Check Valves
Check valves are essential components designed to regulate the flow of gas or fluid through two openings in the valve body. One opening allows the fluid to enter, while the other provides an exit, ensuring unidirectional flow. These self-activating valves respond to the pressure created by the flow rate, which is influenced by the mechanisms they serve. Despite their small size and straightforward design, check valves are integral to many everyday household items. The development of a stainless-steel spring valve is guided by the required cracking pressure, the specific threshold at which the valve will begin operation. Check valve manufacturers offer a range of sizes and price points to accommodate various applications, using materials such as plastics, stainless steel, and polypropylene. Although the fundamental function and structure of check valves remain relatively simple, careful engineering is necessary to guarantee proper material flow and effective backflow prevention.
Applications of Check Valves
Domestic Use
In home rainwater harvesting systems, check valves play a crucial role in regulating water flow within piping systems connected to the main supply. By preventing continuous water movement, these valves ensure that rainwater does not contaminate the primary water source while also serving as a backup mechanism in case of sump pump failure.
In agricultural applications, check valves are integrated into drip and sprinkler irrigation systems to maintain consistent water distribution. These small yet effective valves prevent drainage when the system is turned off, ensuring efficiency and water conservation. Additionally, they play a vital role in domestic heating systems by controlling vertical convection, particularly in solar thermal installations, where they help regulate heat distribution.
Industrial Use
Check valves are widely employed in industrial settings, including chemical and power plants, where they help maintain controlled flow rates and pressure within complex piping systems. In the nuclear sector, they are essential for supplying cooling water to reactors at a precise speed, pressure, and volume, ensuring operational safety. The aerospace and aircraft industries also rely on check valves to withstand extreme vibrations, high temperatures, and exposure to corrosive fluids.
In public safety applications, high-pressure piping systems in fire engines incorporate check valves to maintain consistent water flow for firefighting operations. These valves also contribute to critical functions in aircraft hydraulic systems, propulsion propellant control, attitude control systems, and reaction control systems used in spacecraft and launch vehicles. In industries where multiple gases combine into a single stream, check valves play a crucial role in preventing gas mixing at the source, maintaining safety and efficiency.
Check valves also find application in piston-driven and diaphragm pumps. In metering and chromatography pumps, inlet and outlet ball check valves regulate fluid movement, preventing backflow. Similarly, large-scale fluid transfer systems utilize ball check valves to maintain directional flow. Steam boiler injectors incorporate control valve fittings to prevent reverse flow, ensuring stable operation.
Various types of check valves serve specific functions within industrial processes. Ball check valves, swing check valves, wafer check valves, and lift check valves facilitate continuous downstream fluid movement while blocking upstream contamination. Spring check valves mitigate valve clapping and overflow issues caused by high differential pressure.
Double check valves, designed with multiple valve components, enhance durability and minimize the risk of backflow, reducing the potential for cross-contamination, flooding, and pressure surges. Available in iron, plastic, or stainless steel, these valves provide reliable performance across diverse applications. In medical settings, diaphragm check valves ensure that liquids flow in a controlled manner, preventing unintended fluid migration within the human body, making them indispensable in hospital environments.
History and Evolution
In 1907, Frank P. Cotter introduced a simple, self-sealing check valve that could be easily integrated into existing piping systems without requiring specialized tools. Nearly a decade later, in 1916, Nikola Tesla developed a one-way valve for fluids, now known as the Tesla valve, which he patented in 1920.
Today, check valves are indispensable across virtually every industry, including aerospace, automotive, agriculture, water treatment, and manufacturing. Their evolution has paved the way for innovative designs, such as plastic diaphragm valves, which are widely utilized in the medical field. The choice of materials for check valve construction varies based on industry requirements, ensuring durability and optimal performance in diverse applications.
Design and Engineering of Check Valves
Check valves serve essential functions across commercial, industrial, and domestic applications, ensuring the safe and consistent flow of various substances, including acids, bases, water, slurry, oxygen, fuel, and hazardous materials. The effectiveness of a check valve is heavily influenced by the materials used in its construction. Selecting a material compatible with the gas or fluid it will handle is crucial, as incompatible materials can degrade, erode, or contaminate the process stream. Fortunately, compatibility is always achievable due to the wide range of materials available, including plastics, metals, and synthetics. Common options include PVC, brass, ductile iron, copper, polyethylene, polypropylene, aluminum, steel, stainless steel, and rubber. Plastics, known for their lightweight durability and ease of installation, are particularly well-suited for household applications, whereas stainless steel and iron components offer enhanced strength for industrial use. Other critical factors to consider when selecting a check valve include media temperature and the valve’s flow coefficient.
PVC check valves, often referred to as relief valves, are widely used alongside brass check valves due to their resilience against constant wear and chemical corrosion. Proper check valve configuration helps mitigate unnecessary wear, extending the product’s lifespan. The versatility of silicone diaphragms has enabled the development of check valves specifically designed for medical applications, where precision and reliability are paramount.
Check valves are available in a range of sizes, with the most crucial aspect being the diameter of the seat and stopping mechanism, which can measure anywhere from less than an inch to several feet across. Proper sizing ensures seamless integration into pre-existing flow lines, with the pipe or tubing dimensions determining the appropriate valve size. The size of a check valve directly affects its pressure rating or cracking pressure—the minimum pressure required for the valve to open. If a valve is too large, the process stream may lack the necessary force to activate it, even when opposing pressure is exceeded. Conversely, an undersized valve may remain open, allowing continuous flow without closing when needed. Such malfunctions can lead to equipment damage, material waste, and hazardous cross-contamination, underscoring the importance of precise valve selection and installation.
Some Benefits of Check Valves
Check valves regulate the pressure flow rate of fluids within piping systems across various industry sectors, ensuring smooth and controlled movement while preventing cross-contamination between substances like water and oil. Their role in maintaining fluid integrity is critical in applications where purity and separation of materials are essential.
Stainless steel check valves offer exceptional durability and resistance to corrosion, making them a reliable choice for handling oil, gas, and water. Their robust construction ensures that stainless steel springs maintain an uninterrupted flow, even under demanding conditions.
