Ceramic Manufacturing
Ceramic manufacturing, at its core, is the process of producing ceramic materials that serve as essential components in a wide array of advanced engineering products and machinery. True to their name, these materials are derived from ceramics, primarily composed of clay and other non-metallic substances. To ensure they meet the necessary strength and durability requirements for the machinery they support, these raw materials are carefully blended with highly purified chemical solutions, resulting in a final product engineered for precision and performance.
Applications of Industrial Ceramics
When people think of ceramics, they often picture artistic and decorative pottery crafted from clay and composite materials. However, industrial ceramics serve an entirely different purpose while being made from the same foundational materials. These ceramics play a critical role in supporting machines and machine components, improving the efficiency and durability of manufacturing processes. The reach of the ceramic industry extends across a vast spectrum of sectors, serving a diverse range of customers.
Industries that depend on ceramic components and products include aerospace, automotive, military and defense, medicine and healthcare, power generation, refractory applications, general industrial sectors, food processing, chemical processing, and construction. Each of these industries relies on ceramics for their unique properties, such as high-temperature resistance, wear resistance, and superior insulation capabilities.
Ceramic Manufacturing Products
Ceramic products are broadly categorized into four primary groups: structural ceramics, refractories, whitewares, and technical ceramics—also referred to as engineering ceramics or advanced ceramics.
Structural ceramic products encompass materials like bricks and ceramic tiles, which are widely used in construction and infrastructure projects. Refractory ceramics include kiln linings and crucibles, essential for high-temperature industrial applications. Whiteware ceramics cover products such as fine bone china for dining and other decorative pottery. Technical ceramics, on the other hand, represent the highest-performance category, comprising components designed for aerospace, nuclear power, biomedical applications, military and defense systems, and automotive engineering. These advanced ceramic materials exhibit exceptional resistance to heat, corrosion, and wear, making them indispensable in critical applications requiring superior durability.
A specialized but lesser-known category within ceramics is electrical ceramics, which includes products such as ceramic insulators, capacitors, magnets, and superconductors. These materials are engineered to provide excellent electrical insulation and conductivity properties, playing an essential role in power distribution, electronic devices, and high-tech applications.
Additional products created through ceramic manufacturing include electric motor components, ceramic magnet elements, ceramic balls, and ceramic rods. Ceramic blades and rotary bearings are widely used in wind turbines and jet engines, offering durability and high-performance efficiency. Ceramic insulators and spacers provide essential electrical insulation, while shuttle tiles and floor tiles demonstrate ceramics' exceptional heat resistance and structural integrity. The medical field benefits from ceramic tubes, prosthetic limbs, and bone and teeth replacements, which offer biocompatibility and longevity. In defense and personal protection, ceramic body armor delivers superior impact resistance. Chemical and environmental applications utilize ceramic fibers, membranes, and catalysts for filtration, separation, and chemical processing. Additionally, ceramic coatings enhance surface protection and temperature regulation, ensuring longevity and performance in extreme conditions.
History of Ceramic Manufacturing
The use of ceramics to fulfill both everyday and industrial needs is a practice that dates back thousands of years. From ancient clay-based pottery to modern high-tech applications, ceramics have played a vital role in human development. However, the origins of industrial ceramics as we know them today can be traced back to the 1700s.
In 1709, Abraham Darby pioneered a breakthrough in ceramic engineering by using coke combined with clay to enhance the efficiency of the smelting process at his production facility. This marked the first documented instance of ceramics being used in industrial applications. Just fifty years later, Josiah Wedgwood established the first dedicated ceramics manufacturing factory in Stoke-on-Trent, England, laying the foundation for the large-scale production of ceramic goods.
The 19th century saw significant scientific advancements in ceramics. In 1880, brothers Pierre and Jacques Curie discovered piezoelectricity, a crucial property of electroceramics, which led to the development of piezoelectric ceramic manufacturing. The industry advanced further in 1888 when Austrian chemist Carl Josef Bayer introduced a process for extracting aluminum from bauxite ore, a method still in use today that made ceramic production more efficient and cost-effective. Just five years later, in 1893, E.G. Acheson invented a method for synthesizing silicon carbide, an extremely durable ceramic material that remains widely used in industrial applications.
Throughout the first half of the 20th century, chemists continued to develop new ceramic materials while engineers refined and expanded manufacturing techniques. These advancements allowed ceramics to become essential to military applications, particularly during World War II, when they were utilized in the production of weapons and protective equipment.
Today, the ceramic industry is pushing the boundaries of material science, developing even more advanced compounds with specialized properties. Scientists have successfully synthesized hydroxyapatite, the mineral component of bone, enabling the creation of bioceramic products such as synthetic bones and dental implants. Meanwhile, Japan’s high-speed trains now utilize the Meissner effect with ceramic magnets to achieve magnetic levitation. As research and innovation continue, ceramics remain at the forefront of technological progress, shaping industries and applications that extend far beyond their ancient origins.
Process of Industrial Ceramic Manufacturing
The production of industrial ceramic products follows a multi-stage process that ensures precision, durability, and performance. These stages include milling, batching, mixing, forming, drying, and sintering, each contributing to the transformation of raw materials into high-quality ceramic components.
Milling
At this initial stage, raw materials are reduced to a desired particle size, a crucial step in achieving the final product’s mechanical and structural integrity. Milling consists of several sub-stages, including destruction, compression, and impact processing, which refine the material into a uniform and workable form.
Batching
This phase involves precisely measuring and combining materials according to a predefined ceramic formulation. The batching process ensures consistency in the ceramic composition and often incorporates additive manufacturing techniques to enhance material properties.
Mixing
During mixing, the ceramic ingredients are thoroughly blended using specialized procedures and machinery. To create homogenous slurries, water or other liquid additives are introduced, allowing for easier handling and improved material distribution.
