Ball Screws
A ball screw consists of two primary components: a screw shaft, which functions as the screw assembly, and a ball nut containing ball bearings, which serves as the nut. In a conventional ball screw, the screw shaft is threaded. In contrast, a threadless ball screw uses a smooth shaft, with a precisely engineered ball nut to define the rotational and linear motion properties.
Ball screws are a type of mechanical www.iqsdirectory.com/ball-screws, engineered to convert rotational motion into linear motion while minimizing friction as much as possible.
History of Ball Screws
The ball screw emerged as a significant advancement over the traditional lead screw with a threaded shaft and nut. Sometime in the late 19th century, it was discovered that integrating ball bearings into the nut could reduce friction, enhance efficiency, and eliminate backlash.
While this innovation was conceived early on, the inconsistency in ball bearing manufacturing at the time meant that ball screws remained more of a novelty. It wasn't until improvements in ball bearing production during the mid-20th century that the manufacturing of ball nuts and ball screws became commercially viable and dependable.
Threadless ball screw designs were also developed during this period but have remained limited in their use, finding application only in specific industries.
Applications of Ball Screws
A ball screw works by converting radial torque, or rotary motion, into linear motion or thrust. As the end rotates, the shaft moves in a straight line based on the threading and/or ball nut configuration.
In simple terms, a ball screw is a lead screw that incorporates ball bearings in the nut to improve efficiency and reduce friction. This design creates a unique profile, where it costs more to produce than a standard lead screw but offers a longer lifespan and requires less maintenance.
Since becoming commercially viable, ball screws have been widely used across many industries. Almost every manufacturing or mechanical industry requires the conversion of radial motion to linear motion at some stage, making ball screws or other cost-effective alternatives essential. Applications range from basic screw jacks to high-precision screw and nut assemblies used in advanced aerospace technologies.
The Design of a Ball Screw
Ball screws are designed to be highly precise and efficient, so it's crucial to ensure they are engineered to exact standards. Failing to consider key aspects of design and application can result in wasted investment, especially when choosing ball screws over alternative components.
There are two main methods for producing ball screw shafts: rolled ball screws and ground ball screws.
Rolled ball screws are made by pushing uncut bar stock through a rotating die in a single operation, deforming the material to create threads without removing material.
Ground ball screws, on the other hand, use a slower process in which threads are cut gradually through abrasion. The blanks must be cut to length before this process begins.
Rolled ball screw tend to cost less than ground ball screws, while still meeting many of the same standards. Therefore, they are often a more cost-effective option. However, rolled ball screws tend to be stronger but can have rougher surfaces and less precision compared to ground ball screws. Be sure to discuss your specific needs with both your manufacturer and engineers before opting for rolled ball screws as a cost-saving choice.
Load and preload considerations are also important in many ball screw designs. Some applications require precise preload to function correctly, while others may need minimal preload. In some cases, variable preload is necessary, requiring an adjustable system to manage load on a case-by-case basis.
Material selection is another factor to consider. Ball screws can be made from stainless steel or other common machining materials. Depending on factors such as load, temperature, corrosion resistance, and other environmental conditions, choosing the right material is essential for optimal performance.
Characteristics and Features of Ball Screws
Ball screws distinguish themselves from comparable technologies by offering exceptionally high efficiency. While a precision Acme lead screw typically achieves an efficiency of 20-40% in most applications, a ball screw in the same size and application can reach efficiencies of 90% or higher. This increased efficiency makes ball screws more durable, lower-maintenance, and overall more effective. Additionally, ball screws excel at handling high or consistent loads due to the reduced friction on the shaft, making them an ideal choice for demanding applications.