In flood management systems, check valves play a crucial role in directing storm surges and excess water into the appropriate drainage channels, effectively preventing contamination of fresh water sources. This function is vital in municipal infrastructure, where maintaining clean and safe water supplies is a top priority.
Pressure regulation, particularly in psi-controlled systems, is another critical aspect of check valve functionality. Their ability to manage pressure fluctuations makes them essential in designing pressure-controlled devices such as scuba tanks, where precise regulation ensures safety and efficiency in underwater environments.
Check Valve Images, Diagrams and Visual Concepts
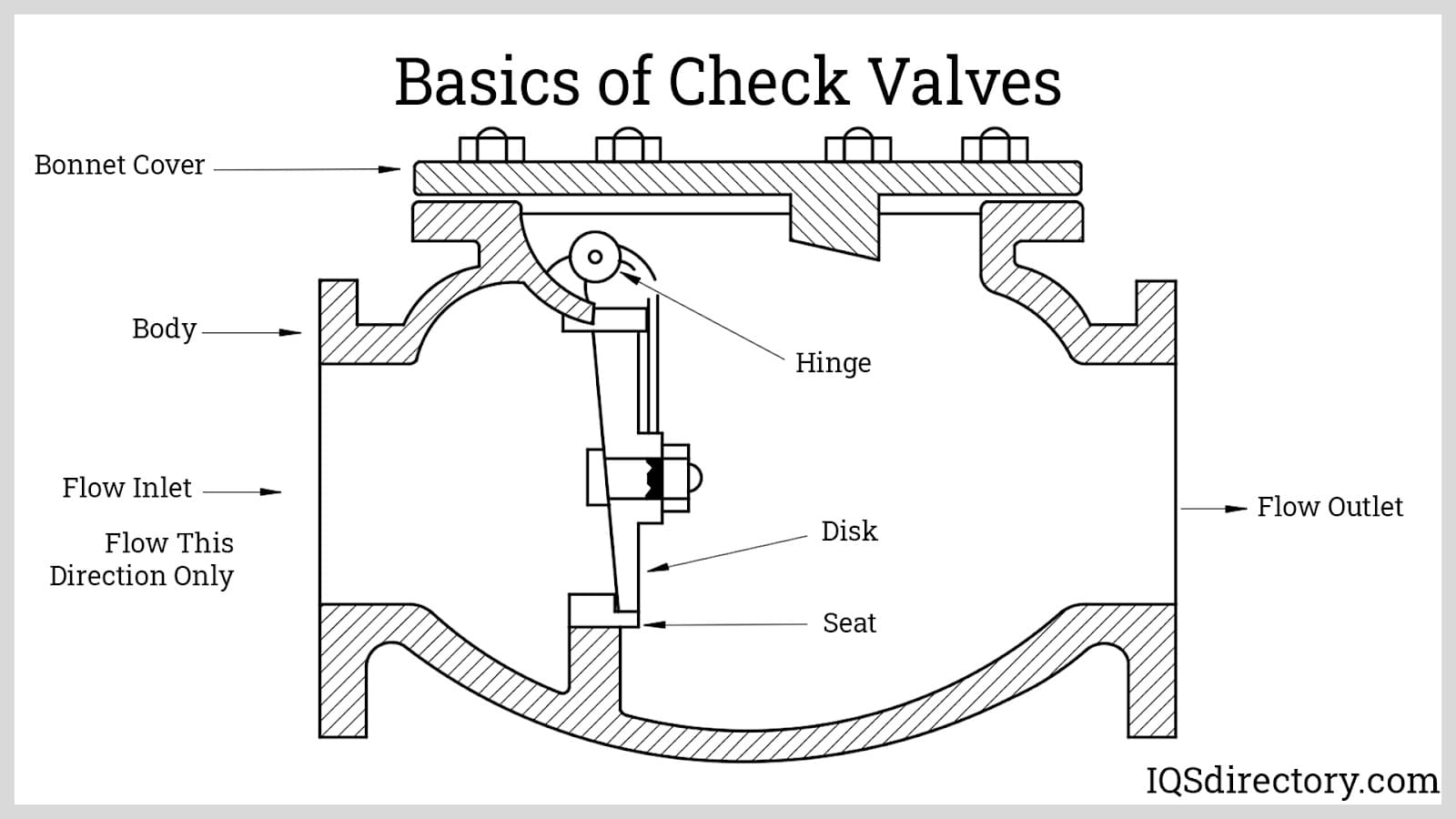
Check valves are an automatic safety device designed to allow fluids and gasses to flow in one direction to prevent reverse flow.
