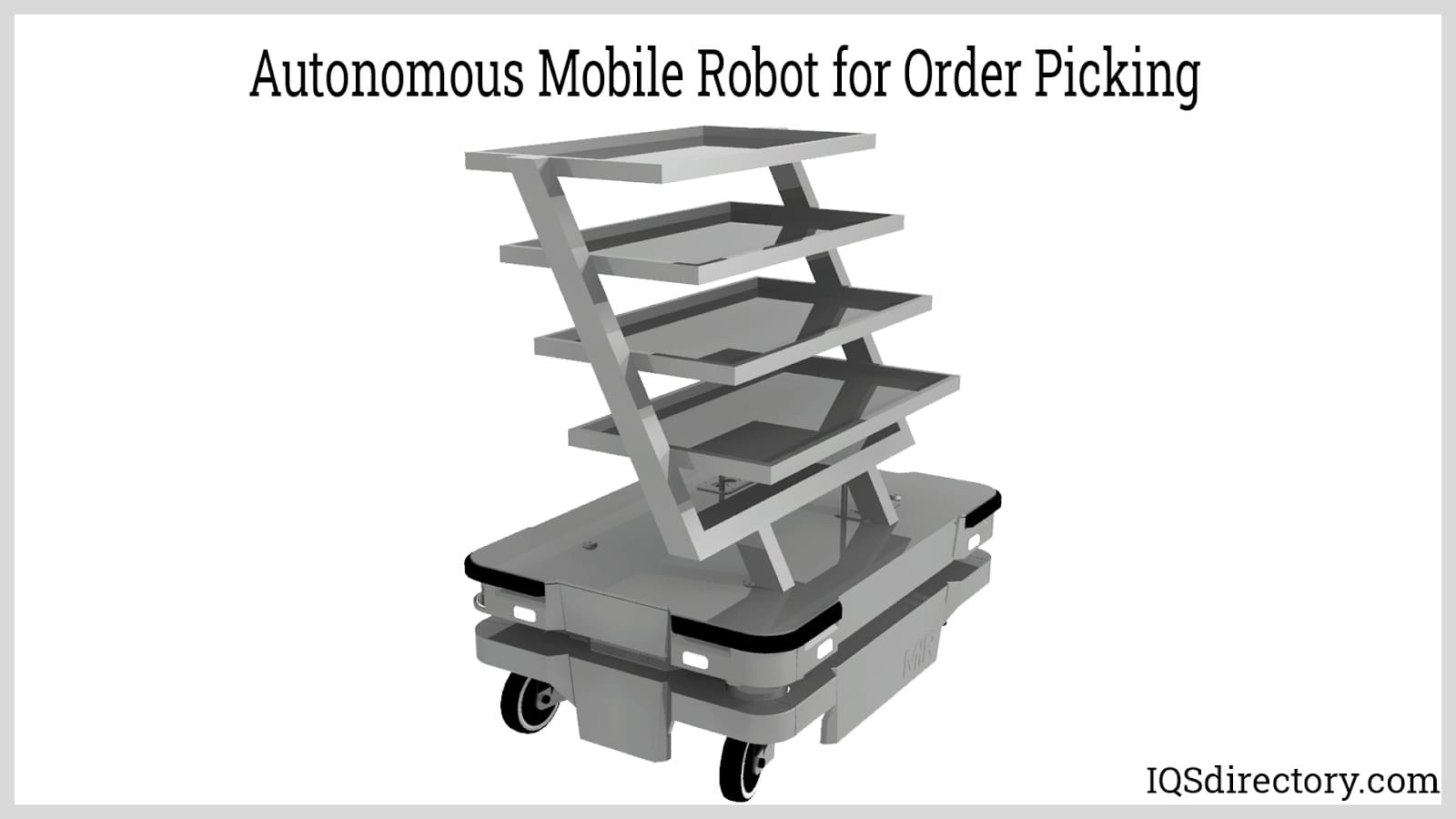
Sortation
Sortation is a method for distributing pieces, cases, totes, and baggage for packing. AMRs designed for sortation come with tilt trays, cross belt systems, and belt trays for parcel sortation, e-commerce preparation, and classifying returns. In the sortation process, high-speed AMRs are used to rapidly complete the sortation process.