Forming
Once the base material is prepared, the shaping of ceramic components begins. Manufacturers employ various forming techniques depending on the application and complexity of the design. These methods include slip casting, pressing, extrusion, and injection molding.
- Slip casting is ideal for mass production, particularly for intricate shapes, thin-walled structures, and sanitary ware.
- Pressing techniques such as hot pressing and hot isostatic pressing are preferred for advanced ceramics requiring high density and strength.
- Extrusion and injection molding are well-suited for producing simple yet precise ceramic parts like pipes and tubes.
Drying
Following the forming process, ceramic components must undergo thorough drying. This step ensures that excess moisture evaporates, solidifying the material and maintaining its intended shape before it enters the final phase of production.
Sintering
To complete the ceramic formation process, the dried components—referred to as greenware—are subjected to extreme heat in specialized ovens or kilns. Sintering strengthens the ceramic by bonding its oxides, a process that results in desification and crystal structure formation through ionic and covalent bonding. The chemical transformation occurring at this stage determines the ceramic's final mechanical and thermal properties, influenced by the electronegativity difference between cations and anions.
After sintering, ceramic parts may undergo secondary processes such as glazing, polishing, grinding, cutting, or machining to achieve the desired surface finish, dimensional accuracy, or enhanced performance.
Ceramic Manufacturing Design and Engineering
Throughout the ceramic manufacturing process, product designers and engineers focus on optimizing material selection and production methods to meet the specific demands of the intended application. Various ceramic compositions offer distinct characteristics, including translucency, hardness, corrosion resistance, heat tolerance, wear resistance, weight efficiency, microwave absorption, and thermal insulation.
For instance, oxides such as silica and zirconia exhibit unique optical and mechanical properties, while non-oxides like silicon nitride and silicon carbide provide exceptional strength and thermal stability. Materials such as aluminum oxide and boron carbide are particularly valued in armor applications due to their extreme hardness.
The manufacturing process relies on precision equipment, including sintering ovens, silicone or metal molds, rubber extrusion machines, injection molding systems, and computer-aided design (CAD) programs for blueprint development. Ceramic production systems can be fully customized to align with application-specific requirements, with adjustments made based on production volume, speed, quality standards, shape complexity, and necessary secondary processing. This flexibility ensures that ceramic components meet the rigorous demands of industries ranging from aerospace and defense to medical and industrial manufacturing.
Benefits of Using Industrial Ceramics
The long-term advantages of ceramics stem from their exceptional durability, with many ceramic components delivering performance lifespans up to three times longer than those of other materials. This extended longevity makes ceramics a highly cost-effective choice for a wide range of industrial applications.
Ceramic parts offer an impressive combination of properties, including a high melting point, oxidation resistance, extreme hardness, and lightweight composition. They also exhibit a remarkable versatility, mimicking the desirable characteristics of metals, polymers, and rubbers. For instance, certain ceramics match stainless steel in corrosion resistance, while others surpass titanium in hardness. Some formulations can be injection-molded or cast like polymers and rubbers, while others share the lightweight nature of aluminum or synthetic materials.
In many demanding environments, advanced ceramics outperform metals, providing superior wear resistance and stability under extreme temperatures or corrosive conditions. Certain ceramics even surpass copper in electrical conductivity, making them invaluable in electronic and high-performance applications. Additionally, ceramics are indispensable in aerospace and defense technologies—components such as space shuttles and missile cones rely on ceramic insulation to withstand intense heat and prevent structural failure.
Beyond industrial and technological applications, ceramics also contribute to environmental sustainability. Specialized ceramic materials help absorb toxic substances, reduce pollution, and aid in water purification processes, making them essential for ecological protection and resource management.
Choosing the Right Ceramic Manufacturer
Because ceramic products vary widely in composition, design, and functionality, working with the right manufacturer is essential to achieving high-quality, reliable solutions. More than just a contract manufacturer, the ideal partner must meet precise specifications, operate within required timeframes and budgets, and remain committed to delivering exceptional results.
Finding the best manufacturer begins with exploring reputable suppliers. To streamline this process, we have compiled a list of top ceramic manufacturers, which can be found near the top of this page. By visiting their websites and requesting quotes, you can connect with a trusted industry expert who will ensure your ceramic components meet the highest standards of performance and durability.