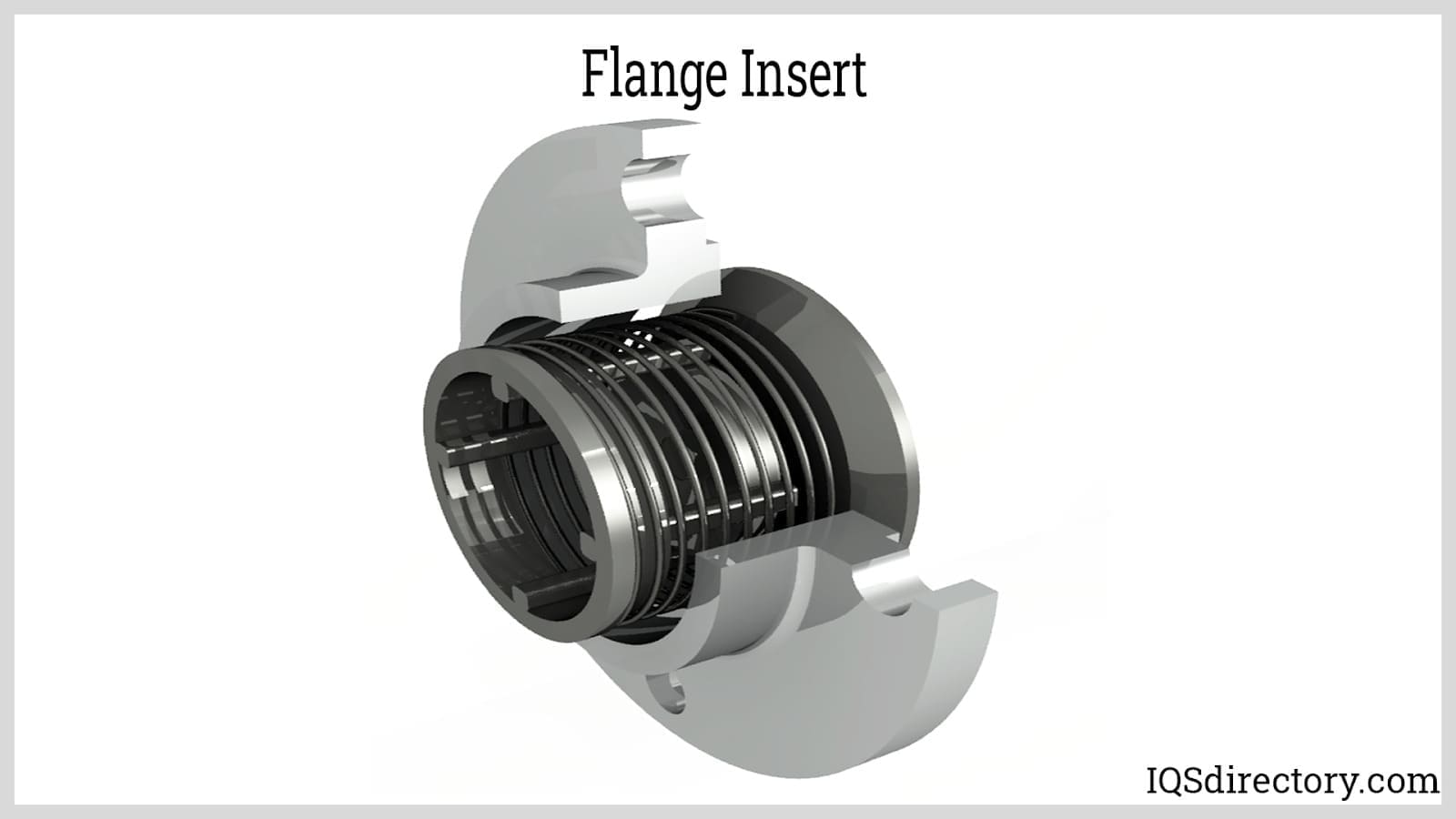
The end of the check valve which prevents the reversal of the fluids flow.
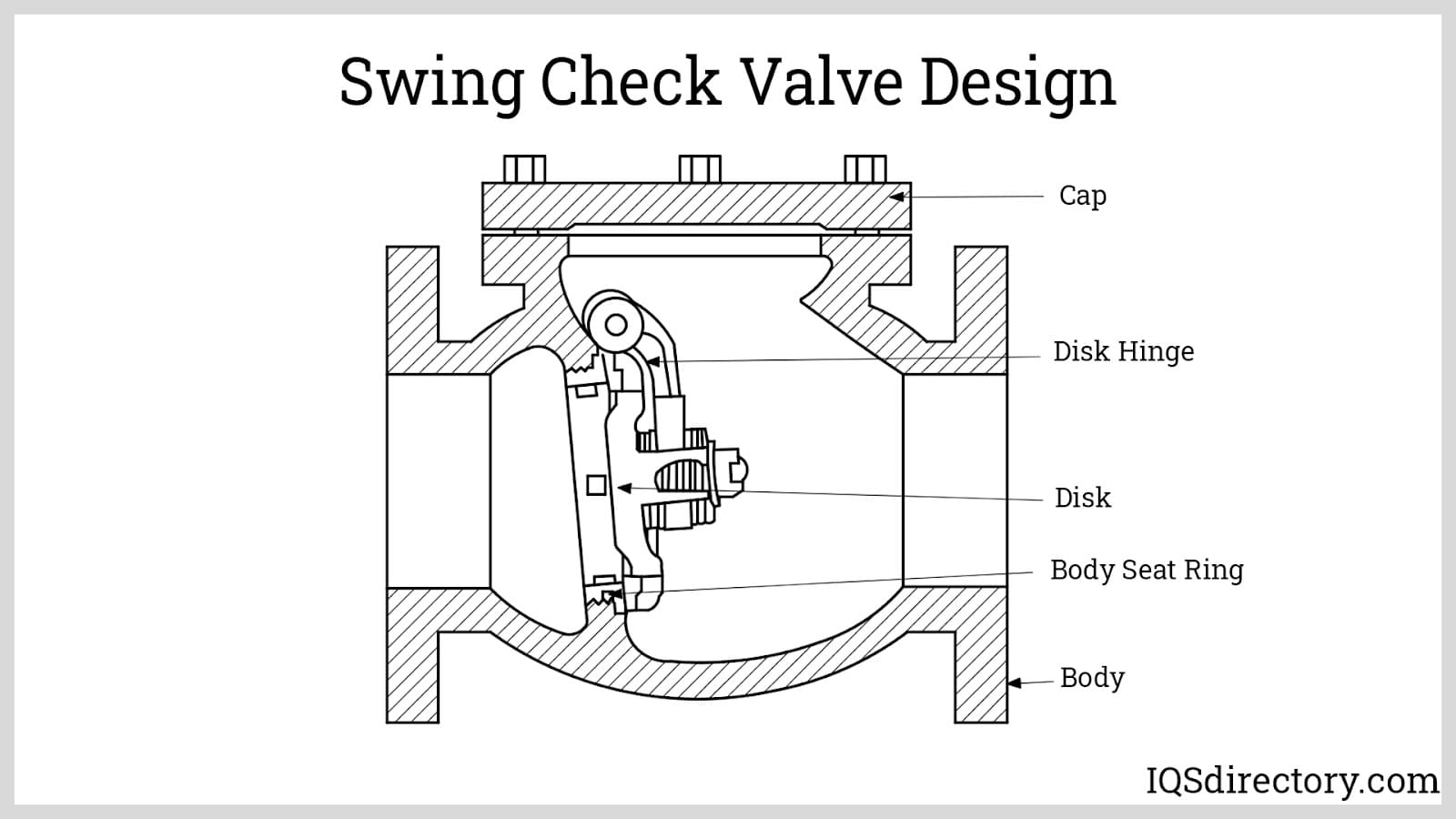
Swing check valves have an unguided disc which moves into a fully open position when flow pressure is applied.