Ball Screws Images, Diagrams and Visual Concepts
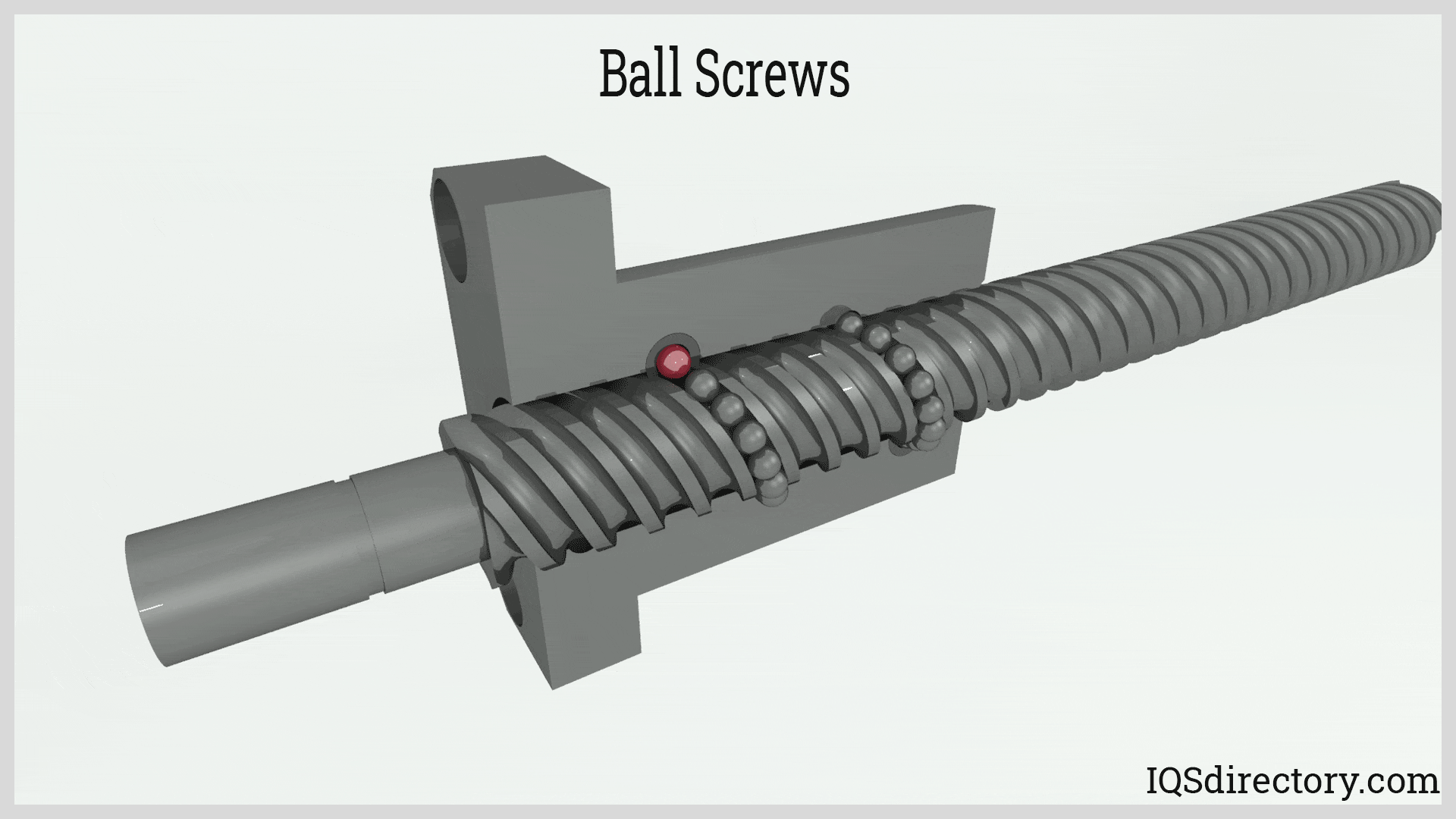
Ball screws, mechanical linear actuators that consist of a screw shaft and a nut that contains ball bearings that rolls between their matching helical grooves.