Ceramic Properties
General Characteristics of Structural Materials:
Characteristic |
Ceramics |
Metals |
Polymers |
Density |
Low to High |
Low to High |
Low |
Hardness |
High |
Medium |
Low |
Tensile Strength |
Low to Medium |
High |
Low |
Compressive Strength |
High |
Medium to High |
Low to Medium |
Young’s Modulus |
Medium to High |
Low to High |
Low |
Melting Point |
High |
Low to High |
Low |
Dimensional Stability |
High |
Low to Medium |
Low |
Thermal Expansion |
Low to Medium |
Medium to High |
High |
Thermal Conductivity |
Medium |
Medium to High |
Low |
Thermal Shock |
Low |
Medium to High |
High |
Electrical Resistance |
High |
Low |
High |
Chemical Resistance |
High |
Low to Medium |
Medium |
Oxidation Resistance |
Medium to High |
Low |
Low |
Machinability |
Medium |
Low |
Medium |
Ceramic Manufacturing Images, Diagrams and Visual Concepts
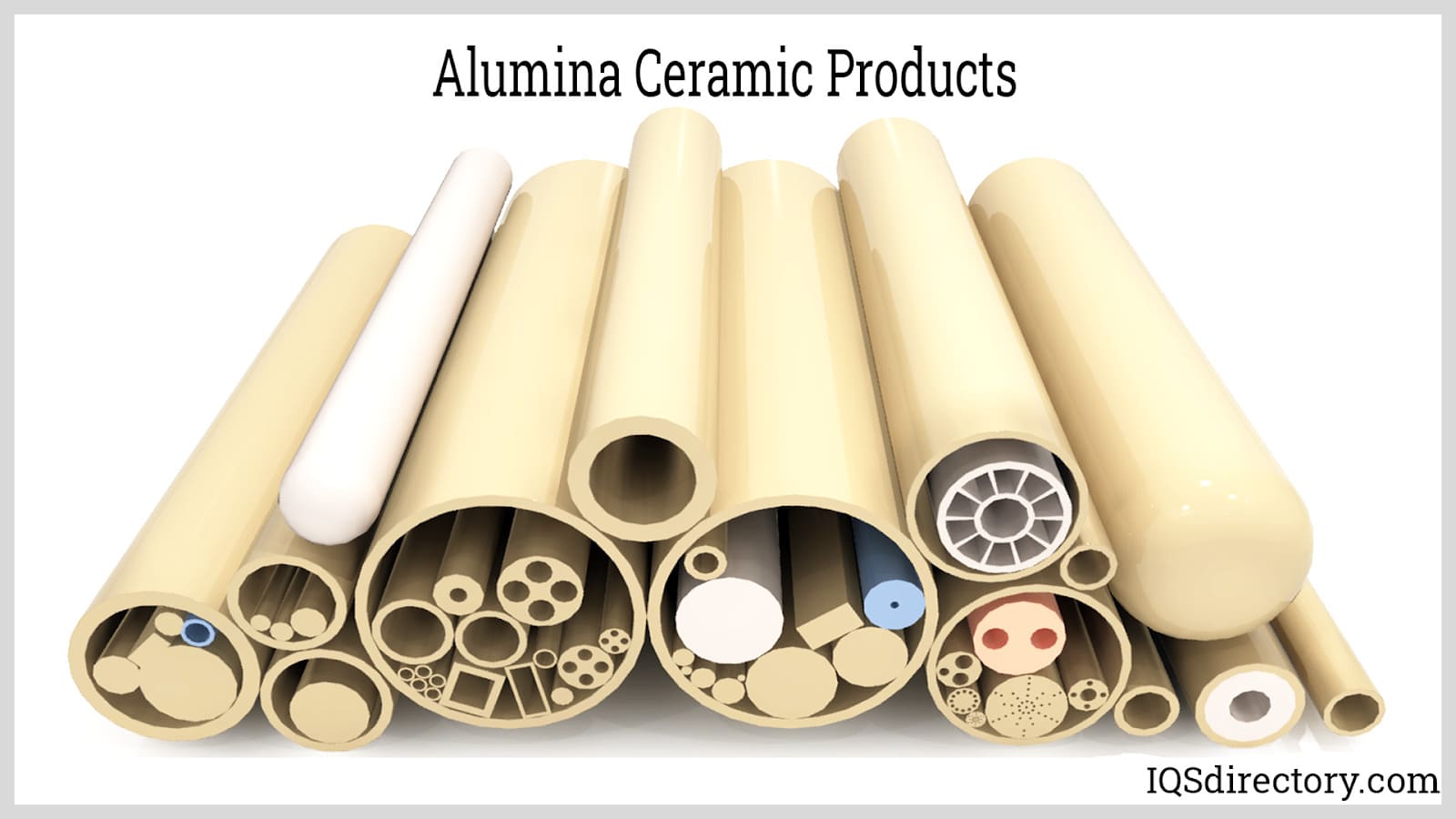
Alumina ceramic is an industrial oxide ceramic that is wear and corrosion resistance.
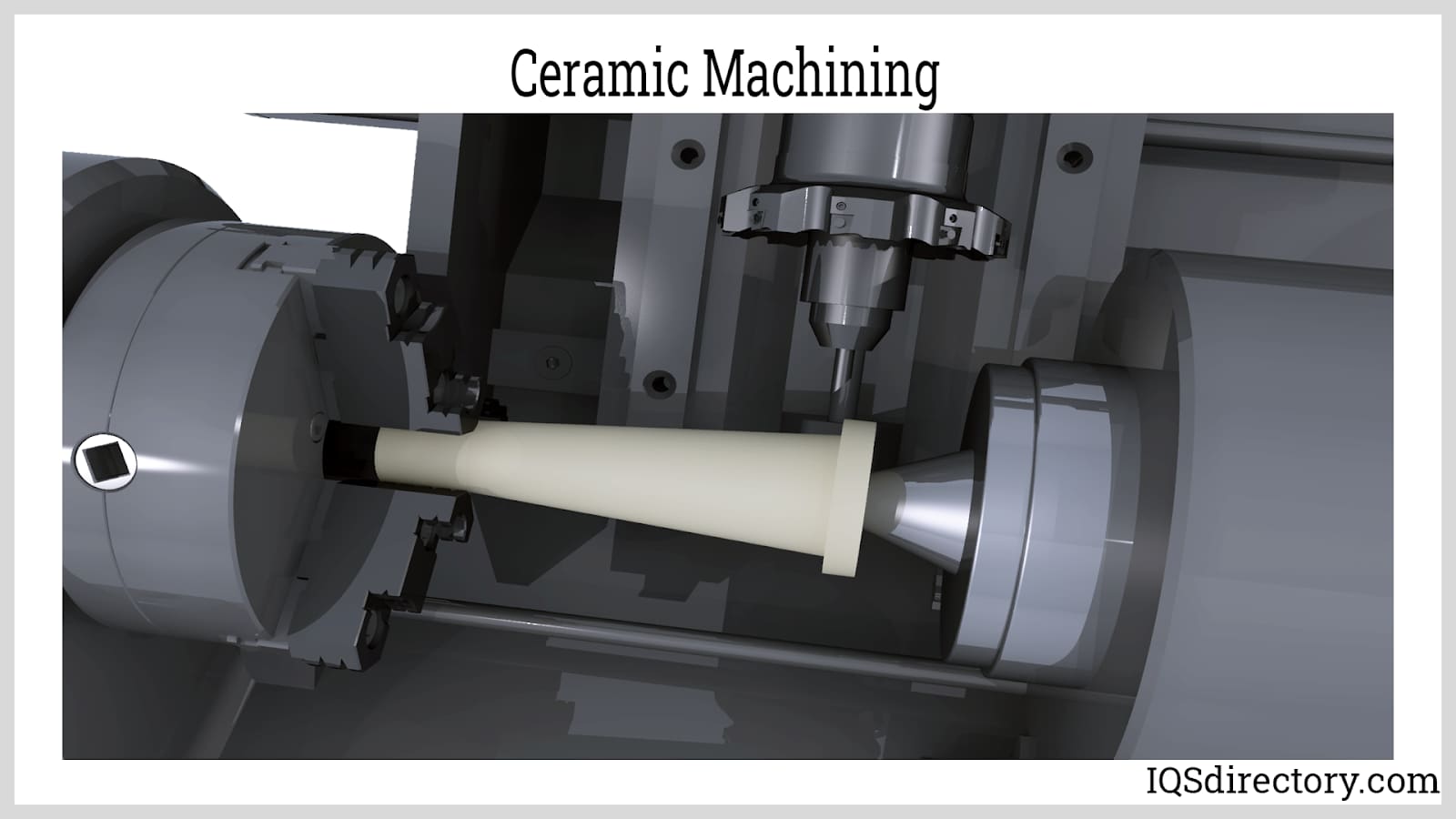
Ceramic machining refers to the manufacture of ceramic materials into finished products.