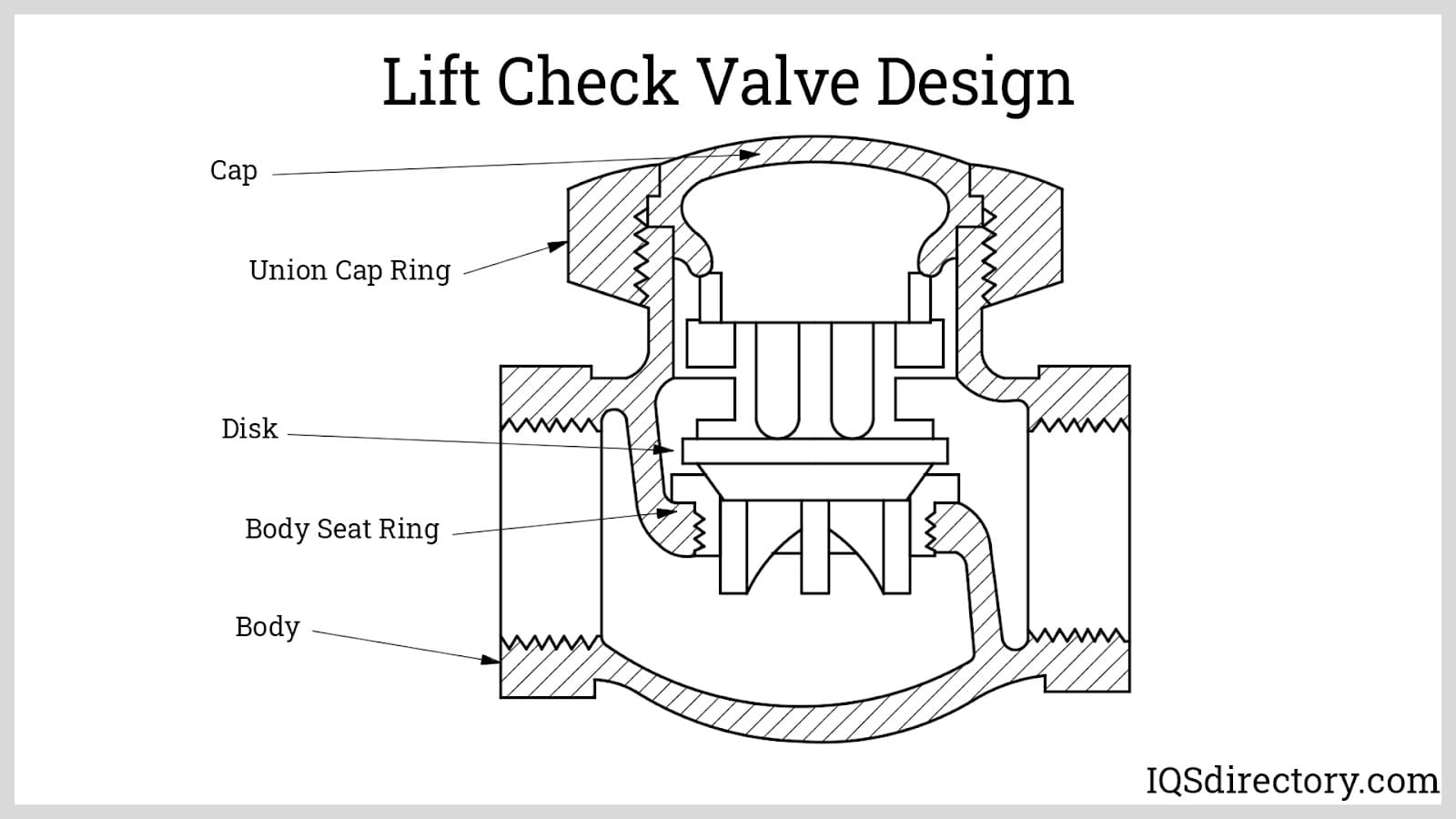
Lift check valves have a guided piston that lifts when the flow enters the check valve.