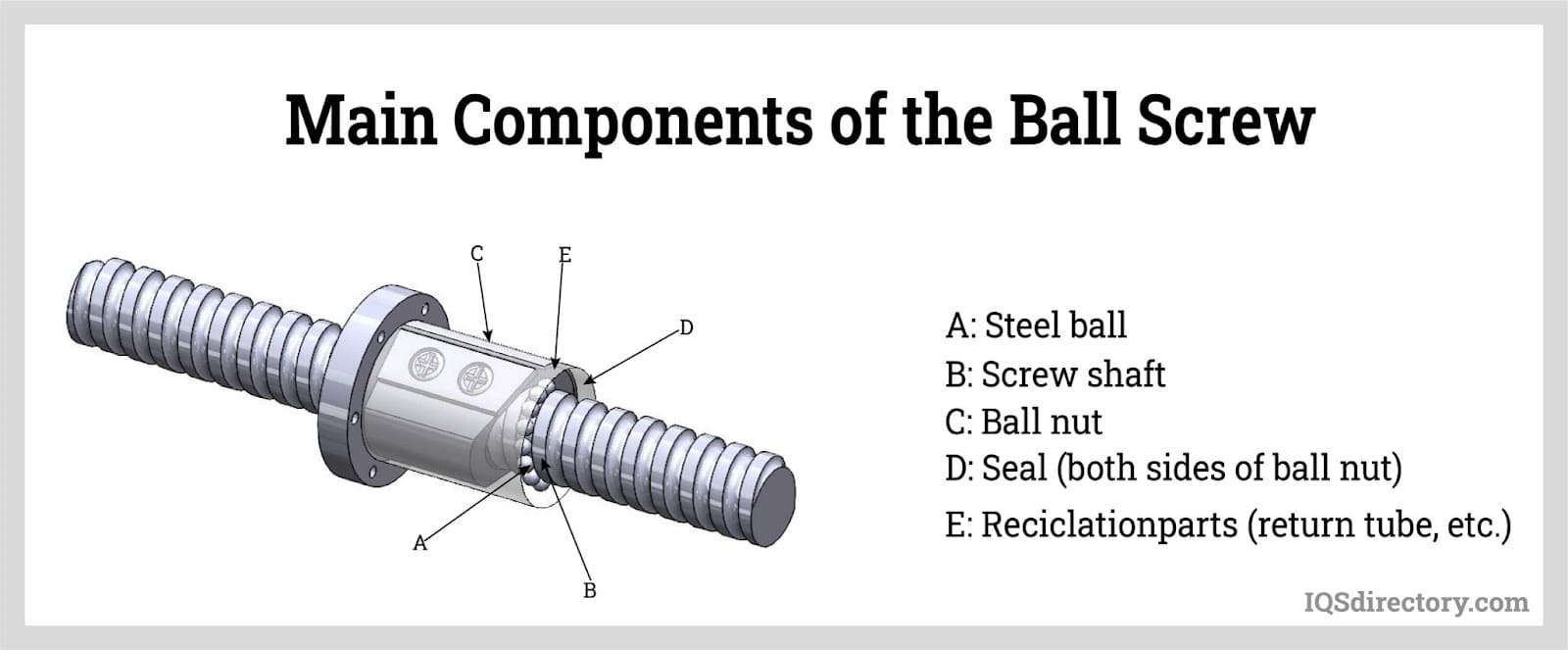
The main components of ball screws are the screw shaft, the nut, and the ball bearings.
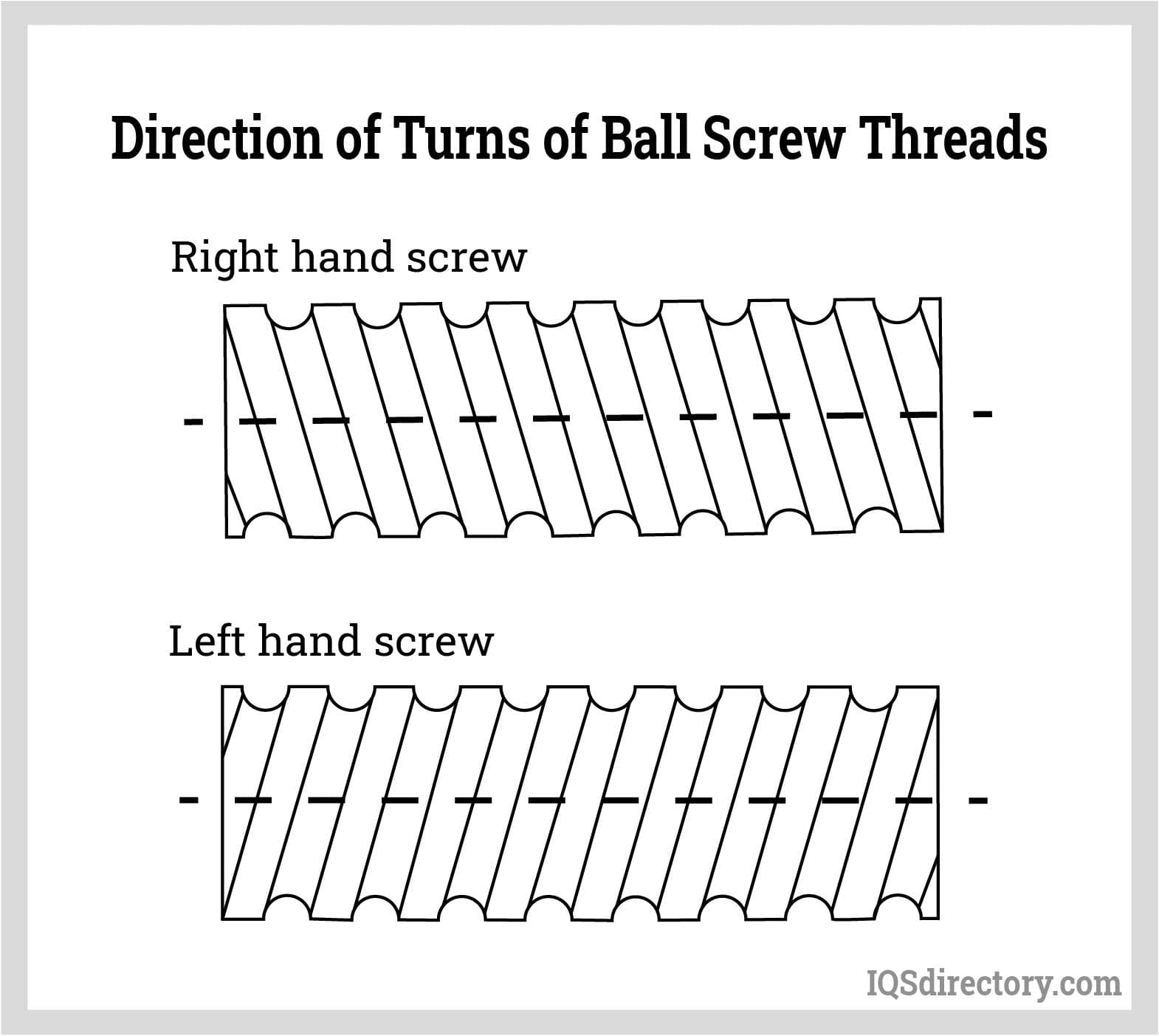
A right-hand ball screw if the groove is in a clockwise direction around the screw shaft and slants right, while a left-hand ball screw if the groove runs counterclockwise and it slants left.
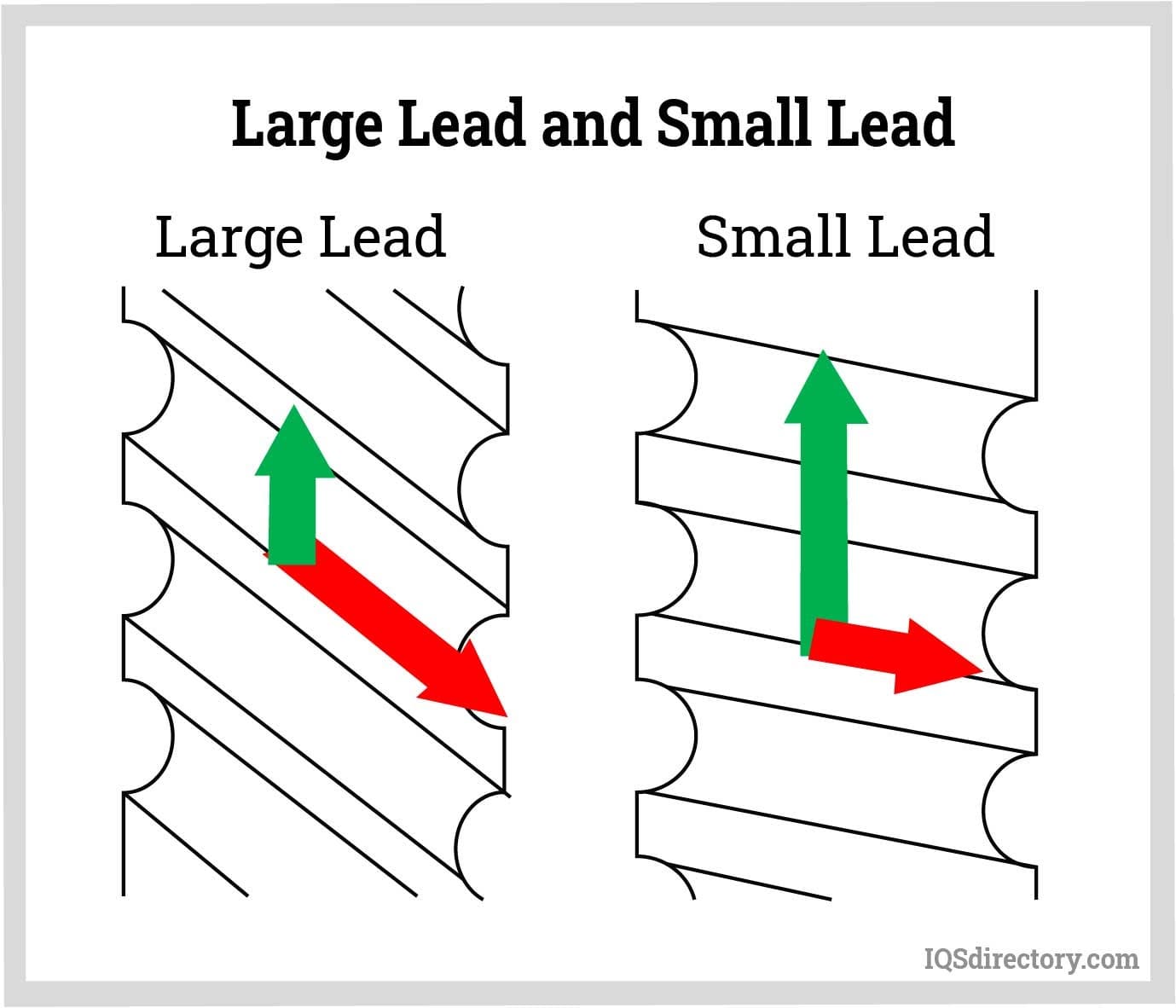
Lead is the linear distance along the axis of the screw which determines linear travel and speed and load capacity.
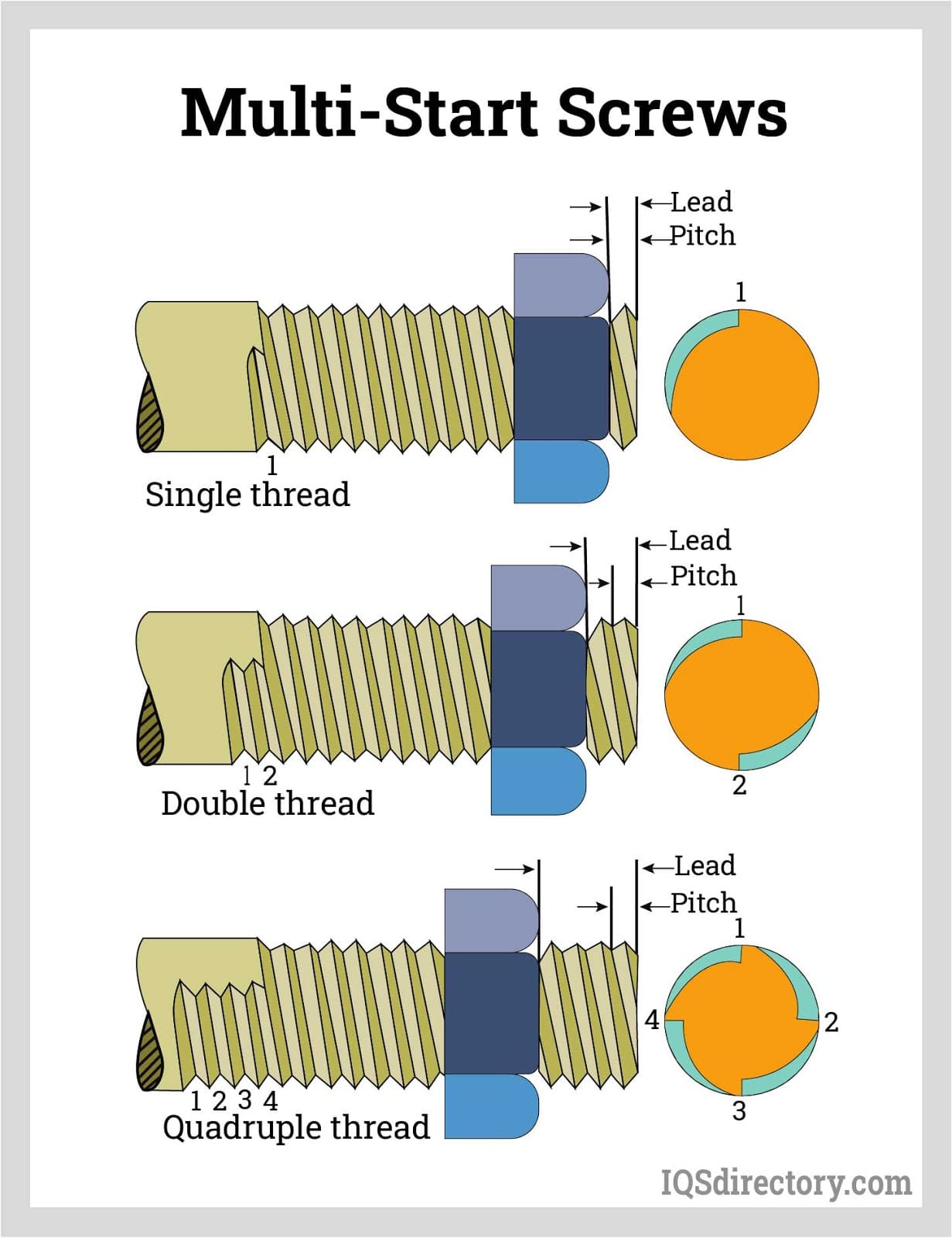
The start, the number of independent helices that runs around the screw shaft, multiple starts uses a lesser number of rotations and a high load capacity.
Ball Screws Types
Acme Screws
Lead screws that generate sliding friction between the screw and nut. Acme screws are typically 30% less efficient than ball screws but are often more cost-effective. They are commonly used in applications that require high accuracy at low speeds.