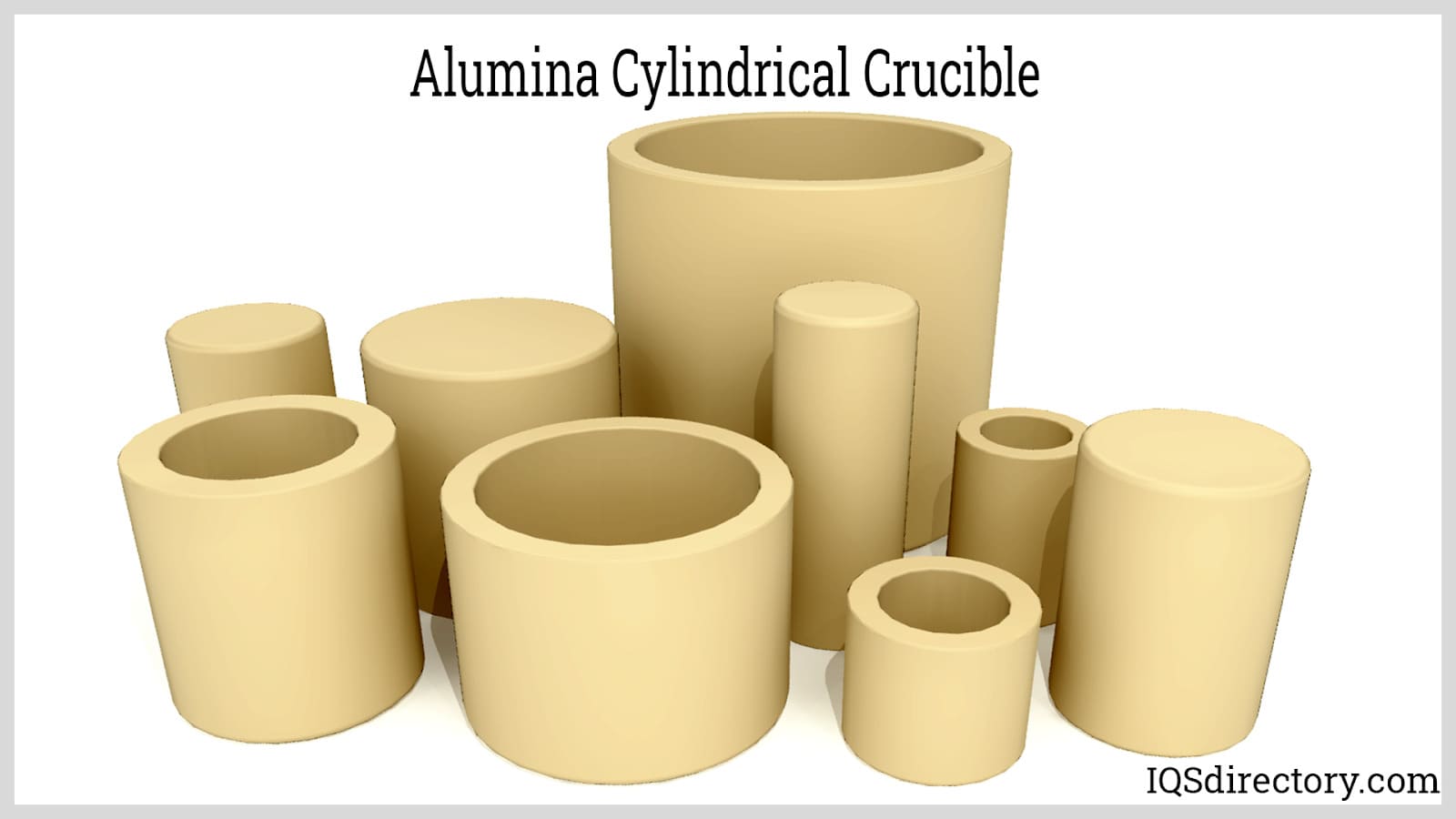
Alumina ceramic can with stand high temperatures and has high durability.