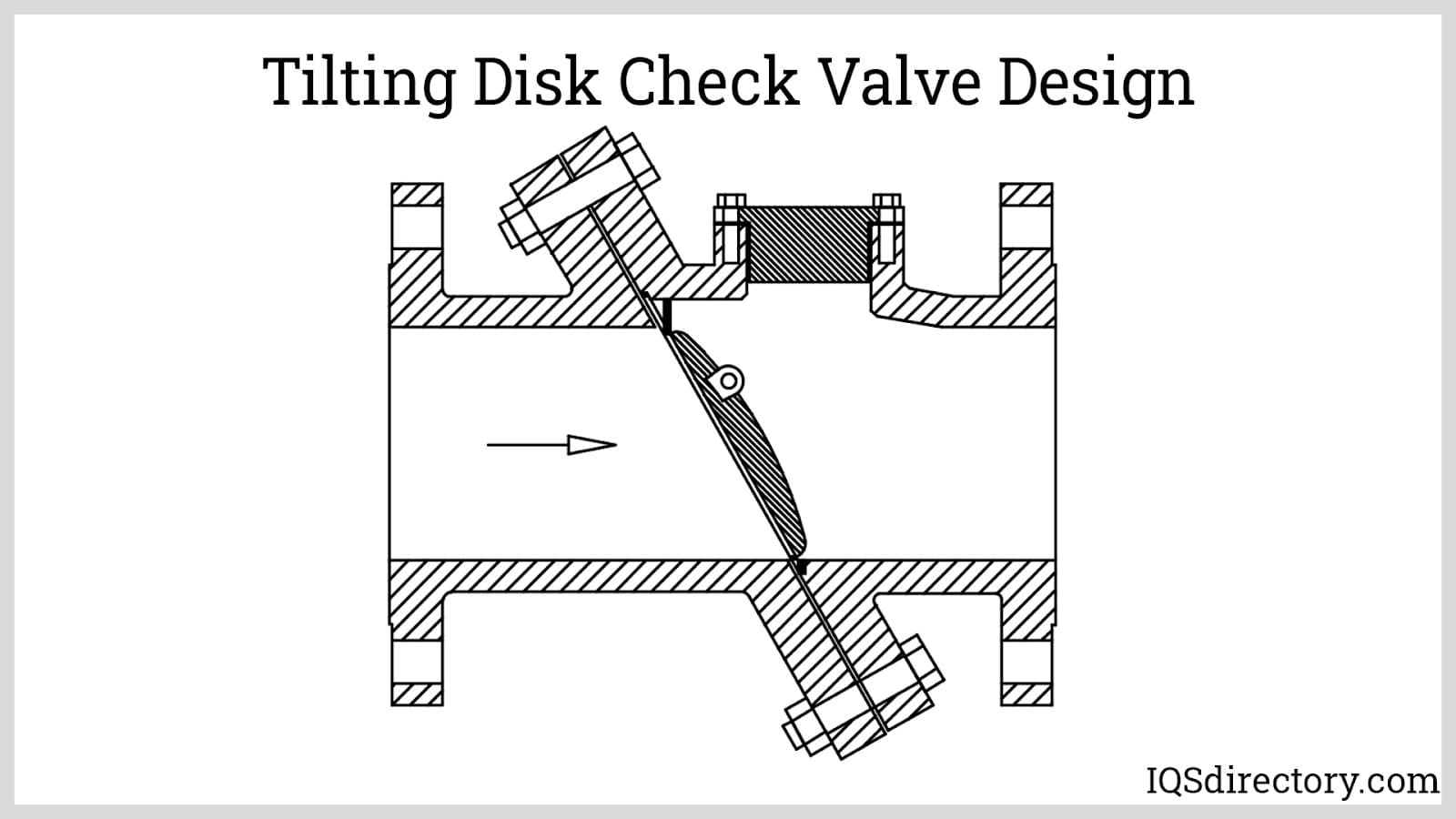
The design of tilting check valves are capable of remaining open when the flow has a low velocity and close quickly.
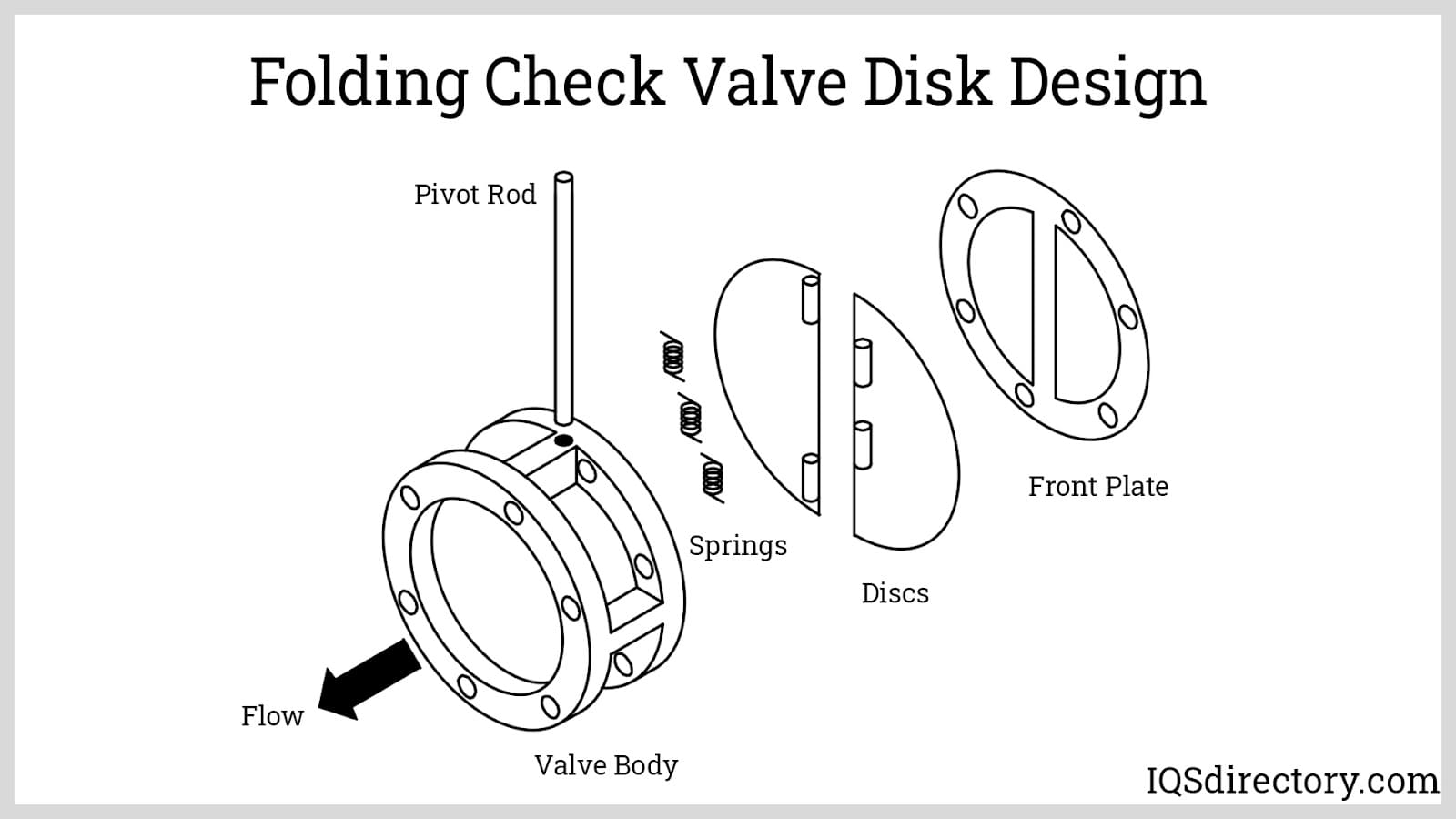
The folding disc check valve is a split disc designed to open under pressure.