Acme Threaded Rods
Primarily used as lead screws in various machines and devices, these rods are designed with a 29-degree thread angle and a thread height that is half the pitch.
Ball Screw Assemblies
A combination of a threaded screw and an internally threaded nut, filled with ball bearings that travel in corresponding helical grooves, converting rotary motion into linear motion.
Ball Screw Nut
Critical components that convert rotational motion into linear motion. The nut houses ball bearings that move within the helical grooves of the paired screw shaft. Ball screw nuts transform torque into thrust without rotating themselves.
Custom Ball Screws
Manufactured to specific, non-standardized specifications to meet particular requirements.
Ground Ball Screws
Produced using a grinding wheel instead of the typical rolling technique, ground ball screws offer precise tolerances but can be more costly to produce.
Comprising a threaded shaft and nut, lead screws create friction through sliding, unlike the rolling friction of ball screws. Lead screws are more efficient with an increased lead and are especially advantageous for managing high shock loads.
Linear Ball Screws
Convert rotational motion (torque) into linear motion, referred to as thrust.
Metric Ball Screws
Designed using the metric system, as opposed to the American system of measurements.
Miniature Ball Screws
Ball screws as small as three millimeters in diameter, commonly used in industrial applications such as computers, electronics, fiber optics, and semiconductors. Despite their small size, they maintain high efficiency.
Precision Ball Screws
Used in manufacturing for critical functions due to the level of control they provide while handling heavy loads.
Rolled Ball Screws
Made up of a threaded screw, nut, and ball bearings, these assemblies are manufactured through cold rolling metal, offering durability and efficiency.
Screw Jacks
Used in lifting applications, such as jacks, for mechanical advantage in moving heavy loads.
Threaded and Thread Less Ball Screw Differences
There are various types of ball screws available, each suited for different applications, precision requirements, and other factors. While it would be impractical to list every type, we can focus on the strengths of two primary variations: threaded ball screws and threadless ball screws.
Threaded Ball Screws
Threaded ball screws are the most common type of ball screw. Essentially, they are lead screws with ball bearings integrated into the nut. They function in a similar way to lead screws and are used in many of the same applications. The choice between a threaded ball screw and other options depends on factors like wear and tear, ease of maintenance, and expected load requirements. Threaded ball screws offer excellent performance in a variety of environments and are often the go-to choice for most applications.