Medical Disinfection
Medical disinfection autonomous mobile robots combine an AMR with a disinfecting system to disinfect and sanitize rooms using sprays and ultraviolet light. The purpose of medical disinfection AMRs is to protect medical personnel from contaminated environments that may be dangerous to humans.
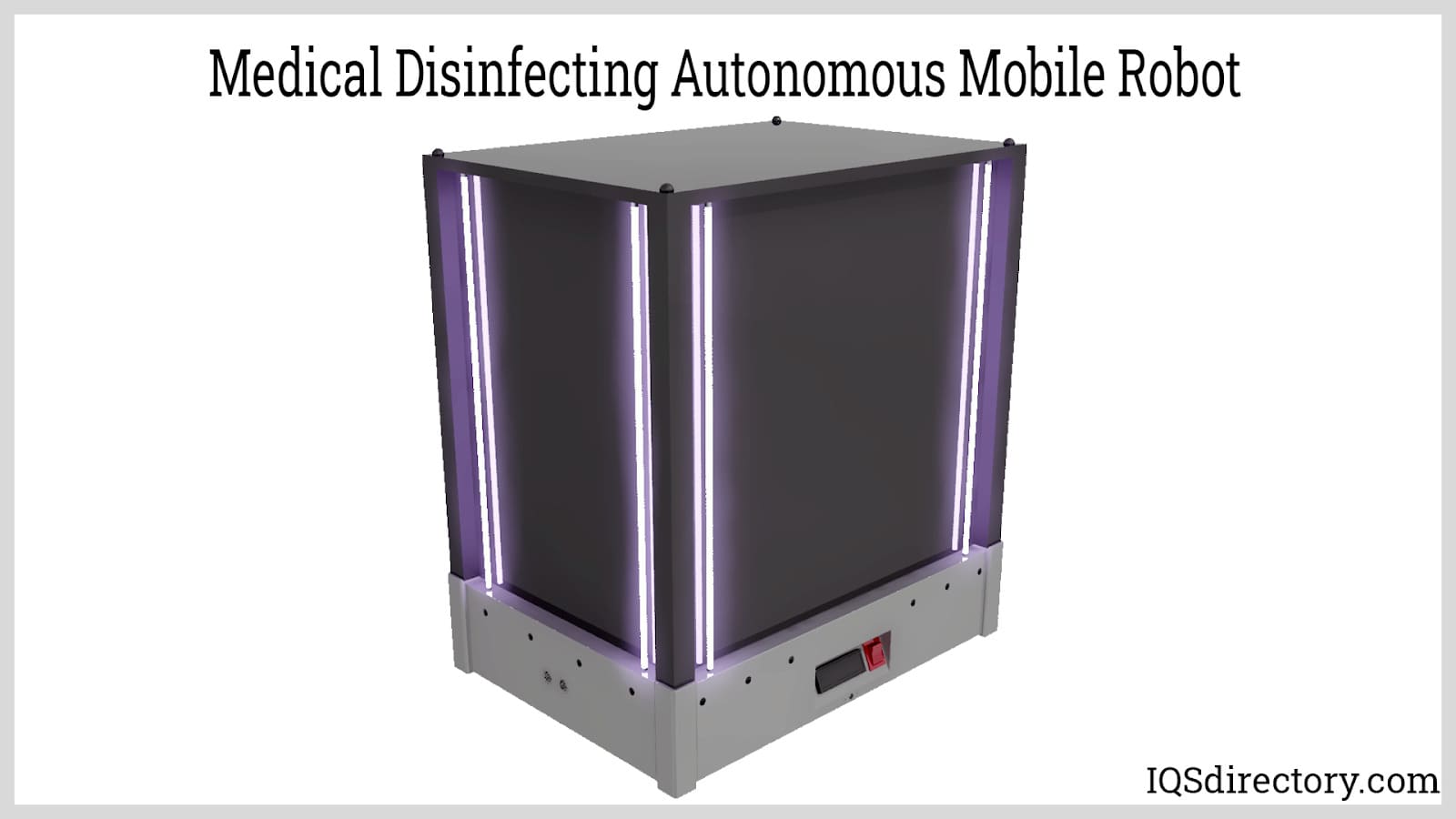