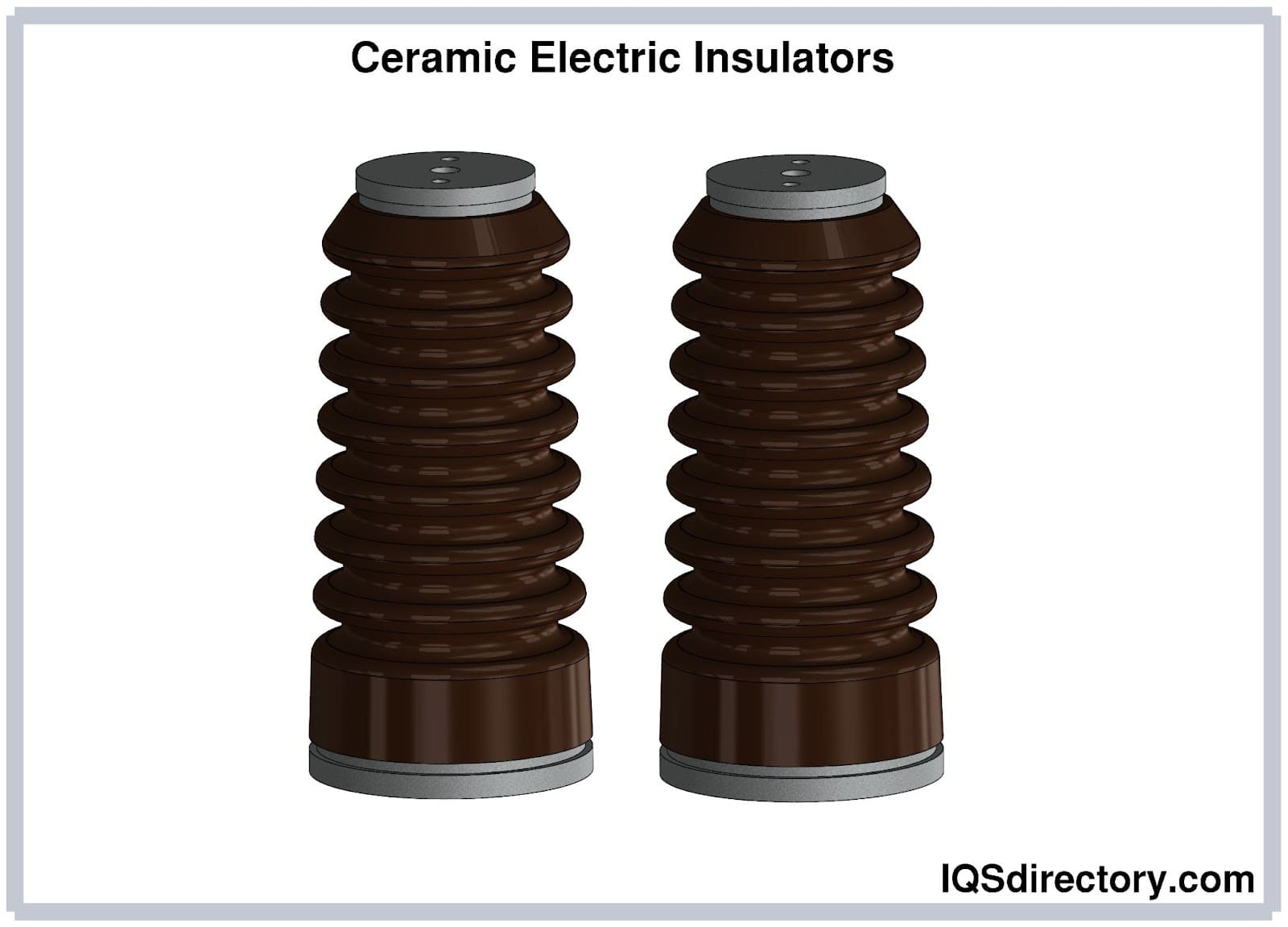
Ceramic insulator, a non-conductive insulator made from porous clay which provides a bridge between electronic components and has high dielectric strength.
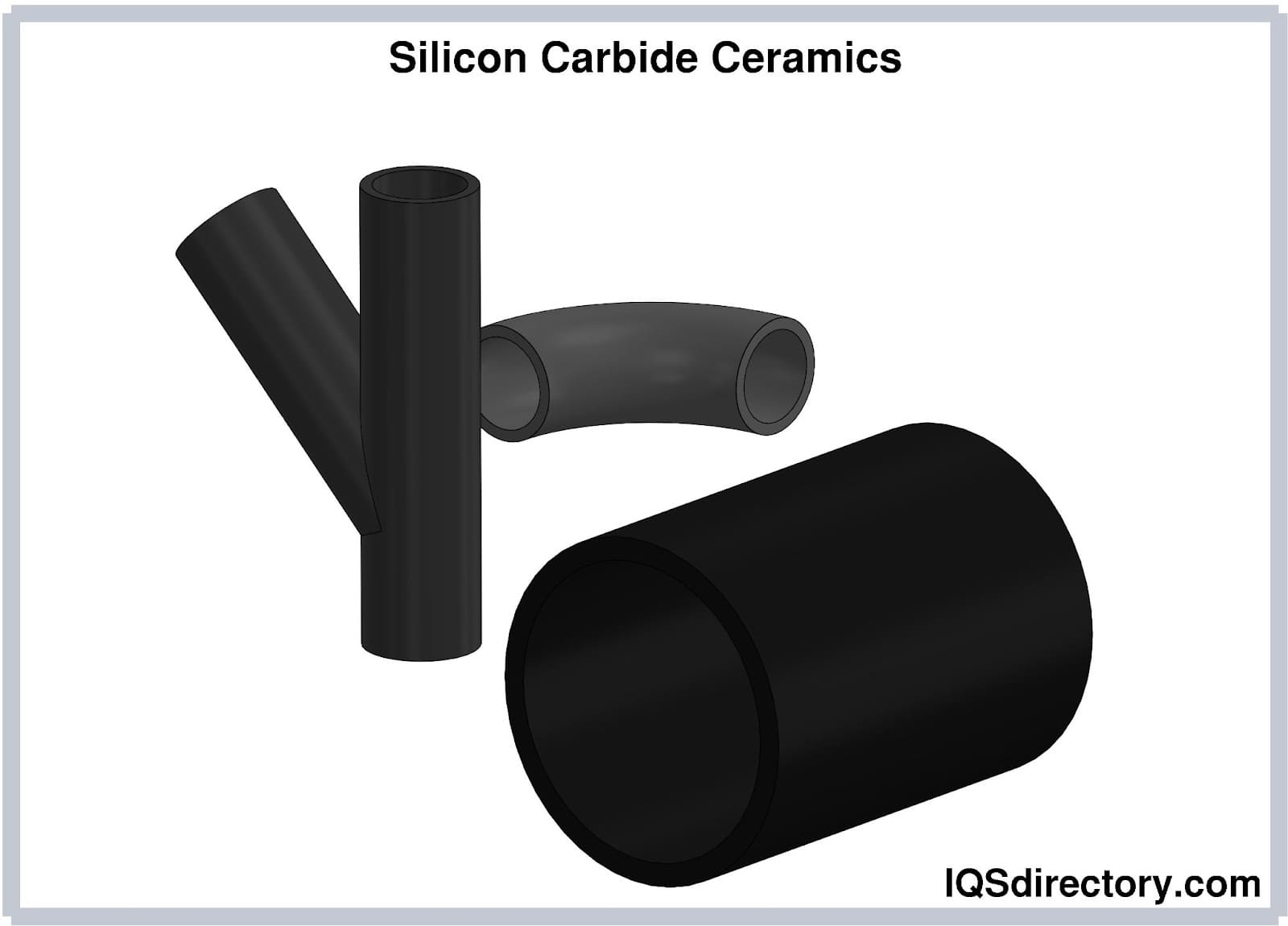