Threadless Ball Screws
Threadless ball screws, though older than threaded versions, are used less frequently. Instead of using threads on the shaft to guide the ball nut and control the motion, threadless ball screws rely on precisely configured ball bearing assemblies to rotate along a smooth shaft. While this design requires high precision during manufacturing, it eliminates issues such as backlash. However, threadless ball screws are better suited for applications with lower, more predictable loads. High, unexpected loads can cause slipping, which could lead to significant issues.
Although rare, some advanced threadless ball screw assemblies allow for on-the-fly adjustments of linear motion. These systems provide dynamic control, but their availability is limited at the moment.
Ball Screws Versus Lead Screws
When compared to other precision screw assemblies, ball screws are highly efficient and require significantly less maintenance, lubrication, and parts replacement. In many cases, this efficiency outweighs their initially higher cost compared to alternatives like Acme lead screws.
Pros of Ball Screws
- Ball screws are much more efficient than lead screws, needing less torque to operate.
- They run at lower temperatures and introduce less friction into the system.
- When properly lubricated, ball screws tend to last longer than lead screws in most applications.
- Over time, ball screws can be more cost-effective than lead screws due to their reduced maintenance and wear.
- They perform well in high-speed and high-throughput applications, where lead screws may overheat.
Cons of Ball Screws
- They are more expensive upfront than comparable lead screws of the same diameter.
- Ball screws tend to be weaker in vertical load applications compared to lead screws.
- They can generate more noise than lead screws.
- Ball screws require braking systems, while lead screws are self-locking.
Ultimately, neither ball screws nor lead screws hold a clear advantage across all applications. The decision should be based on the specific needs of your operation. While the advantages of ball screws may justify the higher initial cost in many scenarios, there are times when a lead screw will be more than sufficient. In contrast, in situations where lead screws cannot handle the required throughput or performance, they can create bottlenecks.
Typically, lead screws are preferred for smaller applications or where ease of replacement is important. Ball screws are ideal for high-load applications or scenarios where long lifespan is a priority.
Ball Screw Standards and Specifications
There are several widely recognized standards that govern the accuracy, load tolerances, and general dimensions of ball screws. Key standards include various ISO standards, starting with ISO 3408, DIN Standard 69051, and JIS B 1192-1997.
The specific standards and compliance requirements for a company using ball screws will vary based on the type of machinery, industry, and environment in which the ball screw is employed. Since there is no universal set of rules that applies to all ball screw applications, thorough research is recommended to ensure proper compliance.
Things to Consider When Purchasing Ball Screws
When using ball screws in a project, several factors must be taken into consideration. While ball screws tend to have a higher initial cost compared to other options, their efficiency and long-term benefits may justify the investment.
Best Suited for Application
Ball screws are widely used for converting radial torque into linear thrust, often serving as a suitable alternative to Acme lead screws. They are particularly beneficial in applications where improved efficiency and reduced friction can offset their higher initial cost.
Environmental Stressors for Ball Screws
In certain work environments, factors such as temperature, corrosion, load, and other stressors need to be evaluated when choosing ball screws. In these cases, it may be necessary to invest in specialized manufacturing or opt for simpler alternatives due to high wear-and-tear or exceptionally high load conditions.
Upkeep Cost
Ball screws typically require low maintenance costs due to their high efficiency. However, in environments with high stress or wear, upkeep costs may increase significantly. It's essential to consider these costs as they can escalate quickly in demanding settings.
Choosing the Right Manufacturer
When selecting a manufacturer for ball screws and related components, it's important to evaluate both their overall reputation and their ability to meet your specific needs. Ensuring both factors will result in the best fit for your requirements.
Manufacturer’s Character
- Transparent: Clear pricing and expectations are essential. You should always know exactly what you're paying for and what you'll be receiving.
- Professional: Whether it's ball screws or any other product, you want a manufacturer who keeps their word and meets deadlines.
- Experienced: Ball screws are precision components, and their efficiency depends on their correct manufacturing. Look for manufacturers with extensive experience in making high-quality ball screws.
Manufacturer’s Expertise
- Familiar With Your Application: A manufacturer with experience in your specific application can save you significant time and frustration. Ideally, they should have knowledge of similar industries or standards.