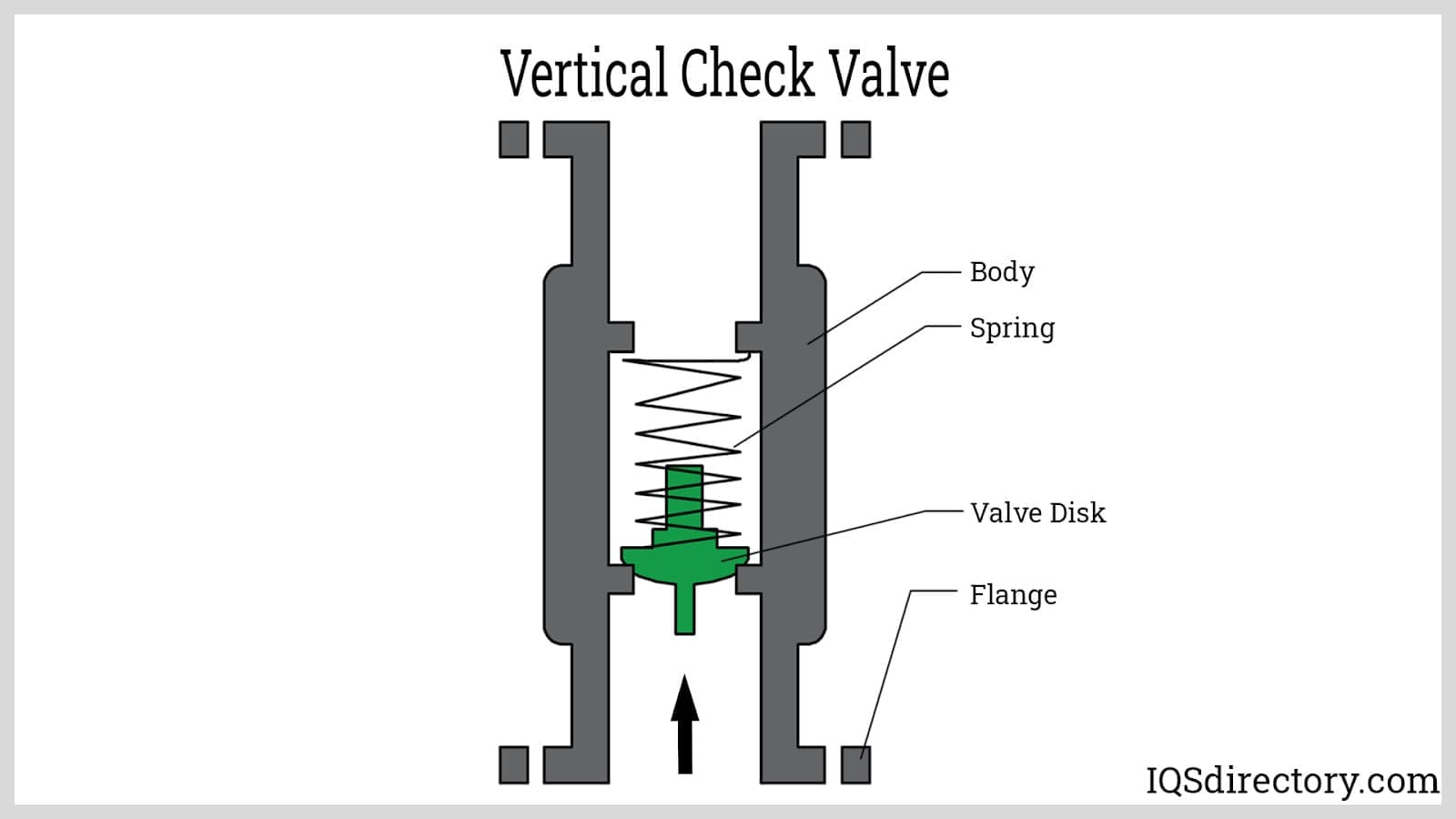
Vertical check valves are used to keep the disc against the seat, then the valve is held shut by the spring until a sufficient amount of pressure is applied to push the spring back and open the valve.
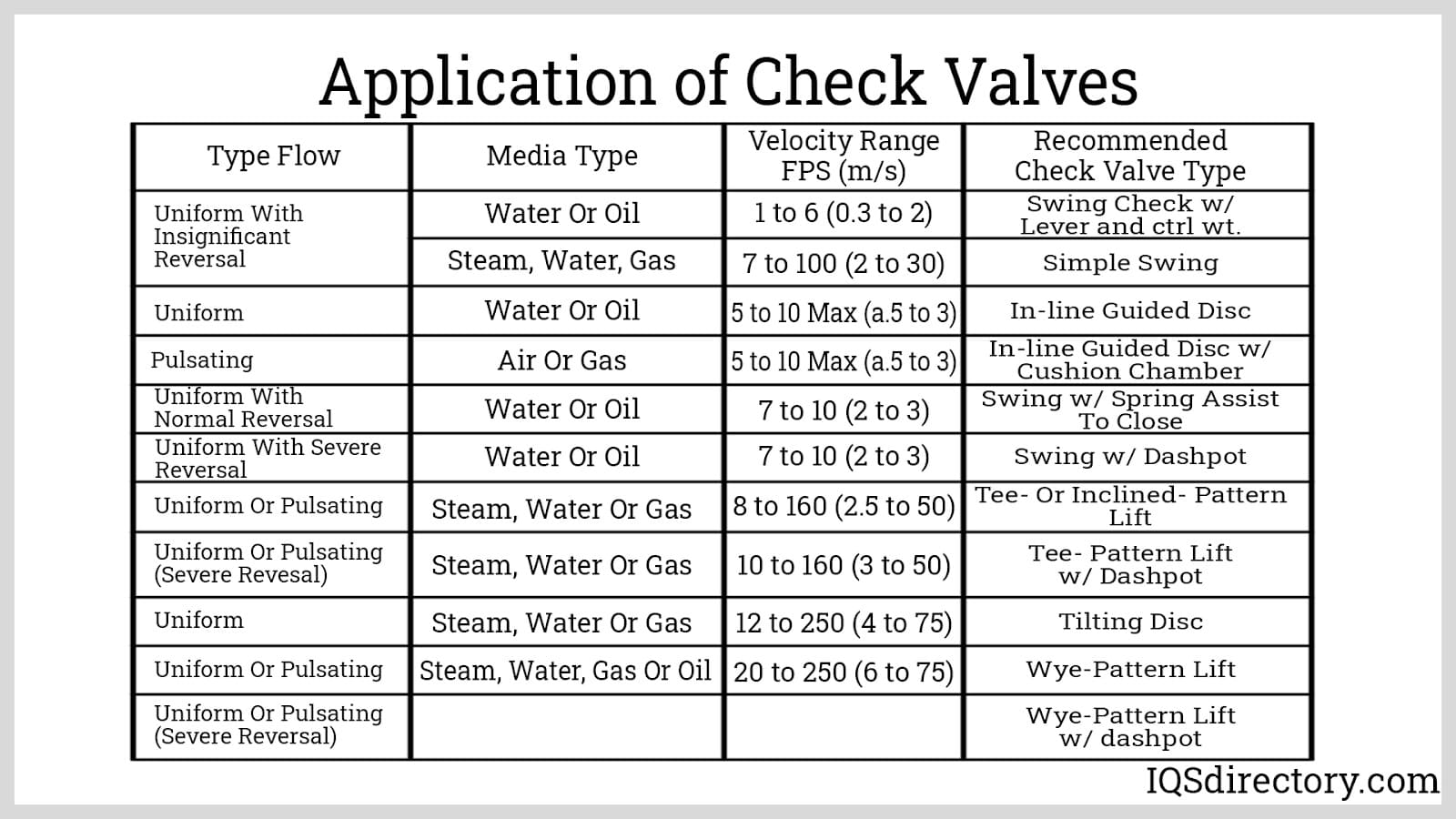
The different varieties of check valves, the type of media, and the type of flow.
Check Valve Accessories
Various check valves come equipped with specialized accessories to enhance performance and durability. Among these are ductile iron body check valves and center-guided silent check valves, designed with straighter vanes to effectively eliminate water hammer and reduce pressure fluctuations. Additionally, check valves often include aluminum-bronze and stainless steel discs, providing enhanced resistance to wear and corrosion for long-lasting functionality. Some manufacturers also produce globe-style body check valves, engineered to minimize pressure loss while maintaining efficient fluid control within the system.
Check Valve Installation and Care
For proper installation and servicing, a licensed professional contractor is best suited to handle the task. Their expertise ensures correct installation, preventing potential issues that could arise from an improperly fitted check valve. A well-installed valve guarantees reliable performance and longevity.
Manufacturers design check valves with directional arrows, typically marked on the valve body or tag, to indicate the proper flow direction, ensuring optimal functionality. The correct application of a check valve depends on several factors, including flow type, pressure, temperature, volume, and psi requirements. Using certified check valves is essential to prevent premature equipment failure and contamination, safeguarding both the system and the materials being transferred.
Routine maintenance is crucial for sustained efficiency. During inspections, check valve operations through a transparent cover to verify proper function. Lubricant the O-ring thoroughly with silicone grease before reassembling the valve to maintain a secure seal and ensure smooth operation.
Important Standards Related to Check Valves
The Drinking Water Act, enacted in January 2014, was introduced to minimize lead levels in drinking water and enhance public health safety. According to this legislation, any component that comes into contact with drinking water must contain no more than 0.25% lead. To prevent lead contamination and ensure compliance, individuals with older piping systems are encouraged to transition to modern alternatives that incorporate stainless steel or plastic components, both of which provide a safer and more durable solution for clean water distribution.
Types of Check Valves
Ball Check Valve