Silicon carbide ceramics are durable and are used in cutting tools to power systems.
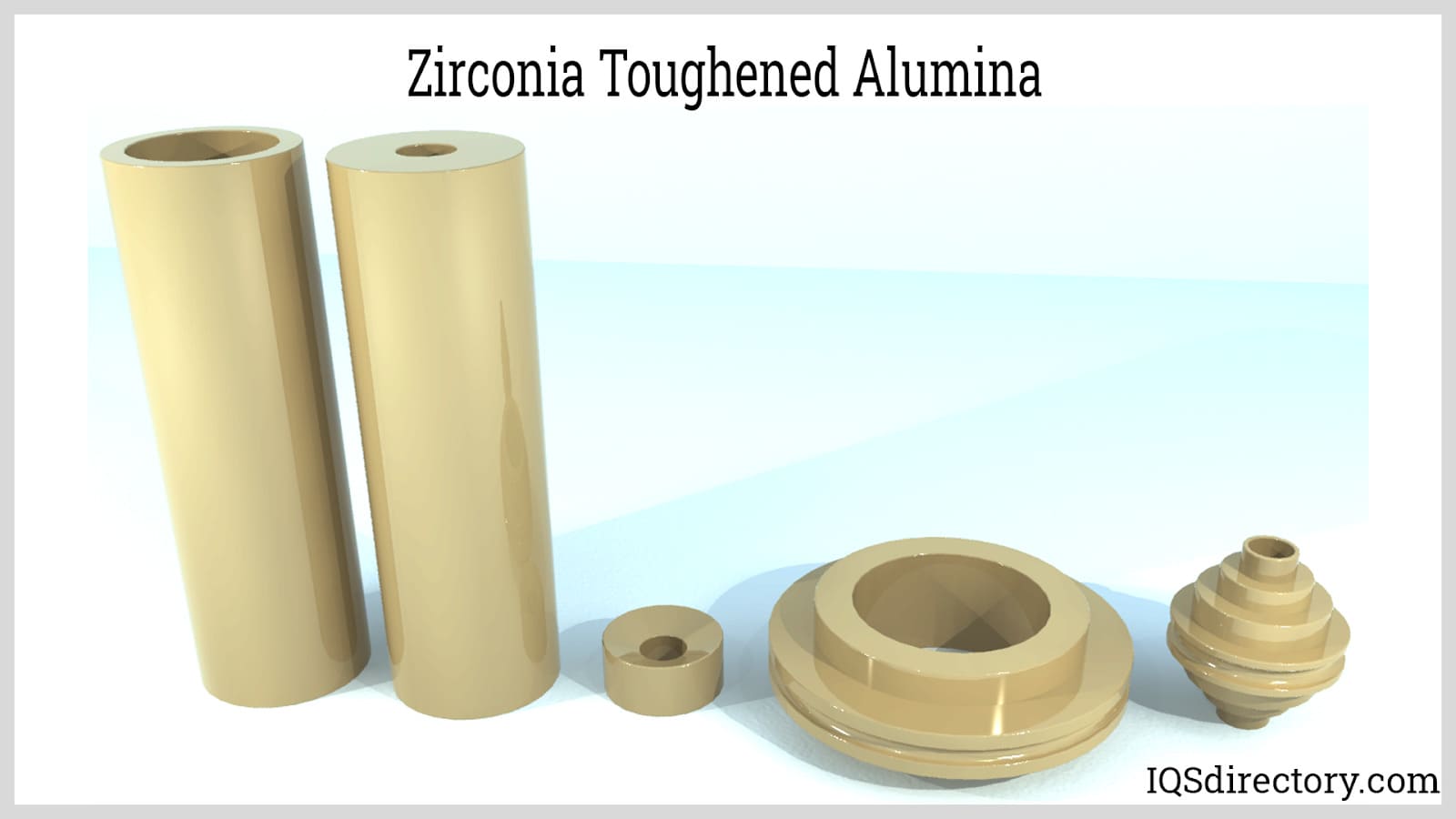
Zirconia ceramics are technical ceramic materials with excellent durability and corrosion resistance without being brittle.