- Easy to Communicate With: Clear and effective communication is vital to avoid errors or missteps in the manufacturing process.
- Can Match Your Logistical Needs: Ensure the manufacturer can meet your shipping and production timelines. Discuss the details of scheduling, repair, and future needs to ensure seamless logistics.
Repeat Purchases
When considering a manufacturer for ongoing ball screw needs, it’s important to assess their capacity, reliability, and pricing for future orders. Will you be able to count on them for repeat purchases? And if so, will the terms of your deals remain consistent?
For a list of trusted ball screw manufacturers, refer to the top of this page.
Proper Care for Ball Screws
The high efficiency and low friction of ball screws generally lead to low maintenance requirements, but regular care is crucial to maintaining their long-term performance. A ball screw that isn't kept clean and properly lubricated can lose a significant portion of its efficiency, negating the advantages that led you to choose a ball screw over a traditional lead screw.
Lubricants should be chosen based on the recommendations of either the machine manufacturer or your ball screw manufacturer, depending on your specific application needs. Once you've determined the appropriate lubricant, you can reach out to a manufacturer listed on IQS Directory to source it. Additionally, hand-testing your ball nut for smooth, easy rotation can help prevent misalignment issues. Misalignment under torque can cause severe damage to the ball screw.
Preload considerations are also essential in ball screw systems, as improper preload can impact performance. To keep your ball screw assembly in optimal condition, it is advisable to keep it sealed in its original packaging until you're ready for installation, reducing the risk of dust and debris contamination. If ball screws are stored for extended periods, rotating them every few months helps ensure that oil is evenly distributed across the surface.
Accessories for Screws
A range of support bearings and related components work in conjunction with ball screws. If you’re using standard designs for your ball screws, you can rely on standardized support bearings. These components and accessories can help reduce the need for customization, streamline the ordering and assembly process, minimize inherent risks, address specific challenges, and reduce maintenance. Be sure to consult with your manufacturer about the potential accessories that best suit your application.
Ball Screws Terms
Backdrive
The conversion of thrust motion back into torque motion. Backdrive can be reduced by using a self-locking mechanism.
Backlash
The movement of a screw and nut from its original position. Unlike creep, backlash is not caused by vibration or heavy loads.
Creep
The movement of a screw and nut from its initial position due to vibration, shock, or heavy loads.
Column Strength
When a screw is loaded in compression, its limit of flexible stability can be exceeded, potentially leading to failure from buckling or bending in the future.
Critical Speed
The speed at which a revolving screw shaft vibrates, determined by its length, size, and end shape. This vibration occurs at a predictable speed known as the critical speed.
Efficiency
A measure, expressed as a percentage, that compares the power output to the power input of a screw assembly.
End Fixity
Refers to the method by which the ends of the screw are supported. The three basic types of end fixity are free, simple, and fixed.
Freewheeling
A condition in ball screw assemblies where the screw continues to rotate without causing linear movement.
Friction
The resistance to movement between the screw and nut. There are different types of friction, including sliding friction, which is typical of Acme screws and lead screws, and rolling friction, which is characteristic of ball screws.
Lead
The amount of movement a nut makes along a screw, measured in inches per revolution (in/rev).
Pitch
The axial measurement between threads. Pitch also refers to the number of full rotations a screw makes to produce one inch of nut movement along the screw.
Root Diameter
The minor diameter of a screw thread or the major diameter of a nut thread.
RPM (Revolutions Per Minute)
The rotary speed of a ball screw, indicating the number of full rotations a screw makes in one minute.
Screw Starts
Refers to the number of independent threads on a screw shaft, typically found in configurations of 1, 2, or 4.
Self-Locking
A feature of Acme screws and other screw types that prevents backdrive by disallowing the conversion of thrust to torque.
Shaft
The portion of the screw that contains the threads.
Speed
The rate of linear movement in ball screw assemblies, expressed in inches per minute. It is calculated by multiplying the screw lead by the RPM (revolutions per minute).
Stroke
The linear motion or thrust of a ball screw system, measured in inches.
Thread
The raised helical rib wrapped around the shaft of a screw.
Thrust
The linear movement produced by the torque generated by ball screw assemblies.
Torque
The rotational motion in a ball screw system that translates into linear movement, known as thrust.
More Ball Screws Information