A loose, spherical ball is used to block fluid flow within the valve. In some designs, the ball is spring-loaded with a stainless steel spring to keep it securely shut. If the valve is not spring-loaded, the ball relies on reverse flow to move back into its seat, creating a reliable sealing mechanism. A three-way ball valve can incorporate a ball, gate, or globe valve element, typically positioned at the center of the apparatus to regulate flow.
Brass Check Valve
Constructed from an alloy of copper and zinc, these pipe fittings are designed to regulate process stream flow while preventing back pressure and backflow, ensuring smooth operation in various plumbing and industrial systems.
Butterfly Check Valve
Designed to regulate pressure flow in large piping systems, the disc within the valve takes the shape of the tube and remains in the flow path at all times. Regardless of the valve's position, any psi changes induce movement in the disc. Butterfly check valves are available in iron body and stainless steel configurations to meet the demands of different applications.
Carbon Steel Check Valve
Featuring stainless steel internal components, including butterfly valve elements, carbon steel check valves are well-suited for utility applications and industrial processes such as chemical processing, steam systems, petrochemical operations, water distribution, and gas flow management.
Clapper Valve
A check valve commonly used in firefighting systems, it features a hinged gate, often reinforced with a spring mechanism that keeps it shut unless the flow direction pushes it open. This ensures unidirectional flow control, making it a critical safety component in emergency water distribution.
Diaphragm Check Valve
Designed with a flexible rubber diaphragm that creates a normally-closed valve, this type of check valve requires upstream pressure to be higher than downstream pressure to open. When the positive pressure stops, the diaphragm automatically flexes back to its original closed position. This valve is particularly useful in applications with low upstream pressure, as it allows for minimal cracking pressure to initiate flow.
Double Check Valve
Comprising at least two independently operating check valves within a single system, these valves are commonly used in liquid service applications where enhanced protection against backflow is required.
Duckbill Valve
Shaped like a duck’s mouth, this valve effectively prevents backflow using a flexible synthetic elastomer or rubber construction that resists corrosion and wear.
Foot Valve
Primarily used in conjunction with pumps, foot valves facilitate water movement while preventing backflow, ensuring consistent pressure and efficient operation in pumping systems.