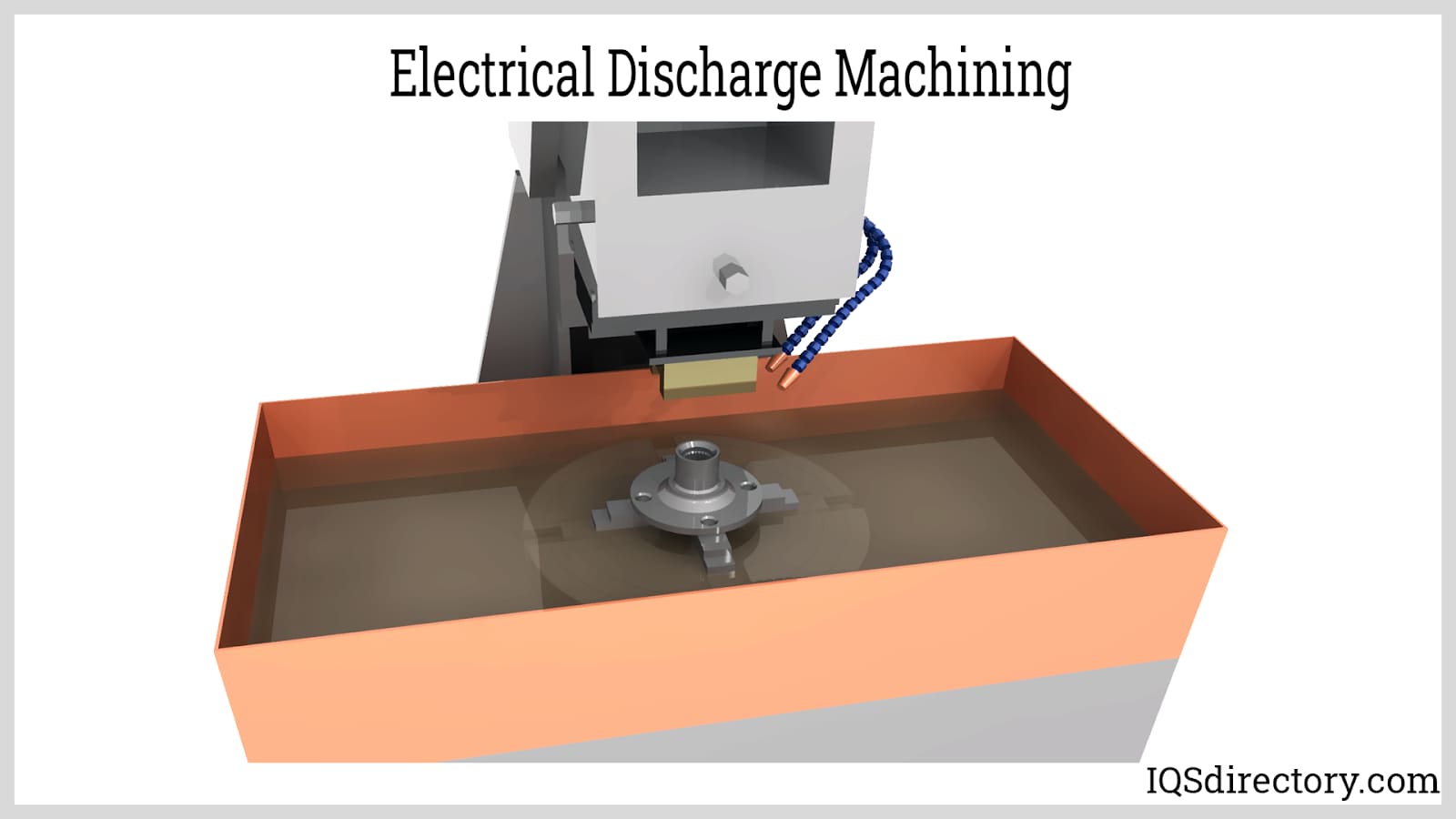
Electrical discharge machining requires workpieces to have a electrical resistivity less than 1000 ohm-centimeter.
Ceramic Manufacturing Types
Alumina Ceramic
Also known as aluminum oxide, this highly durable and cost-effective ceramic material is widely used in industrial and commercial applications due to its exceptional strength and wear resistance.
Alumina Crucibles
These specialized crucibles are made from alumina, the same material used in aluminum metal production. The ceramic form of alumina is frequently chosen for crucible manufacturing because of its remarkable strength, affordability, and ability to withstand extreme temperatures exceeding 3,272°F.
Ceramic Armor
An incredibly hard nonmetallic material known for its excellent fracture toughness, superior wear and corrosion resistance, and high capacity to absorb ballistic impacts, making it ideal for military and defense applications.
Ceramic Balls
Spherical rolling elements made from inorganic, nonmetallic materials, ceramic balls are essential components in rotary and linear motion applications, as well as in a variety of precision-based functions.
Ceramic Bearings
Lightweight and exceptionally smooth, ceramic bearings offer high tolerance and increased rotational speeds, making them advantageous for high-performance machinery and equipment.
Ceramic Bushings
Known for their reliability and durability, ceramic bushings are often composed of alumina ceramics or steatite, providing excellent insulation and resistance to wear.
Ceramic Coatings
Despite their higher cost, ceramic coatings significantly extend the lifespan of coated objects, often by up to ten times, thanks to their superior heat and wear resistance.
Ceramic Composites
Created by blending raw ceramic materials with other substances to enhance strength, durability, and resistance to damage, ceramic composites offer tailored performance for specialized applications.
Ceramic Crucibles
High-temperature-resistant crucibles made from kiln-fired ceramic materials, commonly used in laboratories and industrial processes requiring extreme heat tolerance.
Ceramic Grinding
A precision design and manufacturing process that utilizes abrasives for material removal, shaping, and finishing of ceramic components, ensuring accuracy and smooth surfaces.
Ceramic Insulators
Widely used in electrical applications due to their excellent insulating properties, ceramic insulators help maintain conductivity while preventing unwanted electrical discharge.
Ceramic Machining
The specialized process of designing and manufacturing precision ceramic components, often involving advanced CNC and grinding techniques to achieve exact specifications.
Ceramic Manufacturers
Companies that specialize in producing high-quality ceramic materials and components tailored to a variety of industrial and commercial needs.
Ceramic Rods
Solid cylindrical ceramic components valued for their strength, electrical insulation, and heat resistance in various industrial applications.
Ceramic Spacers
Designed to provide uniform and consistent spacing between materials or components, ceramic spacers ensure stability in electrical, mechanical, and structural applications.
Ceramic Tubes
Hollow cylindrical ceramic components available in single or multi-bore designs, used for high-temperature, electrical, and structural applications.
Ceramic Washers
Highly resistant to abrasion, extreme temperatures, and corrosion, ceramic washers are used in demanding environments where metal alternatives may fail.
Clay Ceramics
Encompassing earthenware, stoneware, porcelain, and bone china, clay ceramics are primarily used for decorative and consumer applications rather than industrial-grade ceramic components.
Industrial Ceramics
Manufactured using non-metallic, inorganic, mineral-based compounds, industrial ceramics are produced in large quantities or sizes for applications requiring high resistance and superior insulation properties.
Mullite Ceramics
A rare and expensive material, mullite ceramics offer unmatched strength and high-temperature resistance, making them ideal for applications requiring low thermal conductivity, low pressure, and high thermal expansion tolerance.
Silicon Carbide
Also known as carborundum, silicon carbide is an extremely hard ceramic composed of silicon and carbon atoms bonded in a crystal lattice. It is widely used for its exceptional hardness, thermal conductivity, and wear resistance.
Sapphire Machining
Employing the same diamond grinding techniques used for dense alumina oxide materials, sapphire machining works with anisotropic, rhombohedral crystal formations of aluminum oxide. Sapphire exhibits high thermal expansion and extreme hardness, making it valuable for precision applications.
Steatite Ceramics
Made from magnesium silicate, steatite ceramics provide advanced electrical insulation, exceptional durability, and mechanical strength. These qualities make steatite a preferred material in thermostat manufacturing and various commercial and residential electrical components.
Zirconia Ceramics
Zirconia is a crucial material in automotive oxygen sensors and dental ceramics, offering outstanding resistance to corrosion, breakage, and abrasion. With its high durability and wear resistance, zirconia ceramics are a top choice for manufacturing precision components that require exceptional longevity and performance.
Ceramic Manufacturing Terms
Adsorption
The process by which one material adheres to another. In ceramics, water molecules are loosely bonded to the surface of clay through this mechanism.
Amorphous
A property indicating that a material lacks a regular, crystalline structure. Glass is an example of an amorphous material, as rapid cooling prevents the formation of an organized crystal lattice.
Attribute
A defining characteristic or quality of an object.
Bisque
Clay that has been fired but remains unglazed, serving as an intermediate stage in ceramic production.
Bloating
A distortion that occurs when gases become trapped within a ceramic material due to excessively rapid firing.
Blunging
The mechanical mixing of clay slurry to achieve a consistent composition.
Ceramic Change
The transformation point during firing when clay undergoes a permanent chemical and structural shift, becoming a ceramic material.
Coefficient of Thermal Expansion
A measurement of how ceramic materials expand when heated and contract when cooled, essential for understanding material stability under temperature fluctuations.
Deflocculation
A process in which a thick clay slurry is thinned into a pourable consistency by adding small amounts of liquid or powder.
Devitrification
The crystallization of a ceramic melt during the cooling phase, resulting in a matte surface texture rather than a glossy finish.
Dunting
Cracking that occurs in fired ceramics due to rapid cooling, often leading to structural weaknesses.
Eutectic
The lowest temperature at which two materials will melt together, an important factor in ceramic glazes and sintering processes.
Firing
The process of heating clay in a kiln to harden and mature it into a durable ceramic product.
Flocculation
A technique used to thicken liquid clay slurry into a gel-like consistency, preventing drips and improving material suspension.
Flux
A substance added to a ceramic mix to lower its melting temperature, aiding in vitrification and glaze formation.
Glaze
A liquid coating applied to bisque or greenware that, when fired, forms a hard, glass-like surface, enhancing durability and aesthetics.
Greenware
Unfired clay objects that are still in their most fragile state, awaiting the firing process.
Kiln
A high-temperature furnace or oven used to fire ceramics, achieving the necessary heat for structural and chemical transformation.
Maturity
The stage at which a ceramic piece has undergone the correct amount of firing, achieving its intended hardness and durability.
Mold
A fixed form used to shape clay into a specific design before firing, often used in mass production.
Porosity
The measure of empty spaces or pores within a ceramic material, which affects its absorption properties and structural integrity.
Refractory
The ability of a material to withstand high temperatures without melting, deforming, or breaking down.
Sintering
The process of heating clay to the point at which its particles bond together, preventing water absorption while maintaining structural integrity.
Thermal Shock
The stress and potential cracking caused by sudden temperature changes, which can lead to fractures in ceramic materials.
Vitrification
The stage during firing at which clay particles transform into a glass-like substance, forming a dense, non-porous ceramic.
More Ceramic Manufacturing Information