Hydraulic Check Valve
Designed specifically for hydraulic systems, these valves prevent reverse flow using a ball or poppet mechanism, maintaining pressure integrity and system efficiency.
Lift Check Valve
A type of disc check valve where the lift disc is raised from its seat when the inlet fluid psi exceeds a certain threshold, allowing downstream fluid flow. Once the pressure equalizes or reverses, gravity or downstream pressure forces the disc back into its seat, functioning as a safety relief valve. These systems do not use stainless steel rings for control.
Miniature Check Valves
Engineered for precision fluid or gas flow regulation in small-scale applications, these micro valves maintain unidirectional flow using the same principles as larger check valves but in a significantly compact form.
Non-Return
Another term for check valves, these devices regulate the directionality of gas or liquid process streams. Also known as one-way directional valves, they are used in industrial, commercial, and domestic applications to ensure unidirectional material flow.
Pilot-operated Check Valves
Non-modular valves arranged in flanged mounting configurations, these valves enable the locking and feeding of hydraulic cylinders while offering exceptional sealing capabilities.
Plastic
Unidirectional flow control devices made from organic, synthetic, or processed polymers, these valves are lightweight, corrosion-resistant, and ideal for various applications.
Pneumatic
Designed to regulate air or fluid flow in pneumatic systems, these valves can allow flow in one or two directions. When bidirectional flow is permitted, it is typically metered to control flow rate and pressure.
PVC Check Valves
Constructed from polyvinyl chloride, a highly versatile thermoplastic resin, these unidirectional flow regulators are well-suited for industrial, commercial, and domestic applications. PVC can be formulated to meet the specific requirements of various check valve applications.
Relief
These valves prevent excessive pressure buildup in piping systems or closed-top vessels. Normally closed, they open only when system pressure reaches a predetermined setpoint, allowing safe pressure relief.
Sanitary
Used in applications where fluid purity is critical, these valves help maintain germ-free conditions, making them ideal for medical, food processing, and dairy industries.
Silent Check Valves
Engineered to eliminate water hammer and pressure shock in piping systems, these valves close before fluid flow reversal occurs. Their silent operation ensures smooth performance and minimizes hammering noises.
Spring
Incorporating coiled metal components, these valves require increased pressure to open, helping maintain closure against strong reverse flow surges.
Stainless Steel Valves
Highly resistant to corrosion, these durable valves are widely used in stainless steel spring equipment for handling water, oil, and gasoline under pressure.
Stop
A specialized check valve with an override control feature, allowing the user to halt flow regardless of direction or pressure. When open, it functions as a standard check valve, but it can also be manually closed to stop flow entirely.
Swing Check Valve
These valves feature a flat disc that pivots or swings on a hinge pin, opening to permit forward flow and closing to prevent backflow. Unlike spring-loaded check valves, swing check valves rely on gravity and fluid movement for operation.
Traditional Swing Check Valves
In vertical pipe installations, these valves may experience slamming due to the long stroke and inertia of the disc. Some designs include a lever and weight accessory to mitigate this issue. Larger swing check valves are commonly used in wastewater management systems, including sewage treatment and toilet facilities, as they can handle a mixture of liquids and solids.
Wafer Check Valves
One-way valves that prevent backflow by allowing fluids to move in a single direction, wafer check valves open when the forward fluid pressure reaches a sufficient level and close in response to back pressure. Available in stainless steel and iron body configurations, they provide reliable flow control in industrial and commercial applications.
Check Valve Terms and Definitions
Actuator
A critical component of a regulating check valve that transforms various energy sources—such as electrical or fluid power—into mechanical motion, enabling the opening or closing of the valve seats.
Backflow
The unintended reversal of a system’s normal fluid flow, occurring when downstream pressure surpasses supply pressure, potentially leading to contamination or operational inefficiencies.
Back Pressure
The resistance created by gravity, pumps, or pipeline restrictions, which slows or alters the main flow. This pressure is measured in inches of water (H₂O) or pounds per square inch (PSI).
Elastomer
A flexible material widely used by leading check valve manufacturers to produce custom check valves. It possesses the ability to stretch or distort under stress but will return to its original shape once the stress is removed.
Extended Bonnet
A protective device designed to safeguard sealing materials within check valves when handling extremely high or low-temperature substances. By creating a thermal barrier, it helps prevent degradation or damage.
Fluid Power
The application of compressed liquids or gases to generate motion and force within mechanical systems. This broad category includes both hydraulic and pneumatic technologies, which are essential for controlling and operating check valves.
Penstock Valve
A specialized gate valve commonly found in wastewater treatment plants. It serves as a containment mechanism, regulating the flow of fluids through check valves and custom check valve assemblies.
Pilot Valve
A small but powerful valve designed to control a larger check valve with minimal energy input. It is particularly useful in applications where the system requires the no-return function of check valves for only part of the operational cycle.
Pneumatic
A term describing systems or devices that operate using pressurized air or gas to generate movement or force.
Pneumatic Actuator
A device that harnesses pneumatic energy to regulate, open, or close check valves. Many custom check valves incorporate an internal spring that facilitates automatic closure when air pressure is released.
Poppet
A moving component within check valves that travels perpendicularly to or from its seat, controlling fluid or gas flow.
Positioner
An essential device that ensures the closing mechanism of check valves remains correctly aligned, maintaining proper sealing and operation.
Pressure Differential
The variance in pressure between the inlet and outlet of a check valve, which determines its ability to regulate fluid flow effectively.
Pressure Spike
A sudden and rapid increase in system pressure, frequently observed in custom check valves, which can impact performance and longevity if not properly managed.
PSI (Pounds Per Square Inch)
A standard unit of pressure measurement, equivalent to the metric kilonewtons per square centimeter, used to quantify force applied over an area.
Tank Valves
Check valves specifically designed for insertion at the base of tanks, providing efficient flow regulation and backflow prevention in storage applications.
Valve Seats
The stationary sealing surface within custom check valves that restricts fluid or gas movement when it comes into contact with the movable closure component, ensuring precise flow control.
More Check Valves Information